Aluminio frente a acero: Estrategias de preparación de superficies para componentes de vehículos eléctricos
14 de febrero de 2025
Los vehículos eléctricos siguen evolucionando, aluminio y acero desempeñan un papel crucial en la fabricación de componentes ligeros y duraderos. La elección del estrategia de preparación de superficies es esencial para optimizar el rendimiento, la longevidad y la adherencia en los revestimientos.

¿Por qué son importantes el aluminio y el acero en la fabricación de vehículos eléctricos?
Ambos materiales se utilizan en distintos componentes de vehículos eléctricos debido a sus distintas propiedades:
Componente | Material común | Razón |
---|---|---|
Carcasas para baterías | Aluminio | Ligereza, disipación del calor |
Chasis y bastidor | Acero | Gran solidez, resistencia a los choques |
Componentes de suspensión | Aluminio/acero | Equilibrio entre peso y fuerza |
Carcasa del motor | Aluminio | Resistencia a la corrosión, conductividad térmica |
Refuerzos estructurales | Acero | Resistencia a los golpes |
Comprender las aplicaciones de estos materiales ayuda a seleccionar los métodos de tratamiento de superficies adecuados para mejorar su durabilidad y rendimiento.
Desafíos de la preparación de superficies para componentes de vehículos eléctricos
Aluminio (ligero pero reactivo)
Forma una capa de óxido que dificulta la adherencia del revestimiento
Más blando que el acero, requiere técnicas de granallado más suaves
Propenso a la corrosión galvánica en contacto con metales distintos
Acero (resistente pero propenso a la corrosión)
Susceptible a la oxidación sin la protección adecuada
Requiere un chorreado agresivo para eliminar la cascarilla de laminación y los contaminantes.
Necesita revestimientos adicionales para una mayor longevidad
Estrategias optimizadas de preparación de superficies
Para componentes de aluminio:
1) Medios de voladura:
- Óxido de aluminio fino - Elimina las capas de óxido sin erosión excesiva
- Cuentas de cerámica - Proporciona un acabado superficial uniforme
2)Pretratamiento:
- Grabado químico - Mejora la adherencia antes de pintar
- Tratamiento con plasma - Limpia y activa la superficie sin dañarla
3)Soluciones de revestimiento:
- Anodizado - Crea una capa protectora resistente a la corrosión
- Recubrimiento en polvo - Añade durabilidad y atractivo visual
Para componentes de acero:
1)Medios de voladura:
- Granate o arena de acero - Elimina eficazmente el óxido y la cascarilla de laminación
- Granallado - Aumenta la resistencia a la fatiga de las piezas estructurales
2) Pretratamiento:
- Fosfatado - Mejora la protección contra la corrosión antes del revestimiento
- Limpieza con disolventes - Elimina el aceite y los contaminantes
3) Soluciones de revestimiento:
- Galvanización - El revestimiento de zinc evita la formación de óxido
- Imprimación epoxi - Protege contra entornos agresivos

Innovaciones del sector y tendencias futuras
Ventajas de las perlas de circonio
Nanorrevestimientos para una mayor protección:
Emergentes nanorecubrimientos cerámicos proporcionan una resistencia superior a la corrosión, tanto para el aluminio como para el acero, sin añadir peso.
Limpieza láser como alternativa al chorreado:
Nuevo tecnología de ablación láser ofrece un método no abrasivo para eliminar los contaminantes, mejorando la adherencia del revestimiento con un impacto medioambiental mínimo.
Ingeniería de superficies de materiales híbridos:
Combinación de recubrimientos poliméricos avanzados con las técnicas tradicionales de anodizado y galvanizado prolonga la vida útil de los componentes de los VE.
Elegir el método adecuado para fabricar VE
Aluminio: Necesita chorreado suave, tratamientos químicos y anodizado para aumentar la durabilidad.
Acero: Requiere granallado agresivo, fosfatado y revestimientos protectores para evitar la oxidación.
Seleccionar el óptimo estrategia de preparación de superficies garantiza que los componentes EV permanezcan ligero, duradero y resistente a la corrosión, mejorar el rendimiento a largo plazo.
¿Le gustaría recibir casos prácticos o una comparación más profunda de los efectos de la rugosidad superficial sobre la adherencia del revestimiento?
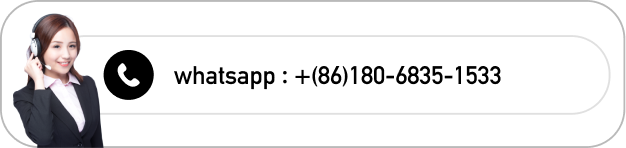