Cuenta de cerámicas Manual del usuario: 7 pasos para mejorar el acabado del molde
12 de febrero de 2025
Mantener un acabado uniforme es uno de los objetivos clave durante la fabricación y el mantenimiento de moldes. Sin embargo, aunque se siga estrictamente el proceso estándar, muchos clientes siguen encontrándose con los siguientes problemas:
"¿Por qué el acabado del molde aún no está a la altura?".
"¿Cómo evitar rayar la superficie del molde durante el chorro de arena?"
"¿Cómo optimizar la eficiencia de uso de las microesferas cerámicas?"
Las necesidades esenciales de estos problemas son:
- Repetibilidad - el acabado de los distintos lotes de moldes debe ser homogéneo.
- Controlabilidad de los costes - reducir la pérdida de medios y los costes de mano de obra y mejorar el rendimiento de los costes.
- Seguridad operativa - Garantizar una producción segura mediante el control del polvo y la protección de los equipos.
En respuesta a las necesidades anteriores, hemos resumido un proceso profesional de 7 pasos para ayudarle a mejorar el acabado del molde de forma eficaz y segura.
Paso 1: Inspección previa al tratamiento para eliminar la fuente de peligros ocultos
Puntos débiles del cliente
- Ignorar los defectos menores (como arañazos de 0,1 mm) provoca fallos posteriores en el pulido.
- Un mal estado del equipo (como el desgaste de las boquillas) desperdicia material y reduce el efecto del chorro de arena.
Solución
1.1 Detección de defectos de moho
Utilice una lupa de 20 aumentos para comprobar la superficie del molde, centrándose en la línea de separación y la ranura de ventilación. Se recomienda utilizar un rugosímetro portátil (como el Mitutoyo SJ-210) para medir con precisión el estado de la superficie.
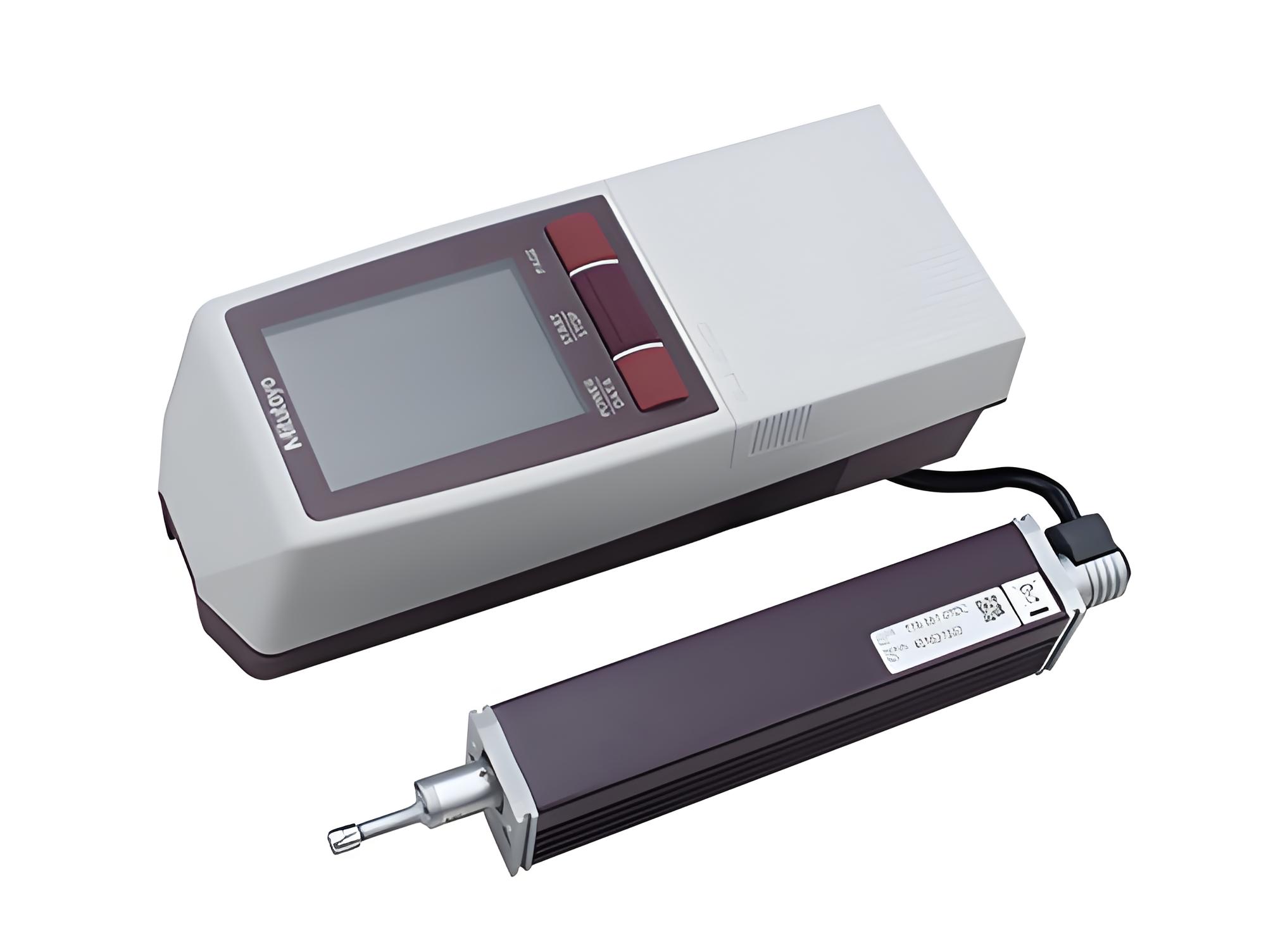
1.2 Lista de inspección previa de los equipos
- Desgaste de la boquilla: El cambio de diámetro interior debe ser≤5%, y necesita ser reemplazado si excede.
- Estabilidad de la presión del aire: Fluctuación range≤±2 PSI para evitar la inyección inestable.
Paso 2: fórmula de ajuste de la presión, la ciencia sustituye a la experiencia
Puntos débiles del cliente
- Confiar en la experiencia para ajustar la presión conduce a un rectificado excesivo de los materiales blandos o a una limpieza insuficiente de los materiales duros.
Tipo de material | Coeficiente de material |
---|---|
Plástico (ABS) | 0.8 |
Aleación de aluminio | 1.2 |
Acero inoxidable | 1.5 |
Aleación de titanio | 2.0 |
Carburo | 2.5 |
Solución
2.1 Fórmula de cálculo de la PSI
PSI = dureza media × coeficiente del material de la pieza × 10
Ejemplo de cálculo:
Molde de aleación de titanio, con perlas de cerámica de dureza 7 Mohs:
PSI = 7 × 2.0 × 10 = 140
2.2 Consejos para ajustar la presión
Mida el valor Ra después de la primera operación: si el valor Ra es demasiado alto, aumentar 5-10 PSI; si el valor Ra es demasiado bajo, reducir 5-10 PSI.
Protección de material blando: Para los moldes de plástico, el límite superior de PSI es de 80 para evitar un rectificado excesivo.
Limpieza eficaz de materiales duros: Para moldes de aleación de titanio, el límite inferior de PSI es de 140 para garantizar el efecto de limpieza.
Paso 3: Control de ángulos y distancias, la victoria de la mecánica geométrica
Puntos débiles del cliente
- La inyección vertical provoca un exceso de rectificado local, y el ángulo de incidencia de 30° es difícil de controlar con precisión.
Solución
3.1 Solución de optimización del ángulo de incidencia de 30
- Con un ángulo de incidencia de 30°, la fuerza tangencial representa 70% y la fuerza normal 30%, lo que equilibra la eficacia de la limpieza y la protección de la superficie.
- Distancia de pulverización = diámetro de la boquilla × 10 (por ejemplo: boquilla de 8 mm → distancia de 80 mm).
3.2 Herramientas prácticas
El indicador de ángulo láser (error ±1°) garantiza un control preciso del ángulo.
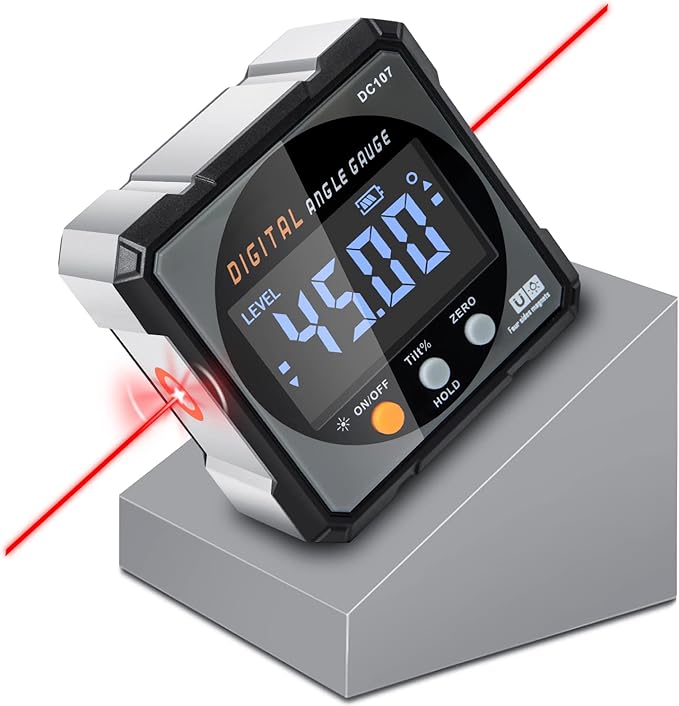
Paso 4: Control del estado de los soportes, la clave para alargar su vida útil
Puntos débiles del cliente
- Imposibilidad de determinar cuándo sustituir las microesferas cerámicas, con el consiguiente desperdicio de costes o degradación de la calidad.
Solución
4.1 Detección del índice de aplastamiento
Tomar 100 g de material y clasificar manualmente las partículas trituradas. Si el índice de trituración es >5%, es necesario sustituirlo.
4.2 Supervisión inteligente en línea
Instale un sensor de tamaño de partículas en línea para controlar el cambio del tamaño de las partículas del medio en tiempo real.
Modelo de bolas de cerámica HLH | Tamaño estándar de las partículas (µm) | Desviación admisible (µm) |
---|---|---|
B20 | 600-850 | ±50 |
B30 | 425-600 | ±35 |
B40 | 250-425 | ±20 |
B60 | 125-250 | ±15 |
B80 | 180-250 | ±15 |
B100 | 125-180 | ±10 |
B120 | 63-125 | ±8 |
B125 | 0-125 | ±8 |
B170 | 45-90 | ±5 |
B205 | 0-63 | ±5 |
B400 | 30-63 | ±3 |
B505 | 10-30 | ±2 |
Paso 5: Normas de inspección de la calidad posterior al tratamiento, aceptación basada en datos
Puntos débiles del cliente
- Sólo la inspección visual conduce a la exposición tardía del problema del acabado deficiente.
Solución
5.1 Herramientas recomendadas para medir el valor Ra
Modelo básico: Rugosímetro manual Time 3220
Ventajas: portátil y fácil de usar, adecuado para la detección rápida in situ, precisión ±5%.
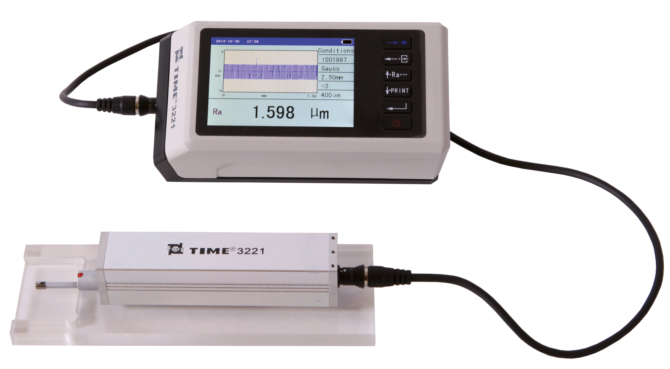
Modelo de alta precisión: Perfilómetro óptico 3D Zygo NewView 9000.
Ventajas: medición de alta precisión, adecuada para superficies complejas, resolución hasta el nivel nanométrico.
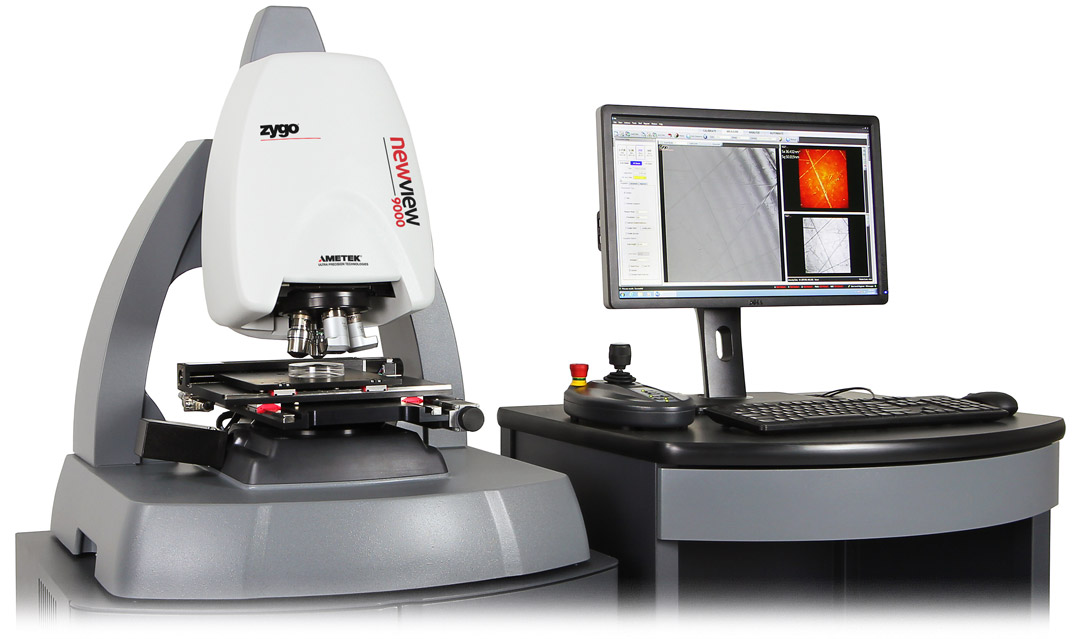
5.2 Normas de valor Ra del sector
Industrias seleccionadas | Materiales comunes | Requisitos Ra (µm) | Número de puntos de prueba |
---|---|---|---|
Componentes electrónicos | Conectores de aleación de cobre | ≤0.4 | ≥10 puntos/㎡ |
Carcasas de plástico de precisión | ≤0.6 | ≥8 puntos/㎡ | |
Autopartes | Piezas del motor de aleación de aluminio | ≤0.8 | ≥5 puntos/㎡ |
Discos de freno de acero inoxidable | ≤1.0 | ≥6 puntos/㎡ | |
Productos sanitarios/implantes | Implantes ortopédicos de aleación de titanio | ≤0.4 | ≥12 puntos/㎡ |
Instrumental quirúrgico de acero inoxidable | ≤0.6 | ≥10 puntos/㎡ | |
Aeroespacial | Palas de turbina de aleación de titanio | ≤0.3 | ≥15 puntos/㎡ |
Piezas de motor de aleación de alta temperatura | ≤0.5 | ≥10 puntos/㎡ |
Paso 6: Especificaciones de tratamiento de residuos, conformidad y reducción de costes en paralelo
Puntos débiles del cliente
- Los costes de tratamiento de los residuos son elevados y existen riesgos medioambientales.
Solución
6.1 proceso de reciclado de microesferas cerámicas
Separación magnética (eliminación de impurezas metálicas) → separación por aire (eliminación de polvo) → cribado (clasificación y reutilización).
Tasa de recuperación: ≥85% (la tasa de trituración debe controlarse <5%).
6.2 Conformidad del tratamiento de los residuos
- Polvo de cerámica (vertedero inofensivo)
- Residuos metálicos (reciclaje profesional)
Paso 7: Solución de problemas comunes, guía de respuesta rápida
Puntos débiles del cliente
- Los problemas repentinos (como una superficie irregular) provocan el estancamiento de la línea de producción
Solución
Fenómeno problemático | Motivos posibles | Solución |
---|---|---|
Mate parcial | Distribución desigual de los medios de comunicación | Comprobar el separador de arena y limpiar el punto de obstrucción |
Rayas periódicas | Desgaste excéntrico de la boquilla | Sustituir la boquilla y calibrar la concentricidad |
Pulido excesivo de los bordes | El ángulo de incidencia es demasiado grande (>45°) | Ajuste el ángulo a 30° y reduzca el PSI |
Arañazos superficiales | Selección incorrecta de la granularidad de los medios | Sustituir la arena cerámica por la granulometría adecuada |
Excesivos residuos de polvo | El sistema de eliminación de polvo es ineficaz | Compruebe el equipo de eliminación de polvo y limpie el elemento filtrante |
Sobrecalentamiento parcial del molde | El tiempo de inyección es demasiado largo | Acortar el tiempo de inyección única y aumentar el intervalo de enfriamiento |
PREGUNTAS FRECUENTES: Respuestas rápidas a preguntas frecuentes
Q: ¿Cuántas veces hay que cambiar las cuentas de cerámica después de reciclarlas?
R: Se recomienda que sea 20 veces, o que el índice de trituración sea >5% (lo que ocurra primero).
Q: ¿Cómo se trata el polvo de adsorción electrostática del molde tras la operación de perlas cerámicas?
R: Utilice una pistola de aire ionizado para soplar + limpiar con etanol anhidro.
Q: ¿Cómo evitar la deformación de moldes de paredes finas (<1 mm)?
R: Utilice arena fina superior a #220, PSI≤50, y reduzca el ángulo de incidencia a 20°.
A través de este proceso profesional de 7 pasos, no sólo puede resolver el problema de la superficie de los acabados del molde que no cumplen con la norma, sino también lograr:
- Reducción de costes: la pérdida de medio se reduce en 30%, y el intervalo de mantenimiento del equipo se prolonga 2 veces.
- Mejora de la calidad: la consistencia del acabado (valor CV) se comprime de 5% a ≤2%.
- Garantía de conformidad: 100% cumple la norma ISO 9001/14001 y las normas específicas del sector.
Ve a practicarlo ahora.
Si tiene alguna pregunta, por favor contacte con nosotros para una consulta gratuita~
Filtros