Dominio del proceso de chorreado: Tratamiento óptimo de superficies
27 de agosto de 2024
El proceso de chorreado de arena es un paso crucial en el tratamiento de superficies, que determina la calidad final y el rendimiento de la pieza. Desde la configuración del equipo de chorro de arena hasta cada detalle de la operación, requiere no sólo apoyo técnico sino también la meticulosidad y precisión del operario. Este artículo le guiará a través de los diversos aspectos del proceso de chorreado de arena, ayudándole a dominar este proceso de principio a fin para garantizar que cada operación logre los resultados deseados.
Preparación para el chorro de arena
La preparación para el chorreado es clave para garantizar el efecto final del tratamiento y la calidad de la pieza. Este proceso puede dividirse en los siguientes aspectos importantes: preparación de la pieza, selección del medio de chorreado y selección y configuración del equipo.
1. Preparación de la pieza
Antes del chorreado de arena, la limpieza inicial de la pieza es crucial. Los pasos de limpieza pueden eliminar grasa, suciedad, óxido u otros materiales superficiales sueltos para garantizar la uniformidad y eficacia del chorreado. Los distintos materiales de las piezas de trabajo tienen diferentes requisitos de preparación:
- Piezas metálicas: En primer lugar, elimine la grasa y la suciedad de la superficie mediante limpieza con disolventes, fregado mecánico o limpiadores químicos. En el caso de las piezas de hierro, la eliminación del óxido suele realizarse con cepillos o agentes químicos. La pieza limpia debe secarse a fondo para evitar que la humedad residual afecte al resultado del chorreado.
- Piezas de plástico: El plástico es relativamente frágil y requiere una manipulación cuidadosa. Utilice limpiadores suaves y paños suaves para limpiar la superficie y eliminar la grasa y la suciedad. Para manchas difíciles, utilice limpiadores especializados para plástico. Tenga especial cuidado con los cepillos ásperos o los limpiadores fuertes, ya que pueden dañar la superficie de plástico.
- Piezas de cerámica: Las piezas de cerámica son relativamente duras y suelen tener grasa natural o polvo en la superficie. Utilice un cepillo suave o una corriente de aire para eliminar el polvo, luego lave con agua tibia y detergente neutro y, por último, seque bien.
2. Selección del medio de chorreado
La elección del material de chorreado afecta directamente al proceso de chorreado y a los resultados finales. Por lo tanto, es crucial seleccionar el abrasivo adecuado en función del material de la pieza, el efecto superficial deseado y los requisitos del tratamiento. Entre los medios de chorreado más comunes se incluyen:
- Óxido de aluminio: Con gran dureza y resistencia al desgaste, adecuado para aplicaciones que requieren una fuerte abrasión, ideal para tratar superficies metálicas, eliminar óxidos o revestimientos antiguos. Debido a su mayor coste, suele utilizarse para aplicaciones de gama alta o tratamientos especiales.
- Cuentas de vidrio: Más suave, adecuado para tratamientos superficiales finos, como carcasas de electrónica de consumo. El chorreado con microesferas de vidrio elimina eficazmente los contaminantes superficiales, mejora la suavidad de la superficie y no provoca un desgaste excesivo de la pieza.
- Medios cerámicos: De dureza moderada, entre el óxido de aluminio y las microesferas de vidrio, adecuadas para procesos que requieren una mayor rugosidad superficial. Las bolas cerámicas se utilizan a menudo para desbarbar o reforzar la superficie de piezas metálicas, proporcionando una rugosidad uniforme y una buena durabilidad.
- Disparo de acero: Adecuada para la limpieza de superficies metálicas a gran escala, como el tratamiento anticorrosión de estructuras de acero. La granalla de acero es dura y resistente al desgaste, elimina eficazmente el óxido y los revestimientos viejos.
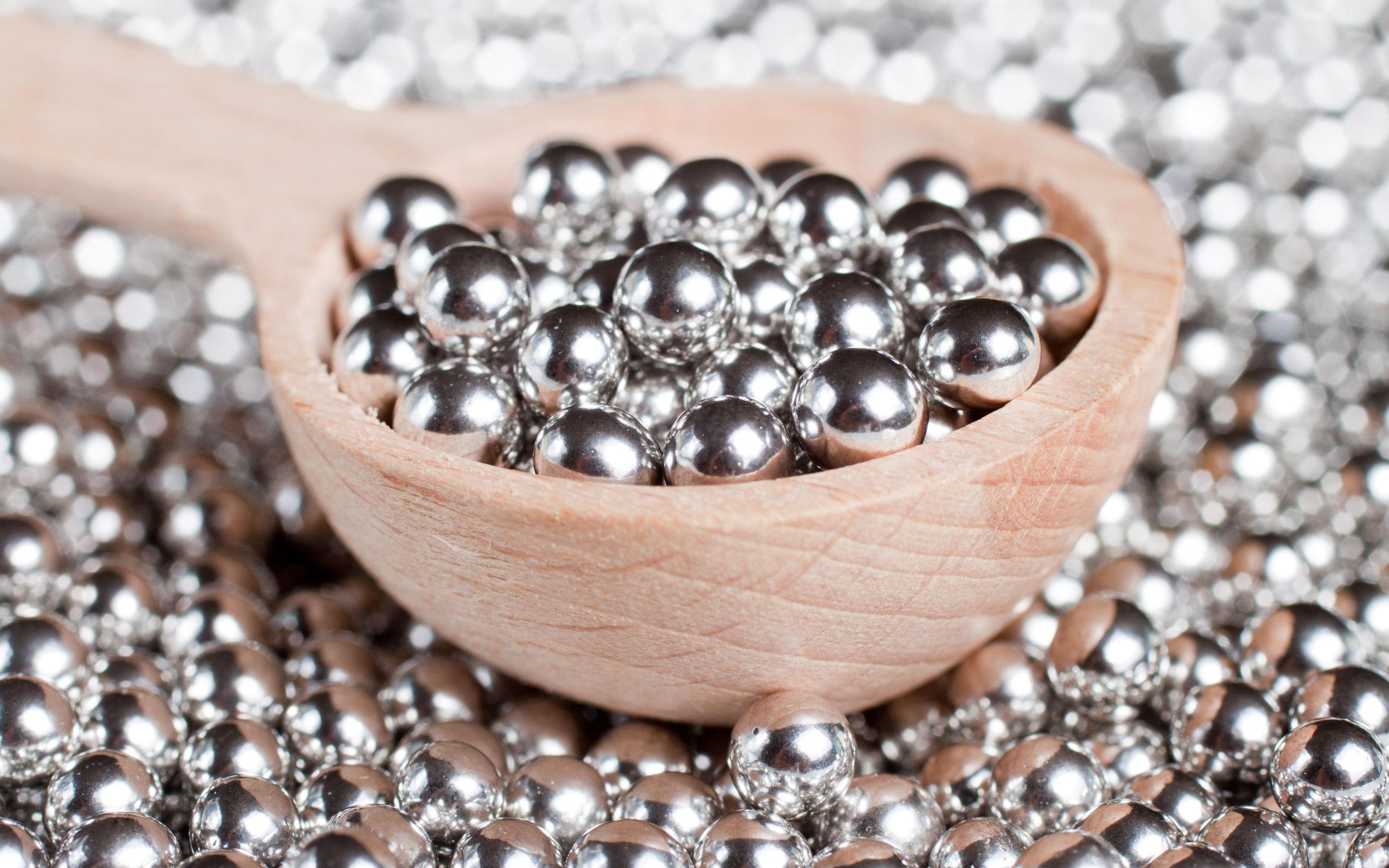
granalla de acero
3. Selección de equipos
La elección y la configuración del equipo de chorreado también influyen en el efecto del chorreado. Los principales tipos de equipos son:
- Equipos de chorreado a presión: Utiliza aire comprimido para suministrar abrasivos a la boquilla, adecuado para aplicaciones que requieren gran caudal y presión. El equipo suele incluir el control de la presión del aire, el almacenamiento del abrasivo y los componentes de la boquilla. Al ajustar, se regula la presión de chorreado, normalmente entre 4 y 8 bares, en función de los requisitos del tratamiento.
- Equipos de chorreado por succión: Utiliza el flujo de aire para arrastrar los abrasivos hacia la boquilla, adecuado para piezas más pequeñas u operaciones precisas. Al ajustar, regule el diámetro de la boquilla y el ángulo de chorreado, que suelen ser más flexibles y ajustables según sea necesario.
4. Configuración de los parámetros del equipo:
- Presión de chorro
La presión de chorreado es uno de los parámetros fundamentales del proceso de chorreado, ya que afecta directamente a la velocidad de chorreado y al efecto del tratamiento. La presión de chorreado suele medirse en unidades de presión (por ejemplo, psi o bar). En el proceso de chorreado, la presión de chorreado determina la fuerza de impacto de los abrasivos. Una mayor presión de chorreado aumenta la velocidad de los abrasivos, mejorando su impacto sobre la superficie de la pieza y la eficacia de la eliminación. Sin embargo, una presión de chorreado excesiva puede provocar un desgaste excesivo o incluso dañar las superficies más blandas o finas de la pieza.
- Diámetro de la boquilla
El diámetro de la boquilla determina el alcance de la pulverización y la uniformidad de los abrasivos. El diámetro de la boquilla suele medirse en milímetros. Los diámetros de boquilla más grandes (normalmente entre 6 y 12 mm) aumentan el área de cobertura y mejoran la eficacia del tratamiento, por lo que son adecuados para tareas de grandes superficies, como la eliminación de óxido de carrocerías metálicas o la limpieza de superficies de hormigón. Sin embargo, un diámetro de boquilla mayor puede provocar un chorreado desigual, especialmente en superficies más finas, lo que puede dar lugar a un tratamiento excesivo o insuficiente en algunas zonas.
- Ángulo de chorro
El ángulo de chorreado es otro parámetro importante en el proceso de chorreado, que se fija ajustando el soporte del equipo o la propia boquilla. El ángulo de chorreado afecta directamente a la dirección y uniformidad de los impactos del abrasivo. Normalmente, el ángulo de chorreado debe ajustarse en función de la geometría de la pieza y los requisitos de tratamiento para garantizar un tratamiento uniforme de la superficie. El ángulo puede influir en la finura del efecto de chorreado. Los ángulos de chorreado habituales oscilan entre 30° y 90°. Cuando la boquilla está perpendicular a la superficie de la pieza (90°), la fuerza de impacto de los abrasivos es mayor, lo que resulta adecuado para la limpieza a fondo de superficies planas. Este ángulo garantiza que los abrasivos golpeen uniformemente toda la superficie, especialmente en superficies grandes o uniformes; los ángulos de chorreado mayores (60°-90°) son adecuados para la limpieza a gran escala, pero pueden provocar un tratamiento local desigual; los ángulos de chorreado menores (30°-45°) son adecuados para el tratamiento detallado, proporcionando una mayor calidad superficial.
Ajustando con precisión estos parámetros, el proceso de chorreado puede lograr un tratamiento de superficies más eficaz y preciso, que satisfaga las necesidades de los distintos campos de aplicación. Comprender y dominar el ajuste de estos parámetros es crucial para optimizar los efectos del chorro de arena y mejorar la eficiencia de la producción.
Una cuidadosa atención a los trabajos de preparación anteriores garantiza la ejecución sin problemas del proceso de arenado, logrando el efecto de tratamiento deseado.
Proceso específico de arenado
- Ajuste de los parámetros de voladura:
- Ajuste de la presión: Discutir cómo ajustar la presión de chorreado en función del material de la pieza y el tipo de abrasivo, y las consecuencias de ajustar una presión demasiado alta o demasiado baja.
- Ángulo y distancia de voladura: Analizar la relación entre el ángulo de granallado y la planitud y rugosidad de la superficie de la pieza, así como el impacto de la distancia en los efectos del tratamiento.
- Velocidad de movimiento de la boquilla: Explique cómo afecta la velocidad de desplazamiento de la boquilla por la superficie de la pieza a la uniformidad y eficacia del chorreado.
- Posicionamiento y fijación de la pieza: Asegúrese de que la pieza permanece estable durante el chorreado para obtener un efecto de tratamiento superficial uniforme.
- Métodos y dispositivos habituales de fijación de piezas: (Véase la imagen de abajo)
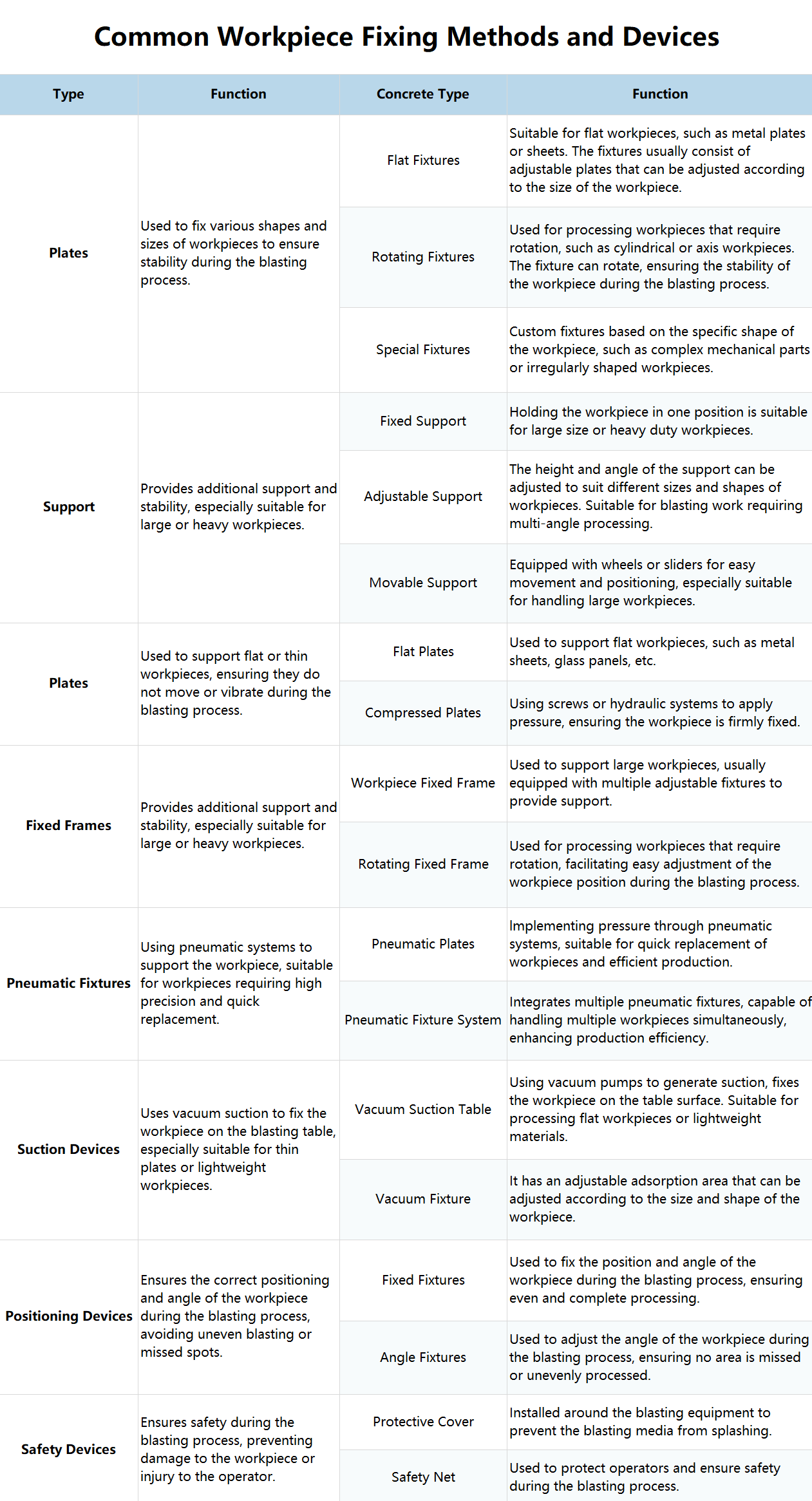
- Procedimiento de limpieza con chorro de arena:
- Iniciar voladura: Ponga en marcha el equipo de chorreado, aumente gradualmente la presión de chorreado hasta el valor ajustado. Comience a chorrear desde un extremo de la pieza y muévase gradualmente hacia el otro extremo, asegurándose de cubrir toda la superficie. Mantenga un movimiento suave de la boquilla, evite permanecer demasiado tiempo en una misma posición para evitar el desgaste excesivo, y asegúrese de cubrir toda la superficie, incluidos los bordes y las zonas de difícil acceso.
- Comprobar el estado de la superficie: Compruebe regularmente la superficie de la pieza durante el tratamiento para asegurarse de que presenta la rugosidad o limpieza deseadas. Ajuste la presión de chorreado, el ángulo de la boquilla o el diámetro de la boquilla según sea necesario en función de los resultados de la inspección para optimizar los efectos del tratamiento.
- Pases múltiples: Si es necesario, realice varias pasadas, especialmente en superficies complejas, donde el tratamiento paso a paso puede ser más eficaz.
- Tratamiento e inspección posteriores al chorreado:
- Limpieza posterior al chorreado: Utilice sopladores de aire, cepillos o aspiradoras para eliminar los residuos abrasivos y el polvo de la superficie de la pieza de trabajo. Compruebe cuidadosamente que no queden residuos abrasivos u otras impurezas en la superficie.
- Inspección y medición de superficies: Utilice instrumentos de medición de la rugosidad de la superficie para comprobar la calidad de la superficie de la pieza y asegurarse de que cumple los requisitos. Si el tratamiento de la superficie es desigual o incompleto, realice las reparaciones necesarias o un chorreado adicional.

El patrón del chorro de arena
Entre los instrumentos de detección comunes se incluyen:
- Instrumentos de medición de la rugosidad superficial: Incluye los medidores de rugosidad de tipo contacto (que registran las variaciones de la superficie mediante una sonda) y los medidores de rugosidad ópticos (que utilizan láseres o sistemas ópticos para medir la superficie sin contacto) para evaluar la rugosidad de la superficie de las piezas chorreadas mediante la comparación de los valores de ensayo con las normas establecidas.
- Rugosímetros: Incluye rugosímetros manuales (prácticos para el trabajo sobre el terreno y adecuados para diferentes formas de piezas de trabajo) y rugosímetros de sobremesa (adecuados para entornos de laboratorio, que proporcionan una mayor precisión de medición) para registrar los valores de rugosidad y compararlos con los requisitos de diseño.
- Perfilómetros: Se utiliza principalmente para medir los perfiles y las formas de la superficie de la pieza de trabajo a fin de garantizar la coherencia del tratamiento de arenado.
- Analizadores de tamaño de partículas abrasivas: Se utiliza para medir la distribución granulométrica de los medios de chorreado para garantizar que cumplen los requisitos.
- Manómetros: Mida la presión del aire o del fluido en el equipo de chorro de arena para asegurarse de que funciona dentro del rango establecido.
- Termómetros: Mida la humedad del entorno de chorreado para evitar que la humedad afecte a los efectos del chorreado y a la calidad del abrasivo.
- Caudalímetros de gas: Mida el caudal de gas durante el chorreado para garantizar efectos de chorreado estables.
- Comprobadores de desgaste: Medir el grado de desgaste de la superficie de la pieza por los abrasivos durante el chorreado para asegurar que el desgaste está dentro de los límites permitidos.
Mantenimiento del equipo de chorro de arena
- Limpie el equipo: Limpie regularmente el equipo de arenado, especialmente las boquillas y los tubos, para evitar que se obstruyan o desgasten.
- Comprobar el desgaste: Inspeccione diversas piezas del equipo de chorreado de arena, como las boquillas, los manómetros y las tuberías, para asegurarse de que funcionan correctamente.
- Sustituir boquillas: Sustituya las boquillas periódicamente en función del uso, especialmente cuando se deteriore el efecto del chorro de arena.
- Mantener el equipo: Realice el mantenimiento y la conservación de acuerdo con las recomendaciones del fabricante del equipo para garantizar la estabilidad y el rendimiento a largo plazo.
Problemas comunes en el proceso de arenado y sus soluciones
- Selección incorrecta del soporte: El uso de medios demasiado gruesos o demasiado finos puede provocar daños en la superficie o un tratamiento insuficiente. Por lo tanto, primero asegúrese de que la distancia y el ángulo entre la boquilla y la pieza de trabajo son coherentes, luego ajuste el diámetro de la boquilla para que el patrón de pulverización sea más uniforme y, por último, compruebe y limpie periódicamente el equipo de arenado para evitar obstrucciones o pulverizaciones irregulares.
- Desgaste y obstrucción de la boquilla: Las boquillas tienden a desgastarse con la pulverización a alta presión, lo que puede reducir la eficacia del chorro de arena y provocar una dispersión irregular del material. Utilice boquillas fabricadas con materiales resistentes al desgaste, como carburo de boro o carburo de tungsteno. Controle la presión de pulverización durante el uso para evitar el desgaste acelerado de la boquilla debido a una presión excesiva. No olvide comprobar periódicamente el estado de las boquillas y sustituir las que estén muy desgastadas.
- Presión insuficiente o fluctuante del equipo: Un control inadecuado de la presión de pulverización puede provocar un tratamiento desigual de la superficie o un mayor desgaste del equipo. Si es necesario, utilice un regulador de presión para controlar con precisión la presión de pulverización, evitando presiones demasiado altas o demasiado bajas. Ajuste la presión a un intervalo adecuado en función del material y la forma de la pieza. Compruebe también periódicamente el sistema de presión.
- Cuestiones de seguridad para operadores de arenado: Si los operarios no toman las medidas de seguridad adecuadas durante el chorreado de arena, pueden producirse lesiones personales. Para evitarlo, imparta a los operarios una formación completa sobre seguridad, haciendo hincapié en los procedimientos operativos y las medidas de protección. Asegúrese de que los operarios lleven el equipo de protección necesario, como guantes, gafas y ropa protectora, durante el funcionamiento del equipo.
- Baja eficacia de la recuperación de medios: Una baja eficiencia en la recuperación de los medios puede aumentar los costes de producción y afectar al medio ambiente. Optimice el sistema de recuperación del equipo de chorreado de arena para garantizar una recuperación eficaz del material después de su uso. Además, compruebe y limpie periódicamente el sistema de recuperación para evitar obstrucciones o daños, o utilice medios de alta calidad que puedan reciclarse varias veces.
Dominar el proceso de chorreado implica una preparación cuidadosa, una configuración exacta del equipo y un funcionamiento preciso. Conociendo y controlando los parámetros del chorreado de arena, como la presión, el diámetro de la boquilla y el ángulo, así como la inspección y el mantenimiento periódicos, puede conseguir resultados óptimos en el tratamiento de superficies. Ya sea para la limpieza, el desbarbado o el acabado de superficies, el dominio del proceso de chorreado de arena garantiza que cada operación cumpla las normas más estrictas, contribuyendo a la calidad y el rendimiento generales de la pieza de trabajo.
Filtros