セラミック・ビーズs ユーザーマニュアル金型の仕上がりを向上させる7つのステップ
2月 12, 2025
一貫した仕上がりを維持することは、金型の製造やメンテナンスにおける重要な目標のひとつです。しかし、標準的な工程を厳格に守っていても、多くのお客様が次のような問題に遭遇します:
"なぜ金型の仕上げがまだ標準に達していないのか?"
「サンドブラスト中に鋳型の表面に傷をつけないようにするには?
「セラミックビーズの使用効率を最適化するには?
これらの問題の本質的なニーズは以下の通りである:
- 再現性 - 異なるロットの金型の仕上がりは一定でなければならない。
- コスト管理能力 - メディアの損失と人件費を削減し、コストパフォーマンスを向上させる。
- 操業上の安全性 - ダストコントロールと機器保護により、安全な生産を確保する。
以上のようなニーズに応えるため、金型の仕上がりを効率的かつ安全に向上させるための7段階のプロフェッショナル・プロセスをまとめました。
ステップ1:隠れた危険の原因を排除する前処理検査
顧客のペインポイント
- 微細な欠陥(0.1mmの傷など)を無視すると、その後の研磨不良につながります。
- 装置の状態不良(ノズルの摩耗など)は、媒体を浪費し、サンドブラスト効果を低下させます。
ソリューション
1.1 カビの欠陥検出
20倍の拡大鏡を使い、パーティングラインとベント溝を中心に金型表面をチェックする。表面状態を正確に測定するには、携帯用表面粗さ計(ミツトヨSJ-210など)を推奨する。
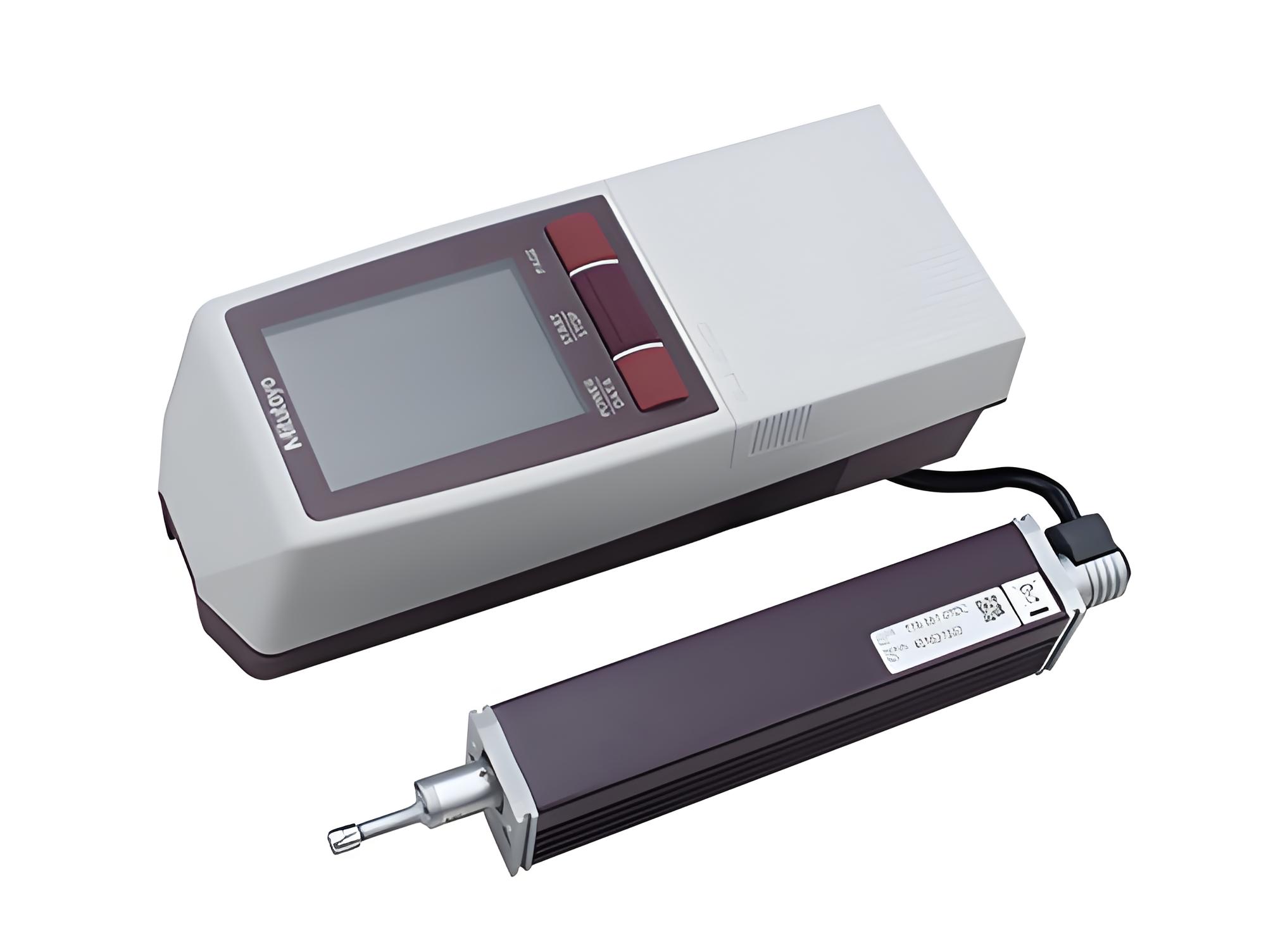
1.2 機器の事前点検リスト
- ノズルの摩耗:内径変化は≤5%であるべきであり、それを超える場合は交換する必要があります。
- 空気圧の安定性:不安定な注入を避ける変動範囲≤±2 PSI。
ステップ2:圧力設定式、科学が経験に取って代わる
顧客のペインポイント
- 経験に頼った圧力設定は、軟質材料の過研磨や硬質材料の洗浄不足を招く。
素材タイプ | 材料係数 |
---|---|
プラスチック(ABS) | 0.8 |
アルミニウム合金 | 1.2 |
ステンレス | 1.5 |
チタン合金 | 2.0 |
カーバイド | 2.5 |
ソリューション
2.1 PSI計算式
生販在 = 中程度の硬さ × 被削材係数 × 10
計算例:
チタン合金の金型で、モース硬度7のセラミックビーズを使用:
生販在 = 7 × 2.0 × 10 = 140
2.2 圧力調整のヒント
最初の操作の後にRa値を測定する: Ra値が高すぎる場合はPSIを5~10増加させ、Ra値が低すぎる場合はPSIを5~10減少させる。
ソフトな素材による保護: プラスチック金型の場合、過研磨を避けるため、PSIの上限は80である。
硬い素材を効率的に洗浄: チタン合金の金型の場合、洗浄効果を確保するためにPSIの下限は140である。
ステップ3:角度と距離のコントロール、幾何力学の勝利
顧客のペインポイント
- 垂直射出は局所的な過粉砕を招き、30°の入射角は正確に制御するのが難しい。
ソリューション
3.1 30°入射角最適化ソリューション
- 入射角30°の場合、接線方向の力が70%、法線方向の力が30%となり、洗浄効率と表面保護のバランスが取れている。
- 噴射距離=ノズル径×10(例:ノズル径8mm→噴射距離80mm)
3.2 実践的なツール
レーザー角度指示器(誤差±1°)により、正確な角度制御が可能。
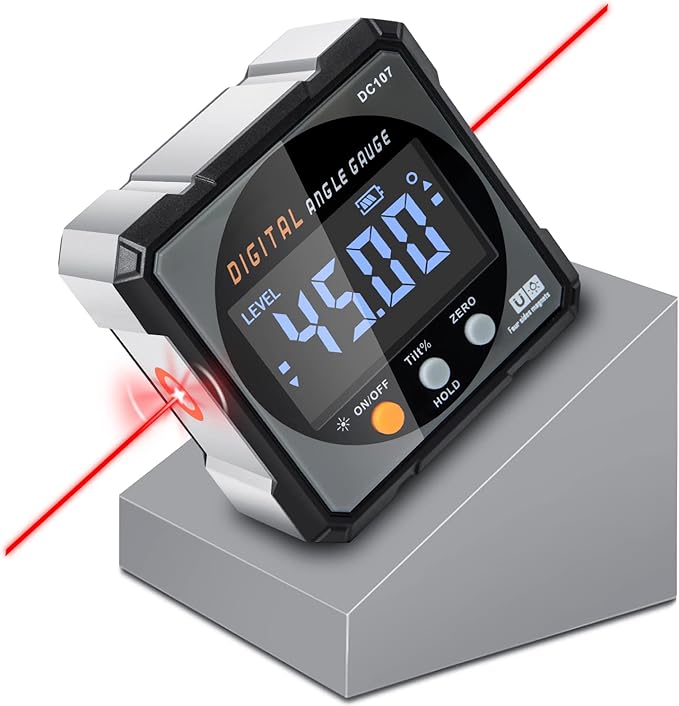
ステップ4:メディア状態の監視、寿命延長の鍵
顧客のペインポイント
- セラミックビーズの交換時期を判断できず、コストの無駄や品質の低下を招く。
ソリューション
4.1 破砕率の検出
メディア100gを取り出し、粉砕された粒子を手作業で選別する。粉砕率が5%以上の場合は交換が必要。
4.2 オンライン・インテリジェント・モニタリング
オンライン粒度センサーを設置し、メディアの粒度変化をリアルタイムで監視する。
HLHセラミックビーズモデル | 標準粒子径(µm) | 許容偏差 (µm) |
---|---|---|
B20 | 600-850 | ±50 |
B30 | 425-600 | ±35 |
B40 | 250-425 | ±20 |
B60 | 125-250 | ±15 |
B80 | 180-250 | ±15 |
B100 | 125-180 | ±10 |
B120 | 63-125 | ±8 |
B125 | 0-125 | ±8 |
B170 | 45-90 | ±5 |
B205 | 0-63 | ±5 |
B400 | 30-63 | ±3 |
B505 | 10-30 | ±2 |
ステップ5:加工後の品質検査基準、データに基づく検収
顧客のペインポイント
- 目視検査だけでは、規格外仕上げの問題の発覚が遅れる。
ソリューション
5.1 推奨されるRa値測定ツール
基本モデル: タイム3220ハンドヘルド粗さ計
利点:ポータブルで使いやすく、現場での迅速な検出に適しており、精度は±5%。
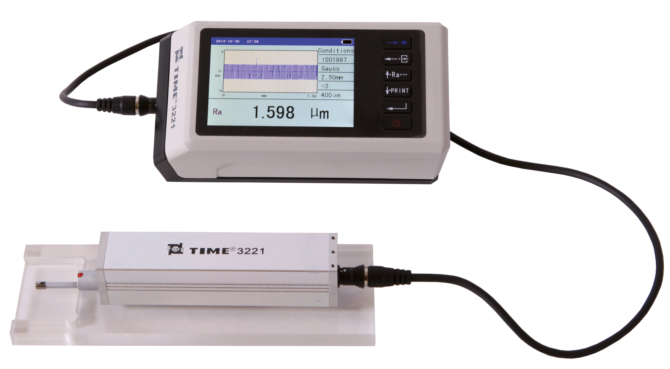
高精度モデル: Zygo NewView 9000 3D光学式プロファイラー。
利点:高精度測定、複雑な表面に最適、ナノメートルレベルの分解能。
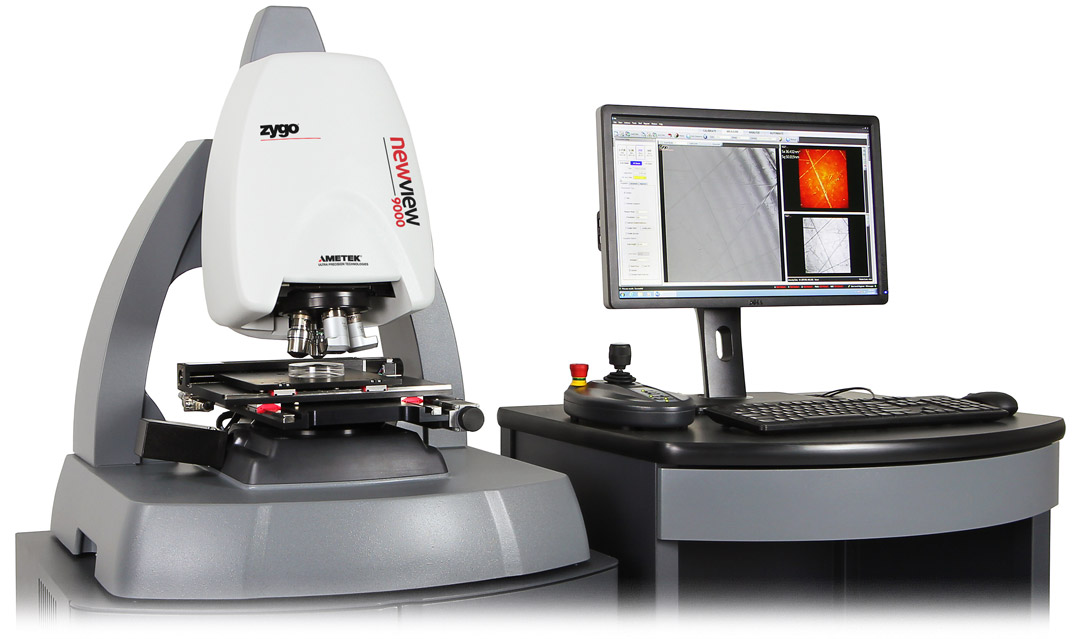
5.2 業界のRa値基準
特定産業 | 一般的な材料 | Raの要件(μm) | テストポイント数 |
---|---|---|---|
電子部品 | 銅合金製コネクター | ≤0.4 | ≥10点/㎡以上 |
精密プラスチックハウジング | ≤0.6 | ≥8点/㎡以上 | |
自動車部品 | アルミ合金製エンジン部品 | ≤0.8 | ≥5点/㎡以上 |
ステンレス製ブレーキディスク | ≤1.0 | ≥6点/㎡以上 | |
医療機器/インプラント | チタン合金整形外科インプラント | ≤0.4 | ≥12点/㎡以上 |
ステンレス製手術器具 | ≤0.6 | ≥10点/㎡以上 | |
航空宇宙 | チタン合金タービンブレード | ≤0.3 | ≥15点/㎡以上 |
高温合金エンジン部品 | ≤0.5 | ≥10点/㎡以上 |
ステップ6:廃棄物処理仕様、コンプライアンス、コスト削減の並行作業
顧客のペインポイント
- 廃棄物処理コストは高く、環境リスクもある。
ソリューション
6.1 セラミックビーズのリサイクル工程
磁気分離(金属不純物の除去)→空気分離(粉塵の除去)→選別(等級分けと再利用)
回収率:≧85%(破砕率は<5%に制御されなければならない)。
6.2 廃棄物のコンプライアンス処理
- セラミックダスト(無害な埋立地)
- 金属くず(業務用リサイクル)
ステップ7:よくある問題のトラブルシューティング、クイック・レスポンス・ガイド
顧客のペインポイント
- 突発的な問題(表面の凹凸など)が生産ラインの停滞を引き起こす
ソリューション
問題現象 | 考えられる理由 | ソリューション |
---|---|---|
部分マット | メディアの偏在 | サンドセパレーターを点検し、詰まり箇所を清掃する。 |
周期的ストライプ | ノズル偏心摩耗 | ノズルを交換し、同心度を校正する。 |
エッジの磨きすぎ | 入射角が大きすぎる(45°以上) | 角度を30°に調整し、PSIを下げる。 |
表面の傷 | メディア粒度の不適切な選択 | セラミック砂を適切な粒度のものに交換する。 |
過度の残留粉塵 | 除塵システムの効率が悪い | 除塵装置の点検とフィルターエレメントの清掃 |
金型の部分的過熱 | 射出時間が長すぎる | 1回の注入時間を短くし、冷却間隔を長くする。 |
よくある質問頻度の高い質問に対する迅速な回答
Q: リサイクル後、セラミック・ビーズは何回交換が必要ですか?
A: 20倍、または破砕率5%以上(どちらか早い方)を推奨する。
Q: セラミックビーズ加工後の金型の静電吸着粉塵はどのように処理するのですか?
A: イオンエアーガンでブロー+無水エタノールで拭き取り。
Q: 薄肉金型(1mm未満)の変形を避けるには?
A: #220、PSI≤50以上の細砂を使用し、入射角を20°にする。
この7段階のプロフェッショナルなプロセスを通じて、金型仕上げの表面問題が標準を満たさないことを解決するだけでなく、達成することができます:
- コスト削減:媒体の損失が30%減少し、装置のメンテナンス間隔が2倍に延びる。
- 品質向上:仕上がりの一貫性(CV値)を5%から≦2%に圧縮。
- コンプライアンス保証:100%は、ISO 9001/14001および業界固有の規格に適合しています。
今すぐ練習してこい
ご質問がある場合は 無料カウンセリング~
フィルター