How to Choose the Best Sandblasting Equipment for Mold Finishing
February 6, 2025
Mold finishing is a critical process that directly impacts the quality of final products. According to the Global Mold Surface Treatment Market Report (Grand View Research, 2023), improper surface preparation can lead to a defect rate of 15%-20%.
In India, where the manufacturing sector is rapidly expanding, many mold manufacturers face challenges with traditional sandblasting equipment, such as excessive dust, high media consumption, and frequent maintenance issues.
This guide will help you understand the key factors to consider when selecting sandblasting equipment for mold finishing, compare five popular machine types, and explore how advanced equipment can optimize the performance of ceramic blast beads.
Common Challenges of Traditional Sandblasting Equipment
Dust Issues
One of the most critical challenges faced by mold manufacturers in India is the excessive dust emissions generated by traditional sandblasting equipment. This leads to serious environmental issues, poor working conditions and increased health risks for operators.
According to industry feedback, dust concentrations in traditional sandblasting processes can be as high as 200-300 mg/m³, far exceeding the 50 mg/m³ limit set by the Central Pollution Control Board (CPCB) of India.
Abrasive Consumption
Another major disadvantage of traditional sandblasting equipment is the high abrasive consumption rate. For example, when using glass beads, the media loss rate can be as high as 40-50%, resulting in frequent refilling and increased operating costs.
In contrast, advanced ceramic sandblasting media can reduce media consumption to less than 10%, significantly improving cost efficiency.
Equipment Maintenance Costs
Reports show that such equipment has a 30% higher failure rate due to dust-related clogging and component wear. As a result, companies need to pay an additional $5,000 in maintenance costs each year, further affecting profitability.
These challenges highlight the urgent need for more efficient and environmentally friendly sandblasting solutions in the Indian industrial market. Manufacturers looking to improve their operations should consider investing in modern sandblasting equipment that minimizes dust emissions, reduces abrasive consumption.
3 Core Metrics for Mold Finishing Equipment
When choosing sandblasting equipment, three critical metrics determine its effectiveness: PSI control, media recovery rate, and dust collection efficiency.
PSI Control System
Precision mold finishing requires adjustable PSI ranges (typically 50-120 PSI). Traditional equipment often operates at a fixed PSI (e.g., 80 PSI), resulting in uneven surface treatment. For example, an Indian automotive mold manufacturer reported a 50% improvement in surface finish (Ra value reduced from 1.2µm to 0.6µm) after switching to equipment with precise PSI control.
Abrasive Recycling System
Abrasive media recovery rate directly impacts operational costs. Traditional equipment recovers only 60%-70% of the media, while advanced systems achieve over 90% recovery. This reduces media consumption by up to 30%, making it a cost-effective solution for long-term use.
Dust Collection Unit
Low-dust blasting solutions are essential for both worker safety and environmental compliance. High-performance dust collection systems can reduce dust emissions to below 20 mg/m³, significantly lower than the 200-300 mg/m³ typical of traditional equipment. An Indian electronics mold manufacturer noted a 50% reduction in worker health complaints after upgrading to a low-dust system.
Comparison of 5 Sandblasting Machine Types
Here’s a detailed comparison of five popular sandblasting machine types, highlighting their strengths, weaknesses, and suitability for mold finishing applications.
Pneumatic Blasting Cabinet
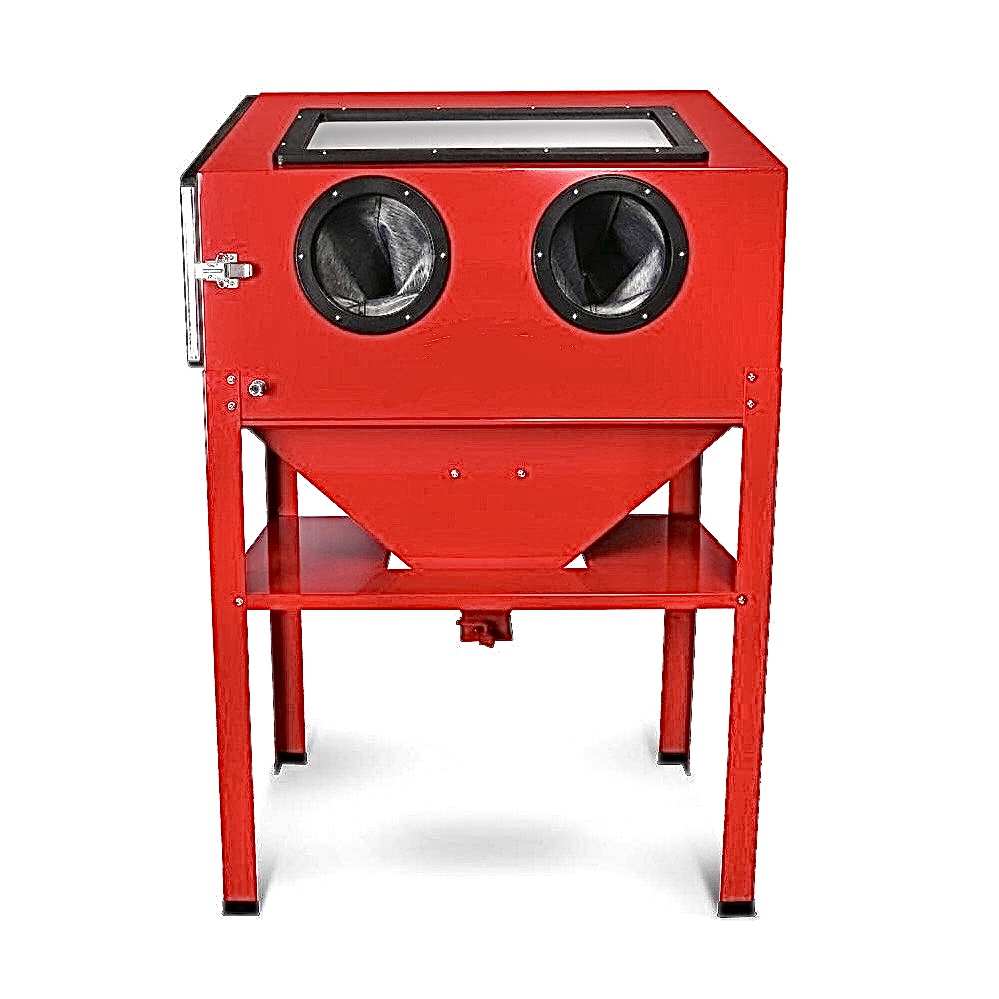
Ideal for small-scale operations, pneumatic cabinets offer flexible PSI control (50-120 PSI) and are cost-effective. However, their media recovery rate is relatively low (around 65%), and dust control is moderate.
Example: An Indian plastic mold manufacturer reduced media consumption by 20% using a pneumatic cabinet with an upgraded dust collection system.
Wet Blasting Machine
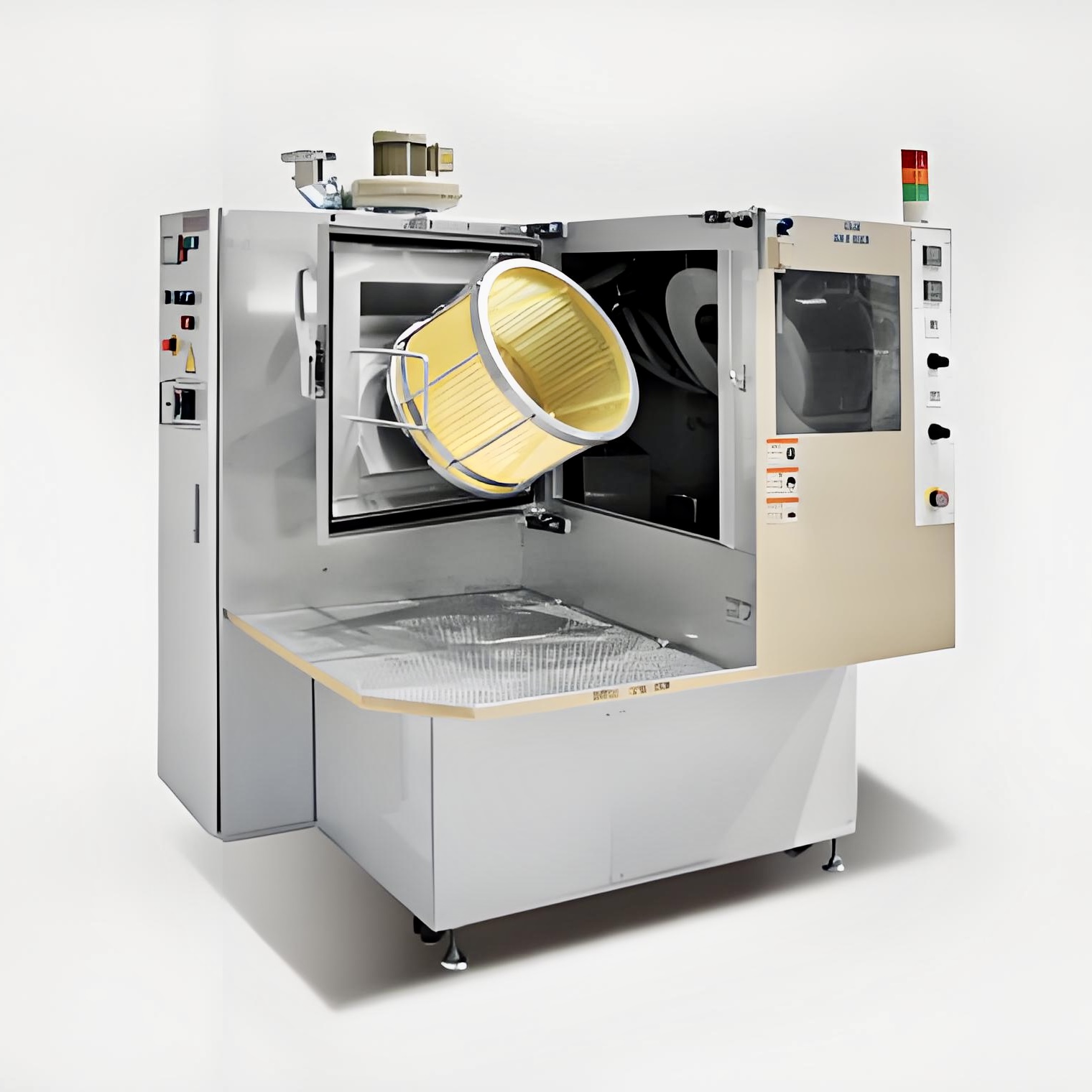
Wet blasting is perfect for delicate molds, offering near-zero dust emissions and exceptional surface finishes. However, media recovery rates are lower (around 60%), and maintenance can be complex.
Example: A medical mold manufacturer achieved consistent Ra values below 0.4µm using wet blasting for high-precision components.
Automated Robotic Blasting System
Robotic systems provide unmatched consistency and dust control, making them ideal for complex molds. While the initial cost is high, they significantly reduce labor expenses.
Example: An automotive mold manufacturer cut labor costs by 30% and improved finish uniformity with an automated system.
Wheel Blasting Machine
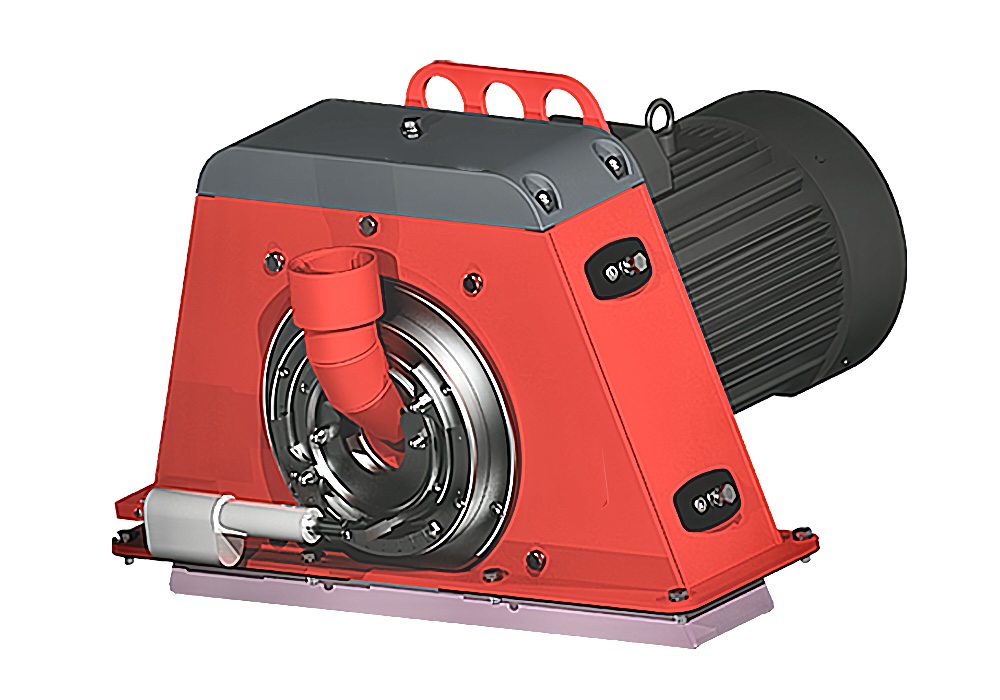
Designed for high-volume processing, wheel blasters excel in media recovery (up to 85%) and are highly efficient for large molds. However, their PSI range is limited (80-100 PSI), and the initial investment is higher.
Example: A die-casting mold manufacturer increased productivity by 40% after adopting a wheel blasting system.
Portable Blasting Equipment
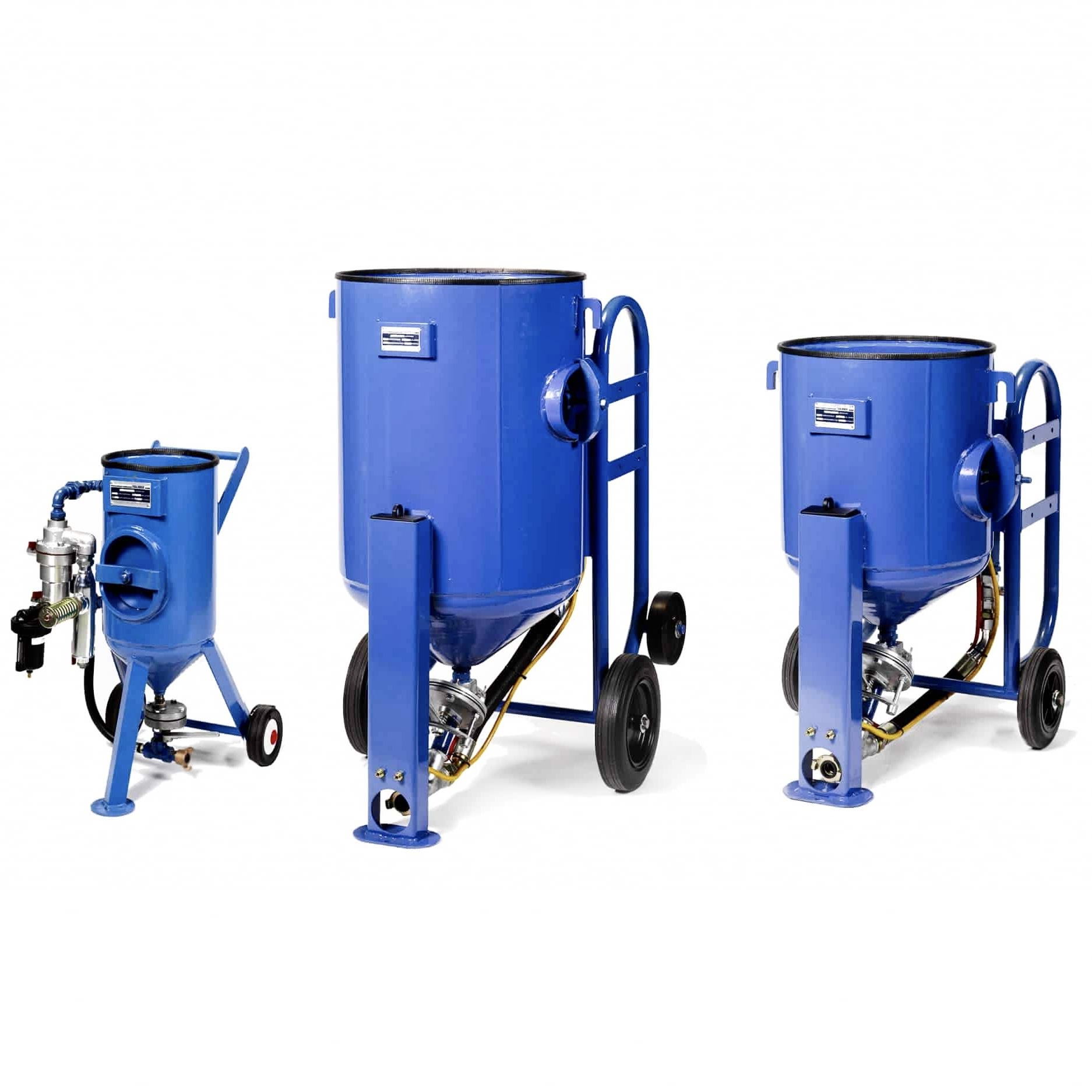
Portable units are highly flexible, suitable for on-site mold repairs. However, they have lower media recovery rates (around 50%) and limited dust control capabilities.
Example: A construction mold manufacturer reduced on-site repair time by 50% using portable equipment.
Synergy Between Equipment and Media
The right equipment can significantly enhance the performance of ceramic blast beads, ensuring optimal mold finishing results.
Optimizing Ceramic Beads Performance
By adjusting equipment parameters such as PSI and blast angle, you can maximize the lifespan and efficiency of ceramic beads. For instance, a customer case study showed that ceramic beads lasted three times longer than glass beads when used at 80 PSI and a 30° blast angle.
Extending Media Life Through Equipment Maintenance
Regular equipment maintenance, such as cleaning and calibrating the dust collection system, can reduce media consumption by up to 15%. This not only lowers costs but also ensures consistent surface finishes.
Choosing the right sandblasting equipment is crucial for achieving perfect mold finishing. By focusing on PSI control, media recovery, and dust collection, you can significantly improve efficiency and reduce costs. Whether you opt for a pneumatic cabinet, wheel blaster, or automated system, each machine type offers unique advantages tailored to specific applications.
If you’re unsure which equipment is best for your needs, contact us for a free consultation and let our experts guide you to the ideal solution.
Stay tuned for our next blog, where we’ll dive deeper into the benefits of ceramic blast beads for mold finishing!
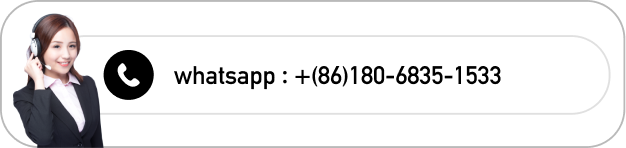