Laser rust removal and sandblasting rust removal
November 9, 2024
In recent years, with the improvement of industrial automation and environmental protection needs, laser rust removal has gradually become a new favorite in metal surface treatment. Especially in scenarios that require high-precision and efficient processing, laser rust removal stands out with its excellent performance. In contrast, as a traditional and mature surface treatment technology, sandblasting rust removal remains dominant in many industries.
This article will start from the basic concepts, advantages, and disadvantages of laser rust removal and sandblasting rust removal, deeply explore the practical applications of the two in different industrial scenarios, conduct a comprehensive analysis of their advantages, and finally help readers better understand the differences and complementarity of these two rust removal methods.
What is laser rust removal?
The application of laser rust removal technology originated in the early days of laser research in the 1960s. With the continuous development of laser technology, especially the increase in laser power and the improvement of beam accuracy, laser rust removal has begun to become a new type of surface treatment method.
The widespread application of laser rust removal began in industries such as automobiles, aerospace, and military. These industries have extremely high requirements for surface quality, and laser rust removal meets these needs with its efficiency and precision.
Especially in the 1990s, laser technology gradually shifted from scientific research to industrial production, and the industrial application of laser rust removal began to expand.
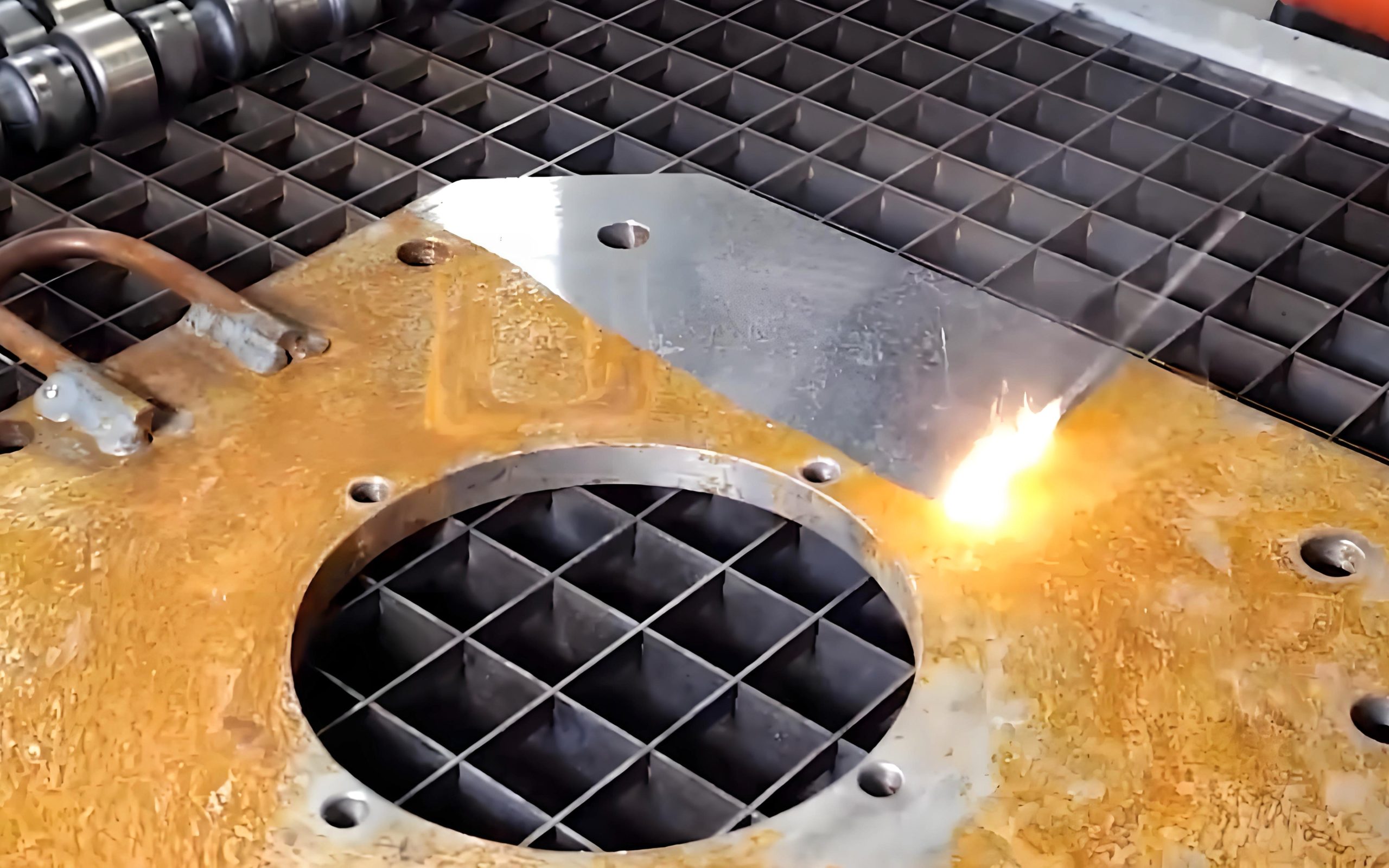
Laser rust removal is a technology that uses high-energy laser beams to irradiate the metal surface and evaporate, melt, or peel off the rust through laser radiation. The laser beam has an extremely high energy density and can be precisely controlled. It is usually suitable for removing lighter rust or occasions that require high-precision surface treatment.
Advantages:
- High precision and controllability: Laser rust removal can achieve very high precision, especially for precision workpieces with extremely high surface requirements.
- Non-contact operation: Unlike traditional mechanical cleaning methods, laser rust removal does not directly contact the workpiece surface, avoiding mechanical damage to the substrate.
- Fast and efficient: For thin rust or slight rust, laser rust removal can remove the rust layer in a short time, and its speed is faster than traditional methods.
Disadvantages:
- High cost: The equipment investment for laser rust removal is high, the laser equipment needs regular maintenance, and the operation is also difficult.
- Limited scope of application: Laser rust removal is suitable for thin rust layers or precision parts, and the removal effect of heavy rust is poor.
- High technical threshold: Professionally trained operators are required to effectively control laser rust removal equipment.
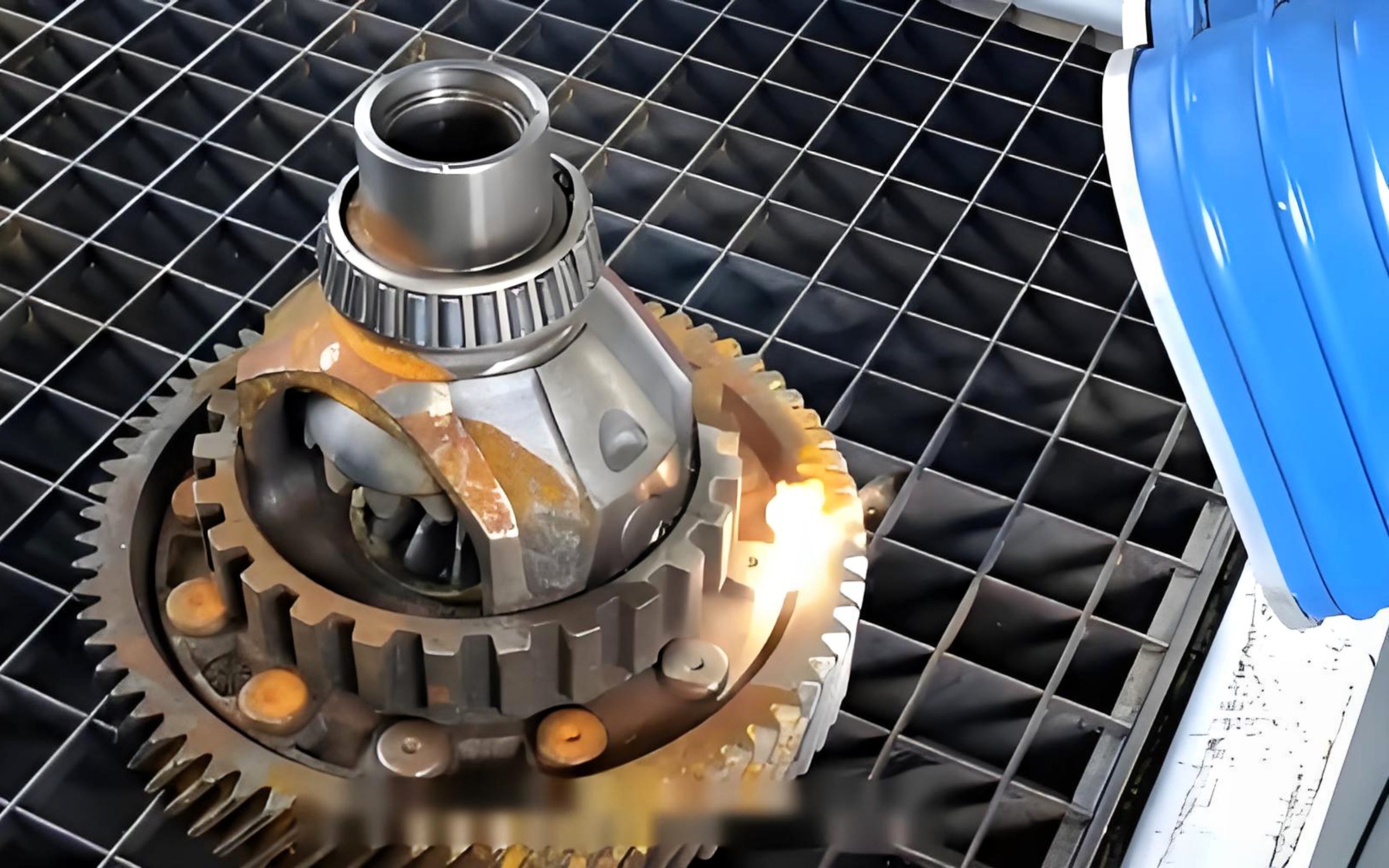
Suitable for rust removal of precision equipment
What is sandblasting rust removal?
Sandblasting technology first appeared in the early 20th century and was invented by American engineer Benjamin Chew Tilghman. With the continuous advancement of sandblasting technology, especially in the 1950s, sandblasting equipment began to be widely used in many industries such as steel, aerospace, and construction. It is mainly used to remove rust, welding slag, and other dirt on the metal surface, and to smooth or roughen the metal surface.
Sandblasting rust removal technology uses the impact force of sand particles to remove rust and pollutants on the surface by spraying sand or other abrasives at high pressure onto the metal surface. Sandblasting rust removal can not only remove the rust layer but also roughen the metal surface to provide better adhesion for subsequent painting or anti-corrosion coating.
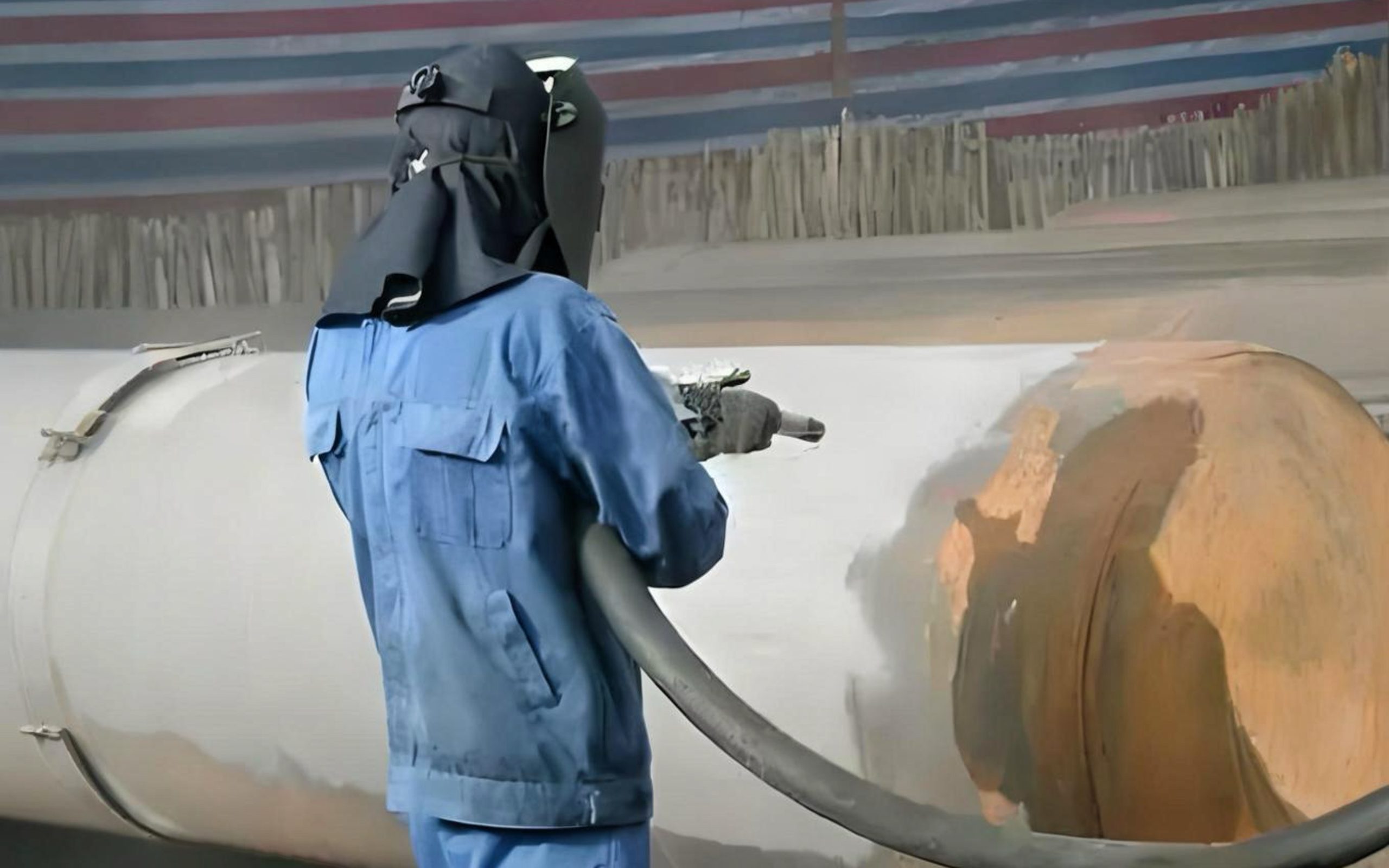
Sandblasting rust removal technology is still the preferred method in many industries, especially when dealing with large areas of metal surfaces, sandblasting has unparalleled efficiency.
Advantages:
- Economical and efficient: Sandblasting equipment has low purchase and operation costs and is suitable for large-scale applications.
- Wide application: Sandblasting can handle surfaces of various shapes and materials, whether complex geometric shapes or large flat surfaces.
- Customizable: By adjusting the sandblasting medium, spray pressure, and angle, sandblasting can flexibly achieve different surface effects, including roughness and cleanliness control.
Disadvantages:
- Dust and noise pollution: The sandblasting process will generate a lot of dust and noise, so it is necessary to equip a complete exhaust and noise reduction system.
- High labor consumption: Although automated sandblasting equipment has gradually become popular, it still requires certain manual management and operation, which increases labor costs.
What is chemical rust removal?
Chemical rust removal technology was first applied in the late 19th century. With the development of the chemical industry, various chemicals with rust removal effects have been developed. In the mid-20th century, with the gradual strengthening of environmental protection regulations, traditional strong acid rust removers were gradually replaced by more gentle and environmentally friendly chemicals.
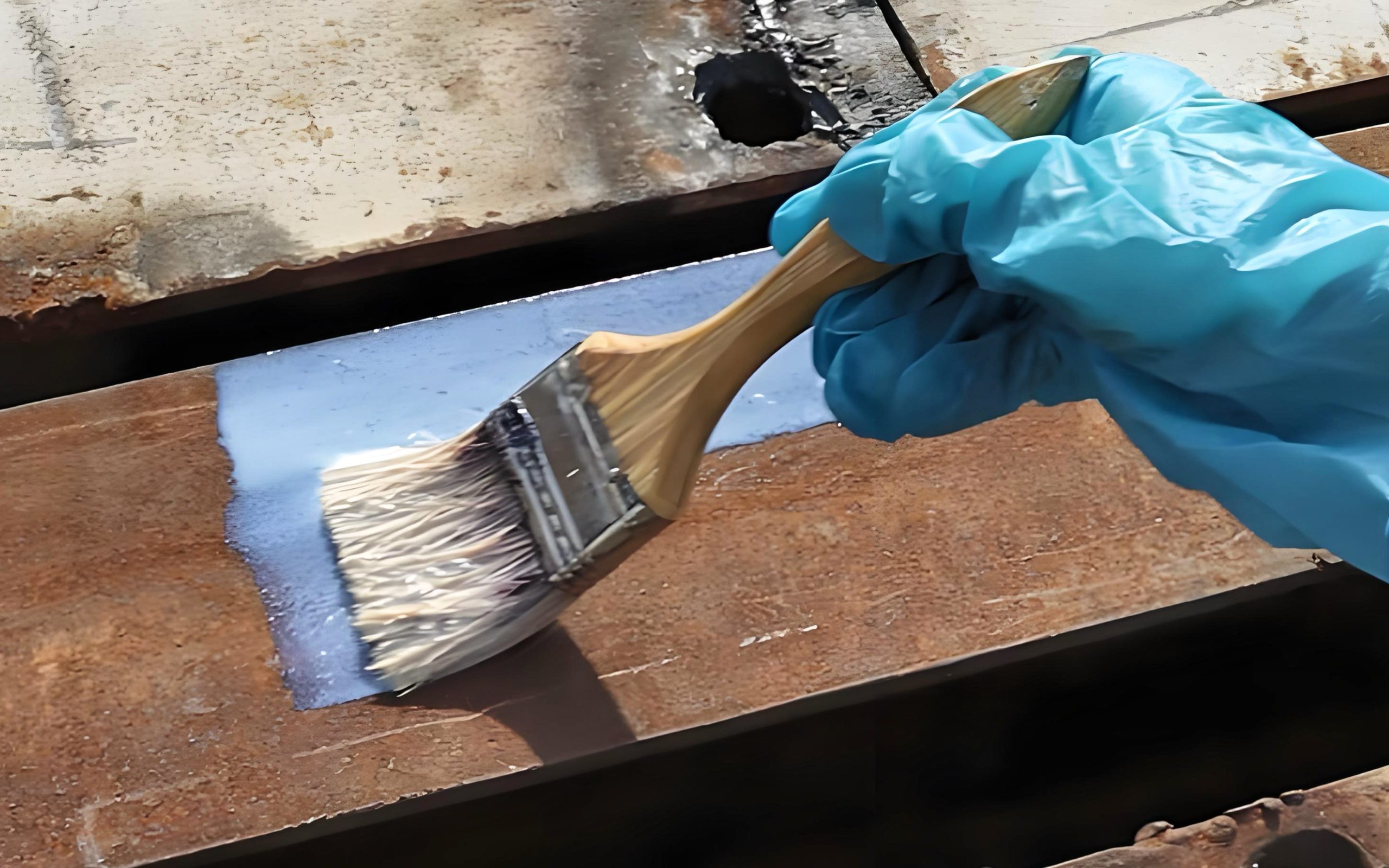
Chemical rust removal is to remove the rust layer by reacting chemical solvents with rust to dissolve or peel off the oxides on the metal surface. Common chemical rust removers include acidic, alkaline, and neutral solutions. Chemical rust removal is usually applied to complex geometric shapes or difficult-to-reach surfaces, especially when traditional physical cleaning methods are difficult to apply.
Chemical rust removal has a long history and is still widely used in some specific industrial applications, especially in metal surface detail cleaning and surface treatment.
Advantages:
- Applicable to complex shapes: For some workpieces with complex structures and difficult-to-reach surfaces, chemical rust removal can easily penetrate and remove the rust layer.
- Simple operation: When using chemical rust removers, you only need to apply or soak the surface, which is relatively simple to operate.
Disadvantages:
- Strong corrosiveness: Some chemical rust removers are highly corrosive and may have adverse effects on metal surfaces.
- Environmental issues: Many chemical rust removers contain harmful substances, which pose a potential threat to the environment and the health of operators.
- Limited effect: For severe rust or heavy rust layers, chemical rust removers are not as effective as sandblasting and laser rust removal.
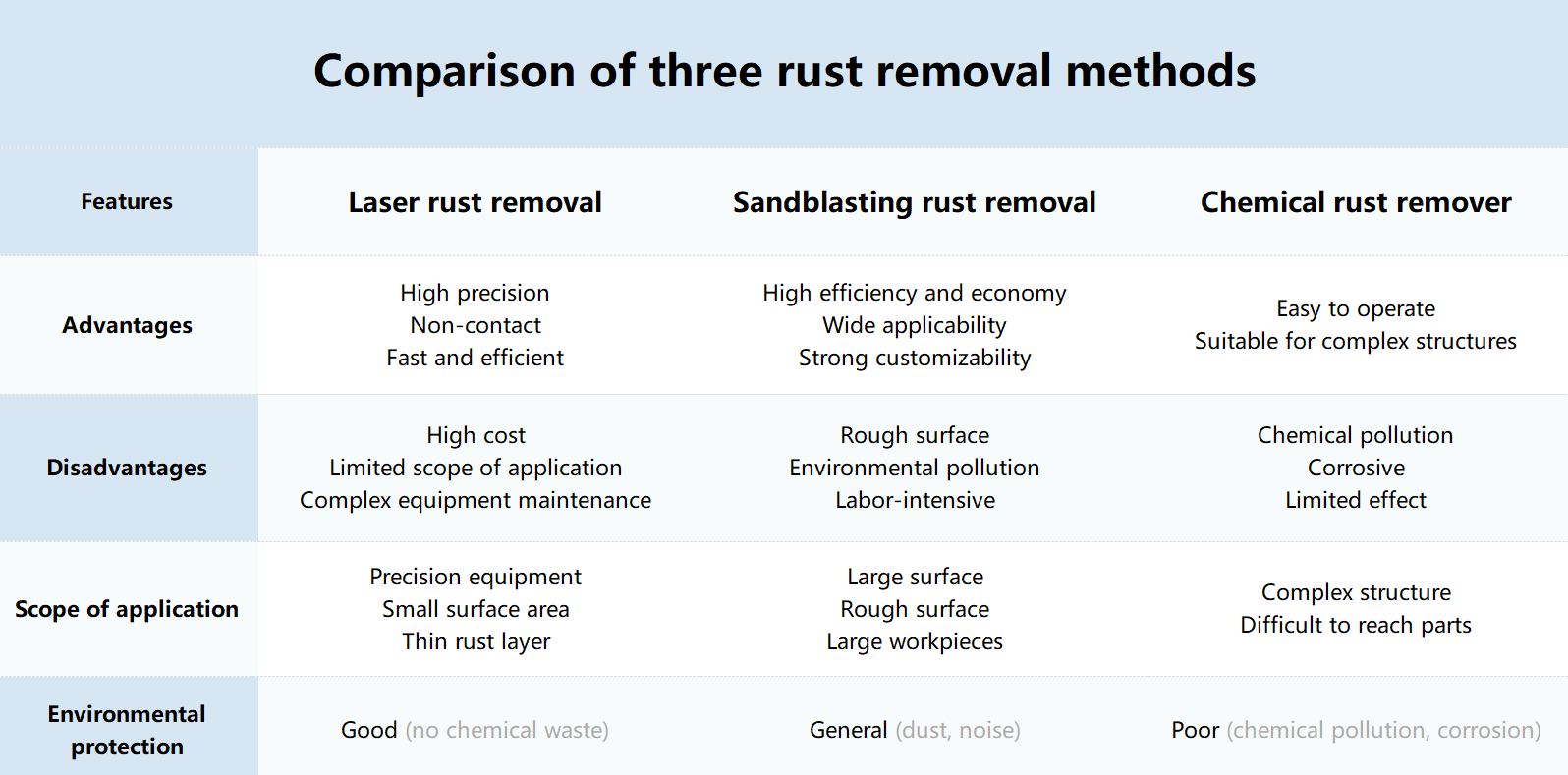
The core advantages of sandblasting rust removal
High efficiency and large-area applicability
Compared with laser rust removal, which requires a long operation time, sandblasting can complete large-area metal surface cleaning in a shorter time.
In addition, sandblasting cleans the surface by spraying abrasives at high speed, which can quickly remove rust and other dirt, and is suitable for large-scale or large-area processing. For example, sandblasting can be used to clean rust on the surface of ships, metal structures of buildings, large mechanical equipment, etc., significantly improving work efficiency.
Shipyards use sandblasting technology to remove rust from the hull, and the cleaning area of the entire hull can reach several thousand square meters. Through sandblasting, production efficiency has increased by more than 30%, and the cost has been reduced by more than 50% compared with laser rust removal.
Environmental protection and safety
With the increasingly stringent environmental protection policies, sandblasting rust removal technology has also shown great advantages in environmental protection. Compared with traditional chemical rust removers, sandblasting does not involve the use of harmful chemicals, and the emissions are mainly removed from rust and abrasives, which will not pollute the environment.
The dust and noise problems generated during sandblasting can be improved through appropriate equipment control to ensure that the impact on the environment and operators is minimized.
Cost-effectiveness
Compared with laser rust removal, sandblasting equipment has lower procurement and maintenance costs, and less operation and labor input. Therefore, for applications where a large amount of rust removal is required, sandblasting technology provides a more economical solution.
Sandblasting rust removal technology is not only suitable for rust removal on metal surfaces but also for surface roughening, which is beneficial to the adhesion of subsequent coatings. In large steel companies, the use of sandblasting for equipment surface rust removal reduces operating costs by 20% compared with traditional chemical rust removal methods, while equipment procurement and maintenance costs are nearly one-third lower than laser rust removal.
Flexibility and diversity
According to different needs, sandblasting operations can choose different types of abrasives (such as steel sand, aluminum sand, glass beads, etc.), each of which has a different effect on the surface, and can produce a variety of surface effects from smooth to rough.
In addition, the operation mode of sandblasting (such as spray angle, spray pressure, etc.) can be adjusted according to the shape of the metal surface and the thickness of the rust to ensure the best rust removal effect.
Easy to automate and scale
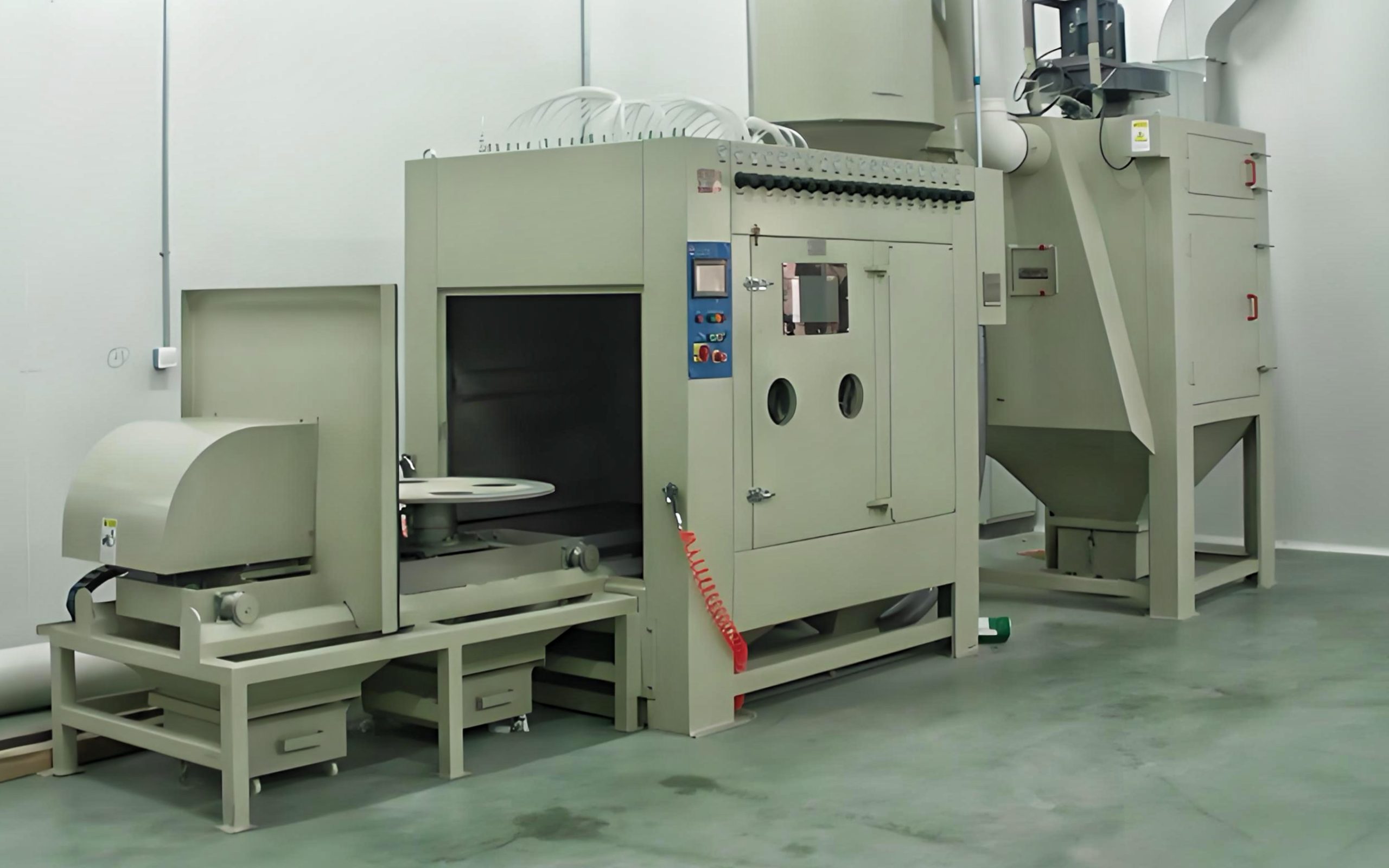
Fully automatic sandblasting machine
The operation process of sandblasting rust removal is relatively simple and easy to automate. Many industrial plants have been equipped with fully automatic sandblasting systems, which not only improve operating efficiency but also reduce the instability caused by manual intervention. With the development of automation technology, the automation level of sandblasting equipment is getting higher and higher, which can realize large-scale production operations, especially suitable for industries that require high-quality and large-scale cleaning, such as precision industry, automobile manufacturing, aerospace, etc.
Comprehensive comparison of laser rust removal and sandblasting rust removal
After analyzing the advantages and disadvantages of laser rust removal and sandblasting rust removal, we can make a comprehensive comparison of the two technologies through the following dimensions to help industry customers make more appropriate choices in different application scenarios.
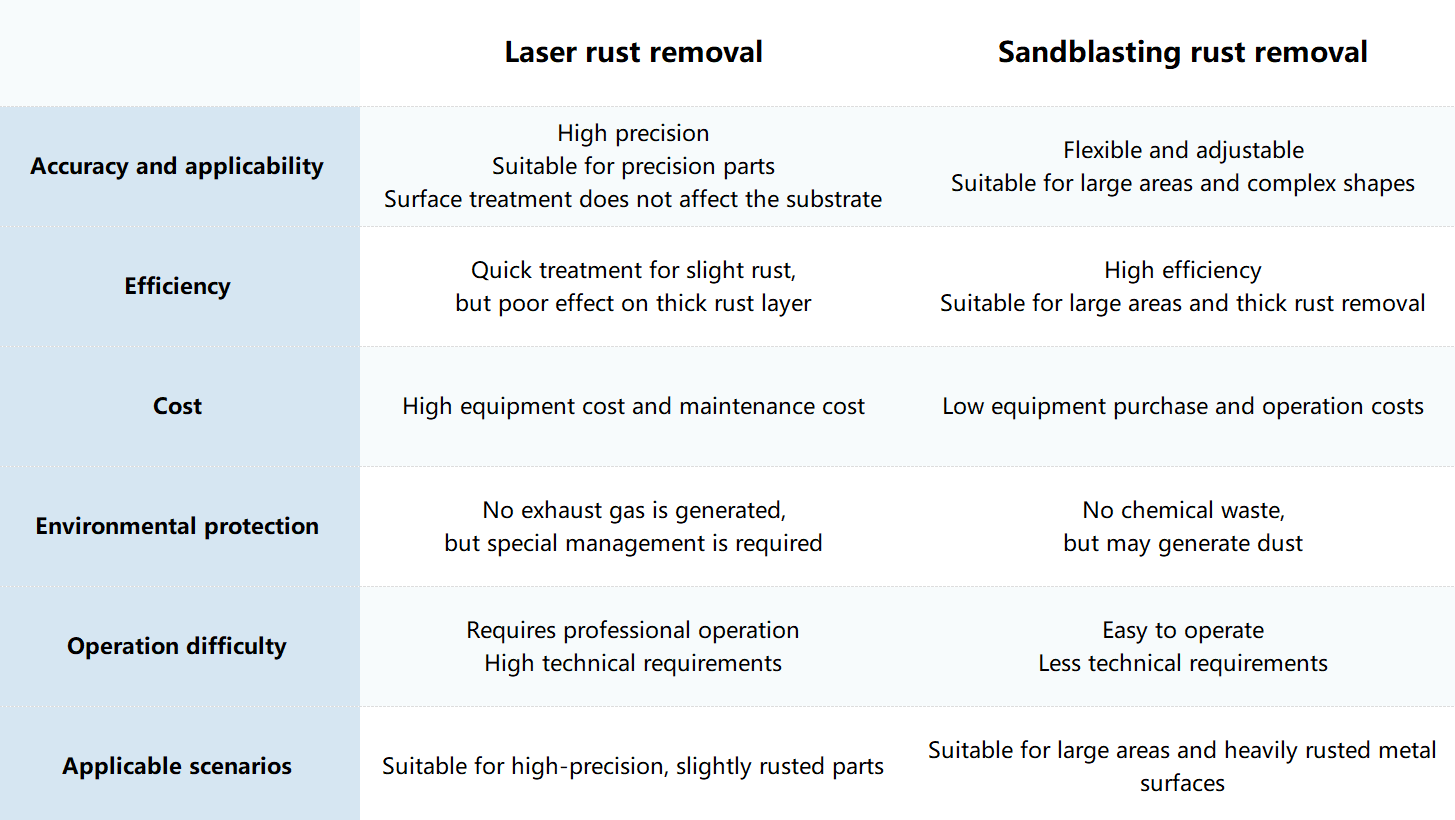
Adaptable workpiece materials
- Laser rust removal: Laser rust removal is suitable for high-precision metal surfaces, especially in those fields with very high requirements for workpiece surfaces, such as electronic equipment, aerospace, precision medical instruments, etc.
It can remove rust on the metal surface without damaging the substrate.
For special metal materials such as titanium alloy, stainless steel, etc., laser rust removal is particularly advantageous.
- Sandblasting rust removal: Sandblasting is suitable for various metal materials, including steel, aluminum alloy, copper, etc. It is especially suitable for rust removal of large-area steel structures, heavy equipment, ships, steel plant equipment, and automotive parts.
Sandblasting can not only remove rust but also provide a specific roughness or texture to the metal surface by selecting different types of abrasives, which helps the subsequent coating to adhere.
Applicable degree of rust
- Laser rust removal: Laser rust removal is more suitable for the removal of slight or local rust, and has limited effect on the removal of thick rust layers, so it is not as effective as sandblasting for deep rust.
Suitable for precision parts with slight rust, such as electronic parts and medical equipment.
- Sandblasting rust removal: Sandblasting rust removal can handle more serious rust, is especially suitable for the removal of thick rust layers and has a good cleaning effect on relatively strong and large metal surfaces
Suitable for large-area rust cleaning of heavy machinery and equipment, building steel structures, ships, etc.
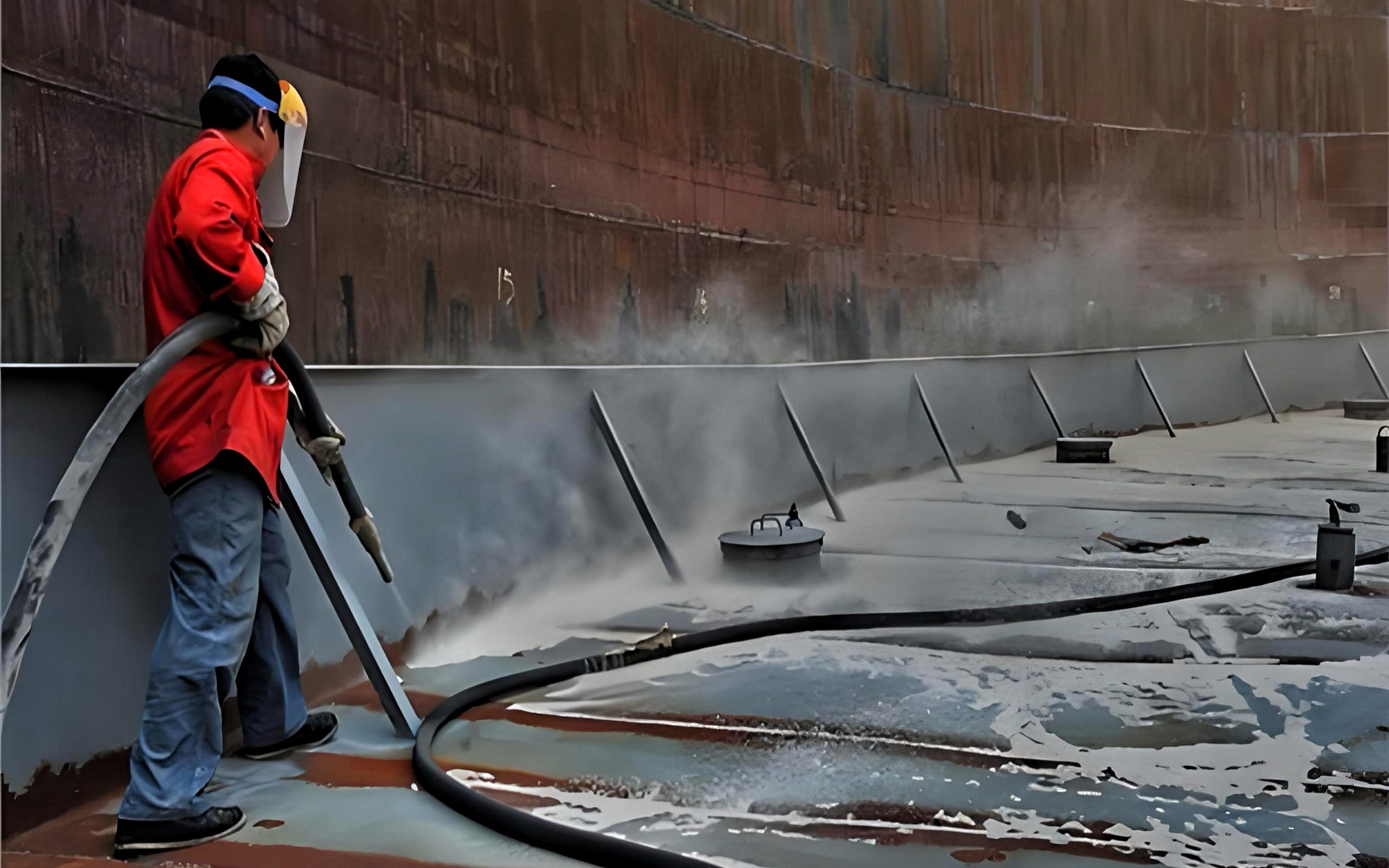
Sandblasting is more suitable for heavy rust layers
Applicable surface effects
- Laser rust removal: Laser rust removal can provide a smoother surface effect, which is suitable for applications that do not need to change the roughness of the metal surface. It can remove rust while trying to maintain the smoothness of the original metal surface and avoid unnecessary roughening.
Applicable to precision fields with extremely high requirements for surface quality, such as high-precision fields such as aerospace and medical equipment.
- Sandblasting rust removal: Sandblasting forms a certain roughness on the metal surface through the impact of abrasives, which helps the adhesion of paint, spray coating, or anti-corrosion layer. Therefore, it is not only used for rust removal, but also can achieve metal surface texture processing, and is often used for parts that require a certain degree of roughness.
Suitable for scenes where the surface needs to be roughened, such as automotive parts, building metal materials, and surface treatment before painting.
Process requirements and complexity
- Laser rust removal: Laser rust removal technology is relatively complex, requiring high-precision laser equipment and operating technology, and operators need to undergo professional training to effectively perform it.
Although laser rust removal is simple to operate, the equipment cost is high and the maintenance cost is also relatively expensive.
In addition, laser rust removal equipment has high environmental requirements and needs to maintain good operating conditions.
- Sandblasting rust removal: The sandblasting rust removal process is relatively simple, with less equipment investment and a low technical threshold.
Sandblasting systems are mostly closed systems, and dust and noise are more obvious during operation, so dust removal and noise control equipment are required.
Economy and efficiency
- Laser rust removal: Laser rust removal is suitable for rust removal of high-value, low-volume metal parts. Although its single-operation efficiency is high, due to the high cost of equipment, laser rust removal is only suitable for precision industrial fields with high precision requirements and low-volume production.
- Sandblasting rust removal: Sandblasting rust removal has significant advantages in efficiency and cost. The purchase cost of sandblasting equipment is relatively low, and it can process large-area surfaces in a short time. It is especially suitable for large-scale, highly repetitive industries such as steel, construction, and shipbuilding.
Through the comparison in this article, we can conclude that the selection of suitable rust removal technology should be determined according to specific application requirements, workpiece types, and surface requirements. For workpieces that require high precision and less rust, laser rust removal is the best choice; while for large-scale production and heavy rust metal parts rust removal, sandblasting rust removal provides a more efficient and economical solution.
In actual production, combining the advantages of the two technologies, flexibly selecting and applying them according to the requirements of different workpieces and rust removal tasks will help improve rust removal effects and production efficiency, reduce costs, and promote the development and innovation of rust removal technology in various industries.
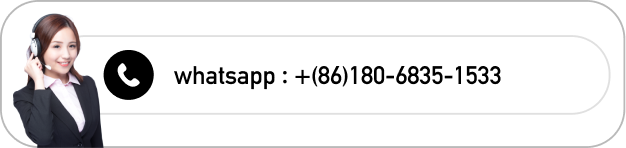