The Top 10 Applications of Ceramic Blasting in Manufacturing
Februar 21, 2025
Ceramic blasting has revolutionized industrielle Oberflächenbehandlung, offering superior precision, durability, and material compatibility. Compared to traditional blasting media like Glasperlen oder Aluminiumoxid, ceramic abrasives enhance efficiency while minimizing material degradation. This article explores 10 key applications of ceramic blasting in manufacturing, detailing how this technology is shaping high-performance industries.
1. Aerospace: Enhancing Fatigue Resistance and Coating Adhesion
In aerospace, components like turbine blades, landing gear, and structural parts require superior surface preparation for thermal barrier coatings (TBCs) and fatigue resistance.
Ceramic blasting advantages:
- Creates a uniform, roughened surface for stronger coating adhesion.
- Reduces surface defects, preventing crack initiation and fatigue failures.
- Meets AMS2431 and AS9100 standards, ensuring high-quality surface treatment.
Example: A study on titanium alloy components showed that ceramic blasting improved coating bond strength by 30%, leading to longer service life in aircraft engines.

2. Medical Implants: Improving Biocompatibility and Osseointegration
Medical implants—such as hip joints, dental implants, and orthopedic screws—require surface roughness to ensure proper bone integration and bio-coating adhesion.
Why ceramic blasting is preferred:
- Bietet Ra values between 2-5 µm, ideal for hydroxyapatite and plasma spray coatings.
- Does not introduce metallic contamination, crucial for ISO 13485 compliance.
- Enhances osseointegration, improving implant stability.
Fallstudie: Titanium spinal implants treated with ceramic blasting showed 25% faster bone integration compared to untreated surfaces.
3. Automotive: Surface Preparation for Lightweight & High-Strength Components
With the shift to lightweight materials in electric vehicles (EVs), components made from aluminum, magnesium, and carbon fiber composites require controlled surface roughness for coating adhesion and fatigue resistance.
Applications in the automotive industry:
- Cylinder heads & engine blocks: Prepares surfaces for wear-resistant coatings.
- EV battery enclosures: Ensures proper adhesion of insulation coatings.
- Suspension components: Improves surface strength and fatigue resistance.
OEM manufacturers are increasingly using ceramic blasting to achieve consistent surface textures without material deformation.
4. Electronics: Precision Cleaning of Micro-Components
In der semiconductor and electronics industries, ceramic blasting is used for deburred PCBs, semiconductor packaging, and connector housings.
Vorteile:
- Removes oxides and flux residues without affecting conductive layers.
- Ensures ultra-smooth surfaces for high-precision bonding.
- Sicher für delicate materials like silicon wafers and gold-plated connectors.


5. Molds & Tooling: Extending Lifespan and Performance
Mold surfaces must remain smooth and contamination-free to produce high-quality injection-molded parts.
Ceramic blasting helps by:
Removing residues without damaging the mold profile.
Improving wear resistance for longer mold lifespans.
Ensuring uniform texture for optical-grade plastics.
Example: A mold manufacturer increased productivity by 40% using ceramic blasting for regular mold maintenance.
6. Energy Industry: Preparing Wind Turbine and Nuclear Components
High-performance steel and composite materials used in wind turbines, nuclear reactors, and offshore platformsrequire precise surface roughness to withstand extreme environments.
Key benefits:
- Prepares surfaces for anti-corrosion coatings.
- Removes oxides without weakening structural integrity.
- Enhances friction bonding for composite materials.
Example: Wind turbine blades treated with ceramic blasting achieved 20% higher adhesion strength for protective coatings, improving lifespan in marine environments.
7. Defense & Firearms: Enhancing Durability and Functionality
Firearms and defense equipment require surface treatment for corrosion resistance, wear resistance, and heat dissipation.
Applications in defense manufacturing:
- Gun barrels and components: Reduces friction and heat buildup.
- Armor plating: Prepares surfaces for advanced ballistic coatings.
- Optical devices: Ensures clean, high-precision optics.
Ceramic blasting ensures compliance with military-grade coatings, such as MIL-STD-171.
8. Luxury Goods: Improving Surface Aesthetics and Durability
High-end watches, jewelry, and decorative metals require fine blasting techniques to create matte, satin, or textured finishes.
Why ceramic blasting is ideal:
- Erzeugt uniform, fine textures without scratches.
- Enhances gold plating and anodized aluminum finishes.
- Ensures consistent results for mass production.
Example: A luxury watch manufacturer used ceramic blasting to achieve a flawless matte finish on titanium cases.


9. Additive Manufacturing (3D Printing): Post-Processing for Metal & Plastic Parts
Ceramic blasting is essential for removing powder residue, improving surface roughness, and enhancing coating adhesion on 3D-printed parts.
Post-processing benefits for 3D printing:
- Removes unfused metal particles from SLM & DMLS prints.
- Improves paint and coating adhesion for polymer prints.
- Bietet consistent surface textures for high-precision aerospace and medical components.
Example: A medical device manufacturer reduced post-processing time by 50% using ceramic blasting for titanium implants.
10. Sustainable Manufacturing: Recyclable and Low-Dust Abrasives
Ceramic blasting media is highly recyclable, reducing industrial waste. Compared to traditional abrasives:
Ceramic media lasts 6-10 times longer than glass beads.
Produces less dust, improving workplace safety.
Minimizes energy consumption in manufacturing processes.
Fallstudie: A manufacturer using ceramic blasting cut abrasive consumption by 70%, reducing operational costs.
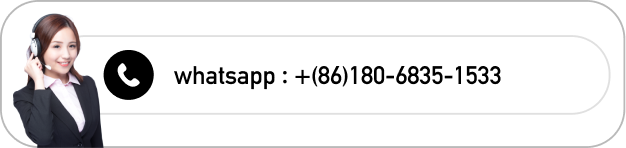