Wie man Keramikbeschichtungen effizient entfernt?
Oktober 30, 2024
Im Bereich der Präzisionsfertigung ist die Frage, wie keramische Beschichtungen effizient entfernt werden können, ohne das Substrat zu beschädigen, eine große Herausforderung für die Kunden. Angesichts der zunehmenden Anwendung keramischer Beschichtungen in Branchen wie der Luft- und Raumfahrt, der Medizintechnik und der Automobilindustrie ist es besonders wichtig, die Oberflächenqualität und -konsistenz nach dem Entfernen der Beschichtung zu gewährleisten. Bei herkömmlichen Abtragsverfahren ist es schwierig, Effizienz, Umweltschutz und Präzision unter einen Hut zu bringen, was zu höheren Produktionskosten führt, das Substrat leicht beschädigt und die Leistung und Lebensdauer des Endprodukts beeinträchtigt. Daher ist die Wahl eines Verfahrens, mit dem sich Beschichtungen effizient, genau und sicher entfernen lassen, zu einem Problem geworden, das viele Branchen dringend lösen müssen.
Industrielle Nachfrage nach der Entfernung von Keramikbeschichtungen
- Anwendungsszenarien für keramische Beschichtungen
Keramische Beschichtungen sind in der Präzisionsfertigung weit verbreitet, insbesondere in Branchen wie der Luft- und Raumfahrt und der Automobilindustrie, um Teile vor extremen Umgebungsbedingungen wie Verschleiß, Korrosion und hohen Temperaturen zu schützen. Im Folgenden werden die spezifischen Anforderungen an keramische Beschichtungen in verschiedenen Anwendungen näher erläutert:
- Hohe Verschleißfestigkeit und Korrosionsbeständigkeit: So müssen beispielsweise Teile wie Turbinenschaufeln, Brennkammerinnenwände und Kolben in Automotoren in der Luft- und Raumfahrt häufig unter hohen Temperaturen und hohem Druck arbeiten. Keramische Beschichtungen verlängern die Lebensdauer der Teile, indem sie eine hochharte, chemikalienbeständige Schutzbarriere bilden.
- Thermische Barrierewirkung: In Umgebungen mit extrem hohen Temperaturen (z. B. Gasturbinen und Verbrennungsmotoren) können keramische Beschichtungen als thermische Barrieren fungieren und dazu beitragen, die Betriebstemperatur von Teilen aufrechtzuerhalten, die thermische Belastung zu verringern und die Leistungsstabilität zu verbessern.
- Vielfalt der industriellen Bedürfnisse: Keramische Beschichtungen werden nicht nur in der Luftfahrt- und Automobilindustrie verwendet, sondern auch bei Bohrgeräten in der Öl- und Gasindustrie, bei empfindlichen Teilen in der Elektronikindustrie usw. In diesen Bereichen steigt die Nachfrage nach der Entfernung keramischer Beschichtungen mit den Produkt-Upgrades und Wartungszyklen weiter an, und es werden präzisere Entfernungsmethoden benötigt, um die Leistung der Teile nach der Aktualisierung zu gewährleisten.
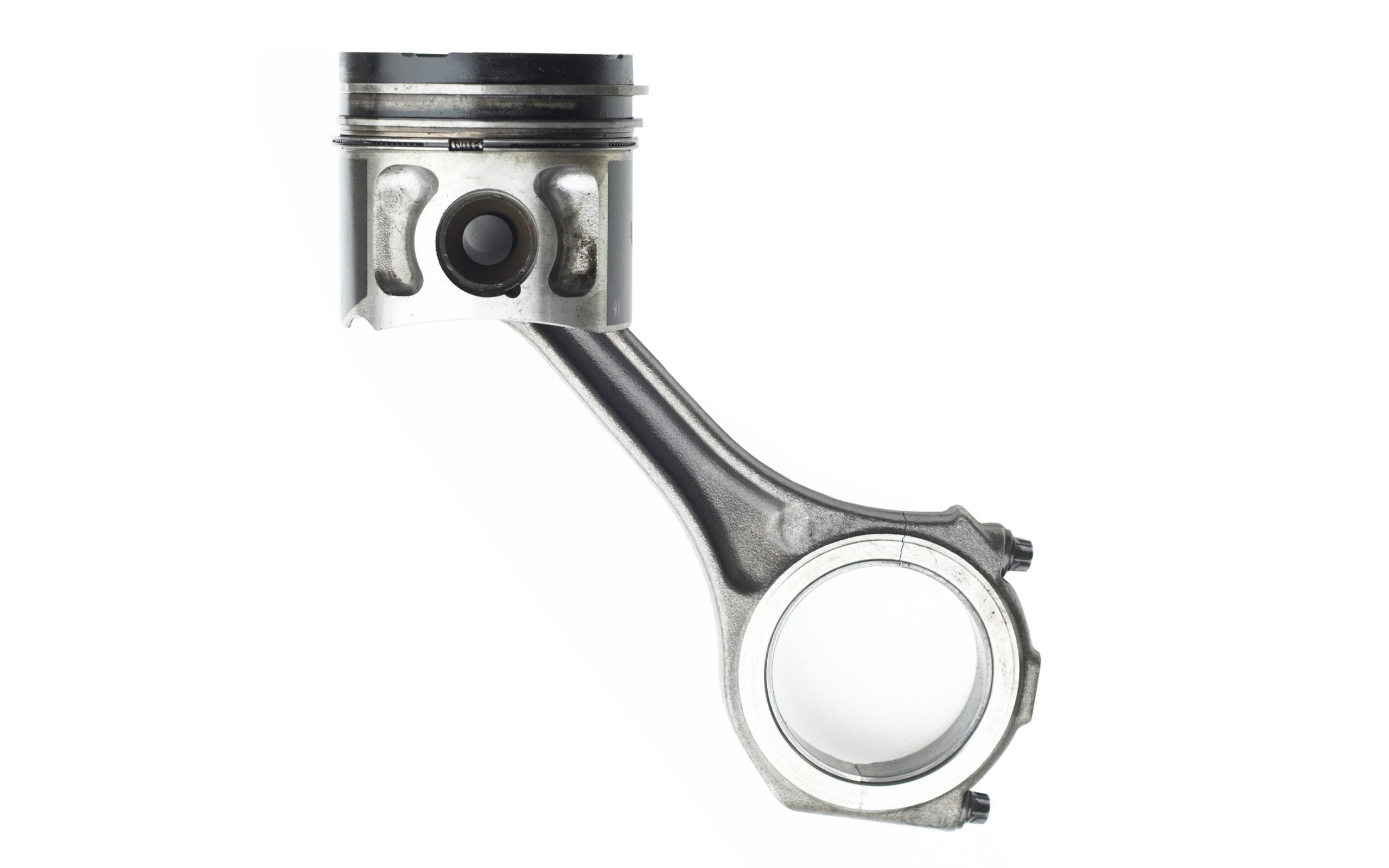
Motorkolben und Pleuelstange
- Schwierigkeiten bei der Entfernung alter Beschichtungen
Mit zunehmender Nutzungsdauer altert die keramische Beschichtung jedoch allmählich oder nutzt sich ab, wodurch sie ihre Schutzwirkung verliert oder sogar Risse bekommt, was die Funktion der Teile beeinträchtigt. Um die Lebensdauer der Teile zu verlängern, ist es daher notwendig, die alte Beschichtung zu entfernen und eine neue Beschichtung aufzutragen, aber in verschiedenen Branchen ist die Entfernung alter Beschichtungen oft nicht so einfach. Im Folgenden werden die wichtigsten Problembereiche erörtert:
- Haftungs- und Rückstandsprobleme bei alten Beschichtungen: Keramische Beschichtungen haben in der Regel eine starke Haftung und eine hohe Härte, was den Abtragsprozess erschwert. Mit herkömmlichen Methoden ist es schwierig, Rückstände vollständig zu entfernen, ohne das Substrat zu beschädigen, was die Gleichmäßigkeit der nachfolgenden Beschichtungen beeinträchtigen kann.
- Komplexe Formen und empfindliche Teile von Teilen: Triebwerksschaufeln von Flugzeugen, Teile von Automotoren usw. haben oft komplexe geometrische Formen, und beim Entfernen der Beschichtung können kleine Strukturen oder scharfe Ecken leicht beschädigt werden.
- Unterschiede in Dicke und Material: Die Dicke, die Härte und das Material der Beschichtung variieren, was höhere Anforderungen an den Entfernungsprozess stellt. Es ist notwendig, die geeignete Entfernungsmethode zu wählen, um die beste Wirkung zu erzielen.
- Hohe Standards für die Entfernung keramischer Beschichtungen in der Präzisionsfertigung
Besonders in der Präzisionsfertigung sind die Oberflächenqualität und der Schutz des Substrats der Teile von entscheidender Bedeutung, so dass strenge Anforderungen an den Entschichtungsprozess gestellt werden.
- Die Notwendigkeit, den Untergrund zu schützen: In Industriezweigen wie der Luft- und Raumfahrt und der Medizintechnik besteht das Substrat von Teilen in der Regel aus teuren Hochleistungsmetallen oder -legierungen, und eine unsachgemäße Entfernung kann zu Schäden am Substrat führen. Insbesondere bei der Verbrennungskammer oder den Leitschaufeln eines Triebwerks wird die Leistung und Sicherheit der Teile beeinträchtigt, wenn die Festigkeit des Substrats beim Entfernen der Beschichtung geschwächt wird.
- Effizienz und Kostenkontrolle: Herkömmliche Verfahren zur Entfernung von Beschichtungen sind oft zeit- und kostenaufwändig und können dazu führen, dass sich Teile verformen oder durch Hitze verunreinigt werden. Moderne Fertigungsunternehmen benötigen ein Verfahren, das eine effiziente Beschichtungsentfernung gewährleistet und das Substrat schützt, um Produktionszyklen zu verkürzen und Wartungskosten zu senken.
Vorteile des Sandstrahlens bei der Entfernung von Keramikbeschichtungen
Im industriellen Bereich hat sich das Sandstrahlen allmählich zu einer wichtigen Methode zur Entfernung von Keramikbeschichtungen entwickelt. Seine Vorteile liegen vor allem in der präzisen Kontrolle, dem Umweltschutz und der Anpassungsfähigkeit an komplexe Formen. Im Folgenden werden die wichtigsten Merkmale des Sandstrahlens und die verschiedenen Abtragsverfahren im Detail beschrieben.
- Merkmale des Sandstrahlens
- Präzise Kontrolle des Dickenabtrags: Bei der Entfernung keramischer Beschichtungen kann das Sandstrahlen je nach Dicke der Beschichtung sowie der Art und Komplexität des Substrats präzise arbeiten. Durch die Einstellung von Sandstrahldruck, Durchflussmenge und -winkel kann beispielsweise die Dicke des Abtrags wirksam gesteuert werden. Insbesondere bei der Entfernung dünner Beschichtungen vermeidet diese Präzision das Risiko einer übermäßigen Abnutzung des Substrats.
- Umweltfreundlich und frei von Chemikalien: Im Vergleich zu chemischen Lösungsmittel-Entfernungsmethoden beruht das Sandstrahlen ausschließlich auf physikalischen Einwirkungen, um keramische Beschichtungen zu entfernen, wodurch die chemische Belastung der Umwelt reduziert wird. Sandstrahlen eignet sich besonders für Branchen mit hohen Umweltschutzanforderungen, wie die Luft- und Raumfahrtindustrie und die Herstellung medizinischer Geräte.
- Anpassung an komplexe Formen: Herkömmliche mechanische Abtrags- oder chemische Auflösungsmethoden haben das Problem der geringen Effizienz und der unzureichenden Kantenbearbeitung, wenn es um komplexe Teileformen geht. Die Flexibilität des Sandstrahlverfahrens ermöglicht es, diese Herausforderungen problemlos zu meistern. So können beispielsweise spezielle strukturelle Oberflächen wie Klingen, scharfe Ecken und innere Hohlräume gleichmäßig abgetragen werden, und die menschliche Fehlerquote ist gering, was für standardisierte Bearbeitungsanforderungen in der Massenproduktion geeignet ist.
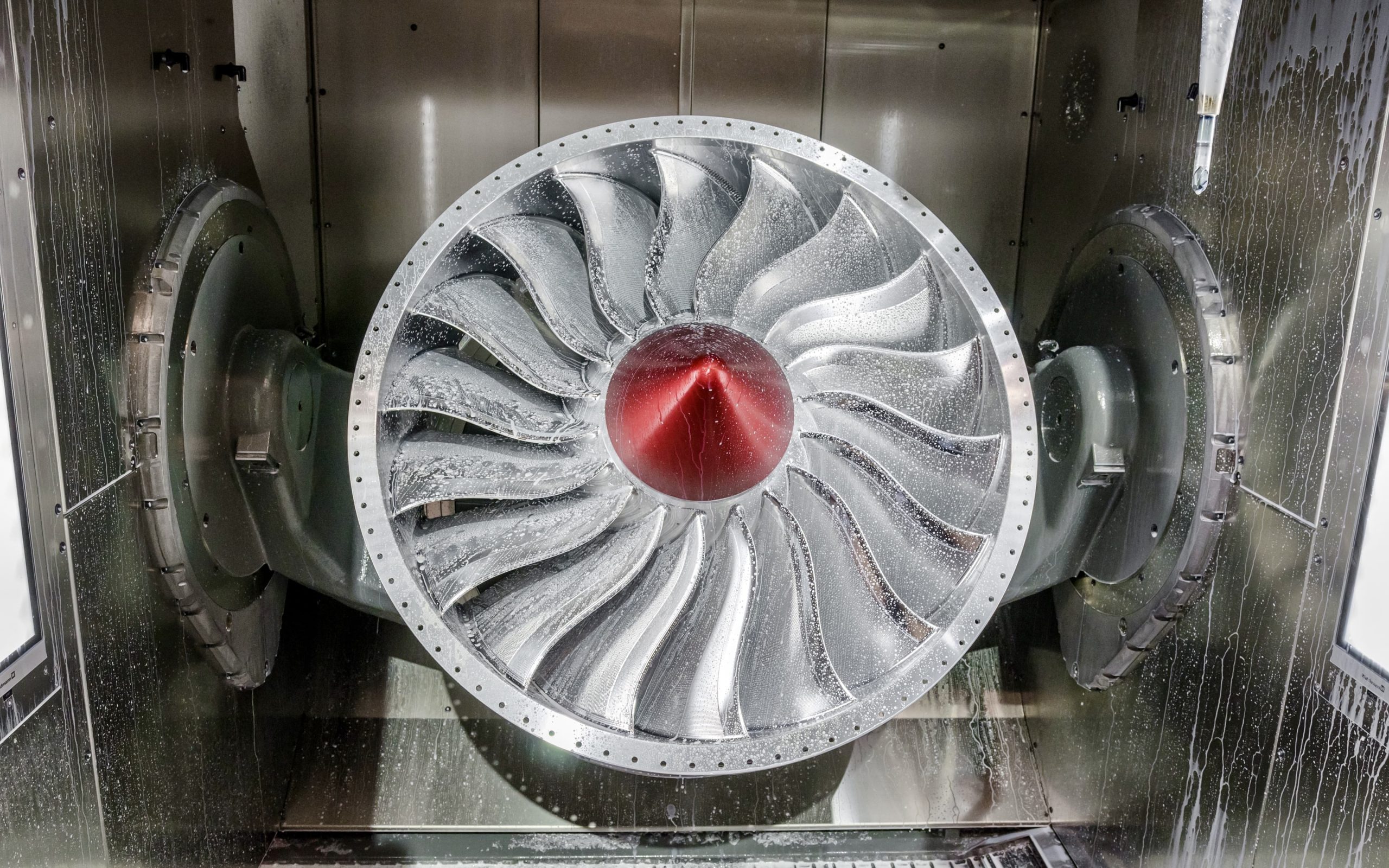
.
- Effizienz der Sandstrahlentfernung
Im Vergleich zu herkömmlichen mechanischen Schleif- und chemischen Lösungsmittelentfernungsmethoden hat das Sandstrahlverfahren offensichtliche Vorteile hinsichtlich Geschwindigkeit und Qualitätskontrolle:
- Schnelle Entfernung von Beschichtungen: Beim Sandstrahlen wird die Beschichtung durch Hochgeschwindigkeitsaufprall von Partikeln auf der Oberfläche abgeschält. Im Vergleich zur chemischen Entfernung spart es Bearbeitungszeit und vermeidet den langen Prozess des Eintauchens und Auflösens der Beschichtung. Es eignet sich für Produktionslinien mit hohen Anforderungen an die Abtragseffizienz.
- Reduzieren Sie die thermische Belastung des Werkstücks: Die beim Sandstrahlen verwendeten Partikel haben eine niedrigere Temperatur und erzeugen keine thermische Belastung des Substrats, wodurch die Genauigkeit und strukturelle Integrität der Teile gewährleistet wird.
- Entfernungslösungen für unterschiedliche Dicken
Mit dem Sandstrahlverfahren kann durch die Auswahl verschiedener Strahlmittel eine effiziente Entfernung von Beschichtungen unterschiedlicher Dicke erreicht werden. In der industriellen Praxis gibt es folgende Optimierungslösungen für dünne und dicke Keramikbeschichtungen:
- Entfernung von dünnen Keramikbeschichtungen: Feinkörnige Sandstrahlmittel (wie z. B. Ultrafeines Aluminiumoxid-Strahlmittel) kann die Dicke des Abtrags genau steuern, was sich besonders für kleinere Reparaturen von Präzisionsteilen eignet. Aluminiumoxidpartikel sind hart und fein und erzeugen eine schwache, aber stabile Schlagkraft auf dünne Beschichtungen, wodurch sich die Beschichtung allmählich ablöst, ohne die Mikrostruktur des Substrats zu beeinträchtigen.
- Entfernung von dicken Keramikbeschichtungen: Dicke keramische Beschichtungen erfordern in der Regel höherfeste Sandstrahlmittel (z. B. Siliziumkarbid), die eine starke Schneidfähigkeit und hohe Verschleißfestigkeit aufweisen. Durch schichtweises Abtragen können Schlagschäden am Substrat durch großflächiges Abblättern vermieden werden, was für Werkstücke mit hohen Anforderungen an Hitzebeständigkeit und Härte geeignet ist. Darüber hinaus ermöglichen die Härte und Schärfe der Siliziumkarbidpartikel, dass jeder Schlag genau die vorgegebene Dicke abträgt, wodurch die Abtragseffizienz verbessert wird.
Sandstrahlmittel für die Entfernung von Keramikbeschichtungen geeignet
Um die Anforderungen an die Entfernung keramischer Beschichtungen unterschiedlicher Dicke und Materialien zu erfüllen, ist die Auswahl geeigneter Sandstrahlmittel entscheidend. Die Eigenschaften des Sandstrahlmittels bestimmen die Effizienz des Abtragsprozesses, die Schutzwirkung des Substrats und den Grad der Veredelung. Im Folgenden werden vier häufig verwendete Sandstrahlmittel im Detail vorgestellt und ihre jeweiligen Vor- und Nachteile sowie typische Anwendungsszenarien analysiert.
- Tonerde
- Grundlegende Merkmale: Aluminiumoxid ist weiß oder braun, meist in Form von kantigen Partikeln, mit hoher Härte und guter Verschleißfestigkeit. Die scharfen Kanten der Aluminiumoxidpartikel eignen sich zum Entfernen dünnerer keramischer Beschichtungen und sorgen für eine stabile Schlagkraft bei gleichzeitiger Vermeidung von übermäßigem Verschleiß des Substrats.
- Anwendungsszenarien: In anspruchsvollen Branchen wie der Luft- und Raumfahrt und der Automobilindustrie wird Aluminiumoxid-Sandstrahlen häufig für kleinere Reparaturen von Präzisionsteilen eingesetzt. Wenn zum Beispiel die Beschichtung ungleichmäßig abgenutzt ist oder neu lackiert werden muss, kann Aluminiumoxid die alte Beschichtung auf der Oberfläche gleichmäßig entfernen, ohne die Ebenheit des Substrats zu beeinträchtigen. Diese Eigenschaft macht es effizient und kontrollierbar bei der Entfernung dünner Beschichtungen, besonders geeignet für die Notwendigkeit einer detaillierten Oberflächenbehandlung von Teilen, wie z. B. die Oberflächenreinigung und das Aufrauen von Kleinteilen. Nach der Verwendung von Aluminiumoxid zum Entfernen dünner Schichten keramischer Beschichtungen kann die Oberfläche des Werkstücks relativ glatt bleiben, und das Substrat wird kaum beeinträchtigt, was den strengen Anforderungen der Präzisionsfertigungsindustrie an den Substratschutz entspricht.
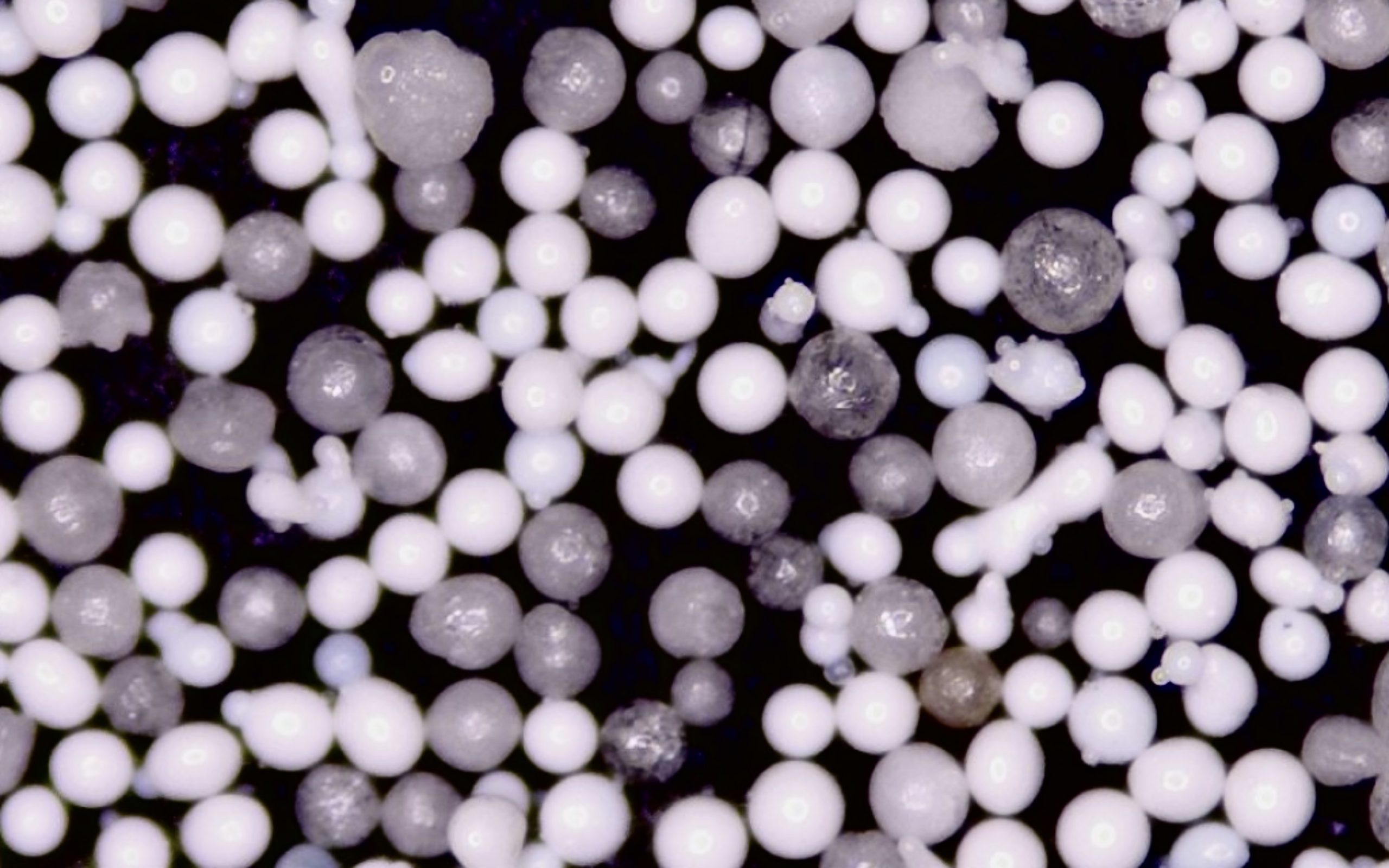
Ultrafeines Aluminiumoxid-Strahlmittel von HLH
- Siliziumkarbid
- Grundlegende Merkmale: Siliziumkarbid ist dunkelgrau oder schwarz, hat scharfe Partikel und eine höhere Härte als Aluminiumoxid. Durch seine extrem hohe Schneidkraft eignet es sich hervorragend zum Entfernen dicker Beschichtungen. Es eignet sich besonders für die Oberflächenbehandlung von hochtemperaturbeständigen und hochharten Teilen und kann dicke Keramikbeschichtungen schnell ablösen.
- Anwendungsszenarien: Siliziumkarbid wird häufig in der Luftfahrt, bei der Energieerzeugung und in anderen Industriezweigen eingesetzt, die häufig hohen Temperaturen ausgesetzt sind. In der Vergangenheit war die herkömmliche mechanische Entfernung von dicken Beschichtungen oft zeitaufwändig und verursachte große Schäden am Substrat, während Siliziumkarbid keramische Beschichtungen Schicht für Schicht auf effiziente Weise entfernen kann, insbesondere bei thermischen Spritz- oder Galvanikbeschichtungen. Durch das Entfernen dicker Beschichtungen mit Siliziumkarbid wird die Oberfläche des Werkstücks glatt und das Substrat in hohem Maße intakt, was den Oberflächenanforderungen komplexer Formen und hochharter Materialien entspricht. Die Härte und Stabilität von Siliziumkarbid gewährleistet eine hohe Abtragsgeschwindigkeit und verhindert eine sekundäre Abnutzung des Substrats, wodurch die Anforderungen an die Wiederaufbereitung von Teilen mit hohem Standard erfüllt werden.
- Glasperlen
- Grundlegende Merkmale: Glasperlen sind durchsichtige bis durchscheinende, runde Partikel mit relativ mäßiger Härte, die sich für die sanfte Entfernung von leichten Beschichtungen eignen. Ihre runde Partikelstruktur kann eine relativ gleichmäßige Aufprallkraft auf der Oberfläche erzeugen, wodurch eine Beschädigung des Substrats durch scharfe Kanten vermieden wird.
- Anwendungsszenarien: Glasperlen werden häufig für medizinische Geräte und kleine Präzisionsteile verwendet. Bei Teilen mit zerbrechlichen Materialien oder extrem hohen Oberflächenanforderungen können Glasperlen eine schonende Entfernung gewährleisten. Bei der Wiederaufbereitung medizinischer Geräte beispielsweise kann die Verwendung von Glasperlen zur Entfernung alter Beschichtungen Schäden am Gerät selbst vermeiden und die Integrität und Glätte des Substrats erhalten. Die Oberflächenstruktur nach dem Entfernen der Glasperlen ist fein und glatt, ohne offensichtliche Kratzer, was für Präzisionsteile mit hohen Anforderungen an die Oberflächengüte geeignet ist und eine gute Grundlage für die nachfolgende Bearbeitung bietet.
- Keramische Perlen
- Grundlegende Merkmale: Keramikkugeln sind im Allgemeinen weiß oder grau, haben eine relativ runde und glatte Partikelform und eine mittlere Härte und Zähigkeit. Es hat eine ausgezeichnete Hochtemperaturbeständigkeit und hat eine gute Wirkung bei der Entfernung von harten keramischen Beschichtungen.
- Anwendungsszenarien: Keramikkugeln werden häufig für Teile mit hohen Anforderungen an die Oberflächenqualität verwendet, insbesondere in der Automobil- und Elektronikindustrie. Im Vergleich zu Aluminiumoxid und Siliziumkarbid haben Keramikkugeln eine relativ milde Schlagkraft, die sich zum Entfernen von Beschichtungen eignet, wobei die Oberfläche intakt bleibt und der Aufprall auf feine Strukturen vermieden wird. In Situationen, in denen höhere Anforderungen an die Oberflächengüte und -gleichmäßigkeit gestellt werden, können Keramikkugeln eine stabile Abtragswirkung erzielen und die Oberflächenrauhigkeit des Werkstücks verringern. Die Oberfläche des Werkstücks nach dem Abtragen durch Keramikkugeln ist glatt und weist eine hohe Konsistenz auf. Sie bildet die Grundlage für die Verbesserung des Aussehens und der Leistung des Produkts und eignet sich für die Bearbeitung hochwertiger Unterhaltungselektronik und anspruchsvoller Automobilteile.
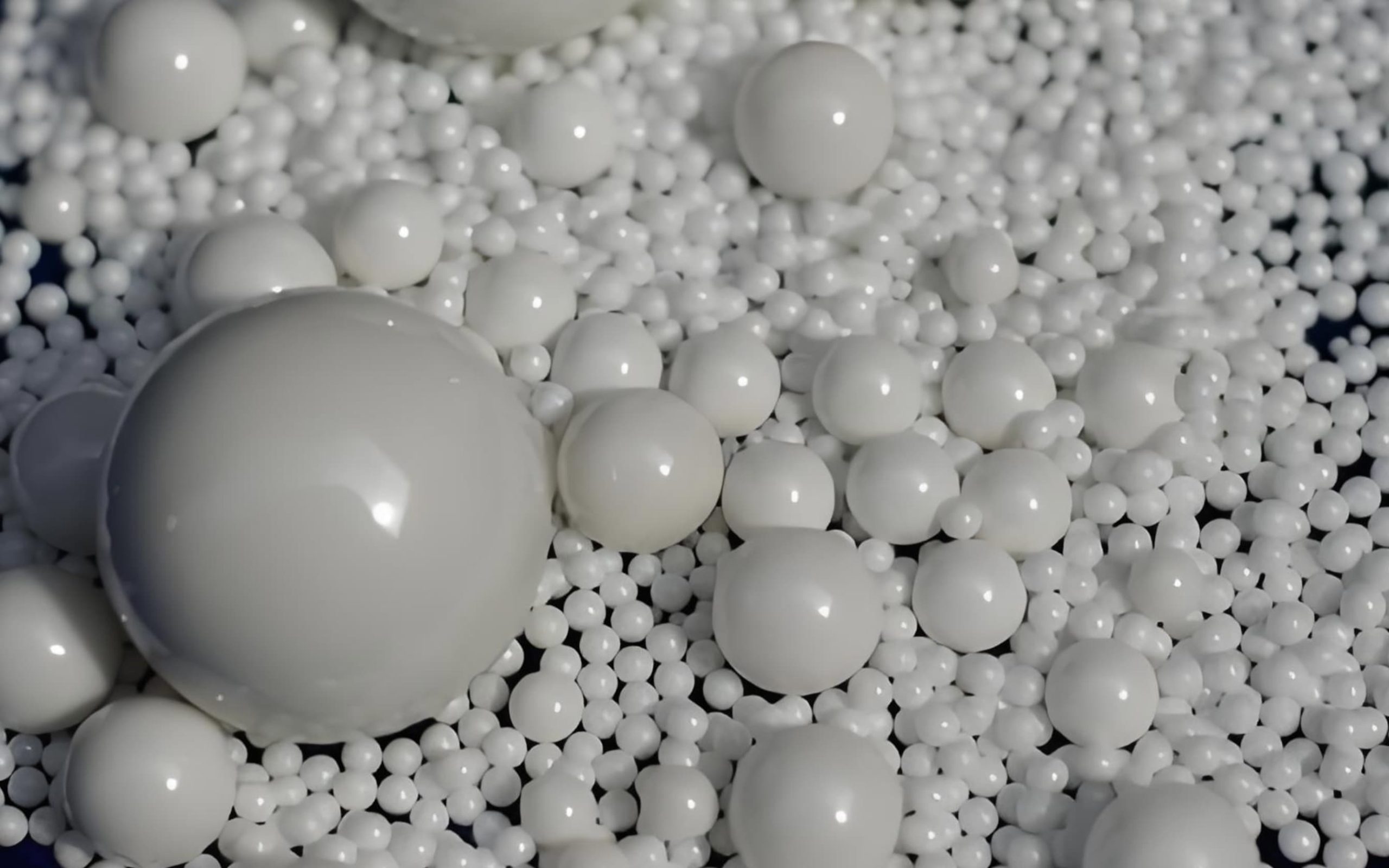
Keramische Perlen von HLH
Die Sandstrahltechnik bietet offensichtliche Vorteile bei der Entfernung von Keramikbeschichtungen. Durch die Auswahl des richtigen Sandstrahlmittels können Genauigkeit, Geschwindigkeit und Umweltfreundlichkeit der Beschichtungsentfernung gewährleistet und gleichzeitig die Integrität des Substrats wirksam geschützt werden. Diese flexible Oberflächenbehandlungsmethode bietet nicht nur eine zuverlässige Lösung für die Entfernung von Beschichtungen, sondern erfüllt auch die unterschiedlichsten industriellen Anforderungen. Im Folgenden finden Sie eine Zusammenfassung der wichtigsten Vorteile der Sandstrahltechnologie bei der Entfernung von Beschichtungen:
- Effizient und kontrollierbar: Die Vielfalt der Sandstrahlmittel ermöglicht es, sowohl leichte dünne Beschichtungen als auch starke dicke Beschichtungen zu entfernen und so eine präzise Oberflächenbehandlung zu erreichen.
- Umweltfreundlich und schadstofffrei: Im Vergleich zu herkömmlichen chemischen Entfernungsmethoden vermeidet die Sandstrahltechnik den Einsatz schädlicher Chemikalien und verringert das Risiko der Umweltverschmutzung.
- Breite Anwendbarkeit: Die Auswahl an Sandstrahlmitteln passt sich an eine Vielzahl von Substraten und komplexen Strukturen an und eignet sich daher für den Einsatz in zahlreichen Branchen wie Luftfahrt, Medizintechnik, Elektronik und Automobilbau, was sie zu einer idealen Wahl für die Präzisionsfertigung macht.
- Gewährleistung der Sicherheit des Substrats: Während die Beschichtungen effektiv entfernt werden, kann das Sandstrahlverfahren die ursprünglichen Eigenschaften des Substrats beibehalten, was besonders für Branchen mit strengen Schutzanforderungen an das Substrat geeignet ist.
- Entspricht den Industrienormen: Das Sandstrahlverfahren kann den hohen Anforderungen der Industrie an Präzisionsteile gerecht werden, erfüllt die einheitlichen Standards für Sicherheit und Oberflächenqualität und ist eine wichtige Methode zur Entfernung von Beschichtungen bei der Bearbeitung in verschiedenen Branchen.
Die kontinuierliche Weiterentwicklung der Sandstrahltechnologie zur Entfernung keramischer Beschichtungen und die Innovation von Sandstrahlmitteln haben es der Präzisionsfertigung ermöglicht, höhere technische Anforderungen zu erfüllen und die Kosten zu kontrollieren. Mit der eingehenden Anwendung der Sandstrahltechnologie werden die Auswahl verschiedener Sandstrahlmittel und ihre Optimierungslösungen weiterhin eine unersetzliche Rolle bei der Entfernung keramischer Beschichtungen spielen und die Produktqualität und Produktionseffizienz in allen Bereichen des Lebens begleiten.
Filter