Cómo elegir el mejor equipo de chorro de arena para el acabado de moldes
6 de febrero de 2025
El acabado de moldes es un proceso crítico que repercute directamente en la calidad de los productos finales. Según el informe Global Mold Surface Treatment Market (Grand View Research, 2023), Una preparación inadecuada de la superficie puede provocar una tasa de defectos de 15%-20%.
En la India, donde el sector manufacturero está en rápida expansión, muchos fabricantes de moldes se enfrentan a problemas con los equipos tradicionales de chorro de arena, como el exceso de polvo, el elevado consumo de medios y los frecuentes problemas de mantenimiento.
Esta guía le ayudará a comprender los factores clave que hay que tener en cuenta a la hora de seleccionar el equipo de chorreado para el acabado de moldes, comparar cinco tipos de máquinas populares y explorar cómo los equipos avanzados pueden optimizar el rendimiento de los granalladores cerámicos.
Desafíos comunes de los equipos de chorreado tradicionales
Problemas de polvo
Uno de los retos más críticos a los que se enfrentan los fabricantes de moldes de la India es el exceso de emisiones de polvo que generan los equipos tradicionales de chorro de arena. Esto provoca graves problemas medioambientales, malas condiciones de trabajo y mayores riesgos para la salud de los operarios.
Según los comentarios del sector, las concentraciones de polvo en los procesos tradicionales de chorro de arena pueden alcanzar los 200-300 mg/m³, superando con creces el límite de 50 mg/m³ establecido por la Junta Central de Control de la Contaminación (CPCB) de la India.
Consumo de abrasivo
Otra gran desventaja de los equipos de chorreado tradicionales es la elevada tasa de consumo de abrasivo. Por ejemplo, cuando se utilizan microesferas de vidrio, la tasa de pérdida de abrasivo puede llegar a ser de 40-50%, lo que obliga a rellenarlas con frecuencia y aumenta los costes de explotación.
En cambio, los abrasivos cerámicos avanzados pueden reducir el consumo de abrasivos a menos de 10%, lo que mejora significativamente la rentabilidad.
Costes de mantenimiento de los equipos
Los informes demuestran que estos equipos tienen una tasa de averías 30% más alta debido a la obstrucción relacionada con el polvo y al desgaste de los componentes. Como resultado, las empresas tienen que pagar $5.000 más en costes de mantenimiento cada año, lo que afecta aún más a la rentabilidad.
Estos retos ponen de manifiesto la urgente necesidad de soluciones de chorreado más eficientes y respetuosas con el medio ambiente en el mercado industrial indio. Los fabricantes que deseen mejorar sus operaciones deberían plantearse invertir en equipos de chorreado modernos que minimicen las emisiones de polvo y reduzcan el consumo de abrasivo.
3 Métricas básicas para equipos de acabado de moldes
A la hora de elegir un equipo de chorreado de arena, hay tres parámetros fundamentales que determinan su eficacia: El control del PSI, la tasa de recuperación del material y la eficacia de la captación de polvo.
Sistema de control PSI
El acabado de precisión de moldes requiere rangos de PSI ajustables (normalmente de 50 a 120 PSI). Los equipos tradicionales suelen funcionar a una PSI fija (por ejemplo, 80 PSI), lo que da lugar a un tratamiento desigual de la superficie. Por ejemplo, un fabricante indio de moldes para automóviles informó de una mejora de 50% en el acabado superficial (el valor Ra se redujo de 1,2µm a 0,6µm) tras cambiar a un equipo con control preciso de PSI.
Sistema de reciclaje de abrasivos
La tasa de recuperación de abrasivo repercute directamente en los costes operativos. Los equipos tradicionales recuperan sólo 60%-70% del abrasivo, mientras que los sistemas avanzados consiguen recuperar más de 90%. Esto reduce el consumo de abrasivo en hasta 30%, lo que lo convierte en una solución rentable para un uso a largo plazo.
Unidad de recogida de polvo
Las soluciones de chorreado con bajo nivel de polvo son esenciales tanto para la seguridad de los trabajadores como para el cumplimiento de la normativa medioambiental. Los sistemas de captación de polvo de alto rendimiento pueden reducir las emisiones de polvo por debajo de 20 mg/m³, significativamente menos que los 200-300 mg/m³ típicos de los equipos tradicionales. Un fabricante indio de moldes electrónicos observó una reducción de 50% en las quejas sobre la salud de los trabajadores tras la actualización a un sistema de bajo nivel de polvo.
Comparación de 5 Tipos de arenadoras
A continuación se ofrece una comparación detallada de los cinco tipos de arenadoras más populares, destacando sus puntos fuertes y débiles y su idoneidad para aplicaciones de acabado de moldes.
Cabina de chorreado neumático
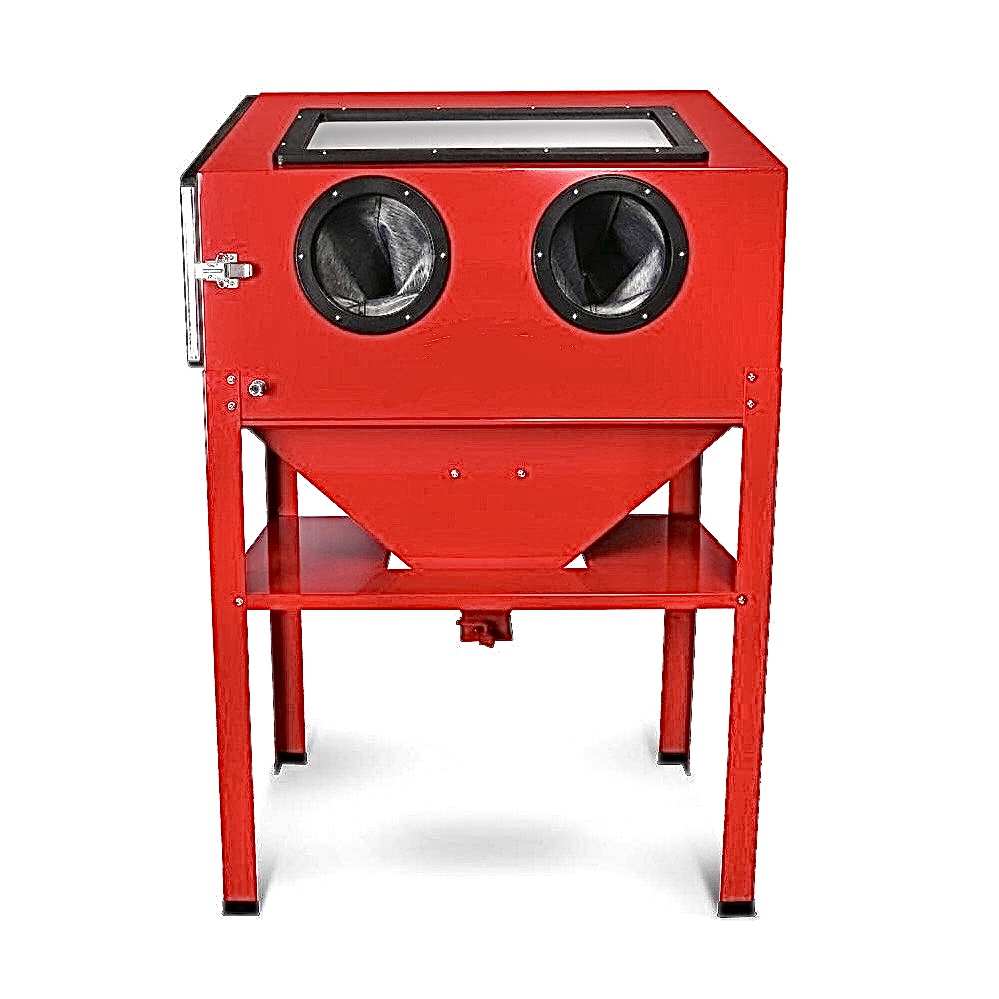
Ideales para operaciones a pequeña escala, las cabinas neumáticas ofrecen un control flexible de PSI (50-120 PSI) y son rentables. Sin embargo, su tasa de recuperación de medios es relativamente baja (en torno a 65%) y el control del polvo es moderado.
Ejemplo: Un fabricante indio de moldes de plástico redujo el consumo de medios en 20% utilizando una cabina neumática con un sistema de captación de polvo mejorado.
Granalladora en húmedo
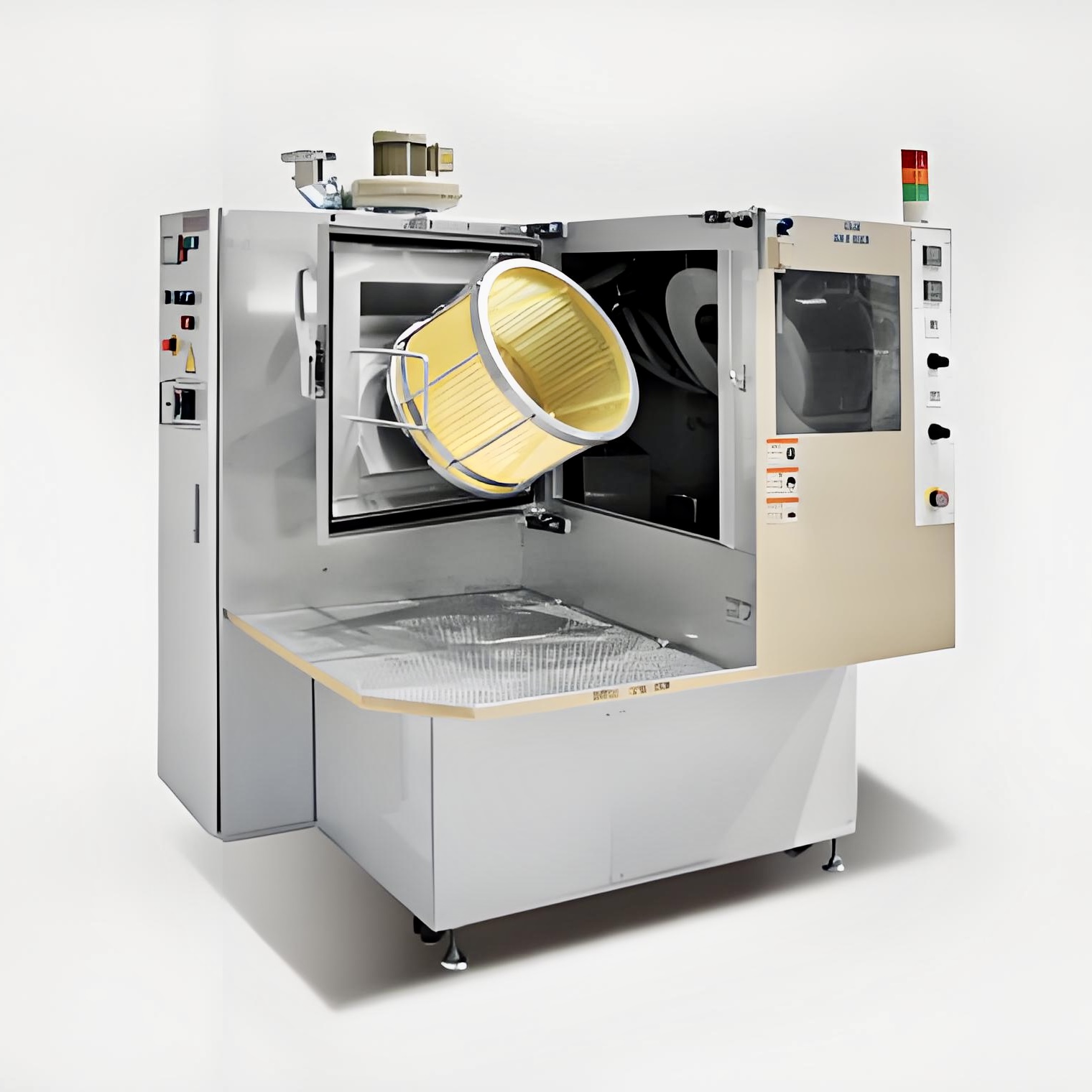
El chorreado húmedo es perfecto para moldes delicados, ya que ofrece emisiones de polvo casi nulas y acabados superficiales excepcionales. Sin embargo, los índices de recuperación de material son más bajos (en torno a 60%) y el mantenimiento puede ser complejo.
Ejemplo: Un fabricante de moldes médicos consiguió valores de Ra constantes por debajo de 0,4 µm utilizando granallado húmedo para componentes de alta precisión.
Sistema de chorreado robotizado automatizado
Los sistemas robotizados proporcionan una consistencia y un control del polvo inigualables, lo que los hace ideales para moldes complejos. Aunque el coste inicial es elevado, reducen considerablemente los gastos de mano de obra.
Ejemplo: Un fabricante de moldes de automoción redujo los costes de mano de obra en 30% y mejoró la uniformidad del acabado con un sistema automatizado.
Granalladora de ruedas
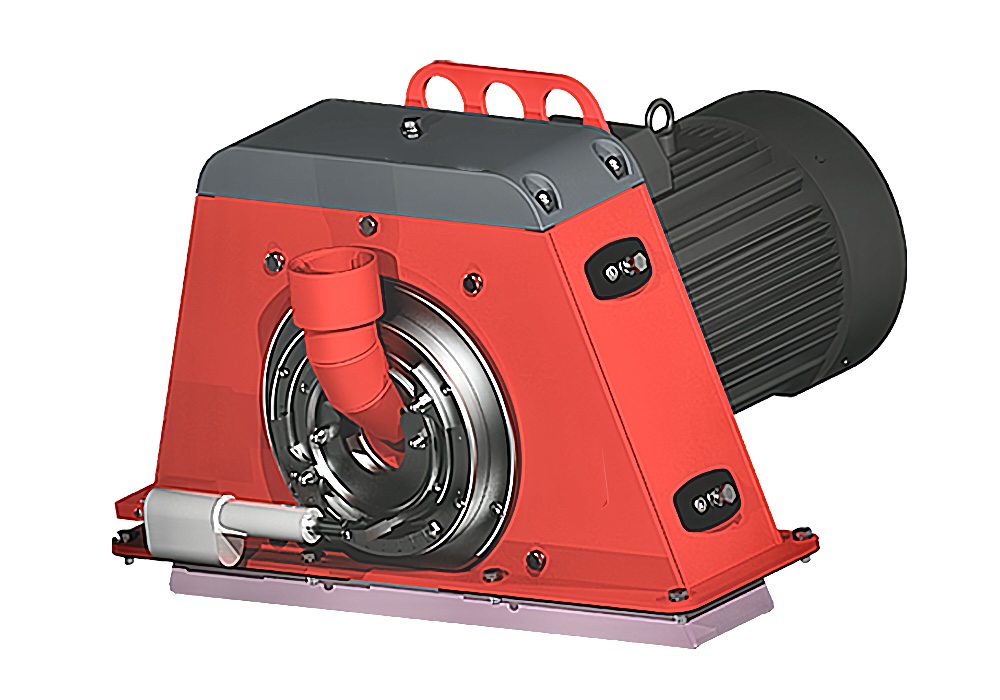
Diseñadas para procesar grandes volúmenes, las granalladoras de turbina destacan en la recuperación de material (hasta 85%) y son muy eficaces para moldes grandes. Sin embargo, su rango de PSI es limitado (80-100 PSI) y la inversión inicial es mayor.
Ejemplo: Un fabricante de moldes de fundición a presión aumentó su productividad en 40% tras adoptar un sistema de granallado por turbina.
Equipos portátiles de voladura
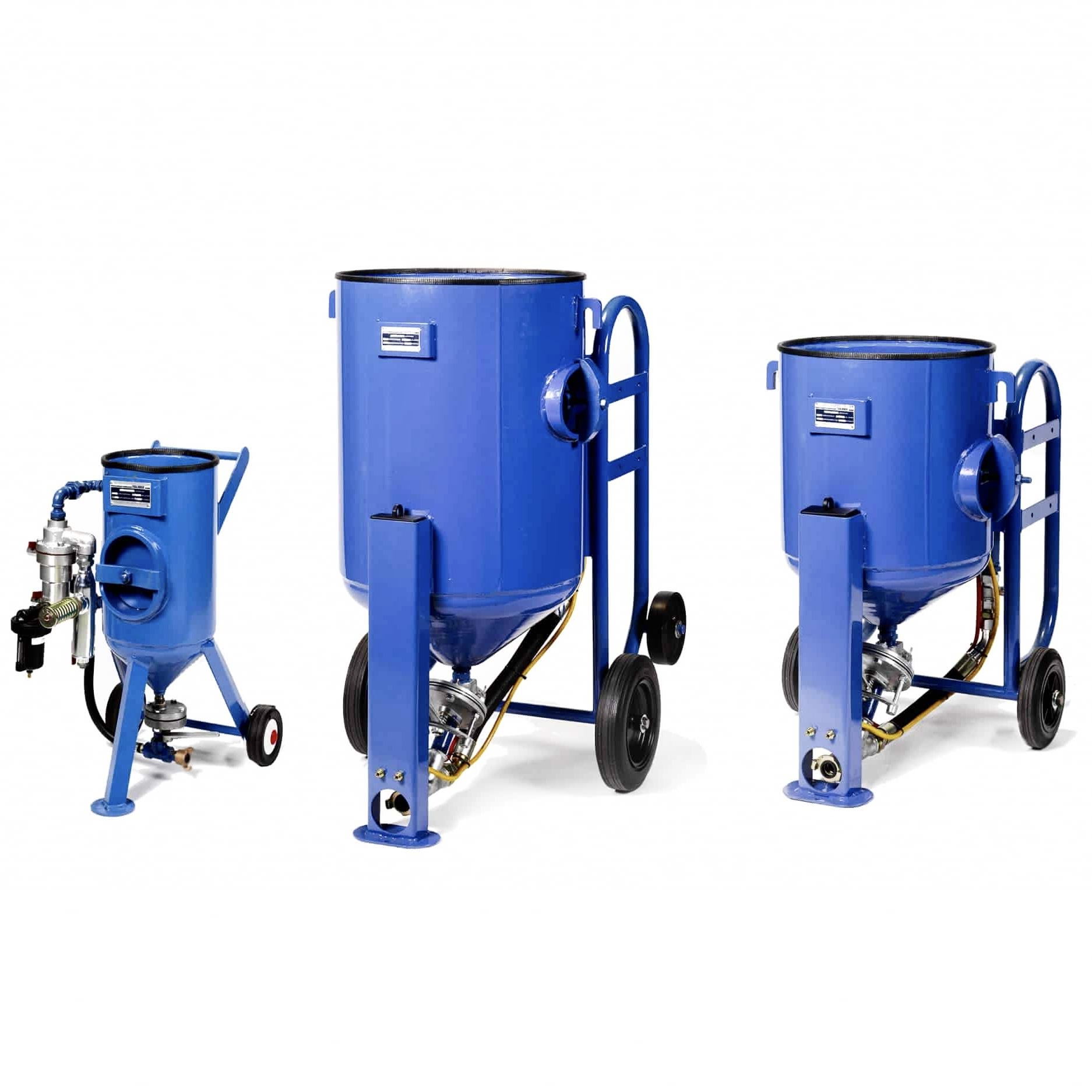
Las unidades portátiles son muy flexibles y adecuadas para las reparaciones de moldes in situ. Sin embargo, tienen menores tasas de recuperación de medios (alrededor de 50%) y capacidades limitadas de control de polvo.
Ejemplo: Un fabricante de moldes de construcción redujo el tiempo de reparación in situ en 50% utilizando equipos portátiles.
Sinergia entre equipos y medios
El equipo adecuado puede mejorar significativamente el rendimiento de las granallas cerámicas, garantizando unos resultados óptimos en el acabado de moldes.
Optimización del rendimiento de las microesferas cerámicas
Ajustando los parámetros del equipo, como la PSI y el ángulo de chorreado, puede maximizar la vida útil y la eficacia de las microesferas cerámicas. Por ejemplo, un estudio de caso de un cliente demostró que las bolas de cerámica duraban tres veces más que las de vidrio cuando se utilizaban a 80 PSI y un ángulo de chorreado de 30°.
Prolongación de la vida útil de los medios mediante el mantenimiento de los equipos
El mantenimiento periódico del equipo, como la limpieza y calibración del sistema de recogida de polvo, puede reducir el consumo de material hasta 15%. Esto no solo reduce los costes, sino que también garantiza unos acabados superficiales uniformes.
Elegir el equipo de chorreado adecuado es crucial para conseguir un acabado perfecto de los moldes. Si se centra en el control de PSI, la recuperación de medios y la recogida de polvo, puede mejorar significativamente la eficacia y reducir los costes. Tanto si opta por una cabina neumática, una arenadora de ruedas o un sistema automatizado, cada tipo de máquina ofrece ventajas únicas adaptadas a aplicaciones específicas.
Si no está seguro de qué equipo se adapta mejor a sus necesidades, contacte con nosotros para una consulta gratuita y deje que nuestros expertos le guíen hacia la solución ideal.
Esté atento a nuestro próximo blog, en el que profundizaremos en las ventajas del granallado cerámico para el acabado de moldes.
Filtros