9月 27, 2024
サンドブラスト工程は広く使用されている表面処理技術であり、主に金属、プラスチック、セラミックなどのさまざまな材料の洗浄、バリ取り、研削、研磨に使用されます。工業化の加速に伴い、製造業におけるサンドブラスト工程の位置づけは、特に航空宇宙、自動車、エレクトロニクス、医療などの分野でますます重要になっている。しかし、製品の色差、光沢、粗さの不一致など、サンドブラスト工程で直面するいくつかの問題は、製品の外観品質および市場競争力に深刻な影響を及ぼしている。
色差とは、同じロットの製品間で明らかに色が異なることを指す。この現象は製品の美観に影響を与えるだけでなく、顧客の不満や返品につながる可能性がある。光沢の不一致は、視覚効果において製品をプロフェッショナルでないように見せ、不均一な粗さは、特に表面品質に対する要求が厳しい業界において、製品の性能に影響を与える可能性がある。これらの状況は非常に深刻である。したがって、これらの問題の根本原因を理解し、解決策を探ることは、現在のサンドブラスト工程を改善するための重要なテーマとなっている。
本稿では、このような「"arrow "の "arrow"」について深く掘り下げてみたい。 色差、光沢、粗さの不一致の原因 サンドブラスト工程における問題を分析し、これらの問題に対処する現在の企業の成功事例を分析し、これらの問題を完全に克服できない場合に採用される緩和策を分析する。体系的な分析と研究を通じて、関連企業に実用的な提案と参考資料を提供し、サンドブラスト工程の継続的な改善と革新を促進することを目的としています。
色差問題の原因
色の違いは、サンドブラスト工程、特に美的要求の高い製品でよく見られる問題です。色差の原因を理解することは、サンドブラスト効果と製品の品質を向上させる上で極めて重要です。
原材料の違い
ロットや供給元が異なる材料には色の違いがある場合があり、これは色差問題の主な原因の一つである。例えば、同じ原料であっても、製造工程、配合、保管条件などが異なると、原料の色に影響を与えることがある。また、添加物の種類や割合など、原料の組成が変わることでも、最終製品の色に違いが生じることがある。従って、原料の産地と組成の均一性を確保することは、色の違いを減らすために極めて重要である。
サンドブラスト媒体の選択
サンドブラスト媒体の種類と特性は、サンドブラスト後の表面色に直接影響します。たとえば、酸化アルミニウムブラスト媒体を使用する場合とセラミックブラスト媒体を使用する場合では、表面の光沢および色が異なることがあります。媒体の硬度、形状、粒子径は、サンドブラスト中の摩擦と表面粗さに影響し、それによって色の均一性に影響します。したがって、サンドブラスト媒体を選択する際には、最終的な色への影響を十分に考慮する必要があります。
プロセスパラメータの変更
ブラスト圧力、距離、角度などのブラスト工程パラメータの変化も、ブラスト後の表面効果に大きく影響します。ブラスト圧力が高すぎても低すぎても、表面処理が不均一になり、その結果、色の違いが生じることがあります。たとえば、ブラスト距離が近すぎると、一部の領域で過剰な摩耗を引き起こす可能性があります。 (これについては以前にも書いた、 クリックで表示) の場合、ブラスト媒体の表面への衝撃力が異なるため、一貫性のない色になる可能性があります。したがって、標準化されたブラスト パラメータを設定することが非常に重要です。
環境要因
湿度、温度、光などの環境要因も、ブラスト工程における色の違いに影響します。高湿度環境では、ブラスト媒体の吸湿性が増加するため、その物理的特性が変化し、ブラスト効果に影響を及ぼす可能性があります。さらに、温度変化により材料の熱膨張が生じ、それによって色性能が変化することがあります。照明条件の違いも視覚的な色判断に影響することがあるため、ブラスト工程では環境要因をできる限り制御して、一貫した処理効果を維持する必要があります。
以下では、正しい方法を選択することの重要性を理解していただくために、さまざまなブラスト方法(ドライサンディングやウェットサンディングなど)の効果と、色の違いや光沢への影響を示します。
以下では、正しい方法を選択することの重要性を理解していただくために、さまざまなブラスト方法(ドライサンディングやウェットサンディングなど)の効果と、色の違いや光沢への影響を示します。
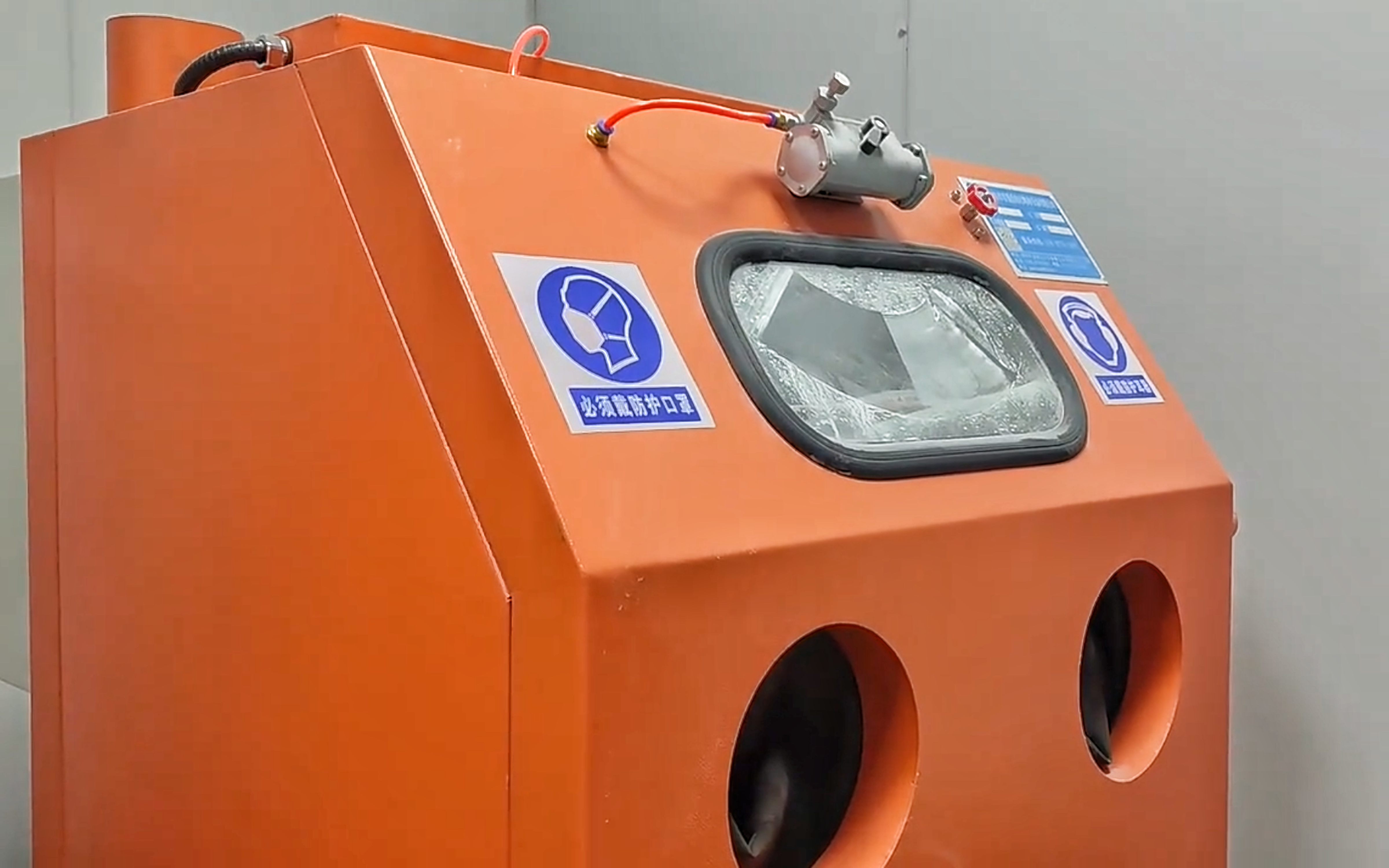
湿式サンドブラスト機
サンドブラスト法の概要
ドライサンドブラスト
- 特徴さまざまな材料に適した乾式サンドブラスト媒体を使用。
- 利点バリや汚れの除去効果に優れ、金属ワークに適している。
- デメリット表面粗さが大きくなり、色差が発生しやすくなる。
ウェットサンドブラスト
- 特徴サンドブラスト媒体に水を混ぜて、粉塵と飛散を抑える。
- 利点表面仕上げの要求が高いワークに適しており、粗さを効果的に制御できる。
- デメリット装置のメンテナンスと処理がより複雑で、乾燥時間が長くなる。
光沢と粗さ
- ドライサンドブラスト
使用するメディアが乾いているため、サンドブラスト中に不均一な摩耗が発生し、特に滑らかな表面を扱う場合に色の違いが生じることがあります。
色差を必要としないが、需要の高い用途で後処理が必要な場合に適している。
- ウェットサンドブラスト
乾式サンドブラスト中に発生する静電気は、水の介在によって低減され、ワークピースの表面により均一に分布させることができるため、色差が発生する可能性が低くなります。
医療機器や電子部品など、高い一貫性が要求される製品に適しています。
色差効果
- ドライサンドブラスト
摩耗力が大きいため、表面粗さが大きくなり、光沢が低下することがある。
光沢のある装飾部品など、平滑な表面処理が必要なワークには適さない。
- ウェットサンドブラスト
媒体の分散を抑え、表面の濡れ性を向上させることで、サンドブラスト後も良好な光沢と低い粗さを維持することができる。
ウェットサンドブラストは、高い光沢と低い粗さを必要とする産業で優れた性能を発揮します。
適用場面
- ドライサンドブラスト
金属表面の洗浄とバリ取りに適しており、重工業でよく使用される。
外観の要求が厳しい製品には適さない。
- ウェットサンドブラスト
精密部品、美術品、医療機器など、表面品質への要求が高い製品に適している。
ワークピースの表面仕上げと均一性に対する要求が高い産業に適しています。
要約すると、高い光沢と低い粗さが必要な製品の場合、ウェットサンドブラストの方が利点が多い可能性があり、ドライサンドブラストは効率とコストで一定の利点があります。特定の製品要件および業界標準に従って適切なサンドブラスト方法を選択することが極めて重要です。
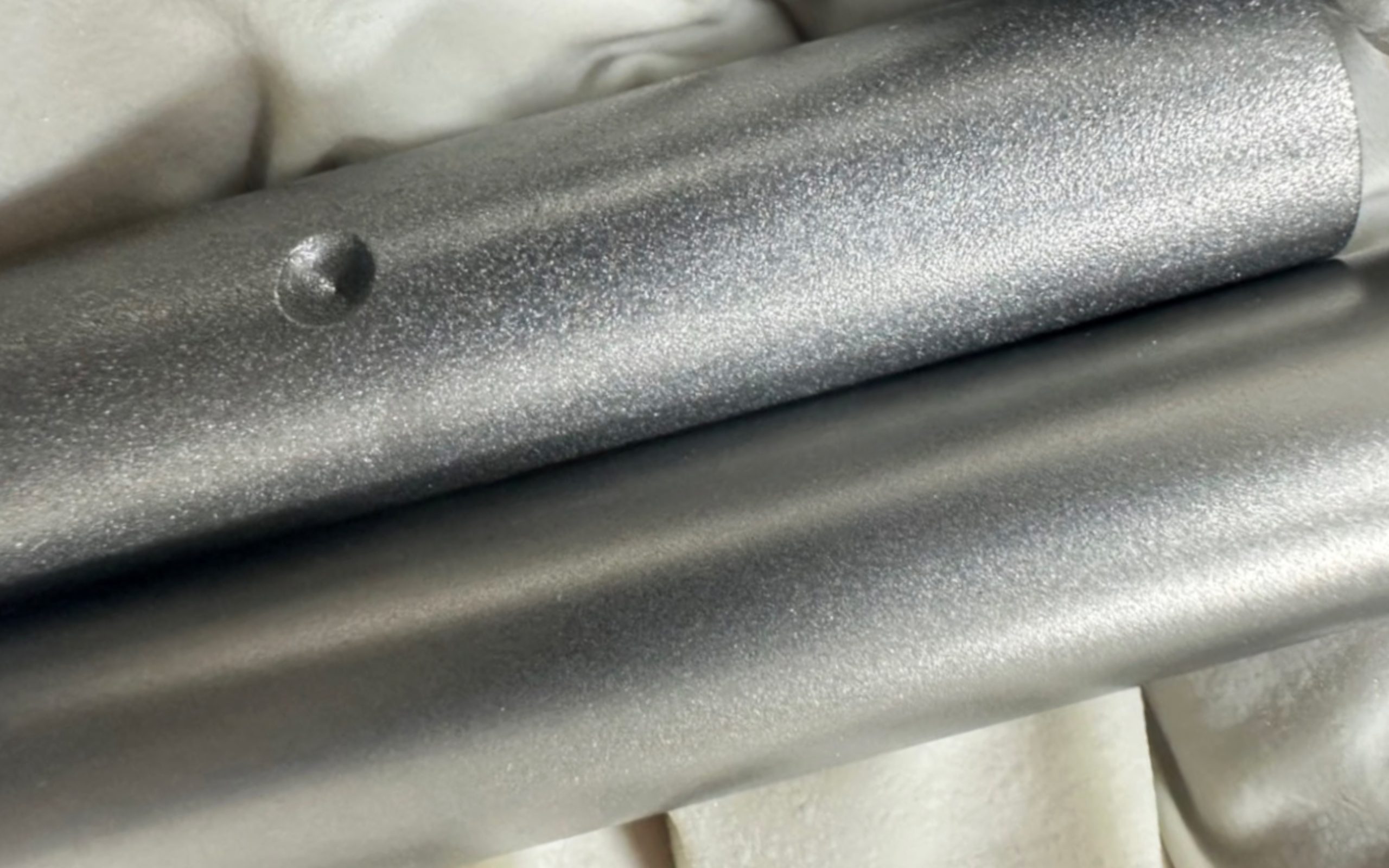
同じワークピースに対する異なるメディアの影響
粗さが一定しない原因
不均一な粗さは、製品の美観に影響を与えるだけでなく、特に精密部品を必要とする用途では、その機能性にも影響を与える可能性があります。粗さが一定しない主な原因は以下の通りです。
ブラスト媒体の特性
ブラスト媒体の硬度、形状、粒径は粗さに直接影響します。たとえば、角のあるブラスト媒体を使用すると表面粗さが高くなることがありますが、球状の媒体を使用すると滑らかな表面が得られやすくなります。したがって、ブラスト媒体を選択する場合は、その特性が表面粗さに及ぼす影響を考慮する必要があります。
ブラストプロセスの矛盾
ブラスト距離、圧力の変動、不安定な媒体の流れなど、ブラスト工程における一貫性の欠如はすべて、粗さのばらつきにつながります。均一な粗さを達成するには、ブラスト工程の一貫性を維持することが不可欠です。
設備のメンテナンス状況
ブラスト装置の保守状況もブラスト効果に影響します。装置の老朽化、摩耗、故障によりブラスト結果が不安定になり、粗さが一定しない場合があります。そのため、サンドブラスト装置の定期的な保守点検は、加工品質を確保するための重要な対策です。
既存企業はこれらの問題をどのように克服しているか
サンドブラスト工程では、色差、光沢度、粗さの不均一性などの課題があるものの、多くの企業がこれらの問題を克服するために一連の効果的な対策を講じてきた。
材料管理
統一された供給元から高品質の原料を選択することは、サンドブラスト効果の一貫性を確保するための基礎である。企業は信頼できるサプライヤーと協力関係を築き、原材料の品質と安定性を確保する必要があります。これにより、材料の違いによる問題を減らすだけでなく、最終製品の品質を向上させることができる。さらに、原材料が生産要件を満たしていることを確認するための厳格な試験と検証も、企業が注意を払わなければならない関連事項です。
標準化された生産
サンドブラスト効果の一貫性を高めるには、厳格な工程パラメーターと作業手順を確立することが重要です。企業は、サンドブラスト媒体の選択、サンドブラスト圧力、サンドブラスト距離、ノズルの角度など、サンドブラスト工程のすべてのリンクを明確にする必要があります。また、作業マニュアルを標準化することで、作業者一人ひとりを指導・標準化し、各サンドブラスト作業の一貫性を確保することで、人的要因による品質のばらつきを抑えることができます。
設備のアップグレード
高度なサンドブラスト装置を使用することで、サンドブラスト効果の一貫性を大幅に向上させることができます。最新のサンドブラスト設備は通常、サンドブラストパラメーターを正確に調整し、サンドブラスト工程中のさまざまな指標をリアルタイムで監視できるインテリジェント制御システムを備えている。企業は生産効率と製品品質を向上させるため、設備を定期的に評価、更新し、生産ニーズに合った新技術を採用する必要があります。
社員教育
オペレータの体系的な訓練は、プロセスの安定性を確保するための重要な対策である。企業は定期的に研修コースを実施し、従業員がサンドブラストの基本原理、装置の操作方法、一般的な問題の解決策を理解できるようにする必要があります。従業員のプロ意識を向上させることにより、企業は操作ミスを減らし、サンドブラスト工程の安定性を向上させ、製品品質の一貫性を確保することができる。
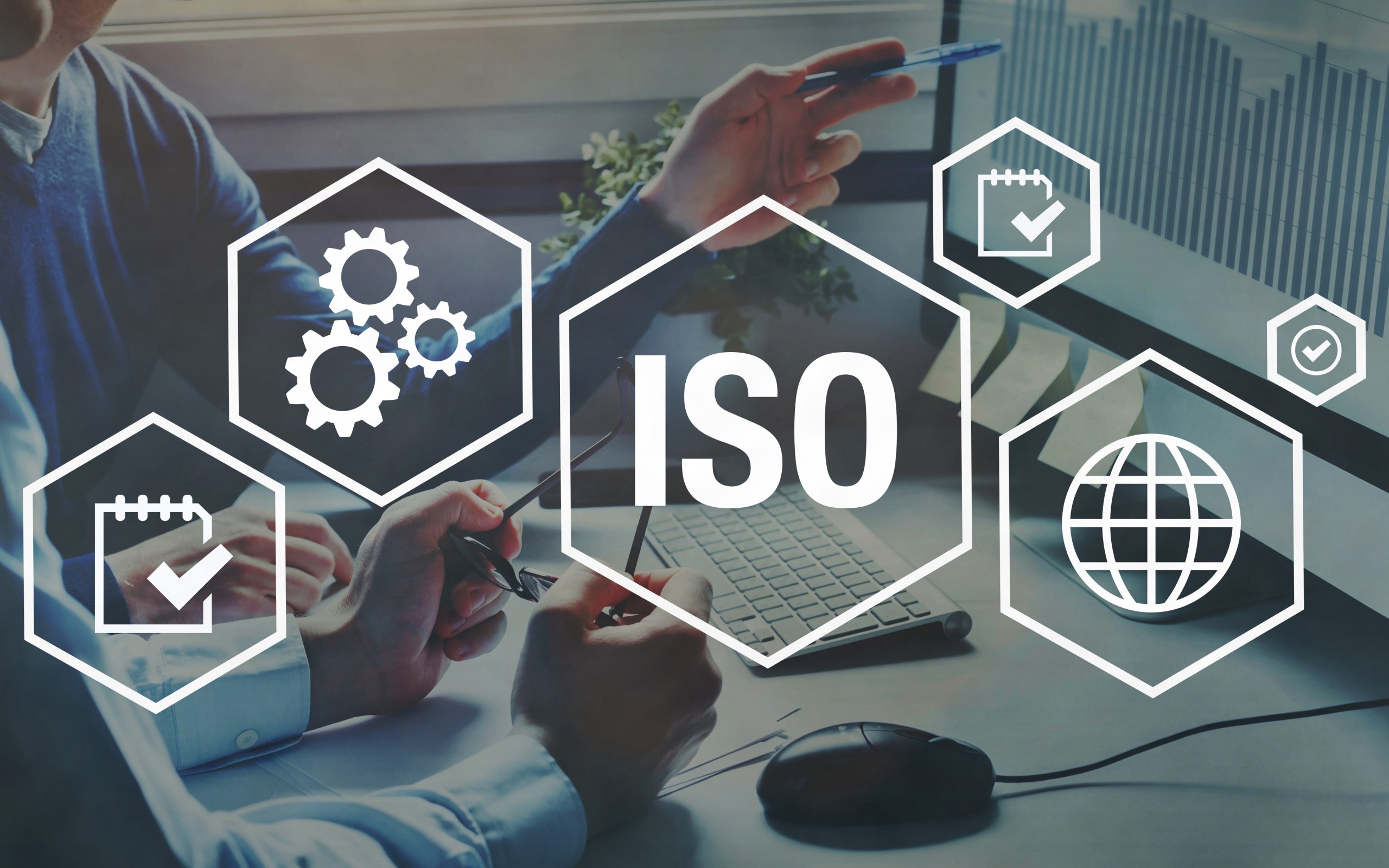
軽減措置
上記の対策を講じても、サンドブラスト工程で完全に除去できない色差、光沢度、粗さの不一致が生じる場合があります。この場合、企業は以下の緩和策を検討することができる。
色差補正技術
サンドブラスト処理されたワークピースの場合、その後のコーティングや着色処理によって色差を修正することができる。適切なコーティングや染色技術を適用することで、色差の問題をある程度カバーまたは改善することができる。これにより、製品の外観品質が向上するだけでなく、耐食性と耐摩耗性が強化され、製品の耐用年数が延長される。
プロセスパラメーターの最適化
サンドブラストパラメーターを常に調整することで、企業は色の違いや不一致を最小限に抑えることができます。たとえば、サンドブラスト効果を最適化するために、サンドブラスト工程中の圧力、速度、ノズルの角度を改良する。これらの調整を実施した後、企業は継続的な品質検査を行い、最終製品の品質が基準を満たしていることを確認する必要があります。
定期検査
厳格な品質検査メカニズムを確立することは、サンドブラスト工程における問題を迅速に検出し修正することに役立ちます。企業は、サンドブラスト前、サンドブラスト中、サンドブラスト後に複数レベルの品質検査を実施し、各ワークピースが指定された品質基準を満たしていることを確認できます。リアルタイムの監視とデータ分析により、企業は潜在的な問題を迅速に特定し、必要な調整と修正を行うことができます。
サンドブラスト工程で色差、光沢、粗さの不一致などの問題に直面した場合、企業はさまざまな方法で克服し緩和することができます。材料管理、標準化された生産、設備のアップグレード、従業員のトレーニングなど、企業は継続的な最適化の過程で製品の品質を向上させることができます。これらの問題を完全に取り除くことができなくても、色差補正技術、工程パラメータの最適化、定期的な検査メカニズムの確立などの対策により、品質の変動を効果的に低減し、市場競争における製品の優位性を確保することができる。継続的な改善を通じて、企業は熾烈な市場環境において競争力を維持し、顧客の信頼と満足を勝ち取ることができる。
フィルター