¿Qué son las perlas de desbarbado de poliestireno?
12 de septiembre de 2024
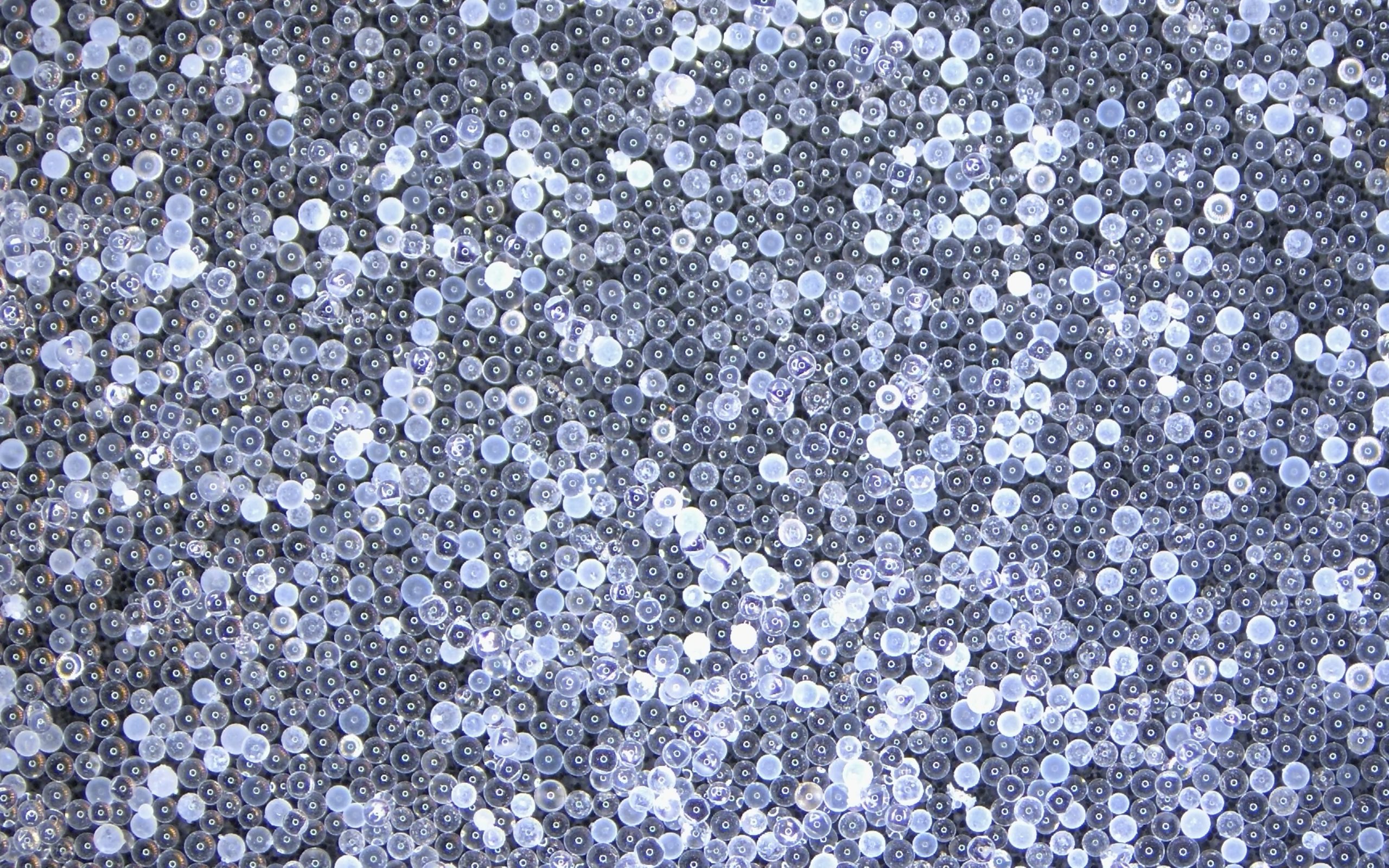
En el rápido desarrollo de la industria moderna, la fabricación de precisión se ha convertido en la clave para conseguir una calidad excelente en diversos campos. En el proceso de producción de piezas de precisión, el desbarbado es un eslabón crucial, que afecta directamente al rendimiento, la fiabilidad y la calidad estética del producto. Los métodos tradicionales de desbarbado, como el manual, la vibración, el calentamiento, el laminado, etc., suelen tener muchas limitaciones, como la baja eficacia, la facilidad para dañar las piezas y la contaminación ambiental. En los últimos años, las perlas de desbarbado de poliestireno, como un nuevo tipo de medio de desbarbado, han surgido en el campo del mecanizado de precisión con sus ventajas únicas, proporcionando nuevas ideas y métodos para resolver el problema del desbarbado.
¿Qué son las perlas de desbarbado de poliestireno?
Haga clic en aquí para ver la página del producto
Propiedades físicas
- Color: Blanco transparente, de aspecto puro y hermoso.
- Forma: Las partículas esféricas, con un tamaño entre 0,2~1,2 mm, de tamaño uniforme, pueden satisfacer las necesidades de desbarbado de diferentes piezas de precisión.
- Volumen: La densidad es de 0,93-0,96 g/cm3Es relativamente ligero y fácil de manejar y transportar. También se puede distribuir fácil y uniformemente sobre la superficie tratada en la aplicación, con una amplia cobertura, reduciendo eficazmente el tiempo de trabajo y el consumo de energía durante el proceso de limpieza.
- Resistividad superficial: Inferior a 109 ohmios, con ciertas propiedades antiestáticas.
- Absorción de agua: Baja, sin deformación ni degradación del rendimiento del material debido a la absorción de agua. Esta propiedad hace que sea adecuado para aplicaciones que requieren a prueba de humedad o en ambientes húmedos, tales como el envasado y la protección de los componentes electrónicos y dispositivos médicos.
- Termoplasticidad: Su temperatura de deformación térmica es de 205°C y su punto de fusión es de 220° Tiene una gran resistencia al calor y puede trabajar de forma estable dentro de un determinado rango de temperaturas. Dentro de esta gama de temperaturas, puede plastificarse por calentamiento y solidificarse en un producto de forma fija por enfriamiento. Esta propiedad lo convierte en un material ideal ampliamente utilizado en procesos de fabricación como el moldeo por inyección y el moldeo por extrusión.
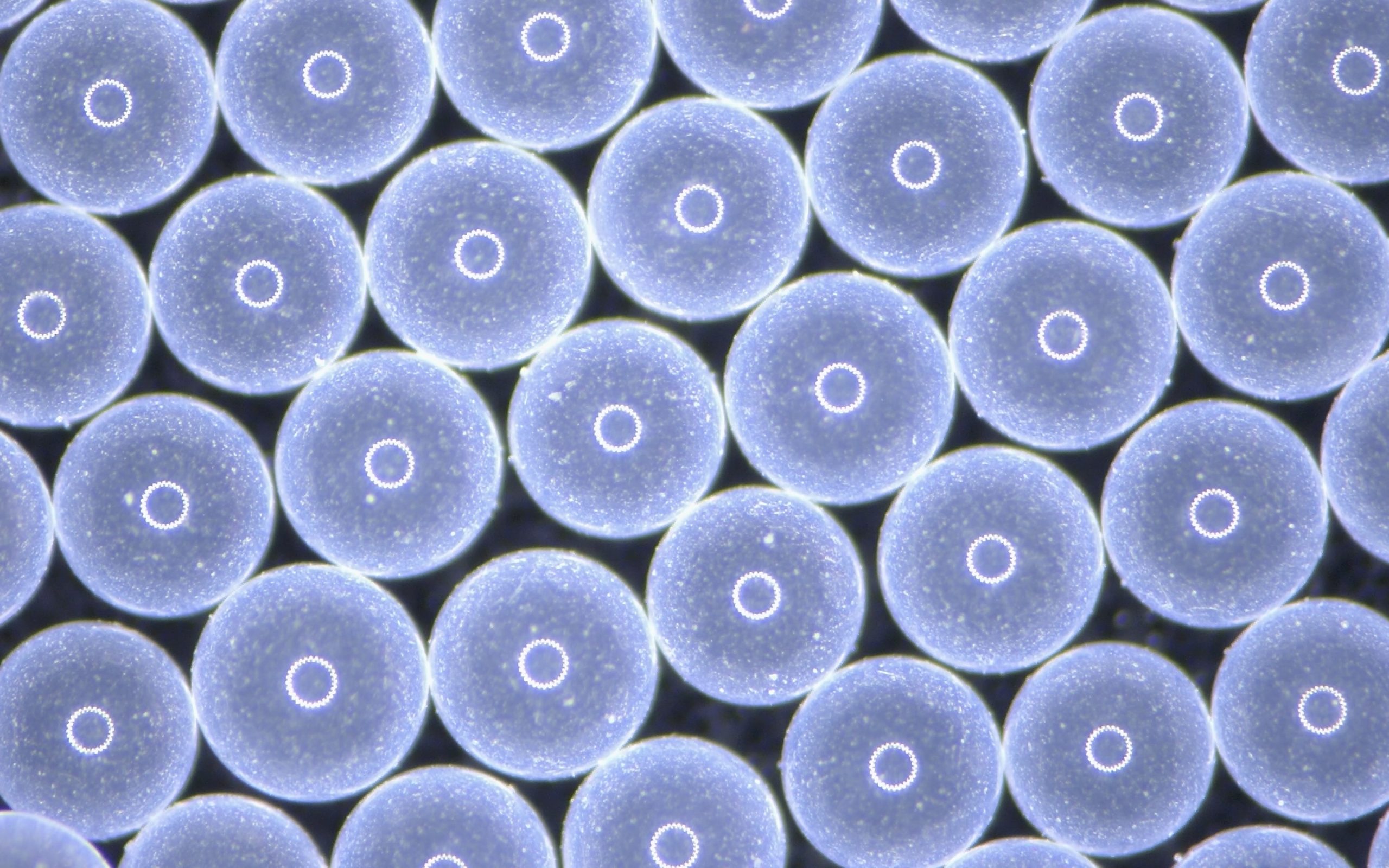
Esfera transparente
Propiedades químicas
- Componente principal: Poliestireno, con propiedades químicas estables. No es fácil que reaccione con la mayoría de los productos químicos. Tiene buena resistencia a los ácidos, a los álcalis y a la corrosión química, pero es sensible a algunos disolventes orgánicos, como el benceno y el tolueno, y se hincha o incluso se disuelve.
- Olor: Inodoro e insípido, no causará efectos adversos en el entorno de trabajo.
Ventajas
Cierta solidez y estabilidad
La fuerza de tracción es de 2750, la tensión de flexión es de 21000, y la contracción de moldeo está entre 1,2 - 1,5. Estas características indican que tiene cierta resistencia y estabilidad, y no es fácil de deformar o dañar durante el proceso de desbarbado. Puede garantizar un uso a largo plazo, reducir la frecuencia de cambio del medio y ahorrar costes.
Partículas esféricas uniformes
El tamaño uniforme puede entrar en contacto con la superficie de la pieza de trabajo de manera más uniforme, mejorar el efecto y la eficacia del desbarbado, y en comparación con los medios de forma irregular, las partículas esféricas están sometidas a una tensión más uniforme durante el movimiento, y pueden adaptarse a piezas de precisión de diferentes formas.
No tóxico, inocuo y sin polvo
Las perlas de desbarbado de poliestireno son inodoras, insípidas y no tóxicas. Además, su densidad volumétrica es ligera, y no es fácil que levanten polvo durante el funcionamiento, manteniendo limpio el entorno de trabajo. Esto es especialmente importante para el procesamiento de piezas de precisión, porque si el polvo entra en el interior de la pieza, es probable que afecte a su rendimiento y fiabilidad. Al mismo tiempo, un entorno de trabajo limpio también es beneficioso para la salud de los trabajadores, ya que reduce problemas de salud como las enfermedades respiratorias causadas por la inhalación de polvo.
Sin residuos
Su bajo contenido en hierro garantiza que no se introduzcan impurezas durante el proceso de desbarbado. La propiedad antiestática ayuda a reducir la posibilidad de que las impurezas sean atraídas por la electricidad estática. Es especialmente adecuado para campos eléctricos y electrónicos que requieren un alto rendimiento de aislamiento, y puede evitar fallos o interferencias causados por la electricidad estática durante el proceso de desbarbado. Esta ventaja garantiza el rendimiento y la fiabilidad de los componentes de precisión.
No daña la capa galvánica
Las perlas de desbarbado de poliestireno tienen una temperatura de deformación por calor y un punto de fusión elevados, y no dañarán la capa galvánica debido a los cambios de temperatura durante el proceso de desbarbado. Al mismo tiempo, sus propiedades químicas estables no reaccionarán con la capa galvánica. Esto es muy adecuado para algunas piezas con superficies galvánicas, porque la capa galvánica suele tener un efecto protector y decorativo. Si se daña, no sólo afectará al aspecto de la pieza, sino que también puede reducir su resistencia a la corrosión y otras propiedades.
Diferencias con los medios de desbarbado de poliamida de nailon
Aspectos físicos
- Forma: Las bolas de desbarbado de poliestireno son esféricas, mientras que los medios de desbarbado de poliamida de nailon tienen forma cilíndrica o irregular. Cuando la esfera entra en contacto con la pieza, se trata de un contacto puntual. Gracias a su forma especial, puede rodar y ajustar su posición con mayor flexibilidad durante el proceso de desbarbado para adaptarse a las superficies de piezas con formas diferentes. De este modo, la fuerza de desbarbado es relativamente uniforme y no es fácil que se forme un sobredesbaste local en la superficie de la pieza. El medio cilíndrico es relativamente regular durante el movimiento, normalmente rodando o deslizándose en una dirección específica. Esta característica de movimiento puede dar lugar a una cobertura relativamente estrecha del desbarbado, y en el caso de algunas piezas de trabajo con formas complejas, es posible que no se eliminen completamente todas las rebabas.
- Densidad: La densidad volumétrica de las perlas de desbarbado de poliestireno es de 0,93-0,96 g/cm3que es relativamente más ligera, mientras que la densidad de los medios de desbarbado de nylon y poliamida suele ser mayor. La menor densidad hace que las bolas de desbarbado de poliestireno sean más ligeras y fáciles de controlar durante la operación.
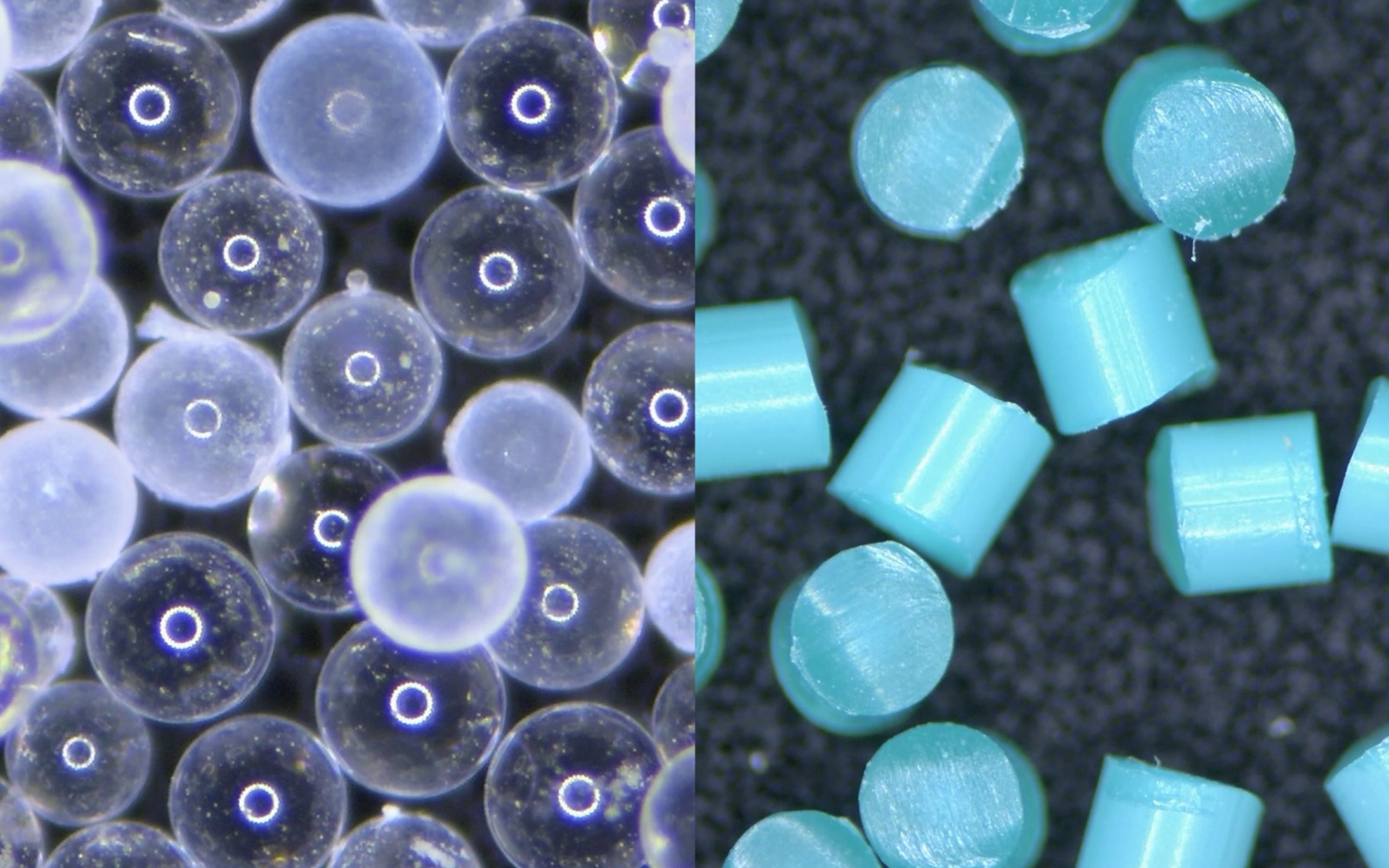
Distintas formas producen distintos efectos
Rendimiento
- Efecto deflector: Las perlas de desbarbado de poliestireno no dañan la capa galvánica durante el desbarbado y no dejan residuos. Es adecuado para piezas de precisión con requisitos de alta precisión, mientras que los medios de desbarbado de poliamida de nylon pueden necesitar ser ajustados y optimizados para algunas piezas de trabajo especiales y complejas.
- Ámbito de aplicación: Los medios esféricos de las perlas de desbarbado de poliestireno se tensionan uniformemente durante el movimiento, lo que puede reducir los arañazos y daños en la superficie de la pieza de trabajo. Son especialmente adecuados para piezas con elevados requisitos de calidad superficial, como piezas de plástico de precisión y superficies galvánicas. Los medios de desbarbado de poliamida de nailon son principalmente cilíndricos, y el contacto con la pieza de trabajo suele ser de línea o superficial. Este modo de contacto puede producir una mayor fricción en la superficie de la pieza durante el desbarbado, y es más adecuado para piezas como metales y plásticos que requieren una alta resistencia al desgaste.
Campo de aplicación
Componentes electrónicos
- Antecedentes: Los componentes electrónicos, como chips y microprocesadores, tienen unos requisitos de limpieza y precisión dimensional extremadamente altos durante el proceso de producción. A medida que los dispositivos electrónicos se miniaturizan cada vez más, cualquier rebaba residual o impureza diminuta puede provocar fallos en los componentes o afectar a su rendimiento eléctrico. Los métodos de desbarbado mecánicos tradicionales a menudo no pueden cumplir estos requisitos de alta precisión, mientras que las bolas de desbarbado de poliestireno funcionan bien en la limpieza de carcasas de componentes electrónicos y componentes internos. Su diseño esférico no abrasivo garantiza que la capa superficial del componente no se dañará ni causará problemas de electricidad estática al eliminar las rebabas.
- Aplicación: Bosch, un conocido fabricante alemán de productos electrónicos, utiliza esta tecnología para desbarbar conectores de precisión. Los resultados muestran que la tasa de defectuosidad de los componentes de los conectores se ha reducido en unas 15%, la eficiencia de la producción ha aumentado en 20%, la tasa de cualificación de la producción de componentes ha mejorado significativamente y se han reducido los fallos eléctricos causados por problemas de rebabas.
Piezas de caucho de precisión
- Antecedentes: En industrias como la automovilística y la médica, las piezas de caucho de precisión deben mantener un alto grado de acabado superficial y exactitud dimensional. Los métodos tradicionales de desbarbado pueden causar daños en la superficie de goma o un desgaste excesivo, mientras que los cordones de desbarbado de poliestireno pueden evitarlo eficazmente gracias a sus propiedades de material blando.
- Aplicación: Las perlas de poliestireno se utilizan ampliamente en las líneas de producción de fabricantes de automóviles como Toyota. Toyota introdujo la tecnología de desbarbado de poliestireno en el proceso de fabricación de juntas de motor de automóviles, reduciendo con éxito la tasa de aparición de defectos superficiales de las juntas de caucho: los problemas de rebabas se redujeron en 30%. Dado que las rebabas no permanecen en las juntas mientras se garantiza el rendimiento de sellado, los costes de producción de Toyota se controlan eficazmente.
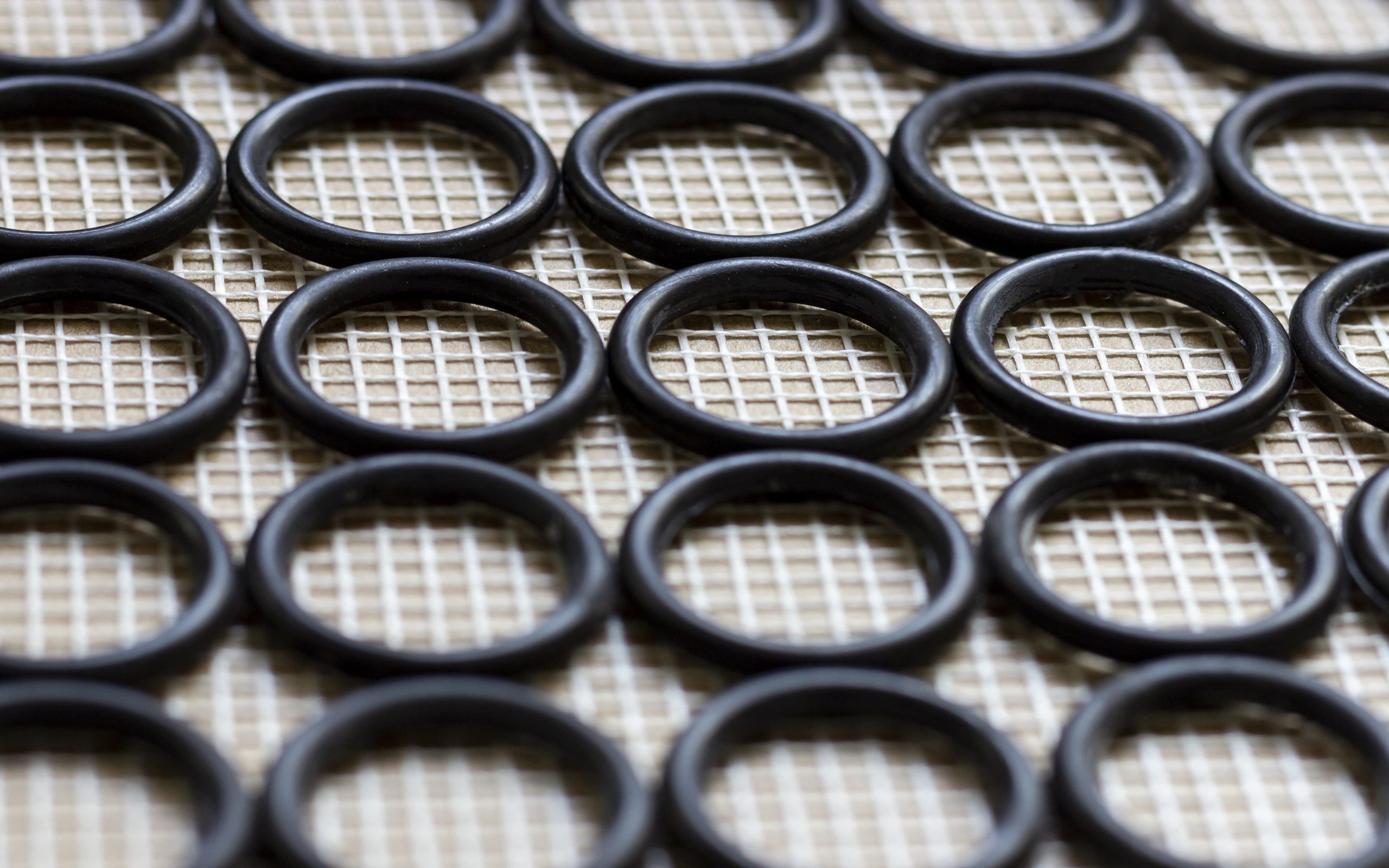
Anillos de estanqueidad
Piezas de plástico de precisión
- Antecedentes: Las piezas de plástico de precisión se utilizan ampliamente en industrias con requisitos de alta precisión, como la médica y la aeroespacial. El desbarbado es fundamental en la fabricación de estos componentes, especialmente en piezas de plástico con formas complejas o muchas cavidades. Unos medios de desbarbado inadecuados pueden dañar la superficie de las piezas de plástico o afectar a su funcionalidad.
- Aplicación: La empresa estadounidense de productos sanitarios Medtronic utiliza perlas de desbarbado de poliestireno en el proceso de limpieza de las carcasas de plástico de sus implantes médicos. Los resultados muestran que este material no abrasivo puede eliminar microabrasiones manteniendo el acabado liso de la superficie del plástico sin afectar a la funcionalidad y seguridad del implante. Este proceso reduce con éxito la necesidad de un procesamiento secundario y mejora la eficacia de la línea de producción. Con la introducción de este proceso, Medtronic ha aumentado la tasa de cualificación de los implantes de plástico en unos 18% y ha acortado el ciclo de producción en 12%, ahorrando a la empresa mucho tiempo y costes.
Beneficios económicos y protección del medio ambiente
Beneficios económicos
- Mejorar la eficiencia de la producción: El rendimiento de desbarbado de alta eficiencia de las perlas de desbarbado de poliestireno puede acortar en gran medida el tiempo de procesamiento y mejorar la eficiencia de la producción. En comparación con los métodos tradicionales de desbarbado, el uso de perlas de desbarbado de poliestireno puede aumentar la eficiencia de la producción en más de 40%.
- Reducir costes: La larga vida útil y el bajo índice de pérdida de las bolas de desbarbado de poliestireno permiten reducir los costes de producción de las empresas. En comparación con los medios de desbarbado tradicionales, el uso de perlas de desbarbado de poliestireno puede reducir los costes en más de 30%.
Protección del medio ambiente
- No tóxico e inocuo: Las perlas de desbarbado de poliestireno no son tóxicas y no dañan el medio ambiente ni la salud humana. Durante el proceso de producción y uso, no se producirán sustancias nocivas, lo que cumple los requisitos de protección medioambiental.
- Reciclable: Los cordones de desbarbado de poliestireno pueden reciclarse, lo que reduce el despilfarro de recursos y la contaminación ambiental. Las empresas pueden recoger y procesar los cordones de desbarbado usados y reutilizarlos en la producción, reduciendo los costes de producción y contribuyendo a la protección del medio ambiente.
Como nuevo tipo de plástico para chorro de arena, las perlas de desbarbado de poliestireno han mostrado amplias perspectivas de aplicación en el campo del mecanizado de precisión gracias a sus ventajas únicas, como limpieza y ausencia de polvo, ausencia de residuos y ausencia de daños en la capa galvánica. Sus buenas propiedades físicas y químicas, como partículas esféricas uniformes, menor densidad volumétrica, buena resistencia al calor y resistencia al agua, potencian aún más sus ventajas. A través de la presentación de datos de casos reales de empresas, podemos ver los notables efectos de las perlas de desbarbado de poliestireno en diversos campos. Al mismo tiempo, también tiene buenos beneficios económicos y de protección del medio ambiente, proporcionando un fuerte apoyo para el desarrollo sostenible de las empresas. Con el avance continuo de la ciencia y la tecnología y el desarrollo sostenible de la industria, se cree que los cordones de desbarbado de poliestireno se utilizarán en más campos y contribuirán en mayor medida a promover el desarrollo de la fabricación de precisión.
Proceso de producción y control de calidad
Proceso de producción
- Selección de materias primas
HLH selecciona poliestireno de alta calidad como materia prima principal y, tras un estricto cribado, garantiza su alta pureza, una distribución uniforme del peso molecular y buenas propiedades físicas y químicas. Con el fin de satisfacer las necesidades de diferentes escenarios de aplicación, también se pueden añadir algunos aditivos especiales, como agentes antiestáticos, lubricantes, etc., para mejorar el rendimiento de las perlas de desbarbado.
- Método de moldeo
Adoptando una avanzada tecnología de moldeo por inyección, el poliestireno se calienta hasta un estado fundido y, a continuación, se inyecta en un molde de precisión y, tras enfriarse y solidificarse, se forman cordones desbarbadores esféricos. El proceso de moldeo por inyección garantiza que los cordones de desbarbado tengan una gran precisión dimensional, una forma regular y una superficie lisa, lo que contribuye a mejorar el efecto y la eficacia del desbarbado.
Control de calidad
- Detección estricta del tamaño
Durante el proceso de producción, se utilizarán equipos de medición de alta precisión para detectar estrictamente el tamaño de las perlas de desbarbado y garantizar que su tamaño se encuentra dentro del intervalo especificado. En el caso de las perlas de desbarbado cuyo tamaño no cumpla los requisitos, se llevará a cabo un cribado y procesamiento oportunos para garantizar la consistencia y fiabilidad del producto.
- Prueba de resistencia
Para garantizar que los cordones de desbarbado tengan suficiente resistencia y estabilidad durante su uso, se llevarán a cabo pruebas de resistencia. Los métodos de ensayo incluyen pruebas de tracción, flexión, etc. para evaluar la fuerza de tracción, la tensión de flexión y otros indicadores de rendimiento de los cordones de desbarbado. Sólo los cordones de desbarbado que superen la prueba de resistencia pueden entrar en el mercado para su venta, a fin de garantizar la calidad y seguridad del producto.
- Verificación del rendimiento antiestático
Dado que los cordones de desbarbado de poliestireno tienen determinadas propiedades antiestáticas, es necesario verificar su rendimiento antiestático. Los métodos de verificación incluyen pruebas de resistividad de la superficie, pruebas de tiempo de decaimiento estático, etc. para garantizar que el rendimiento antiestático de los cordones de desbarbado cumple los requisitos. Si el rendimiento antiestático no cumple los requisitos, se realizarán los ajustes y mejoras correspondientes para mejorar el rendimiento antiestático del producto.
- Sistema de trazabilidad de la calidad
Establecer un sistema completo de trazabilidad de la calidad, numerar y registrar cada lote de perlas de desbarbado de poliestireno, de modo que cuando se produzcan problemas de calidad, se puedan rastrear a tiempo hasta el eslabón de producción, averiguar la causa raíz del problema y solucionarlo. El sistema de trazabilidad de la calidad puede mejorar eficazmente el nivel de control de calidad de los productos y proteger los derechos e intereses de los usuarios.
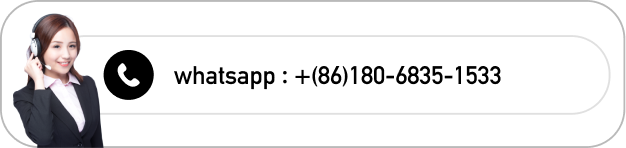