金型仕上げ:表面仕上げの一般的な問題と解決策
1月 17, 2025
表面仕上げは、金型の仕上げにおいて最も重要な検討事項の1つです。部品の美しさや機能性に影響を与えるだけでなく、金型の耐用年数や製品の品質にも直結します。医療機器から自動車部品まで、業界によって金型に求められる表面は異なります。金型材料、公差、テクスチャー、離型性能、材料流動特性、加工方法などが最終的な仕上げ効果に影響します。この記事では、金型仕上げの表面仕上げ問題に焦点を当て、その原因を分析し、金型メーカーが複雑な加工課題に対処するための解決策を提供します。
金型表面仕上げに関する一般的な問題
不均一な表面粗さ
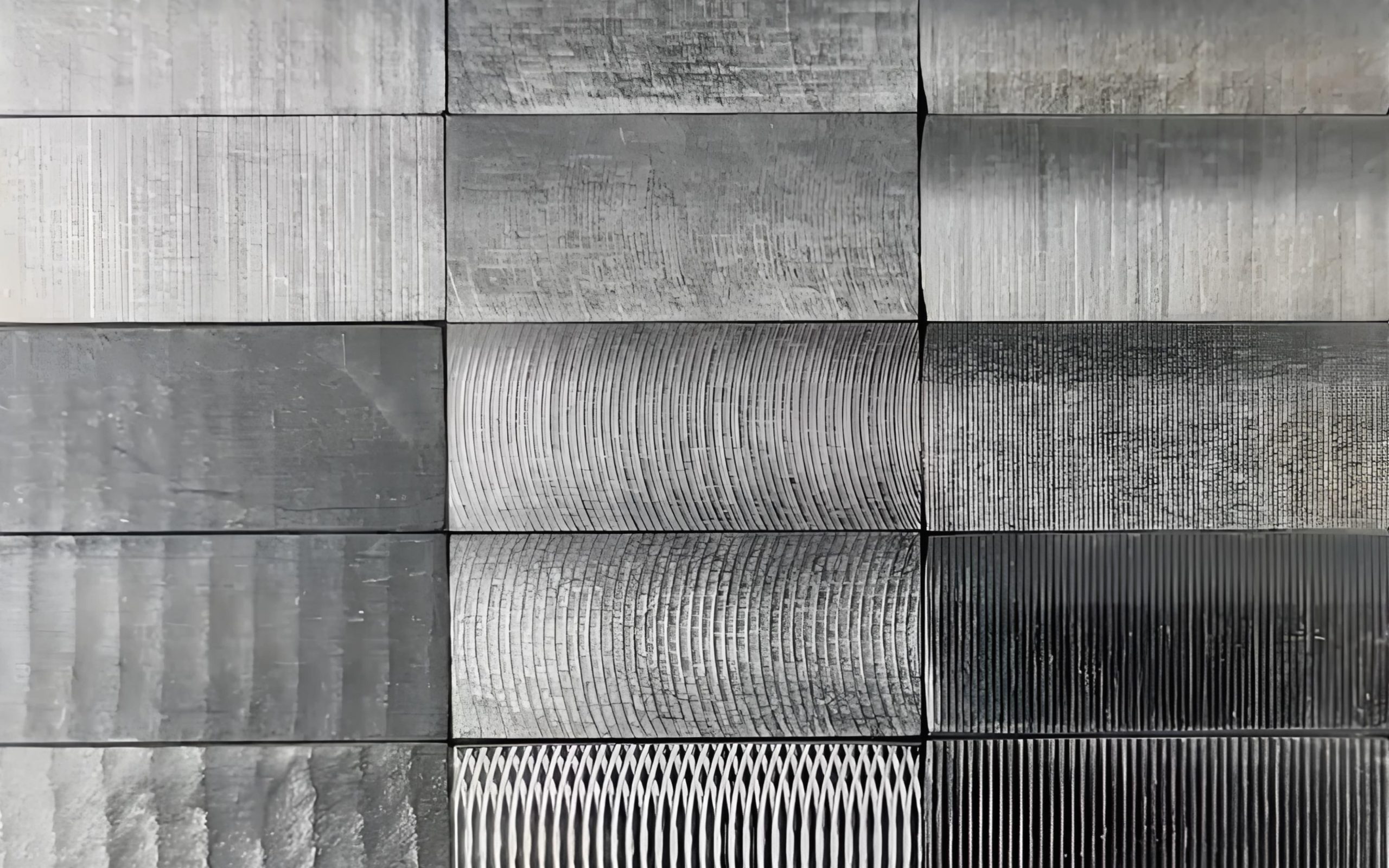
問題の顕在化
- 金型表面の異なる領域の粗さは著しく異なり、製品の一貫性に影響を与える。
- 光量が多い部分やエッジの位置は、過度のざらつきが出やすい。
- CNC加工後の表面にはナイフの跡がかなり残っており、仕上げや視覚効果に影響を及ぼしている。
- 部分的にテクスチャーの深さが異なり、その後の研磨効果に影響する。
原因分析
- 加工精度が不十分で、複雑な部分を最適化できない。
- 工具の摩耗は時間内に交換されず、表面品質に影響を与える。
- プロセスパラメータの設定が不適切で、送り速度と回転速度が一致せず、表面の質感が異なる。
- 不適切な表面処理工程、研磨およびサンドブラスト工程における不適切な媒体の選択。
表面の欠陥が脱型の困難につながる
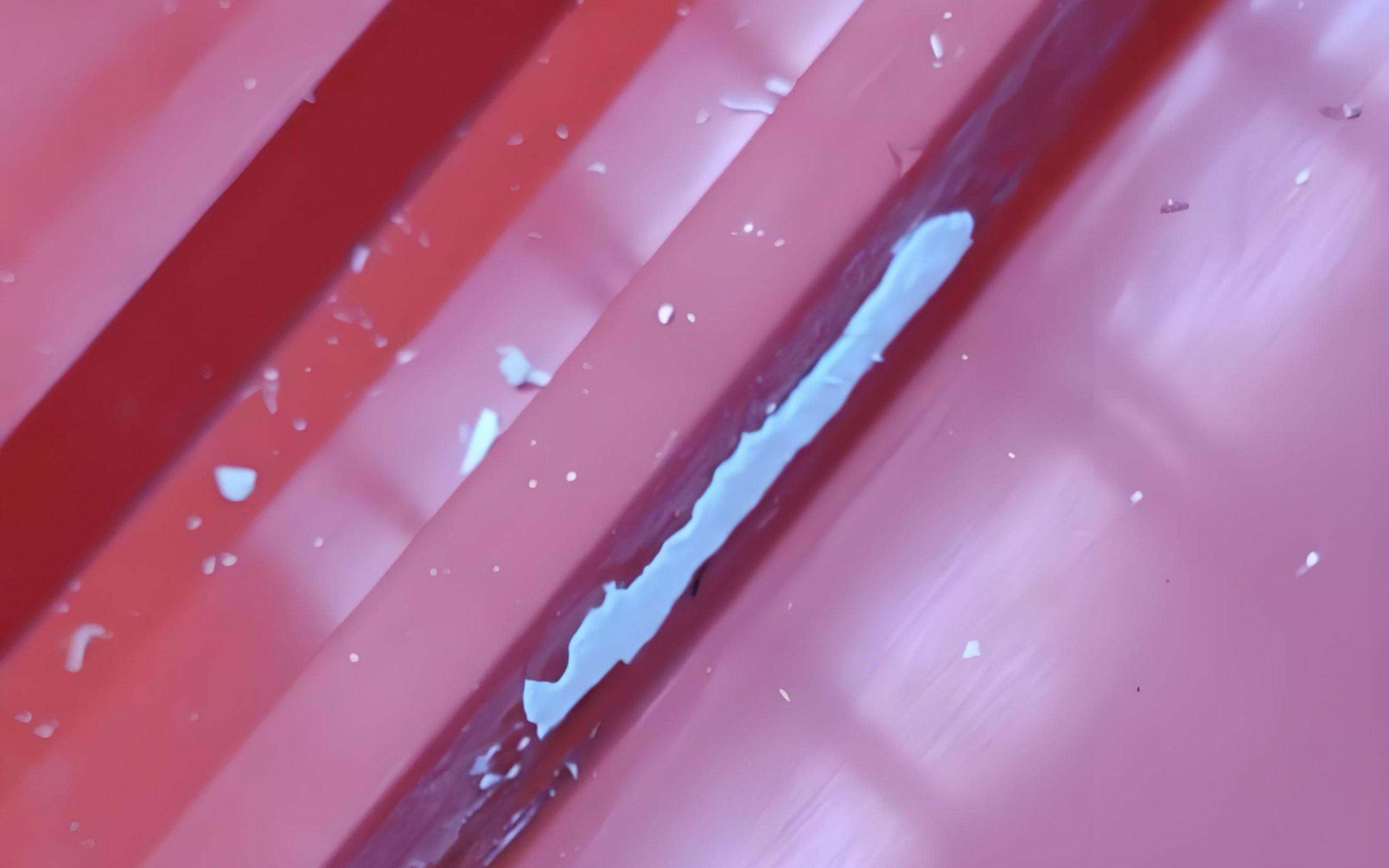
問題の顕在化
- 脱型時に材料が金型表面に付着し、生産効率に影響する。
- 熱可塑性プラスチックやシリコーンの中には、脱型後に絞りや残留痕を生じるものがある。
原因分析
- 不十分な仕上げと粗い表面は、金型キャビティ内の材料の付着を増加させる。
- 脱型角度の不合理な設計、複雑な幾何学的形状の脱型要件を十分に考慮していない。
- 表面テクスチャーの欠如、特にシリコーンのような粘着性のある材料では、表面が滑らかであると、脱型が困難になる可能性がある。
表面クラックと気泡の問題
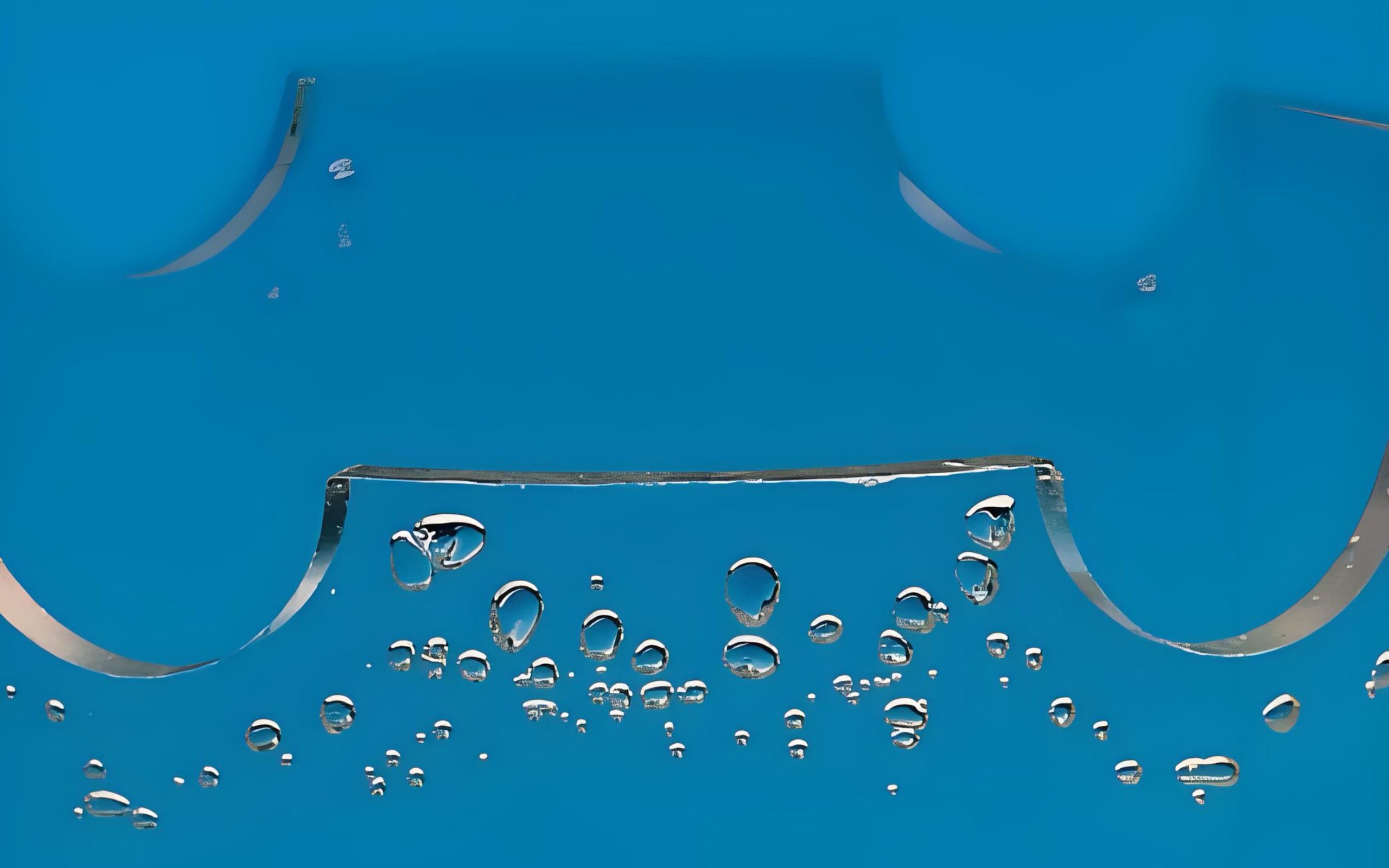
問題の顕在化
- 部品表面に銀色の傷や斑点が生じ、外観や強度に影響を及ぼす。
- ひび割れが拡大すると、使用時に部品が破損する可能性がある。
原因分析
- 射出成形材料の含水率が高すぎて、冷却時に気泡が発生する。
- 金型ベントの設計に無理があり、ガスが金型キャビティからスムーズに排出されず、クラックが発生する。
- 加工後の効果的なひび割れ補修・強化処理がない。
表面不純物が加工結果に影響
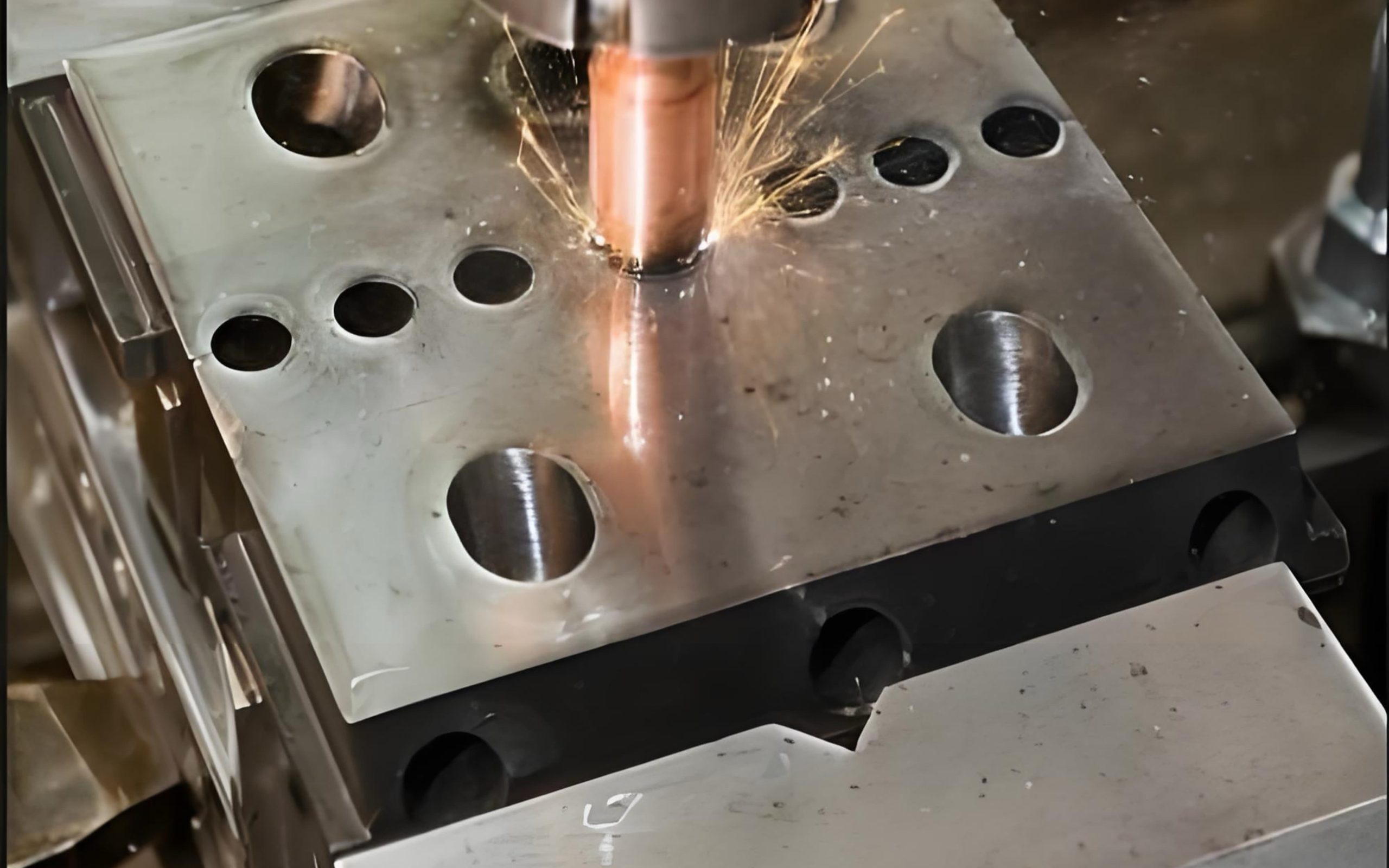
問題の顕在化
- サンドブラストや研磨の後、鋳型の表面にほこりや粒子が残っている。
- 不純物は、その後のコーティングや加工工程に影響を与える。
原因分析
- 普通のガラスビーズや粗悪なメディアを使用しているため、洗浄効率が低い。
- 不適切なサンドブラストパラメーター、最適化されていないスプレー角度または圧力、不純物は完全に除去できません。
- その後の洗浄工程が不足しているか、標準化されていない。
素材の流動性が不十分
問題の顕在化
- 射出成形工程では、材料が金型キャビティを満たすことができず、不完全な部品成形となる。
- 充填圧力不足、冷えた材料の跡、金型の溶接部などの問題が発生する。
原因分析
- 表面が粗すぎたり、光沢がありすぎたりすると、材料の流路が変化し、抵抗が増加する。
- ランナー設計の欠陥:不適切なゲート位置とサイズ、材料充填効率の不十分な最適化。
- 不均一な冷却は、材料の早期凝固を引き起こす。
ソリューション
加工前の準備
- 射出成形前に材料が完全に乾燥していることを確認し、含水率を制御するための材料の前処理。
- ソフトウェアを使用して、テクスチャーと流路設計を最適化し、均一な流れとテクスチャーの一貫性を確保する。
プロセスの最適化
- 5軸加工技術と組み合わせることで、パス間隔を調整し、ツールマークを減らし、表面の均一性を向上させる。
- 高速ミリング技術により、送りと速度の比率を最適化し、加工品質をきめ細かくコントロールする。
- 設備、高精度CNC工作機械、レーザー彫刻技術をアップグレードし、複雑なテクスチャーや細部の加工能力を向上させる。
- 工具の摩耗をリアルタイムで検知し、タイムリーに交換することで加工の安定性を確保。
加工後の洗浄と表面処理
- セラミックサンドブラストビーズなどのメディアを使用し、サンドブラストで加工残渣を除去し、平滑性を確保する。
- 超音波洗浄やガスパージを追加して、微小な不純物を完全に除去する。
- 強化処理のための鏡面研磨やサンドブラストと組み合わせることで、表面の耐久性をさらに向上させ、マイクロクラックを低減する。
脱型とその後の最適化
- 金型の傾斜を調整し、補助テクスチャーを追加し、脱型性能を最適化し、接着の問題を回避する。
- 主要部品に粘着防止コーティングを施し、摩擦係数を下げ、脱型効率を向上させる。
- ゾーニングされた温度制御システムを使用し、吹き出し口の設計を最適化することで、冷却ムラや気泡の問題を軽減する。
プロセスの検証と改善
- 材料が完全かつ均一に充填されるように、ランナーとゲートを最適化する。
- 最終テスト:金型を実際に使用し、質感、仕上げ、機能性が要件を完全に満たしているかどうかを評価する。
サンドブラスト媒体で表面仕上げを実現
鋳型の仕上げ工程では、サンドブラストは、他の加工方法の欠点を効果的に補い、表面品質を最適化できる不可欠な技術です。特に、微小な加工テクスチャ、不純物の残留、表面欠陥を解決するには、サンドブラスト媒体の選択が特に重要です。その中でも、セラミックサンドブラストビーズは、その優れた性能により、鋳型の表面仕上げを改善するための理想的な選択肢となっています。その利点は次のとおりです:
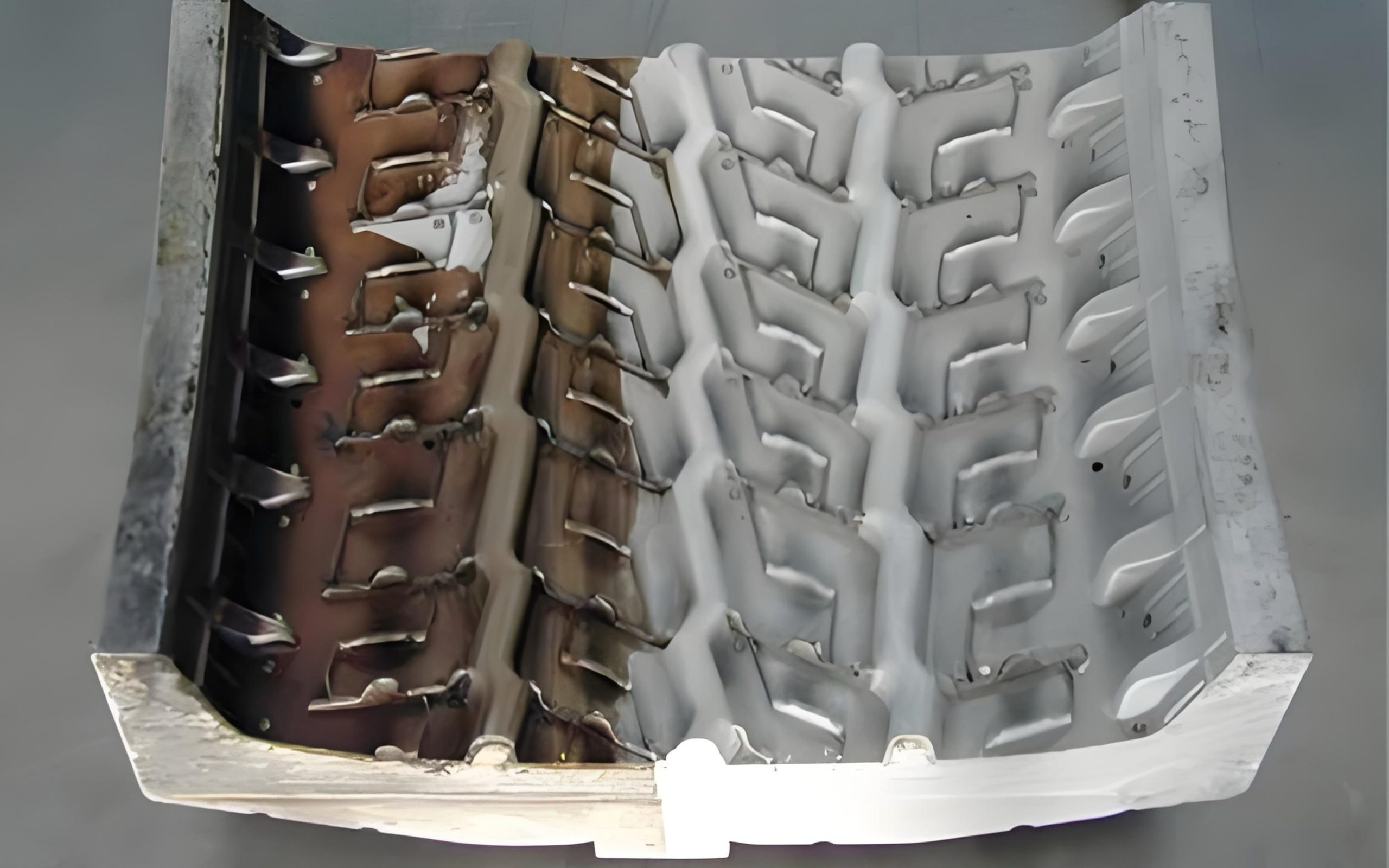
マイクロクラックを除去し、テクスチャーを加工する。 セラミックビーズはモース硬度が高く、粒子が均一です。金型表面を傷つけることなく、金型加工で残ったマイクロクラックやテクスチャーを効果的に除去し、仕上がりを最適化することができます。
表面の一貫性を高める。 セラミックメディアは、均一な密度分布と一貫したサイズを持ち、金型表面を均一に覆うことができるため、不均一なテクスチャーや過度の局所的な粗さによって引き起こされる機能上および外観上の問題を回避することができる。
接着の問題を軽減する。 セラミックビーズは良好な表面平滑性と低発塵特性を有し、金型表面の摩擦係数を効果的に低減し、脱型工程における材料の付着による損傷を低減することができる。
ワークの耐久性を向上させる。 サンドブラストはまた、金型の表面を強化し、疲労強度と耐食性を向上させ、金型の寿命を延ばすことができる。
労働環境を最適化する。 従来のガラスビーズと比較して、セラミックサンドブラストビーズは粉塵が少なく、加工精度が向上するだけでなく、健康リスクも低減します。
セラミックサンドブラストビーズの長所を組み合わせることで、金型メーカーは表面仕上げを大幅に改善できるだけでなく、ひび割れ、表面不純物、脱型の難しさなどの一般的な問題を効果的に回避し、顧客に高性能の金型ソリューションを提供することができます。
より詳細なサンドブラスト工程とメディアの推奨事項が必要な場合は、以下をご覧ください。 ご相談はこちらまで.
フィルター