Comparación de perlas cerámicas y granalla de acero en componentes de turbinas
4 de enero de 2025

Como componente clave en los sectores aeroespacial y energético, los componentes de las turbinas tienen unos requisitos extremadamente exigentes en cuanto a su rendimiento y fiabilidad. El shot peening es un importante medio técnico para optimizar la superficie de los componentes de las turbinas mediante la introducción de tensiones residuales de compresión para mejorar la vida útil a la fatiga y la resistencia a la corrosión de los materiales.
Las granallas cerámicas y las granallas de acero son los dos medios de granallado más utilizados. Aunque ambos pueden lograr un cierto efecto de refuerzo, existen diferencias significativas en cuanto a rendimiento, durabilidad y coste. En este artículo se analizan estos puntos de comparación para ayudar a los usuarios a elegir mejor el medio de granallado adecuado.
Perlas de cerámica y granalla de acero
Perlas cerámicas de granallado son un tipo de medios de granallado fabricados con materiales cerámicos de gran pureza, y los colores habituales son el blanco o el gris claro. Tienen una dureza elevada, normalmente entre 9,0 de dureza Mohs, y son adecuados para el tratamiento fino de superficies. La forma suele ser esférica o casi esférica, con gran uniformidad y consistencia. La densidad suele estar entre 2,5-3,0 g/cm³. En comparación con los medios de granallado metálicos, sus características de ligereza ayudan a reducir el impacto sobre el sustrato y a mejorar la calidad y el efecto de la superficie.
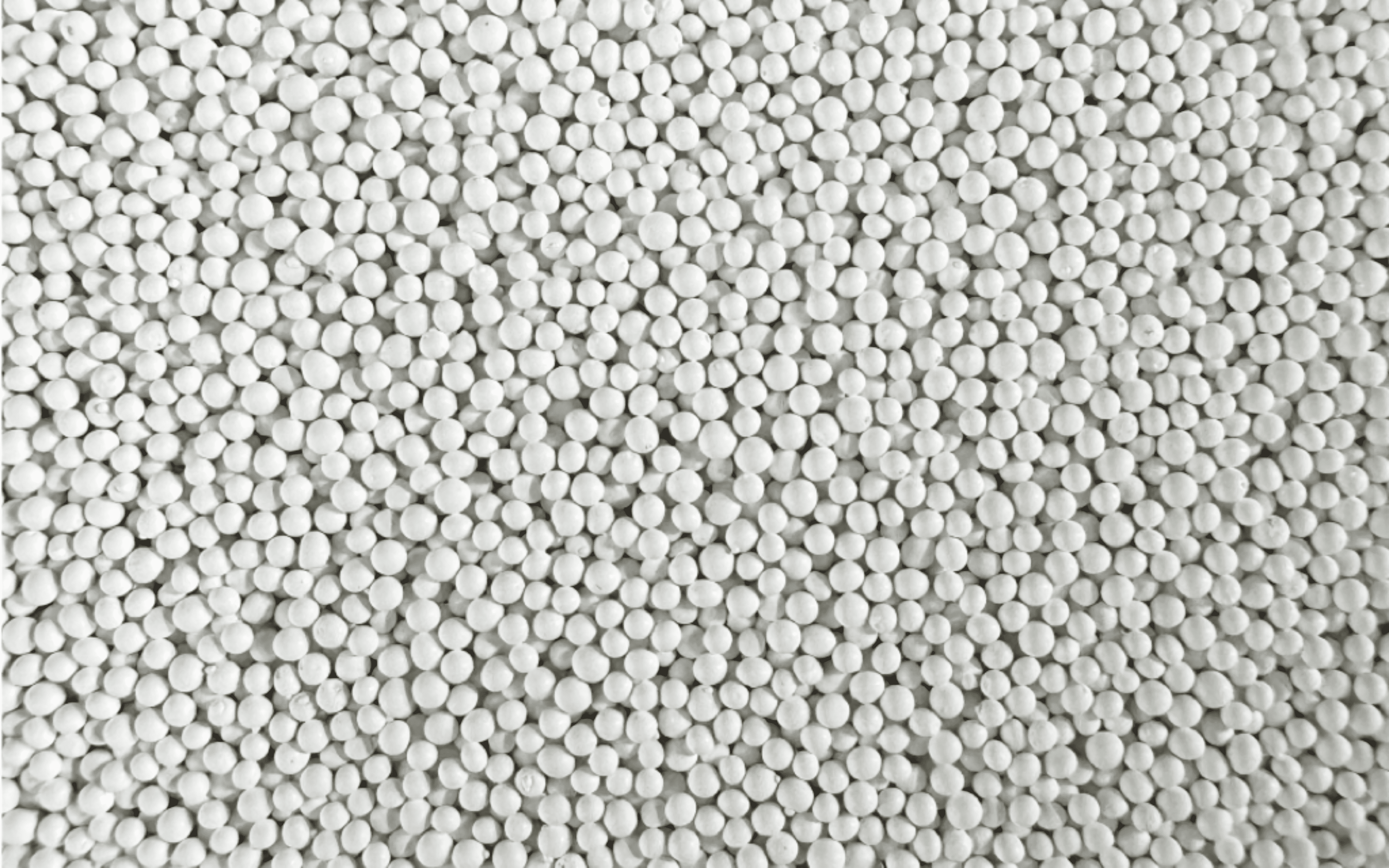
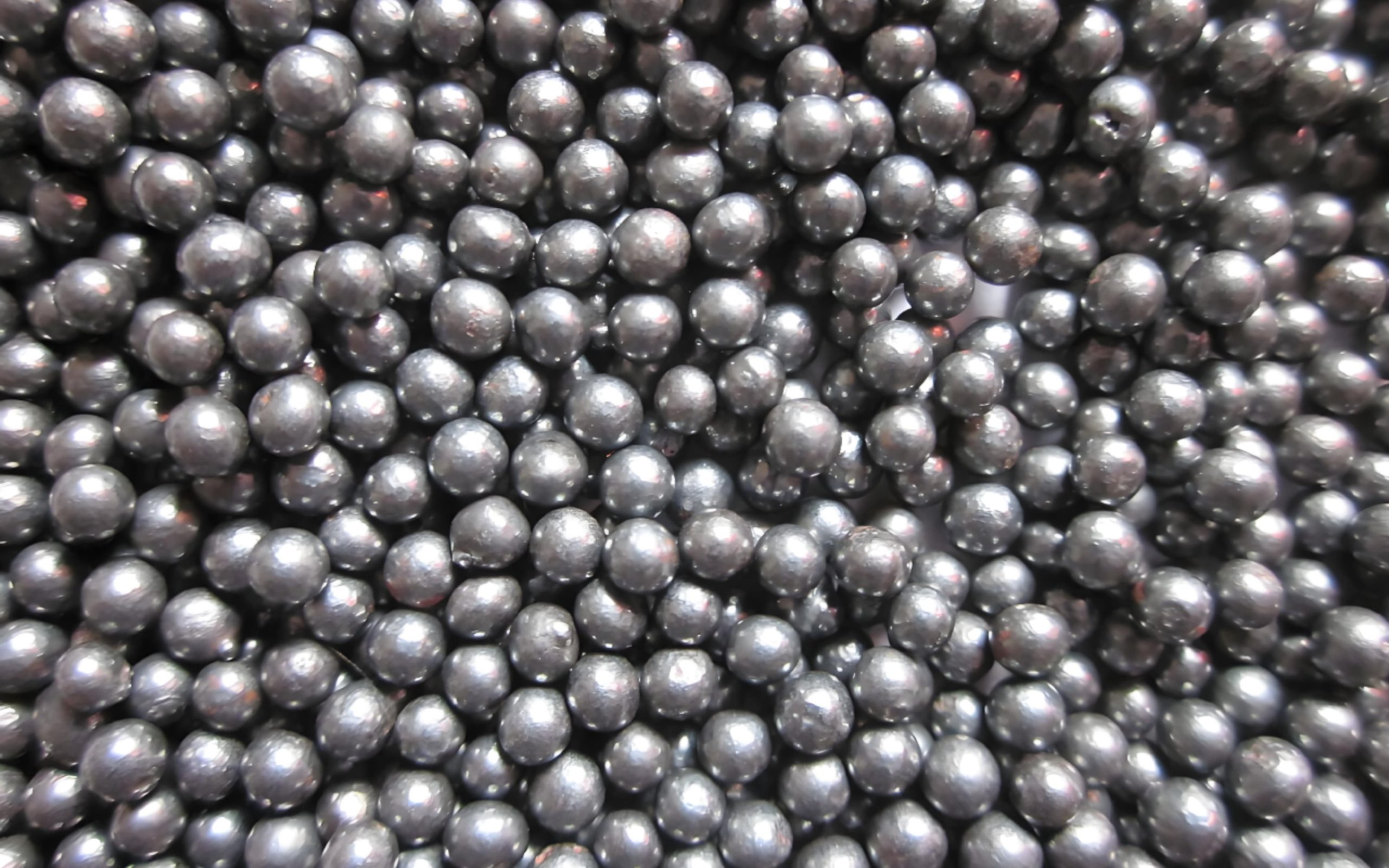
Granalla de acero es un medio de granallado fabricado con material de acero de alto contenido en carbono, normalmente de color gris metálico, con una dureza elevada de unos 45-55 HRC (dureza Rockwell, inferior a la de una granalla cerámica). La granalla de acero es generalmente esférica o casi esférica, con una alta densidad de 7,5-8,0 g/cm³. Su dureza la hace adecuada para el tratamiento superficial de piezas sometidas a grandes fuerzas de impacto. Puede eliminar eficazmente incrustaciones de óxido e impurezas y reforzar la superficie. Funciona bien en el tratamiento de superficies rugosas y en aplicaciones de shot peening con grandes cargas.
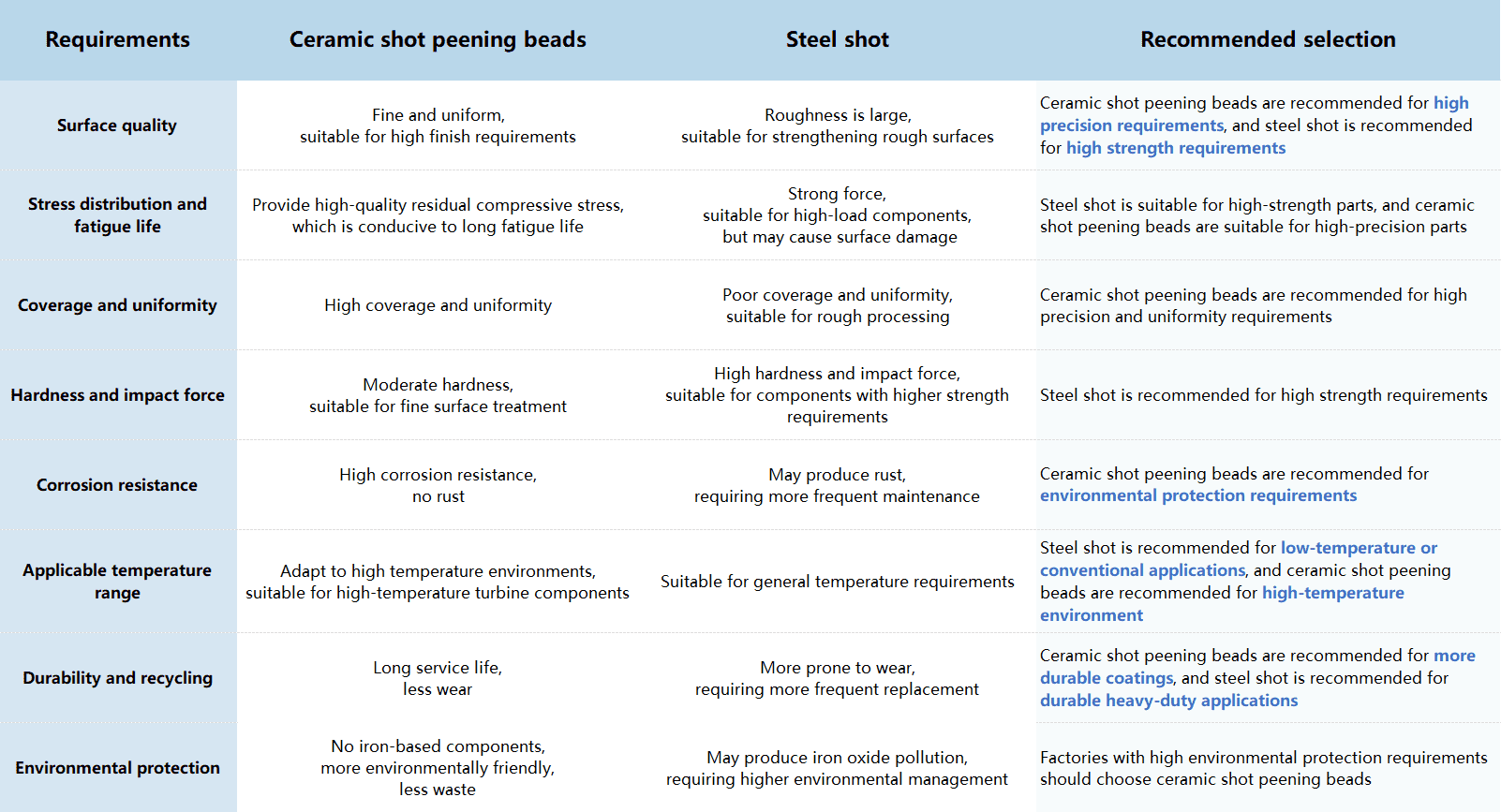
Comparación de los efectos del shot peening en piezas de turbinas
- Rugosidad de la superficie
Aunque las microesferas cerámicas de granallado tienen una dureza elevada, no dañan la superficie y pueden producir una baja rugosidad superficial manteniendo la eficacia del proceso. Suele ser adecuado para piezas de turbina con elevados requisitos de acabado superficial, como los álabes de turbina de los motores aeronáuticos.
Aunque tiene una gran fuerza de impacto, es fácil que produzca una gran rugosidad y no es adecuado para piezas de turbinas que requieren un tratamiento superficial delicado.
- Acabado superficial
La superficie de la granalla de cerámica de circonio es lisa, y no es fácil que se formen arañazos o abolladuras tras el impacto, lo que permite conseguir un efecto de tratamiento superficial uniforme.
La granalla de acero suele estar hecha de acero con alto contenido en carbono o de acero aleado. Aunque el acero tiene una gran dureza, su estructura de partículas es relativamente frágil. Es fácil que se deforme o se desintegre en condiciones de alta intensidad o uso frecuente, lo que puede provocar un efecto de impacto desigual, afectando así al acabado general.
- Distribución de tensiones
Las microesferas cerámicas tienen un tamaño uniforme y pueden introducir una profundidad uniforme y moderada de tensión de compresión residual en la capa superficial, lo que contribuye a mejorar la vida a fatiga. La profundidad de la distribución de la tensión de compresión suele alcanzar 0.1-0.15 mm, que es la opción preferida para piezas sensibles a la tensión.
La granalla de acero puede introducir una distribución más profunda de la tensión de compresión residual (la profundidad puede alcanzar más del 0,2 mm) debido a su mayor fuerza de impacto, pero la uniformidad de la distribución de las tensiones puede no ser tan buena como la de las bolas de granallado cerámicas, lo que tiene cierta repercusión en la vida útil de las piezas.
- Cobertura
Las perlas cerámicas tienen una gran consistencia en tamaño y forma, y el proceso de granallado puede lograr fácilmente una mayor cobertura, y la eficiencia de cobertura suele ser 10%-15% superior a la de la granalla de acero.
Las granallas de acero son propensas a una cobertura local insuficiente debido a las diferencias de forma y dureza, y puede requerir tiempo adicional o múltiples granallados para cumplir los requisitos.
- Uniformidad
Las granallas cerámicas se componen principalmente de óxido de circonio (que representa 60%-70%), combinado con otros óxidos. La estructura cristalina única tiene una excelente resistencia a la compresión y tenacidad, no es fácil de romper, y es especialmente adecuada para entornos de trabajo de alta intensidad e impactos repetidos. Puede mantener un efecto de impacto consistente durante el proceso de shot peening y mejorar la uniformidad del tratamiento.
Sin embargo, la tasa de rotura de las granallas de acero es mayor, y pueden producirse partículas de diferentes tamaños tras el granallado, lo que afecta a la consistencia del proceso de granallado.
Comparación de resultados
- Resistencia a la corrosión
Los cordones de granallado cerámicos tienen una excelente resistencia a la corrosión y no se ven afectados fácilmente por la humedad y los productos químicos. Son adecuados para piezas expuestas a entornos corrosivos durante mucho tiempo. Por ejemplo, en condiciones marinas o de alta humedad, la granalla cerámica de circonio puede proteger eficazmente la integridad de la superficie de las piezas de turbinas.
Las granallas de acero se ven fácilmente afectadas por la humedad y los productos químicos. Su uso prolongado puede provocar óxido, lo que perjudica la calidad de la superficie de las piezas de la turbina. Se requiere un tratamiento antioxidante adicional, lo que aumenta el coste y la complejidad de uso.
- Rango de temperatura aplicable
Los materiales cerámicos tienen una gran resistencia al calor y suelen mantener una estructura estable en entornos de altas temperaturas. El material no se ablanda ni cambia de forma. Son adecuados para piezas de alta temperatura, como los álabes de turbina de los motores de aviación.
Las granallas de acero pueden fallar debido a la oxidación o a la degradación del rendimiento en entornos de temperatura ultra alta y no son adecuadas para operaciones de granallado a temperaturas extremadamente altas.
Durabilidad y coste
- Durabilidad
Los granalla cerámicos tienen una gran resistencia al desgaste y una vida útil mucho más larga que la granalla de acero. Los estudios han demostrado que, en las mismas condiciones, los granalla cerámicos pueden utilizarse 2-3 veces más que la granalla de acero.
Debido a razones estructurales, la granalla de acero es más propensa a agrietarse durante el uso de alta frecuencia, lo que conduce al fallo, y su vida útil es significativamente inferior a la de las bolas de granallado cerámicas.
- Tasa de reciclaje
Las perlas cerámicas tienen un alto índice de reciclado y pueden volver a utilizarse tras una sencilla limpieza. La tasa de pérdida es baja, lo que ayuda a reducir el consumo de medios de la operación global de granallado.
La tasa de reciclaje de la granalla de acero es inferior a la de la granalla de cerámica de circonio. Debido al agrietamiento y la deformación, tiene mayores pérdidas y es necesario sustituirla y manipularla con más frecuencia, lo que aumenta la complejidad y el coste del mantenimiento.
- Economía
El coste unitario de la granalla cerámica de circonio es más elevado, pero su durabilidad y alto índice de reciclado la hacen más económica para su uso a largo plazo. La granalla de acero tiene un coste de adquisición inicial bajo y es adecuada para proyectos con presupuestos limitados o proyectos a corto plazo. Debe prestarse más atención a las operaciones de granallado de alta intensidad.
Comparación de escenarios de aplicación
- Requisitos de alta precisión
Las perlas cerámicas de granallado dan buenos resultados en el tratamiento de piezas de alta precisión, como álabes de turbina y piezas de motores de aviación. Con una dureza moderada y un tamaño de partícula uniforme, pueden proporcionar efectos de refuerzo superficial de alta calidad sin dañar la superficie.
Especialmente en el caso de piezas con detalles complejos y elevados requisitos de calidad superficial, como las ranuras y los bordes de los álabes de turbina, estas piezas suelen requerir un control preciso de la fuerza de impacto y la uniformidad del medio de granallado.
- Requisitos de alta resistencia
La granalla de acero presenta ventajas significativas en piezas que requieren un granallado de alta intensidad, como los cojinetes de turbinas de gran tamaño y las piezas que soportan presión, debido a su gran fuerza de impacto.
Adecuado para el refuerzo superficial de piezas metálicas gruesas y pesadas, se puede conseguir rápidamente una tensión de compresión residual profunda, aumentando así la vida a fatiga de las piezas.
- Requisitos de protección del medio ambiente
Las perlas cerámicas no contienen componentes a base de hierro, producen menos polvo y contaminantes y cumplen las normas de protección del medio ambiente. Los residuos generados durante su uso también son relativamente pequeños, lo que contribuye a reducir los costes de gestión de la protección medioambiental de la fábrica.
Las granallas de acero pueden producir partículas de óxido de hierro tras su desgaste, lo que requiere una elevada gestión medioambiental. La sustitución frecuente también aumentará la cantidad de eliminación de residuos, lo que no es adecuado para entornos de producción que hacen hincapié en la fabricación ecológica.
Las bolas de cerámica y las granallas de acero tienen ventajas únicas y son adecuadas para las diferentes necesidades de shot peening de componentes de turbinas.
Las microesferas cerámicas tienen un buen rendimiento en el tratamiento superficial de álabes de turbina y componentes complejos con requisitos de alta precisión y pueden proporcionar efectos de refuerzo superficial uniformes y detallados, que son adecuados para aplicaciones que requieren una alta calidad superficial y una larga vida útil. Las granallas de acero, por su parte, presentan ventajas incomparables con una mayor fuerza de impacto cuando se procesan componentes que requieren una profunda tensión de compresión, como los cojinetes de turbinas de gran tamaño y los componentes que soportan presión.
Los dos medios tienen su importancia, y la selección debe basarse en los requisitos específicos de rendimiento, los requisitos medioambientales y el presupuesto económico de los componentes de la turbina.
Con el continuo avance de la tecnología y los materiales de shot peening, es posible que en el futuro aparezcan medios de shot peening más innovadores, que ofrezcan soluciones más precisas y respetuosas con el medio ambiente para el tratamiento eficaz de los componentes de las turbinas.
Filtros