Cómo mejorar la vida útil de los muelles en la industria del automóvil
9 de septiembre de 2024
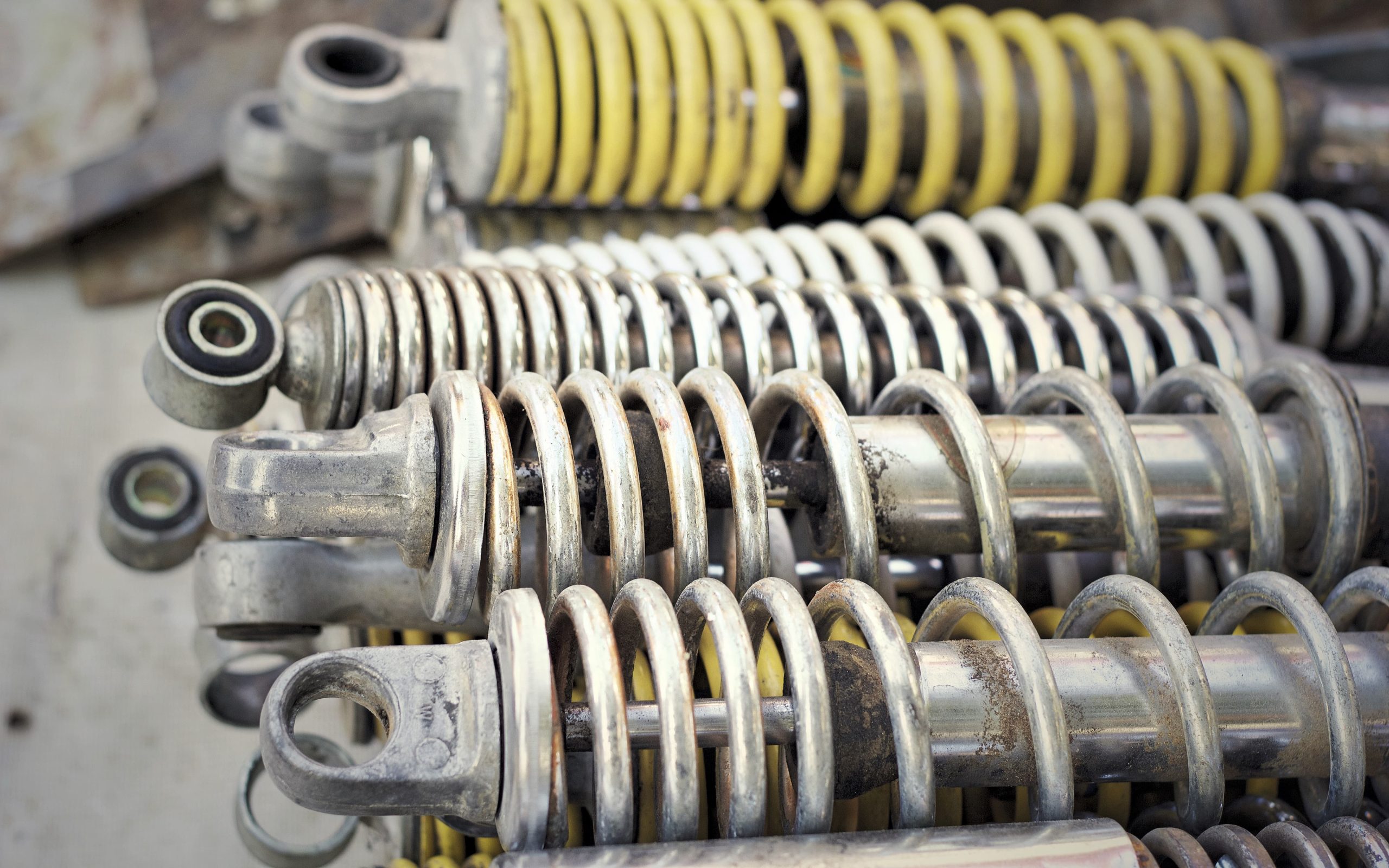
En la fabricación de automóviles, los muelles son uno de los componentes importantes. Desempeñan un papel clave en componentes como los sistemas de suspensión, embragues, cajas de cambio, sistemas de frenado y asientos. Por lo tanto, la vida útil y el rendimiento de los muelles afectarán directamente a la seguridad y el confort del vehículo. Sin embargo, los muelles están sometidos a diversas tensiones durante su uso, como la carga cíclica, los cambios de temperatura y la corrosión, que provocan fatiga y desgaste. Por lo tanto, cómo alargar la vida útil de los muelles se ha convertido en un importante tema de preocupación para los fabricantes de automóviles y los ingenieros de materiales, y la tecnología de shot peening ha entrado así en el campo de visión. Esta tecnología mejora enormemente la resistencia a la fatiga y la durabilidad de los muelles mediante la introducción de tensiones residuales de compresión, y las perlas cerámicas de granallado han superado al resto de materiales de granallado con su rendimiento superior y se han convertido en la opción preferida.
Permítanme presentarles en primer lugar los tipos de muelles más comunes en la industria del automóvil y sus aplicaciones:
- Muelles helicoidales
Los muelles helicoidales se utilizan en los sistemas de suspensión de los automóviles. Al absorber los baches y las vibraciones de la carretera, garantizan una buena estabilidad y confort durante la conducción. Suelen utilizarse junto con amortiguadores y son adecuados para la mayoría de los turismos y camiones ligeros.
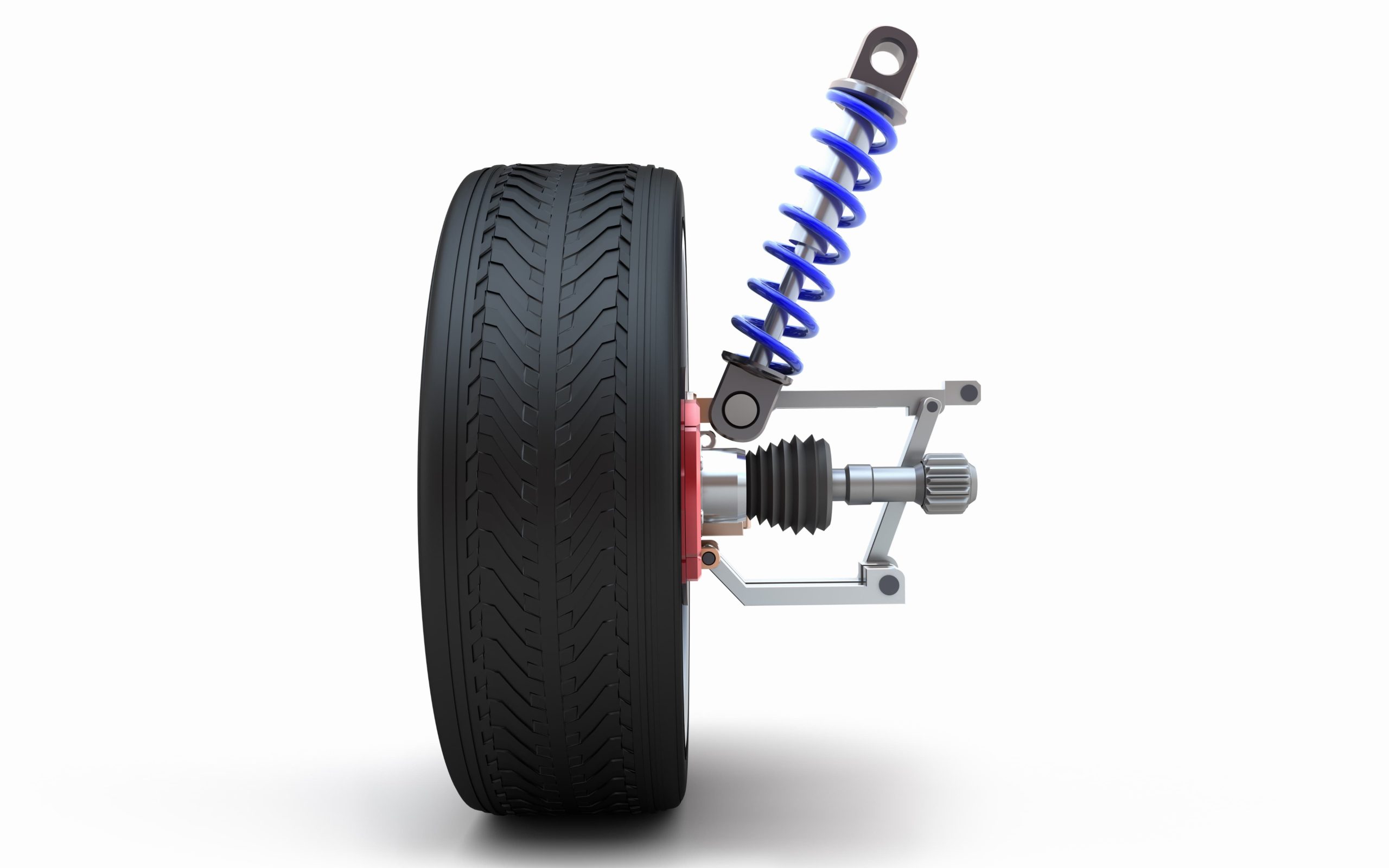
Muelle helicoidal con amortiguador
- Ballestas
Las ballestas de estructura robusta se utilizan principalmente en los sistemas de suspensión trasera de camiones, todoterrenos y vehículos comerciales. Fabricadas con múltiples capas de finas placas de acero, tienen una fuerte capacidad de carga y durabilidad (debe ser) y se suelen utilizar en vehículos pesados.
- Muelle neumático
El muelle neumático utiliza aire comprimido como medio elástico, que puede ajustar la dureza de la suspensión en función de la carga y las condiciones de conducción para proporcionar una experiencia de conducción confortable. Suele utilizarse en los sistemas de suspensión de coches de gama alta y camiones pesados.
- Muelle de barra de torsión
Absorbe y libera energía a través de la barra de torsión para conseguir el efecto de un muelle. Suele utilizarse en los sistemas de suspensión de todoterrenos y camiones. Como tiene que adaptarse a las duras condiciones de la carretera, debe tener una durabilidad extremadamente fuerte.
- Muelle de válvula
Se utiliza en las válvulas de admisión y escape del motor para garantizar que la válvula pueda rebotar rápidamente y permanecer cerrada a altas velocidades. Debe tener una gran resistencia y estabilidad a altas temperaturas para garantizar el funcionamiento normal del motor a altas velocidades.
- Muelle de embrague
Se utiliza para la separación y combinación del embrague para garantizar una transmisión de potencia suave. Debe soportar operaciones frecuentes y entornos de trabajo a alta temperatura para mantener un rendimiento estable.
- Muelle de freno
Aplicado a los sistemas de frenos de tambor, se utiliza para devolver las zapatas de freno a su posición original y garantizar la fiabilidad y seguridad del sistema de frenos.
- Muelles de asiento
Utilizados habitualmente en respaldos y bases de asientos, proporcionan un cómodo apoyo y elasticidad, y reducen la fatiga del conductor tras una conducción prolongada.
- Muelles de airbag de suspensión
Como parte del sistema de suspensión neumática, los muelles neumáticos pueden ajustar automáticamente la dureza de la suspensión en función de las condiciones de la carretera, proporcionando un excelente confort de conducción y control del vehículo, especialmente cuando se sobrecarga o se recorren largas distancias. Por eso se suelen utilizar en coches de lujo, todoterrenos y camiones.
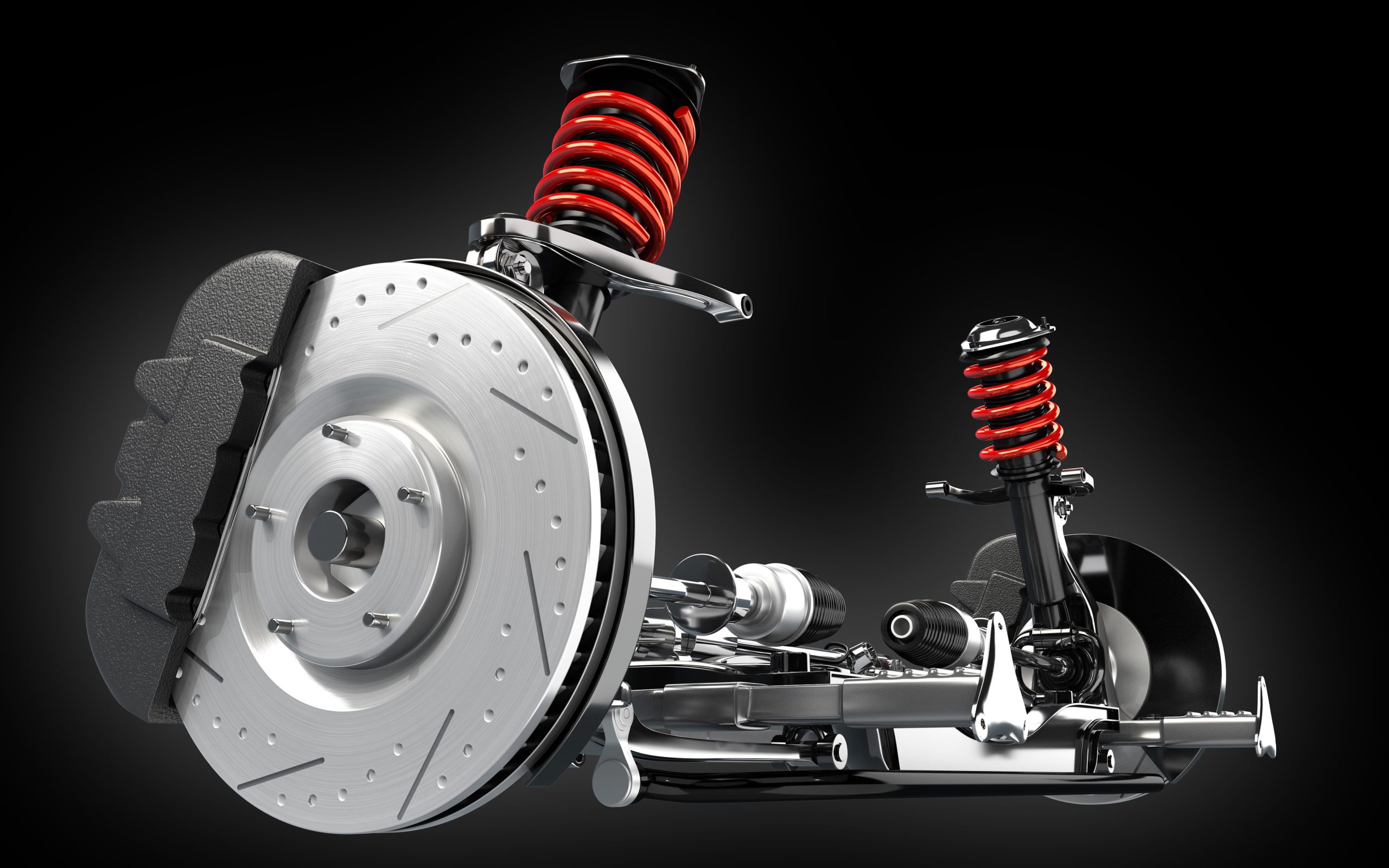
Muelle de suspensión del automóvil
En resumen, tenemos un conocimiento general de los tipos y funciones de estos muelles. Se utilizan ampliamente en la industria del automóvil para satisfacer las necesidades de los distintos sistemas y aplicaciones de los vehículos. Su importancia es evidente. Sin embargo, debido a la relajación de tensiones, los muelles sufrirán pequeñas deformaciones permanentes cuando trabajen bajo fuerzas externas durante mucho tiempo, especialmente en el caso de los muelles que trabajan a altas temperaturas, donde la relajación de tensiones será más grave. Además, no se pueden ignorar los defectos superficiales como arañazos, pliegues, oxidación y descarburación. Son riesgos potenciales. Por lo tanto, la tecnología de shot peening es necesaria para mejorar la calidad de la superficie y la resistencia superficial de los muelles, de modo que la superficie se encuentre en un estado de tensión de compresión, lo que puede mejorar eficazmente la resistencia a la fatiga y la vida útil de los muelles.
En la tecnología del shot peening, ¿por qué elegir bolas de cerámica como medio? ¿Cuáles son sus ventajas frente a los medios tradicionales de granallado con bolas de acero? A continuación responderemos a sus preguntas a través de cuatro partes: daño superficial tras el tratamiento, efecto de la tensión residual, efecto de la rugosidad y comparación de la vida a fatiga:
Daños superficiales tras el tratamiento
Las bolas cerámicas de peening tienen una mayor dureza y pueden eliminar más eficazmente las impurezas y microfisuras de la superficie, pero al mismo tiempo pueden reducir los daños superficiales. Sin embargo, la fuerza de impacto de las bolas de acero es demasiado grande, lo que puede dejar fácilmente grandes picaduras en la superficie, causando daños superficiales. Además, la mayor velocidad de desgaste de las bolas de acero también puede causar contaminación y afectar a la calidad de la superficie.
Según las investigaciones de Toyota, cuando se utilizan bolas cerámicas de peening para tratar piezas de motor, el daño superficial es significativamente menor que el de las bolas de acero. Esta diferencia mejora la calidad general de las piezas y reduce la necesidad de tratamiento posterior.
Efecto de la tensión residual
La elevada dureza (superior a la de las bolas de vidrio y algunas bolas de acero) y la baja resistencia al desgaste de las bolas cerámicas de granallado les permiten producir una capa de tensión residual de compresión más profunda y uniforme durante el proceso de granallado, mejorando eficazmente la resistencia a la fatiga del muelle. Sin embargo, las bolas de acero pueden producir grandes concentraciones locales de tensión durante el proceso de granallado. Especialmente cuando se trata de materiales de alta resistencia, esta distribución desigual de las tensiones puede provocar el fallo prematuro del material.
El análisis de difracción de rayos X muestra que la tensión residual superficial de la granalla cerámica Z210 es superior a la de la granalla de acero S230. La tensión superficial media del muelle granallado con granalla Z210 es de aproximadamente -600~-650 MPa, mientras que la tensión superficial normal del granallado con granalla de acero es de -400 MPa, que es 50% superior. Ajustando la intensidad del shot peening, se puede ajustar el efecto del shot peening sobre la profundidad. Podemos concluir que la tensión residual superficial y la tensión máxima en profundidad son muy importantes a la hora de considerar el comportamiento a fatiga de los muelles. 1
Según la prueba publicada por BMW, cuando los muelles de suspensión se tratan con perlas cerámicas de granallado, la distribución de la tensión residual es más uniforme y la resistencia a la fatiga del material mejora notablemente.
Efecto de rugosidad
En el proceso de prolongación de la vida útil del muelle, la rugosidad de la superficie es un factor importante que afecta al crecimiento de las grietas de fatiga. Dado que la superficie de las bolas cerámicas es relativamente lisa, la rugosidad superficial de las piezas tratadas es baja, lo que resulta adecuado para aplicaciones que requieren un tratamiento superficial de precisión, como la fabricación de otras piezas de alta precisión, como los muelles de las válvulas de los motores. Sin embargo, las bolas de acero pueden provocar grandes cambios de rugosidad superficial durante el shot peening debido a su fuerza de impacto y dureza, especialmente cuando se trata de superficies irregulares, lo que puede afectar a la calidad del producto final.
Generalmente, la rugosidad superficial (valor Ra) tras el tratamiento de granallado cerámico se sitúa entre 0,2-0,4 μm, mientras que la rugosidad superficial tras el tratamiento de granallado de acero puede alcanzar 0,8 μm o más.
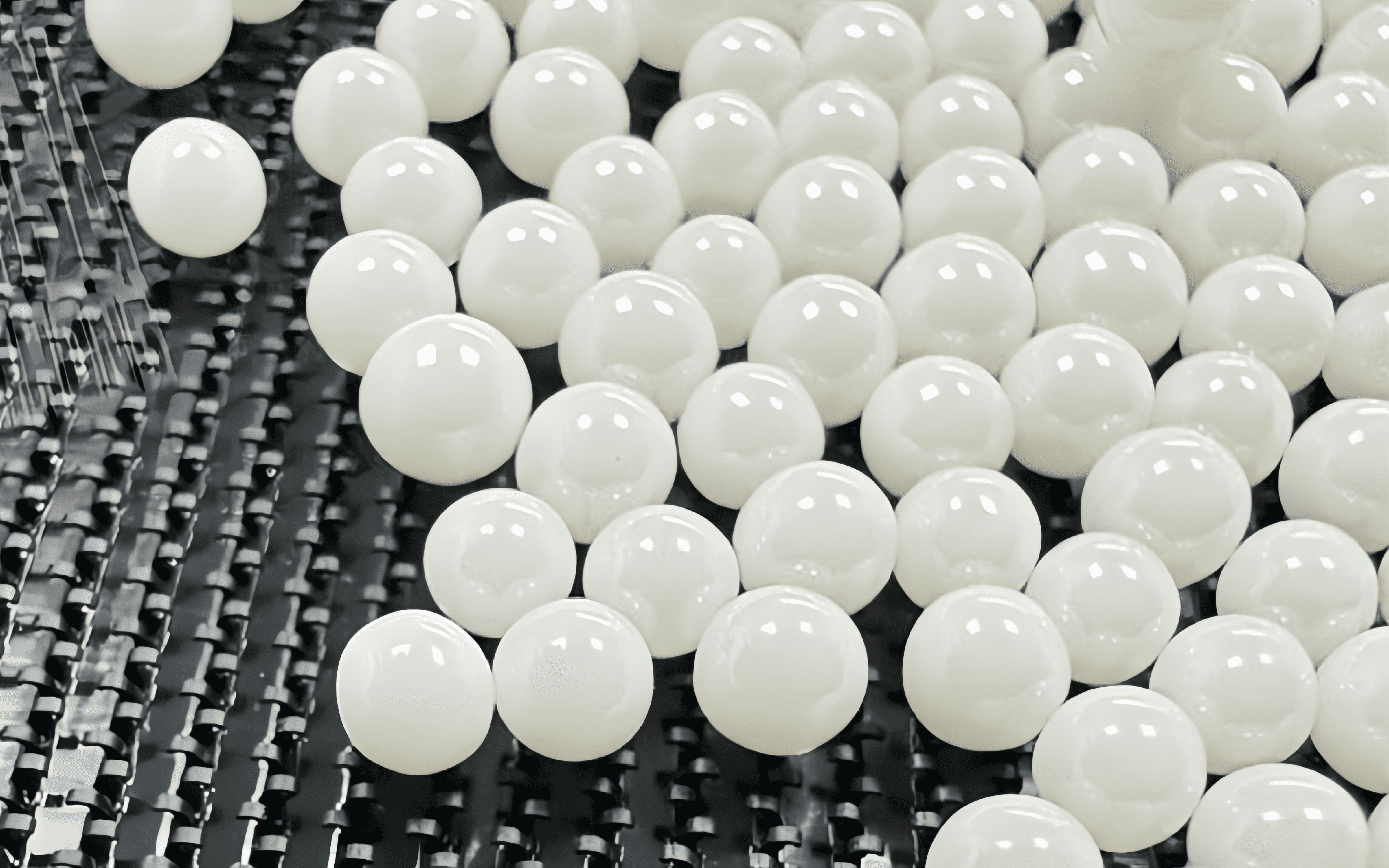
Perlas de cerámica lisas y redondas
Comparación de la vida útil a la fatiga
Los muelles tratados con microesferas cerámicas tienen una menor rugosidad superficial y una menor probabilidad de agrietamiento. Además, la tensión residual de compresión introducida por las perlas cerámicas puede compensar eficazmente la tensión de tracción durante el funcionamiento y evitar la propagación de grietas, mejorando así significativamente la vida a fatiga del muelle. Por el contrario, tras el tratamiento con bolas de acero, la rugosidad de la superficie es mayor. Aunque hay una capa de tensión residual de compresión más profunda, es fácil que se formen puntos de concentración de tensiones en la superficie, lo que afecta al rendimiento a fatiga.
Los datos de las pruebas de Toyota muestran que la vida a fatiga de los muelles de suspensión tratados con bolas cerámicas de granallado aumentó unos 30%, mientras que los resultados del tratamiento con bolas de acero no consiguieron el mismo efecto.
Con el fin de mejorar la durabilidad de los muelles de sus modelos de alto rendimiento, un conocido fabricante de automóviles europeo decidió utilizar perlas de granallado cerámico para tratar los muelles. Tras las pruebas de fatiga estándar, los muelles sin tratar se agrietaban después de unos 50.000 ciclos, pero tras el tratamiento con perlas cerámicas de granallado, la vida a fatiga de los muelles aumentó hasta unos 80.000 ciclos, un incremento de 60%. Esta mejora aumenta significativamente la fiabilidad y la seguridad del vehículo, al tiempo que reduce los costes de mantenimiento, demostrando con éxito la eficacia de las microesferas cerámicas de granallado para mejorar la vida a fatiga de los muelles. 2
En Estados Unidos, un proveedor de piezas de automoción también ha implantado un programa similar de tratamiento de cordones por granallado cerámico. El proveedor se dedica a suministrar componentes de muelles de alto rendimiento a varios fabricantes de automóviles. Para optimizar la durabilidad de los muelles, la empresa utiliza microesferas cerámicas de granallado con un tamaño de 150 micras (0,15 mm) para el tratamiento. Según las estadísticas, la vida media a fatiga de los muelles no tratados en pruebas de carga estándar es de 40.000 ciclos. En cambio, tras el tratamiento con perlas cerámicas de peening, la vida a fatiga de los muelles aumentó a 65.000 ciclos, un incremento de 62,5%. Además, este proceso también ayuda a que los muelles mantengan un buen rendimiento en entornos de alta tensión, mejorando así la competitividad del producto final en el mercado. 3
En un fabricante de automóviles asiático, la aplicación de perlas cerámicas de peening también ha dado excelentes resultados. La empresa introdujo perlas cerámicas de granallado con distintos tamaños de partícula para satisfacer los requisitos de procesamiento de distintos tipos de muelles. Tras las pruebas, los muelles empezaron a mostrar grietas de fatiga en 100.000 pruebas de carga sin granallado. Tras el tratamiento con perlas cerámicas de granallado, la vida a fatiga de los muelles aumentó a 150.000 ciclos, un incremento de 50%. La introducción de esta tecnología no sólo prolongó la vida útil de los muelles, sino que también mejoró el rendimiento del producto en general, lo que proporcionó a la empresa una ventaja significativa en el mercado. 4
A través de los casos anteriores, podemos ver el efecto significativo de las microesferas cerámicas de granallado en varios aspectos, especialmente en la mejora de la vida a fatiga de los muelles. Estas aplicaciones de éxito demuestran el gran potencial de las microesferas cerámicas de granallado para mejorar el rendimiento y la durabilidad de los muelles de automoción, pero hay que tener en cuenta que el tamaño de los muelles utilizados en la industria del automóvil no es constante. Los distintos tipos de muelles presentan diferencias significativas en cuanto a forma, tamaño, finalidad y material. Su diseño se basa en diferentes requisitos de carga, funciones y limitaciones de espacio de instalación. Por lo tanto, el tamaño requerido para el shot peening también variará en función del tamaño específico del muelle, el material y el efecto de mejora de la superficie requerido.
- Muelles helicoidales
El diámetro, la longitud y el número de espiras de los muelles helicoidales dependen de los requisitos del sistema de suspensión y suelen ser mayores, con diámetros que oscilan entre unos pocos milímetros y varios centímetros. Por lo tanto, el tamaño de granalla requerido suele ser de 0,3-1,2 mm de granalla cerámica. Esto depende del grosor del muelle y de la dureza objetivo. Las granallas más grandes se utilizan para mejorar la dureza superficial, mientras que las más pequeñas son adecuadas para un tratamiento superficial más fino.
- Ballestas
Los muelles de ballesta suelen ser tiras largas de placas de acero multicapa de mayor tamaño y se suelen utilizar en vehículos pesados. Por lo general, se seleccionan disparos de 0,5-1,5 mm. Dado que los muelles de ballesta son más gruesos y requieren fuerzas de impacto más fuertes, se pueden utilizar disparos más grandes para mejorar la resistencia a la fatiga del muelle.
- Amortiguadores de aire
Los muelles neumáticos están compuestos principalmente de caucho y acero y son más grandes en su conjunto, pero no siempre es necesario el shot peening porque su núcleo está hecho de material de caucho. Si se trata de granallar piezas de acero, pueden utilizarse disparos de 0,4-0,8 mm para garantizar el refuerzo de la superficie de las piezas de acero.
- Muelles de barra de torsión
Los muelles de barra de torsión son barras rectas con longitudes y diámetros variables. Suelen ser más finos que los muelles helicoidales. Se suelen seleccionar tiros de 0,4-1,0 mm. Dependiendo del diámetro de la barra de torsión, las barras de torsión más pequeñas pueden utilizar disparos más finos, mientras que las barras de torsión más grandes requieren disparos más grandes para el tratamiento superficial.
- Muelles de válvula
Los muelles de válvula son de menor tamaño, con diámetros que suelen oscilar entre unos pocos milímetros y unos pocos centímetros. Dado que los muelles de válvula son delicados y tienen elevados requisitos de acabado superficial, se suelen utilizar granallas más pequeñas para reforzar la superficie. Las granallas de 0,2-0,6 mm son las más adecuadas.
- Muelles de embrague
Los muelles de embrague suelen ser de tamaño medio y diámetro pequeño, pero su longitud y forma pueden variar. Dado que los muelles de embrague trabajan en un entorno de alta tensión, el objetivo del shot peening es mejorar su resistencia a la fatiga, por lo que se seleccionan granallas de tamaño medio de 0,3-0,8 mm.
- Muelles de freno
Los muelles de freno son más pequeños, normalmente de unos pocos milímetros a un centímetro de diámetro. El shot peening de menor tamaño se utiliza para muelles de freno pequeños de precisión a fin de mantener su precisión y la calidad de su superficie, el shot peening de 0,1-0,4 mm es el mejor.
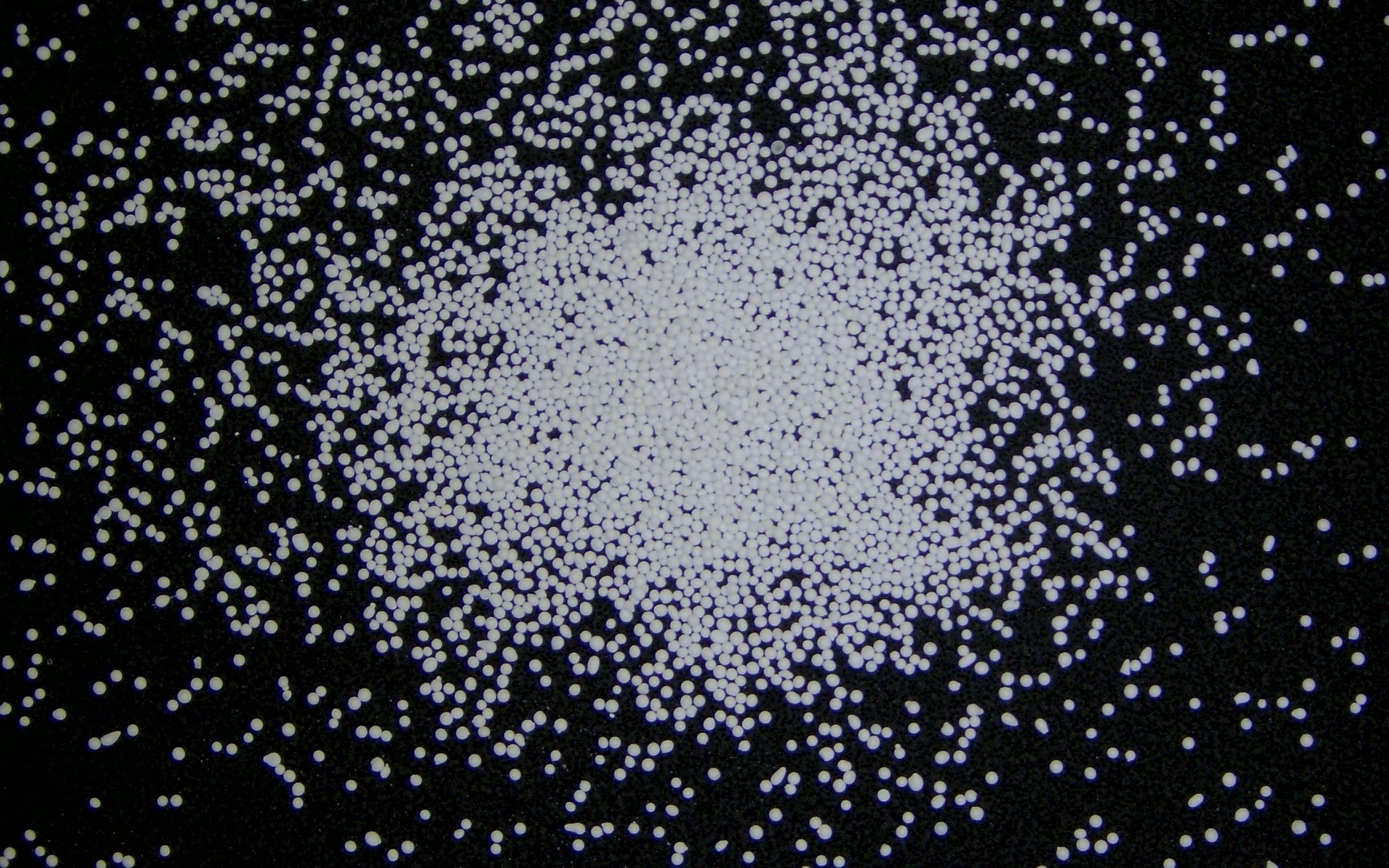
Granallado de piezas de precisión
- Muelles de asiento
Los muelles de asiento suelen ser delgados y de pequeño diámetro, similares a los muelles de válvula. Para mejorar la durabilidad y la resistencia a la fatiga de los muelles, utilice granallado de 0,2-0,5 mm.
- Muelles de airbag de suspensión
Los muelles de airbag de suspensión tienen componentes de acero más grandes y suelen ser de varios tamaños. Dependiendo del tamaño de las piezas de acero de la suspensión, elija un granallado más grande de 0,5-1,0 mm para reforzar la superficie y prolongar su vida útil.
En resumen, dado que los distintos tipos de muelles tienen diferentes requisitos de diseño y entornos de uso, es crucial elegir el tamaño de cordón de granallado adecuado. Tanto si se trata de un muelle helicoidal, un muelle de ballesta o un muelle de válvula más pequeño, el shot peening para los requisitos especiales de los diferentes muelles puede lograr el mejor efecto de refuerzo de la superficie. Puede elegir el shot peening específico para su muelle de acuerdo con la tabla de tamaños de nuestros productosTambién podemos personalizar el tamaño según sus necesidades.
Cuando exploramos cómo mejorar la vida útil de los muelles en la industria del automóvil, no sólo hablamos de mejoras técnicas, sino que también nos centramos en cómo aportar una mejor experiencia de conducción a través de la innovación tecnológica. Como "héroe invisible" del automóvil, el muelle soporta en silencio los retos del vehículo en diversas condiciones de trabajo. La introducción de la tecnología de granallado cerámico es precisamente para hacer que estos "héroes invisibles" sean más duraderos y fiables. Desde los muelles helicoidales hasta los muelles neumáticos, la optimización de cada muelle se traduce en un menor mantenimiento, una mayor vida útil y una mayor seguridad. Cuando sepa que los muelles de su coche han sido sometidos al tratamiento más avanzado y pueden resistir diversos retos, su confianza y sensación de seguridad aumentarán considerablemente. Esta mejora de la experiencia de conducción y la sensación de seguridad son los objetivos últimos que persigue cualquier innovación tecnológica.
La aplicación generalizada de la tecnología de granallado cerámico nos permite ver cómo una tecnología ha pasado de la sombra al primer plano y se ha convertido en la clave para mejorar la calidad del producto y la experiencia del usuario. No sólo promueve el desarrollo de la industria automovilística, sino que también demuestra cómo la tecnología puede desempeñar un papel importante en lugares sutiles. En el futuro, con la innovación continua y la aplicación de más tecnologías, podemos esperar que la industria del automóvil aporte más avances y cambios sorprendentes.
Referencias
- APLICACIÓN DE GRANALLA CERÁMICA PARA EL GRANALLADO DE MUELLES HELICOIDALES DE SUSPENSIÓN DE AUTOMÓVILES
- Estudio de caso: Granallado cerámico en muelles de automoción - Fabricante europeo
- Proveedor estadounidense de automoción: Mejora del rendimiento con granallado cerámico
- Fabricante asiático de automóviles: Innovaciones en Shot Peening
Filtros