¿Qué es un proceso de desincrustación?
16 de octubre de 2024
En el campo del procesamiento de metales, el proceso de desincrustación es un paso importante para garantizar la calidad del material. La cascarilla es un óxido formado por el metal a alta temperatura o en un ambiente húmedo, que a menudo se adhiere a la superficie del metal y afecta al posterior proceso de tratamiento y revestimiento. Especialmente en la industria de fabricación de acero, la cascarilla no sólo reduce la resistencia y la tenacidad del metal, sino que también puede causar efectos adversos en el proceso de transformación posterior, como una mala adherencia del revestimiento y una menor calidad de la soldadura. Por lo tanto, es esencial comprender en profundidad la formación de la cascarilla y su proceso de eliminación.
Formación de la escala
Las incrustaciones suelen formarse cuando el metal se expone a altas temperaturas, oxígeno y humedad. Cuando la superficie del metal entra en contacto con el oxígeno del aire, especialmente en estado fundido, se produce una reacción de oxidación en la superficie del metal. Con el tiempo, estos óxidos se acumulan y forman una capa dura llamada cascarilla. Concretamente, en el proceso de fabricación del acero, la cascarilla se compone principalmente de óxido de hierro, óxido de manganeso y otros componentes. Las razones de su formación son, entre otras
- Calentamiento a alta temperatura: Durante el tratamiento térmico o la soldadura, la temperatura del metal aumenta y la reacción de oxidación superficial se intensifica.
- Ambiente húmedo: La superficie metálica queda expuesta al aire húmedo durante mucho tiempo, lo que hace que la humedad se combine con el oxígeno y acelere la oxidación.
- Almacenamiento inadecuado: La falta de protección adecuada durante el almacenamiento de materiales metálicos puede provocar la oxidación de la superficie.
Las incrustaciones de óxido no sólo afectan al acabado de la superficie metálica, sino que también pueden causar defectos en procesos posteriores. Por ejemplo, durante la soldadura, una incrustación de óxido puede provocar una resistencia insuficiente de la soldadura; y durante el proceso de recubrimiento, la presencia de una incrustación de óxido impedirá que el recubrimiento se adhiera bien, lo que afectará al efecto anticorrosión.
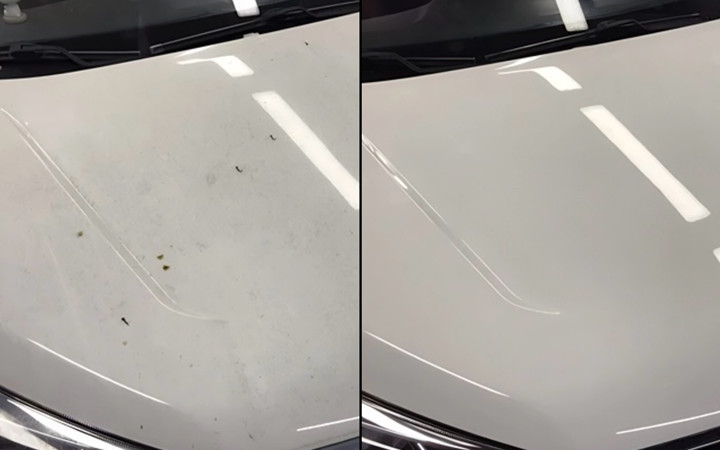
Comparación de la reparación de coches oxidados
Proceso de desincrustación
El proceso de eliminación de las incrustaciones de óxido incluye principalmente la eliminación mecánica, la eliminación química y la eliminación por chorro de arena. Cada método tiene sus propias ventajas y escenarios de aplicación, que se detallarán a continuación.
Eliminación mecánica
- Resumen del método
La eliminación mecánica consiste en eliminar físicamente las incrustaciones de óxido mediante equipos manuales o mecánicos, como amoladoras y rascadores. Este método es adecuado para piezas pequeñas o para la eliminación localizada.
- Ventajas
- Alta precisión: Puede eliminar con precisión las incrustaciones de óxido sin dañar el sustrato, lo que resulta adecuado para piezas con elevados requisitos de acabado superficial.
- Fácil manejo: El equipo para la eliminación mecánica es relativamente sencillo, fácil de manejar y adecuado para diversas ocasiones de trabajo.
- Escenarios aplicables
- Piezas pequeñas: Las piezas metálicas pequeñas, como moldes y herramientas, deben procesarse con precisión para garantizar el efecto de procesamiento posterior.
- Reparación local: La eliminación mecánica puede lograr eficazmente un tratamiento selectivo para la eliminación local de óxido en equipos de gran tamaño.
Eliminación química
- Resumen del método
La eliminación química utiliza soluciones ácidas (como ácido clorhídrico, ácido sulfúrico, etc.) para disolver el óxido. Los métodos de eliminación química son adecuados para piezas grandes y pueden eliminar eficazmente capas de óxido difíciles de limpiar mecánicamente.
- Ventajas
- Efecto de eliminación significativo: Los agentes químicos pueden eliminar rápida y completamente las capas de óxido, especialmente las gruesas.
- Amplia aplicabilidad: Adecuado para piezas de trabajo de diversas formas complejas, no limitadas por el contacto físico.
- Escenarios aplicables
- Grandes piezas estructurales: En el caso de grandes componentes metálicos como puentes, barcos y estructuras de acero, la eliminación química puede limpiar eficazmente el óxido de sus superficies.
- Piezas con formas complejas: Para piezas metálicas con formas irregulares o detalles complejos, la eliminación química puede garantizar una limpieza a fondo.
Eliminación por chorro de arena
- Resumen del método
La eliminación por chorro de arena elimina los óxidos pulverizando medios granulares (como óxido de aluminio, arena, etc.) con fuerza de impacto físico. Este método puede eliminar rápidamente grandes áreas de óxido y tiene una amplia gama de aplicaciones.
- Ventajas
- Alta eficiencia y velocidad: El arenado puede procesar un gran número de piezas en poco tiempo, con gran eficacia y adecuado para la producción industrial.
- Gran capacidad de ajuste: Según el material y los requisitos de la pieza, se pueden seleccionar diferentes medios de arenado y presión de pulverización para lograr un procesamiento personalizado.
- Escenarios aplicables
- Fabricación de acero: En la industria siderúrgica, el chorro de arena se utiliza a menudo para eliminar el óxido y las capas de óxido a fin de preparar la posterior pintura o soldadura.
- Industria automovilística y aeronáutica: Chorreado de carrocerías de automóviles, piezas de aviación, etc. para garantizar su acabado superficial y mejorar la calidad del producto.
- Industria del petróleo y el gas: Se utiliza para el tratamiento superficial de tuberías y equipos de petróleo y gas para eliminar óxidos e impurezas, evitar la corrosión de los equipos y prolongar su vida útil.
Tras considerar exhaustivamente los tres procesos de eliminación mecánica, eliminación química y eliminación por chorro de arena, podemos constatar que cada método tiene sus ventajas, pero en la fabricación industrial moderna, el proceso que puede satisfacer simultáneamente los requisitos de eficacia, adaptabilidad y calidad superficial en la producción a gran escala es, sin duda, el chorro de arena. Las principales razones son las siguientes:
- Alta eficiencia y velocidad: La eliminación por chorro de arena puede procesar grandes superficies de piezas en poco tiempo, lo que mejora enormemente la eficacia de la producción. Esto es especialmente importante para las industrias modernas que persiguen la velocidad y la eficiencia de la producción.
- Gran adaptabilidad: El equipo de chorreado de arena puede ajustarse en función de los distintos materiales de la pieza y el grosor de la capa de óxido para satisfacer diversas necesidades de producción. Esta flexibilidad lo hace adecuado para diversas aplicaciones industriales, como la fabricación de acero, la automoción y la aviación.
- Calidad de la superficie: El chorreado de arena no sólo puede eliminar eficazmente las incrustaciones de óxido, sino también mejorar el acabado superficial de las piezas de trabajo, creando una buena base para el posterior revestimiento y procesamiento.
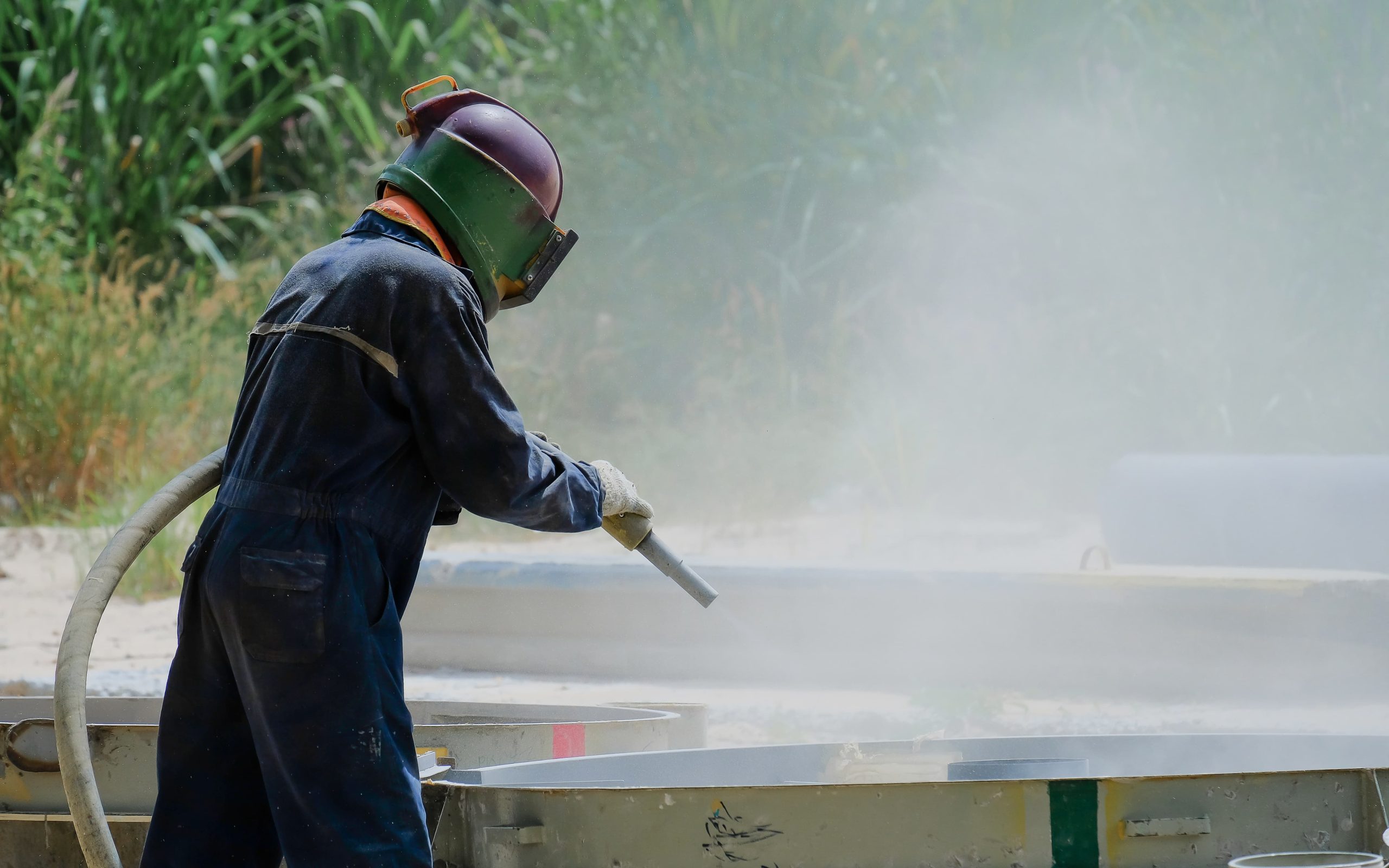
Demostración de chorro de arena
Equipos y materiales para el proceso de desincrustación
En el proceso de decapado, es crucial elegir el equipo de arenado adecuado. A continuación se indican tres equipos de arenado de uso común, a saber, la arenadora de alta presión, la arenadora a presión y la arenadora de turbina, cada uno de los cuales tiene diferentes ventajas y desventajas y escenarios aplicables.
- Arenadora de alta presión
Una arenadora de alta presión utiliza aire a alta presión para acelerar y rociar el medio de arenado sobre la superficie de la pieza de trabajo, lo que resulta adecuado para ocasiones que requieren una fuerza de impacto de alta intensidad. Muy utilizada en la producción industrial a gran escala y el procesamiento de piezas pesadas.
Ventajas:
- Alta eficacia: Puede eliminar rápidamente las capas gruesas de óxido y la suciedad y mejorar la eficacia del trabajo.
- Amplia gama de aplicaciones: Puede utilizarse para el tratamiento de superficies de diversos materiales y es adecuado para diferentes requisitos de proceso.
Desventajas:
- Alto coste de los equipos: En comparación con otros tipos de equipos de arenado, la inversión en máquinas de arenado de alta presión es relativamente grande.
- Elevados requisitos de mantenimiento: El mantenimiento y la gestión de los sistemas de alta presión son relativamente complejos y requieren un manejo profesional.
- Chorreadora a presión
La arenadora a presión controla la intensidad y el efecto del arenado ajustando la presión y el caudal del medio, lo que resulta adecuado para necesidades de limpieza de intensidad media. Adecuada para piezas de trabajo más pequeñas y tratamiento de superficies.
Ventajas:
- Coste relativamente bajo: En comparación con las máquinas de chorreado a alta presión, las máquinas de chorreado a presión tienen menores costes de adquisición y mantenimiento y son adecuadas para su uso por parte de pequeñas y medianas empresas.
- Fácil manejo: El funcionamiento del equipo es relativamente sencillo y fácil de usar.
Desventajas:
- Efecto de eliminación limitado: En el caso de escamas de óxido gruesas y suciedad, el efecto de limpieza puede no ser tan bueno como el de las máquinas de chorro de arena a alta presión.
- No es adecuado para el tratamiento de grandes superficies: Adecuada para operaciones a pequeña escala o finas, pero no para la producción industrial a gran escala.
- Chorreadora de turbina
La arenadora de turbina utiliza palas de turbina giratorias de alta velocidad para acelerar el medio de arenado y formar un chorro potente, adecuado para el tratamiento de superficies. Se utiliza principalmente en procesos de tratamiento de superficies con altos requisitos.
Ventajas:
- Buena uniformidad: El medio de arenado se pulveriza uniformemente, lo que puede lograr mejores efectos de tratamiento de superficies.
- Alta eficiencia y bajo consumo energético: En comparación con otros equipos, las arenadoras de turbina son más eficientes en el consumo de energía.
Desventajas:
- Inversión inicial elevada: El coste de adquisición es relativamente elevado, lo que resulta adecuado para empresas con presupuestos suficientes.
- Altos requisitos técnicos: El funcionamiento y el mantenimiento requieren cierto apoyo técnico.
A la hora de elegir el equipo de chorro de arena adecuado, hay que tener en cuenta factores como las características de la pieza, el grosor de la cascarilla de óxido y el presupuesto. Comprender las características y los escenarios aplicables de los distintos tipos de equipos de chorro de arena puede ayudar a su empresa a conseguir los mejores resultados en el proceso de eliminación de la cascarilla de óxido. Por supuesto, en el proceso de eliminación de la cascarilla de óxido también es fundamental elegir el material de chorreado adecuado. A continuación se indican cuatro materiales de chorreado de arena de uso común. Explicaré en detalle sus respectivas ventajas e inconvenientes y los escenarios aplicables. Según las necesidades y el presupuesto de cada pieza, puede elegir el material más adecuado para conseguir el mejor efecto de eliminación.
- Grano de acero
Ventajas:
- Gran dureza: La granalla de acero tiene una gran dureza y puede eliminar eficazmente las incrustaciones de óxido y la suciedad más resistentes.
- Económico: En comparación con otros medios de arenado, la granalla de acero tiene un coste inferior y es adecuada para aplicaciones de gran superficie.
Desventajas:
- Fácil de oxidar: La granalla de acero se oxida fácilmente durante su uso y puede dejar óxido en la superficie.
- Generación de polvo: Es posible que se genere más polvo durante el proceso de voladura, por lo que deben reforzarse las medidas de ventilación y seguridad.
Escenarios aplicables:
La granalla de acero se utiliza a menudo para el tratamiento de superficies de fabricación industrial y maquinaria pesada, especialmente para eliminar incrustaciones de óxido y residuos de soldadura en la superficie de piezas grandes.
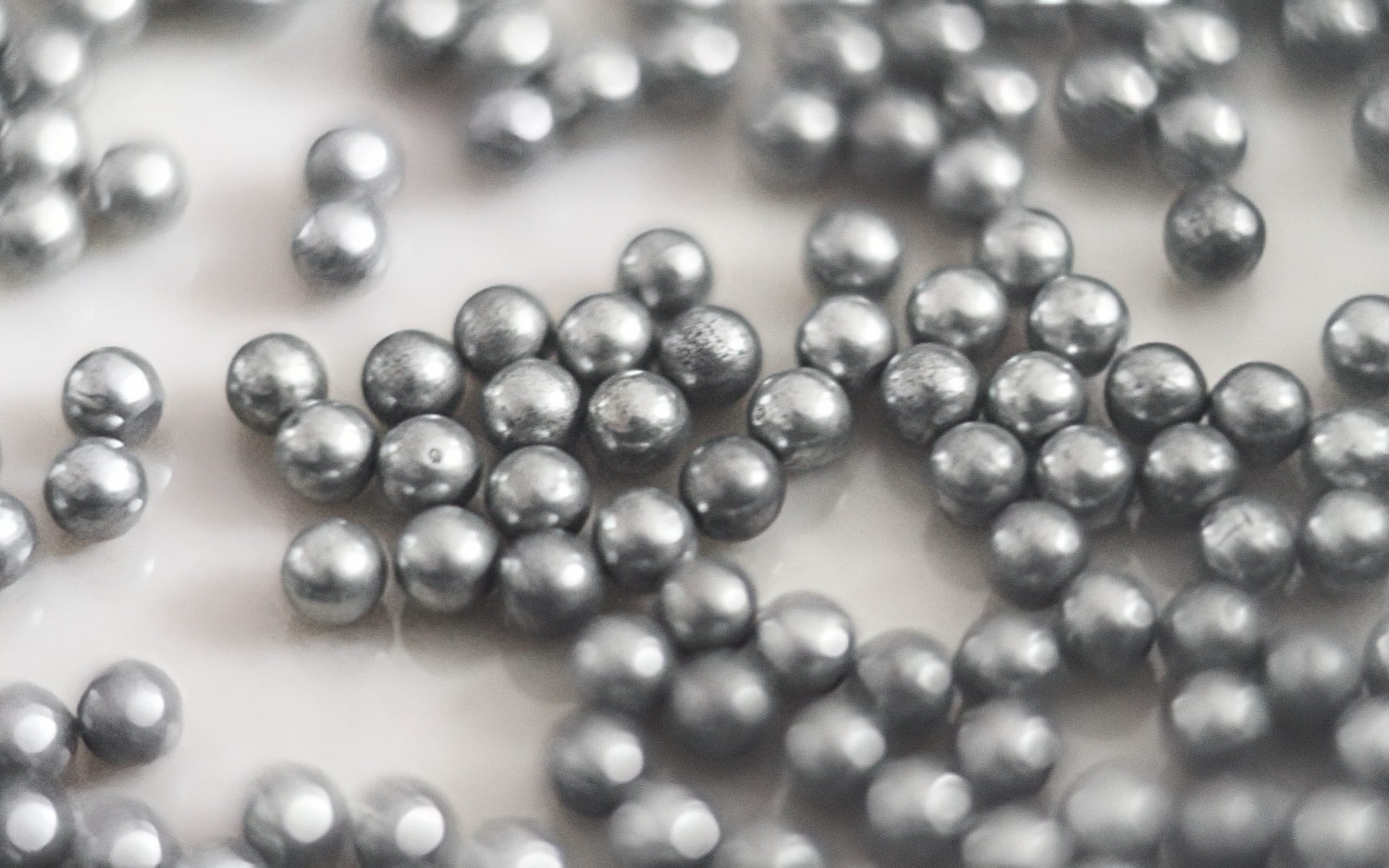
Bola de acero
- Corindón marrón
Ventajas:
- Gran resistencia al desgaste: La dureza y la resistencia al desgaste del corindón marrón lo hacen excelente para eliminar óxidos.
- No hay contaminación: Sus propiedades químicas son estables y no contaminan la superficie de la pieza.
Desventajas:
- Mayor coste: Comparado con la gravilla de acero, el corindón marrón tiene un precio más elevado y puede no ser adecuado para proyectos con presupuestos limitados.
- Gran fragilidad: Durante su uso, puede romperse y generar polvo.
Escenarios de aplicación: El corindón marrón es adecuado para el tratamiento y la limpieza de superficies finas, como los requisitos de alta calidad superficial de las industrias aeroespacial y automovilística.
- Granalla de acero
Ventajas:
- Superficie lisa: La granalla de acero puede formar una superficie lisa sin dañar el sustrato durante el proceso de pulverización.
- Larga vida útil: Gracias a su resistencia al desgaste, la granalla de acero puede reutilizarse muchas veces y resulta económica.
Desventajas:
- Efecto de limpieza limitado: Para una costra de óxido gruesa, el efecto limpiador de la granalla de acero puede no ser tan bueno como el de la granalla de acero y el corindón marrón.
- Más pesado: En comparación con otros medios, la granalla de acero es más pesada y requiere más energía al pulverizar.
Escenarios aplicables: La granalla de acero se utiliza principalmente para pulir y reforzar superficies, y se emplea ampliamente en el tratamiento de superficies de automóviles, fabricación de maquinaria y productos metálicos.
Ventajas:
- Excelente efecto de limpieza: El óxido de aluminio tiene una gran dureza y puede eliminar eficazmente las incrustaciones de óxido sin causar demasiados daños al sustrato.
- Protección del medio ambiente: Sus características no tóxicas e inocuas le confieren una ventaja en la protección del medio ambiente.
Desventajas:
- Coste elevado: El óxido de aluminio es relativamente caro en comparación con otros medios de chorreado y no es adecuado para proyectos a gran escala y de bajo presupuesto.
- No apto para capas de óxido pesadas: El óxido de aluminio puede requerir un largo tiempo de procesamiento cuando se trata de capas gruesas de óxido.
Escenarios aplicables:
El óxido de aluminio es adecuado para industrias con elevados requisitos de acabado superficial, como el tratamiento de superficies de dispositivos electrónicos y maquinaria de precisión.
Casos de aplicación industrial
La eliminación de incrustaciones de óxido se utiliza ampliamente en diversas industrias. He aquí algunos estudios de casos concretos:
Fabricación de acero
En la industria siderúrgica, suele formarse una capa de óxido durante el tratamiento térmico y la soldadura del acero. El chorro de arena o la limpieza química pueden eliminar eficazmente la capa de óxido y mejorar la calidad de los tratamientos posteriores (como el revestimiento y la soldadura). Los fabricantes de acero han conseguido reducir la tasa de desprendimiento de los revestimientos posteriores y mejorar la calidad de la superficie y la durabilidad de los productos utilizando óxido de aluminio.
Aeroespacial
En el sector aeroespacial, la eliminación de las incrustaciones de óxido es clave para garantizar el rendimiento de los componentes. Las piezas de aleación de alta temperatura son propensas a formar capas de óxido durante la fabricación y la soldadura. El uso de un limpiador ultrasónico para eliminarlas puede mantener la precisión geométrica y el acabado superficial de los componentes, lo que es crucial para mejorar la fiabilidad de los componentes aeronáuticos.
Industria del petróleo y el gas
En la industria del petróleo y el gas, las superficies de los equipos suelen estar contaminadas por óxidos y depósitos, especialmente en entornos de alta temperatura y presión. Por ejemplo, equipos clave como las brocas y las válvulas forman una capa de óxido durante su funcionamiento. Utilizar un chorro de arena para tratarlos puede prolongar eficazmente la vida útil de los equipos y mejorar su eficacia de trabajo.
Buenas prácticas para el proceso de descalcificación
Para garantizar la eficacia y la seguridad del trabajo, puede prestar atención a las siguientes sugerencias operativas clave durante el proceso de eliminación de las incrustaciones de óxido:
Normalizar el proceso operativo
Asegurarse de que el proceso operativo está estandarizado, incluyendo el pretratamiento, el tratamiento principal y el postratamiento. Los operarios deben estar familiarizados con los requisitos de cada eslabón para garantizar la integridad de la eliminación de las incrustaciones de óxido.
Precauciones de seguridad
- Equipo de protección individual: Los operadores deben llevar equipo de protección adecuado, como gafas protectoras, máscaras, guantes y tapones para los oídos, para evitar lesiones durante el funcionamiento.
- Ventilación y extracción: Cuando utilice productos químicos de limpieza o equipos de chorro de arena, asegúrese de que la zona de trabajo está bien ventilada para reducir la acumulación de gases y polvo nocivos.
Formación de operadores
Reforzar la formación de los operarios para garantizar que comprenden el uso de los equipos, los peligros y las medidas de respuesta ante emergencias. Realizar periódicamente simulacros de seguridad para hacer frente a emergencias.
Mantenimiento de los equipos
Mantenga y revise periódicamente el equipo de desincrustación para garantizar su funcionamiento normal. En el caso de las máquinas de chorro de arena, debe comprobarse periódicamente el estado de la boquilla, la presión del aire y el abrasivo para garantizar la consistencia del efecto de eliminación.
El decapado es de gran importancia en el proceso de tratamiento de superficies metálicas, que está directamente relacionado con la calidad y la eficacia de producción del producto. La elección de métodos y materiales de eliminación adecuados no sólo puede mejorar el efecto del tratamiento de superficies, sino también reducir los costes de producción y el impacto medioambiental. En el futuro, con el continuo avance de la tecnología, el proceso de decapado será más eficaz, respetuoso con el medio ambiente e inteligente. Los profesionales del sector deben prestar atención al proceso de decapado para garantizar la alta calidad y el rendimiento de los productos metálicos y satisfacer así las necesidades de la industria moderna.
Filtros