Keramische Perles Benutzerhandbuch: 7 Schritte zur Verbesserung der Formverarbeitung
Februar 12, 2025
Die Aufrechterhaltung einer gleichmäßigen Oberfläche ist eines der wichtigsten Ziele bei der Herstellung und Wartung von Formen. Doch selbst wenn der Standardprozess strikt eingehalten wird, stoßen viele Kunden auf die folgenden Probleme:
"Warum entspricht die Oberfläche der Form immer noch nicht dem Standard?"
"Wie vermeidet man Kratzer auf der Oberfläche der Form beim Sandstrahlen?"
"Wie kann man die Effizienz der Nutzung von Keramikperlen optimieren?"
Die wesentlichen Erfordernisse bei diesen Problemen sind:
- Reproduzierbarkeit - Die Oberflächenbeschaffenheit verschiedener Chargen von Formen muss gleichmäßig sein.
- Kostenkontrollierbarkeit - Medienverluste und Arbeitskosten zu reduzieren und die Kostenleistung zu verbessern.
- Betriebliche Sicherheit - Gewährleistung einer sicheren Produktion durch Staubkontrolle und Schutz der Ausrüstung.
Als Antwort auf die oben genannten Anforderungen haben wir ein professionelles Verfahren in 7 Schritten zusammengefasst, das Ihnen hilft, die Formoberfläche effizient und sicher zu verbessern.
Schritt 1: Inspektion vor der Behandlung, um die Quelle versteckter Gefahren zu beseitigen
Schmerzpunkte der Kunden
- Das Ignorieren kleinerer Defekte (z. B. 0,1-mm-Kratzer) führt zu späteren Polierfehlern.
- Ein schlechter Gerätezustand (z. B. Düsenverschleiß) führt zu einer Verschwendung von Strahlmittel und mindert den Strahlungseffekt.
Lösung
1.1 Erkennung von Schimmelpilzdefekten
Prüfen Sie die Formoberfläche mit einer 20-fachen Lupe und konzentrieren Sie sich dabei auf die Trennfuge und die Entlüftungsnut. Zur genauen Messung der Oberflächenbeschaffenheit wird ein tragbares Oberflächenrauhigkeitsmessgerät (z. B. Mitutoyo SJ-210) empfohlen.
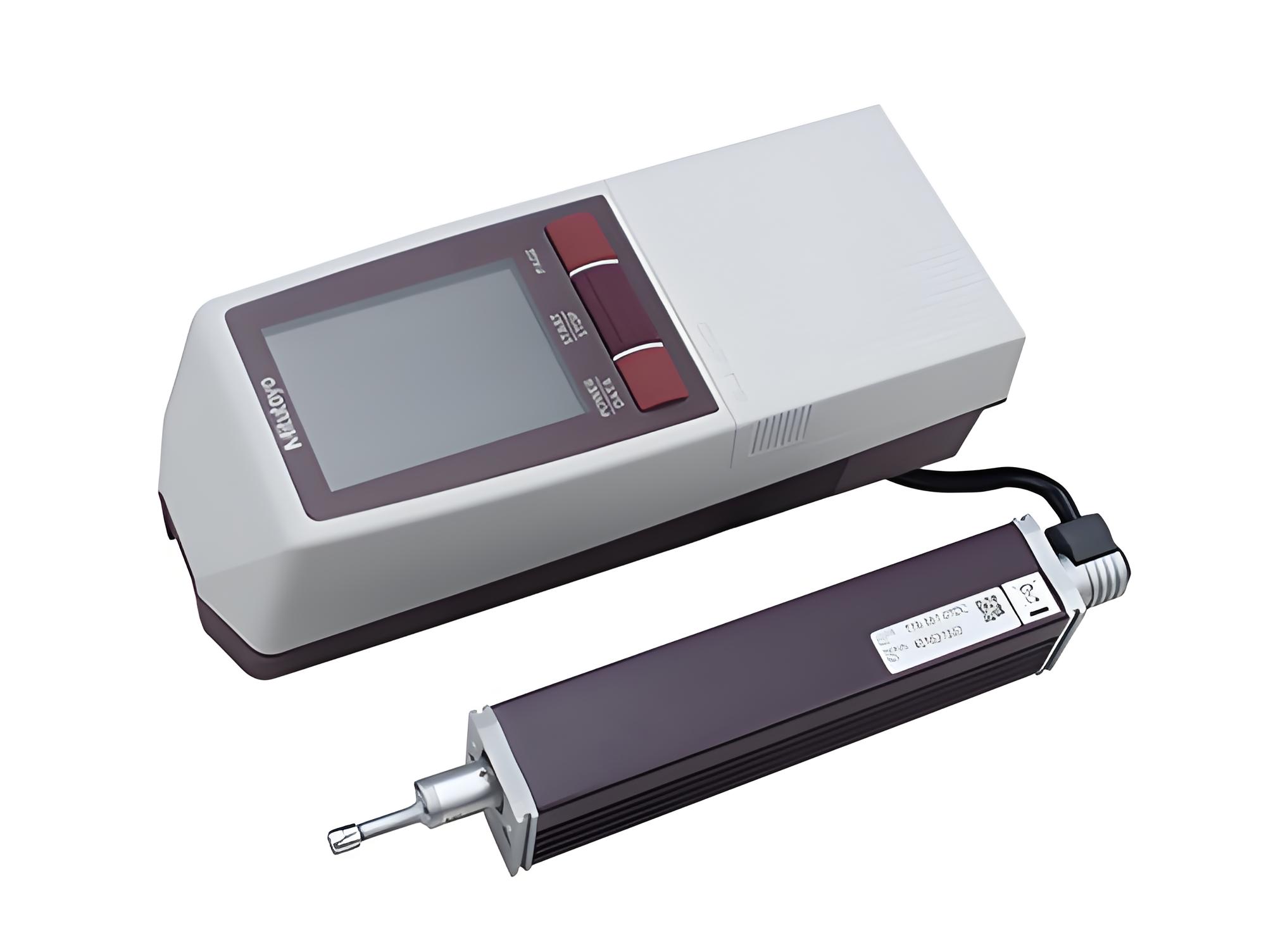
1.2 Liste der Ausrüstung vor der Inspektion
- Verschleiß der Düse: Die Änderung des Innendurchmessers sollte≤5% sein, und es muss ersetzt werden, wenn es überschreitet.
- Stabilität des Luftdrucks: Schwankungsbereich≤±2 PSI, um eine instabile Einspritzung zu vermeiden.
Schritt 2: Druckeinstellungsformel, Wissenschaft ersetzt Erfahrung
Schmerzpunkte der Kunden
- Wenn man sich bei der Einstellung des Drucks auf die Erfahrung verlässt, führt dies zu einem Überschleifen weicher Materialien oder einer unzureichenden Reinigung harter Materialien.
Art des Materials | Materialkoeffizient |
---|---|
Kunststoff (ABS) | 0.8 |
Aluminiumlegierung | 1.2 |
Rostfreier Stahl | 1.5 |
Titan-Legierung | 2.0 |
Hartmetall | 2.5 |
Lösung
2.1 PSI-Berechnungsformel
PSI = mittlere Härte × Werkstoffkoeffizient des Werkstücks × 10
Beispielrechnung:
Form aus Titanlegierung unter Verwendung von Keramikkugeln mit 7 Mohs-Härte:
PSI = 7 × 2.0 × 10 = 140
2.2 Tipps zur Druckeinstellung
Messen Sie den Ra-Wert nach dem ersten Einsatz: Wenn der Ra-Wert zu hoch ist, erhöhen Sie den PSI-Wert um 5-10; wenn der Ra-Wert zu niedrig ist, verringern Sie den PSI-Wert um 5-10.
Schutz durch weiches Material: Bei Kunststoffformen liegt die Obergrenze des PSI bei 80, um ein Überschleifen zu vermeiden.
Effiziente Reinigung von harten Materialien: Bei Formen aus Titanlegierungen liegt die Untergrenze des PSI-Wertes bei 140, um die Reinigungswirkung zu gewährleisten.
Schritt 3: Kontrolle von Winkel und Abstand, der Sieg der geometrischen Mechanik
Schmerzpunkte der Kunden
- Die vertikale Einspritzung führt zu lokalem Überschleifen, und der Auftreffwinkel von 30° ist schwer genau zu kontrollieren.
Lösung
3.1 Optimierungslösung für 30°-Einfallswinkel
- Bei einem Auftreffwinkel von 30° beträgt die Tangentialkraft 70% und die Normalkraft 30%, wodurch ein Gleichgewicht zwischen Reinigungseffizienz und Oberflächenschutz erreicht wird.
- Sprühabstand = Düsendurchmesser × 10 (zum Beispiel: 8mm Düse → 80mm Abstand)
3.2 Praktische Instrumente
Die Laser-Winkelanzeige (Fehler ±1°) gewährleistet eine präzise Winkelkontrolle.
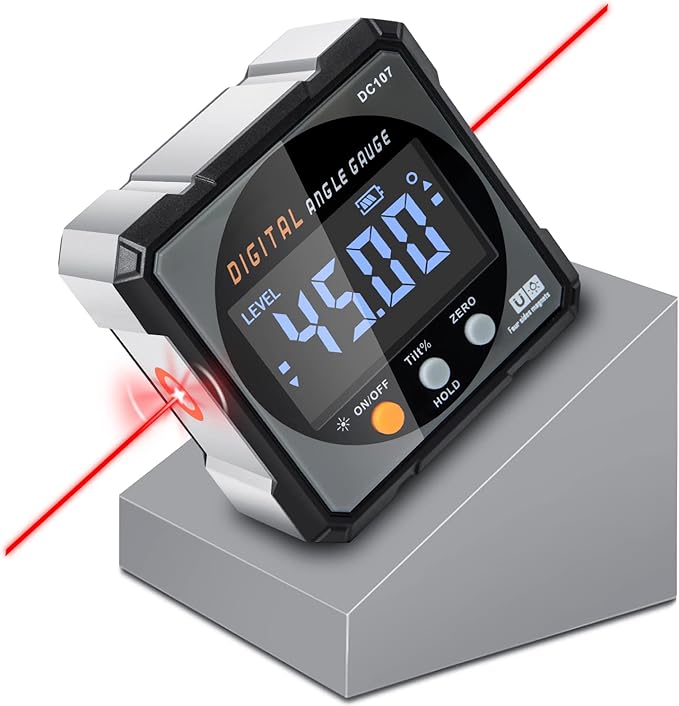
Schritt 4: Überwachung des Medienzustands - der Schlüssel zur Verlängerung der Lebensdauer
Schmerzpunkte der Kunden
- Sie können nicht bestimmen, wann die Keramikkugeln ersetzt werden müssen, was zu Kostenverschwendung oder Qualitätseinbußen führt.
Lösung
4.1 Erkennung der Quetschgeschwindigkeit
Nehmen Sie 100 g des Mediums und sortieren Sie die zerkleinerten Partikel manuell. Wenn die Zerkleinerungsrate >5% ist, muss es ersetzt werden.
4.2 Intelligente Online-Überwachung
Installieren Sie einen Online-Partikelgrößensensor, um die Veränderung der Partikelgröße des Mediums in Echtzeit zu überwachen.
HLH Keramikperlen Modell | Standard-Partikelgröße (µm) | Zulässige Abweichung (µm) |
---|---|---|
B20 | 600-850 | ±50 |
B30 | 425-600 | ±35 |
B40 | 250-425 | ±20 |
B60 | 125-250 | ±15 |
B80 | 180-250 | ±15 |
B100 | 125-180 | ±10 |
B120 | 63-125 | ±8 |
B125 | 0-125 | ±8 |
B170 | 45-90 | ±5 |
B205 | 0-63 | ±5 |
B400 | 30-63 | ±3 |
B505 | 10-30 | ±2 |
Schritt 5: Qualitätsprüfungsstandards für die Nachbearbeitung, datenbasierte Abnahme
Schmerzpunkte der Kunden
- Eine reine Sichtprüfung führt dazu, dass das Problem der mangelhaften Verarbeitung erst spät erkannt wird.
Lösung
5.1 Empfohlene Werkzeuge zur Messung des Ra-Werts
Grundmodell: Time 3220 Handmessgerät für die Rauheit
Vorteile: tragbar und einfach zu bedienen, geeignet für schnelle Vor-Ort-Detektion, Genauigkeit ±5%.
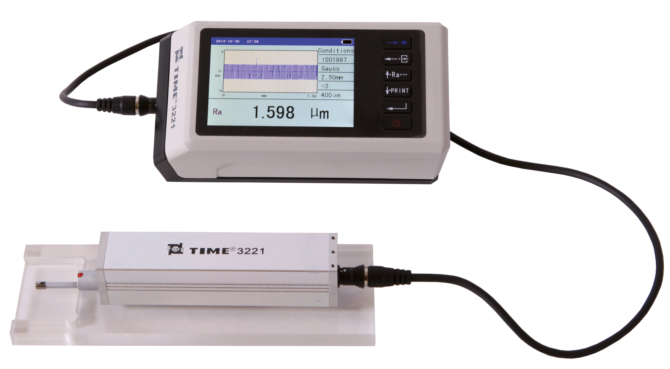
Hochpräzises Modell: Optisches 3D-Profilmessgerät Zygo NewView 9000.
Vorteile: hochpräzise Messung, geeignet für komplexe Oberflächen, Auflösung bis in den Nanometerbereich.
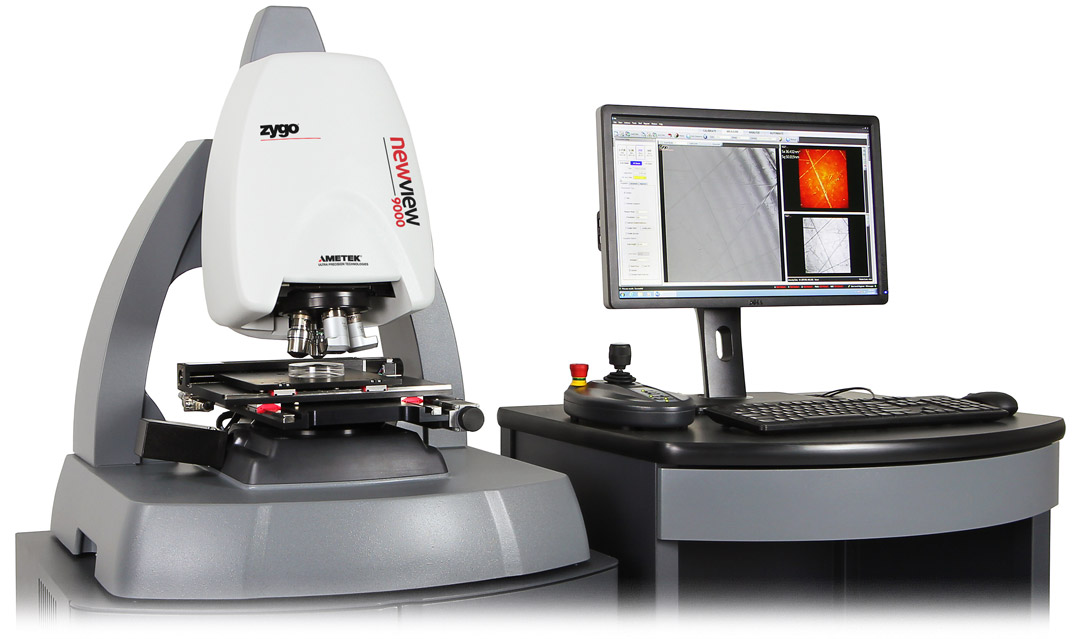
5.2 Industrie-Ra-Wert-Standards
Ausgewählte Branchen | Gewöhnliche Materialien | Ra-Anforderungen (µm) | Anzahl der Prüfpunkte |
---|---|---|---|
Elektronische Komponenten | Anschlüsse aus Kupferlegierung | ≤0.4 | ≥10 Punkte/㎡ |
Präzisions-Kunststoff-Gehäuse | ≤0.6 | ≥8 Punkte/㎡ | |
Autoteile | Motorteile aus Aluminiumlegierung | ≤0.8 | ≥5 Punkte/㎡ |
Bremsscheiben aus rostfreiem Stahl | ≤1.0 | ≥6 Punkte/㎡ | |
Medizinische Geräte/Implantate | Orthopädische Implantate aus Titanlegierungen | ≤0.4 | ≥12 Punkte/㎡ |
Chirurgische Instrumente aus rostfreiem Stahl | ≤0.6 | ≥10 Punkte/㎡ | |
Luft- und Raumfahrt | Turbinenschaufeln aus einer Titanlegierung | ≤0.3 | ≥15 Punkte/㎡ |
Motorteile aus Hochtemperaturlegierungen | ≤0.5 | ≥10 Punkte/㎡ |
Schritt 6: Abfallbehandlungsspezifikationen, Einhaltung der Vorschriften und gleichzeitige Kostensenkung
Schmerzpunkte der Kunden
- Die Kosten für die Abfallbehandlung sind hoch, und es bestehen Umweltrisiken.
Lösung
6.1 Recyclingverfahren für Keramikkugeln
Magnetische Trennung (Entfernung von Metallverunreinigungen) → Luftzerlegung (Entfernung von Staub) → Siebung (Sortierung und Wiederverwendung)
Rückgewinnungsrate: ≥85% (Zerkleinerungsrate muss <5% kontrolliert werden).
6.2 Konforme Behandlung von Abfallstoffen
- Keramischer Staub (unschädliche Deponie)
- Metallabfälle (professionelles Recycling)
Schritt 7: Fehlersuche bei häufigen Problemen, Kurzanleitung
Schmerzpunkte der Kunden
- Plötzliche Probleme (z. B. unebene Oberfläche) führen zum Stillstand der Produktionslinie
Lösung
Problematisches Phänomen | Mögliche Gründe | Lösung |
---|---|---|
Teilweise matt | Ungleiche Verteilung der Medien | Überprüfen Sie den Sandabscheider und reinigen Sie die Verstopfungsstelle |
Periodische Streifen | Verschleiß der Düsenexzenter | Die Düse austauschen und den Rundlauf kalibrieren |
Überpolieren von Kanten | Der Einfallswinkel ist zu groß (>45°) | Stellen Sie den Winkel auf 30° ein und reduzieren Sie den PSI-Wert. |
Kratzer auf der Oberfläche | Falsche Auswahl der Mediengranularität | Ersetzen Sie den keramischen Sand durch die entsprechende Korngröße |
Übermäßige Staubrückstände | Das Entstaubungssystem ist ineffizient | Überprüfen Sie die Entstaubungsanlage und reinigen Sie den Filtereinsatz |
Teilweise Überhitzung der Form | Die Injektionszeit ist zu lang | Verkürzung der einmaligen Einspritzzeit und Verlängerung des Abkühlintervalls |
FAQ: Schnelle Antworten auf häufig gestellte Fragen
Q: Wie oft müssen die Keramikkugeln nach dem Recycling ausgetauscht werden?
A: Empfohlen wird das 20-fache oder eine Zerkleinerungsrate von >5% (je nachdem, was zuerst eintritt).
Q: Wie gehen Sie mit dem elektrostatischen Adsorptionsstaub aus der Form nach der Bearbeitung der Keramikperlen um?
A: Verwenden Sie eine Ionenluftpistole zum Abblasen und Wischen mit wasserfreiem Ethanol.
Q: Wie lässt sich die Verformung von dünnwandigen Formen (<1mm) vermeiden?
A: Verwenden Sie feinen Sand über #220, PSI≤50, und reduzieren Sie den Einfallswinkel auf 20°.
Durch dieses 7-stufige professionelle Verfahren können Sie nicht nur das Oberflächenproblem der nicht der Norm entsprechenden Formoberflächen lösen, sondern auch erreichen:
- Kostenreduzierung: Der Verlust des Mediums wird um 30% reduziert, und das Wartungsintervall der Anlage wird um das 2-fache verlängert.
- Qualitätsverbesserung: Die Oberflächenkonsistenz (CV-Wert) wird von 5% auf ≤2% komprimiert.
- Konformitätsgarantie: 100% erfüllt ISO 9001/14001 und branchenspezifische Normen.
Geh und übe es jetzt.
Wenn Sie Fragen haben, wenden Sie sich bitte an Kontaktieren Sie uns für eine kostenlose Beratung~
Filter