Perle en céramiques Manuel de l'utilisateur : 7 étapes pour améliorer la finition des moules
12 février 2025
Le maintien d'une finition homogène est l'un des principaux objectifs de la fabrication et de l'entretien des moules. Cependant, même si le processus standard est strictement suivi, de nombreux clients rencontrent encore les problèmes suivants :
"Pourquoi la finition du moule n'est-elle toujours pas conforme aux normes ?
"Comment éviter de rayer la surface du moule pendant le sablage ?
"Comment optimiser l'efficacité de l'utilisation des billes de céramique ?
Les besoins essentiels de ces problèmes sont les suivants :
- Répétabilité - la finition des différents lots de moules doit être cohérente.
- Maîtrise des coûts - réduire les pertes de supports et les coûts de main-d'œuvre et améliorer la rentabilité.
- Sécurité opérationnelle - assurer une production sûre grâce au contrôle des poussières et à la protection des équipements.
En réponse à ces besoins, nous avons résumé un processus professionnel en 7 étapes pour vous aider à améliorer la finition des moules de manière efficace et sûre.
Étape 1 : Inspection avant traitement pour éliminer la source des dangers cachés
Points faibles du client
- Ignorer des défauts mineurs (tels que des rayures de 0,1 mm) conduit à un échec ultérieur du polissage.
- Un mauvais état de l'équipement (comme l'usure des buses) gaspille le produit et réduit l'effet de sablage.
Solution
1.1 Détection des défauts de moisissure
Utilisez une loupe 20x pour vérifier la surface du moule, en vous concentrant sur le plan de joint et la rainure d'aération. Il est recommandé d'utiliser un rugosimètre portable (tel que le Mitutoyo SJ-210) pour mesurer avec précision l'état de la surface.
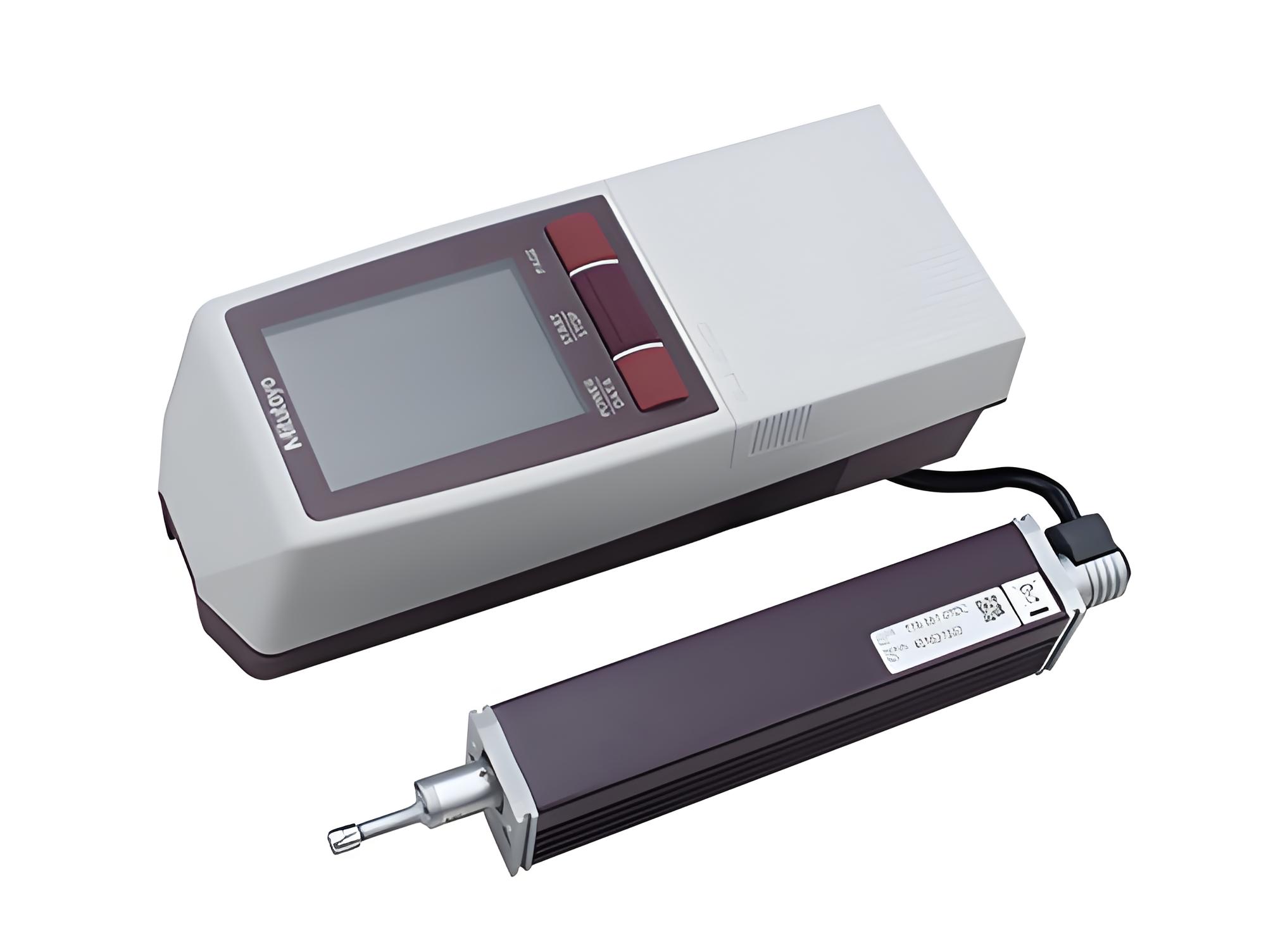
1.2 Liste d'inspection préalable des équipements
- Usure de la buse : La variation du diamètre intérieur doit être≤5%, et doit être remplacée si elle est supérieure.
- Stabilité de la pression d'air : Plage de fluctuation≤±2 PSI pour éviter une injection instable.
Étape 2 : Formule de mise sous pression, la science remplace l'expérience
Points faibles du client
- Le fait de se fier à l'expérience pour régler la pression conduit à un surbroyage des matériaux tendres ou à un nettoyage insuffisant des matériaux durs.
Type de matériau | Coefficient de matière |
---|---|
Plastique (ABS) | 0.8 |
Alliage d'aluminium | 1.2 |
Acier inoxydable | 1.5 |
Alliage de titane | 2.0 |
Carbure | 2.5 |
Solution
2.1 Formule de calcul du PSI
PSI = dureté moyenne × coefficient de matériau de la pièce × 10
Exemple de calcul :
Moule en alliage de titane, utilisant des billes de céramique d'une dureté de 7 Mohs :
PSI = 7 × 2.0 × 10 = 140
2.2 Conseils pour le réglage de la pression
Mesurer la valeur Ra après la première opération : si la valeur Ra est trop élevée, augmenter le PSI de 5 à 10 ; si la valeur Ra est trop basse, réduire le PSI de 5 à 10.
Protection par un matériau souple : Pour les moules en plastique, la limite supérieure de PSI est de 80 afin d'éviter un broyage excessif.
Nettoyage efficace des matériaux durs : Pour les moules en alliage de titane, la limite inférieure de PSI est de 140 pour garantir l'effet de nettoyage.
Étape 3 : Contrôle de l'angle et de la distance, la victoire de la mécanique géométrique
Points faibles du client
- L'injection verticale entraîne un surbroyage local et l'angle d'incidence de 30° est difficile à contrôler avec précision.
Solution
3.1 Solution d'optimisation de l'angle d'incidence de 30
- A un angle d'incidence de 30°, la force tangentielle représente 70%, et la force normale représente 30%, ce qui permet d'équilibrer l'efficacité du nettoyage et la protection de la surface.
- Distance de pulvérisation = diamètre de la buse × 10 (par exemple : buse de 8 mm → distance de 80 mm)
3.2 Outils pratiques
L'indicateur d'angle laser (erreur ±1°) assure un contrôle précis de l'angle.
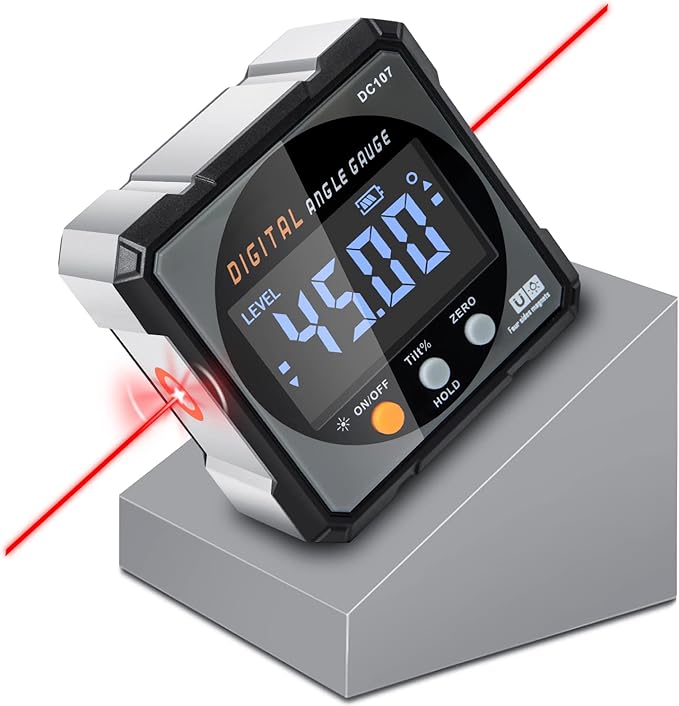
Étape 4 : Surveillance de l'état des médias, la clé de l'allongement de la durée de vie
Points faibles du client
- Impossibilité de déterminer quand remplacer les billes de céramique, ce qui entraîne des pertes de coûts ou une dégradation de la qualité.
Solution
4.1 Détection du taux d'écrasement
Prenez 100 g de produit et triez manuellement les particules broyées. Si le taux de broyage est >5%, il doit être remplacé.
4.2 Surveillance intelligente en ligne
Installer un capteur de taille de particules en ligne pour surveiller la modification de la taille des particules en temps réel.
Modèle de billes de céramique HLH | Taille standard des particules (µm) | Écart admissible (µm) |
---|---|---|
B20 | 600-850 | ±50 |
B30 | 425-600 | ±35 |
B40 | 250-425 | ±20 |
B60 | 125-250 | ±15 |
B80 | 180-250 | ±15 |
B100 | 125-180 | ±10 |
B120 | 63-125 | ±8 |
B125 | 0-125 | ±8 |
B170 | 45-90 | ±5 |
B205 | 0-63 | ±5 |
B400 | 30-63 | ±3 |
B505 | 10-30 | ±2 |
Étape 5 : Normes d'inspection de la qualité après traitement, acceptation basée sur les données
Points faibles du client
- Seule l'inspection visuelle permet d'identifier tardivement le problème de la mauvaise finition.
Solution
5.1 Outils de mesure de la valeur Ra recommandés
Modèle de base : Testeur de rugosité portable Time 3220
Avantages : portable et facile à utiliser, adapté à la détection rapide sur site, précision ±5%.
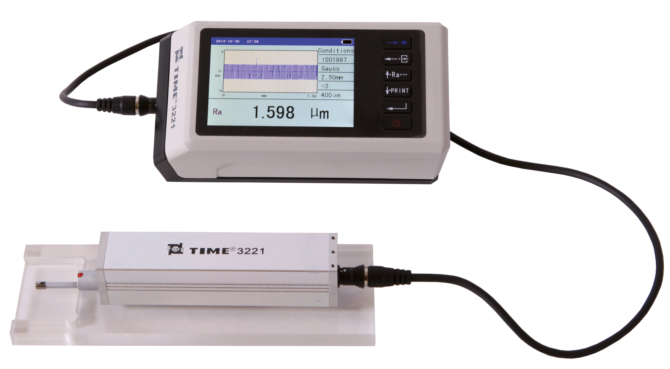
Modèle de haute précision : Profileur optique Zygo NewView 9000 3D.
Avantages : mesures de haute précision, adaptées aux surfaces complexes, résolution jusqu'au niveau du nanomètre.
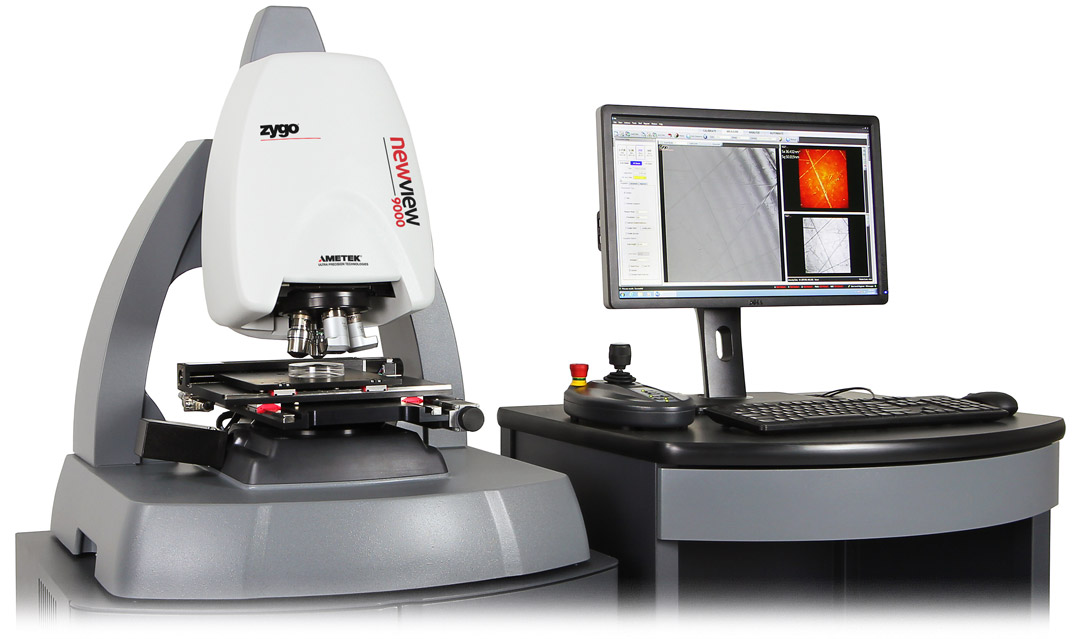
5.2 Normes de valeur Ra de l'industrie
Secteurs d'activité sélectionnés | Matériaux communs | Exigences Ra (µm) | Nombre de points de test |
---|---|---|---|
Composants électroniques | Connecteurs en alliage de cuivre | ≤0.4 | ≥10 points/㎡ |
Boîtiers de précision en plastique | ≤0.6 | ≥8 points/㎡ | |
Pièces détachées automobiles | Pièces du moteur en alliage d'aluminium | ≤0.8 | ≥5 points/㎡ |
Disques de frein en acier inoxydable | ≤1.0 | ≥6 points/㎡ | |
Dispositifs médicaux/implants | Implants orthopédiques en alliage de titane | ≤0.4 | ≥12 points/㎡ |
Instruments chirurgicaux en acier inoxydable | ≤0.6 | ≥10 points/㎡ | |
Aérospatiale | Aubes de turbine en alliage de titane | ≤0.3 | ≥15 points/㎡ |
Pièces de moteur en alliage haute température | ≤0.5 | ≥10 points/㎡ |
Étape 6 : Spécifications du traitement des déchets, conformité et réduction des coûts en parallèle
Points faibles du client
- Les coûts de traitement des déchets sont élevés et il existe des risques pour l'environnement.
Solution
6.1 Processus de recyclage des billes de céramique
Séparation magnétique (élimination des impuretés métalliques) → séparation par air (élimination des poussières) → criblage (classement et réutilisation)
Taux de récupération : ≥85% (le taux d'écrasement doit être contrôlé <5%).
6.2 Traitement de conformité des déchets
- Poussière de céramique (décharge inoffensive)
- Débris métalliques (recyclage professionnel)
Étape 7 : Dépannage des problèmes courants, guide de réponse rapide
Points faibles du client
- Des problèmes soudains (tels qu'une surface irrégulière) entraînent une stagnation de la chaîne de production.
Solution
Phénomène problématique | Raisons possibles | Solution |
---|---|---|
Partiellement mat | Distribution inégale des médias | Vérifier le séparateur de sable et nettoyer le point de blocage |
Bandes périodiques | Usure de l'excentrique de la buse | Remplacer la buse et calibrer la concentricité |
Polissage excessif des bords | L'angle d'incidence est trop grand (>45°) | Ajuster l'angle à 30° et réduire le PSI |
Rayures de surface | Mauvaise sélection de la granularité du support | Remplacer le sable céramique par des particules de taille appropriée. |
Résidus de poussière excessifs | Le système de dépoussiérage est inefficace | Vérifier l'équipement de dépoussiérage et nettoyer l'élément filtrant |
Surchauffe partielle du moule | Le temps d'injection est trop long | Réduire le temps d'injection unique et augmenter l'intervalle de refroidissement |
FAQ : Réponse rapide aux questions les plus fréquentes
Q : Combien de fois les billes de céramique doivent-elles être remplacées après avoir été recyclées ?
R : Il est recommandé de le multiplier par 20 ou d'obtenir un taux d'écrasement >5% (selon ce qui se produit en premier).
Q : Comment traitez-vous la poussière d'adsorption électrostatique du moule après l'opération de fabrication des billes de céramique ?
R : Utiliser un pistolet à air ionique pour souffler + essuyer avec de l'éthanol anhydre.
Q : Comment éviter la déformation des moules à parois minces (<1mm) ?
R : Utilisez du sable fin supérieur à #220, PSI≤50, et réduisez l'angle d'incidence à 20°.
Grâce à ce processus professionnel en 7 étapes, vous pouvez non seulement résoudre le problème de surface des finitions de moules qui ne répondent pas aux normes, mais aussi atteindre les objectifs fixés :
- Réduction des coûts : la perte de fluide est réduite de 30%, et l'intervalle de maintenance de l'équipement est multiplié par deux.
- Amélioration de la qualité : la cohérence de la finition (valeur CV) est ramenée de 5% à ≤2%.
- Garantie de conformité : le 100% est conforme aux normes ISO 9001/14001 et aux normes industrielles spécifiques.
Allez-y et pratiquez-la dès maintenant.
Si vous avez des questions, n'hésitez pas à contactez-nous pour une consultation gratuite~
Filtres