Shot Peening y láser peening en el acabado de metales
25 de octubre de 2024
En el mundo del acabado de metales, mejorar la resistencia a la fatiga, aumentar la dureza superficial y mejorar la resistencia a la corrosión son factores clave para determinar la vida útil y el rendimiento de las piezas. Estas mejoras de rendimiento se consiguen mediante diversos procesos diseñados para modificar las características superficiales de las piezas metálicas. Entre ellos, el granallado y el granallado de choque por láser son dos de los métodos más eficaces que pueden introducir tensiones de compresión beneficiosas en los metales, alargando así la vida útil de los componentes críticos.
Sin embargo, a pesar de tener el mismo objetivo, las dos tecnologías presentan diferencias significativas en cuanto a profundidad de penetración, precisión, coste y aplicaciones aplicables. En este artículo se comparan en profundidad el shot peening y el shock peening por láser, examinando sus diferencias técnicas, aplicaciones típicas y factores clave que influyen en la elección entre ambas. Se utilizarán estudios de casos de industrias como la aeroespacial, la automovilística y la de dispositivos médicos para explorar las ventajas y limitaciones de cada proceso.
Shot Peening
Descripción del proceso
El granallado es un proceso de trabajo en frío que utiliza proyectiles para impactar contra una superficie metálica. Estos proyectiles suelen estar hechos de materiales esféricos como acero, vidrio o cerámica. Durante el proceso de granallado, el material esférico se acelera mediante chorros de aire o fuerza centrífuga para impactar en la superficie a gran velocidad. Cada impacto crea una pequeña abolladura en la superficie, comprimiendo el material que hay debajo. Esto crea una capa de compresión que actúa como barrera protectora contra la iniciación y propagación de grietas, aumentando así la resistencia a la fatiga del material y la resistencia a las grietas por corrosión bajo tensión.
La profundidad de la tensión de compresión producida por el granallado suele afectar a los 0,1 - 1 mm superiores de la superficie del material, lo que es suficiente para muchas aplicaciones generales. Su desventaja es que suele dejar una superficie más rugosa que puede requerir un acabado adicional. Por supuesto, la rugosidad puede variar en función del material de los medios de granallado utilizados y, en general, los medios de acero dejarán una superficie más rugosa que las bolas de cerámica o vidrio.
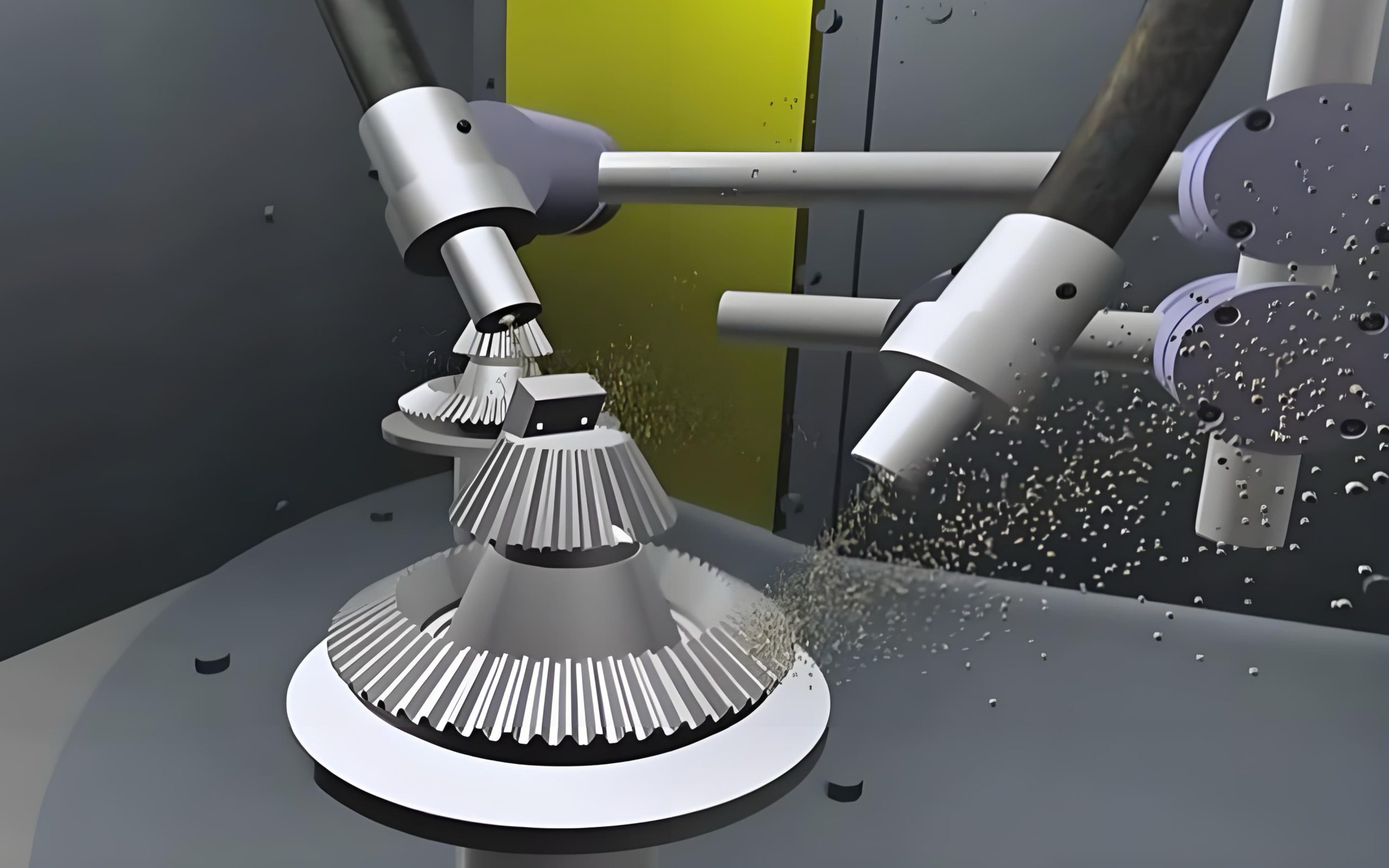
Diagrama esquemático del shot peening
Aplicaciones típicas
El shot peening se utiliza ampliamente en la industria del automóvil para reforzar componentes como engranajes, muelles helicoidales y ejes, sometidos a tensiones repetidas durante su vida útil. En el ámbito aeroespacial, el shot peening se aplica a componentes como los trenes de aterrizaje y las piezas del fuselaje, donde la durabilidad es fundamental para la seguridad y estas piezas suelen tener geometrías más sencillas que se adaptan bien a los impactos más amplios y menos precisos del shot peening.
Visión general del granallado de choque por láser
Descripción del proceso
El granallado de choque por láser es una técnica más avanzada que utiliza pulsos láser de alta energía dirigidos a la superficie metálica, que suele estar protegida de la ablación directa por una capa de recubrimiento transparente, como el agua. La energía láser crea una onda de choque que se propaga a través del material, creando tensiones de compresión profundas bajo la superficie. El proceso es más preciso que el shot peening y puede producir una capa de compresión más profunda, por lo que es ideal para aplicaciones de alta tensión para lograr resistencia a la fatiga y al agrietamiento por corrosión bajo tensión.
Una ventaja clave del granallado de choque por láser es su capacidad para producir tensiones de compresión mucho más profundas que el granallado. En algunos casos, estas tensiones pueden penetrar hasta 10 mm por debajo de la superficie, proporcionando una mayor protección a las piezas sometidas a altas cargas de fatiga. Pero a diferencia del shot peening, el shock peening por láser deja una superficie más lisa. Esto es especialmente beneficioso en aplicaciones que requieren tanto una mejora de las tensiones como de la calidad del acabado superficial, como las palas de turbinas aeroespaciales y los implantes médicos. La reducción de la rugosidad de la superficie puede eliminar la necesidad de pasos de postprocesado, lo que ahorra tiempo y costes.
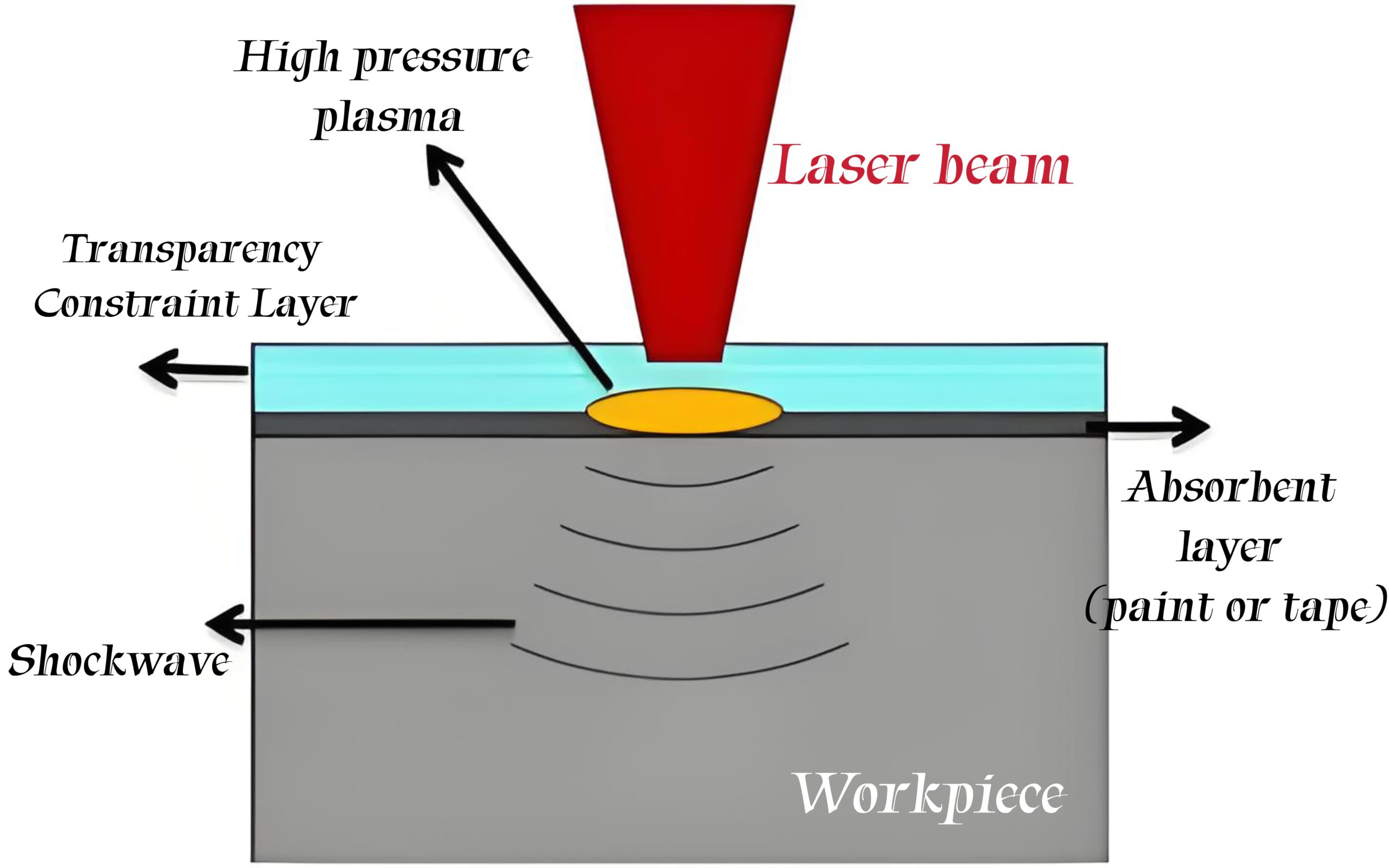
Granallado de choque por láser
Sin embargo, el granallado de choque por láser es bastante más caro y requiere equipos especializados. Su uso suele limitarse a componentes críticos y de alto valor en los que el coste añadido se amortiza mediante una mayor vida útil y un mejor rendimiento. Aunque el coste inicial puede ser elevado, los beneficios a largo plazo suelen compensar la inversión inicial, especialmente en sectores como el aeroespacial y el energético, donde no hay margen para posibles fallos.
Aplicaciones típicas
El granallado por láser se utiliza principalmente en industrias en las que los componentes se enfrentan a tensiones térmicas y mecánicas extremas. Por ejemplo, los álabes de las turbinas de las industrias aeroespacial y de generación de energía suelen someterse a granallado por láser para prolongar su vida útil bajo cargas cíclicas. Los componentes de automoción, como las piezas del motor sometidas a grandes esfuerzos, como los pistones, también se benefician de las tensiones de compresión más profundas producidas por el peening láser. En el campo de la medicina, el granallado por láser se utiliza para prolongar la vida útil de los implantes mejorando su resistencia a la fatiga y minimizando los fallos relacionados con la corrosión.
Diferencias entre Shot Peening y Laser Peening
Aunque el shot peening y el peening láser tienen el mismo objetivo básico de mejorar la resistencia a la fatiga, difieren en varias áreas clave. Estas son las principales diferencias entre ambos métodos:
Método de aplicación del estrés
El granallado se basa en el impacto aleatorio de proyectiles de alta velocidad sobre la superficie del material. El impacto mecánico produce tensiones de compresión, pero el proceso es menos preciso. El peening por láser, en cambio, utiliza pulsos láser focalizados para crear ondas de choque controladas, lo que permite una aplicación más precisa de la tensión.
Profundidad de penetración
La profundidad de la tensión de compresión es una diferencia clave entre los dos procesos. El shot peening suele producir tensiones poco profundas (0,1 - 1 mm), mientras que el peening láser puede penetrar hasta 10 mm en el material. Esta penetración más profunda hace que el peening láser sea más adecuado para componentes sometidos a altos niveles de tensión, como álabes de turbinas o piezas de automoción de alto rendimiento.
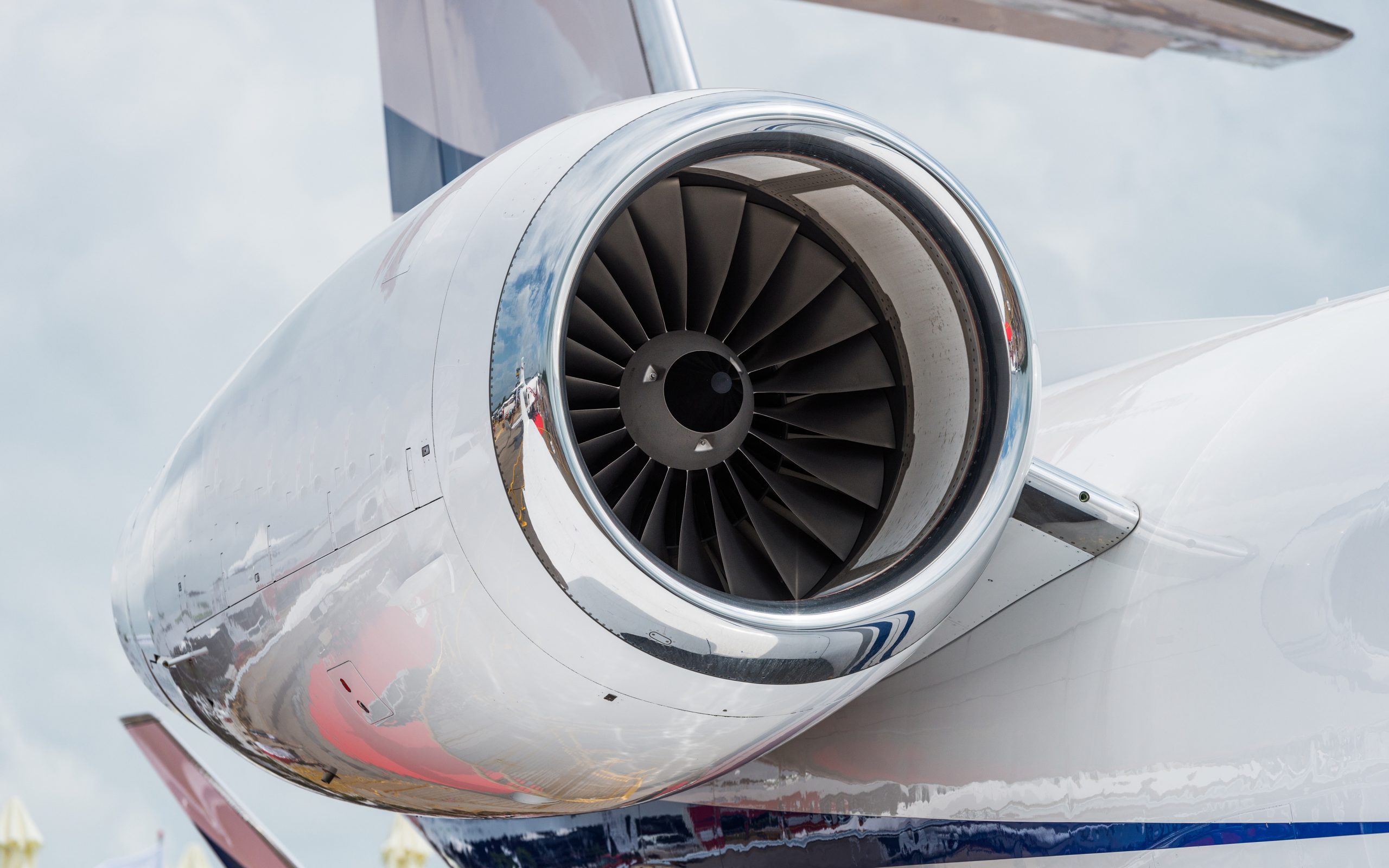
Álabes de turbina
Precisión y control
Debido a la naturaleza del impacto del proyectil, el shot peening ofrece menos precisión y es más adecuado para superficies más anchas o geometrías más sencillas. En cambio, el peening por láser permite aplicaciones muy específicas, por lo que es más adecuado para tratar zonas concretas, como componentes complejos o delicados.
Acabado superficial
El granallado suele dejar una superficie rugosa que puede requerir un acabado adicional en aplicaciones delicadas. Sin embargo, el granallado por láser produce una superficie más lisa con menos defectos, lo que reduce la necesidad de tratamiento posterior.
Coste y accesibilidad
En términos de coste, el shot peening es más accesible debido a sus menores gastos de instalación y funcionamiento. Se utiliza mucho en sectores como la automoción y la construcción, donde la rentabilidad es una prioridad. El granallado por láser, en cambio, es más caro y suele utilizarse para mejorar el rendimiento de componentes críticos en industrias como la aeroespacial y la energética, lo que supone un ahorro a largo plazo gracias a la prolongación de la vida útil de los componentes y la reducción del mantenimiento.
El tipo de metal determina el método
Los distintos metales reaccionan de forma diferente a las tensiones producidas por el shot peening y el peening láser. La elección del método de peening adecuado depende de las características del metal, el entorno de aplicación y los resultados de rendimiento deseados.
Acero
El acero es uno de los metales más comúnmente tratados en aplicaciones industriales, especialmente en las industrias del automóvil y aeroespacial. El shot peening se utiliza habitualmente para piezas de acero, especialmente las expuestas a cargas cíclicas, como muelles, engranajes y componentes del fuselaje de los aviones. Las tensiones de compresión poco profundas producidas por el shot peening son suficientes para estas piezas. Sin embargo, para las aleaciones de acero de alto rendimiento utilizadas en la industria aeroespacial o de generación de energía, el granallado por láser es más popular debido a su capacidad para producir tensiones más profundas, mejorando la resistencia a la fatiga en condiciones extremas.
Aluminio
El aluminio se utiliza mucho en industrias como la automovilística y la aeroespacial, donde los materiales ligeros son fundamentales. Para las piezas de aluminio de uso general, el granallado es suficiente, mientras que para las aleaciones de aluminio de uso aeroespacial, el granallado por láser se utiliza más a menudo cuando es necesario mejorar la resistencia a la fatiga para hacer frente a las elevadas tensiones del vuelo.
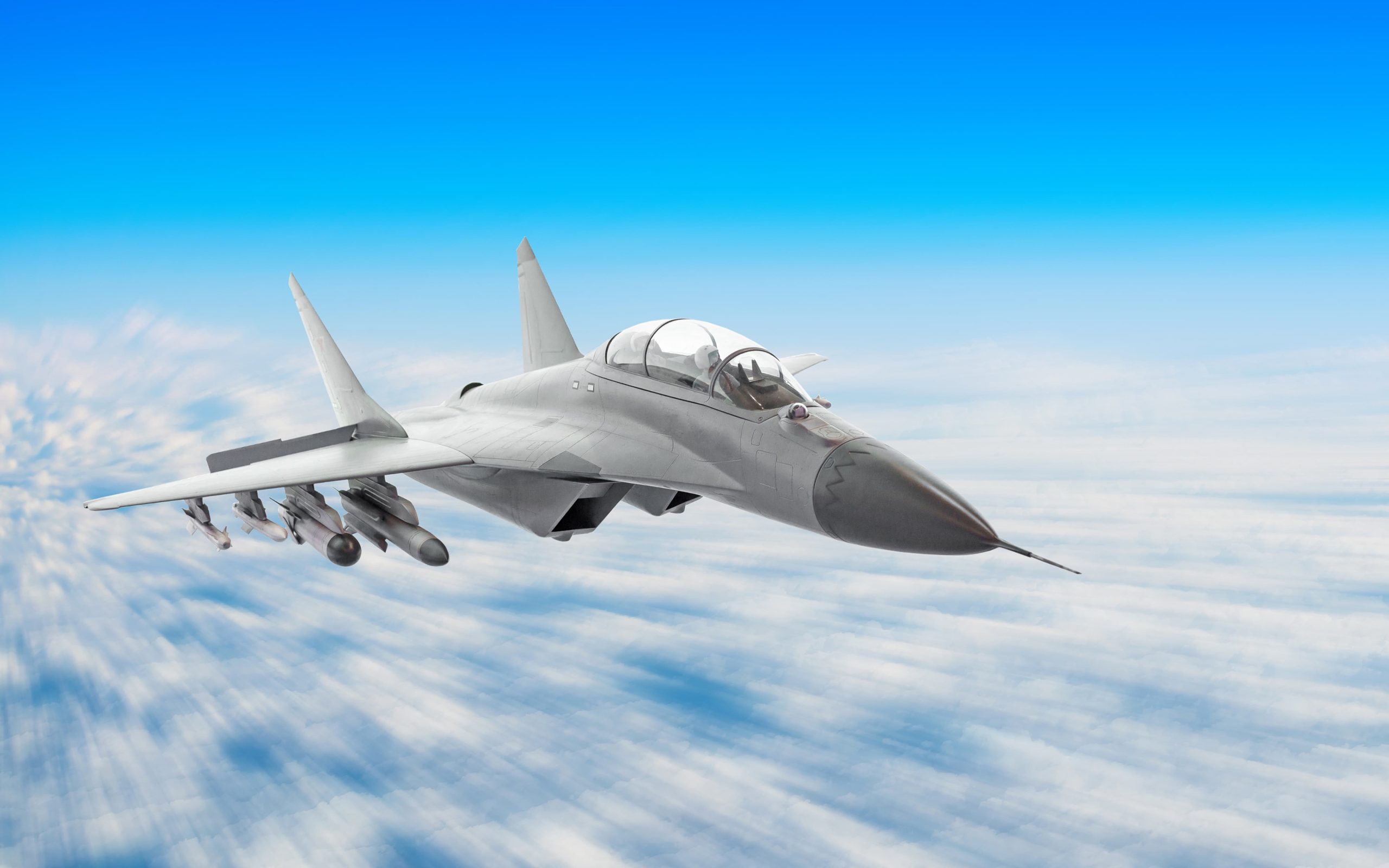
Los materiales de uso aeroespacial deben soportar condiciones ambientales más extremas.
Titanio
El titanio es conocido por su elevada relación resistencia-peso y su resistencia a la corrosión, lo que lo hace popular en aplicaciones aeroespaciales y médicas. Tanto si se trata de aspas de ventilador de titanio que deben soportar altas tensiones mecánicas y temperaturas cada vez más elevadas, como de prótesis articulares o implantes dentales que deben mejorar la resistencia a la fatiga y la vida útil, el peening por láser crea una capa de compresión profunda que mejora la vida útil a la fatiga sin comprometer el acabado superficial del material, y puede proporcionar precisión y control exactos.
Aleaciones de níquel
Las superaleaciones de níquel se utilizan a menudo en entornos de alta temperatura, como las turbinas de gas y otras aplicaciones críticas de generación de energía. Debido a sus condiciones de funcionamiento, estas aleaciones son susceptibles a la fatiga y a las tensiones térmicas, por lo que el tratamiento superficial es fundamental para su rendimiento. El peening por láser es el método preferido para el tratamiento de componentes de aleaciones de níquel, ya que las tensiones de compresión más profundas que produce protegen los álabes de las turbinas y otros componentes críticos de fallos bajo cargas cíclicas y exposición a altas temperaturas, alargando así la vida útil de estos componentes.
Estudios de casos comparativos
Casos de la industria del automóvil
- Granallado de piezas de cajas de cambios
El shot peening se utiliza habitualmente en la industria del automóvil para mejorar la vida útil a la fatiga de componentes de cajas de cambios como engranajes, ejes y carcasas. El impacto a alta velocidad del proyectil metálico induce tensiones de compresión en la superficie, mejorando eficazmente la resistencia al desgaste y a la fatiga. Las investigaciones han demostrado que el shot peening puede mejorar la resistencia a la fatiga de las piezas de la caja de cambios hasta 30%. En el caso de componentes sometidos a cargas cíclicas, esta mejora ayuda a evitar fallos prematuros.
El shot peening es generalmente más rentable que el peening láser y más adecuado para la producción de automóviles a gran escala debido a su menor coste de preparación y menor tiempo de procesamiento.
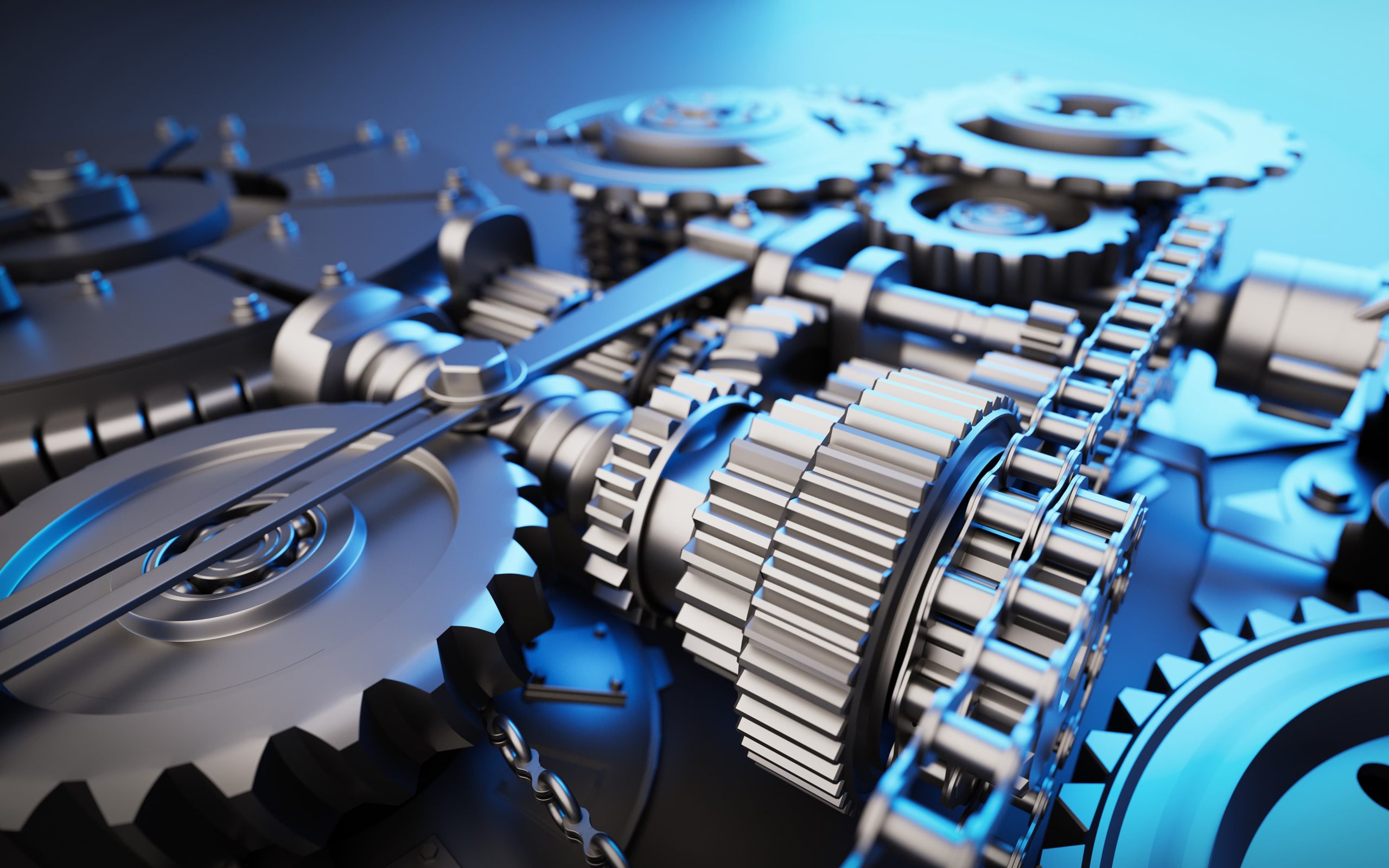
Estructura del engranaje
- Granallado por láser de componentes de motores
El granallado por láser se utiliza cada vez más para componentes críticos del motor, como pistones y cigüeñales. El proceso implica pulsos láser focalizados que producen tensiones de compresión más profundas que el shot peening. Las mejoras de la vida útil a la fatiga en las zonas sometidas a grandes esfuerzos con el peening láser suelen ser superiores a 50%. Esto es especialmente importante en componentes expuestos a condiciones térmicas y mecánicas extremas.
Aunque el granallado por láser es más caro, sus ventajas en términos de vida útil y rendimiento también son significativas, por lo que resulta ideal para vehículos de alto rendimiento.
Casos aeroespaciales
- Granallado de componentes del fuselaje
El shot peening se utiliza ampliamente para componentes del fuselaje, incluidos elementos estructurales como las pieles del fuselaje y los componentes de las alas. El proceso mejora la resistencia a la fatiga de estos componentes y puede aumentar la vida útil a la fatiga de los materiales del fuselaje hasta en 200%, lo que es fundamental para mantener la integridad estructural y la seguridad.
El menor coste y la mayor sencillez de configuración del shot peening lo convierten en la mejor opción para muchos componentes de fuselajes de aviones, lo que permite a los fabricantes aplicarlo eficazmente a una gran variedad de piezas.
- Granallado de choque por láser de álabes de turbina
En cambio, el granallado de choque por láser se utiliza más comúnmente para álabes de turbinas en motores a reacción, donde los requisitos de resistencia a la fatiga y distribución de tensiones son críticos. Las tensiones de compresión más profundas producidas por el granallado de choque por láser aumentan significativamente la durabilidad de los álabes de turbina y pueden prolongar su vida útil hasta 70%, lo que es fundamental para la seguridad de vuelo, especialmente en entornos de alta tensión donde el fallo del álabe puede tener consecuencias catastróficas.
Las inversiones en granallado de choque por láser pueden justificarse por la reducción del riesgo de fallo y la prolongación de la vida útil de estos componentes críticos, lo que lo convierte en un proceso valioso en ingeniería aeroespacial.
- Casos de la industria médica
Granallado de choque por láser de implantes médicos
El granallado de choque por láser se utiliza cada vez más en dispositivos ortopédicos como implantes de cadera y rodilla. Estos implantes soportan importantes cargas mecánicas a lo largo del tiempo, y la capacidad del método para inducir eficazmente tensiones de compresión profundas puede prolongar su vida útil. Los implantes médicos sometidos a choque láser tienen un aumento medio de vida de 100%. En comparación con los tratamientos superficiales tradicionales, el peening láser ofrece una solución más eficaz para mejorar la durabilidad de los implantes, reduciendo el riesgo de complicaciones y la necesidad de cirugía de revisión.
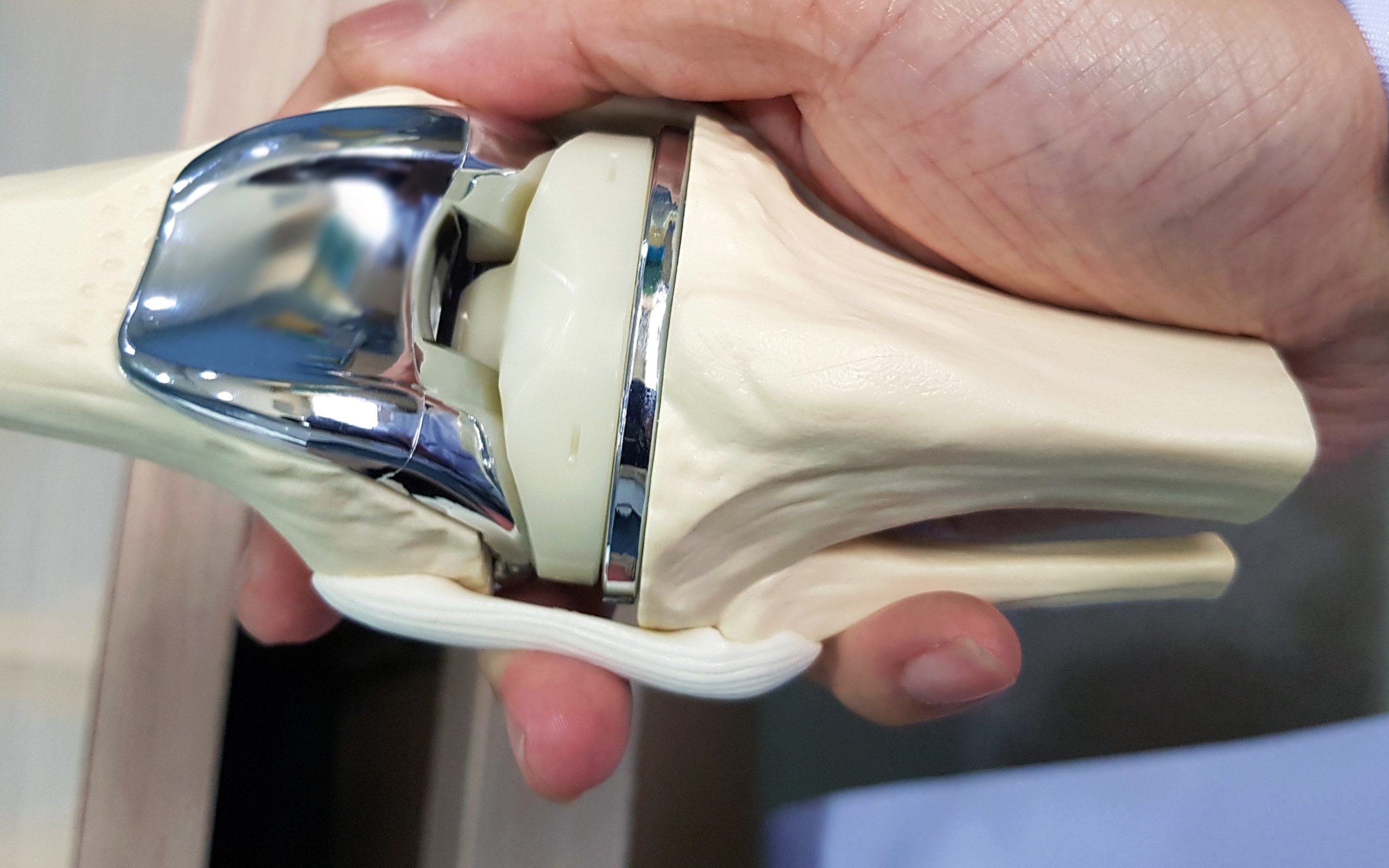
Implantes articulares
En resumen, el shot peening y el shock peening por láser tienen sus propias ventajas e inconvenientes en el acabado de metales.
Las ventajas del shot peening son bajo coste de instalación y funcionamientoy se utilizan ampliamente en industrias rentables como la automovilística. Puede mejorar eficazmente la resistencia a la fatiga de los materiales y suele utilizarse para piezas de acero en general y piezas geométricas sencillas, como engranajes y muelles de automóviles. Sin embargo, sus desventajas son que dejar una superficie más rugosaque puede requerir un acabado adicional, y la tensión de compresión generada es poco profunda.
Las ventajas del láser shock peening son evidentes. Puede producir tensiones de compresión más profundas, incluso penetrando 10 mm por debajo de la superficie del material, lo que es adecuado para aplicaciones de alta tensión como los álabes de turbina; tiene alta precisión y es adecuado para procesar piezas complejas o delicadas; puede dejan una superficie más lisa y reducir los pasos posteriores al tratamiento. Sin embargo, es caro y requiere equipos especializados. Suele utilizarse para piezas críticas de alto valor, como las aeroespaciales.
En diferentes aplicaciones metálicas, los dos también tienen diferentes opciones debido a las propiedades del metal y al entorno de aplicación. En general, los dos métodos de refuerzo desempeñan un papel importante en sus respectivos campos de aplicación y deben considerarse de forma exhaustiva en función de las necesidades específicas.
Revisando el artículo completo, verá que tanto el shot peening como el peening láser desempeñan un papel vital en la mejora del rendimiento y la longevidad de los componentes en una gran variedad de industrias. Sea cual sea el método elegido, deben tenerse en cuenta factores como el tipo de material, la complejidad de la pieza, los requisitos de rendimiento y el impacto en los costes. Comprender las ventajas únicas de cada método le permitirá tomar una decisión informada para su aplicación específica.
Filtros