Cómo eliminar eficazmente los revestimientos cerámicos?
30 de octubre de 2024
En el campo de la fabricación de precisión, uno de los principales retos a los que se enfrentan los clientes es cómo eliminar eficazmente los revestimientos cerámicos sin dañar el sustrato. Con la creciente aplicación de revestimientos cerámicos en sectores como el aeroespacial, los dispositivos médicos y la automoción, es especialmente importante garantizar la calidad y consistencia de la superficie tras la eliminación del revestimiento. Los métodos tradicionales de eliminación dificultan el equilibrio entre eficacia, protección del medio ambiente y precisión, lo que se traduce en un aumento de los costes de producción, daños fáciles al sustrato y afecta al rendimiento y la vida útil del producto final. Por lo tanto, elegir un proceso que pueda eliminar los revestimientos de forma eficaz, precisa y segura se ha convertido en un punto delicado que muchas industrias necesitan resolver urgentemente.
Demanda industrial de eliminación de revestimientos cerámicos
- Escenarios de aplicación de los recubrimientos cerámicos
Los revestimientos cerámicos se utilizan ampliamente en el campo de la fabricación de precisión, especialmente en industrias como la aeroespacial y la automovilística, para proteger las piezas de entornos extremos como el desgaste, la corrosión y las altas temperaturas. A continuación se detallan las necesidades específicas de los revestimientos cerámicos en distintas aplicaciones:
- Gran resistencia al desgaste y a la corrosión: Por ejemplo, piezas como los álabes de las turbinas, las paredes interiores de las cámaras de combustión y los pistones de los motores de los automóviles en el sector aeroespacial a menudo tienen que trabajar en entornos de alta temperatura y alta presión. Los revestimientos cerámicos prolongan la vida útil de las piezas formando una barrera protectora de gran dureza y resistente a los productos químicos.
- Efecto barrera térmica: En entornos de temperaturas extremadamente altas (como turbinas de gas y motores de combustión interna), los revestimientos cerámicos pueden actuar como barreras térmicas para ayudar a mantener la temperatura de funcionamiento de las piezas, reducir el estrés térmico y mejorar la estabilidad del rendimiento.
- Diversidad de necesidades industriales: Los revestimientos cerámicos no sólo se utilizan en los sectores de la aviación y la automoción, sino también en equipos de perforación de la industria del petróleo y el gas, piezas sensibles de la industria electrónica, etc. En estos campos, la demanda de eliminación de revestimientos cerámicos sigue aumentando con las actualizaciones de productos y los ciclos de mantenimiento, y se necesitan métodos de eliminación más precisos para garantizar el rendimiento de las piezas tras las actualizaciones.
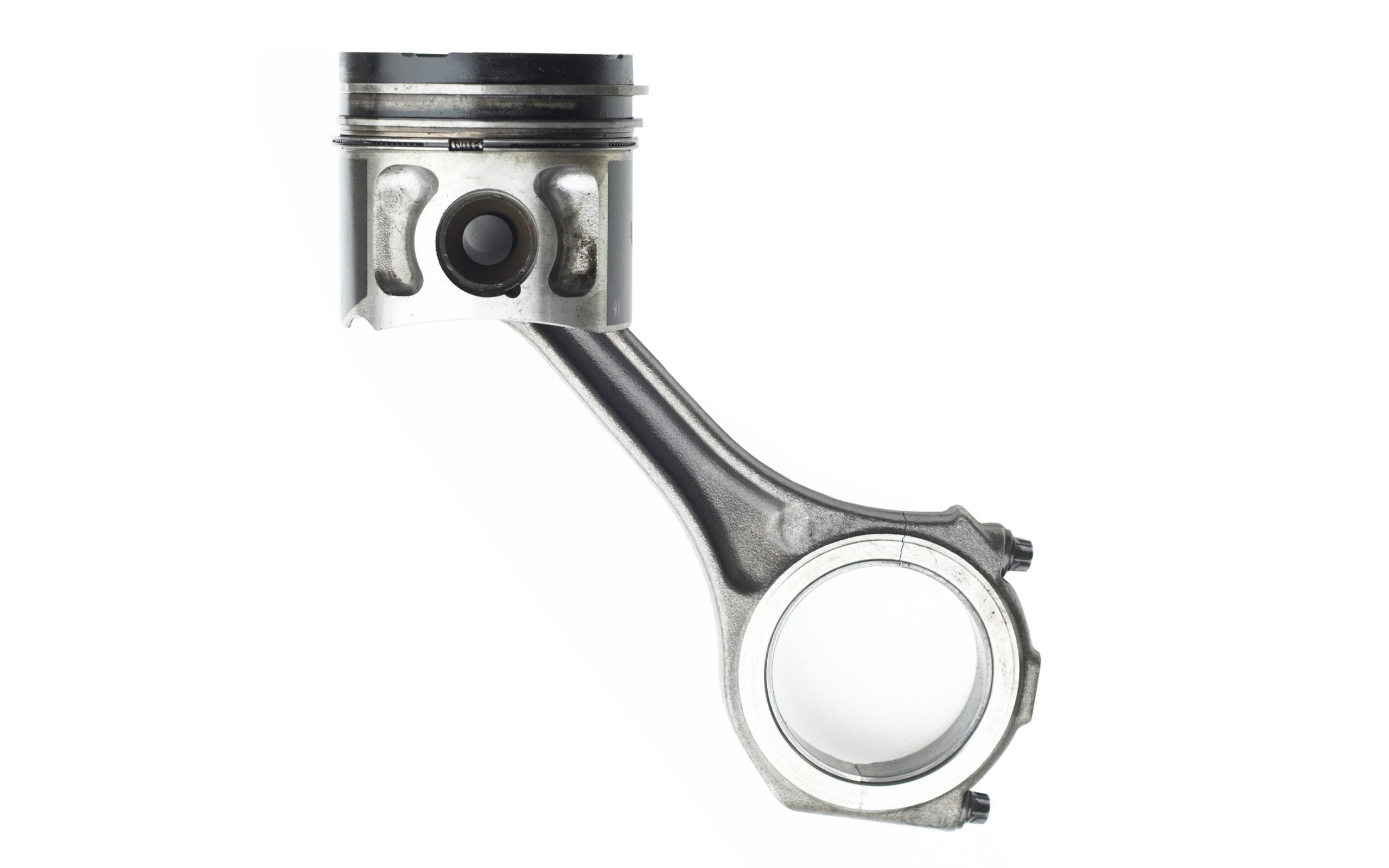
Pistón y biela del motor
- Dificultades para eliminar revestimientos antiguos
Sin embargo, a medida que aumenta el tiempo de uso, el revestimiento cerámico envejecerá o se desgastará gradualmente, haciendo que pierda su efecto protector o incluso se agriete, lo que afectará al funcionamiento de las piezas. Por lo tanto, para prolongar la vida útil de las piezas, es necesario eliminar el revestimiento antiguo y volver a aplicar uno nuevo, pero en diversas industrias, la eliminación de los revestimientos antiguos no suele ser tan fácil. A continuación se exponen los principales puntos problemáticos:
- Problemas de adherencia y residuos de revestimientos antiguos: Los revestimientos cerámicos suelen tener una fuerte adherencia y una gran dureza, lo que dificulta el proceso de eliminación. Los métodos tradicionales dificultan la eliminación completa de los residuos sin dañar el sustrato, lo que puede afectar a la uniformidad de los revestimientos posteriores.
- Formas complejas y partes vulnerables de partes: Los álabes de los motores de los aviones, las piezas de los motores de los automóviles, etc. suelen tener formas geométricas complejas, y es fácil dañar las estructuras pequeñas o las esquinas afiladas al retirar el revestimiento.
- Diferencias de grosor y material: El grosor, la dureza y el material del revestimiento varían, lo que impone mayores exigencias al proceso de eliminación. Es necesario elegir el método de eliminación adecuado para garantizar el mejor efecto.
- Normas estrictas para la eliminación de revestimientos cerámicos en la fabricación de precisión
Especialmente en la fabricación de precisión, la calidad de la superficie y la protección del sustrato de las piezas son cruciales, por lo que existen requisitos estrictos para el proceso de eliminación del revestimiento.
- La necesidad de proteger el sustrato: En industrias como la aeroespacial y la médica, el sustrato de las piezas suele estar hecho de metales o aleaciones caros de alto rendimiento, y cualquier eliminación inadecuada puede causar daños al sustrato. Especialmente en el caso de la cámara de combustión o los álabes guía del motor, si la resistencia del sustrato se debilita al retirar el revestimiento, afectará al rendimiento y la seguridad de las piezas.
- Eficacia y control de costes: Los métodos tradicionales de eliminación de revestimientos suelen ser lentos y costosos, y pueden provocar que las piezas se deformen o contaminen debido al calor. Las empresas de fabricación modernas necesitan un proceso que garantice la eliminación eficaz del revestimiento y proteja el sustrato para acortar los ciclos de producción y reducir los costes de mantenimiento.
Ventajas del chorro de arena en la eliminación de revestimientos cerámicos
En el ámbito industrial, el chorro de arena se ha convertido gradualmente en una opción clave para eliminar revestimientos cerámicos. Sus ventajas se reflejan principalmente en el control preciso, la protección del medio ambiente y la adaptabilidad a formas complejas. A continuación se describen detalladamente las principales características del chorro de arena y los distintos sistemas de eliminación.
- Características del chorro de arena
- Control preciso de la eliminación del espesor: Durante la eliminación de revestimientos cerámicos, el chorro de arena puede funcionar con precisión en función del grosor del revestimiento y del tipo y la complejidad del sustrato. Por ejemplo, ajustando la presión del chorro de arena, el caudal y el ángulo, se puede controlar eficazmente el grosor de la eliminación. Especialmente en la eliminación de capas finas de revestimiento, esta precisión evita el riesgo de desgaste excesivo del sustrato.
- Respetuoso con el medio ambiente y sin productos químicos: En comparación con los métodos de eliminación con disolventes químicos, el chorreado con arena se basa totalmente en el impacto físico para eliminar los revestimientos cerámicos, lo que reduce la contaminación química del medio ambiente. El chorro de arena es especialmente adecuado en industrias con elevados estándares de protección medioambiental, como la aeroespacial y la fabricación de equipos médicos.
- Adaptarse a formas complejas: Los métodos tradicionales de eliminación mecánica o disolución química presentan los problemas de la baja eficacia y el tratamiento inadecuado de los bordes cuando se trata de piezas de formas complejas. La flexibilidad del proceso de chorro de arena le permite afrontar fácilmente estos retos. Por ejemplo, en superficies estructurales especiales como cuchillas, esquinas afiladas y cavidades interiores se pueden conseguir efectos de eliminación uniformes, y el error humano es pequeño, lo que resulta adecuado para los requisitos de procesamiento estandarizado en la producción en serie.
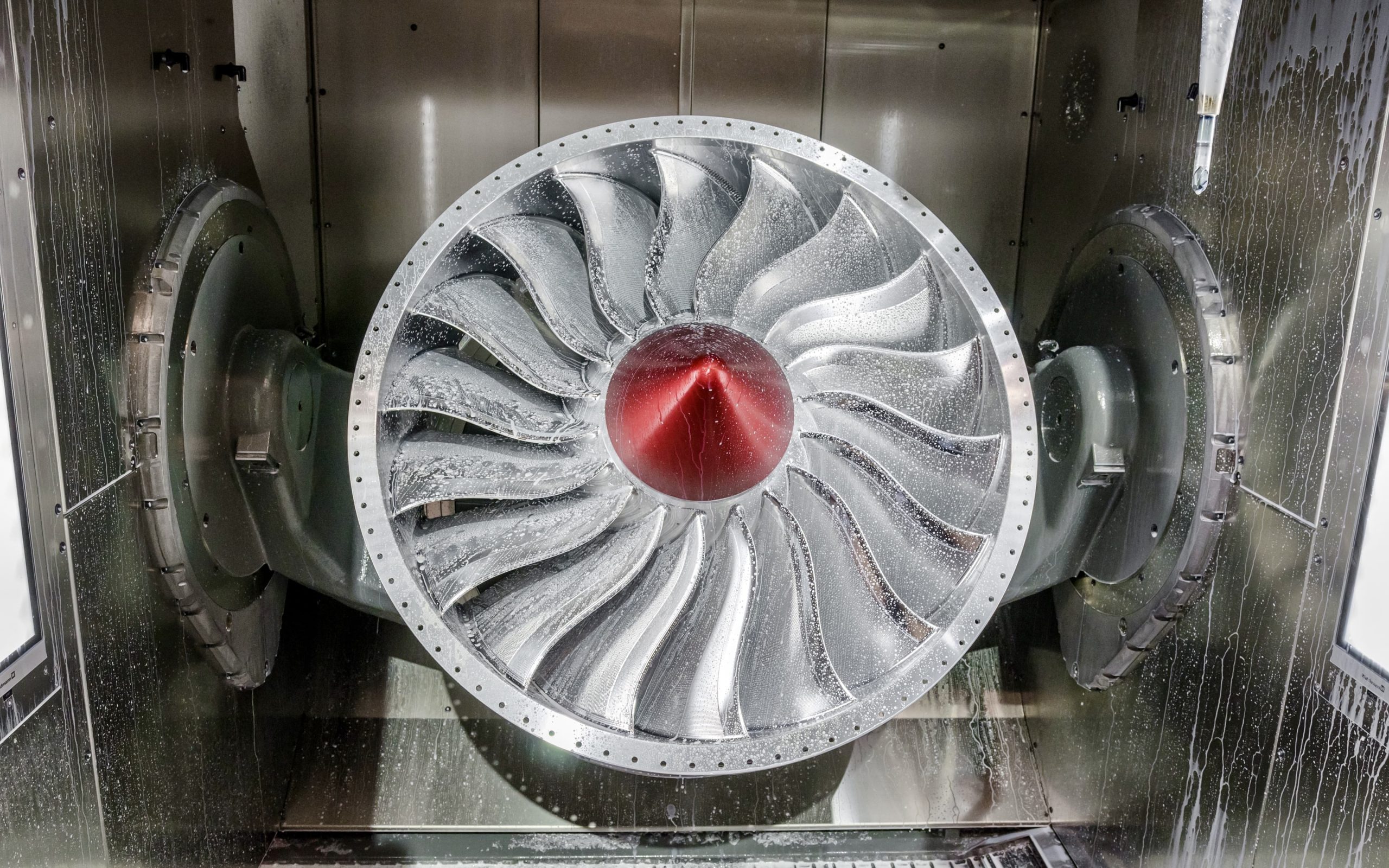
turbina
- Eficacia de la eliminación por chorro de arena
En comparación con los métodos tradicionales de rectificado mecánico y eliminación química de disolventes, el proceso de arenado presenta ventajas evidentes en cuanto a rapidez y control de calidad:
- Eliminación rápida de revestimientos: El arenado desprende el revestimiento mediante el impacto a alta velocidad de partículas sobre la superficie. En comparación con la eliminación química, puede ahorrar tiempo de procesamiento y evitar el largo proceso de inmersión y disolución del revestimiento. Es adecuado para líneas de producción con altos requisitos de eficacia de eliminación.
- Reducir el impacto térmico en la pieza de trabajo: El proceso de eliminación mecánica suele provocar la deformación de la pieza debido a la generación de calor por fricción, mientras que las partículas utilizadas en el arenado tienen una temperatura más baja y no generan tensión térmica en el sustrato, lo que garantiza la precisión y la integridad estructural de las piezas.
- Soluciones de eliminación para diferentes espesores
El proceso de arenado puede conseguir una eliminación eficaz de revestimientos de distintos grosores seleccionando diferentes medios de arenado. En la práctica industrial, existen las siguientes soluciones de optimización para revestimientos cerámicos finos y gruesos:
- Eliminación de revestimientos cerámicos finos: Granalla fina (por ejemplo granalla ultrafina de óxido de aluminio) pueden controlar con precisión el grosor de la eliminación, lo que resulta especialmente adecuado para reparaciones menores de piezas de precisión. Las partículas de óxido de aluminio son duras y finas, y producen una fuerza de impacto débil pero estable sobre revestimientos finos, haciendo que el revestimiento se desprenda gradualmente sin afectar a la microestructura del sustrato.
- Eliminación de revestimientos cerámicos gruesos: Los revestimientos cerámicos gruesos suelen requerir medios de arenado de mayor resistencia (como el carburo de silicio), que tiene una gran capacidad de corte y una alta resistencia al desgaste. Al eliminar capa por capa, pueden evitarse los daños por impacto en el sustrato causados por el pelado de grandes superficies, lo que resulta adecuado para piezas con elevados requisitos de resistencia al calor y dureza. Además, la dureza y el filo de las partículas de carburo de silicio permiten que cada impacto elimine con precisión el grosor preestablecido, mejorando la eficacia de la eliminación.
Medios de chorreado adecuados para eliminar revestimientos cerámicos
Para satisfacer las necesidades de eliminación de revestimientos cerámicos de distintos grosores y materiales, es fundamental seleccionar los medios de chorreado adecuados. Las características del medio de chorreado determinan la eficacia del proceso de eliminación, el efecto de protección del sustrato y el grado de refinamiento del tratamiento. A continuación se presentan en detalle cuatro abrasivos de uso común y se analizan sus respectivas ventajas, desventajas y escenarios de aplicación típicos.
- Alúmina
- Características básicas: La alúmina es blanca o marrón, mayoritariamente en forma de partículas angulares, con gran dureza y buena resistencia al desgaste. Los bordes afilados de las partículas de óxido de aluminio la hacen adecuada para eliminar revestimientos cerámicos más finos, proporcionando una fuerza de impacto estable y evitando al mismo tiempo un desgaste excesivo del sustrato.
- Escenarios de aplicación: En industrias de gran demanda, como la aeroespacial y la automovilística, el chorreado con óxido de aluminio se utiliza a menudo para reparaciones menores de piezas de precisión. Por ejemplo, cuando el revestimiento está desgastado de forma irregular o necesita ser repintado, el óxido de aluminio puede eliminar uniformemente el revestimiento antiguo de la superficie sin afectar a la planitud del sustrato. Esta característica lo hace eficaz y controlable a la hora de eliminar revestimientos finos, especialmente adecuado para la necesidad de un tratamiento detallado de la superficie de las piezas, como la limpieza de la superficie y el desbastado de la superficie de piezas pequeñas. Después de utilizar óxido de aluminio para eliminar capas finas de revestimientos cerámicos, la superficie de la pieza puede permanecer relativamente lisa y el sustrato casi no se ve afectado, cumpliendo los estrictos requisitos de la industria de fabricación de precisión para la protección del sustrato.
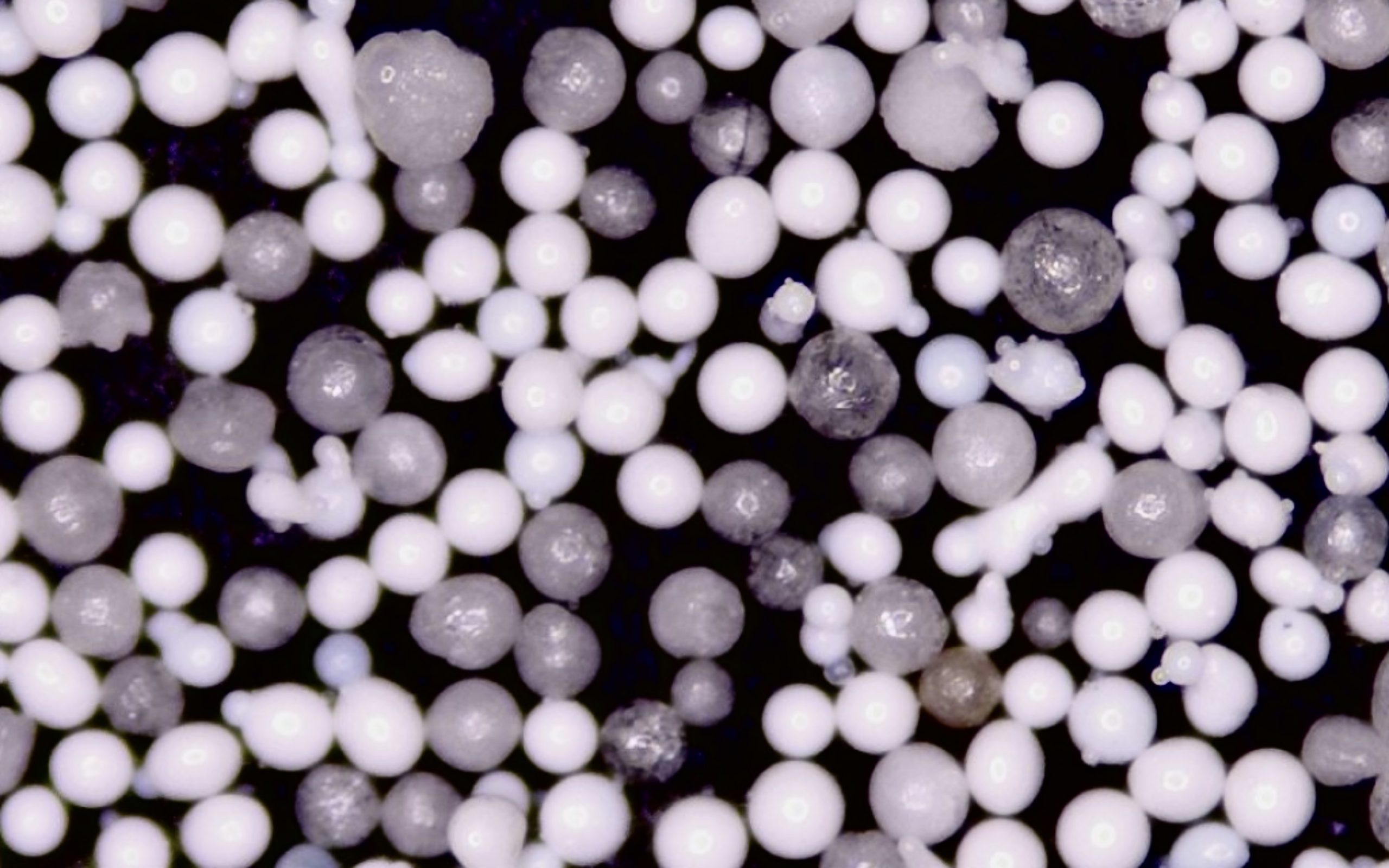
Granalla ultrafina de óxido de aluminio de HLH
- Carburo de silicio
- Características básicas: El carburo de silicio es de color gris oscuro o negro, con partículas afiladas y mayor dureza que el óxido de aluminio. Su fuerza de corte extremadamente alta lo hace excelente para eliminar recubrimientos gruesos. Es especialmente adecuado para el tratamiento de superficies de piezas resistentes a altas temperaturas y de gran dureza, y puede desprender rápidamente revestimientos cerámicos gruesos.
- Escenarios de aplicación: El carburo de silicio se utiliza ampliamente en aviación, equipos de generación de energía y otras industrias expuestas con frecuencia a entornos de alta temperatura. En el pasado, la eliminación mecánica tradicional de revestimientos gruesos solía llevar mucho tiempo y causaba grandes daños al sustrato, mientras que el carburo de silicio puede eliminar los revestimientos cerámicos capa por capa de forma eficaz, especialmente en revestimientos de pulverización térmica o galvanoplastia. Al eliminar los revestimientos gruesos con carburo de silicio, la superficie de la pieza es lisa y el sustrato queda muy intacto, cumpliendo los requisitos de superficie de formas complejas y materiales de alta dureza. Al tiempo que se garantiza la velocidad de eliminación, la dureza y la estabilidad del carburo de silicio evitan el desgaste secundario del sustrato, cumpliendo los requisitos de reprocesamiento de piezas de alto nivel.
- Cuentas de vidrio
- Características básicas: Las microesferas de vidrio son partículas transparentes a translúcidas, de forma redonda, dureza relativamente moderada y adecuadas para la eliminación suave de revestimientos ligeros. Su estructura de partículas redondas puede producir una fuerza de impacto relativamente uniforme sobre la superficie, evitando dañar el sustrato por bordes afilados.
- Escenarios de aplicación: Las microesferas de vidrio se utilizan ampliamente en dispositivos médicos y pequeñas piezas de precisión. Para piezas con materiales frágiles o requisitos de superficie extremadamente elevados, las microesferas de vidrio pueden garantizar un efecto de eliminación suave. Por ejemplo, en el reprocesado de dispositivos médicos, el uso de microesferas de vidrio para eliminar revestimientos antiguos puede evitar daños en el propio dispositivo y mantener la integridad y suavidad del sustrato. La textura de la superficie una vez eliminadas las microesferas de vidrio es fina y suave, sin arañazos evidentes, lo que resulta adecuado para piezas de precisión con elevados requisitos de acabado superficial, proporcionando una buena base para el procesamiento posterior.
- Cuentas de cerámica
- Características básicas: Las microesferas cerámicas suelen ser blancas o grises, con una forma de partícula relativamente redonda y lisa, y una dureza y tenacidad moderadas. Tiene una excelente resistencia a altas temperaturas y un buen efecto en la eliminación de revestimientos cerámicos duros.
- Escenarios de aplicación: Las microesferas cerámicas se utilizan ampliamente en piezas con elevados requisitos de calidad superficial, especialmente en las industrias de automoción y electrónica. En comparación con el óxido de aluminio y el carburo de silicio, las microesferas cerámicas tienen una fuerza de impacto relativamente suave, lo que resulta adecuado para eliminar revestimientos manteniendo la superficie intacta y evitando el impacto en estructuras finas. En situaciones en las que se exigen mayores requisitos de acabado y uniformidad de la superficie, las microesferas cerámicas pueden proporcionar un efecto de eliminación estable y reducir la rugosidad de la superficie de la pieza. La superficie de la pieza tras la eliminación mediante microesferas cerámicas es lisa y tiene una gran consistencia, lo que sienta las bases para la mejora del aspecto y el rendimiento del producto, y es adecuada para la electrónica de consumo de gama alta y el procesamiento de piezas de automoción de alta demanda.
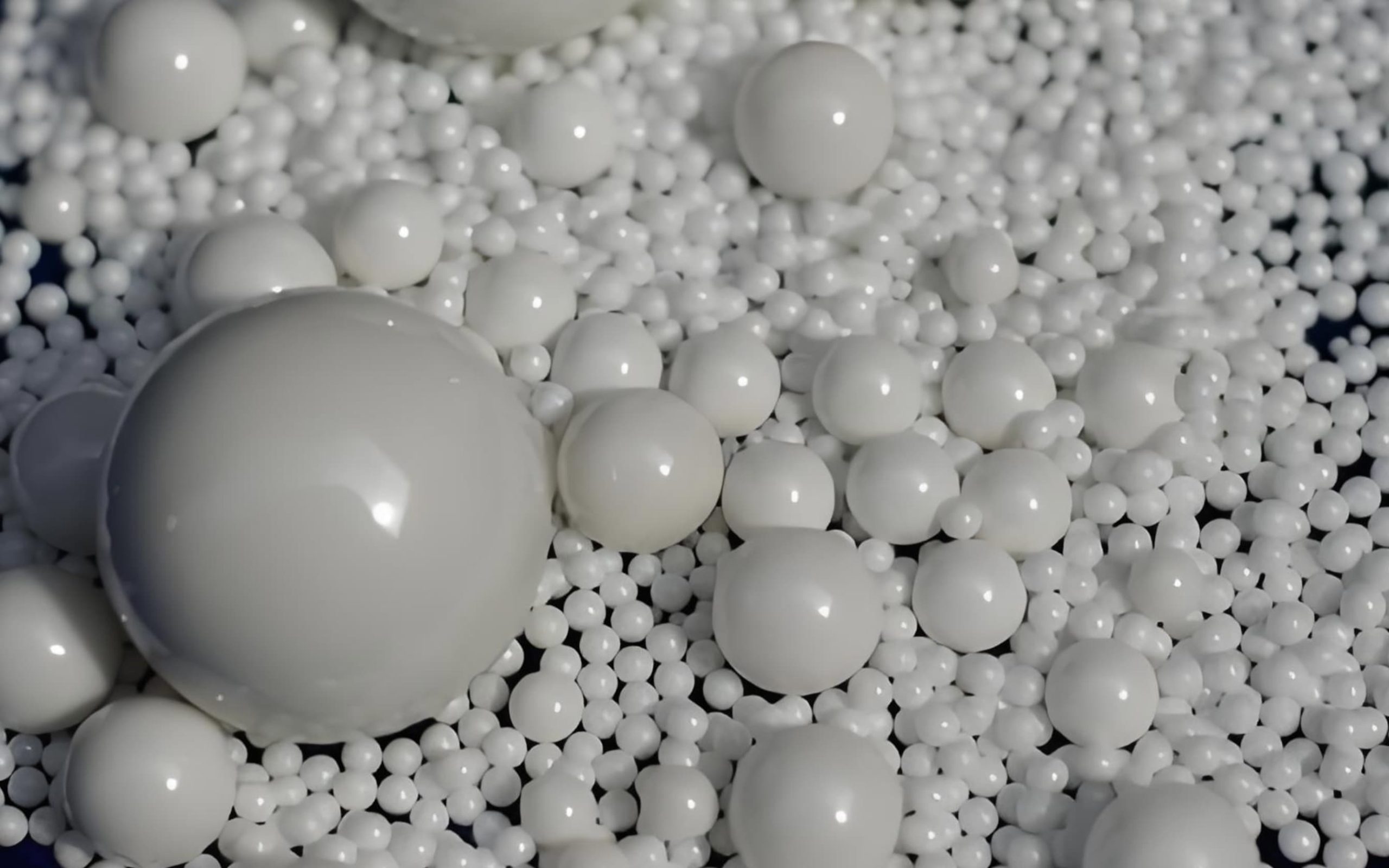
Cuentas de cerámica de HLH
La tecnología de chorro de arena presenta ventajas evidentes en la eliminación de revestimientos cerámicos. Seleccionando los medios de chorreado adecuados, se puede garantizar la precisión, rapidez y respeto medioambiental de la eliminación de revestimientos, al tiempo que se protege eficazmente la integridad del sustrato. Este método flexible de tratamiento de superficies no sólo ofrece una solución fiable para la eliminación de revestimientos, sino que también satisface diversas necesidades industriales. A continuación se resumen varias ventajas clave de la tecnología de chorro de arena en la eliminación de revestimientos:
- Eficaz y controlable: La diversidad de medios de chorreado permite que tanto los revestimientos finos ligeros como los revestimientos gruesos resistentes encuentren soluciones de eliminación adecuadas, con lo que se consigue un tratamiento preciso de la superficie.
- Respetuoso con el medio ambiente y no contaminante: En comparación con los métodos tradicionales de eliminación química, la tecnología de chorro de arena evita el uso de productos químicos nocivos y reduce el riesgo de contaminación ambiental.
- Amplia aplicabilidad: La elección del medio de chorreado se adapta a una gran variedad de sustratos y estructuras complejas, lo que permite su uso en múltiples industrias como la aeronáutica, la médica, la electrónica y la automovilística, convirtiéndolo en una opción ideal para la fabricación de precisión.
- Garantizar la seguridad del sustrato: A la vez que consigue eliminar eficazmente los revestimientos, el proceso de arenado puede mantener las características originales del sustrato, lo que resulta especialmente adecuado para industrias con estrictos requisitos de protección del sustrato.
- Cumplen las normas industriales: El proceso de arenado puede satisfacer los elevados requisitos de la industria en cuanto a piezas de precisión, cumplir las normas de seguridad y calidad superficial, y es un importante método de eliminación de revestimientos en el procesamiento de diversas industrias.
El desarrollo continuo de la tecnología de chorro de arena para eliminar revestimientos cerámicos y la innovación de los medios de chorro de arena han permitido que la fabricación de precisión cumpla mayores requisitos técnicos y objetivos de control de costes. Con la aplicación en profundidad de la tecnología de chorro de arena, la selección de diferentes medios de chorro de arena y sus soluciones de optimización seguirán desempeñando un papel insustituible en la eliminación de revestimientos cerámicos, y escoltar la calidad del producto y la eficiencia de la producción en todos los ámbitos de la vida.
Filtros