レーザー除錆とサンドブラスト除錆
11月 9, 2024
近年、工業の自動化や環境保護のニーズの向上に伴い、レーザーによる錆び取りが金属表面処理の新たな人気となっている。特に、高精度で効率的な加工が要求される場面では、レーザー除錆の優れた性能が際立っています。対照的に、伝統的で成熟した表面処理技術として、サンドブラストによる除錆は多くの産業で依然として主流です。
この記事は、レーザー錆び落としとサンドブラスト錆び落としの基本的な概念、長所、短所から始まり、さまざまな産業シーンにおける両者の実用的な応用を深く探り、両者の長所を総合的に分析し、最終的に読者がこれら2つの錆び落とし方法の違いと補完性をよりよく理解できるようにする。
レーザーによるサビ取りとは?
レーザー除錆技術の応用は、1960年代のレーザー研究の初期に始まった。レーザー技術の継続的な発展、特にレーザー出力の増大とビーム精度の向上により、レーザー錆除去は新しいタイプの表面処理方法となり始めた。
レーザーによる錆除去の普及は、自動車、航空宇宙、軍事などの産業で始まった。これらの産業は表面品質に対する要求が非常に高く、レーザーによる錆除去はその効率と精度でこれらのニーズに応えている。
特に1990年代、レーザー技術は科学研究から工業生産へと徐々に移行し、レーザー錆除去の工業的応用が拡大し始めた。
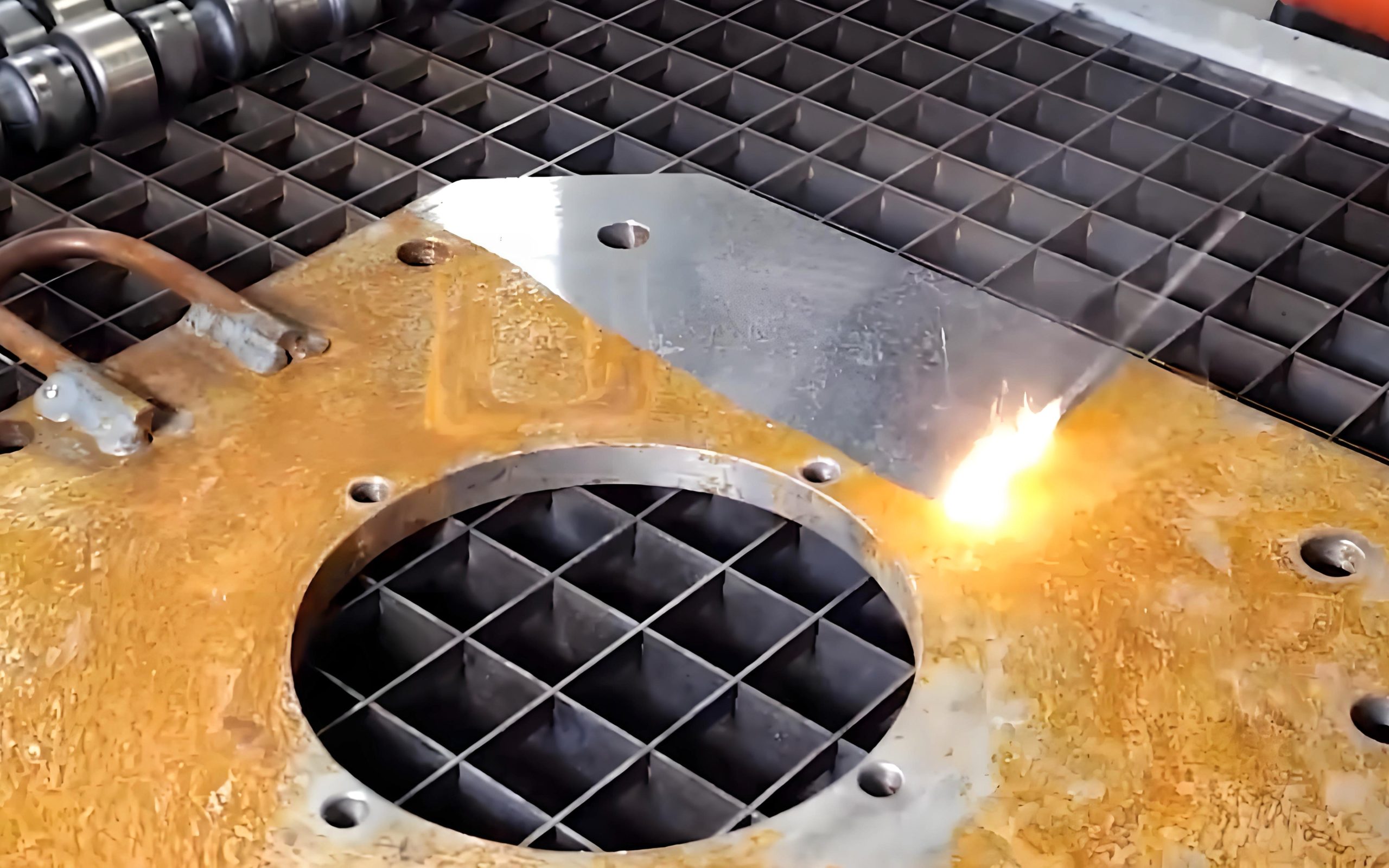
レーザーによる錆び取りは、次のような技術である。 高エネルギーのレーザー光線を金属表面に照射し、レーザー照射によって錆を蒸発、溶融、剥離させる。.レーザービームは非常に高いエネルギー密度を持ち、精密に制御することができる。通常、軽い錆の除去や高精度の表面処理が必要な場合に適しています。
メリット
- 高い精度と制御性: レーザーによる錆除去は、特に極めて高い表面精度が要求される精密加工品において、非常に高い精度を達成することができる。
- 非接触操作: 従来の機械的な洗浄方法とは異なり、レーザーによる錆除去はワーク表面に直接接触しないため、基材への機械的な損傷を避けることができます。
- 迅速かつ効率的: 薄い錆やわずかな錆の場合、レーザー錆取りは短時間で錆の層を取り除くことができ、そのスピードは従来の方法よりも速い。
デメリット
- コストが高い: レーザー除錆の設備投資は高く、レーザー設備は定期的なメンテナンスが必要で、操作も難しい。
- 適用範囲は限定的: レーザーによる錆び取りは、薄い錆び層や精密部品に適しており、重い錆びの除去効果は低い。
- 技術的な敷居が高い: レーザー錆取り装置を効果的に制御するには、専門的な訓練を受けたオペレーターが必要です。
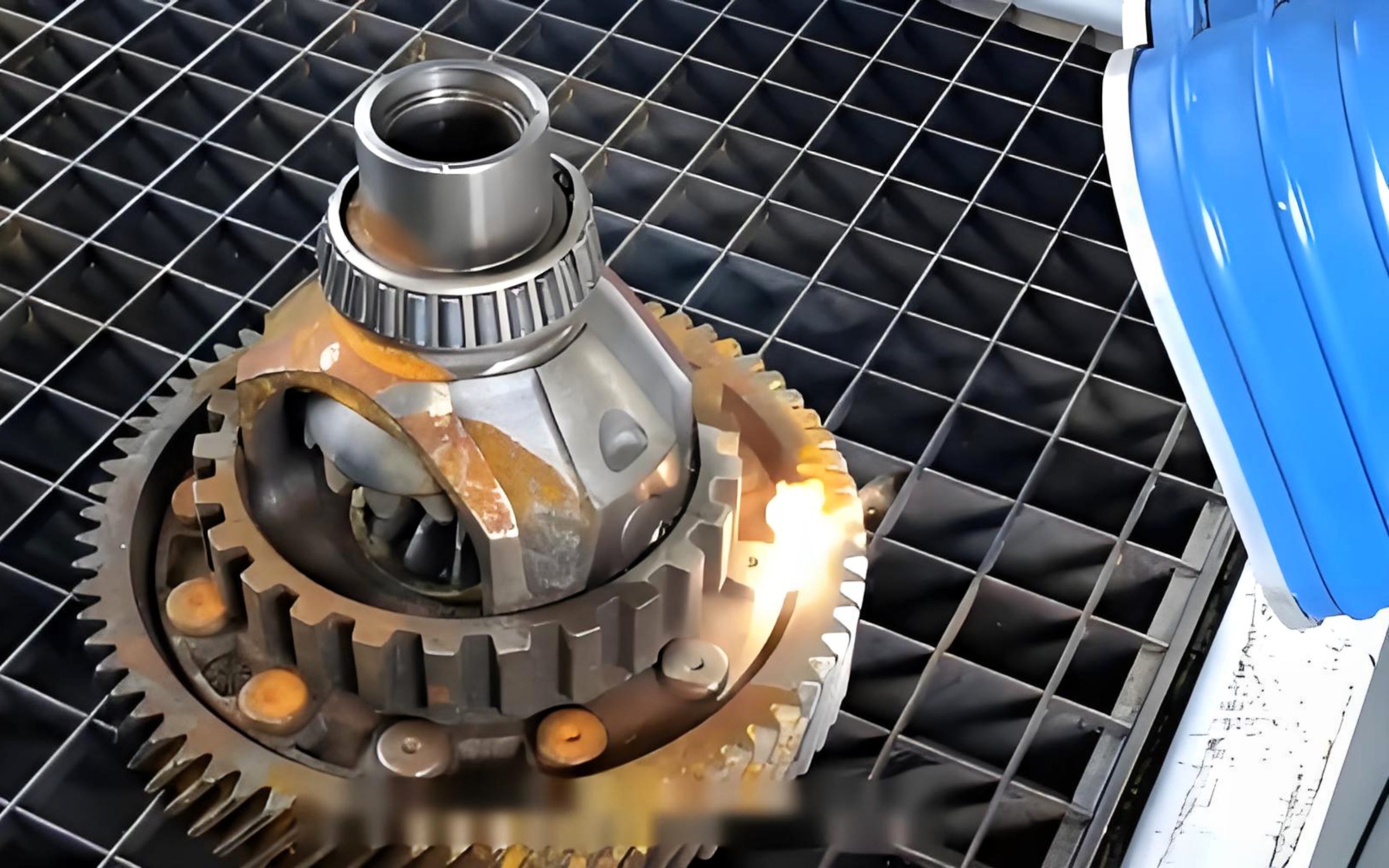
精密機器のサビ取りに最適
サンドブラストによる錆び落としとは?
サンドブラスト技術は20世紀初頭に登場し、米国のエンジニア、ベンジャミン・チュー・ティルマンによって発明された。サンドブラスト技術の継続的な進歩に伴い、特に1950年代には、鉄鋼、航空宇宙、建設など多くの産業でサンドブラスト装置が広く使用されるようになりました。主に、金属表面の錆、溶接スラグ、その他の汚れを除去し、金属表面を平滑化または粗面化するために使用されます。
サンドブラストによる錆除去技術 砂やその他の研磨剤を高圧で金属表面に噴射し、砂粒子の衝撃力で表面の錆や汚染物質を除去する。.サンドブラストによる錆の除去は、錆の層を取り除くだけでなく、金属表面を粗くし、その後の塗装や防錆コーティングの密着性を高めることができます。
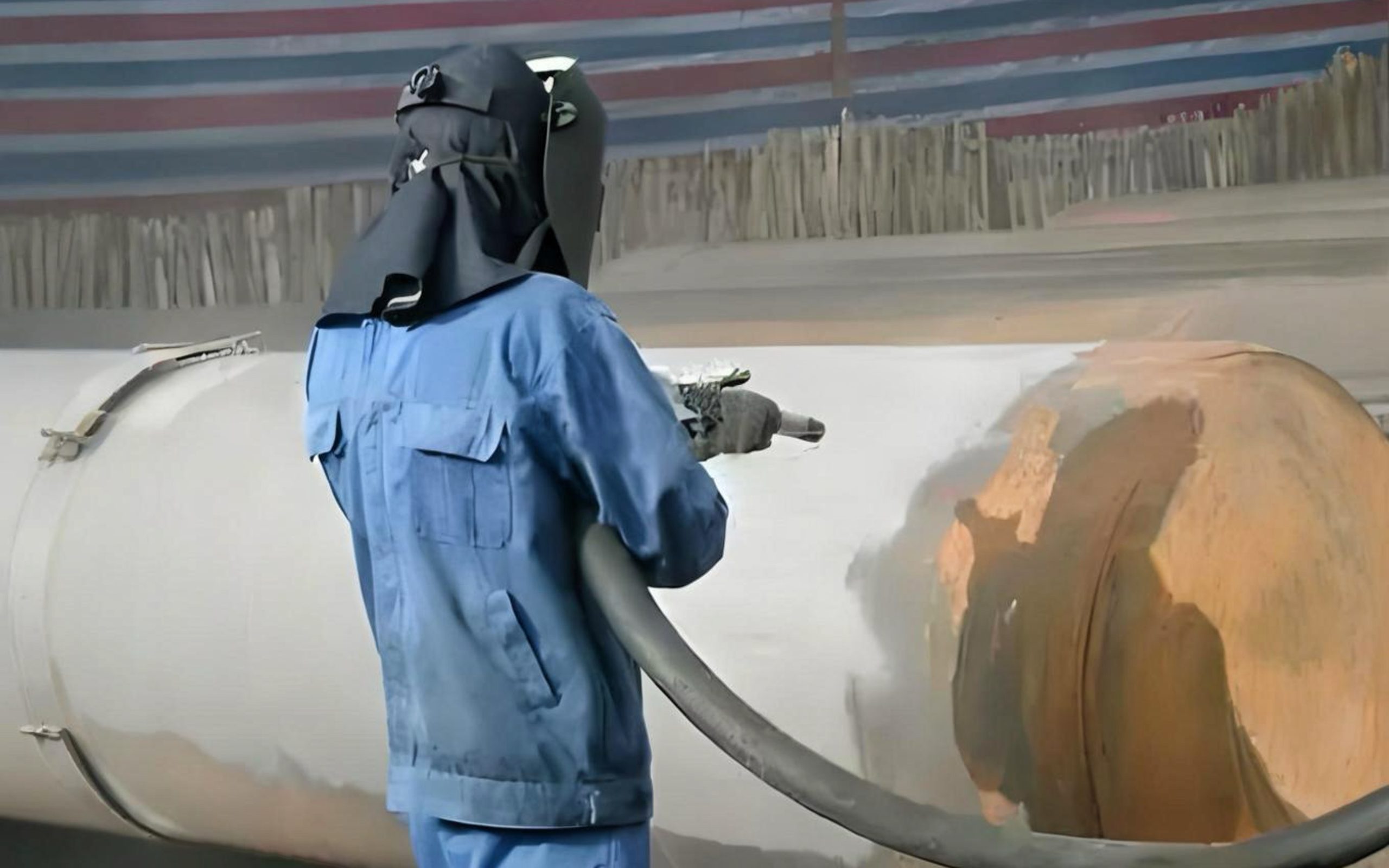
サンドブラストによる錆び除去技術は、現在でも多くの産業で好まれている方法であり、特に広い面積の金属表面を扱う場合、サンドブラストは比類のない効率性を発揮します。
メリット
- 経済的で効率的: サンドブラスト装置は、購入コストおよび運用コストが低く、大規模な用途に適しています。
- 用途は広い: サンドブラストは、複雑な幾何学形状や大きな平面など、さまざまな形状や素材の表面を処理できます。
- カスタマイズ可能: サンドブラスト媒質、噴射圧力、噴射角度を調整することで、粗度や清浄度の制御など、さまざまな表面効果を柔軟に実現できる。
デメリット
- 粉塵と騒音公害: サンドブラスト工程では大量の粉塵と騒音が発生するため、完全な排気および騒音低減システムを装備する必要があります。
- 高い労働力消費: 自動サンドブラスト装置は徐々に普及してきたが、依然として一定の手動管理と操作が必要であり、人件費が増加する。
化学的錆び落としとは?
化学的除錆技術は19世紀後半に初めて応用された。化学工業の発展に伴い、錆び取り効果のある様々な化学薬品が開発された。20世紀半ばには、環境保護規制が徐々に強化され、従来の強酸性除錆剤は徐々に環境に優しい化学薬品に取って代わられた。
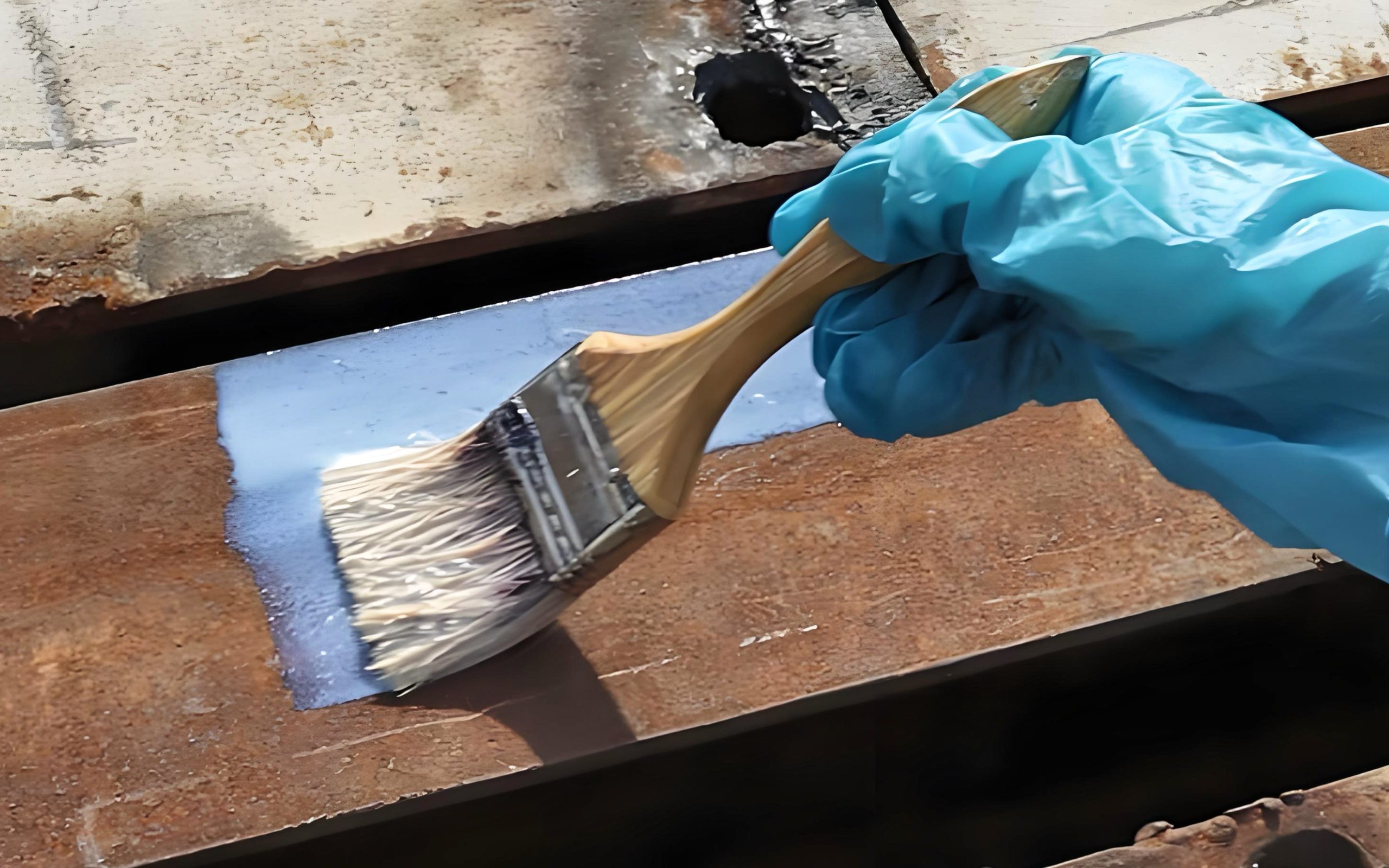
化学的錆び落としとは 化学溶剤と錆を反応させ、金属表面の酸化物を溶かしたり剥がしたりして錆の層を取り除く。.一般的な化学錆び落とし剤には、酸性、アルカリ性、中性の溶液がある。化学薬品による錆び落としは通常、複雑な幾何学的形状や手の届きにくい表面に適用され、特に従来の物理的洗浄方法が困難な場合に適用される。
化学的錆除去には長い歴史があり、特に金属表面の細部洗浄や表面処理など、特定の産業用途では今でも広く使われている。
メリット
- 複雑な形状にも対応: 複雑な構造や手の届きにくい表面を持つワークピースの場合、化学的錆除去は容易に錆の層に浸透し、除去することができる。
- 簡単な操作: 化学的な錆び落とし剤を使う場合は、表面に塗るか浸すだけでよく、操作も比較的簡単だ。
デメリット
- 腐食性が強い: 化学薬品による錆取り剤の中には、腐食性が強く、金属表面に悪影響を及ぼすものもあります。
- 環境問題: 多くの化学薬品による錆取り剤には有害物質が含まれており、環境や作業者の健康を脅かす可能性がある。
- 効果は限定的: ひどい錆や重い錆の層に対しては、化学的な錆除去剤はサンドブラストやレーザーによる錆除去ほど効果的ではありません。
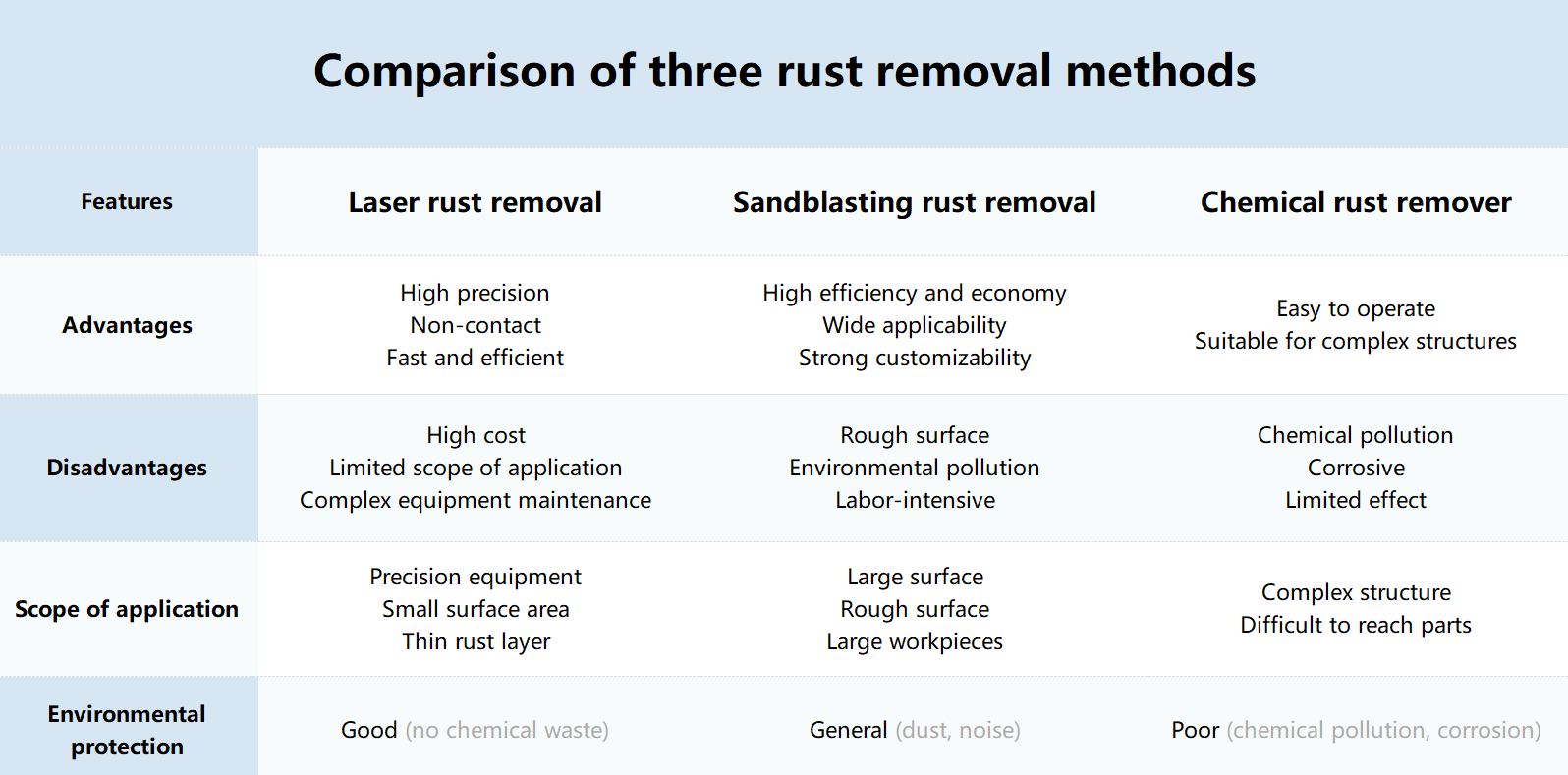
サンドブラストによる錆除去の主な利点
高効率で大面積に対応
長時間の作業を必要とするレーザーによる錆び取りに比べ、サンドブラストは短時間で大面積の金属表面の洗浄を完了できる。
また、サンドブラストは研磨剤を高速で噴射して表面を洗浄するため、錆などの汚れを素早く除去でき、大規模・大面積の加工に適している。例えば、船舶や建築物の金属構造物、大型機械設備などの表面の錆を落とすことができ、作業効率が大幅に向上します。
造船所では、船体の錆を除去するためにサンドブラスト技術を使用しており、船体全体の洗浄面積は数千平方メートルに達します。サンドブラストによって、生産効率はレーザーによる錆除去と比較して30%以上向上し、コストは50%以上削減された。
環境保護と安全性
環境保護政策がますます厳しくなる中、サンドブラストによる錆取り技術も環境保護において大きな優位性を示している。従来の化学的な錆び落としと比べると、サンドブラストは有害な化学薬品を使用せず、排出物は主に錆と研磨剤から除去されるため、環境を汚染することはない。
サンドブラスト中に発生する粉塵と騒音の問題は、環境と作業者への影響を最小限に抑えるための適切な機器制御によって改善できます。
費用対効果
レーザーによる錆除去と比較して、サンドブラスト装置は調達コストおよびメンテナンスコストが低く、操作および労働投入量も少ない。したがって、大量の錆除去が必要な用途では、サンドブラスト技術はより経済的なソリューションを提供します。
サンドブラストによる錆び除去技術は、金属表面の錆び除去に適しているだけでなく、その後のコーティングの接着に有益な表面粗面化にも適しています。大規模な鉄鋼会社では、設備表面の錆除去にサンドブラストを使用することで、従来の化学的錆除去方法と比べて運転コストを20%削減し、設備の調達およびメンテナンスコストはレーザー錆除去と比べて3分の1近く低くなります。
柔軟性と多様性
さまざまなニーズに応じて、サンドブラスト作業ではさまざまな種類の研磨剤(スチール砂、アルミ砂、ガラスビーズなど)を選択でき、それぞれ表面に異なる効果をもたらし、滑らかなものから粗いものまでさまざまな表面効果を生み出すことができる。
また、サンドブラストの操作モード(噴射角度、噴射圧力など)は、金属表面の形状や錆の厚さに応じて調整することができ、最良の錆除去効果を確保することができます。
自動化と拡張が容易
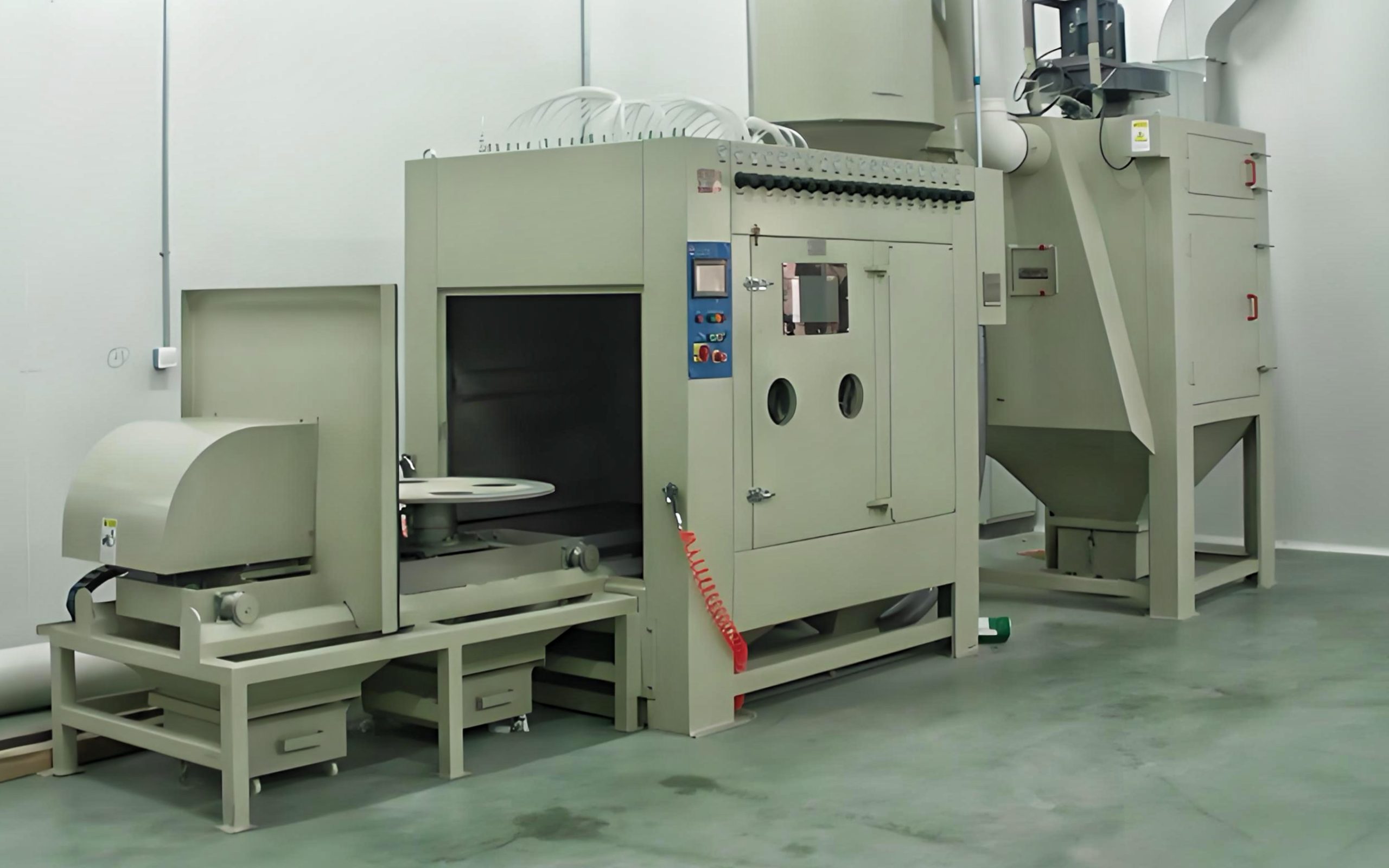
全自動サンドブラスト機
サンドブラストによる錆除去の操作プロセスは比較的単純であり、自動化が容易である。多くの工業工場に全自動サンドブラスト装置が設置され、作業効率を向上させるだけでなく、手作業による不安定性を低減することができる。自動化技術の発展に伴い、サンドブラスト設備の自動化レベルはますます高くなっており、大規模な生産作業を実現することができ、特に精密工業、自動車製造、航空宇宙などの高品質で大規模な洗浄を必要とする産業に適している。
レーザー除錆とサンドブラスト除錆の包括的比較
レーザー錆び落としとサンドブラスト錆び落としの長所と短所を分析した後、私たちは以下の次元を通じて2つの技術の包括的な比較を行うことができ、業界のお客様がさまざまな応用場面でより適切な選択をするのに役立ちます。
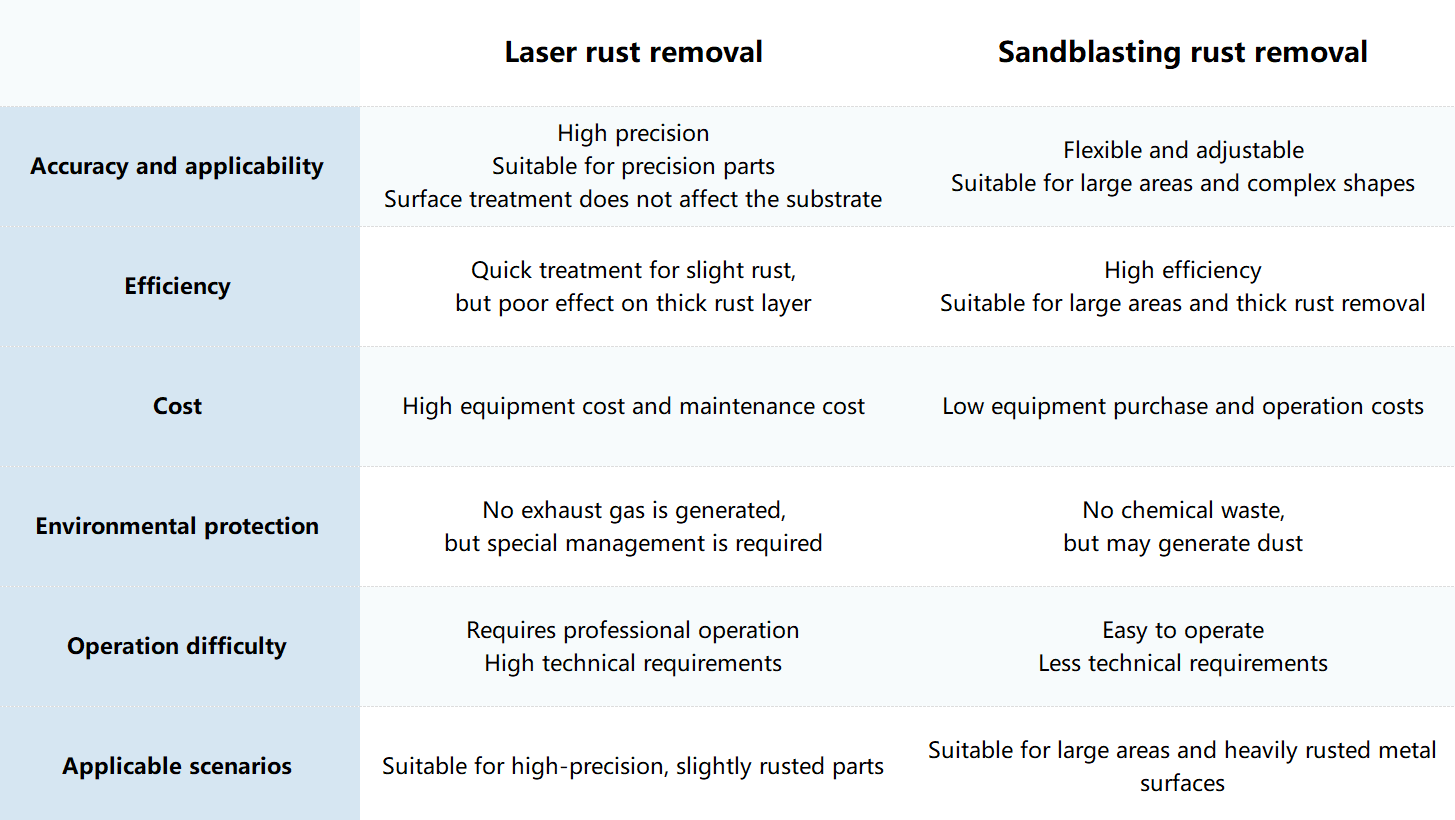
適応可能な被削材
- レーザーによる錆の除去: レーザーによる錆除去は、特に電子機器、航空宇宙、精密医療機器など、ワークピースの表面に対する要求が非常に高い分野で、高精度の金属表面に適しています。
下地を傷つけることなく、金属表面の錆を除去することができる。
チタン合金、ステンレス鋼などの特殊金属材料では、レーザーによる錆除去が特に有利である。
- サンドブラストによる錆取り: サンドブラストは、鉄鋼、アルミニウム合金、銅など、さまざまな金属材料に適しています。特に、大面積の鋼構造物、重機、船舶、製鉄所設備、自動車部品などの錆除去に適しています。
サンドブラストは、錆を除去するだけでなく、さまざまな種類の研磨材を選択することで、金属表面に特定の粗さや質感を与え、その後のコーティングの密着を助けます。
適用錆度
- レーザーによる錆の除去: レーザーによる錆び取りは、わずかな錆びや局所的な錆びの除去に適しており、厚い錆び層の除去には効果が限られるため、深い錆びにはサンドブラストほどの効果はありません。
電子部品や医療機器など、わずかな錆を伴う精密部品に適している。
- サンドブラストによる錆取り: サンドブラストによる錆除去は、より深刻な錆を処理することができ、特に厚い錆層の除去に適しており、比較的丈夫で大きな金属表面に対して良好な洗浄効果を発揮する。
重機や設備、建築鉄骨、船舶などの大面積の錆洗浄に適している。
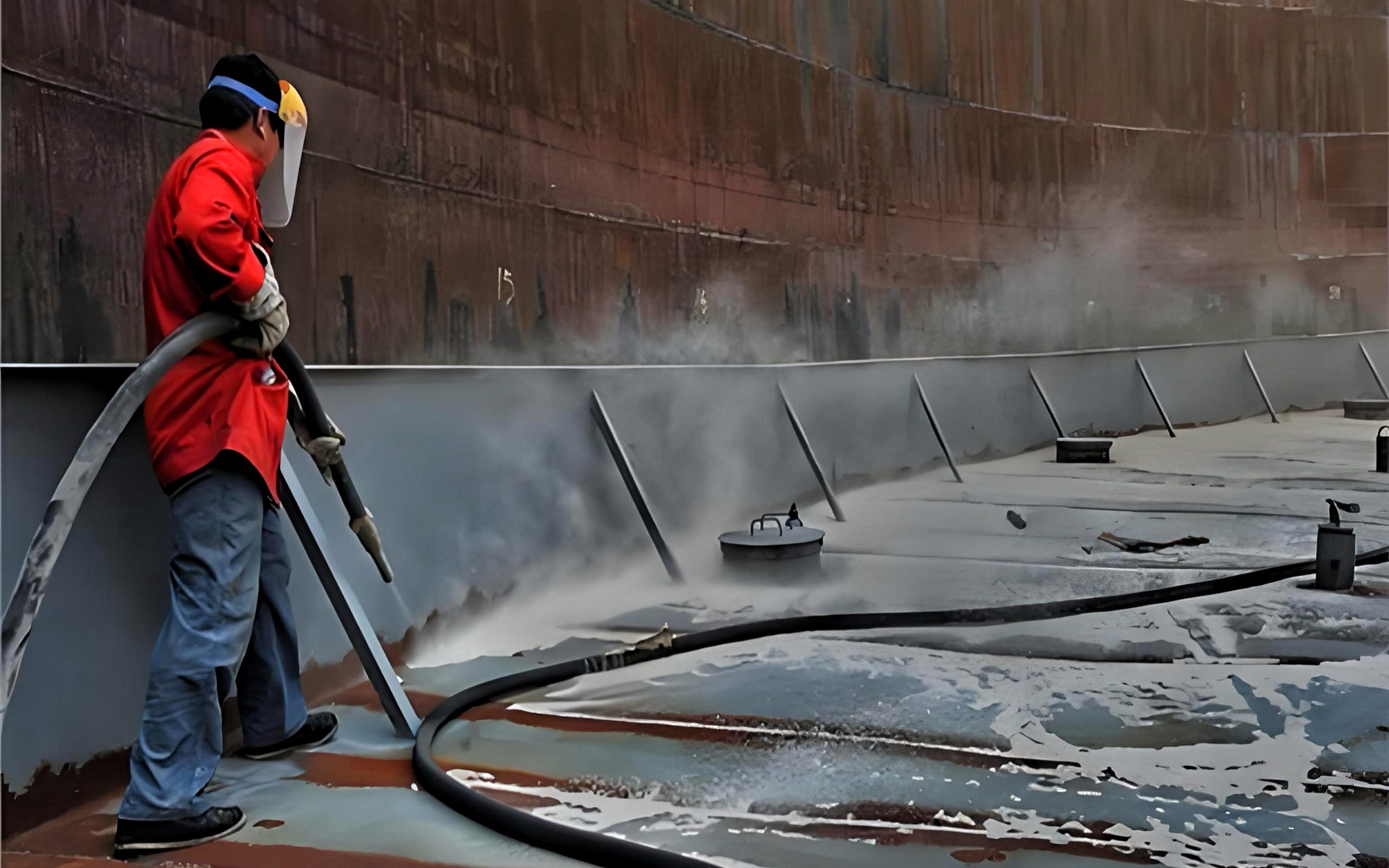
サンドブラストは錆がひどい場合に適している。
適用表面効果
- レーザーによる錆の除去: レーザーによる錆除去は、より滑らかな表面効果を得ることができ、金属表面の粗さを変える必要のない用途に適している。元の金属表面の滑らかさを維持するように努めながら錆を除去することができ、不必要な粗面化を避けることができる。
航空宇宙、医療機器などの高精度分野など、表面品質に対する要求が極めて高い精密分野に適用可能。
- サンドブラストによる錆取り: サンドブラストは、砥粒の衝突によって金属表面に一定の粗さを形成し、塗料や溶射皮膜、防食皮膜の密着性を高める効果があります。そのため、錆び落としだけでなく、金属表面の凹凸加工も可能で、ある程度の粗さが必要な部品によく使用されます。
自動車部品、建築用金属材料、塗装前の表面処理など、表面を粗くする必要があるシーンに適している。
プロセス要件と複雑さ
- レーザーによる錆の除去: レーザーによる錆び取り技術は比較的複雑で、高精度のレーザー機器と操作技術が必要であり、オペレーターが効果的に行うには専門的なトレーニングを受ける必要がある。
レーザーによる錆取りは操作が簡単だが、設備費が高く、維持費も比較的高い。
さらに、レーザー錆び取り装置は高い環境要件があり、良好な動作条件を維持する必要がある。
- サンドブラストによる錆取り: サンドブラストによる錆の除去プロセスは比較的簡単で、設備投資も少なく、技術的な敷居も低い。
サンドブラストシステムはほとんどが密閉システムであり、運転中の粉塵と騒音が目立つため、粉塵除去と騒音防止装置が必要です。
経済性と効率性
- レーザーによる錆の除去: レーザー除錆は、高価値、少量生産の金属部品の除錆に適している。一回の作業効率は高いが、設備コストが高いため、レーザー除錆は精密要求が高く、少量生産の精密工業分野にのみ適している。
- サンドブラストによる錆取り: サンドブラストによる錆の除去は、効率とコストにおいて大きな利点がある。サンドブラスト装置の購入コストは比較的低く、大面積の表面を短時間で処理できる。特に、鉄鋼、建設、造船などの大規模で反復性の高い産業に適しています。
この記事の比較を通じて、適切な錆び除去技術の選択は、特定のアプリケーション要件、ワークピースの種類、および表面要件に応じて決定されるべきであるという結論に達することができます。高い精度と少ない錆が必要なワークには、レーザー錆除去が最適な選択であり、大規模生産と重い錆の金属部品の錆除去には、サンドブラスト錆除去がより効率的で経済的な解決策を提供する。
実際の生産現場では、2つの技術の長所を組み合わせ、さまざまなワークや錆び取り作業の要求に応じて柔軟に選択・適用することで、錆び取り効果と生産効率を向上させ、コストを削減し、各産業における錆び取り技術の発展と革新を促進することができる。
フィルター