¿Cómo se adaptan los componentes electrónicos a entornos difíciles?
3 de enero de 2025
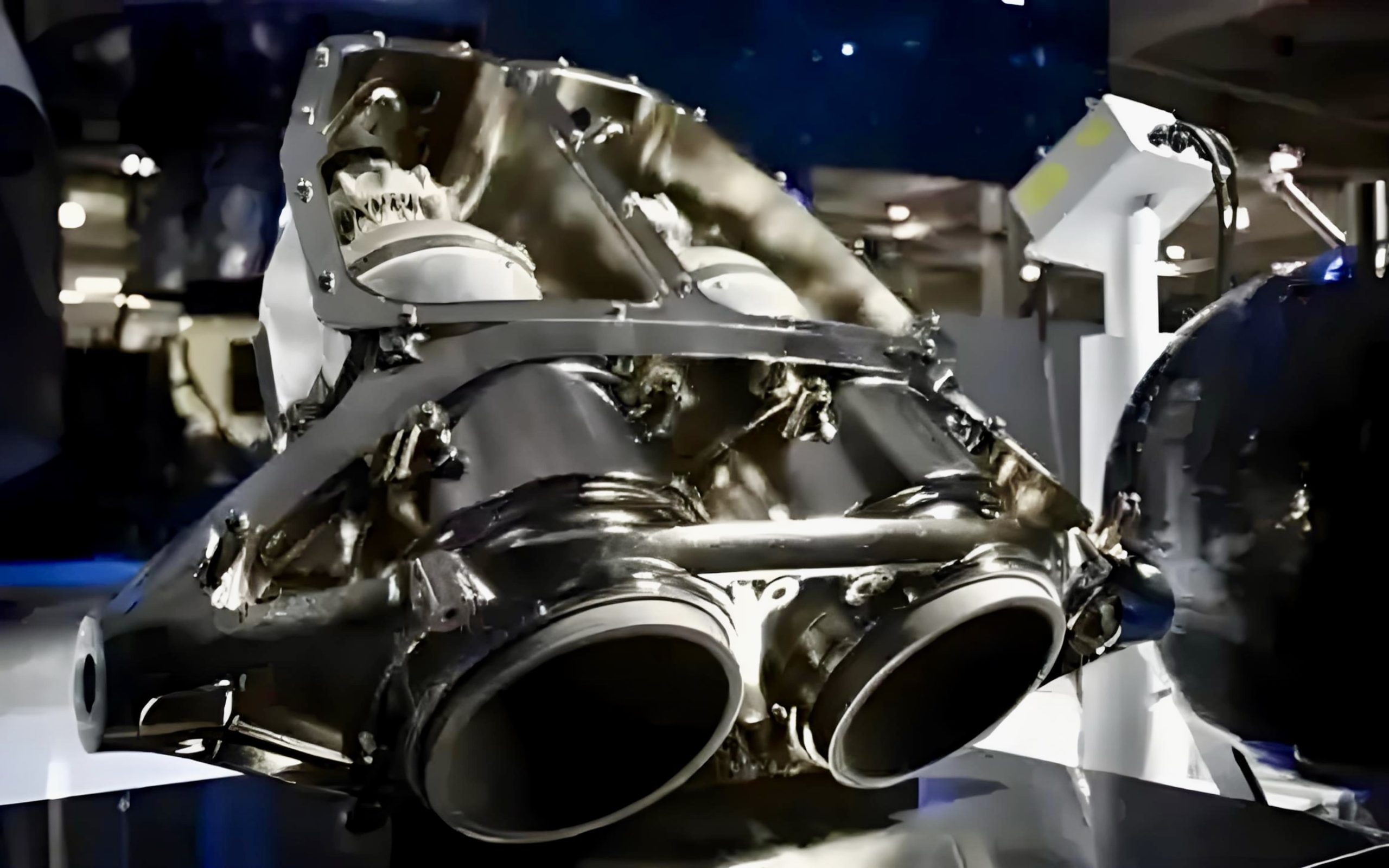
En el sector aeroespacial, los componentes electrónicos de precisión no sólo son los componentes centrales de control de naves espaciales y aeronaves, sino que también asumen tareas clave como la comunicación, la navegación y la gestión de la energía. Por ejemplo, el funcionamiento en órbita de satélites, la navegación de aeronaves, la supervisión de motores de aviones, etc. deben mantener una alta fiabilidad y durabilidad en entornos extremos.
Sin embargo, el entorno operativo del sector aeroespacial es extremadamente complejo y duro. Los componentes electrónicos se enfrentan a cambios extremos de temperatura, fuertes vibraciones y radiaciones, y a pequeños fallos que pueden acarrear graves consecuencias.
Por lo tanto, mejorar la adaptabilidad de los componentes en entornos difíciles se ha convertido en una cuestión clave en la fabricación de componentes electrónicos aeroespaciales y el tratamiento de superficies. Con el desarrollo de la tecnología de refuerzo y protección de superficies, ha surgido gradualmente el potencial de procesos como el chorro de arena y el granallado, que proporcionan una forma eficaz de resolver el problema.
Principales tipos de componentes electrónicos de precisión
En el ámbito aeroespacial, los siguientes componentes electrónicos de precisión son cruciales:
- Componentes de navegación y control: como los sistemas de navegación inercial y los ordenadores de control de vuelo, son responsables de la gestión de la actitud y la trayectoria de las aeronaves.
- Equipo de comunicación: incluidos módulos de radiofrecuencia de alta frecuencia y antenas de satélite para garantizar la transmisión de datos en tiempo real.
- Sensores del sistema eléctrico: como sensores de temperatura, presión y vibración, que controlan el rendimiento del motor y del sistema de propulsión.
- Módulo de gestión de energía: paquetes de baterías y sistemas de distribución de energía eficientes para mantener la estabilidad del suministro eléctrico de las naves espaciales.
- Conectores e interconexiones electrónicas: como conectores PCB y conectores circulares para garantizar la fiabilidad de la transmisión de señales eléctricas y potencia.
Las características comunes de estos componentes son la alta precisión, la alta sensibilidad y la versatilidad, y deben mantener un funcionamiento estable en diversas condiciones extremas.
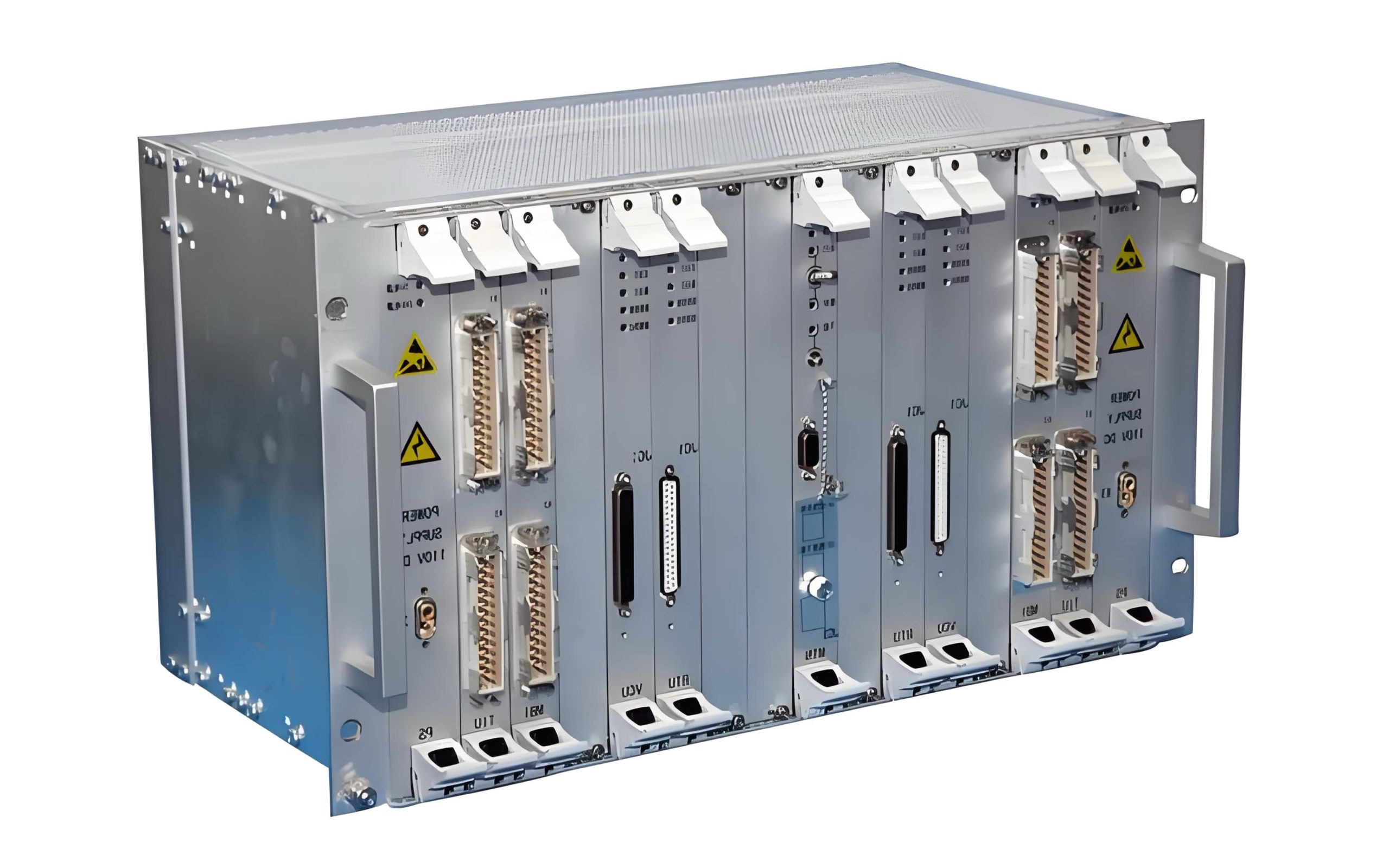
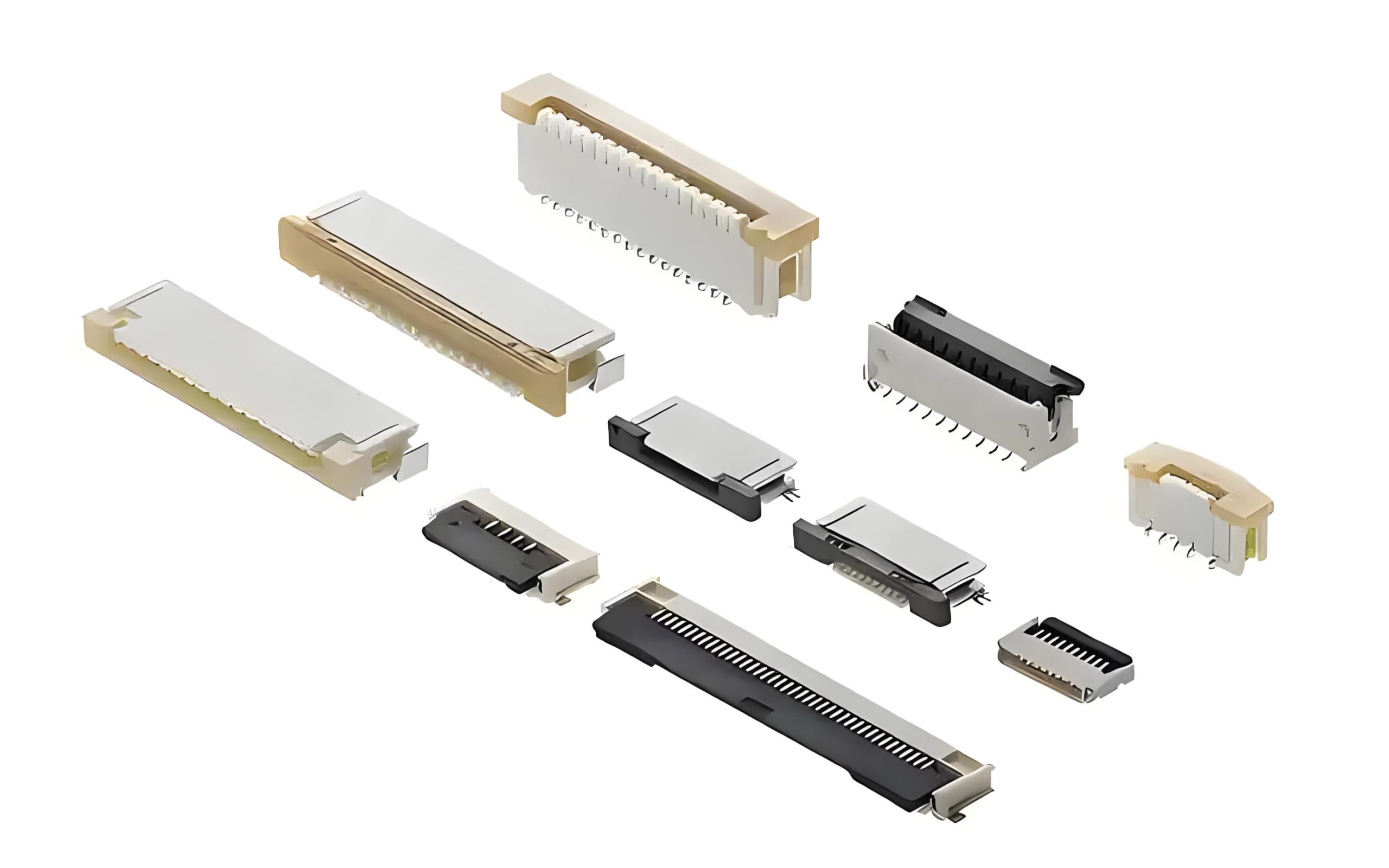
El sector aeroespacial ante los retos de un entorno hostil
- Cambios extremos de temperatura: de -60 °C en la superficie terrestre a +125 °C en el entorno espacial, la temperatura cambia drásticamente.
- Fuertes vibraciones y choques: El despegue y aterrizaje de aeronaves, el encendido del sistema de propulsión y el vuelo de larga duración producirán vibraciones continuas de alta frecuencia.
- Exposición a la radiación cósmica: La radiación de partículas de alta energía tiene un efecto degradante sobre los materiales semiconductores y los microcircuitos de los componentes electrónicos.
- Entorno de baja presión y vacío: lo que reduce la capacidad de disipación del calor y aumenta el riesgo de fallo térmico de los dispositivos.
- Corrosión química y desgaste: como fugas de refrigerante, residuos de combustible o partículas de polvo que erosionan físicamente la superficie de los componentes.
Por este motivo, el tratamiento de refuerzo de la superficie, la optimización del rendimiento de disipación del calor y la tecnología de refuerzo estructural se han convertido en medios clave para resolver estos retos.
Soluciones para mejorar la adaptabilidad
Optimización de materiales y diseño
- Selección de materiales de alto rendimiento
- Materiales cerámicos: tienen una excelente estabilidad a altas temperaturas y resistencia a la corrosión, y pueden utilizarse para carcasas y cubiertas protectoras.
- Aleaciones metálicas especiales: como las aleaciones de titanio y las aleaciones de aluminio, tienen una alta resistencia a la temperatura y al impacto, adecuadas para componentes estructurales y componentes conductores.
- Revestimiento de material polimérico: puede utilizarse para mejorar la resistencia a la radiación y reducir la degradación de las superficies de los componentes causada por la erosión de partículas de alta energía.
- Modularidad y diseño estructural
- Diseño modular: al reducir la complejidad y separar los componentes sensibles, se puede reducir eficazmente el impacto de transmisión de los choques ambientales.
- Diseño estructural amortiguador: uso de materiales amortiguadores y disposición optimizada para resistir los daños en los componentes de precisión causados por vibraciones y choques mecánicos.
El papel clave del proceso de fabricación
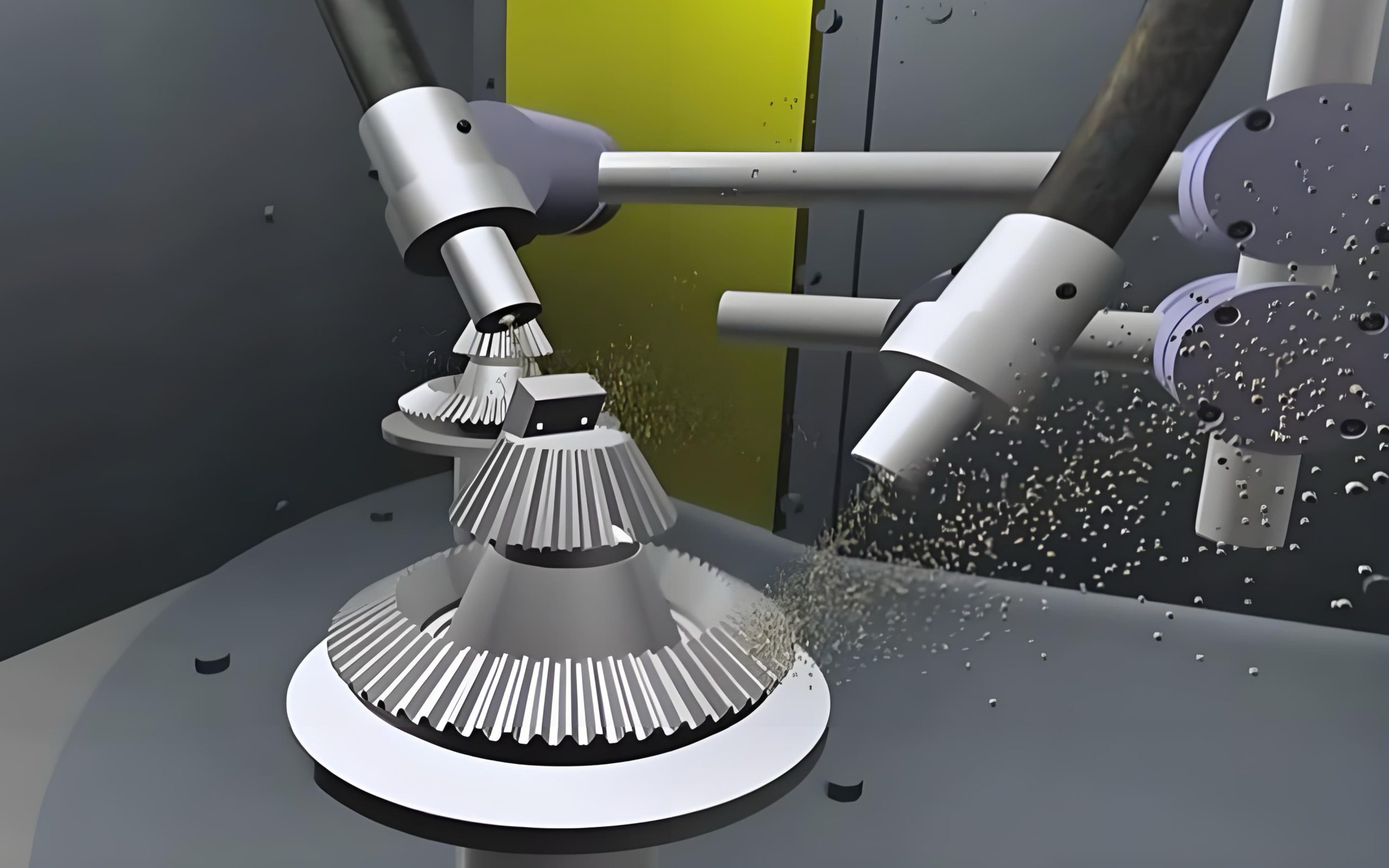
- Tecnología de mecanizado de precisión
- El mecanizado de alta precisión garantiza la coincidencia y durabilidad de los componentes y reduce el riesgo de fallos causados por problemas de tolerancia en entornos difíciles.
- La tecnología de micromecanizado de precisión se utiliza en dispositivos semiconductores para reducir eficazmente los defectos superficiales y mejorar el rendimiento general.
- Tecnología de tratamiento de superficies
- Proceso de arenado: Utiliza microesferas cerámicas de alto rendimiento o medios de alúmina para limpiar la superficie, eliminar rebabas y microfisuras, y mejorar la resistencia a la corrosión y a la fatiga de los componentes.
- Proceso de granallado: Utiliza partículas de alta resistencia para impactar en la superficie del material, inducir la distribución de la tensión de compresión y mejorar la capacidad del componente para resistir impactos mecánicos. Es especialmente adecuado para piezas de motores aeronáuticos que deben soportar vibraciones.
- Tecnología de revestimiento: Por ejemplo, los revestimientos resistentes a las altas temperaturas y a las radiaciones pueden mejorar aún más la adaptabilidad medioambiental de los componentes electrónicos.
Los medios de tratamiento de superficies ayudan a mejorar la durabilidad
El papel de la tecnología de chorro de arena
La tecnología de chorreado de arena proporciona una protección fiable y una optimización del rendimiento de los componentes electrónicos de precisión mediante el uso de medios de alta eficacia para impactar en la superficie del material:
- Mejorar el acabado superficial
Para optimizar el acabado de la carcasa del conector, los medios de arenado (como la alúmina ultrafina) pueden eliminar pequeñas rebabas o superficies irregulares durante el procesamiento y evitar el inicio y la expansión de microfisuras. Esto es crucial para los conectores de naves espaciales o las carcasas de sensores y puede prolongar eficazmente su vida útil.
- Eliminar óxidos metálicos y contaminantes
Los medios de alúmina de gran pureza pueden eliminar rápidamente la capa de óxido de la superficie metálica con su estabilidad química, evitando que la fuente de corrosión afecte a las propiedades conductoras de los componentes de precisión. Por ejemplo, las juntas de soldadura y los puntos de contacto de los módulos de aviónica deben mantenerse limpios y sin oxidación, y el chorreado puede cumplir este requisito con precisión.
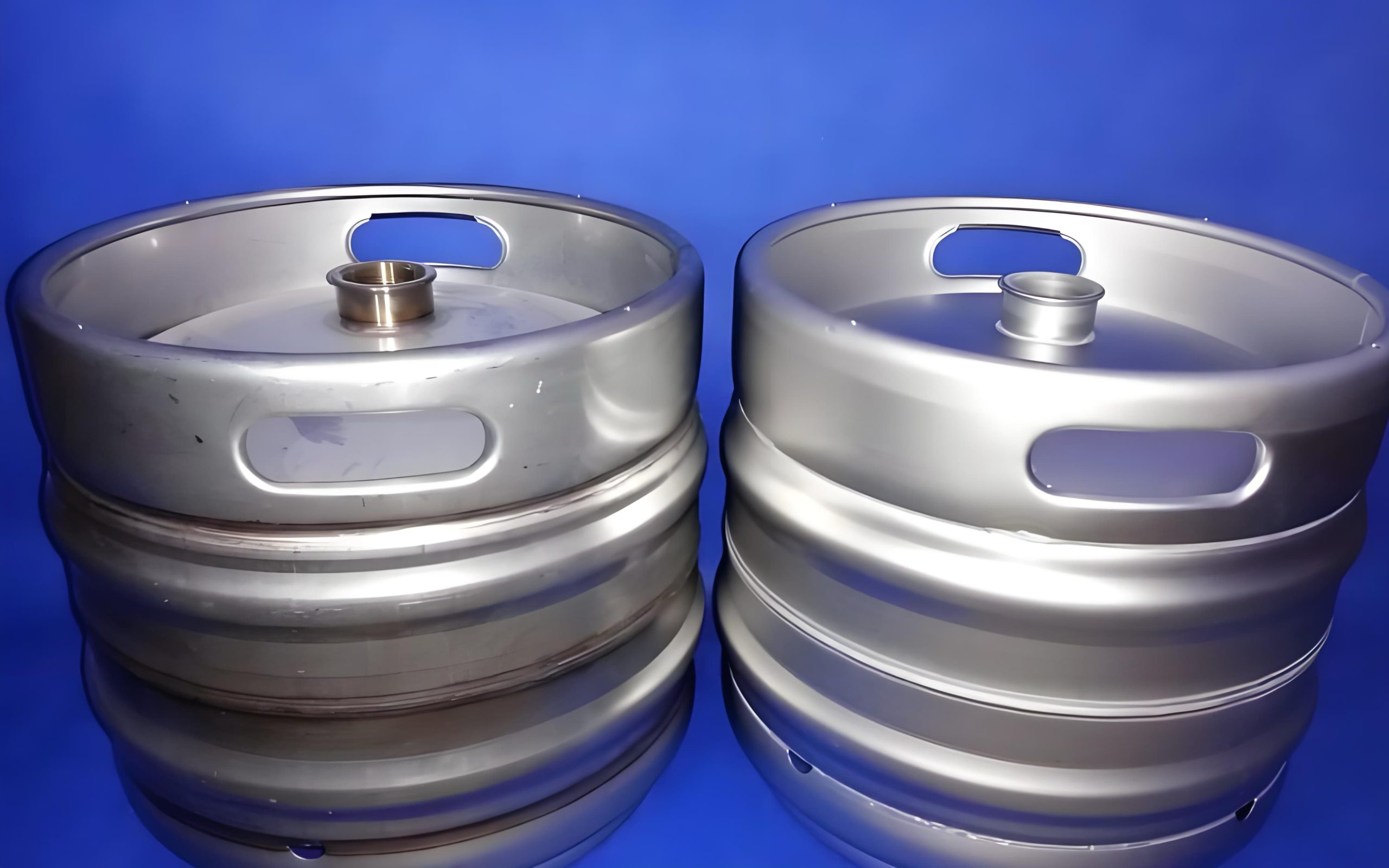
- Adaptación a geometrías complejas
El proceso de arenado, combinado con el refinado tamaño de las partículas del abrasivo, puede penetrar fácilmente en las complejas superficies de los componentes electrónicos, como la estructura multipolo de los conectores de aviación. Esta capacidad garantiza un tratamiento uniforme de toda la superficie, sin ángulos muertos que afecten a la fiabilidad.
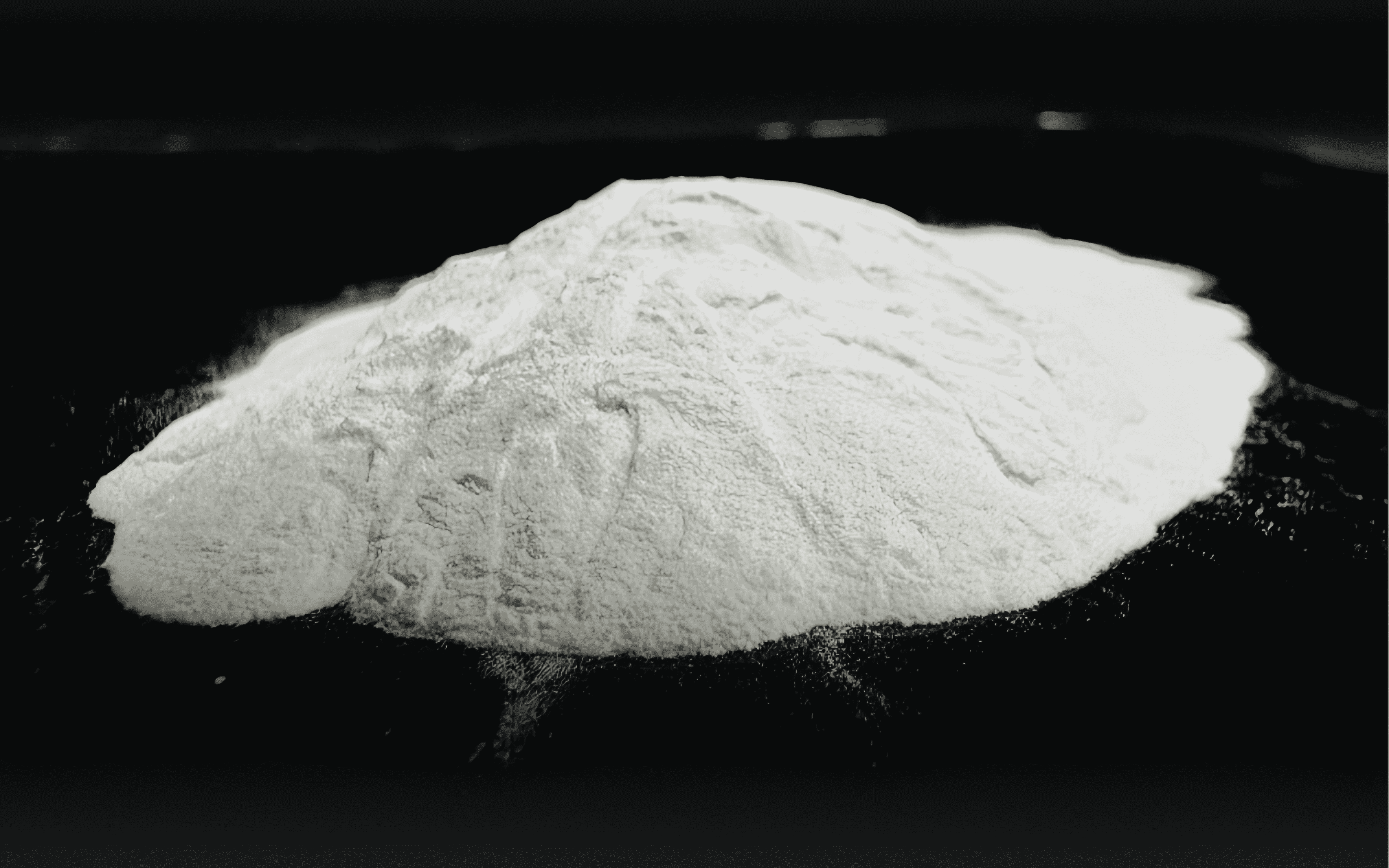
- Mejorar la resistencia a la fatiga
Los componentes electrónicos de precisión son susceptibles de sufrir daños por tensión mecánica en entornos de alta vibración (como los sistemas de propulsión de la aviación). El shot peening con microesferas cerámicas o de óxido de circonio puede formar una capa de tensión compresiva en la superficie de la carcasa, reducir la tasa de crecimiento de grietas y mejorar la vida a fatiga.
- Prevención de la corrosión bajo tensión
Los módulos y controladores electrónicos del sector aeroespacial son propensos a fallar cuando se exponen a productos químicos corrosivos. El shot peening mejora la resistencia de la superficie a la corrosión. Por ejemplo, en las carcasas de embalaje modular utilizadas para las unidades electrónicas de control de vuelo, el granallado puede reducir significativamente la erosión de los materiales metálicos por la niebla salina y la humedad.
- Refuerzo de superficies compuestas
Para los nuevos materiales compuestos utilizados en naves espaciales, el granallado con óxido de circonio puede mejorar su resistencia de unión interfacial, garantizar un diseño ligero y lograr una alta fiabilidad. Esto es especialmente importante para los componentes de los sensores de precisión de los bastidores de soporte de los motores de las aeronaves.
Medios recomendados y sus características
Granalla cerámica para el acabado de superficies
Características: Las perlas de cerámica tienen una alta dureza y una excelente durabilidad, superficie lisa y tamaño de partícula consistente, lo que puede reducir la generación de polvo durante el procesamiento y garantizar la protección del medio ambiente y la limpieza.
Escenarios de aplicación: Adecuado para carcasas de componentes electrónicos que requieren un tratamiento superficial de alta precisión, como carcasas de conectores aeroespaciales y componentes electrónicos sensibles.
Solución de problemas: Elimine eficazmente los defectos superficiales al tiempo que mejora la resistencia a la corrosión para garantizar la fiabilidad en entornos difíciles.
Perlas de circonio estabilizado con itria
Características: Las perlas de circonio son conocidas por su alta densidad y excelente resistencia al impacto. Son adecuadas para reforzar la superficie de los materiales, especialmente mostrando una excelente estabilidad en entornos de alta temperatura y alta tensión.
Escenarios de aplicación: Recomendado para reforzar los procesos de granallado de componentes de motores de aviación, carcasas de motores y capas protectoras de módulos electrónicos.
Solución de problemas: Mejorar la resistencia a la fatiga y a la corrosión bajo tensión de los componentes mediante el refuerzo de la tensión superficial, y prolongar la vida útil de los componentes.

Granalla cerámica para shot peening
Características: Las perlas cerámicas de granallado tienen una distribución granulométrica consistente y una excelente resistencia al desgaste, y pueden introducir con precisión la tensión de compresión durante el tratamiento de la superficie sin dañar la superficie del sustrato.
Escenarios aplicables: Adecuado para reforzar el armazón de naves espaciales y módulos electrónicos sensibles, como unidades de navegación y control en entornos de alta vibración.
Solución de problemas: Reducir la propagación de grietas superficiales, mejorar significativamente la vida a fatiga de los materiales y aumentar la resistencia de la capa superficial a la corrosión.
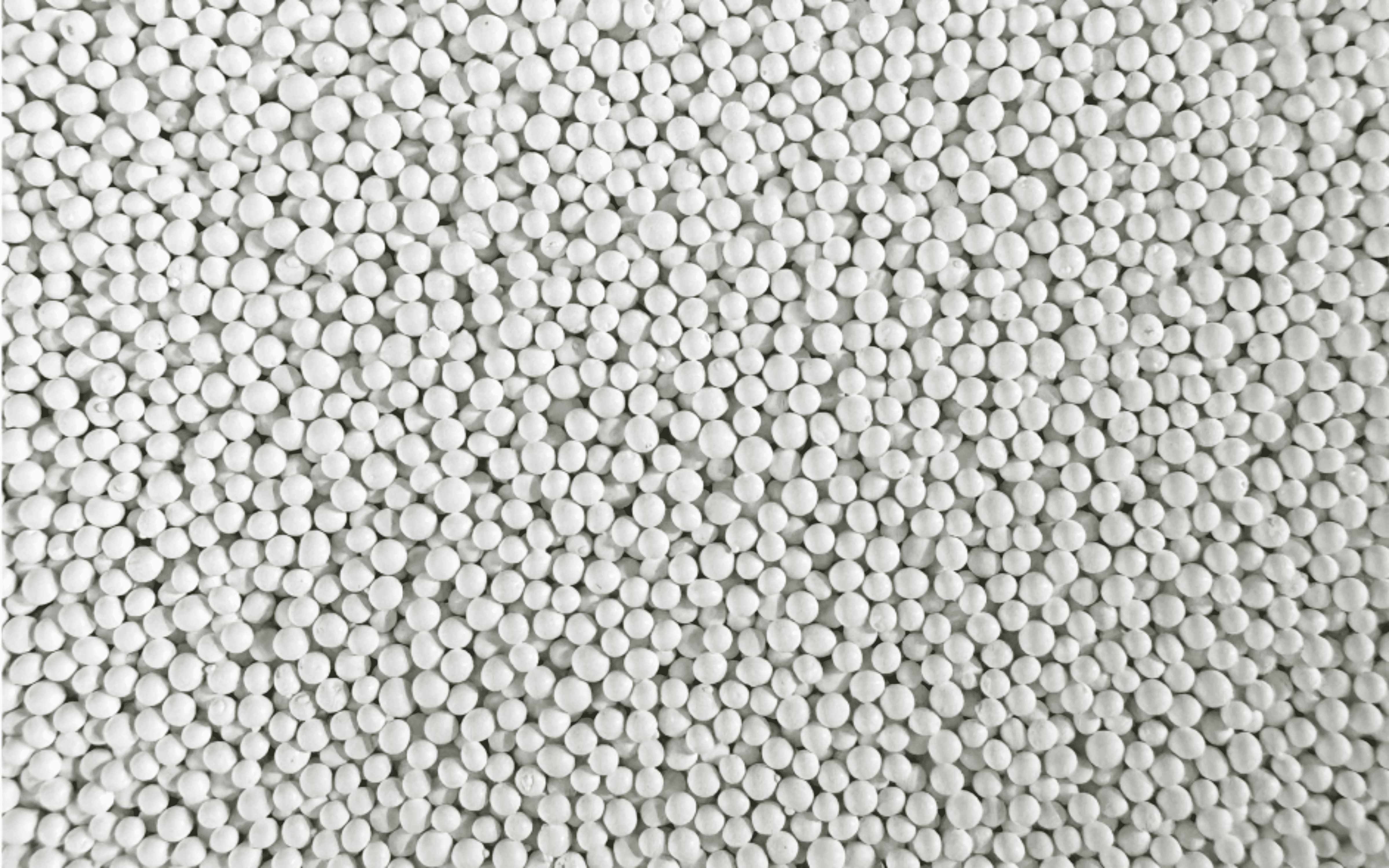
Características: Conocido por su tamaño de partícula ultrafino y su alta dureza, puede lograr un tratamiento de superficies de altísima precisión manteniendo la integridad de la pieza procesada, y propiedades químicas estables, y no contaminará la superficie tratada.
Escenarios de aplicación: Especialmente adecuado para el microprocesado de microsensores, pines de conectores de PCB y otros componentes electrónicos sensibles.
Solución de problemas: Eliminar óxidos y contaminantes, optimizar el acabado superficial y mejorar la conductividad y la resistencia a la corrosión de componentes electrónicos de precisión.
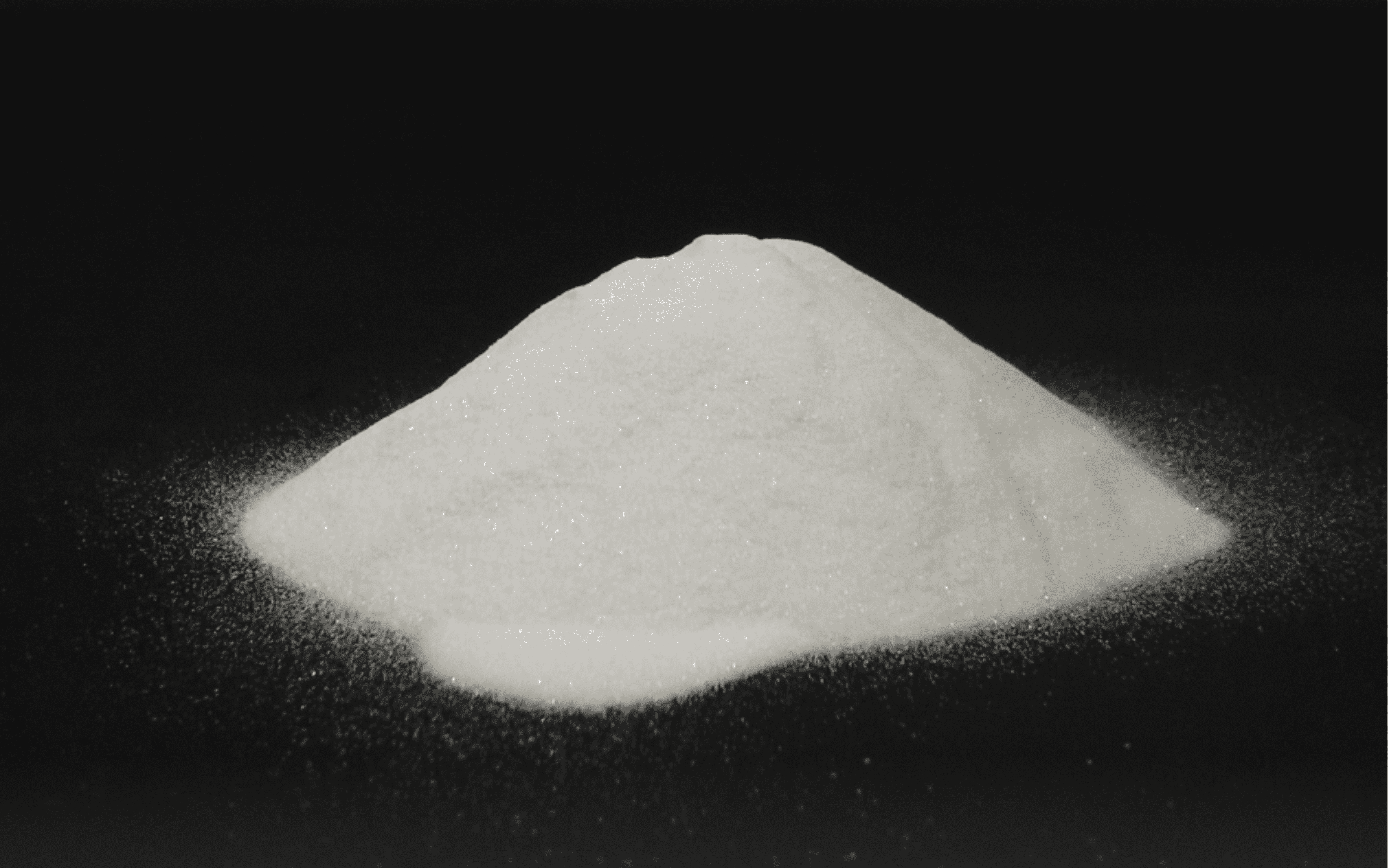
Gracias a la sinergia del chorro de arena y el granallado, estos medios de tratamiento de superficies se han convertido en el principal refuerzo para que los componentes electrónicos de precisión alcancen una alta fiabilidad y durabilidad en entornos difíciles.
Casos reales de aplicación
Las perlas de circonio refuerzan las carcasas de los sensores de las naves espaciales.
El caso: Una empresa aeroespacial utiliza perlas de circonio para granallar la carcasa del sensor de una nave espacial con el fin de mejorar su resistencia a la fatiga y a la corrosión bajo tensión. Las perlas de circonio tienen una dureza y una resistencia al desgaste extremadamente altas. Tras el granallado fino, la carcasa del sensor muestra una mayor resistencia al impacto y a los cambios ambientales. Tras este tratamiento, la resistencia a la fatiga del sensor en entornos extremos mejora en unos 30%, y se prolonga su vida útil.
Las microesferas cerámicas mejoran la rugosidad superficial de los conectores de aviación.
Caso: En un proyecto de aviónica, se utilizan microesferas cerámicas para mejorar la rugosidad superficial de los conectores de aviación. Mediante el proceso de arenado, las microesferas cerámicas pueden eliminar eficazmente pequeños defectos superficiales y mejorar la conductividad eléctrica y el rendimiento de transmisión de señales del conector. La rugosidad de la superficie del conector tratado se reduce en 40%, lo que mejora enormemente la estabilidad del rendimiento del conector en entornos de transmisión de datos a alta velocidad y alta temperatura.
Los medios de alúmina eliminan los óxidos superficiales de los componentes.
Caso práctico: Una empresa militar utiliza medios de alúmina para chorrear piezas de precisión de motores de aviones con el fin de eliminar los óxidos superficiales. Las partículas de alúmina no sólo eliminan las incrustaciones de óxido, sino que también protegen las superficies metálicas de una mayor corrosión. Tras realizar pruebas en entornos de alta temperatura y alta presión, las piezas tratadas mostraron una durabilidad 25% mayor que las no tratadas. Esta tecnología se ha utilizado en múltiples proyectos de motores de aviación, ampliando significativamente la vida útil de los componentes del motor.
A través de estos casos, podemos ver que elegir los medios de tratamiento de superficies adecuados es crucial para los componentes electrónicos de precisión en el sector aeroespacial, que no sólo pueden mejorar el rendimiento de los componentes, sino también prolongar significativamente su vida útil.
Desde su fundación en 2001, Henglihong se ha centrado en el campo de los medios abrasivos para chorro de arena y granallado, combinados con la tecnología alemana de equipos Nabotum para garantizar una producción automatizada de alto nivel. Contamos con 38.000 metros cuadrados de modernas instalaciones y un equipo senior de I+D para ofrecer soluciones personalizadas a clientes de todo el mundo.
Con las certificaciones ISO9001, ISO14001 y CE de la UE, ROHS, nuestros productos tienen un rendimiento superior y el proceso de producción cumple las normas medioambientales. Nos adherimos al principio de "el cliente primero", proporcionamos una entrega eficiente y un servicio personalizado, y establecemos relaciones de cooperación a largo plazo.
En la actualidad, Henglihong se ha ganado la confianza de clientes de todo el mundo gracias a su excelente calidad, su rápida respuesta y su compromiso medioambiental. ¡Elegir a Henglihong significa elegir a un socio digno de confianza!
Ofrecemos servicios gratuitos de consultoría para ayudarle a elegir los materiales de chorreado más adecuados. Envíenos muestras, las probaremos y le recomendaremos la mejor solución según sus necesidades. Al mismo tiempo, apoyamos las pruebas de lotes pequeños para asegurarnos de que realiza una elección acertada.
Para obtener más información sobre el producto o un presupuesto, póngase en contacto con contacta con nosotros!
No olvide marcar nuestro sitio web, actualizaremos el blog periódicamente para ofrecerle más información del sector y consejos prácticos.
Filtros