De la rebaba a la perfección: las perlas de poliestireno optimizan los procesos de producción
14 de septiembre de 2024
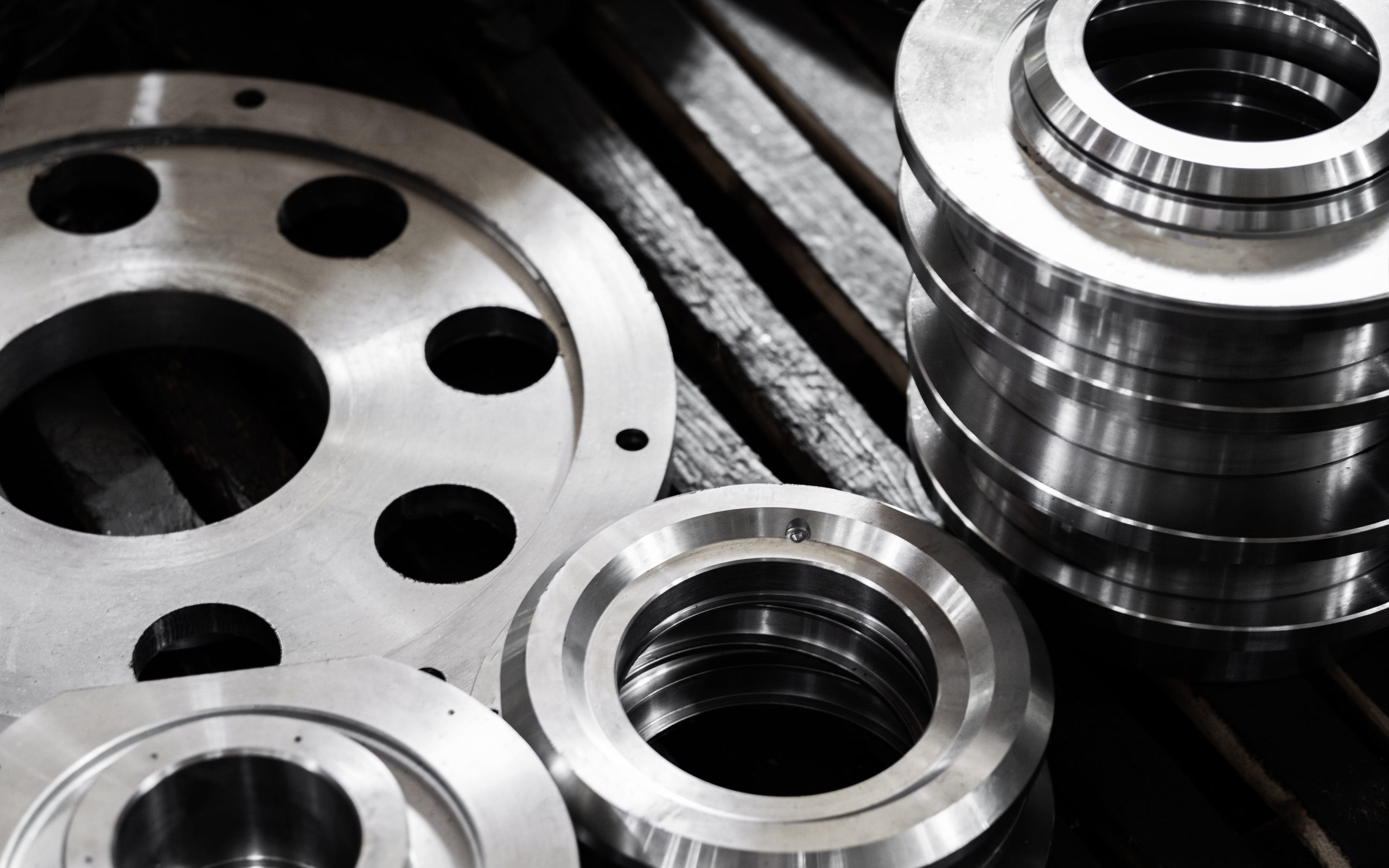
En el campo de la fabricación de precisión, el tratamiento de las rebabas es una cuestión que no puede ignorarse. Las rebabas no sólo afectan al aspecto y funcionamiento de las piezas, sino que también pueden provocar una disminución de la eficacia de la producción. Con el avance de la tecnología de fabricación, la introducción de equipos automatizados y medios eficaces ha proporcionado una nueva solución al problema de las rebabas. Como medio de arenado eficaz, las bolas de desbarbado de poliestireno pueden mostrar ventajas únicas en el procesamiento automatizado, superar las limitaciones de los procesos de desbarbado tradicionales y ayudar a los fabricantes de precisión a lograr un cambio cualitativo de las rebabas a la perfección.
Desafíos de los problemas de rebabas al mecanizado de precisión
En el campo de la fabricación de precisión, las rebabas aparecerán inevitablemente en el mecanizado, fresado, torneado y otros procesos. La presencia de rebabas afectará a la precisión de ajuste de las piezas, debilitará las propiedades mecánicas e incluso provocará fallos durante el montaje y el funcionamiento. En el pasado, los fabricantes solían recurrir a los siguientes métodos tradicionales para tratar las rebabas:
- Descarga manual
- Método: Utilice herramientas manuales (como limas, papel de lija, etc.) para eliminar directamente las rebabas.
- Ventajas: Bajo coste, adecuada para la producción a pequeña escala o el procesamiento de piezas complejas y precisas.
- Desventajas: La operación requiere mucho tiempo y depende de la experiencia de los trabajadores, por lo que es difícil garantizar la coherencia; el coste de la mano de obra es elevado y la eficacia del proceso es baja, lo que puede provocar fácilmente cuellos de botella en la producción.
- Desbarbado mecánico
- Método: Utilizar medios mecánicos como el corte, el esmerilado y el lapeado para eliminar las rebabas.
- Ventajas: Capaz de procesar un gran número de piezas de trabajo, con alta eficiencia, adecuado para piezas de trabajo con formas simples.
- Desventajas: Es fácil eliminar materiales en exceso, lo que reduce la precisión de las piezas, especialmente al procesar piezas complejas o pequeñas.
- Desbarbado térmico
- Método: Utilice altas temperaturas (como combustión o explosión) para fundir y eliminar rápidamente las rebabas.
- Ventajas: Capaz de procesar rebabas internas de difícil acceso, velocidad rápida, adecuada para el procesamiento a gran escala.
- Desventajas: Los equipos son caros y las propiedades del material o el acabado de la superficie pueden verse afectados durante el proceso.
- Desbarbado electroquímico
- Método: Elimina las rebabas mediante reacción electrolítica.
- Ventajas: Adecuado para piezas con formas complejas, y puede lograr el desbarbado a gran escala en poco tiempo.
- Desventajas: Coste elevado, necesidad de un electrolito especial y mantenimiento complejo de los equipos.
Aunque estos métodos tradicionales tienen sus propios escenarios de aplicación, a menudo presentan defectos cuando se enfrentan a los elevados requisitos del mecanizado de precisión. El desbarbado manual es ineficaz, el desbarbado mecánico puede causar daños en la superficie, y el desbarbado térmico y electroquímico son rápidos pero complejos y costosos, especialmente cuando se trata de piezas de precisión delicadas.
Características de las perlas de desbarbado de poliestireno
Para resolver mejor el problema de las rebabas, los fabricantes están recurriendo gradualmente a materiales de desbarbado más blandos y eficaces. Entre ellos, las perlas de desbarbado de poliestireno se han convertido en un medio de arenado ideal por sus propiedades físicas únicas.
- Precisión y coherencia: Las perlas de desbarbado de poliestireno son esféricas, de tamaño de partícula uniforme y gran consistencia. Esto significa que, al procesar piezas de precisión, se puede mantener un efecto de tratamiento de superficie estable, y el tratamiento de superficie desigual no será causado por el tamaño desigual de las partículas.
- Fuerza de corte suave pero eficaz: En comparación con los medios de arenado metálicos o más duros, los granos de desbarbado de poliestireno tienen una fuerza de corte más suave y son adecuados para procesar sustratos más frágiles. Puede eliminar eficazmente las rebabas sin causar daños excesivos en la superficie principal de la pieza, reduciendo así los productos defectuosos causados por un rectificado excesivo.
- Sin residuos: Dado que el propio poliestireno es químicamente estable, no se genera polvo ni residuos nocivos durante el proceso de desbarbado, lo que evita la necesidad de una limpieza secundaria. Esta es una ventaja significativa para los elevados requisitos de limpieza en el mecanizado de precisión.
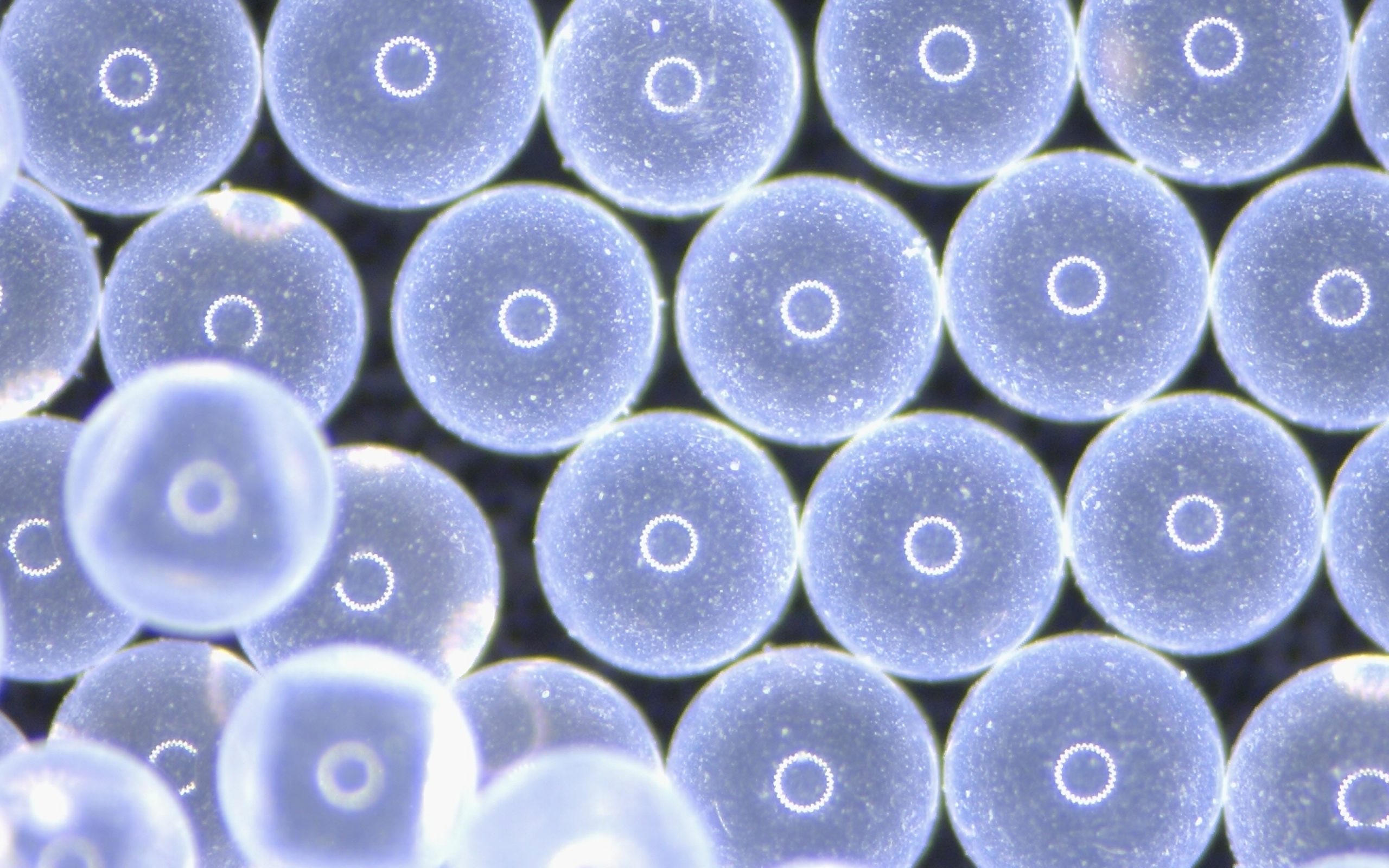
Esfera transparente perfecta
Equipos de chorreado automatizados y control de precisión
En la fabricación moderna, la introducción de equipos automatizados ha mejorado enormemente la eficacia y la uniformidad de la producción. La automatización de los equipos de arenado puede lograr un control eficaz y preciso del tratamiento de la superficie de las piezas, especialmente cuando se requiere una producción a gran escala. El sistema automatizado no sólo puede reducir la intervención manual, sino también mejorar la consistencia y estabilidad de la producción.
Ventajas de los equipos automatizados de chorro de arena
- Funcionamiento automatizado, que reduce la intervención manual: Los equipos automatizados de chorreado de arena pueden procesar piezas de forma continua de acuerdo con programas preestablecidos, evitando errores e incoherencias en la operación manual. Mediante un sistema de control preciso, el equipo puede procesar cada pieza con el mismo estándar, mejorando enormemente la eficiencia de la producción.
- Control de alta precisión: Los equipos de arenado modernos suelen estar equipados con sensores y sistemas de control avanzados, que pueden supervisar en tiempo real parámetros como la presión de arenado, el caudal del medio, el ángulo, etc., y ajustarlos según las distintas necesidades de las piezas para garantizar que el efecto del tratamiento sea preciso y controlable.
- Gran capacidad de procesamiento por lotes: Los equipos de arenado automatizados pueden procesar varias piezas de trabajo al mismo tiempo, lo que resulta especialmente adecuado para la producción de piezas de precisión que requieren una gran uniformidad. Gracias al procesamiento automatizado continuo, el tiempo total de producción de la pieza se acorta considerablemente.
- Adaptarse a diferentes materiales y estructuras complejas: Muchas piezas de precisión tienen estructuras geométricas y formas superficiales complejas, y los equipos automatizados de chorreado de arena pueden adaptarse fácilmente a estos cambios ajustando el ángulo de pulverización, la distancia y el tiempo, garantizando que todas las esquinas puedan ser eficazmente fresadas.
Equipo automatizado para desbarbado de perlas de poliestireno
- Granalladora rotativa
- Principio de funcionamiento: La pieza gira en la cámara de chorreado y la boquilla ajusta automáticamente el ángulo y la posición para garantizar una cobertura uniforme de todas las superficies de la pieza.
- Escenarios aplicables: Las arenadoras rotativas son muy adecuadas para procesar piezas de precisión con formas complejas que requieren un desbarbado completo. Los granos de poliestireno son especialmente adecuados para este tipo de equipos por su peso ligero, su pulverización uniforme y porque no producen demasiado impacto en la pieza.
- Arenadora de cinta continua
- Principio de funcionamiento: La pieza entra en la sala de arenado de forma continua a través de la cinta transportadora, y la boquilla procesa automáticamente la pieza a lo largo de la trayectoria establecida.
- Escenarios aplicables: Adecuado para escenarios de producción continua a gran escala. Las perlas de desbarbado de poliestireno pueden fluir a gran velocidad en este tipo de equipos, lo que garantiza que cada pieza de trabajo se procese uniformemente en el menor tiempo posible, mejorando la eficiencia de la producción.
- Sistema automático de pistola pulverizadora
- Principio de funcionamiento: El sistema de pistola automática utiliza programación CNC para granallar con precisión partes específicas de la superficie de la pieza, lo que resulta adecuado para procesar piezas con estructuras geométricas complejas y superficies de alta exigencia.
- Escenarios aplicables: Este sistema se utiliza a menudo en la producción de piezas de alta precisión y complejidad. La suave fuerza de corte de las perlas de poliestireno garantiza que la superficie de la pieza no se dañe bajo este preciso control. Al mismo tiempo, la presión y el ángulo de pulverización pueden ajustarse para diferentes piezas a fin de lograr un desbarbado preciso.
- Arenadora automática tipo caja
- Principio de funcionamiento: Este equipo suele utilizarse para el procesamiento de piezas de precisión de una sola pieza o de lotes pequeños. Después de que el operario introduzca las piezas en el equipo, el sistema completará automáticamente el desbarbado de acuerdo con los parámetros establecidos.
- Escenarios aplicables: Las arenadoras automáticas tipo caja son adecuadas para piezas que requieren un procesamiento personalizado y de alta precisión, especialmente en industrias como la de piezas médicas y electrónicas. La estabilidad y suavidad de las perlas de poliestireno las convierten en un medio de arenado ideal para este tipo de equipos.

HLH tiro real
Ventajas de las perlas de desbarbado de poliestireno en la automatización
En comparación con los materiales de desbarbado tradicionales, los granos de desbarbado de poliestireno funcionan especialmente bien en los equipos de arenado automatizados. Sus eficientes capacidades de procesamiento automatizado provienen principalmente de los siguientes aspectos:
- Influencia de la forma y la densidad de las partículas
- Las perlas de desarenado de poliestireno suelen presentar partículas esféricas regulares. Esta estructura esférica les confiere una excelente fluidez y uniformidad durante el proceso de chorreado, lo que les permite moverse libremente en el equipo de chorreado y cubrir uniformemente la superficie a procesar. Por el contrario, las partículas de forma irregular pueden atascarse o acumularse durante el proceso de chorreado, dando lugar a resultados de procesado poco uniformes.
- La menor densidad del poliestireno permite que estos granos de desbarbado tengan mayor velocidad y cobertura al granallar. Esto significa que, a la misma presión de chorreado, los granos de poliestireno pueden cubrir más rápidamente una superficie mayor, acelerando así el proceso. La ligereza de la densidad también significa que no ejercerán una fuerza de impacto excesiva sobre el sustrato como las partículas metálicas, lo que reduce el riesgo de dañar piezas delicadas.
- Resistencia al desgaste y durabilidad
- Aunque el poliestireno es un material ligero, tiene una buena resistencia al desgaste y puede utilizarse repetidamente en el equipo de chorreado sin romperse fácilmente. Esta durabilidad significa que, en un funcionamiento automatizado a largo plazo, los cordones de desbarbado de poliestireno no se sustituirán con frecuencia, lo que reduce la frecuencia de las paradas de producción y los costes de mantenimiento.
- Eficacia y coherencia del tratamiento
- Debido a su peso ligero y a la uniformidad de sus partículas esféricas, las perlas de poliestireno se procesan con mayor eficacia en los equipos de chorro de arena. Los equipos de chorro de arena pueden pulverizar estas perlas uniformemente sobre la superficie de la pieza a mayor velocidad, lo que garantiza una eliminación rápida y eficaz de las rebabas. Esta característica proporciona a las perlas de poliestireno una ventaja de tiempo significativa en la producción a gran escala, especialmente en entornos de producción que requieren un control preciso, lo que puede garantizar efectos de tratamiento de superficie altamente consistentes en cada pieza.
La clave para optimizar el proceso de producción: reducir las tasas de reprocesado y de desechos
En la fabricación de precisión, las tasas de retrabajo y de desechos son indicadores clave para medir la eficacia de la producción y la rentabilidad. Un exceso de reprocesado no sólo supone una pérdida de tiempo, sino que también aumenta los costes de producción y afecta a los beneficios de la empresa. Los cordones de desbarbado de poliestireno contribuyen a optimizar los procesos de producción, principalmente en los siguientes aspectos:
- Reducir los daños superficiales: Gracias a la suave fuerza de corte de las perlas de desbarbado de poliestireno, las piezas no sufrirán demasiados daños superficiales durante el proceso de desbarbado, lo que evitará la repetición de trabajos y el desguace causados por un rectificado excesivo. Esto es especialmente importante para piezas de alta precisión y alto coste.
- Reduzca los errores operativos: El uso de equipos automatizados de chorro de arena combinados con perlas de poliestireno puede reducir significativamente los errores operativos humanos. Mediante un control preciso de los parámetros, cada pieza puede obtener un efecto de tratamiento uniforme, lo que reduce los problemas de calidad causados por un tratamiento desigual.
- Reducir los costes de procesamiento posteriores: Dado que las perlas de poliestireno no generan polvo ni residuos durante el proceso de desbarbado, las piezas no suelen requerir procesos de limpieza adicionales tras el desbarbado. Esto no sólo acorta el tiempo de producción, sino que también reduce el coste del procesamiento posterior.
La doble ventaja de reducir el tiempo y el coste de procesamiento
El uso de perlas de desbarbado de poliestireno no sólo puede mejorar la eficacia de la producción, sino también reducir eficazmente los costes generales de procesamiento. Esta doble ventaja proviene de los siguientes puntos:
- Rápida velocidad de procesamiento: Debido a la buena fluidez y alta velocidad de pulverización de las perlas de desbarbado de poliestireno, puede cubrir rápidamente la superficie de la pieza y eliminar las rebabas de manera eficiente. Esto acorta en gran medida el tiempo de procesamiento de cada pieza, especialmente en la producción a gran escala, lo que puede mejorar significativamente la tasa de producción.
- Reducir el consumo de medios de comunicación: Los granos de desarenado de poliestireno tienen una larga vida útil y pueden reciclarse muchas veces durante el proceso de chorreado. En comparación con otros medios de chorreado de arena que se rompen con más facilidad, la resistencia al desgaste de los granos de poliestireno reduce la sustitución frecuente de los medios, con lo que se reduce el consumo de medios y los costes de mantenimiento por inactividad del equipo.
- Reducir la intervención manual: Mediante el uso de equipos automatizados, las perlas de desbarbado de poliestireno pueden completar eficazmente el proceso de desbarbado sin operación manual. Esto no solo reduce los costes de mano de obra, sino que también reduce los errores y los reprocesamientos causados por la operación manual.
En la fabricación de precisión, la calidad y la eficiencia son el núcleo de la competencia. Los granos de desbarbado de poliestireno, como medio de chorreado de gran eficacia y bajas pérdidas, pueden ayudar a los fabricantes a optimizar los procesos de producción, reducir las repeticiones y los desechos y reducir los costes generales gracias a sus propiedades físicas únicas y a su excelente rendimiento en equipos automatizados. Con la introducción de esta innovadora solución de desbarbado, los fabricantes no sólo pueden mejorar la calidad de la superficie de sus productos, sino también mejorar significativamente la eficiencia de la producción, logrando un cambio cualitativo de las rebabas a la perfección.
Filtros