Aplicaciones industriales del granallado con óxido de aluminio ultrafino
21 de agosto de 2024
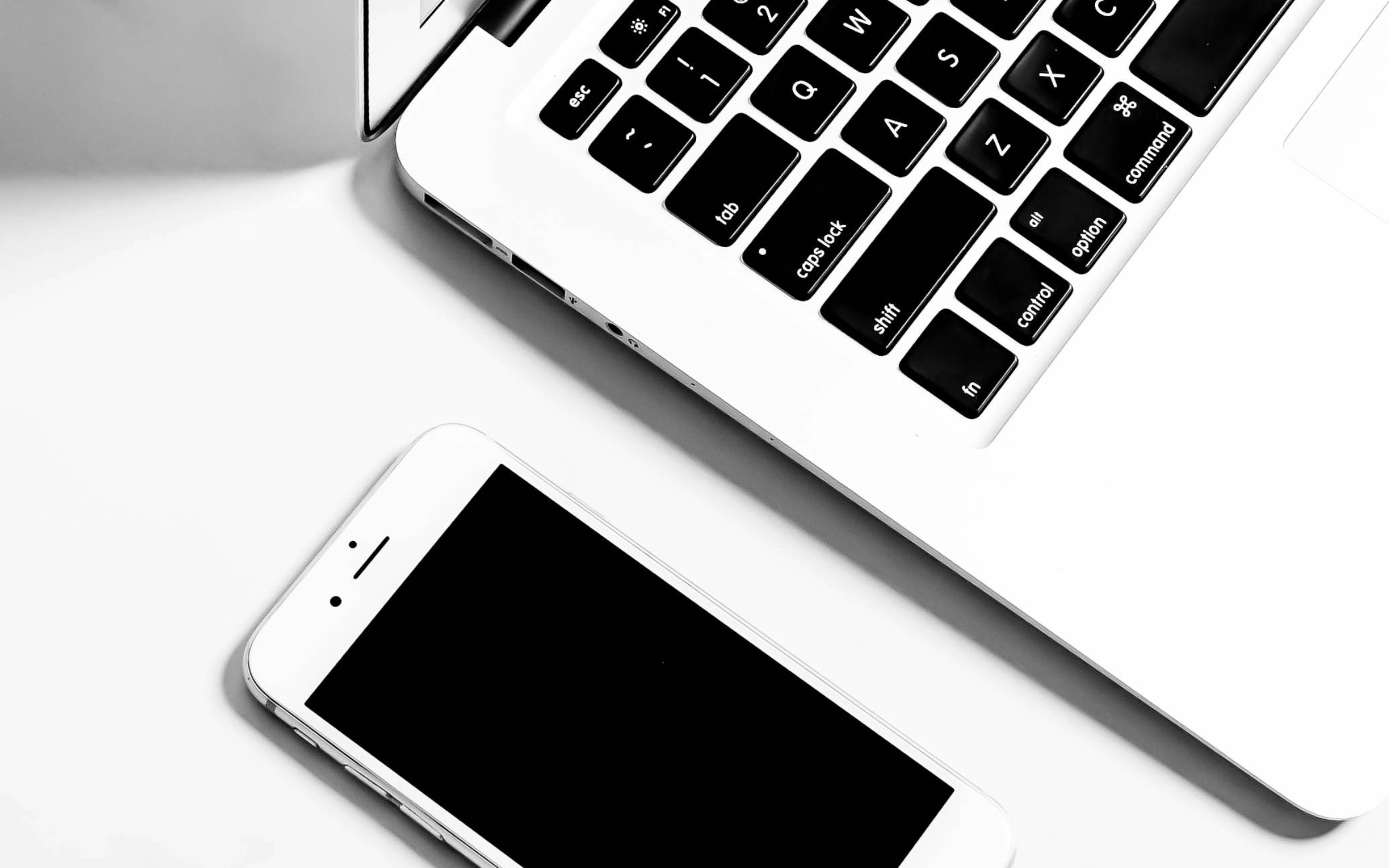
En la fabricación moderna, el avance continuo de la tecnología de tratamiento de superficies repercute directamente en la calidad, el rendimiento y la vida útil de los productos. Entre las muchas tecnologías de tratamiento de superficies, el proceso de chorro de arena se ha convertido gradualmente en la opción preferida en varias industrias debido a su excelente rendimiento en la eliminación de impurezas, la mejora del rendimiento de la superficie y el procesamiento fino.
Como representante destacado entre los materiales de arenado, el arenado con óxido de aluminio ultrafino, con sus características de alta pureza, alta dureza y estabilidad, ha demostrado ventajas insustituibles en industrias de gran demanda como la aeroespacial, la fabricación de automóviles, la fabricación de dispositivos médicos, la electrónica de consumo y la militar. En este artículo se analizarán en profundidad las tres ventajas principales del granallado con óxido de aluminio.perseguir la apariencia y la funcionalidad, garantizando una alta calidad del producto y un excelente rendimiento en entornos difíciles-y le ayudarán a comprender mejor el papel que desempeñan estos medios y su efecto en estos campos combinando los requisitos específicos de la industria.
Antes de explorar las aplicaciones específicas de la granalla de óxido de aluminio ultrafino, es necesario repasar brevemente sus características. El granallado con óxido de aluminio ultrafino se compone principalmente de partículas de alúmina de gran pureza, con tamaños de partícula que suelen oscilar entre 1 y 5 micras. Esta granalla tiene las siguientes características clave(Haga clic para ver):
- Alta dureza y resistencia al desgaste: Con una dureza Mohs de 7-9, sólo superada por el diamante y el carburo de silicio, puede eliminar eficazmente diversas impurezas superficiales. También puede mantener un rendimiento estable tras múltiples usos, alargando su vida útil.
- Alta pureza y baja contaminación: La pureza de la alúmina (Al₂O₃) suele ser superior a 99%, lo que garantiza que no se generen impurezas ni contaminación durante el proceso de arenado.
- Inercia química: No es propenso a reacciones químicas con otros materiales, por lo que es adecuado para diversos entornos agresivos, como altas temperaturas, ácidos fuertes y álcalis fuertes.
- Capacidad de procesamiento fino: La granalla ultrafina de óxido de aluminio tiene una forma multifacética, casi esférica u otras formas irregulares. Debido a su pequeño tamaño, puede penetrar en huecos diminutos o estructuras complejas, logrando un tratamiento uniforme de la superficie. Además, como las partículas son uniformes, puede garantizar unos resultados de tratamiento de superficies uniformes.
Tras comprender las características y ventajas del chorreado con óxido de aluminio, analizaremos sus efectos de aplicación práctica en campos específicos:
Aplicación en electrónica de consumo: Persiguiendo la apariencia y la funcionalidad
Contexto industrial
En el sector de la electrónica de consumo, el tratamiento de la superficie de productos como teléfonos inteligentes, ordenadores portátiles y dispositivos portátiles afecta directamente a la calidad del aspecto del producto y a la experiencia del usuario, lo que influye en las decisiones de compra de los consumidores. Por lo tanto, para garantizar que los productos de electrónica de consumo tengan un aspecto bonito y una funcionalidad fiable, es crucial un tratamiento de superficies de alta precisión. Puede mejorar eficazmente la textura del producto y proporcionar una buena base para los posteriores procesos de recubrimiento e impresión, lo que es de gran importancia.
Efecto de la aplicación práctica
Apple utilizó por primera vez el chorreado con óxido de aluminio para el tratamiento de superficies del iPhone 5 lanzado en 2012. Debido al tamaño extremadamente pequeño de las partículas de granalla, el chorreado con óxido de aluminio puede penetrar en huecos diminutos para un tratamiento uniforme de la superficie, lo que garantiza una textura uniforme de la superficie y evita problemas de calidad durante el montaje o el uso a largo plazo.
Gracias a este proceso, la superficie del cuerpo de aluminio se volvió más lisa y presentó un efecto mate, lo que mejoró enormemente la estética y el tacto del producto. Además, la carcasa arenada ofrece una excelente resistencia a los arañazos y al desgaste, lo que prolonga la vida útil del producto. Para los usuarios que buscan dispositivos duraderos y de alta calidad, este es sin duda un argumento de venta importante. En última instancia, este proceso de tratamiento ayudó a Apple a mejorar con éxito la competitividad de su producto en el mercado, seguido por otros fabricantes de smartphones.
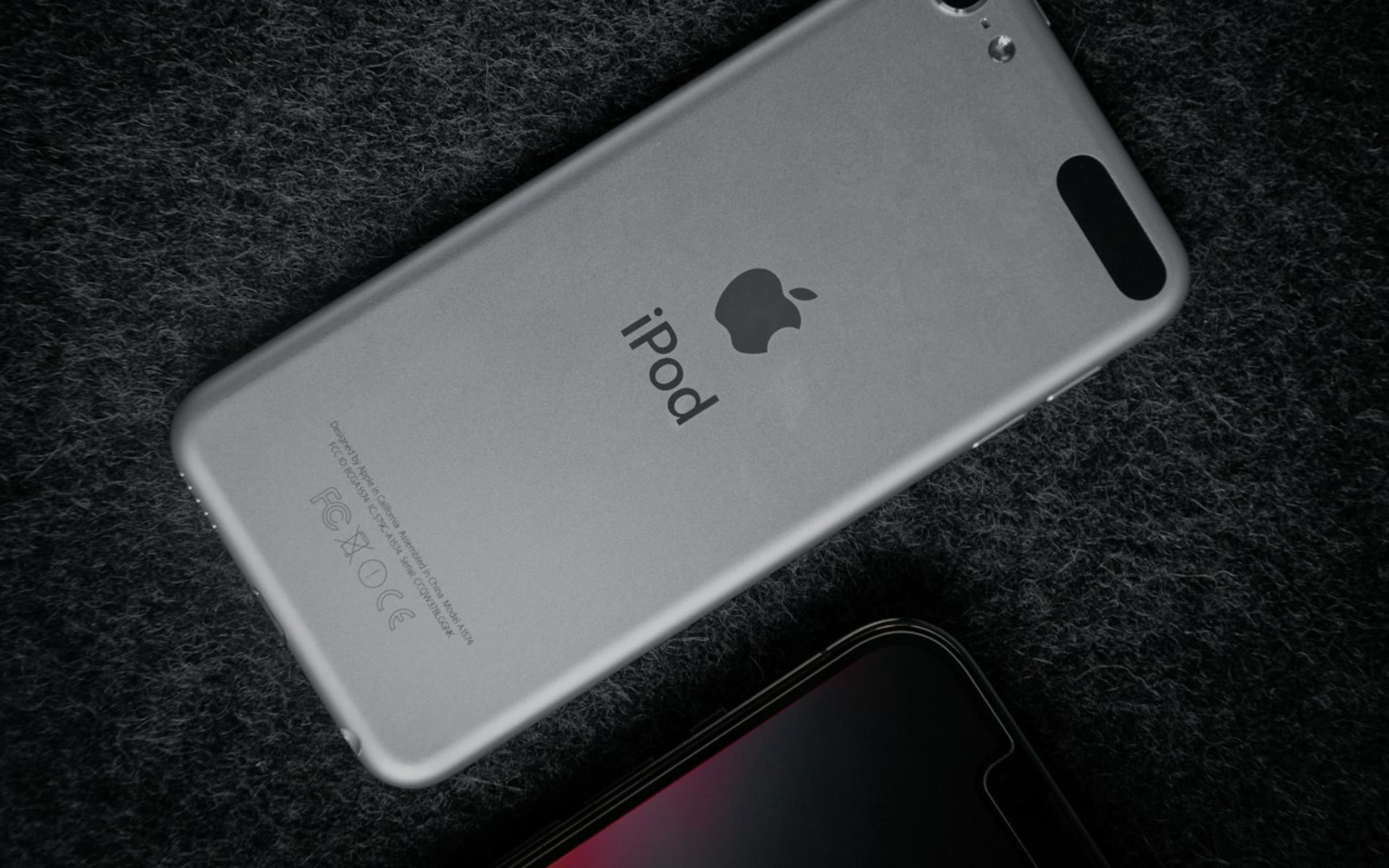
un teléfono con aspecto mate esmerilado
Del mismo modo, algunos fabricantes de portátiles también utilizan la tecnología de granallado con óxido de aluminio para el tratamiento de superficies, como las series ThinkPad X1 Carbon y Yoga de Lenovo, la serie XPS de Dell y la serie ZenBook de ASUS.
Aplicación en el sector aeroespacial: Garantizar la alta calidad del producto
Contexto industrial
La industria aeroespacial tiene unos requisitos de calidad del producto extremadamente exigentes, centrados en la consistencia y durabilidad de los materiales. Los componentes aeroespaciales y de aviación suelen estar fabricados con aleaciones ligeras pero de alta resistencia, como aleaciones de aluminio y aleaciones de titanio. Estos materiales deben soportar cambios extremos de temperatura, vibraciones mecánicas de alta intensidad y otras condiciones ambientales adversas, lo que plantea exigencias extremadamente altas al tratamiento superficial de los materiales. Debido a la particularidad de esta industria, cada componente debe cumplir estrictas normas industriales, y no hay margen para el error, desde la selección del material hasta la precisión del procesamiento. Cualquier pequeño defecto o incoherencia puede acarrear graves consecuencias, como fallos del sistema o incluso catástrofes.
Efecto de la aplicación práctica
El granallado con óxido de aluminio se utiliza para limpiar las capas superficiales de óxido, herrumbre y otras impurezas de las piezas. Las pequeñas partículas uniformes garantizan la limpieza y consistencia de la superficie del objeto pretratado. Tomando como ejemplo las palas de turbina de los motores de aviación, la superficie de las palas debe ser absolutamente lisa y plana para reducir la resistencia del aire y mejorar la eficiencia del combustible.
Las pruebas demuestran que, tras utilizar el granallado con óxido de aluminio ultrafino para tratar la superficie del álabe, sin dañar el sustrato, se puede mejorar la durabilidad del álabe entre 10% y 15%, y el acabado superficial entre 15% y 20% (hasta 30% en el máximo). Estas mejoras son cruciales para el funcionamiento estable de los motores de turbina en condiciones extremas y reducen la dificultad y el coste del tratamiento posterior.
Boeing utiliza la tecnología de arenado con óxido de aluminio en su proceso de fabricación de aviones para tratar los componentes de aleación de aluminio y las superficies de los fuselajes, eliminando eficazmente las capas de óxido y los defectos superficiales, lo que mejora la resistencia y longevidad de los componentes. La NASA también emplea esta tecnología en la fabricación y el mantenimiento de sus naves espaciales y satélites, utilizándola para tratar las superficies de diversos componentes con el fin de mejorar su resistencia a la fatiga y su estabilidad a largo plazo. Airbus también utiliza técnicas de granallado en sus procesos de fabricación y mantenimiento de aeronaves para mejorar el acabado y la adherencia de las superficies, aumentando así el rendimiento y la fiabilidad general de la aeronave. La importancia de la tecnología de granallado con óxido de aluminio para garantizar productos de alta calidad es claramente evidente.
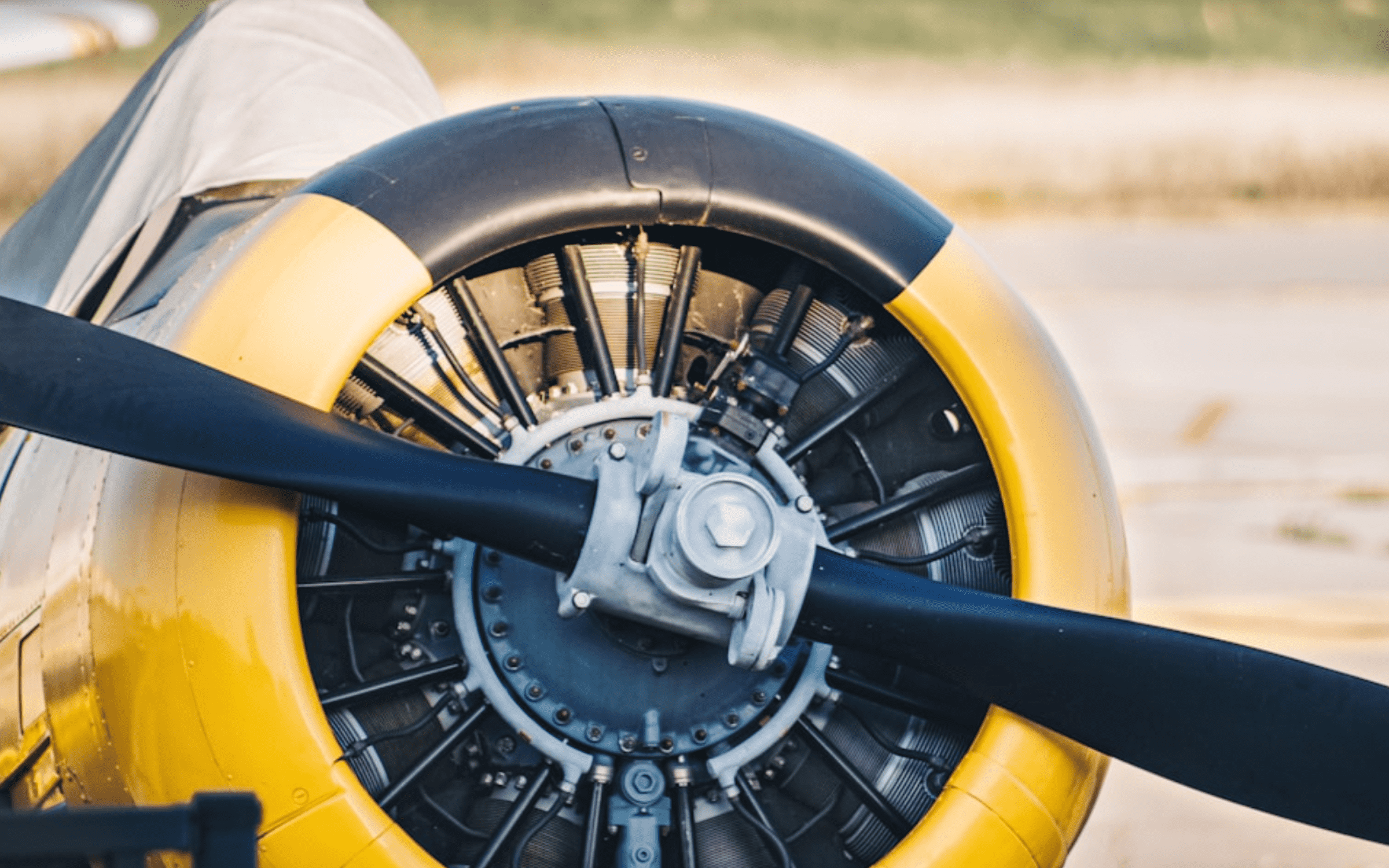
pala de turbina
Aplicación en la industria militar: Excelentes prestaciones en entornos difíciles
Contexto industrial
La industria militar suele superar los requisitos de la industria convencional en cuanto al rendimiento de los productos, especialmente en los entornos extremos a los que deben enfrentarse armas y equipos, vehículos blindados, etc. La durabilidad, resistencia a la corrosión y fiabilidad de los materiales son extremadamente importantes. Los productos militares deben mantener un rendimiento excelente y estable en entornos extremos como alta temperatura, baja temperatura, alta humedad y ácidos fuertes. Por lo tanto, el refuerzo de la superficie de los componentes es la base de suma importancia.
Efecto de la aplicación práctica
Gracias a su altísima dureza e inercia química, el chorreado con óxido de aluminio puede proporcionar una excelente durabilidad y estabilidad en el tratamiento de superficies de productos militares. Ya se trate de piezas de barcos en un entorno marino o de vehículos blindados en un entorno desértico, el chorreado con óxido de aluminio puede contribuir a mejorar la fiabilidad de los equipos militares. Además, las superficies tratadas con chorro de óxido de aluminio pueden evitar eficazmente la formación de microfisuras, mejorando así la resistencia general y la vida útil de los materiales.
Por ejemplo, las empresas militares suelen utilizar el granallado con óxido de aluminio para el tratamiento y refuerzo de la superficie cuando fabrican hélices para buques. La resistencia de la superficie a la corrosión y al desgaste de las hélices mejora considerablemente, lo que no sólo prolonga la vida útil del equipo, sino que también reduce los costes de mantenimiento. En el uso posterior, este método de tratamiento no sólo mejora el rendimiento de la hélice, sino que también reduce la tasa de averías del equipo. Otro ejemplo es que las placas de blindaje de los vehículos militares deben tener una resistencia extremadamente alta a las balas y al desgaste para proteger la seguridad de los ocupantes en diversas condiciones extremas. La superficie de las placas de blindaje tratada con granallado de óxido de aluminio puede mejorar significativamente la resistencia y durabilidad del material, alargando así la vida útil de la placa de blindaje y mejorando la capacidad de protección general.
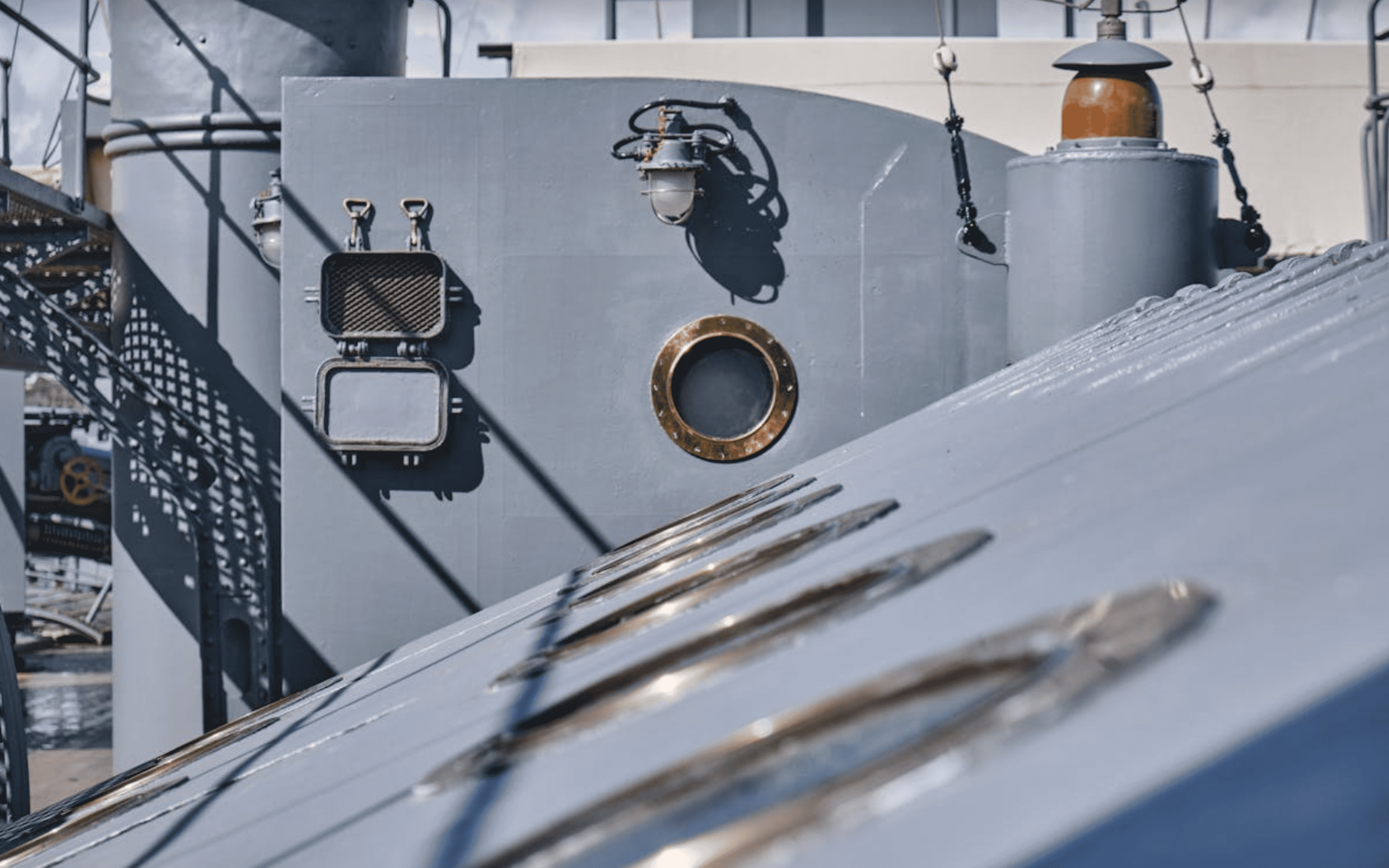
Placas de blindaje militar
Por supuesto, en el actual entorno de mercado altamente competitivo, las expectativas de los clientes respecto a los proveedores han superado la mera calidad del producto. Les preocupa más la estabilidad y coherencia de toda la cadena de suministro. Especialmente en algunas industrias de gran demanda, la calidad estable del producto y la gestión fiable de la cadena de suministro se han convertido en los factores clave que determinan el éxito o el fracaso. Como empresa dedicada a la investigación y producción de nuevos materiales para el tratamiento de superficies, Jangsu Henglihong Industrial Co. Ltd. (HLH) entiende esto profundamente y garantiza un suministro continuo de productos estables y de alta calidad para los clientes mediante una serie de estrictas medidas y sistemas de gestión, ayudando a los clientes a obtener ventajas en el proceso de producción.
Meticuloso sistema de control de calidad
El sistema de control de calidad de HLH se basa en las normas internacionales ISO9001:2008 e ISO14001 (y ha superado las certificaciones CE y RoHS de la UE), combinadas con los años de experiencia acumulada de la empresa en el sector, formando un proceso integral de gestión de la calidad. Cada paso, desde la adquisición de materias primas hasta la producción y las pruebas finales del producto, se controla estrictamente para garantizar que los productos cumplen los requisitos de alto nivel de los clientes.
Selección y adquisición de materias primas: Sabemos que la estabilidad de la calidad del producto depende en primer lugar de la calidad de las materias primas. Por ello, HLH ha establecido relaciones de cooperación a largo plazo con los principales proveedores de materias primas del mundo. Seleccionamos estrictamente a los proveedores, exigiéndoles materias primas certificadas de gran pureza, y realizamos periódicamente controles de calidad de las materias primas para asegurarnos de que cada lote de materias primas cumple nuestras normas de calidad.
Control de precisión del proceso de producción: Durante la producción, HLH utiliza avanzados equipos automatizados y sistemas de control inteligentes para garantizar la precisión y consistencia del proceso de producción. Hemos introducido un sistema de supervisión en tiempo real que puede recoger y analizar datos en cada fase de la producción, identificar y corregir rápidamente posibles problemas y garantizar la estabilidad de la calidad de cada lote de productos.
Inspección y seguimiento exhaustivos de la calidad: Una vez terminado el producto, llevamos a cabo exhaustivas inspecciones de calidad de cada lote de productos, que incluyen la distribución del tamaño de las partículas, la dureza, la composición química y otros indicadores clave. También hemos introducido un sistema de seguimiento avanzado que puede gestionar el seguimiento de todo el ciclo de vida de cada lote de productos, garantizando que cada lote de productos que reciben los clientes tenga una calidad constante.
Medidas para garantizar la estabilidad de la cadena de suministro
Además de garantizar la calidad de los productos, HLH también aplica una serie de medidas para asegurar la estabilidad de la cadena de suministro y satisfacer la demanda de los clientes de un suministro estable. Sabemos que una cadena de suministro estable no solo es crucial para el desarrollo de las empresas, sino también una garantía importante para que los clientes ganen en la competencia del mercado.
Inventario suficiente y mecanismo de respuesta rápida: HLH mantiene siempre un inventario suficiente de materias primas y productos acabados para responder a los pedidos urgentes de los clientes y a las fluctuaciones de la demanda del mercado. Hemos establecido un mecanismo de respuesta rápida, capaz de coordinar la producción y la logística en el menor tiempo posible para garantizar que los pedidos de los clientes se entreguen a tiempo.
Programación flexible de la producción y distribución diversificada de la cadena de suministro: Para responder a los cambios en la demanda del mercado y a las incertidumbres de la cadena de suministro, HLH ha adoptado una estrategia flexible de programación de la producción. Disponemos de múltiples bases de producción y hemos establecido asociaciones estratégicas con múltiples empresas de logística, lo que permite ajustar con flexibilidad los planes de producción y los acuerdos de transporte según sea necesario para garantizar la continuidad del suministro.
Estrecha comunicación y cooperación con los clientes: HLH sabe que una estrecha comunicación con los clientes es la clave para garantizar la estabilidad de la cadena de suministro. Mantenemos una comunicación periódica con los clientes para conocer los cambios en su demanda y ajustar nuestros planes de producción y suministro en función de sus comentarios.
HLH garantiza que sus clientes obtengan resultados de alta calidad en el tratamiento de superficies y reduzcan las incertidumbres y los riesgos en sus procesos de producción mediante un riguroso control de calidad de los productos y una capacidad de suministro fiable.
Elegir a HLH significa seleccionar a un socio con más de veinte años de profunda experiencia, tecnología avanzada y excelente servicio en el campo del tratamiento de superficies. Tanto si se trata de satisfacer las demandas de calidad constante como de garantizar un suministro estable, HLH puede satisfacer estas necesidades y ayudar a los clientes a mantenerse a la cabeza en un mercado competitivo.
A través de la introducción de la aplicación del granallado con óxido de aluminio ultrafino en industrias específicas, podemos ver claramente sus ventajas únicas en la fabricación industrial moderna. A medida que la tecnología sigue avanzando y las demandas de la industria aumentan, el granallado con óxido de aluminio ultrafino seguirá desempeñando un papel importante en las aplicaciones industriales futuras, ayudando a diversas industrias a alcanzar estándares más altos y perspectivas de desarrollo más amplias.
En un entorno de mercado cada vez más complejo, HLH, con su estricto sistema de control de calidad y una gestión estable de la cadena de suministro, satisface con éxito la doble necesidad de los clientes de contar con productos de alta calidad y un suministro estable. Tanto si se trata de afrontar los retos de la producción a gran escala como de cumplir los requisitos de rendimiento en entornos difíciles, HLH, con su tecnología puntera y su excelente servicio, ayuda a los clientes a lograr un mayor éxito en sus respectivos sectores. En el futuro, HLH seguirá posicionándose como líder mundial en chorro de arena, mejorando continuamente la calidad de sus productos y servicios para corresponder al apoyo y la confianza de los clientes.
Filtros