27. September 2024
Das Sandstrahlverfahren ist eine weit verbreitete Technologie zur Oberflächenbehandlung, die hauptsächlich zum Reinigen, Entgraten, Schleifen und Polieren verschiedener Materialien wie Metalle, Kunststoffe und Keramiken eingesetzt wird. Mit der zunehmenden Industrialisierung hat das Sandstrahlverfahren in der Fertigungsindustrie immer mehr an Bedeutung gewonnen, insbesondere in den Bereichen Luft- und Raumfahrt, Automobilbau, Elektronik und Medizintechnik. Einige Probleme, die beim Sandstrahlverfahren auftreten, wie z. B. Farb-, Glanz- und Rauheitsunterschiede, beeinträchtigen jedoch die Qualität des Erscheinungsbildes und die Wettbewerbsfähigkeit der Produkte erheblich.
Unter Farbunterschied versteht man den offensichtlichen Farbunterschied zwischen einer Charge von Produkten. Dieses Phänomen beeinträchtigt nicht nur die Ästhetik des Produkts, sondern kann auch zur Unzufriedenheit der Kunden und zu Rückgaben führen. Ungleichmäßiger Glanz lässt das Produkt optisch unprofessionell erscheinen, während ungleichmäßige Rauheit die Leistung des Produkts beeinträchtigen kann, insbesondere in Branchen mit strengen Anforderungen an die Oberflächenqualität. Diese Situationen sind sehr ernst. Daher sind das Verständnis der Ursachen für diese Probleme und die Suche nach Lösungen ein wichtiges Thema für die Verbesserung des derzeitigen Sandstrahlverfahrens geworden.
In diesem Artikel werde ich mich eingehend mit der Ursachen für Farb-, Glanz- und Rauhigkeitsunterschiede im Sandstrahlverfahren, die Analyse der erfolgreichen Fälle von Unternehmen bei der Bewältigung dieser Probleme und die Abhilfemaßnahmen, die ergriffen werden, wenn sie nicht vollständig überwunden werden können. Durch systematische Analyse und Forschung sollen praktische Vorschläge und Hinweise für die betreffenden Unternehmen gegeben und die kontinuierliche Verbesserung und Innovation des Sandstrahlprozesses gefördert werden.
Ursachen für das Problem der Farbunterschiede
Farbunterschiede sind ein häufiges Problem im Sandstrahlverfahren, insbesondere bei Produkten mit hohen ästhetischen Anforderungen. Das Verständnis der Ursachen für Farbunterschiede ist entscheidend für die Verbesserung des Sandstrahleffekts und der Produktqualität.
Unterschiede bei den Rohstoffen
Material aus unterschiedlichen Chargen oder Quellen kann Farbunterschiede aufweisen, was eine der Hauptursachen für Probleme mit Farbunterschieden ist. So können beispielsweise unterschiedliche Produktionsverfahren, Rezepturen und Lagerbedingungen desselben Materials die Farbe des Materials beeinflussen. Darüber hinaus können auch Änderungen in der Zusammensetzung von Rohstoffen, wie z. B. Art und Anteil von Zusatzstoffen, zu Unterschieden in der Farbe des Endprodukts führen. Daher ist die Sicherstellung der Einheitlichkeit von Herkunft und Zusammensetzung der Rohstoffe entscheidend für die Verringerung von Farbunterschieden.
Auswahl der Sandstrahlmittel
Die Art und die Eigenschaften des Sandstrahlmittels wirken sich direkt auf die Oberflächenfarbe nach dem Sandstrahlen aus. So können beispielsweise Aluminiumoxid-Strahlmittel und keramische Strahlmittel unterschiedliche Oberflächenglanz und -farben erzeugen. Die Härte, Form und Partikelgröße des Strahlmittels wirken sich auf die Reibung und die Oberflächenrauheit beim Sandstrahlen aus und beeinflussen so die Gleichmäßigkeit der Farbe. Daher sollte bei der Auswahl des Sandstrahlmittels dessen Einfluss auf die endgültige Farbe berücksichtigt werden.
Änderungen der Prozessparameter
Änderungen der Parameter des Strahlprozesses, wie z. B. Strahldruck, Abstand und Winkel, können die Oberflächenwirkung nach dem Strahlen ebenfalls erheblich beeinflussen. Ein zu hoher oder zu geringer Strahldruck kann zu einer ungleichmäßigen Oberflächenbehandlung und damit zu Farbunterschieden führen. Wenn beispielsweise der Strahlabstand zu gering ist, kann dies in einigen Bereichen zu übermäßigem Verschleiß führen, und unterschiedliche Strahlwinkel (Wir haben schon einmal darüber geschrieben, zum Ansehen klicken) können unterschiedliche Aufprallkräfte des Strahlmittels auf die Oberfläche verursachen, was zu ungleichmäßigen Farben führt. Daher ist es sehr wichtig, standardisierte Strahlparameter festzulegen.
Umweltfaktoren
Umgebungsfaktoren wie Feuchtigkeit, Temperatur und Licht wirken sich ebenfalls auf den Farbunterschied beim Strahlen aus. Eine hohe Luftfeuchtigkeit kann die Hygroskopizität des Strahlmittels erhöhen, wodurch sich seine physikalischen Eigenschaften verändern und die Strahlwirkung beeinträchtigt wird. Darüber hinaus können Temperaturschwankungen zu einer thermischen Ausdehnung des Materials führen, wodurch sich seine Farbwirkung verändert. Unterschiedliche Lichtverhältnisse können sich ebenfalls auf die visuelle Farbbeurteilung auswirken, so dass die Umgebungsfaktoren während des Strahlprozesses so weit wie möglich kontrolliert werden sollten, um einen gleichmäßigen Verarbeitungseffekt zu erzielen.
Nachfolgend zeige ich die Auswirkungen verschiedener Strahlmethoden (wie Trocken- und Nassschleifen) und ihre Auswirkungen auf Farbunterschiede und Glanz, damit Sie verstehen, wie wichtig es ist, die richtige Methode zu wählen.
Nachfolgend zeige ich die Auswirkungen verschiedener Strahlmethoden (wie Trocken- und Nassschleifen) und ihre Auswirkungen auf Farbunterschiede und Glanz, damit Sie verstehen, wie wichtig es ist, die richtige Methode zu wählen.
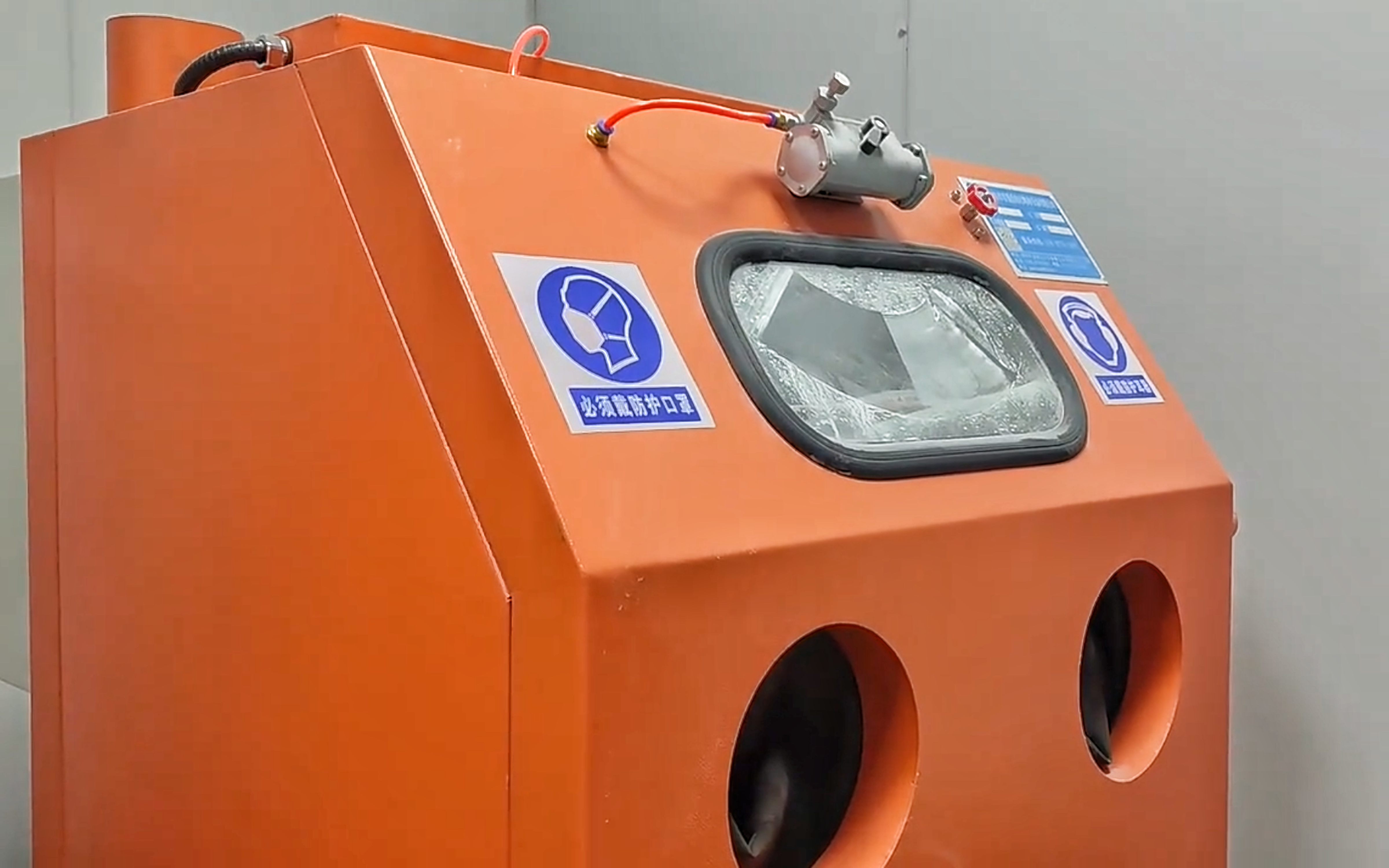
Nass-Sandstrahlgerät
Überblick über Sandstrahlverfahren
Trockenes Sandstrahlen
- Eigenschaften: Verwenden Sie trockene Sandstrahlmittel, geeignet für eine Vielzahl von Materialien.
- Vorteile: Gute Wirkung beim Entfernen von Graten und Schmutz, geeignet für Metallwerkstücke.
- Benachteiligungen: Kann hohe Oberflächenrauhigkeit verursachen und das Risiko von Farbunterschieden erhöhen.
Nasses Sandstrahlen
- Merkmale: Mischen Sie Wasser mit Sandstrahlmitteln, um Staub und Streuung zu reduzieren.
- Vorteile: Geeignet für Werkstücke mit hohen Anforderungen an die Oberflächengüte, und kann die Rauheit effektiv kontrollieren.
- Nachteilig: Die Wartung der Geräte und die Verarbeitung sind komplizierter, und die Trocknungszeit ist länger.
Glanz und Rauheit
- Trockenes Sandstrahlen
Aufgrund der verwendeten trockenen Medien kann es beim Sandstrahlen zu ungleichmäßigem Verschleiß kommen, was zu Farbunterschieden führt, insbesondere bei glatten Oberflächen.
Geeignet für Anwendungen, bei denen kein Farbunterschied erforderlich ist, aber eine nachträgliche Bearbeitung bei anspruchsvollen Anwendungen erforderlich sein kann.
- Nasses Sandstrahlen
Die statische Elektrizität, die beim trockenen Sandstrahlen entsteht, wird durch den Einsatz von Wasser reduziert und kann sich gleichmäßiger auf der Oberfläche des Werkstücks verteilen, wodurch die Möglichkeit von Farbunterschieden verringert wird.
Geeignet für Produkte, die eine hohe Konsistenz erfordern, wie z. B. medizinische Geräte oder elektronische Bauteile.
Farbunterschiedseffekt
- Trockenes Sandstrahlen
Aufgrund der hohen Verschleißkraft kann die Oberflächenrauheit zunehmen und der Glanz abnehmen.
Nicht geeignet für Werkstücke, die eine glatte Oberflächenbehandlung erfordern, wie z. B. hochglänzende dekorative Teile.
- Nasses Sandstrahlen
Durch die Verringerung der Dispersion des Mediums und die Verbesserung der Oberflächenbenetzbarkeit können nach dem Sandstrahlen ein guter Glanz und eine geringe Rauheit erhalten werden.
Nasses Sandstrahlen eignet sich gut für Industrien, die hohen Glanz und geringe Rauheit erfordern.
Anwendbare Anlässe
- Trockenes Sandstrahlen
Geeignet für die Reinigung und Entgratung von Metalloberflächen, häufig in der Schwerindustrie eingesetzt.
Nicht geeignet für Produkte mit strengen Anforderungen an das Aussehen.
- Nasses Sandstrahlen
Besser geeignet für Produkte mit hohen Anforderungen an die Oberflächenqualität, wie z. B. Präzisionsteile, Kunstwerke und medizinische Geräte.
Geeignet für Industrien mit hohen Anforderungen an die Oberflächengüte und Konsistenz der Werkstücke.
Zusammenfassend lässt sich sagen, dass bei Produkten, die einen hohen Glanz und eine geringe Rauheit erfordern, das Nasssandstrahlen möglicherweise mehr Vorteile bietet, während das Trockensandstrahlen gewisse Effizienz- und Kostenvorteile aufweist. Es ist entscheidend, das richtige Sandstrahlverfahren entsprechend den spezifischen Produktanforderungen und Industrienormen zu wählen.
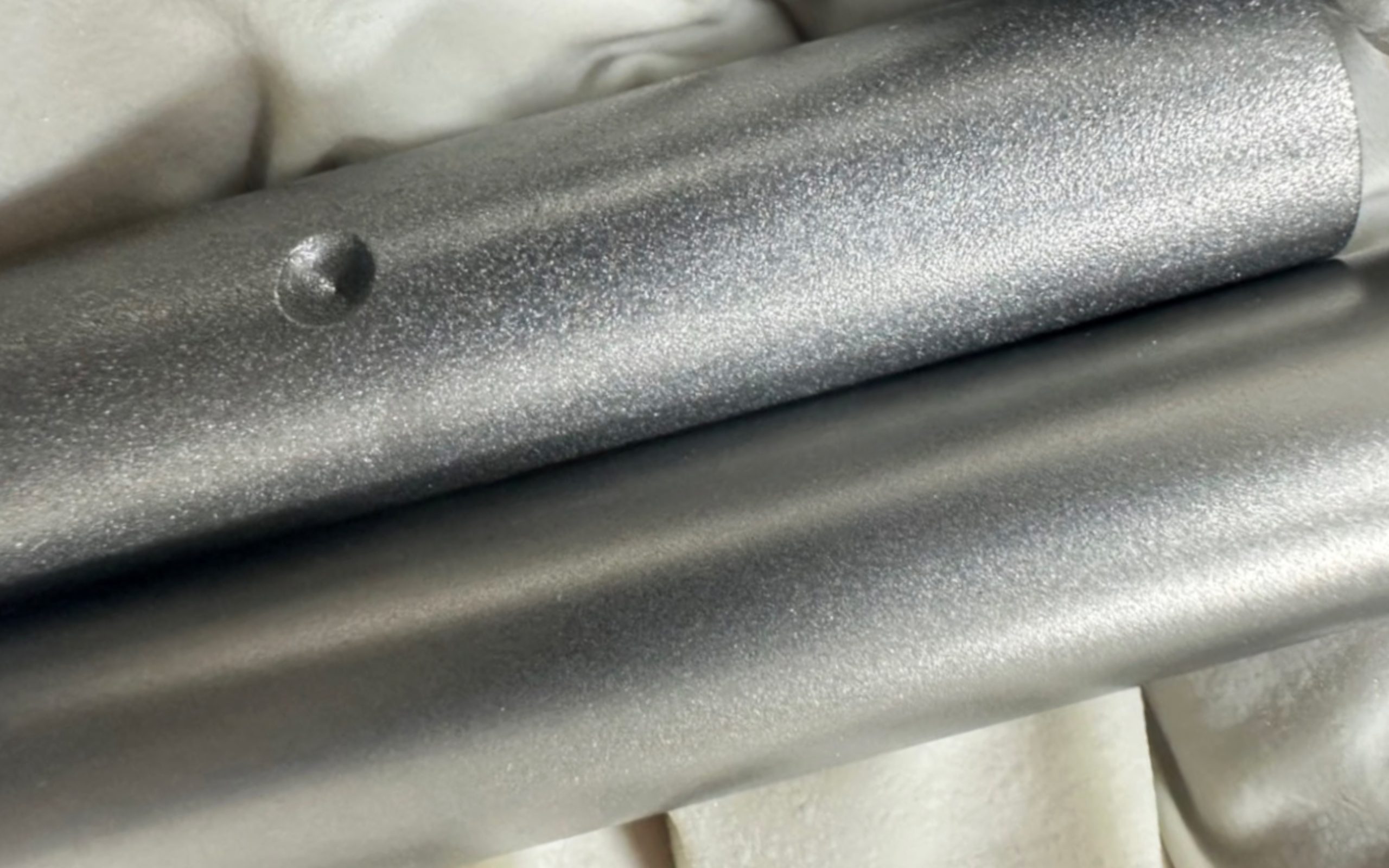
Die Wirkung verschiedener Medien auf dasselbe Werkstück
Ursachen für inkonsistente Rauheit
Ungleichmäßige Rauheit beeinträchtigt nicht nur die Ästhetik des Produkts, sondern kann auch seine Funktionalität beeinträchtigen, insbesondere bei Anwendungen, die Präzisionsteile erfordern. Im Folgenden werden die Hauptursachen für ungleichmäßige Rauheit genannt.
Eigenschaften der Strahlmittel
Die Härte, Form und Partikelgröße des Strahlmittels wirken sich direkt auf die Rauheit aus. So kann beispielsweise die Verwendung von kantigen Strahlmitteln zu einer höheren Oberflächenrauheit führen, während kugelförmige Strahlmittel eher eine glatte Oberfläche erzeugen. Daher sollte bei der Auswahl des Strahlmittels die Auswirkung seiner Eigenschaften auf die Oberflächenrauhigkeit berücksichtigt werden.
Ungereimtheiten im Sprengverfahren
Unstimmigkeiten im Strahlprozess, wie z. B. Strahlabstand, Druckschwankungen und instabiler Strahlmittelfluss, können zu Schwankungen der Rauheit führen. Um eine gleichmäßige Rauheit zu erreichen, ist es wichtig, die Konsistenz des Strahlprozesses aufrechtzuerhalten.
Wartungszustand der Ausrüstung
Auch der Wartungszustand der Strahlanlage wirkt sich auf die Strahlwirkung aus. Alterung, Verschleiß oder Ausfall der Ausrüstung können zu instabilen Strahlergebnissen und damit zu ungleichmäßiger Rauheit führen. Daher ist die regelmäßige Wartung und Inspektion von Sandstrahlanlagen eine wichtige Maßnahme, um die Qualität der Bearbeitung zu gewährleisten.
Wie bestehende Unternehmen diese Probleme bewältigen
Beim Sandstrahlverfahren haben viele Unternehmen trotz der Probleme mit Farbunterschieden, Glanz und Rauheit eine Reihe von wirksamen Maßnahmen ergriffen, um diese Probleme zu überwinden.
Materialkontrolle
Die Auswahl von hochwertigen Rohstoffen aus einer einheitlichen Quelle ist die Grundlage für die Gewährleistung eines gleichbleibenden Sandstrahleffekts. Unternehmen sollten kooperative Beziehungen zu zuverlässigen Lieferanten aufbauen, um die Qualität und Stabilität der Rohstoffe zu gewährleisten. Dadurch lassen sich nicht nur die durch Materialunterschiede verursachten Probleme verringern, sondern auch die Qualität des Endprodukts verbessern. Darüber hinaus ist die strenge Prüfung und Verifizierung von Rohstoffen, um sicherzustellen, dass sie die Produktionsanforderungen erfüllen, ein weiterer Punkt, auf den die Unternehmen achten müssen.
Standardisierte Produktion
Die Festlegung strenger Prozessparameter und Betriebsverfahren ist entscheidend für die Verbesserung der Konsistenz der Sandstrahleffekte. Die Unternehmen sollten jedes Glied im Sandstrahlprozess klären, einschließlich der Auswahl der Sandstrahlmittel, des Sandstrahldrucks, des Sandstrahlabstands und des Düsenwinkels. Darüber hinaus wird durch die Erstellung eines standardisierten Betriebshandbuchs jeder Bediener angeleitet und standardisiert, um sicherzustellen, dass jeder Sandstrahlvorgang einheitlich abläuft, wodurch durch menschliche Faktoren verursachte Qualitätsschwankungen verringert werden.
Aufrüstung der Ausrüstung
Der Einsatz moderner Sandstrahlgeräte kann die Konsistenz der Sandstrahleffekte erheblich verbessern. Moderne Sandstrahlausrüstungen sind in der Regel mit einem intelligenten Steuerungssystem ausgestattet, das die Sandstrahlparameter genau einstellen und verschiedene Indikatoren während des Sandstrahlprozesses in Echtzeit überwachen kann. Unternehmen sollten ihre Anlagen regelmäßig überprüfen und aktualisieren und neue Technologien einsetzen, die ihren Produktionsanforderungen entsprechen, um die Produktionseffizienz und die Produktqualität zu verbessern.
Ausbildung der Mitarbeiter
Die systematische Schulung der Bediener ist eine wichtige Maßnahme zur Gewährleistung der Prozessstabilität. Die Unternehmen sollten regelmäßig Schulungen durchführen, damit die Mitarbeiter die Grundprinzipien des Sandstrahlens, die Betriebsmethoden der Anlagen und die Lösungen für häufige Probleme verstehen. Durch die Verbesserung der Professionalität der Mitarbeiter können die Unternehmen Bedienungsfehler reduzieren und die Stabilität des Sandstrahlprozesses verbessern, wodurch eine gleichbleibende Produktqualität gewährleistet wird.
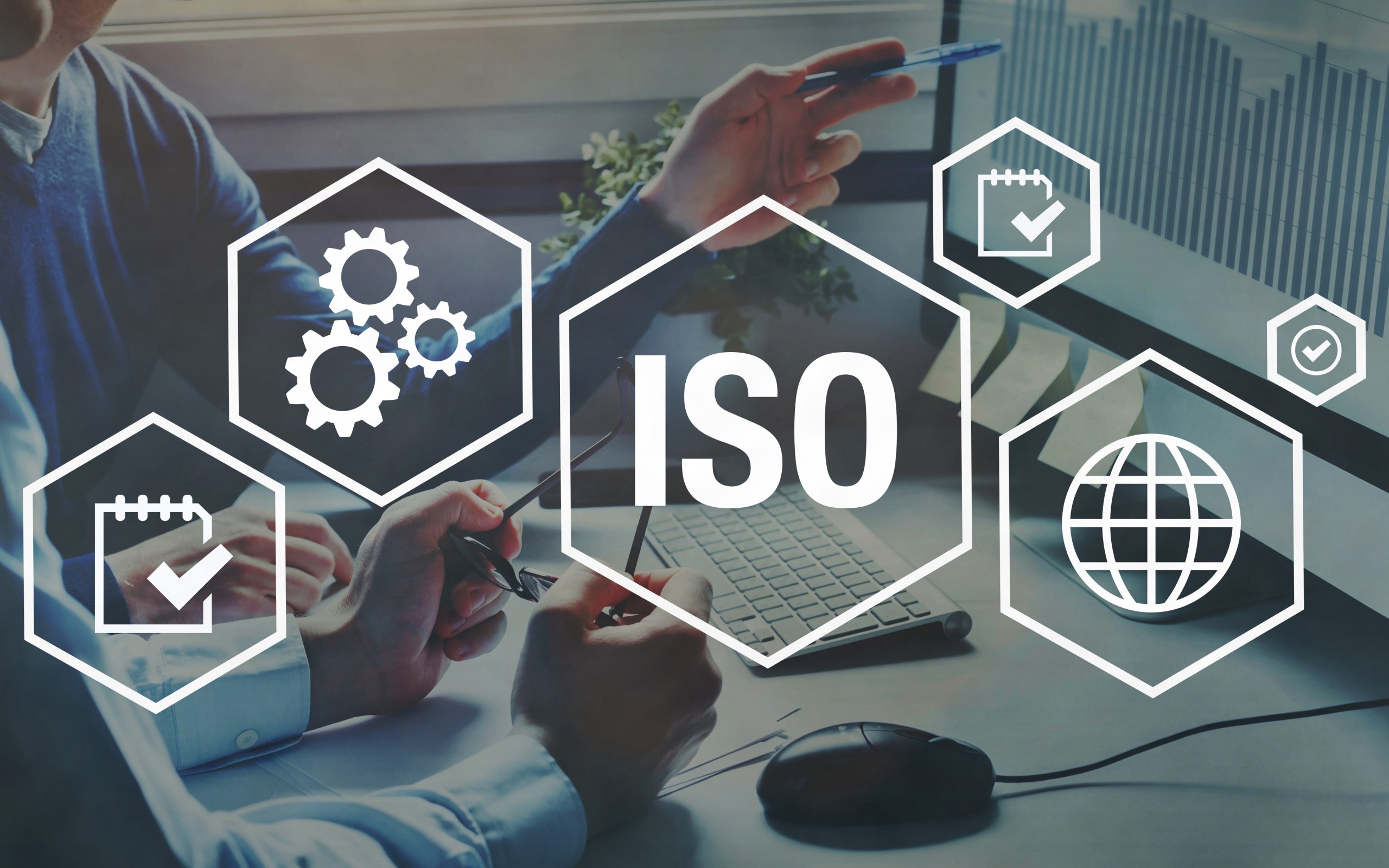
Maßnahmen zur Risikominderung
Selbst wenn die oben genannten Maßnahmen ergriffen werden, kann es immer noch zu Farb-, Glanz- und Rauheitsunterschieden kommen, die während des Sandstrahlens nicht vollständig beseitigt werden können. In diesem Fall können die Unternehmen die folgenden Abhilfemaßnahmen in Betracht ziehen.
Technologie zur Korrektur von Farbunterschieden
Bei sandgestrahlten Werkstücken kann der Farbunterschied durch eine anschließende Beschichtung oder Färbebehandlung korrigiert werden. Durch die Anwendung geeigneter Beschichtungen und Färbetechniken kann das Problem der Farbunterschiede bis zu einem gewissen Grad abgedeckt oder verbessert werden. Dadurch wird nicht nur das Erscheinungsbild des Produkts verbessert, sondern auch seine Korrosions- und Verschleißbeständigkeit erhöht und die Lebensdauer des Produkts verlängert.
Optimieren der Prozessparameter
Durch ständiges Anpassen der Sandstrahlparameter können Unternehmen Farbunterschiede und Inkonsistenzen minimieren. Sie können beispielsweise den Druck, die Geschwindigkeit und den Düsenwinkel während des Sandstrahlvorgangs verfeinern, um den Sandstrahleffekt zu optimieren. Nach der Umsetzung dieser Anpassungen sollten die Unternehmen kontinuierliche Qualitätskontrollen durchführen, um sicherzustellen, dass die Qualität des Endprodukts den Normen entspricht.
Regelmäßige Inspektionen
Die Einrichtung eines strengen Qualitätsprüfungsmechanismus hilft, Probleme im Sandstrahlprozess sofort zu erkennen und zu korrigieren. Unternehmen können vor, während und nach dem Sandstrahlen mehrstufige Qualitätskontrollen durchführen, um sicherzustellen, dass jedes Werkstück den vorgegebenen Qualitätsstandards entspricht. Durch Echtzeitüberwachung und Datenanalyse können Unternehmen potenzielle Probleme schnell erkennen und die notwendigen Anpassungen und Korrekturen vornehmen.
Bei Problemen wie Farbunterschieden, Glanz- und Rauheitsabweichungen im Sandstrahlverfahren können Unternehmen diese durch eine Vielzahl von Methoden überwinden und abmildern. Ob durch Materialkontrolle, standardisierte Produktion, Aufrüstung der Anlagen oder Mitarbeiterschulung, Unternehmen können die Produktqualität im Zuge einer kontinuierlichen Optimierung verbessern. Selbst wenn sich diese Probleme nicht vollständig beseitigen lassen, können Maßnahmen wie die Korrektur von Farbunterschieden, die Optimierung von Prozessparametern und die Einrichtung eines regelmäßigen Kontrollmechanismus Qualitätsschwankungen wirksam reduzieren und den Wettbewerbsvorteil des Produkts auf dem Markt sichern. Durch kontinuierliche Verbesserungen können Unternehmen im harten Marktumfeld wettbewerbsfähig bleiben und das Vertrauen und die Zufriedenheit der Kunden gewinnen.
Filter