Todo sobre el granallado cerámico
29 de agosto de 2024
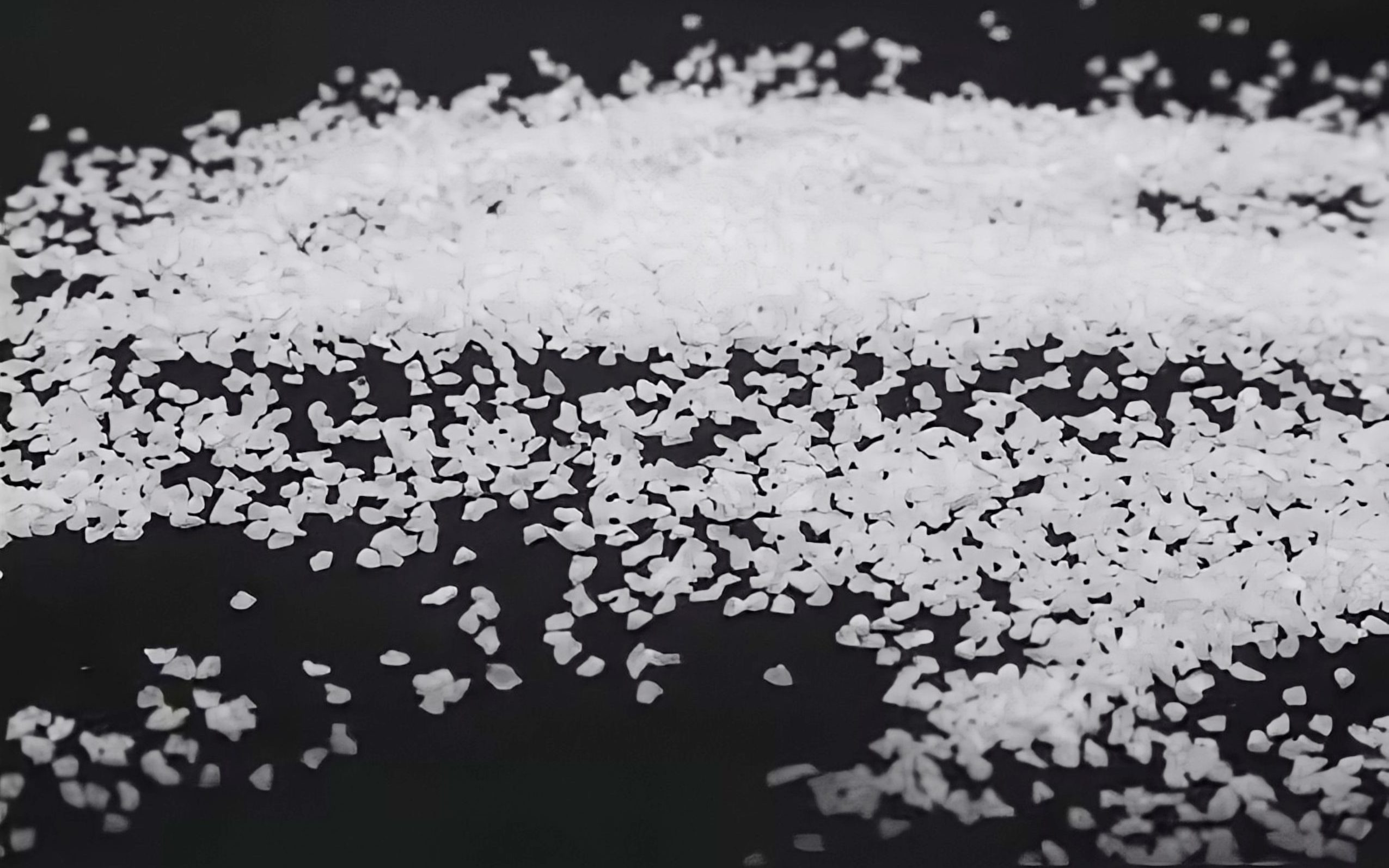
En la fabricación moderna, los procesos de tratamiento de superficies desempeñan un papel crucial. La tecnología de chorro de arena, como método común de tratamiento de superficies, implica la proyección a alta velocidad de abrasivos sobre la superficie de una pieza de trabajo para conseguir limpiarla, desbarbarla o mejorar la dureza de la superficie. Entre los diversos medios de chorreado de arena, las bolas de granalla cerámica destacan por sus propiedades físicas únicas y su rendimiento superior.
Los granos de cerámica y las bolas de cerámica tienen una composición similar, compuesta principalmente por óxido de circonio y dióxido de silicio. Sin embargo, difieren en su forma: los granos cerámicos son angulares, mientras que las bolas cerámicas son esféricas. Esta diferencia de forma afecta significativamente a su rendimiento en la aplicación. En este artículo se analizan en detalle la composición, el proceso de fabricación, las características físicas, las áreas de aplicación, las ventajas y los retos de las microesferas cerámicas, y se ofrecen las mejores prácticas y análisis de rentabilidad para ayudarle a comprender mejor este material.
Composición y proceso de fabricación
Análisis de la composición
Las microesferas cerámicas para granallado están compuestas principalmente de óxido de circonio (ZrO₂), seguido de dióxido de silicio (SiO₂). Esta composición les confiere unas ventajas únicas en el tratamiento de superficies.
- Óxido de circonio (ZrO₂): Proporciona una excelente dureza y resistencia al desgaste, permitiendo que los granos mantengan su estructura durante los procesos de arenado de alta intensidad. Se utiliza ampliamente en aplicaciones que requieren una gran durabilidad.
- Dióxido de silicio (SiO₂): Mejora la estabilidad química de las perlas, aportando cierta tenacidad y resistencia al calor.
Proceso de fabricación
El proceso de fabricación de microesferas cerámicas de granallado consta de tres etapas principales: preparación de la materia prima, conformación y sinterización.
- Preparación de la materia prima: El polvo de óxido de circonio de gran pureza se mezcla con polvo de dióxido de silicio en proporciones específicas. Las materias primas mezcladas se procesan finamente para garantizar la uniformidad y la estabilidad del rendimiento de las microesferas finales.
- Dando forma a: Las perlas iniciales se forman mediante secado por pulverización u otras técnicas de conformación. Para conseguir la estructura angular, suelen utilizarse moldes o procesos de conformación especiales. Esta forma proporciona una mayor fuerza de corte y superficie de contacto.
- Sinterización: Las perlas moldeadas se sinterizan en un horno de alta temperatura. El control de la temperatura y el tiempo durante la sinterización son cruciales para la dureza y densidad finales de las perlas. Tras la sinterización, las perlas se criban y se clasifican para garantizar la uniformidad de tamaño y forma.
Características
Análisis de formas
La estructura angular de los granos cerámicos de chorreado ofrece ventajas significativas. Durante el chorreado, los granos angulares proporcionan una mayor fuerza de corte y unos efectos de limpieza de superficies más potentes que los granos esféricos. Además, son más eficaces para eliminar la suciedad y las impurezas de geometrías complejas o zonas de difícil acceso.
Propiedades físicas clave
- Dureza: Las microesferas cerámicas para granallado suelen tener una dureza de Mohs 7. Esta elevada dureza permite que las microesferas funcionen bien al tratar materiales de gran dureza sin causar un desgaste grave.
- Densidad: Los granos de granalla cerámica suelen tener una densidad de 3,8 g/cm³. Una mayor densidad significa que los granos pueden generar una mayor fuerza de impacto durante el granallado, mejorando el impacto y el efecto de limpieza de la superficie de la pieza, lo que los hace adecuados para tareas de tratamiento de superficies de alta intensidad.
- Resistencia al desgaste: Gracias a su elevada dureza y estructura angular, los granos de chorreado cerámicos presentan una excelente resistencia al desgaste. En operaciones de chorreado de larga duración y alta intensidad, los granos mantienen un buen rendimiento y prolongan su vida útil.
Comparación con granalla cerámica
La principal diferencia entre los granos cerámicos y las bolas cerámicas es su forma. Las bolas esféricas se utilizan normalmente para aplicaciones con menores requisitos de superficie, como el desbarbado o el tratamiento de superficies rugosas, mientras que las bolas angulares, debido a su mayor fuerza de corte y superficie de contacto, son adecuadas para tareas de limpieza de superficies de alta precisión y eficacia. También ofrecen mayor flexibilidad cuando se trata de formas complejas o espacios reducidos.
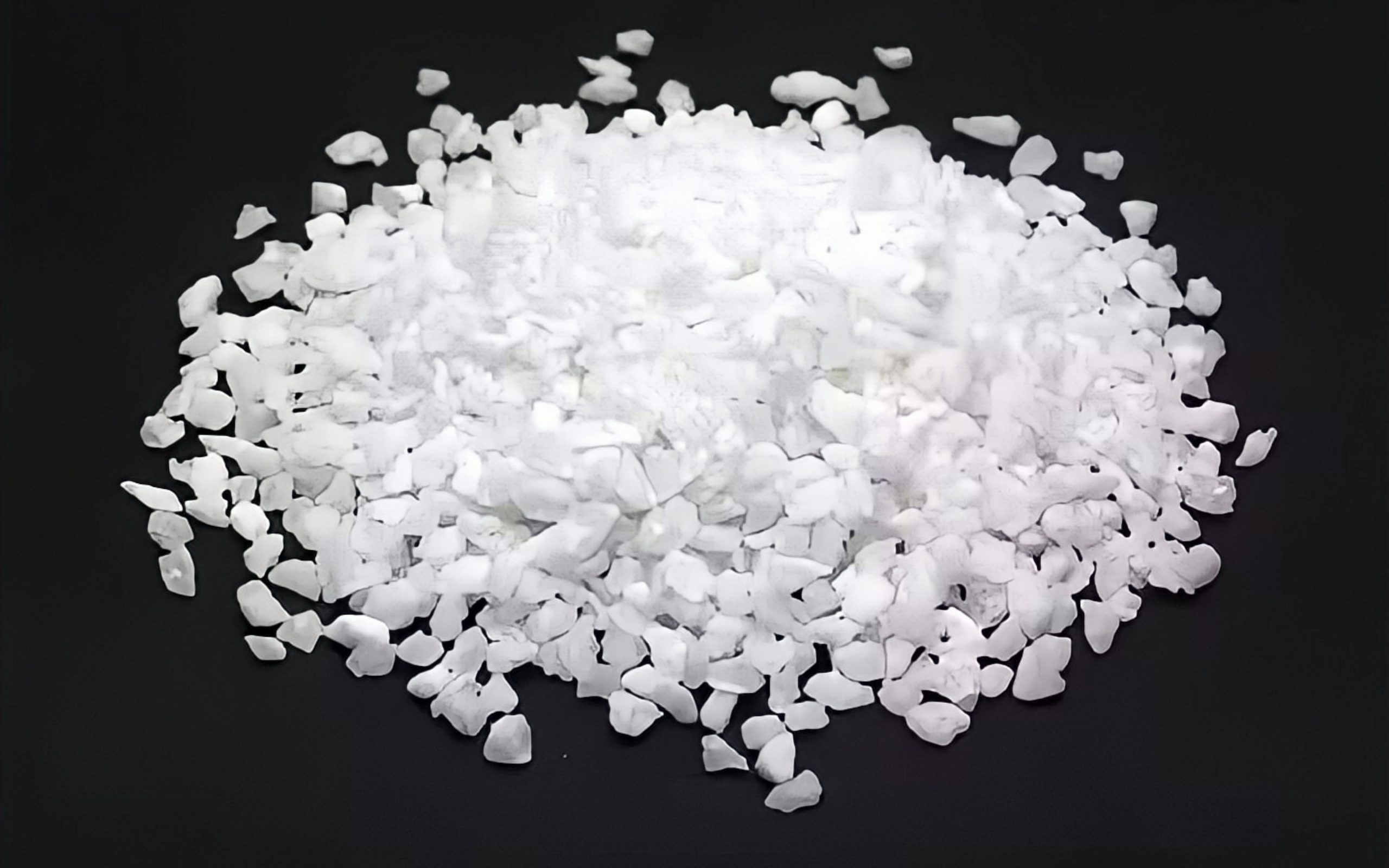
Granalla cerámica prismática
Ámbitos de aplicación
Las granallas cerámicas se utilizan ampliamente en diversas industrias debido a su excelente rendimiento, especialmente en industrias con elevados requisitos de tratamiento de superficies. He aquí algunos escenarios típicos de aplicación:
Aeroespacial
En la industria aeroespacial, el tratamiento superficial de los componentes es crucial para garantizar la seguridad y el rendimiento de las aeronaves. La gran dureza y resistencia al desgaste de las microesferas cerámicas las convierten en la opción ideal para el tratamiento de componentes críticos como álabes de turbina y carcasas de motor. Estas piezas suelen estar fabricadas con aleaciones de alta temperatura de gran dureza y geometrías complejas. Los granalla cerámicos pueden eliminar las capas de óxido y otras impurezas sin dañar la superficie de la pieza, proporcionando una buena base para su posterior procesamiento.
Electrónica de consumo
En la fabricación de productos electrónicos de consumo, como teléfonos inteligentes, tabletas y ordenadores portátiles, la calidad del tratamiento superficial afecta directamente al aspecto y la durabilidad del producto. El granallado cerámico se utiliza para limpiar y mejorar las superficies de las carcasas metálicas, mejorando la adherencia y el aspecto estético. Además, en la fabricación de componentes microelectrónicos, el granallado cerámico puede eliminar rebabas y residuos finos, garantizando la precisión y fiabilidad de los componentes.
Militar
Los equipos militares requieren estrictas normas de tratamiento de superficies. Los granos de arenado cerámicos se utilizan ampliamente para el tratamiento de superficies de blindajes de tanques, componentes de armas y otros equipos militares para eliminar eficazmente el óxido, los residuos de revestimiento y proporcionar una superficie lisa para nuevos revestimientos. Su eficaz efecto de limpieza y su larga vida útil las convierten en un material indispensable en la industria militar.
Fabricación de automóviles
En la fabricación de automóviles, el tratamiento de las superficies de las carrocerías y los componentes del motor es crucial. Las granallas cerámicas se utilizan para limpiar superficies de paneles de carrocería, llantas de aluminio y otras piezas metálicas. Pueden eliminar capas de óxido e impurezas, proporcionando una superficie lisa y uniforme para el posterior pintado y recubrimiento. Además, la durabilidad del granallado cerámico ayuda a reducir los costes de producción y a mejorar la eficacia.
Casos prácticos de aplicación
Caso 1: Industria aeroespacial
- Fondo: Boeing necesitaba procesar un gran número de álabes de turbina y carcasas de motor, lo que requería la eliminación de capas de óxido e impurezas sin dañar las piezas.
- Aplicación: Se utilizaron perlas de arenado cerámicas para el tratamiento con chorro de arena. Su elevada dureza y fuerza de corte eliminaron con éxito las capas de óxido superficiales manteniendo la precisión geométrica.
- Efecto: La calidad de la superficie de las piezas de trabajo mejoró significativamente, y la adherencia de los revestimientos en los pasos de procesamiento posteriores mejoró significativamente, aumentando la eficiencia de la producción en 20%.
Caso 2: Industria de la electrónica de consumo
- Fondo: Apple necesitaba tratar las carcasas metálicas de sus smartphones para mejorar el aspecto y la durabilidad del producto.
- Aplicación: Se utilizaron granallas cerámicas para limpiar y mejorar las superficies de las carcasas metálicas, mejorando la adherencia del revestimiento y la estética.
- Efecto: El aspecto del producto se hizo más suave y consistente, y la satisfacción de los consumidores respecto al aspecto del producto aumentó en 15%.
Caso 3: Industria militar
- Fondo: Lockheed Martin necesitaba tratar las superficies del blindaje de los tanques, eliminando el óxido y los revestimientos antiguos y proporcionando una superficie lisa para los nuevos revestimientos.
- Aplicación: Para el tratamiento con chorro de arena se eligieron perlas de granalla cerámica, que eliminan eficazmente el óxido y los revestimientos antiguos y proporcionan una buena base para los nuevos revestimientos.
- Efecto: La calidad del tratamiento de la superficie de los blindajes mejoró notablemente, y la adherencia y durabilidad de los nuevos revestimientos aumentaron significativamente, lo que redujo los costes de mantenimiento.

Un tanque blindado que requiere piezas precisas para ser ensamblado
Ventajas y retos
Ventajas
- Limpieza eficaz de superficies: La estructura angular de los granos de arenado cerámicos proporciona una mayor fuerza de corte y área de contacto con la superficie, lo que permite una eliminación más eficaz de los contaminantes e impurezas de la superficie.
- Larga vida útil: Su elevada dureza y resistencia al desgaste garantizan un excelente rendimiento durante un uso prolongado, lo que reduce la frecuencia de sustitución y, por tanto, los costes operativos.
- Gran adaptabilidad: Los granos de arenado cerámicos pueden adaptarse a diversas formas y materiales complejos, destacando especialmente en el tratamiento de piezas de gran dureza y geometría compleja.
Desafíos
- Desgaste del equipo: La elevada dureza de los granos de arenado cerámicos, aunque mejora la eficacia de la limpieza, puede acelerar el desgaste del equipo de arenado con el paso del tiempo. Por lo tanto, el mantenimiento del equipo y la sustitución de componentes se convierten en cuestiones críticas.
- Pérdida de cuentas: Durante el chorreado, la estructura angular de los granos cerámicos puede provocar un mayor índice de rotura, lo que afecta a su vida útil y a la eficacia de la limpieza. Es necesario controlar periódicamente el estado de los granos y proceder a su recuperación y sustitución.
¿Cómo conseguir los mejores resultados?
1. Elegir la especificación adecuada
La selección de la especificación adecuada del grano cerámico es crucial para obtener los mejores resultados de chorreado. El tamaño, la forma y la dureza de los granos deben coincidir con el material y los requisitos de tratamiento superficial de la pieza. Por lo general, los granos más grandes son adecuados para tratamientos superficiales gruesos, mientras que los más pequeños se utilizan para tratamientos finos. A continuación se indican las tres especificaciones de nuestras granallas cerámicas y sus respectivas funciones:
F120 63-125 micras
- Ventajas
- Alta eficacia de limpieza: El mayor tamaño de grano proporciona una mayor fuerza de impacto, adecuada para eliminar revestimientos gruesos, óxido o impurezas persistentes.
- Amplia gama de aplicaciones: Capaz de procesar diversos materiales, incluidos metales y hormigón, con efectos significativos.
- Menor índice de desgaste: Los granos más grandes no suelen desgastar excesivamente el equipo durante el tratamiento superficial, lo que prolonga la vida útil del equipo.
- Escenarios de uso
- Limpieza a fondo: Se utiliza para tratar revestimientos gruesos y óxido, como piezas de maquinaria de gran tamaño y equipos de ingeniería.
- Procesamiento de piezas de fundición: Adecuado para limpiar y desbarbar piezas de fundición, especialmente en las industrias de fundición y metalurgia.
- Preparación de la superficie: Tratamiento previo de superficies rugosas antes de la pulverización o el revestimiento para mejorar la posterior adherencia del revestimiento.
F170 45-90 micras
- Ventajas
- Efecto de limpieza uniforme: Las perlas de tamaño medio proporcionan efectos de limpieza uniformes, adecuados para revestimientos e impurezas de grosor medio.
- Tratamiento eficaz de superficies: Equilibra la eficacia de la limpieza y el consumo de microesferas, aplicable a una amplia gama de aplicaciones.
- Menor generación de polvo: En comparación con las perlas de mayor tamaño, la F170 produce menos polvo durante el procesamiento, lo que mejora el entorno de trabajo.
- Escenarios de uso
- Tratamiento superficial fino: Se utiliza en la fabricación de automóviles, electrónica, etc., para limpiar revestimientos finos o impurezas finas.
- Limpieza estándar: Adecuado para diversas aplicaciones de limpieza estándar, como el tratamiento de superficies metálicas en general y la eliminación de óxido ligero.
- Preparación de la superficie para pintar: Eficaz para preparar superficies para pintar o revestir, asegurando una base lisa y limpia.
F20 50-63 micras
- Ventajas
- Alta precisión: El pequeño tamaño de la perla proporciona efectos de limpieza precisos, adecuados para trabajos detallados y piezas de precisión.
- Buen acabado superficial: Capaz de lograr un acabado superficial de alta calidad, mejorando el aspecto y la calidad funcional de la pieza.
- Menor desgaste del equipo: Los granos más pequeños provocan un menor desgaste del equipo, prolongando su vida útil.
- Escenarios de uso
- Limpieza de piezas de precisión: Se utiliza para tratar piezas pequeñas o delicadas en electrónica, aeroespacial, etc.
- Mejora de la superficie: Adecuado para mejorar la calidad de la superficie, como la eliminación de rebabas finas y la obtención de un acabado liso.
- Microprocesamiento: Ideal para procesar piezas pequeñas o piezas complejas, donde la precisión y la calidad de la superficie son cruciales.
2. Optimización de las condiciones de funcionamiento
Para maximizar la eficacia de las bolas de chorreado cerámicas, es esencial optimizar las condiciones de funcionamiento durante el proceso de chorreado. Esto incluye factores como la presión de chorreado, el ángulo de chorreado y el tiempo de chorreado. Una presión de chorreado adecuada garantiza que los granos impacten eficazmente en la superficie de la pieza, mientras que el ángulo y el tiempo de chorreado correctos ayudan a evitar un desgaste excesivo y un tratamiento desigual. (Puede consultar este artículo)
3. Mantenimiento del equipo y recuperación de microesferas
El mantenimiento regular del equipo de chorreado es crucial para garantizar su funcionamiento estable a largo plazo. Es necesario comprobar periódicamente el desgaste del equipo y sustituir rápidamente las piezas desgastadas. Además, la recuperación y reutilización de los granos también ayuda a reducir costes y minimizar los residuos. Mediante un cribado y una limpieza adecuados, los granos usados pueden recuperarse eficazmente, alargando su vida útil.
Beneficios económicos y respeto del medio ambiente
Análisis coste-eficacia
El coste inicial de los granalla cerámicos es más elevado, pero su excelente resistencia a la abrasión y su larga vida útil permiten reducir los costes unitarios con el tiempo. En comparación con otras granallas, los granos cerámicos ofrecen importantes ventajas económicas en la producción a gran escala debido a su eficaz efecto limpiador y a su prolongada vida útil. En concreto, los costes globales de producción pueden reducirse significativamente al disminuir la frecuencia de las sustituciones y los costes de mantenimiento.
Debate sobre el respeto del medio ambiente
Debido a que sus componentes principales son el óxido de circonio y el sílice, que tienen un impacto medioambiental mínimo durante su producción y uso, las granallas de cerámica también son respetuosas con el medio ambiente. Además, son fáciles de reciclar y reutilizar, lo que contribuye a reducir los residuos y disminuir la carga medioambiental. La baja generación de polvo durante su uso también contribuye a mejorar el entorno de trabajo. Además, la introducción de procesos de producción y materiales ecológicos puede mejorar aún más su comportamiento medioambiental.
Futuras tendencias de desarrollo
Avances tecnológicos
Con los avances en la ciencia de los materiales y la tecnología de fabricación, se espera que los procesos de producción y el rendimiento de los granalladores cerámicos sigan mejorando. La aplicación de nuevos materiales cerámicos y de técnicas de fabricación más refinadas hará que los granalladores cerámicos sean más eficientes y económicos.
Demanda del mercado
A medida que se amplían las aplicaciones industriales, crece también la demanda de granalla cerámica. En el futuro, nuevas industrias emergentes y escenarios de aplicación impulsarán el desarrollo del mercado, como la nueva industria energética y los campos de alta tecnología.
Protección del medio ambiente y desarrollo sostenible
Con el telón de fondo de una normativa medioambiental cada vez más estricta, la producción y el uso de granallas cerámicas se centrarán más en la protección del medio ambiente y el desarrollo sostenible. Los avances futuros pueden incluir la reducción del impacto ambiental durante la producción y el aumento de la tasa de reciclaje de las microesferas.
Los granos de arenado cerámicos, con su forma angular única y su elevada dureza, ofrecen numerosas ventajas para las aplicaciones de tratamiento de superficies. Proporcionan una limpieza eficaz, una larga vida útil y se adaptan a diversos materiales y geometrías complejas. A pesar de algunas dificultades, como el desgaste del equipo y la pérdida de microesferas, una selección, mantenimiento y optimización adecuados pueden maximizar sus beneficios. En industrias como la aeroespacial, la electrónica de consumo, la militar y la automovilística, los granalladores cerámicos desempeñan un papel crucial en la consecución de tratamientos superficiales de alta calidad y en la mejora de la eficiencia global de la producción. Sus ventajas económicas, como la rentabilidad y el aumento de la eficacia, las convierten en una opción valiosa para diversas tareas de tratamiento de superficies.
Filtros