Wie man wählt Sandstrahlmaterialien nach der Form des Teils? Umfassender Leitfaden
Oktober 8, 2024
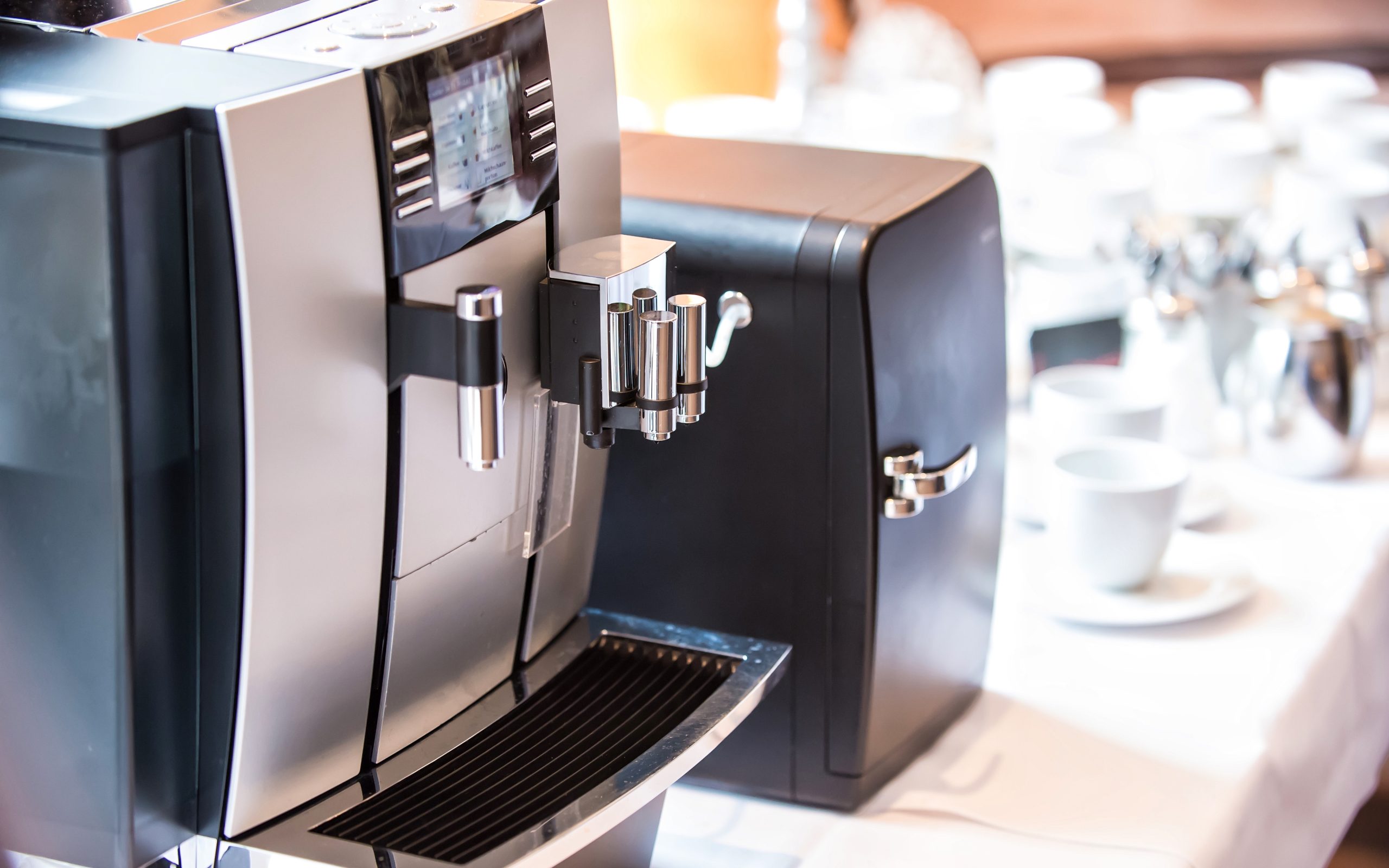
Das Sandstrahlen spielt in der modernen Fertigung eine wichtige Rolle, insbesondere bei der Oberflächenbehandlung von Teilen. Durch das Aufsprühen verschiedener Arten von Sandstrahlmaterialien können wir Oberflächenverunreinigungen wirksam entfernen, unebene Oberflächen polieren und die Qualität des Aussehens von Produkten verbessern. Die Form der verschiedenen Teile bestimmt die Wahl der Sandstrahlmaterialien, und die Wahl der richtigen Sandstrahlmaterialien entsprechend der Form der Teile wirkt sich direkt auf die Wirkung und Effizienz des Sandstrahlens aus.
In diesem Artikel werden wir zunächst einige gängige Teileformen auflisten, die Eigenschaften jeder Form analysieren und die Herausforderungen, denen sie beim Sandstrahlen begegnen können. Dann schlagen wir die Auswahl geeigneter Sandstrahlmaterialien auf der Grundlage dieser Formen vor, insbesondere für einige komplexere oder hochpräzise Teile, wie man flexibel zwei oder mehr Sandstrahlmaterialien verwenden kann, um den idealen Behandlungseffekt zu erzielen.
Gängige Teileformen und Anforderungen
- Flache und großflächige Teile
Diese Art von Teilen ist in vielen Bereichen sehr verbreitet, z. B. im Automobilbau, in der Bauindustrie und bei der Herstellung von Haushaltsgeräten. Konkrete Beispiele sind Autokarosserieteile, Metallgehäuse von Haushaltsgeräten, Glasfassaden für Gebäude usw. Bei diesen Teilen ist es besonders wichtig, die Oberfläche glatt und eben zu halten, da sie in der Regel als äußeres Aushängeschild des Produkts verwendet werden, was sich direkt auf die Ästhetik des Produkts und die Anerkennung auf dem Markt auswirkt.
Bei solchen Teilen erfordert das Sandstrahlverfahren in der Regel eine schnelle Bearbeitung großer Flächen. In diesem Fall sind Aluminiumoxid-Strahlmittel die ideale Wahl, denn Aluminiumoxidpartikel sind hart und haben starke Schneidkräfte, mit denen große Bereiche von Oxiden und Verunreinigungen schnell entfernt werden können, während eine gleichmäßige Oberfläche erhalten bleibt. Darüber hinaus kann die Oberflächenrauheit durch unterschiedliche Korngrößen des Aluminiumoxids an die jeweiligen Prozessanforderungen angepasst werden.
Einige flache Teile erfordern neben der Entfernung von Verunreinigungen während der Bearbeitung auch eine hohe Oberflächenglätte, insbesondere Glas- oder Edelstahloberflächen. In diesem Fall können keramische Strahlmittel mit abgerundeten Partikeln verwendet werden, die die Oberfläche polieren und gleichzeitig den Schmutz entfernen können.
- Runde und zylindrische Teile
Zylindrische Teile werden häufig im Maschinenbau, in der Petrochemie, im Rohrleitungsbau und in anderen Bereichen verwendet. Zum Beispiel sind Teile wie Antriebswellen, Hydraulikzylinder und Rohrverbindungen in der High-End-Industrie wie der Automobil-, Luft- und Raumfahrtindustrie weit verbreitet. Die Schwierigkeit beim Sandstrahlen solcher Teile besteht darin, dass die Gleichmäßigkeit der gesamten Oberflächenbehandlung gewährleistet sein muss, insbesondere im Übergangsbereich des kreisförmigen Querschnitts.
Für die Oberflächenbehandlung von runden Teilen sind keramische Strahlmittel am besten geeignet. Dieses Medium hat eine gute Zähigkeit und Verschleißfestigkeit, und kann auch eine gleichmäßige Schleifwirkung bieten. Durch die harten Partikel wird die Oberfläche des Teils nicht beschädigt. Es eignet sich für die Bearbeitung runder Teile, insbesondere einiger zylindrischer Präzisionsteile, wie z. B. Turbinenwellen von Flugzeugtriebwerken, bei denen der Verschleiß während der Bearbeitung normalerweise minimiert werden muss.
In manchen Fällen muss die Oberfläche zylindrischer Teile ein sehr hohes Finish erreichen. Zu diesem Zeitpunkt können ultrafeine Aluminiumoxid-Strahlmittel in Kombination eingesetzt werden, insbesondere bei der Bearbeitung von Bereichen, die eine präzise Kontrolle erfordern.
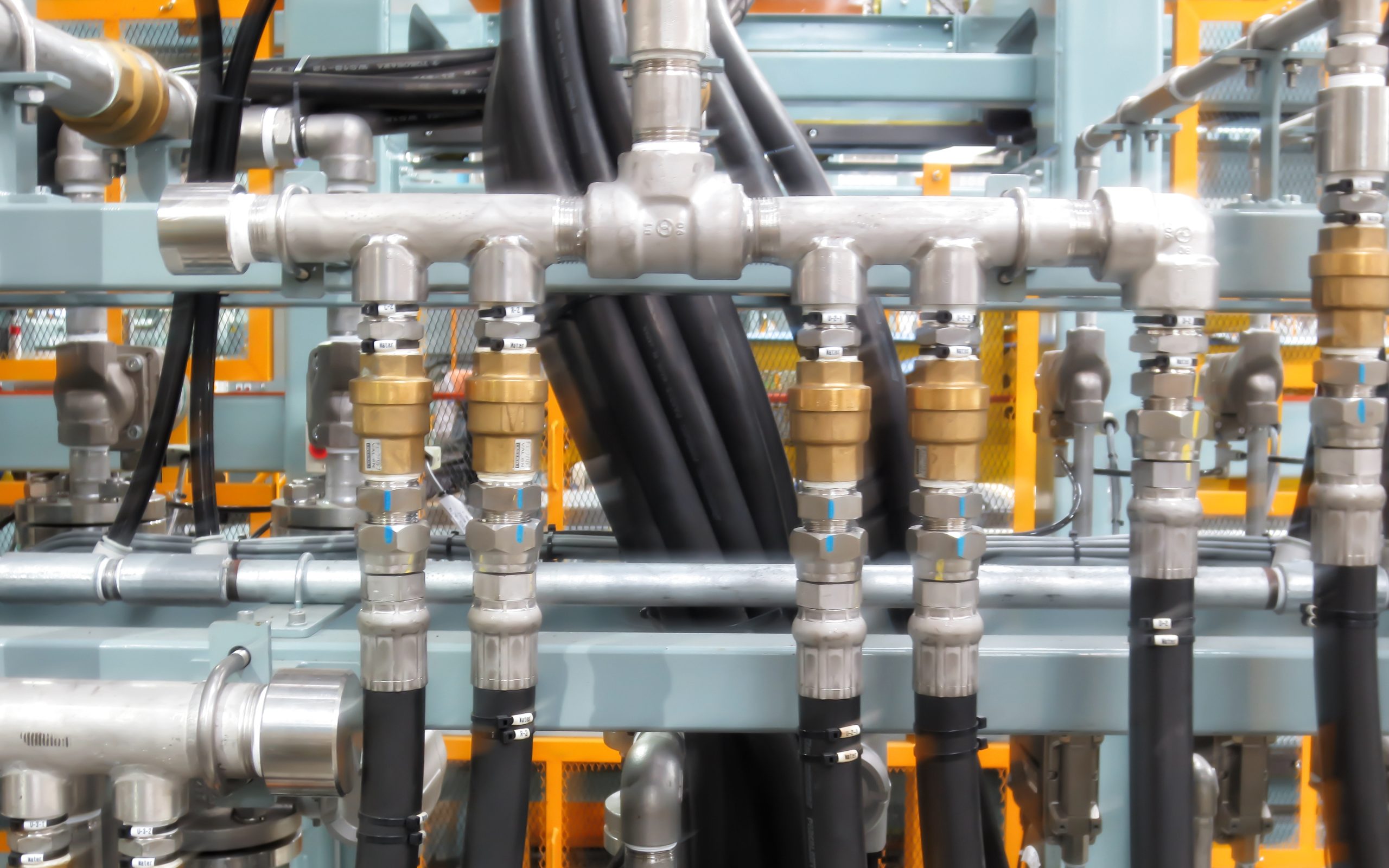
- Komplexe geometrische Formen und polyedrische Teile
Komplexe geometrische Teile sind in der Fertigungsindustrie weit verbreitet, insbesondere Motorgehäuse, Turbinenschaufeln, Gehäuse von elektronischen Geräten usw. Nehmen wir das Motorgehäuse als Beispiel. Es hat in der Regel eine polyedrische Struktur mit zahlreichen Aussparungen und Ecken. Bei solchen Teilen kann es beim Sandstrahlen leicht zu toten Ecken kommen. Bei unsachgemäßer Behandlung werden einige Bereiche nicht richtig bearbeitet, was sich auf die gesamte Oberflächenqualität der Teile auswirkt.
Zur Lösung dieses Problems werden Zirkoniumoxid-Strahlmittel empfohlen. Die hohe Dichte und Härte von Zirkonoxid sorgen dafür, dass es beim Entfernen von Rückständen eine starke Wirkung hat und einige Ecken und kleine Lücken reinigen kann. Aufgrund seiner hohen Härte ist es besonders für die Oberflächenbehandlung von Teilen aus hochfesten Legierungen geeignet.
In einigen Fällen, in denen eine sanftere Behandlung erforderlich ist, z. B. bei der Behandlung feiner Kanten, können Polystyrol-Entgratungsperlen in Kombination verwendet werden. Dieses Material ist relativ sanft und kann feine Grate an Teilen effektiv entfernen, ohne die Oberfläche der Teile zu beschädigen.
- Kleine, präzise Teile
Kleine Präzisionsteile sind in den Bereichen elektronische Produkte, medizinische Geräte und Instrumentenbau sehr verbreitet. Zum Beispiel Lötstellen für elektronische Bauteile, Mikrozahnräder in medizinischen Geräten usw. Diese Teile sind in der Regel klein und erfordern eine sehr hohe Präzision, so dass die Härte und der Aufprall des Strahlmittels während des Sandstrahlprozesses streng kontrolliert werden müssen, um eine Beschädigung der Form und Größe der Teile zu verhindern.
Entgratungsmedien aus Nylon und Polyamid sind ideale Materialien für die Bearbeitung solcher Teile. Nylon ist relativ weich und verursacht keine Schäden an Präzisionsteilen. Außerdem hat es gute antistatische Eigenschaften und eignet sich für die Bearbeitung elektronischer Bauteile, die leicht durch statische Elektrizität beeinträchtigt werden. Um sicherzustellen, dass Präzisionsteile während der Bearbeitung nicht überhitzt oder verformt werden, sind kryogene Entgratungsmedien eine gute Wahl. Durch die Behandlung bei niedrigen Temperaturen kann die Verformung von Teilen durch hohe Temperaturen oder Veränderungen der Materialeigenschaften vermieden werden, wodurch die Unversehrtheit von Präzisionsteilen gewährleistet wird.
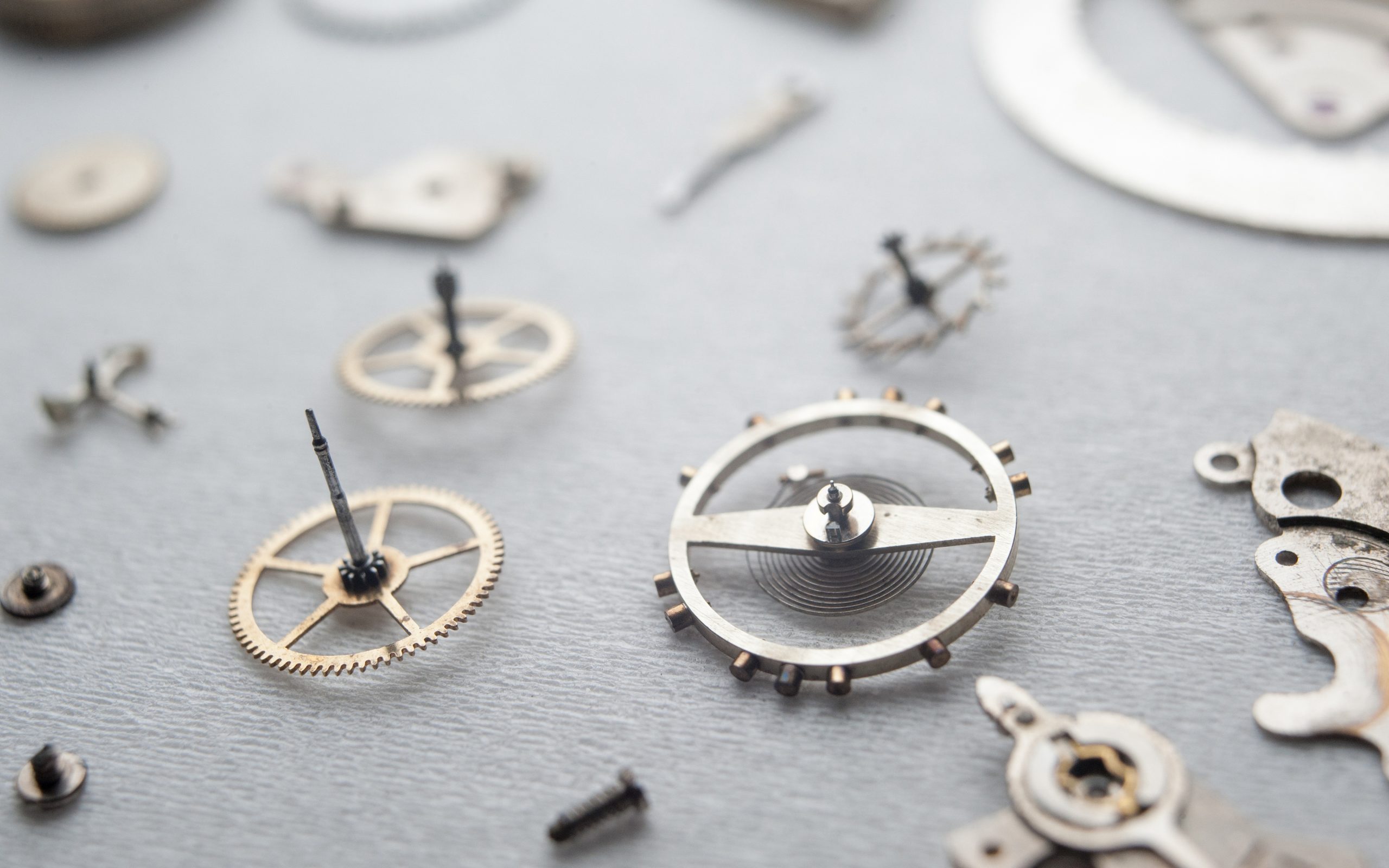
Besondere Fälle: Kombination von zwei oder mehr Sandstrahlmaterialien
In der Praxis sind manche Teile nicht nur komplex geformt, sondern können auch aus mehreren verschiedenen Materialien bestehen, oder die Anforderungen an die Oberflächenbehandlung sind sehr streng. In diesem Fall ist es oft notwendig, zwei oder mehr Strahlmittel zu kombinieren. Hier sind einige typische Beispiele für den kombinierten Einsatz:
Gemischte Behandlung von mehrflächigen Teilen
Nehmen wir als Beispiel den Guss eines Automotors. Das Äußere des Motors ist in der Regel eine vielflächige Struktur, und die Oberfläche muss gleichmäßig gereinigt werden. Aufgrund der großen Formunterschiede zwischen den verschiedenen Teilen des Motors kann ein einziges Strahlmittel jedoch nicht alle Bereiche effektiv behandeln. In diesem Fall können Zirkoniumdioxid-Strahlmittel verwendet werden, um Grate und Rückstände auf dem größten Teil der Oberfläche zu entfernen, und anschließend kann ultrafeines Aluminiumoxid-Strahlmittel für die sekundäre Behandlung einiger empfindlicherer Bereiche verwendet werden, um eine gleichmäßige Oberflächenbeschaffenheit des gesamten Teils zu gewährleisten.
Verarbeitung von Verbundwerkstoffteilen
Ein typisches Beispiel für Verbundwerkstoffteile sind Luftfahrtkomponenten, die in der Regel aus einer Mischung von Metallen und Nichtmetallen bestehen. Verschiedene Werkstoffe reagieren während des Strahlens unterschiedlich auf das Medium, und es ist eine Kombination mehrerer Sandstrahlmaterialien erforderlich. So können beispielsweise Metallteile mit Keramikperlen poliert werden, während Nichtmetallteile mit Polystyrol-Entgratungsperlen behandelt werden können. So wird sichergestellt, dass jedes Material die richtige Oberflächenbehandlung erhält.
Teile mit hochpräzisen Anforderungen
Hochpräzise Teile, wie z. B. Komponenten medizinischer Geräte, erfordern nicht nur eine makellose Oberfläche, sondern müssen auch sicherstellen, dass ihre Präzision während der Bearbeitung nicht beeinträchtigt wird. In diesem Fall werden in der Regel Niedertemperatur-Entgratungsmittel zur Vorbehandlung verwendet, um Oberflächenverunreinigungen zu entfernen. Anschließend werden Nylon-Polyamid-Medien für eine feinere Oberflächenbehandlung eingesetzt, um die Genauigkeit und Oberflächengüte der Teile zu gewährleisten.
Analyse der Eigenschaften verschiedener Sandstrahlmaterialien
Bei der Auswahl von Sandstrahlmaterialien ist es wichtig, ihre physikalischen und chemischen Eigenschaften zu kennen. Die Wahl des Sandstrahlmaterials wirkt sich nicht nur auf die Wirkung der Oberflächenbehandlung von Teilen aus, sondern auch auf die Effizienz, die Kosten und die Schwierigkeit der nachfolgenden Behandlung. Im Folgenden werden wir die oben genannten Sandstrahlmaterialien eingehend untersuchen und ihre einzigartigen Vorteile und Anwendungsszenarien erläutern.
- Ultrafeines Aluminiumoxid-Strahlmittel
Aluminiumoxid ist eines der am häufigsten verwendeten Sandstrahlmaterialien. Aufgrund seiner hohen Härte, starken Druckfestigkeit und guten chemischen Stabilität wird es häufig für die Oberflächenbehandlung verschiedener metallischer und nichtmetallischer Teile verwendet. Die Mohshärte von Aluminiumoxid liegt nahe bei 9 und ist damit nach Diamant und Siliziumkarbid die zweithärteste.
- Anwendbare Szenarien: Geeignet für die Grobbearbeitung von Oberflächen aus hartem Material (wie Stahl und Gusseisen), insbesondere wenn die Oberflächenrauheit verbessert werden muss. Häufige Anwendungen sind das Oberflächenschleifen mechanischer Teile und die Vorbehandlung vor der Beschichtung.
- Vorteile: Aluminiumoxid-Sandstrahlpartikel sind einheitlich und können einen relativ gleichmäßigen Oberflächenbehandlungseffekt aufrechterhalten. Es hat eine hohe Haltbarkeit und Wiederverwendbarkeit, besonders geeignet für Verarbeitungsumgebungen, in denen Sandstrahlmaterialien wiederverwendet werden müssen. Die hohe Härte von Aluminiumoxid ermöglicht es, hartnäckigen Schmutz schnell zu entfernen und die Bearbeitungszeit zu verkürzen.
- Anmerkung: Aufgrund seiner hohen Härte ist Aluminiumoxid nicht für die Bearbeitung von Präzisionsteilen oder empfindlichen Materialien geeignet. Außerdem ist Aluminiumoxid stark abrasiv und kann auf manchen Materialien winzige Kratzer hinterlassen. Daher muss es bei der Auswahl entsprechend den spezifischen Bearbeitungsanforderungen bewertet werden.
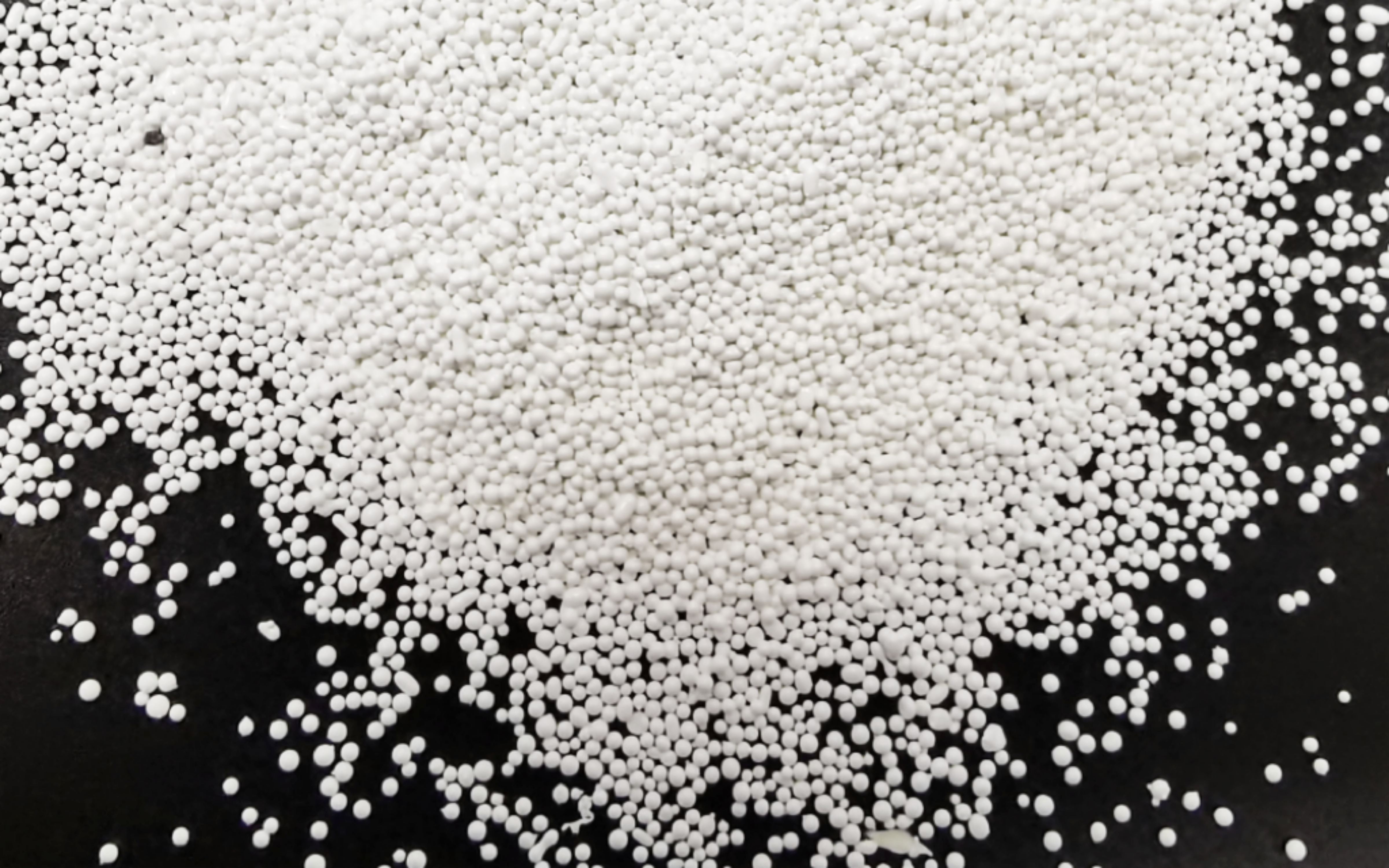
- Keramische Perlen Strahlmittel
Keramikperlen sind eine Art von Sandstrahlmittel, das aus einer Mischung von Zirkonium, Silizium, Aluminium und anderen Materialien besteht und eine runde oder ovale Form hat. Keramikkugeln haben eine gute Schlagfestigkeit und hohe Härte und werden hauptsächlich zum Polieren und Verfestigen von Metalloberflächen in der industriellen Produktion verwendet.
- Anwendbare Szenarien: Aufgrund der gleichmäßigen Partikelgröße und der glatten Oberfläche der Keramikkugeln eignet es sich besonders für Teile mit hohen Anforderungen an die Oberflächengüte, wie Edelstahl, Aluminiumlegierungen usw. Es wird häufig für die Oberflächenbehandlung von Präzisionsteilen in Branchen wie der Luftfahrt, der Automobilbranche und der Medizintechnik eingesetzt.
- Vorteile: Die Partikelform von Keramikkugeln ist relativ rund, so dass sie während des Sandstrahlens keine offensichtlichen Schneideffekte wie Aluminiumoxid verursachen und sich besser für Gelegenheiten mit hohen Anforderungen an die Oberflächengüte eignen. Die Verwendung von Keramikkugeln beim Sandstrahlen kann auch die Ermüdungsbeständigkeit von Metallteilen verbessern und ihre Lebensdauer verlängern. Es ist besonders geeignet für Teile, die eine Oberflächenverfestigung benötigen.
- Anmerkungen: Die Kosten für keramische Perlen sind relativ hoch, aber ihre Haltbarkeit und Wiederverwendbarkeit sind gut, und sie haben immer noch ein hohes Kosten-Nutzen-Verhältnis bei der langfristigen Verarbeitung. Außerdem sind sie aufgrund ihrer relativ glatten Oberfläche nicht für Fälle geeignet, in denen die Oberflächenrauheit erhöht werden muss.
- Keramik-Korn-Strahlperlen
Keramische Strahlperlen sind nichtmetallische Sandstrahlmaterialien, die durch Zerkleinern von geschmolzenen keramischen Materialien bei hohen Temperaturen hergestellt werden. Seine Härte und Zähigkeit liegen zwischen Aluminiumoxid und Keramikkugeln. Es wird häufig bei Werkstücken mit hohen Anforderungen an die Oberflächenreinheit und -rauheit eingesetzt.
- Anwendbare Szenarien: Keramische Strahlperlen werden vor allem für die Oberflächenbehandlung von Materialien wie Metallen, Kunststoffen und Glas verwendet, insbesondere für die Reinigung von Gussteilen, die Entfernung von Schweißnähten und das Aufrauen von Oberflächen. Sie können Defekte wie Oxide und Grate auf der Oberfläche von Teilen entfernen und gleichzeitig die Oberflächenrauhigkeit erhöhen, um die Haftung nachfolgender Beschichtungen zu verbessern.
- Vorteile: Keramikpartikel haben eine mittlere Dichte und Härte, so dass sie Verunreinigungen wirksam entfernen können, ohne die Oberfläche des Werkstücks zu beschädigen. Im Vergleich zu Aluminiumoxid ist der Oberflächenbehandlungseffekt von Keramikpartikeln weicher und verursacht keine übermäßige Oberflächenbeschädigung des Werkstücks. Es hat auch eine hohe chemische Korrosionsbeständigkeit und eignet sich für Sandstrahlarbeiten in Hochtemperatur- oder korrosiven Umgebungen.
- Anmerkung: Obwohl die Leistung von Keramikpartikeln relativ ausgeglichen ist, ist ihre Schleifkraft nicht so gut wie die von Aluminiumoxid, und sie eignet sich für die Oberflächenbehandlung von Materialien mittlerer Härte. Bei Werkstücken, die mit hoher Intensität geschliffen werden müssen, kann es notwendig sein, es mit härteren Materialien wie Aluminiumoxid zu kombinieren.
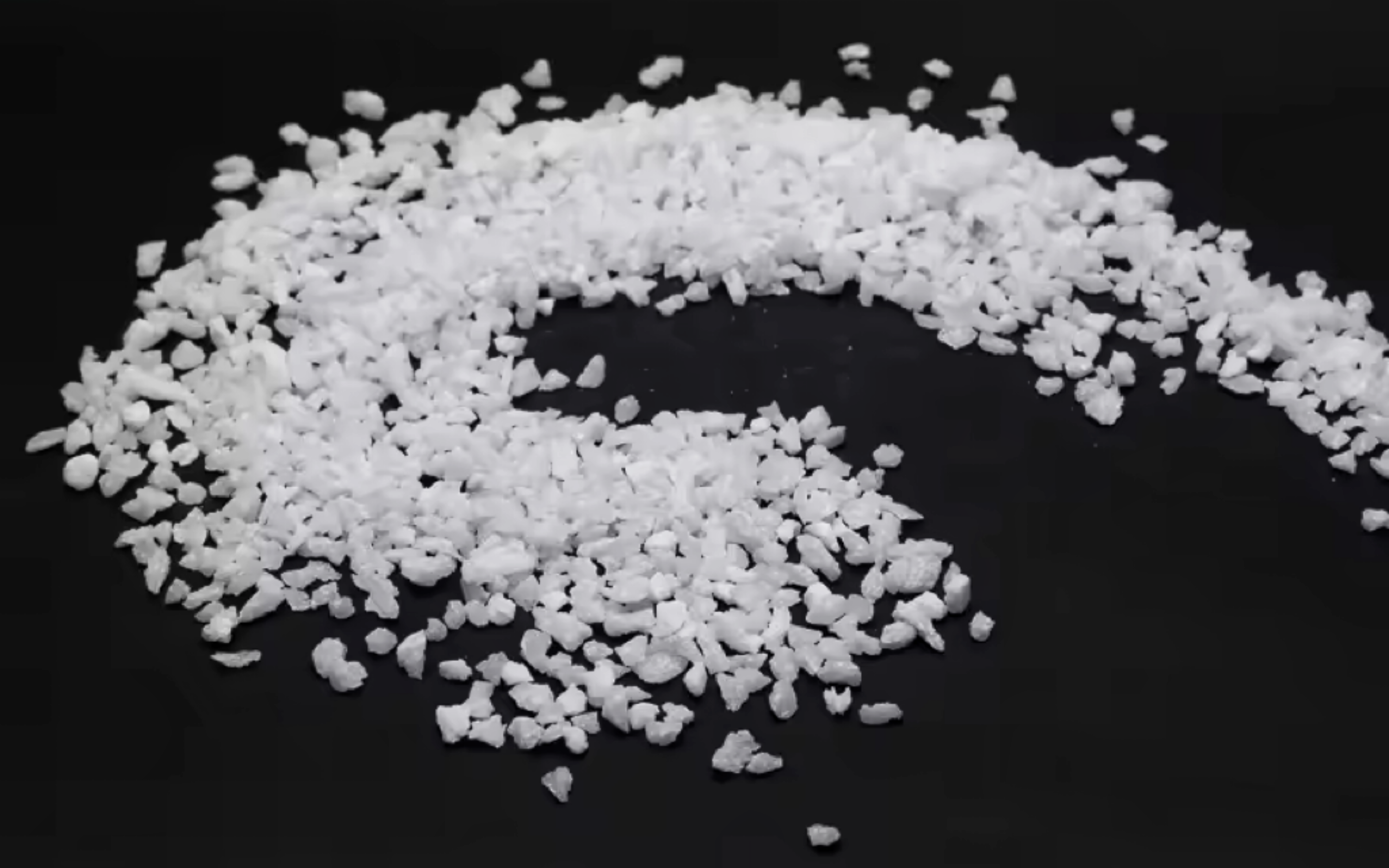
- Zirkoniumdioxid Strahlperlen
Zirkoniumdioxidperlen sind ein hochdichtes Sandstrahlmaterial, das durch Sintern von Zirkoniumoxidpulver hergestellt wird. Ihre Härte und Festigkeit sind besser als die herkömmlicher Keramikkugeln, und sie eignen sich besonders für die Bearbeitung einiger Teile mit hohen Anforderungen an Festigkeit und Verschleißfestigkeit.
- Anwendbare Szenarien: Zirkoniumdioxid-Perlen eignen sich besonders für die Oberflächenbehandlung von hochfesten Legierungen, Titanlegierungen, Edelstahl und anderen Materialien. In der Luft- und Raumfahrt, im Automobilbau und in der Elektronikindustrie werden Zirkoniumdioxidperlen häufig zur Oberflächenverfestigung, Entgratung und Endbearbeitung von Teilen eingesetzt.
- Vorteile: Die hohe Härte und die hohe Schlagkraft von Zirkoniumdioxid-Strahlkugeln ermöglichen es, hartnäckige Schmutz- oder Oxidschichten auf der Oberfläche von Teilen schnell zu entfernen und gleichzeitig die Ermüdungsfestigkeit der Oberfläche zu erhöhen, ohne die Teile zu beschädigen. Die hohe Schlagzähigkeit macht sie auch zur idealen Wahl für die Bearbeitung komplexer Strukturen und hochpräziser Teile.
- Anmerkungen: Aufgrund der hohen Kosten von Zirkoniumdioxidkugeln werden diese meist für die Bearbeitung hochwertiger, hochpräziser Teile verwendet. Bei einigen geringwertigen Werkstücken kann die Verwendung von Zirkoniumdioxidkugeln die Gesamtproduktionskosten erhöhen, so dass ein Gleichgewicht zwischen Kosten und Wirkung gefunden werden muss.
- Nylon Polyamid Entgratungsmittel
Nylon-Polyamid-Medien sind flexible Sandstrahlmaterialien mit geringer Dichte, die hauptsächlich zum Entgraten von Präzisionsteilen verwendet werden. Nylon-Polyamid hat eine gute Schlagfestigkeit und verursacht keine Sekundärschäden am Werkstück. Es eignet sich besonders für die Bearbeitung von spröden Materialien und Werkstücken mit hohen Anforderungen an die Oberflächenbehandlung.
- Anwendbare Szenarien: Wird häufig zum Entgraten und Reinigen von empfindlichen Teilen wie elektronischen Bauteilen, Präzisionsinstrumenten und medizinischen Geräten verwendet. Aufgrund seiner geringen Härte eignet es sich für die Bearbeitung leicht zu beschädigender Materialien wie Kunststoffe, Harze, Aluminiumlegierungen usw.
- Vorteile: Nylon-Polyamid-Sandstrahlmittel haben eine gute Elastizität und können die Präzisionsstruktur der Teile während der Bearbeitung wirksam schützen. Sein geringer Verschleiß sorgt dafür, dass die Oberfläche des Teils beim Entfernen von Graten nicht zerkratzt oder beschädigt wird, was sich besonders für die Oberflächenbehandlung von elektronischen Bauteilen mit hohen Anforderungen eignet.
- Anmerkung: Nylon Polyamid ist wenig verschleißfest und eignet sich für den einmaligen Gebrauch oder zum leichten Entgraten. Daher müssen die Medien bei der Massenproduktion möglicherweise häufig ausgetauscht werden, was die Gesamtmaterialkosten erhöht.
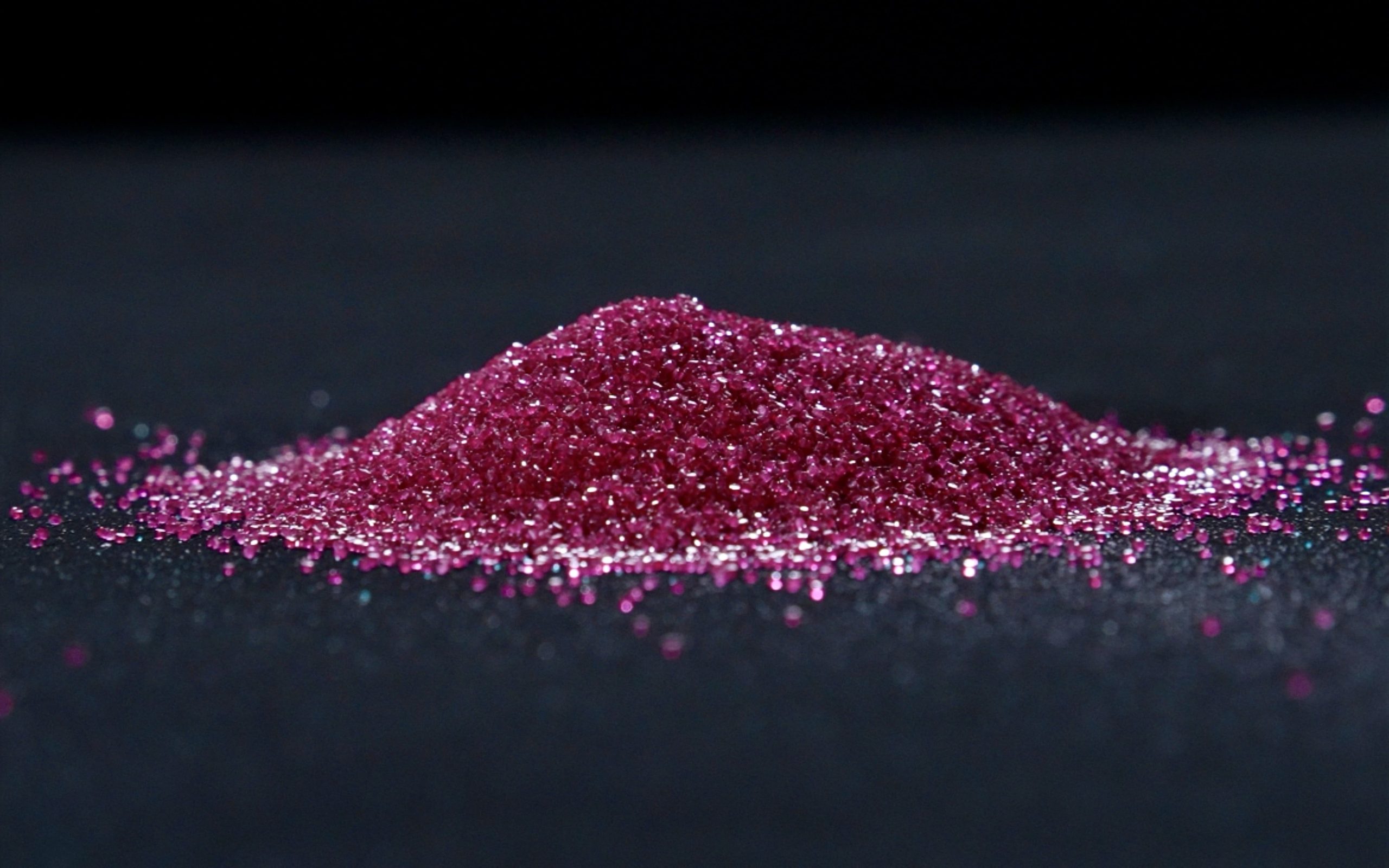
- Polystyrol-Entgratungsperlen
Polystyrol-Entgratungsperlen sind leichte, flexible Entgratungsmittel, die hauptsächlich zur Entfernung von Graten an Präzisionskunststoff- und Leichtmetallteilen verwendet werden. Aufgrund seiner Eigenschaften eignet sich Polystyrol sehr gut für Branchen, die strenge Anforderungen an die Oberfläche des Werkstücks stellen, wie z. B. die Medizin-, Elektronik- und Präzisionsinstrumentenherstellung.
- Anwendbare Szenarien: Polystyrol-Entgratungsperlen werden hauptsächlich zur Entfernung von Graten an Kunststoffteilen und kleinen Defekten auf der Oberfläche von Spritzguss- und Druckgussteilen verwendet. Sie eignen sich besonders gut für die Bearbeitung von leichten Materialien wie Kunststoff- und Aluminiumteilen und für Teile mit hohen Anforderungen an die Oberflächengüte wie medizinische Geräte, Haushaltsgeräte und elektronische Komponenten.
- Vorteile: Polystyrol-Entgratungsperlen eignen sich sehr gut für Entgratungsprozesse bei niedrigen Temperaturen und können Grate auf der Oberfläche von Teilen effektiv entfernen, ohne das Material in Niedrigtemperaturumgebungen zu beschädigen. Aufgrund seines relativ weichen Materials kann die Verwendung dieses Mediums Kratzer oder Oberflächenbeschädigungen des Werkstücks während des Entgratungsprozesses verhindern.
- Anmerkung: Aufgrund der geringen Dichte des Polystyrols ist es in einigen schweren Entgratungsumgebungen möglicherweise nicht so effektiv wie andere Materialien mit hoher Härte. Daher kann es notwendig sein, es in Kombination mit anderen Medien bei Reinigungs- oder Entgratungsarbeiten zu verwenden, die eine höhere Intensität erfordern.

- Kryogenes Entgratungsmedium
Kryogene Entgratungsmedien sind spezielle Medien, die für kryogene Entgratungsprozesse entwickelt wurden und Grate schnell entfernen können, nachdem die Teile auf eine spröde Temperatur eingefroren wurden. Die Medien sind in Niedrigtemperaturumgebungen stabil und werden häufig bei Entgratungsvorgängen von hochpräzisen und empfindlichen Materialien eingesetzt.
- Anwendbare Szenarien: Kryogene Entgratungsmittel eignen sich für Präzisionsteile mit extrem hohen Anforderungen an die Oberflächenqualität, wie z. B. Gummiteile, Kunststoffteile, medizinische Geräte, Luftfahrt- und Automobilteile. Da das Material während des Gefrierprozesses spröde wird, können Grate leicht entfernt werden, ohne das Werkstück selbst zu beschädigen. Es eignet sich auch besonders für die Bearbeitung von Teilen mit komplexer Geometrie und von Teilen, die mit herkömmlichen Methoden nur schwer zu entgraten sind.
- Vorteile: Der kryogene Entgratungsprozess ist sehr schonend und kann die Oberfläche der Werkstücke weitestgehend schützen und gleichzeitig eine hohe Entgratungsgenauigkeit gewährleisten. Die Medien sind zudem sehr anpassungsfähig und können eine Vielzahl von Materialien und Werkstücken mit komplexen Formen effektiv bearbeiten. Im Vergleich zu herkömmlichen Entgratungsmethoden weist die kryogene Entgratungstechnologie eine höhere Präzision und Effizienz auf und eignet sich besonders für Branchen mit strengen Produktionsanforderungen wie die Medizin-, Luftfahrt- und Automobilbranche.
- Anmerkung: Obwohl kryogene Entgratungsmedien bei der Präzisionsbearbeitung gute Leistungen erbringen, sind die Gesamtkosten aufgrund der hohen Anforderungen an die Ausrüstung relativ hoch. Daher eignen sich diese Medien eher für den Einsatz in der Massenproduktion oder bei besonderen Anlässen mit extrem hohen Qualitätsanforderungen.
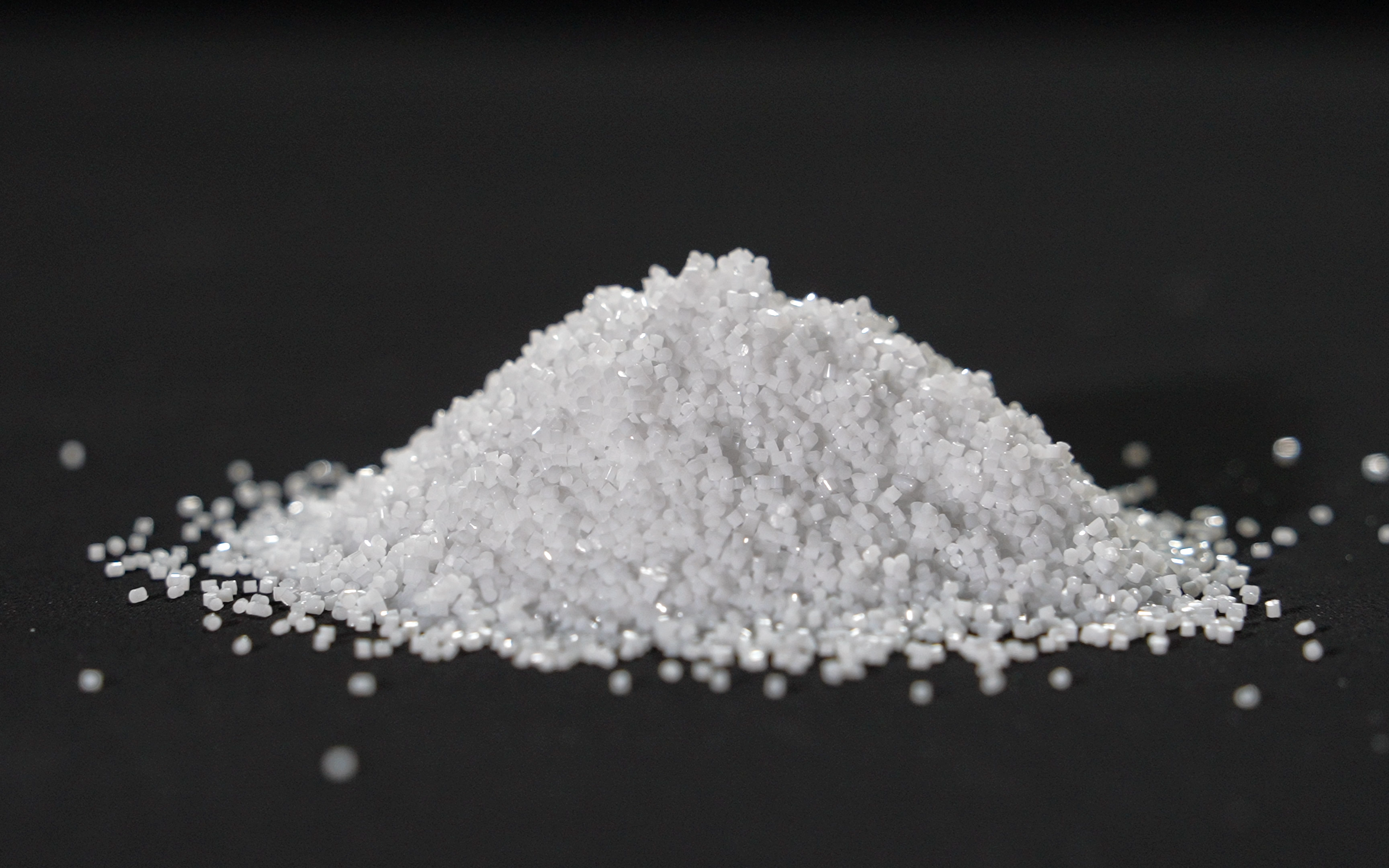
Die Auswahl von Sandstrahlmaterialien in Abhängigkeit von der Form der Teile ist eine komplexe und erfahrungsintensive Aufgabe. Die richtige Wahl des Sandstrahlmaterials kann nicht nur die Wirkung der Oberflächenbehandlung von Teilen sicherstellen, sondern auch die Produktionseffizienz verbessern und unnötigen Materialabfall reduzieren. Bei der Bearbeitung einiger komplexer oder hochpräziser Teile können durch die Kombination mehrerer Sandstrahlmaterialien oft idealere Ergebnisse erzielt werden.
Kurz gesagt, der Kern der Sandstrahltechnik liegt in der Flexibilität und Präzision. Bei der Auswahl von Sandstrahlmaterialien sollten die Hersteller die Form, das Material und die Bearbeitungsanforderungen der Teile umfassend berücksichtigen, um sicherzustellen, dass jedes Glied die beste Bearbeitungswirkung erzielen kann.
Filter