10月 27, 2024
現代の工業生産において、表面処理は重要な基本工程であり、製品の品質と性能に直結している。表面処理の標準化は、コーティングや接着材料の接着性を向上させるだけでなく、ワークピースの耐用年数を効果的に延ばす。環境意識の高まり、技術の絶え間ない進歩、国際標準化の進展に伴い、表面処理基準はより厳しく、細心の注意を払い、持続可能な方向に向かっている。本稿では、現在の表面処理規格の発展傾向、将来の変化、そしてこれらの変化が各業界に与える影響について深く探っていく。
表面処理とは?
表面処理の定義
表面処理とは、ワークピースや材料の表面に、洗浄、粗面化、脱酸、その他の物理的・化学的処理を施し、その後の加工やコーティング工程(塗装、電気めっき、接着など)の土台を作ることを指す。このプロセスは、金属、プラスチック、複合材料などのさまざまな材料に広く使用されており、ワークピース表面の清浄度と粗さを向上させることで、後続プロセスの接着性と耐久性を高めることを目的としている。
表面処理の中心的役割
工業生産と加工の中核をなすステップとして、表面処理は以下の3つの面で重要である:
- コーティングと接着の接着性を向上させる: 表面処理は、表面の粗さと清浄度を向上させることができ、それによってコーティングや接着剤などの接着性を大幅に向上させることができる。
- 材料表面の耐食性を高める: 前処理で表面の酸化物や不純物を除去することで、特定の環境下での材料の腐食を遅らせたり、防いだりすることができる。
- 表面の平坦性と美観の向上: サンドブラストや研磨などによって、素材の表面はより滑らかになり、さらなる装飾処理に便利である。
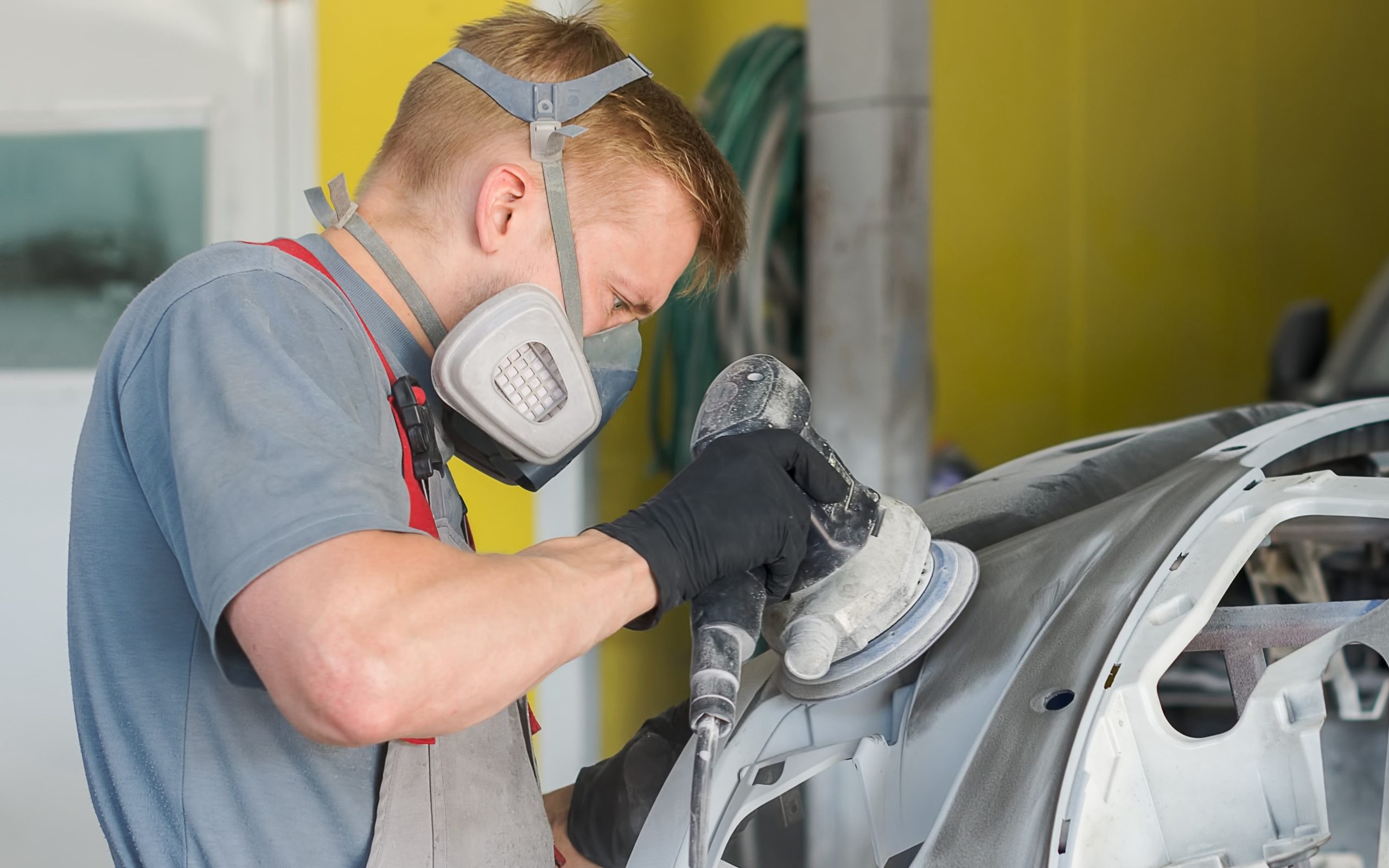
表面処理の基準
表面処理に規格が必要な理由
表面処理標準の確立は、プロセスフローと品質管理要件を標準化することにより、各ワークピースが処理後に一貫した品質レベルを達成できるようにすることを目的としている。標準化のメリットは主に以下の3点に反映される:
- 生産効率の向上: 標準化された作業手順により、試行錯誤の時間や材料の無駄が減り、生産工程全体の効率が向上する。
- 製品品質の一貫性を確保する: 異なるバッチ、異なるオペレーターによるワークピースが同じ基準に従えば、製品品質の一貫性が確保され、作業や材料の違いによる品質変動を避けることができる。
- ワークピースの寿命を延ばす: 厳格な表面処理基準は、コーティングや接着層の安定性と耐久性を向上させ、過酷な環境におけるワークピースの寿命を延ばすのに役立ちます。
さまざまな用途分野での表面処理に必要な条件
表面処理はさまざまな産業で広く使用されているが、応用分野によって要求されるものも異なる。例えば
- 自動車、航空分野: 高温、腐食環境などで安定した性能を発揮するためには、高強度な接着力と耐久性が求められます。
- 造船業、石油・ガス産業 機器や構造物は水分や塩分などの腐食環境に長期間さらされるため、表面処理に求められる防錆性能は特に厳しい。
- 医療機器とエレクトロニクス このような用途では、表面の清浄度に対する要求が極めて高い。表面処理は強力な接着性を確保するだけでなく、化学残留物のような材料の生体適合性や電子性能に影響を与える要因を回避しなければならない。
標準化された表面処理によって、各業界はより信頼性の高い特定のワークピース表面を得ることができ、それによって製品の最終性能を確保することができる。
国際共通基準
世界的には、多くの国や地域が独自の表面処理基準を策定している。ここでは一般的な規格をいくつか紹介する:
- ISO規格: 国際標準化機構(ISO)は表面処理に関するいくつかの規格を発行しており、さまざまな材料やプロセスの仕様を網羅している。例えば、ISO 8501は金属表面のさまざまな錆除去レベルを定義し、ISO 11124は研磨材の品質と性能を規定している。
- ASTM規格: 米国材料試験協会(ASTM)は、表面処理、特に金属や複合材料の前処理に関連する多くの規格を策定している。例えば、ASTM D4417はコーティングされた基材の表面粗さの測定方法を規定しており、ASTM B322は金属表面クリーニングの一般的な仕様です。
- SAE規格: 自動車技術会(SAE)は、自動車ボディの表面粗さを測定するためのSAE J400など、自動車や航空分野の金属表面処理に関する特別な規格を提供している。このような規格は、自動車や航空部品の品質の一貫性を確保する上で極めて重要である。
- 欧州規格EN、日本規格JIS 欧州と日本にはそれぞれEN規格とJIS規格があり、例えばEN 13788は金属表面の清浄度を規定し、JIS G3141は鋼材の表面処理要件を規定している。これらの規格は、それぞれの地域における製品の品質と市場の一貫性を確保する上で重要な役割を果たしている。
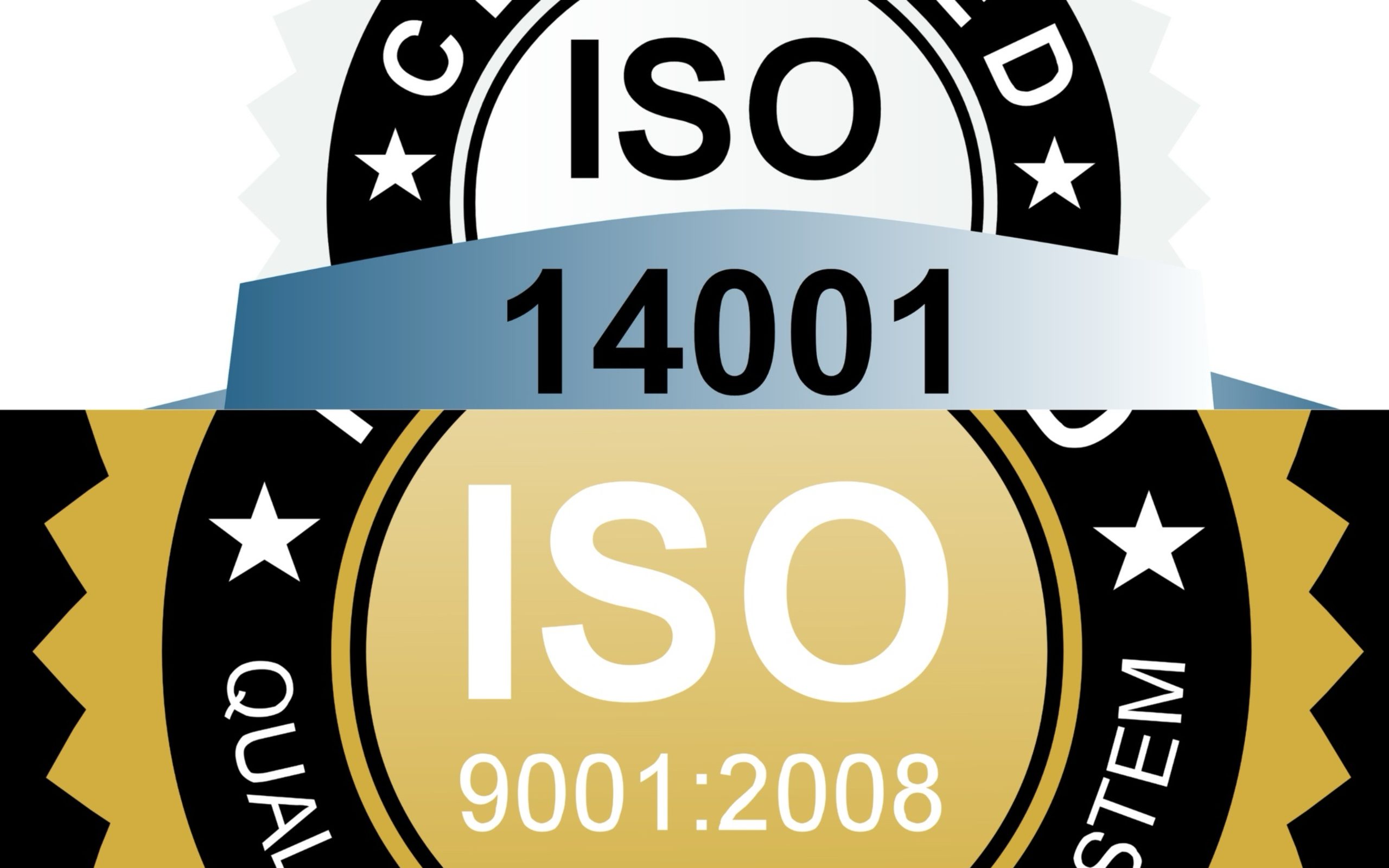
地域差とスタンダードの理由
国や地域によって基準には一定の違いがあり、その違いは通常、以下の3つの側面から生じる:
- 環境規制: 欧州と日本は環境保護に対する要求が高いため、その基準は有害物質の使用を減らす方向に傾いているかもしれないが、一方でこの点に関する要求がより緩やかな国もあるだろう。
- 業界の成熟度 一部の国では、製造業が早くから始まっているため、規格がより成熟し詳細である一方、新興市場では規格の適用範囲が比較的限られている場合がある。
- 輸出製品の適応ニーズ: 多くのメーカーは、製品を輸出する際、対象市場の基準に特別な注意を払い、製品がスムーズに検査を通過し、市場アクセス資格を取得できるようにしている。
標準化の影響
国際表面処理規格は、世界の製造業者に共通言語を提供します。これらの規格に従うことで、様々な国で生産された部品や機器は統一された品質要件を満たすことができ、国境を越えた貿易や協力の障壁を簡素化することができる。例えば、製造業者はISO 8501の清浄度基準に従って製造や試験を行うことができ、製品をより世界共通のものにすることができる。
さまざまなワークピースと材料の表面処理基準
材料、アプリケーション環境、機能要件の違いにより、異なる材料やワークピースには異なる表面処理基準があります。これらの違いにより、表面処理に必要な技術的手段や標準化要件も異なります。以下は、いくつかの一般的な被削材の表面処理基準とその適用範囲です。
金属材料
金属材料は機械、建築、自動車、航空などの分野で広く使用されており、その前処理基準は特に厳しい。金属材料によって前処理技術は異なる。以下に代表的な3つの金属材料の前処理条件を示す。
- スチール: 鋼は工業用途で最も広く使用されている金属材料のひとつであり、一般的な表面処理規格はSa 2.5(ISO 8501)である。この規格では、その後のコーティングの密着性と耐久性を確保するために、表面が一定レベルの錆落としと粗さに達することが要求される。
- アルミニウム合金: アルミニウム合金は、航空、自動車、建築など軽量化の要求が高い分野で広く使用されている。アルミニウムの表面処理規格は通常、塗装の密着性を高めるために表面の酸化皮膜を除去し、粗面化することを含む。一般的な処理方法には、サンドブラスト、酸洗、リン酸塩処理などがあります。
- 銅とその合金: 銅合金は主に電子、電気、配管産業で使用されています。その優れた電気伝導性と熱伝導性のため、表面処理基準は清浄度と非破壊的な表面伝導性を重視しています。
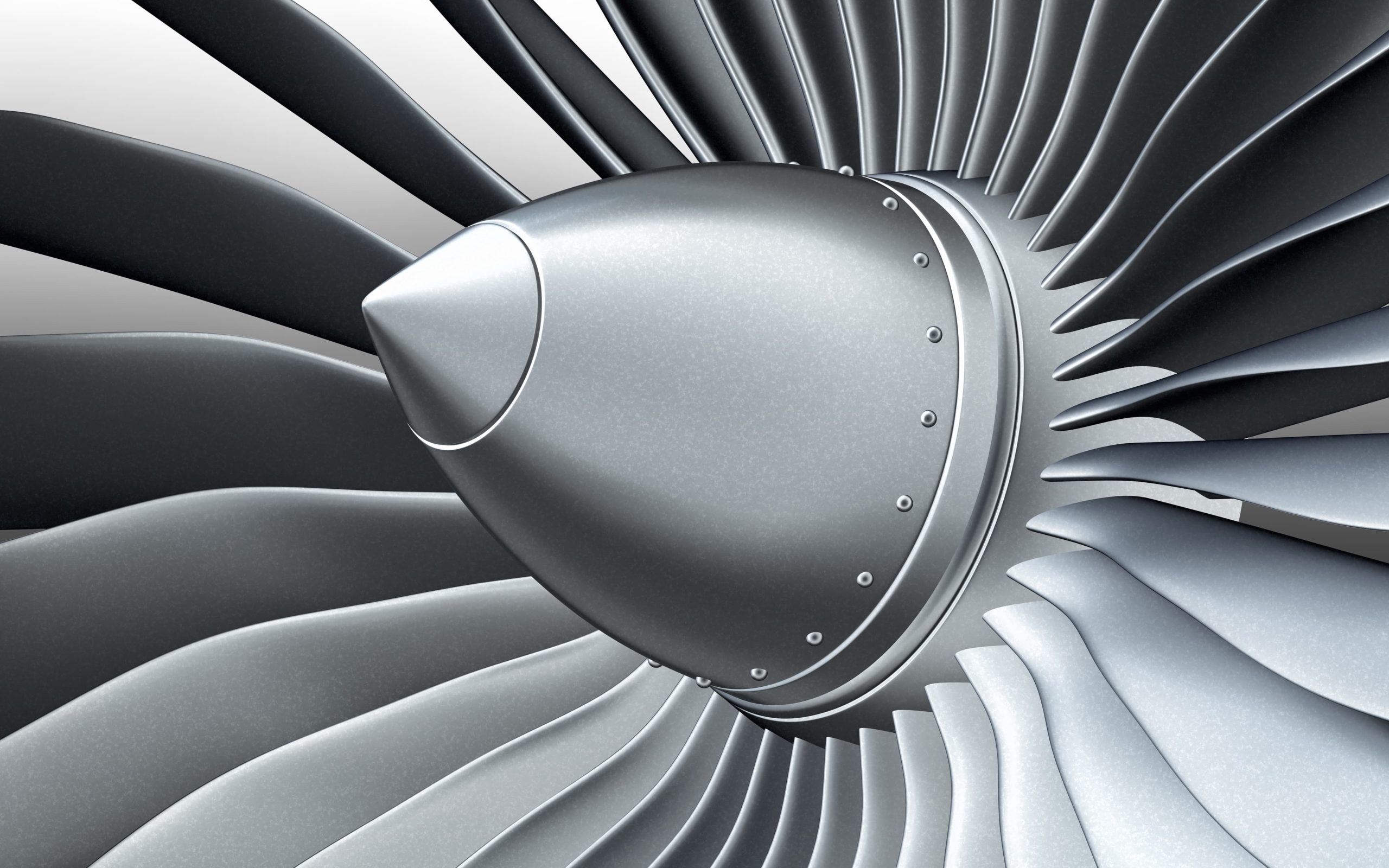
非金属材料
プラスチック、セラミックス、ガラスなどの非金属材料は、自動車、エレクトロニクス、建築などの産業で広く使用されている。材料の特性が異なるため、表面処理の焦点は清浄度と粗さの制御にあります。
- エンジニアリングプラスチック (ABS、PCなど):自動車、電子機器、その他の産業では、ABSやPCなどのエンジニアリング・プラスチックが筐体や構造部品に使用されることが多い。コーティングの密着性を確保するため、通常、プラスチック表面を洗浄し、わずかに粗面化する必要がある。
- セラミックとガラス:セラミックスやガラスは、医療機器や電子製品の筐体などの分野で広く使用されており、その準備基準は通常、表面の清浄度と耐摩耗性に重点が置かれている。
複合材料
複合材料(炭素繊維強化複合材料、CFRPなど)は、自動車、航空、エネルギーなどのハイエンド産業において重要な用途がある。このような材料の前処理基準は、通常、接着剤やコーティング剤の接着性を確保するための表面粗さと清浄度に重点を置いています。
- 炭素繊維複合材料 (CFRP):CFRPは航空・自動車分野で広く使用されており、軽量かつ高強度であることが支持されている。しかし、CFRPの表面処理は、素材そのものの構造を損なわないよう、細心の注意が必要です。
- ガラス繊維複合材料 (GFRP):ガラス繊維は造船や建築などの産業で広く使用されており、その表面処理基準は粗さと清浄度に重点が置かれている。
精密電子部品および医療機器
精密電子部品や医療機器の分野では、機器の性能やバイオセーフティーを確保するために、表面処理の基準として清浄度や表面残留物のないことが極めて高い要件となっている。
- 電子部品:精密電子部品の表面処理に要求されるのは、主に無発塵、無残渣である。
- 医療機器:医療機器、特に手術器具の表面処理基準はより厳しく、材料の生体適合性を確保し、表面に有害物質が残らないようにしなければならない。
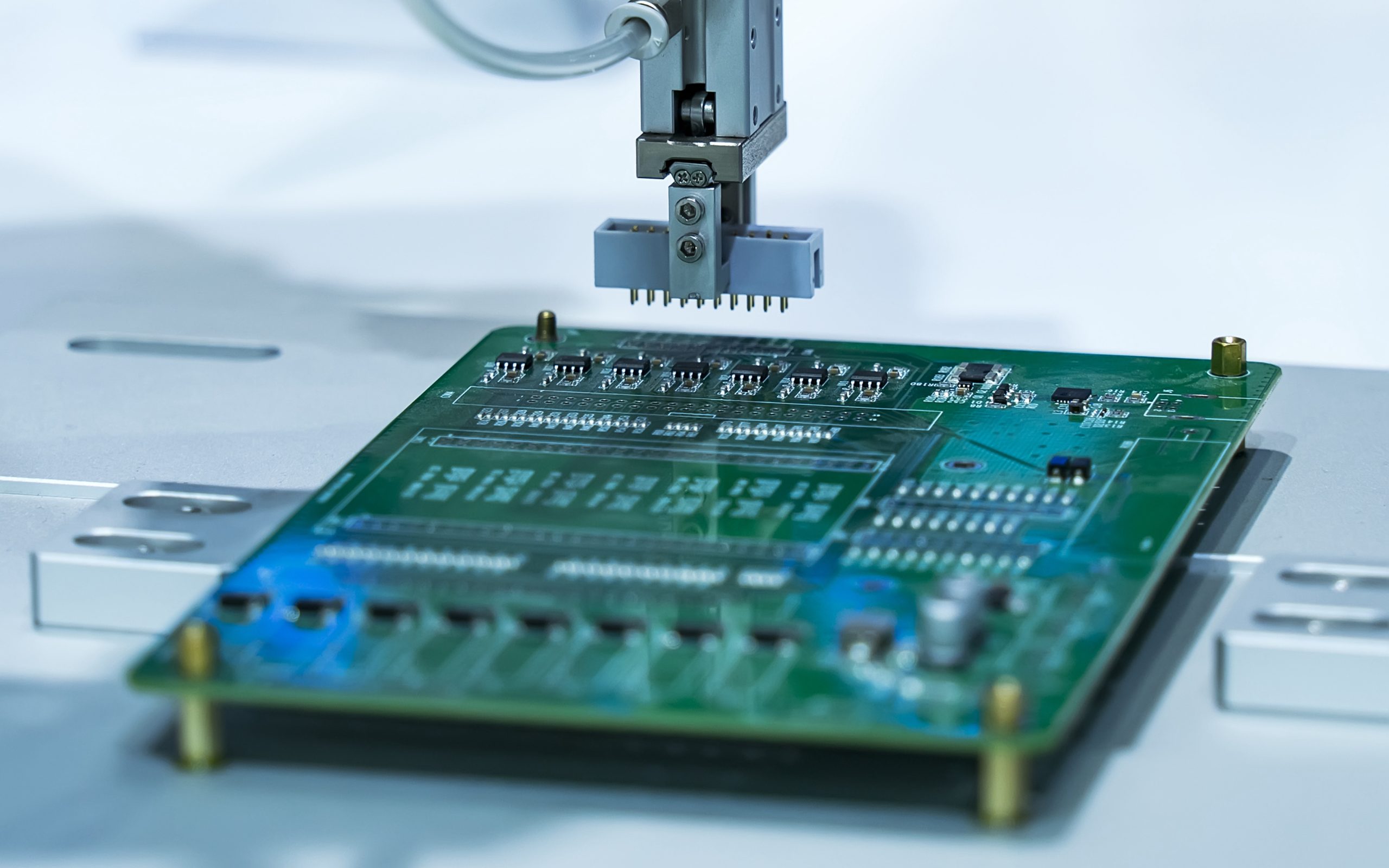
使用環境に応じて前処理基準を調整する。
異なる使用環境では、表面処理の基準が調整される。環境要因(温度、湿度、化学腐食性など)とワークピースの最終的な用途のニーズによって、前処理に求められる条件は異なる。環境の違いに応じて、前処理の深さ、材料の選択、品質管理方法も調整する必要がある。
- さまざまな労働条件に対する準備の必要性
- 高温環境: ワークピースが高温環境で使用される場合、表面処理基準には通常、ワークピースに耐高温性と耐酸化性が要求される。サンドブラストによる表面処理は、有効な表面改質方法の一つである。
- 化学腐食環境: 腐食性環境(海洋、石油、ガス産業など)は、金属表面の急速な酸化や損傷を引き起こす可能性がある。そのため、前処理基準では通常、表面に酸化物やその他の不純物がなく、コーティングがより強固に密着するよう、ある程度の粗さを持つことが要求される。
- 湿度変化の激しい環境: 湿度変化の大きい環境(屋外の建物や港湾設備など)では、ワークの塗膜に剥離やふくれなどのトラブルが発生しやすい。そのため、乾燥と湿潤が交互に繰り返される環境下での塗膜の安定性を確保するため、準備基準では清浄度や粗さを厳しく管理しています。
- 最終用途が規格に与える影響
ワークピースの最終用途は、表面処理の基準を大きく左右する。さまざまな業界では、美観と機能性の観点から、前処理に特別な要件を提示する必要があります。
- 美的要求の高い産業 (家電製品など):これらの分野では、表面の外観品質と耐久性が特に重要です。前処理基準では、表面仕上げや微細バリの除去に高い要求がある。
- 機能要件の高い分野 (軍需産業や航空宇宙など):軍需産業や航空宇宙産業のような需要の高い産業の表面処理基準はより厳しく、過酷な条件下でのコーティングの密着性と機能性を確保するため、耐摩耗性と耐腐食性が要求されます。
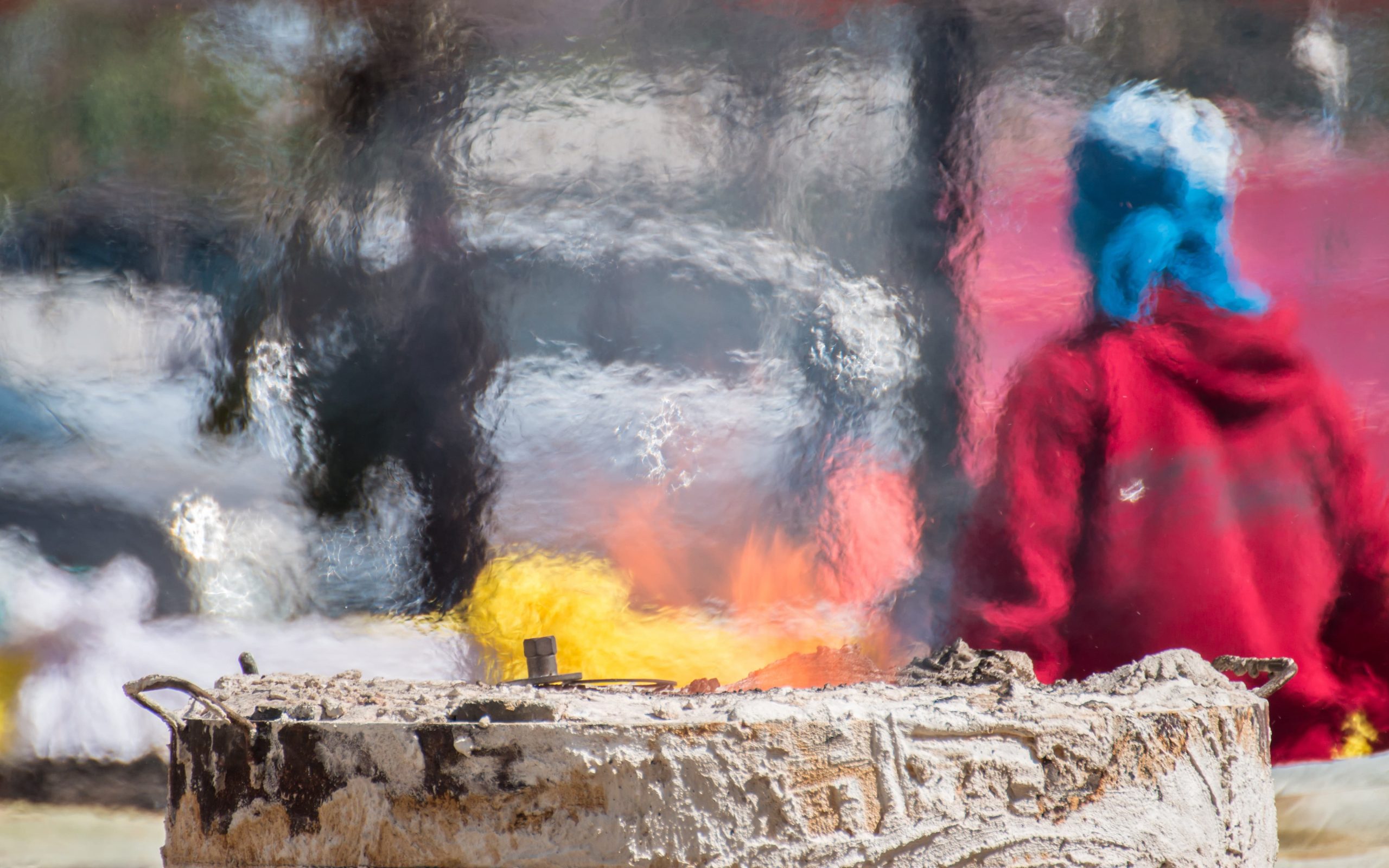
表面処理工程の品質管理と評価基準
工業生産プロセスにおいて、表面処理の品質管理は極めて重要です。厳密な測定と評価方法によって、前処理されたワークピースがさまざまな性能要件を満たしていることが保証され、その後のコーティングや保護処理に適した基盤が提供されます。
表面清浄度の測定方法
表面清浄度は、表面処理工程における重要な指標の一つであり、塗膜の密着性、耐食性、総合的な品質に関係する。一般的に用いられる表面清浄度の評価方法には、以下の3種類がある:
- 目視検査: 目視検査は最も基本的な清浄度評価方法であり、専門家の観察によって、表面に明らかな汚染物質、油汚れ、酸化スケールなどがあるかどうかを確認する。しかし、目視検査は主観的なものであり、通常は予備的な評価方法として用いられる。
- 拭き取りテスト: 拭き取り検査は、ワークの表面に微小な汚染物質が残留しているかどうかを検出することができる。白い布やワイピングツールで表面を拭き、汚染の有無を確認することで清浄度を評価する。この方法は、航空機や電子製品など、より高い要求があるワークに適しています。
- 顕微鏡検査: 顕微鏡検査は表面を拡大し、微小な不純物や汚染残留物を検出することができます。この方法は、高純度金属や精密部品など、高精度の前処理が必要なワークに適しています。HLHサンドブラスト材料は、顕微鏡検査が適格であることを保証するために、効率的で残留物のない洗浄処理を提供できます。
一般的な清浄度分類規格清浄度分類規格は、ISO 8501-1のSa規格や米国規格のSPレベルなど、清浄度要件を明確にするために使用されます。HLHサンドブラスト材料は、Sa 2.5またはSa 3などの清浄度レベルを満たすことができ、ワークピースを均一で残留物のない状態にすることができます。、
表面粗さの測定
粗さも表面処理後の重要な指標である。表面の粗さはコーティングの密着性や耐食性に直接影響するため、粗さの測定は非常に重要です。一般的に使用される粗さ測定ツールには、触針式粗さ計と光学式粗さ計があります。触針式粗さ計はプローブを表面に接触させて測定し、光学式粗さ計は光の反射と散乱を利用して表面粗さを評価します。
業界ごとに異なる粗さへの要求事項粗さの要件は業界によって異なる。例えば、自動車や航空機の分野では、塗膜の密着力を高めるために中程度の粗さが要求されることが多く、家電製品や電子機器の分野では、美しさや使用感を確保するために低い粗さが要求されることがあります。
塗膜密着性試験
コーティングの密着性は、表面処理効果の最終的な表れのひとつである。良好な表面処理は、塗膜と基材との結合を強化し、それによってワークピースの耐用年数を延ばすことができる。一般的な密着性試験方法には次のようなものがある:
- クロスカットテスト: クロスカット試験は、塗膜の密着性を試験する一般的な方法のひとつである。塗膜の表面に格子状の傷をつけ、外力による剥離を観察する。
- せん断強度試験: せん断強度試験は、垂直方向における塗膜の密着性を評価するもので、通常、厚い塗膜や機能性塗膜の試験に用いられる。
表面処理標準は、製品の品質向上、生産コストの削減、環境保護において重要な役割を果たします。標準化された前処理は長期的な経済価値をもたらすだけでなく、熾烈な市場競争において企業に優位性を与える。企業や実務者にとって、さまざまな市場やワークの特性に応じて適切な規格を柔軟に選択することが、持続可能な発展を実現する鍵である。常に業界の変化に適応し、環境保護と技術の進歩に注意を払うことによってのみ、将来の市場で無敵になることができるのである。
フィルター