Finition des moules : problèmes courants et solutions pour l'état de surface
17 janvier 2025
L'état de surface est l'un des aspects les plus importants de la finition des moules. Il affecte non seulement la beauté et la fonctionnalité des pièces, mais détermine aussi directement la durée de vie du moule et la qualité du produit. Qu'il s'agisse d'appareils médicaux ou de pièces automobiles, les exigences en matière de surface des moules varient d'une industrie à l'autre. Les matériaux des moules, les tolérances, les textures, les performances de démoulage, les caractéristiques d'écoulement des matériaux et les méthodes de traitement affecteront l'effet final de la finition. Cet article se concentre sur le problème de l'état de surface de la finition des moules, analyse ses causes et fournit des solutions pour aider les fabricants de moules à faire face à des défis de traitement complexes.
Problèmes courants liés à l'état de surface des moules
Rugosité inégale de la surface
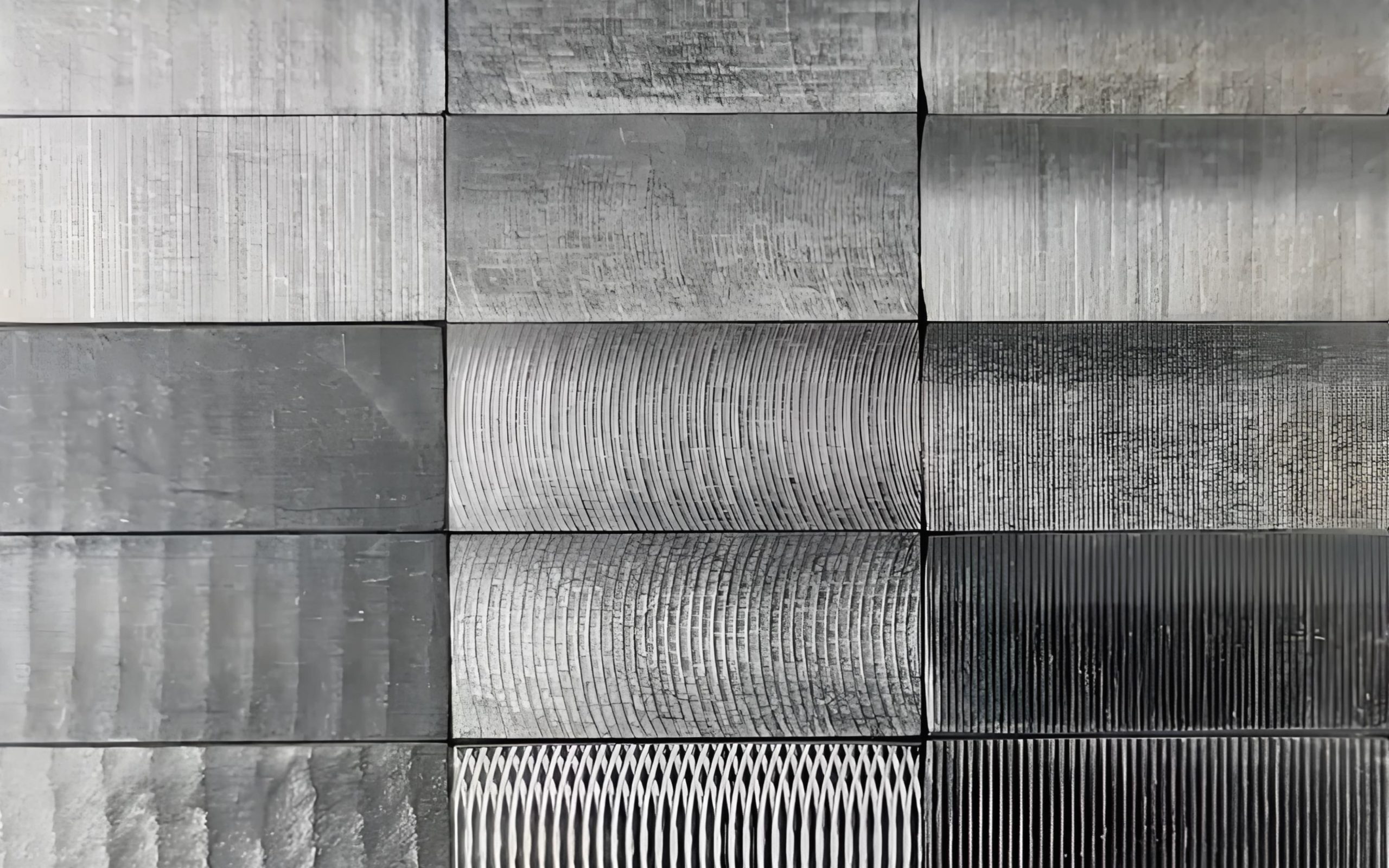
Manifestation du problème
- La rugosité des différentes zones de la surface du moule varie considérablement, ce qui affecte la consistance du produit.
- La zone de haute luminosité et la position des bords sont sujettes à une rugosité excessive.
- D'importantes marques de couteau apparaissent sur la surface après le traitement CNC, ce qui affecte la finition et l'effet visuel.
- La texture de certaines zones est différente en profondeur, ce qui affecte l'effet de polissage ultérieur.
Analyse des causes
- Précision d'usinage insuffisante et absence d'optimisation des zones complexes.
- L'usure de l'outil n'est pas remplacée à temps, ce qui affecte la qualité de la surface.
- Mauvais réglage des paramètres du processus, adaptation déraisonnable de la vitesse d'avance et de la vitesse de rotation, entraînant des différences de texture de la surface.
- Processus de traitement de surface imparfait, sélection incorrecte du médium lors des étapes de polissage et de sablage.
Les défauts de surface entraînent des difficultés de démoulage
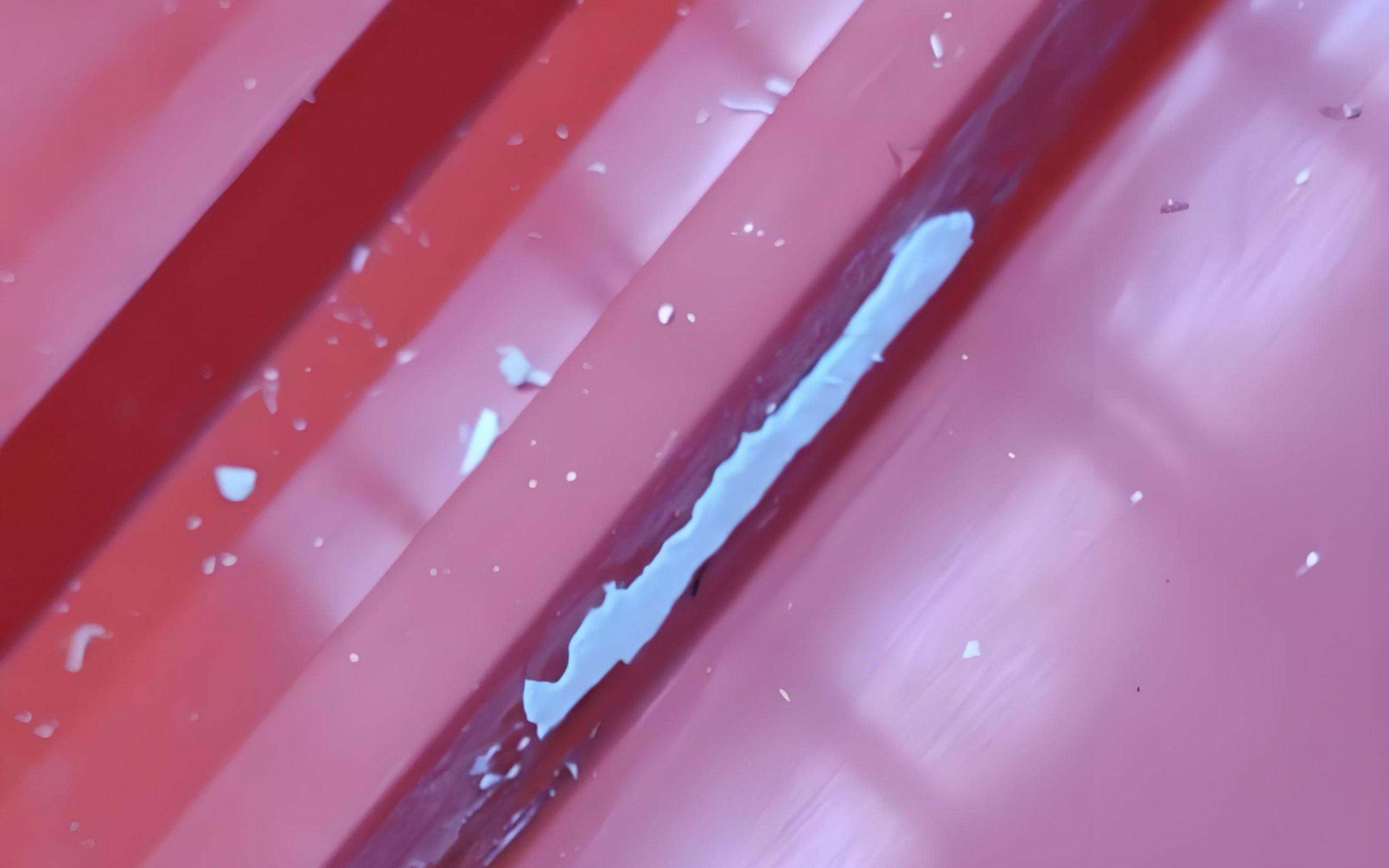
Manifestation du problème
- Le matériau adhère à la surface du moule pendant le démoulage, ce qui nuit à l'efficacité de la production.
- Certains thermoplastiques ou silicones produisent des dessins ou des marques résiduelles après le démoulage.
Analyse des causes
- Une finition insuffisante et une surface rugueuse augmentent l'adhérence des matériaux dans la cavité du moule.
- Conception déraisonnable de l'angle de démoulage et absence de prise en compte des exigences de démoulage de formes géométriques complexes.
- Manque de texture de la surface, en particulier pour les matériaux collants tels que le silicone, une surface lisse peut accroître les difficultés de démoulage.
Fissures superficielles et problèmes de bulles
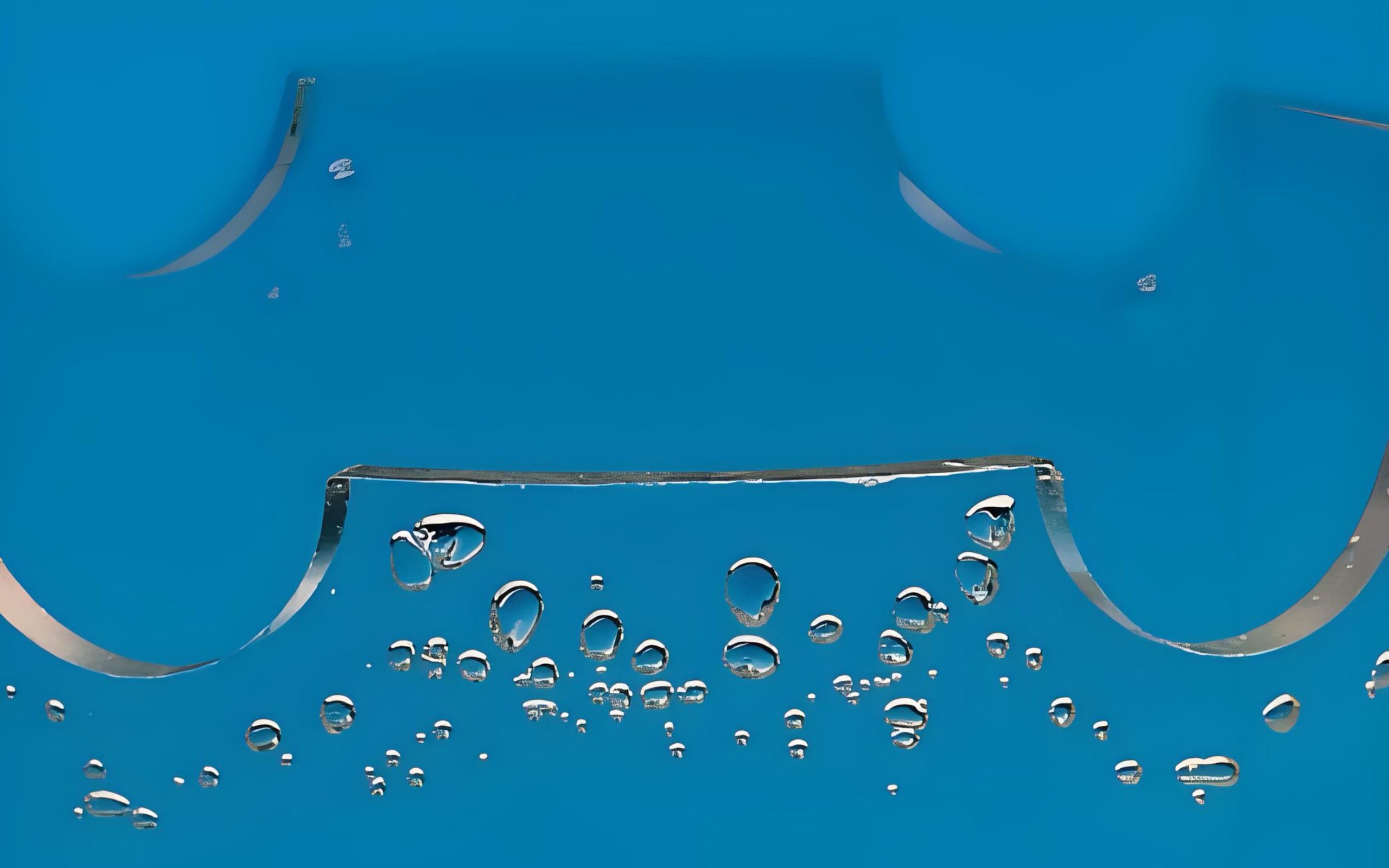
Manifestation du problème
- Des rayures ou des taches argentées apparaissent à la surface de la pièce, affectant son aspect et sa résistance.
- L'extension de la fissure peut entraîner une défaillance de la pièce lors de l'application.
Analyse des causes
- La teneur en eau du matériau de moulage par injection est trop élevée et des bulles se forment pendant le refroidissement.
- La conception de l'évent du moule n'est pas raisonnable, et le gaz ne peut pas être évacué de la cavité du moule en douceur, ce qui entraîne la formation de fissures.
- Pas de traitement efficace de réparation et de renforcement des fissures après le traitement.
Les impuretés de surface affectent les résultats du traitement
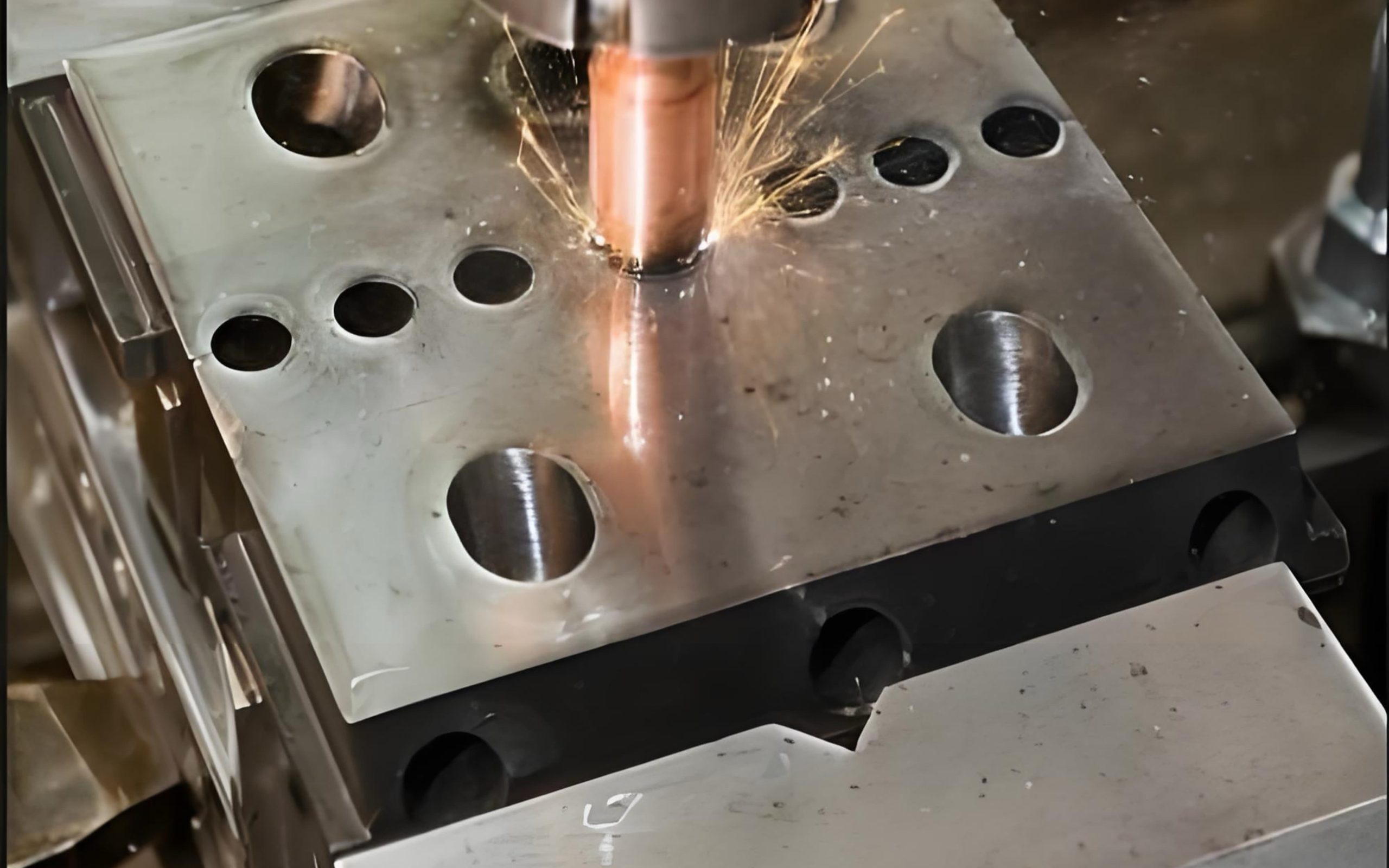
Manifestation du problème
- Des poussières ou des particules restent sur la surface du moule après le sablage ou le polissage.
- Les impuretés affectent l'effet des étapes ultérieures de revêtement ou de traitement.
Analyse des causes
- Des billes de verre ordinaires ou des médias de qualité inférieure sont utilisés, et l'efficacité du nettoyage est faible.
- Des paramètres de sablage inadéquats, un angle ou une pression de pulvérisation non optimisés et des impuretés ne peuvent pas être complètement éliminés.
- Absence d'étapes de nettoyage ultérieures ou processus non normalisés.
Fluidité matérielle insuffisante
Manifestation du problème
- Au cours du processus de moulage par injection, le matériau ne peut pas remplir la cavité du moule, ce qui entraîne un moulage incomplet de la pièce.
- Des problèmes tels qu'une pression de remplissage insuffisante, des marques de matériau froid ou des soudures apparaissent dans le moule.
Analyse des causes
- Une surface trop rugueuse ou trop brillante modifie la trajectoire du matériau et augmente la résistance.
- Défauts de conception des canaux : position et taille de la porte inadéquates, et optimisation insuffisante de l'efficacité du remplissage des matériaux.
- Un refroidissement inégal entraîne une solidification prématurée du matériau.
Solution
Préparation avant transformation
- Prétraitement du matériau pour s'assurer qu'il est complètement sec avant le moulage par injection et contrôler la teneur en humidité.
- Utiliser un logiciel pour optimiser la texture et la conception des canaux d'écoulement afin de garantir l'uniformité de l'écoulement et de la texture.
Optimisation des processus
- Combiné à la technologie d'usinage à cinq axes, il permet d'ajuster l'espacement des trajectoires, de réduire les marques d'outil et d'améliorer l'uniformité de la surface.
- Utiliser la technologie de broyage à grande vitesse pour optimiser le rapport entre l'alimentation et la vitesse et contrôler finement la qualité du traitement.
- Modernisation des équipements, machines-outils CNC de haute précision et technologie de gravure au laser pour améliorer les capacités de traitement des textures complexes et des détails.
- Détection en temps réel de l'usure de l'outil et remplacement en temps voulu pour garantir la stabilité du traitement.
Nettoyage post-traitement et traitement de surface
- Utiliser des billes de sablage en céramique et d'autres médias pour sabler afin d'éliminer les résidus de traitement et d'assurer le lissage.
- Ajoutez un nettoyage par ultrasons ou une purge au gaz pour éliminer complètement les petites impuretés.
- Combiné au polissage miroir ou au sablage pour un traitement de renforcement, il améliore encore la durabilité de la surface et réduit les microfissures.
Démoulage et optimisation ultérieure
- Ajuster la pente du moule, ajouter des textures auxiliaires, optimiser les performances de démoulage et éviter les problèmes d'adhérence.
- Ajouter des revêtements anti-adhérents aux pièces clés pour réduire les coefficients de friction et améliorer l'efficacité du démoulage.
- Utilisez un système de contrôle de la température par zones et optimisez la conception des conduits d'aération pour réduire les problèmes de refroidissement inégal et de bulles d'air.
Vérification et amélioration des processus
- Optimisez les glissières et les portes pour garantir un remplissage complet et uniforme du matériau.
- Test final : Évaluer l'utilisation réelle du moule pour s'assurer que la texture, la finition et la fonctionnalité répondent pleinement aux exigences.
Les médias de sablage permettent d'obtenir une finition de surface
Dans le processus de finition des moules, le sablage est une technologie indispensable qui permet de compenser efficacement les lacunes des autres méthodes de traitement et d'optimiser la qualité de la surface. Le choix du support de sablage est particulièrement important pour résoudre les petites textures de traitement, les résidus d'impuretés et les défauts de surface. Parmi eux, les billes de sablage en céramique sont devenues un choix idéal pour améliorer l'état de surface des moules grâce à leurs excellentes performances. Ses avantages sont les suivants :
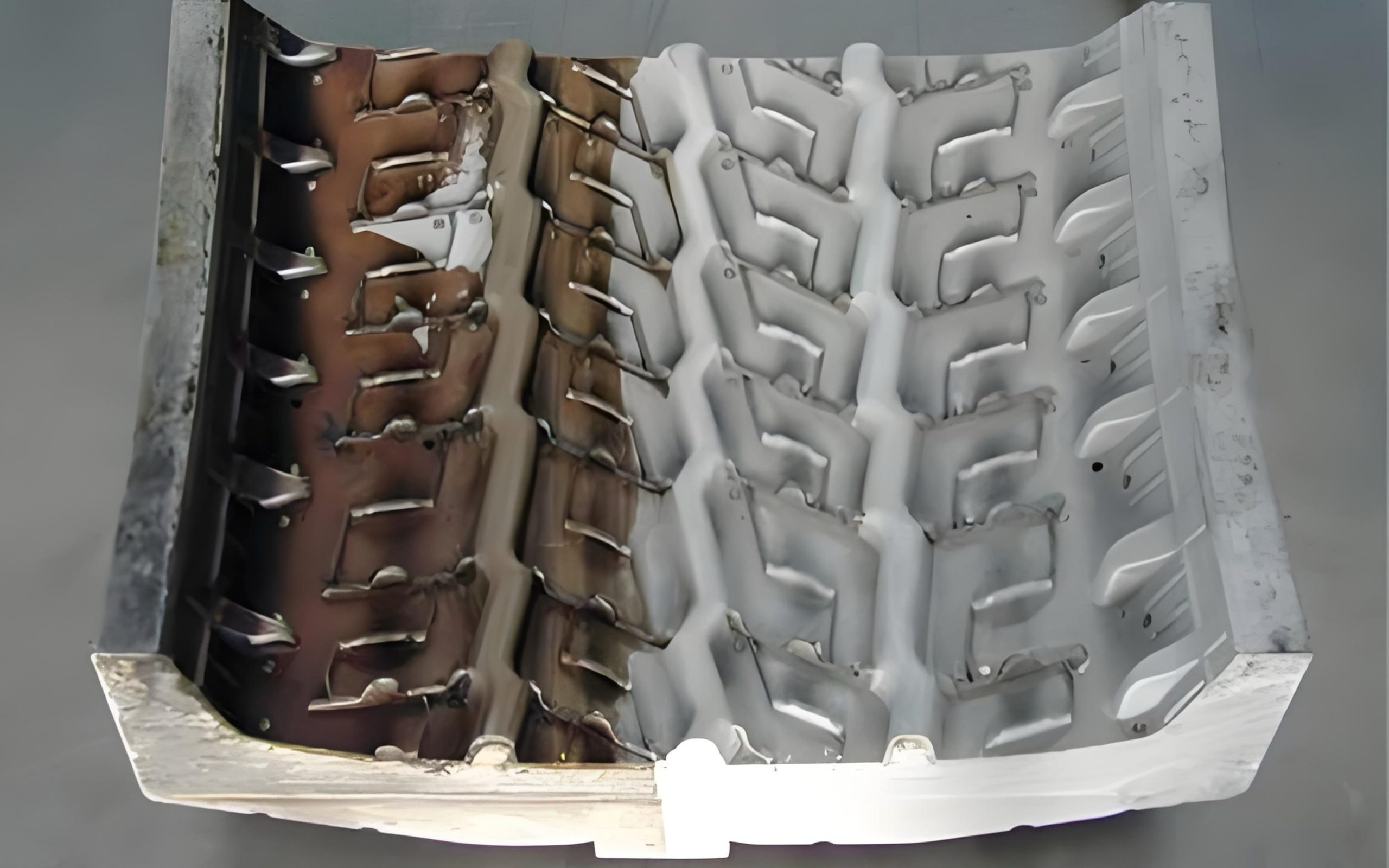
Éliminer les microfissures et les textures de traitement. Les billes de céramique ont une dureté de Mohs élevée et des particules uniformes. Elles peuvent éliminer efficacement les microfissures et les textures laissées par le traitement de l'outil sans endommager la surface du moule, et optimiser la finition.
Améliorer la consistance de la surface. Les médias céramiques ont une distribution de densité uniforme et une taille constante, ce qui permet de couvrir uniformément la surface du moule et d'éviter les problèmes fonctionnels et esthétiques causés par une texture inégale ou une rugosité locale excessive.
Réduire les problèmes d'adhérence. Les billes de céramique ont une bonne surface lisse et peu de poussière, ce qui permet de réduire efficacement le coefficient de frottement de la surface du moule et de limiter les dommages causés par l'adhérence du matériau pendant le processus de démoulage.
Améliorer la durabilité de la pièce. Le sablage peut également renforcer la surface du moule, améliorer sa résistance à la fatigue et à la corrosion, et prolonger la durée de vie du moule.
Optimiser l'environnement de travail. Par rapport aux billes de verre traditionnelles, les billes de sablage en céramique sont moins poussiéreuses, ce qui améliore non seulement la précision du traitement mais réduit également les risques pour la santé.
En combinant les avantages des billes de sablage en céramique, les fabricants de moules peuvent non seulement améliorer considérablement la finition de la surface, mais aussi éviter efficacement les problèmes courants tels que les fissures, les impuretés de surface et les difficultés de démoulage, offrant ainsi aux clients des solutions de moules de haute performance.
Si vous souhaitez obtenir des recommandations plus détaillées sur le processus de sablage et les supports, vous pouvez contactez-nous pour plus d'informations.
Filtres