La conexión entre la poliamida 6 y el poliestireno
27 de septiembre de 2024
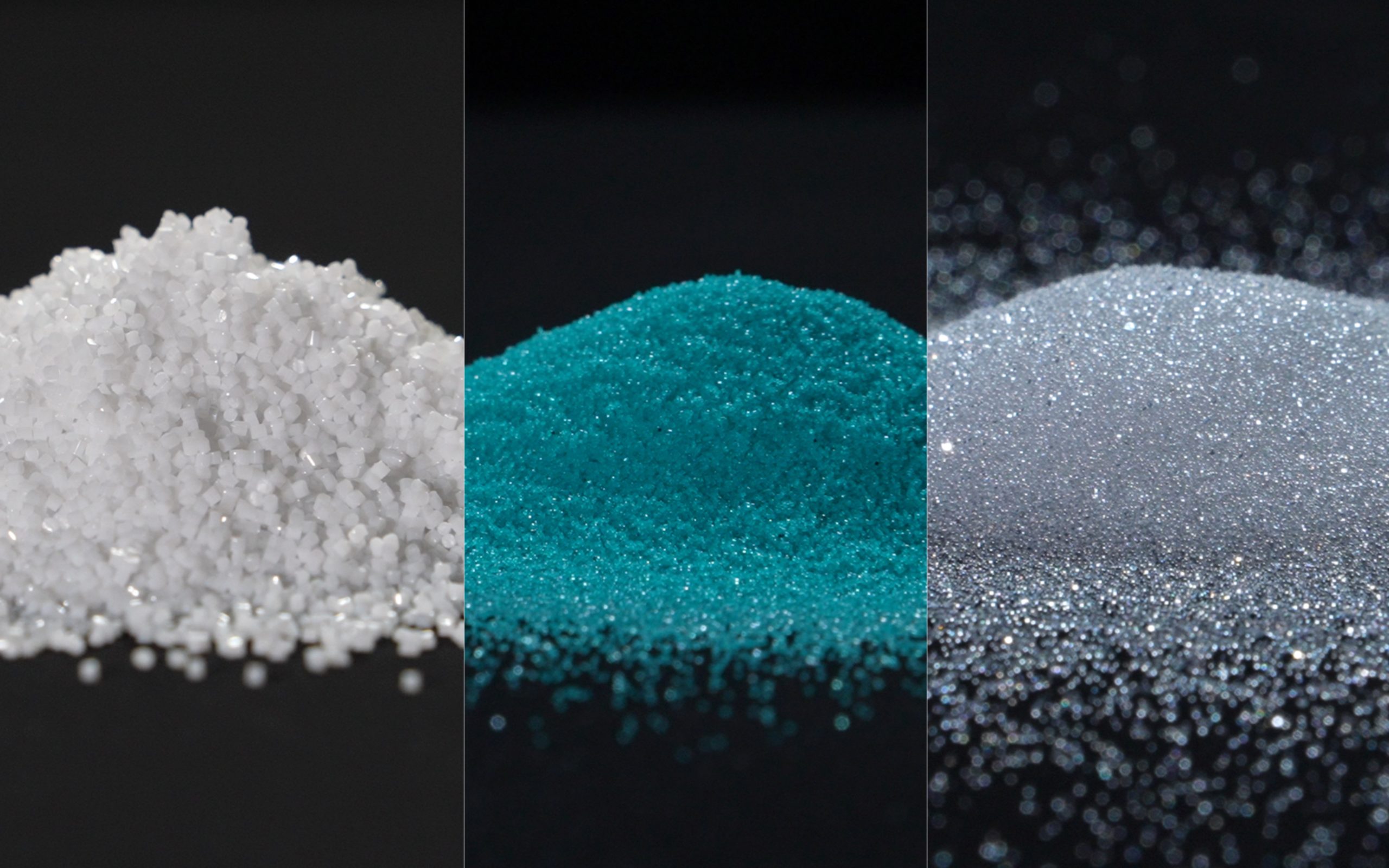
En el mundo de los materiales plásticos, la poliamida (comúnmente conocida como nailon) y el poliestireno son dos materiales poliméricos muy utilizados y con un importante valor de aplicación. Con el avance de la ciencia y la tecnología y el continuo desarrollo de la industria, estos dos materiales desempeñan un papel insustituible en muchos campos. El objetivo de este artículo es explorar las principales diferencias entre la poliamida 6 y el poliestireno, y presentar los medios de desbarbado pertinentes para ayudar a los lectores a comprender mejor sus respectivas características, aplicaciones y normas para seleccionar los materiales adecuados.
Panorama de la poliamida
La poliamida es una importante clase de materiales polímeros sintéticos, ampliamente utilizados en textiles, automóviles, electrónica y plásticos de ingeniería. La poliamida suele producirse por reacción de polimerización, y entre sus principales tipos se encuentran la poliamida 6 (nylon 6), la poliamida 66 (nylon 66), etc. Estos materiales son conocidos por su excelente resistencia al calor, resistencia al desgaste y estabilidad química.
- Composición del material y proceso de producción: La síntesis de poliamida suele llevarse a cabo mediante la reacción de polimerización de diácidos alifáticos y compuestos de amina. Este proceso puede llevarse a cabo por diversos métodos, como la polimerización de apertura en anillo y la reacción de policondensación. La composición de la poliamida determina sus excelentes propiedades físicas y químicas, que la hacen popular en aplicaciones exigentes.
- Características principales:
- Resistencia al calor: La poliamida tiene un punto de fusión elevado (entre 220 °C y 260 °C aproximadamente), lo que le permite mantener un buen rendimiento en entornos de altas temperaturas.
- Resistencia al desgaste: La resistencia al desgaste de la poliamida hace que se utilice ampliamente en piezas mecánicas y materiales de fricción.
- Estabilidad química: Muestra una buena resistencia a muchos productos químicos y es adecuado para una gran variedad de entornos industriales.
Panorama del poliestireno
El poliestireno es un material plástico ligero, rígido y asequible que se utiliza ampliamente en envases, artículos domésticos, electrónica y construcción. El poliestireno puede dividirse en poliestireno ordinario (PS) y poliestireno de alto impacto (HIPS), este último basado en poliestireno ordinario al que se añade caucho para mejorar su dureza.
- Composición del material y proceso de producción: La síntesis de poliestireno se consigue principalmente mediante la reacción de polimerización por radicales libres de monómeros de estireno. Este proceso es sencillo y de bajo coste, adecuado para la producción a gran escala.
- Características principales:
- Ligero: La baja densidad del poliestireno lo convierte en un material de envasado ideal.
- Buena moldeabilidad: El poliestireno puede procesarse mediante diversos métodos de moldeo (como moldeo por inyección y extrusión), y puede adaptarse con flexibilidad a los diferentes requisitos de los productos.
- Transparencia: Algunos tipos de poliestireno tienen una buena transparencia y son adecuados para envases y productos de exposición transparentes.
Las principales diferencias entre los dos componentes
La poliamida y el poliestireno presentan diferencias significativas en cuanto a estructura química, propiedades físicas y ámbitos de aplicación, lo que los hace adecuados para distintas ocasiones.
- Diferencias en la estructura química:
Las moléculas de poliamida contienen grupos funcionales amida (-C(O)NH-), mientras que el poliestireno se polimeriza a partir de monómeros de estireno. La estructura molecular de la poliamida le confiere unas propiedades mecánicas y una resistencia al calor superiores.
- Propiedades físicas:
Por lo general, las poliamidas tienen una densidad mayor (aproximadamente 1,1-1,2 g/cm³), mientras que el poliestireno tiene una densidad menor (aproximadamente 1,04 g/cm³). Las poliamidas tienen una mayor dureza y presentan una buena resistencia al impacto, mientras que el poliestireno es quebradizo.
- Propiedades térmicas:
En general, las poliamidas tienen un punto de fusión más alto que el poliestireno y pueden trabajar a temperaturas más elevadas. El poliestireno tiene una temperatura de deformación térmica relativamente baja, lo que resulta adecuado para aplicaciones en entornos criogénicos.
- Resistencia química:
La poliamida es resistente a muchos productos químicos, mientras que el poliestireno es sensible a ciertos disolventes (como el alcohol) y es propenso a hincharse o agrietarse.
- Diferencias en los ámbitos de aplicación:
La poliamida se utiliza ampliamente en piezas de automoción, estructuras mecánicas y textiles, donde se requiere una gran solidez y resistencia al calor, mientras que el poliestireno se emplea principalmente en aplicaciones más ligeras y económicas, como envases, bienes de consumo y carcasas de productos electrónicos.
Tras comprender las características de los dos componentes plásticos de la poliamida y el poliestireno, podemos examinar más de cerca tres medios de desbarbado relacionados: los medios de desbarbado de poliamida de nailon, los medios de desbarbado criogénicos y las perlas de desbarbado de poliestireno. Estos tres medios no sólo tienen sus propias características en cuanto a composición del material, sino que también presentan diferencias evidentes en cuanto a dureza, forma, color y escenarios de aplicación.
Medios de desbarbado de nylon y poliamida
- Composición del material: Los medios de desbarbado de poliamida de nailon están fabricados principalmente con resina de poliamida 6 (nailon 6). La poliamida es conocida por sus excelentes propiedades mecánicas y su resistencia al desgaste, y es adecuada para aplicaciones de desbarbado exigentes.
- Dureza: Los medios de desbarbado de poliamida de nailon suelen tener una dureza comprendida entre 54 y 62 Barcol, y presentan una buena flexibilidad, lo que les permite adaptarse a piezas de diferentes formas.
- Forma y color: Este medio puede fabricarse normalmente en color, siendo el amarillo y el rojo los colores más utilizados, lo que resulta fácil de distinguir durante la operación. La forma de las partículas es un cilindro o hexaedro con igual diámetro y altura. El tamaño es extremadamente pequeño, suave y ligero, y puede lograr un mejor efecto de desbarbado sin dañar la pieza de trabajo.
- Ventajas
- Desbarbado eficaz: la poliamida 6 de nailon tiene un buen rendimiento de corte y puede eliminar rápidamente las rebabas de la superficie de la pieza.
- No daña el sustrato: Debido a su suavidad, es adecuado para piezas de precisión y no causará arañazos ni daños al sustrato.
- Gran resistencia al desgaste: Puede mantener el rendimiento en el uso a largo plazo, reducir la frecuencia de sustitución y reducir los costes de producción.
- Respetuoso con el medio ambiente y no tóxico: En comparación con algunos métodos químicos de desbarbado, el uso de medios de desbarbado de poliamida de nylon es más respetuoso con el medio ambiente.
- Escenarios aplicables: Ampliamente utilizado en dispositivos médicos, piezas de automóviles, aeroespacial y otras industrias, especialmente adecuado para el mecanizado de precisión con altos requisitos de calidad superficial.
Medios criogénicos de desbarbado
- Composición del material: El medio de desbarbado criogénico suele estar hecho de resina de poliamida. Estos materiales presentan una buena tenacidad y estabilidad en condiciones criogénicas y son adecuados para procesos de desbarbado especiales.
- Dureza: La dureza del medio criogénico de desbarbado es baja, generalmente entre 3 y 4 de dureza Mohs, lo que garantiza que no se cause ningún daño adicional a la pieza al eliminar las rebabas.
- Forma y color: Este medio es mayoritariamente blanco lechoso, y la forma de las partículas es un cilindro o hexaedro con igual diámetro y altura.
- Ventajas
- Funcionamiento criogénico: Puede utilizarse en entornos de baja temperatura y es adecuado para piezas sensibles a la temperatura.
- Buena adaptabilidad: Su suavidad hace que el medio se adapte a piezas de diversas formas, proporcionando una mayor flexibilidad.
- Alta seguridad: No se generan gases nocivos durante el desbarbado criogénico, lo que resulta más seguro y respetuoso con el medio ambiente.
- Rentabilidad: En comparación con otros medios de desbarbado de alto rendimiento, el coste de los medios de desbarbado criogénicos es más económico y adecuado para la producción a gran escala.
- Escenarios aplicables: Adecuado para industrias como la aeroespacial, la electrónica y los productos plásticos, especialmente en situaciones en las que se requiere un desbarbado criogénico, puede proteger eficazmente la integridad del producto.
Perlas de desbarbado de poliestireno
- Composición del material: Los cordones de desbarbado de poliestireno están hechos de resina de poliestireno, favorecida por su ligereza y fácil moldeado.
- Dureza: El poliestireno tiene una dureza relativamente baja, generalmente entre 46 y 54 de dureza Barcol, que es adecuada para aplicaciones generales de desbarbado.
- Forma y color: Suelen ser transparentes y de forma esférica, lo que resulta conveniente para un uso uniforme durante el chorreado.
- Ventajas
- Ligereza: Las características de ligereza del poliestireno facilitan su manejo durante el chorreado y reducen la carga de los equipos.
- Bajo coste: En comparación con otros medios de desbarbado, las perlas de desbarbado de poliestireno tienen un coste inferior y son adecuadas para la producción a gran escala.
- Amplia aplicación: El poliestireno tiene un excelente rendimiento de procesamiento y es adecuado para una gran variedad de entornos industriales.
- Buena moldeabilidad: Puede adaptarse a formas complejas de piezas de trabajo y garantizar una eliminación uniforme de las rebabas.
- Escenarios aplicables: Ampliamente utilizado en industrias tales como productos electrónicos, juguetes y materiales de embalaje, adecuado para necesidades generales de tratamiento de superficies.
Comparación de 3 medios de desbarbado
Similitudes
Los tres medios de desbarbado están diseñados para eliminar las rebabas de la superficie de las piezas y mejorar la calidad del producto, y todos tienen un cierto grado de flexibilidad para adaptarse a piezas de diferentes formas y garantizar que no se dañe el sustrato.
Diferencia
- Composición del material
Los medios de poliamida de nylon y los medios de desbarbado criogénicos están hechos principalmente de resina de poliamida, mientras que las perlas de desbarbado de poliestireno están hechas de resina de poliestireno.
- Diferencia de dureza
Los medios de desbarbado de nylon y poliamida tienen la dureza más alta y son adecuados para el mecanizado de precisión de alta exigencia; los medios de desbarbado criogénicos tienen una dureza inferior; los granos de desbarbado de poliestireno están entre los dos en dureza y son adecuados para aplicaciones generales.
- Rango de tolerancia a la temperatura
Los medios de desbarbado de poliamida de nailon tienen un rendimiento estable a temperaturas más altas, y su punto de fusión se sitúa entre 200-250°C. Debido a su excelente resistencia al calor, es adecuado para procesar materiales o escenarios de aplicación con mayor resistencia al calor. Por el contrario, los medios de desbarbado criogénicos son especialmente adecuados para entornos criogénicos, sobre todo para el procesamiento de piezas en estado congelado. Suelen mantener un rendimiento excelente en un entorno de -80 °C y son adecuados para procesos de desbarbado criogénico y para el procesamiento de piezas pequeñas de alta precisión. El poliestireno tiene una temperatura de funcionamiento más baja y un punto de fusión de unos 100°C, por lo que es adecuado para el tratamiento de superficies a temperaturas bajas y normales, pero rinde mal en entornos de altas temperaturas. Es adecuado para industrias ligeras que no requieren operaciones a alta temperatura.
- Escenarios aplicables
Los medios de desbarbado de nylon y poliamida son más adecuados para el mercado de gama alta, mientras que los medios de desbarbado criogénicos se centran en aplicaciones especiales; las perlas de desbarbado de poliestireno son la opción preferida para aplicaciones sensibles a los costes.
- Efecto del tratamiento
La flexibilidad de los medios de desbarbado de poliamida de nailon los hace adecuados para procesar piezas con formas complejas, y la superficie tratada es relativamente lisa y de gran precisión. Los medios de desbarbado criogénicos son especialmente adecuados para su uso en fabricación de alta precisión y alto brillo, como dispositivos médicos y piezas aeroespaciales. La precisión de la superficie es extremadamente alta y casi no se producen daños secundarios en la pieza, lo que la convierte en una opción ideal para escenarios de alta exigencia. Los cordones de desbarbado de poliestireno se utilizan principalmente en la industria ligera y la electrónica. Aunque tienen una gran capacidad de desbarbado, la precisión de su tratamiento superficial es relativamente baja, por lo que son adecuados para el procesamiento de piezas de gran superficie y sin precisión.
- Vida útil
Los medios de desbarbado de poliamida de nailon son conocidos por su excelente resistencia al desgaste y pueden mantener una larga vida útil en ocasiones de uso frecuente de alta intensidad. Debido a la dureza de su material, la pérdida durante el uso es baja. Los medios de desbarbado criogénicos suelen utilizarse en entornos extremadamente criogénicos, y la pérdida por fricción en criogenia es extremadamente pequeña, lo que resulta adecuado para un uso frecuente. Sin embargo, los cordones de desbarbado de poliestireno tienen una resistencia al desgaste relativamente baja, especialmente en ocasiones de uso de alta intensidad, y su vida útil es relativamente corta. Debido a su ligereza y bajo coste, suelen utilizarse en ocasiones de uso puntual o a corto plazo.
- Beneficios económicos
El coste inicial de compra del nailon es relativamente alto, pero los recursos son abundantes y el coste es controlable. Además, debido a su gran durabilidad, larga vida útil y bajo coste de mantenimiento, la rentabilidad en el uso a largo plazo es muy alta. Aunque la composición de los medios de desbarbado criogénicos también es nylon 6, debido a su uso y proceso de producción especiales, el coste de adquisición puede ser más elevado, pero la tasa de consumo es extremadamente baja. Las bolas de desbarbado de poliestireno tienen el coste más bajo y son abundantes en materias primas. Sin embargo, debido a su baja resistencia al desgaste, se consumen rápidamente, sobre todo en operaciones de alta intensidad, y tienen una vida útil relativamente corta.
- Seguridad operativa
El nailon tiene una alta seguridad de funcionamiento y es un material no tóxico. No produce gases nocivos ni subproductos cuando se utiliza dentro del intervalo normal de temperaturas. No causará daños evidentes a los operarios ni al medio ambiente cuando se utilice. Los medios de desbarbado criogénicos en sí son relativamente seguros, pero debido a que deben utilizarse en un entorno extremadamente criogénico, puede haber ciertos riesgos de seguridad en el funcionamiento de los equipos de refrigeración. Se requieren estrictas medidas de seguridad para proteger a los operarios y evitar la congelación. El poliestireno tiene una mayor seguridad de funcionamiento a temperatura ambiente, pero puede liberar gases nocivos a altas temperaturas, por lo que hay que evitar las operaciones a alta temperatura. Al mismo tiempo, este tipo de material es relativamente ligero y propenso al polvo. Durante su uso, debe prestarse atención a la filtración del aire para evitar su inhalación.
La poliamida y el poliestireno tienen propiedades y ámbitos de aplicación únicos. Comprender las diferencias entre ambos ayudará a ingenieros y diseñadores a tomar decisiones más informadas a la hora de elegir materiales. Para aplicaciones que requieren durabilidad y alto rendimiento, la poliamida es sin duda una mejor opción; mientras que para productos con mayores requisitos de economía y ligereza, el poliestireno es más adecuado. Si se tienen en cuenta todos los aspectos, elegir el material plástico adecuado es la clave para lograr el éxito del producto.
Filtros