¿Por qué los medios de desbarbado criogénicos son el mejor método de desbarbado?
20 de septiembre de 2024
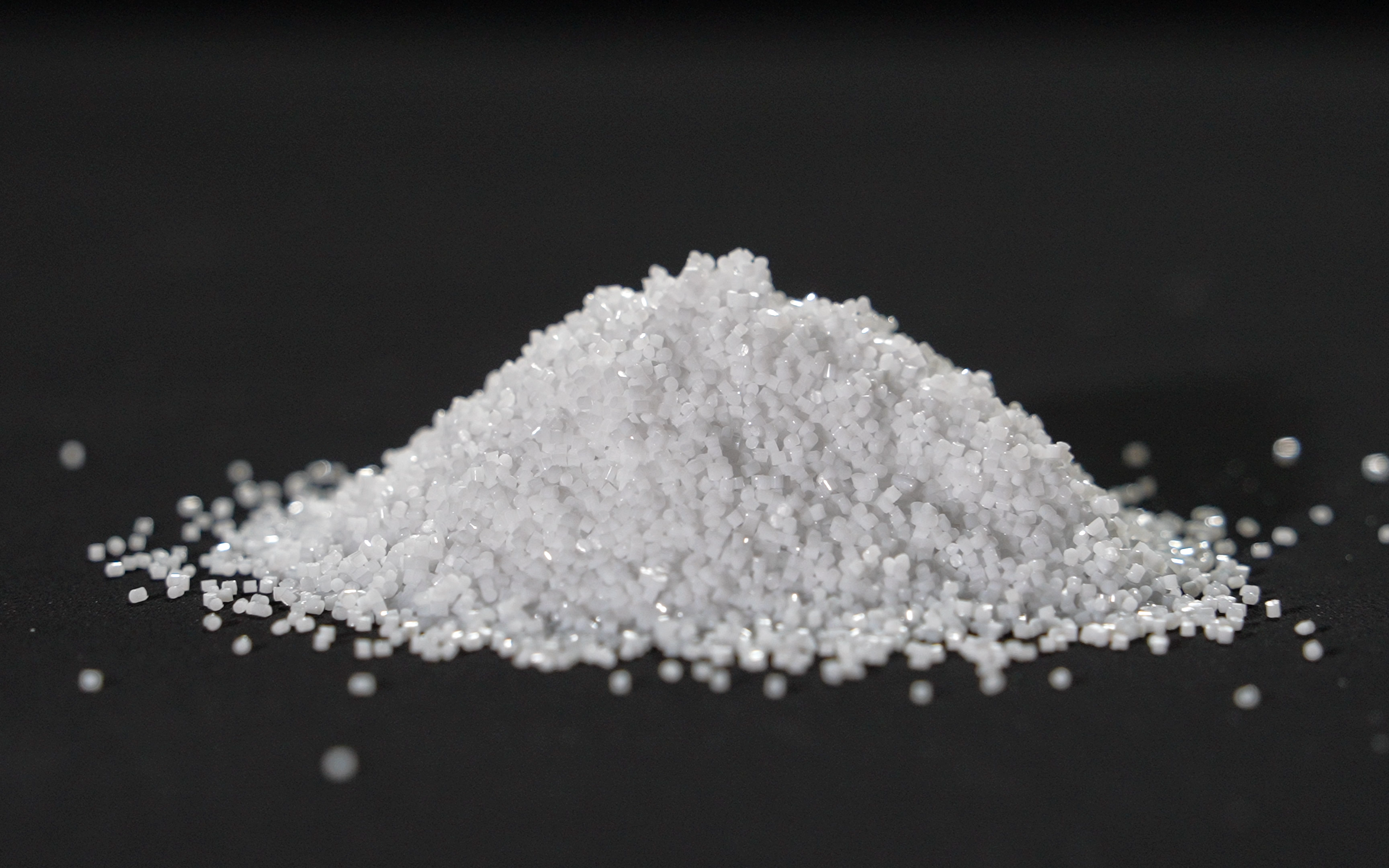
El desbarbado o desbarbado es una parte vital del proceso de fabricación industrial, especialmente para piezas de precisión. Ya se trate de productos de plástico moldeados por inyección, piezas de caucho o piezas de metal fundido, es inevitable que aparezcan pequeñas rebabas durante el proceso de producción, lo que afecta al acabado de la superficie y a la precisión del producto final. En los últimos años, la tecnología de desbarbado criogénico se ha convertido gradualmente en la primera opción para diversas industrias en términos de eliminación de rebabas debido a sus ventajas de alta eficiencia, precisión y protección del medio ambiente. Como uno de los factores clave de este proceso, la selección de los medios criogénicos de desbarbado es especialmente importante. Este artículo explorará en detalle por qué los medios criogénicos de desbarbado son la elección correcta y analizará sus ventajas únicas comparándolos con los métodos tradicionales de desbarbado.
Definición y principio de funcionamiento
El desbarbado criogénico es un proceso que utiliza un entorno de baja temperatura para enfriar y fragilizar rápidamente las rebabas de la superficie de la pieza y, a continuación, eliminarlas con precisión mediante acción mecánica. Este método es especialmente adecuado para materiales blandos como el caucho y los plásticos. Puede eliminar eficazmente las rebabas sin dañar la pieza, y también puede mejorar la eficacia de la producción y la calidad del producto.
Los pasos específicos se dividen en tres etapas principales:
- Refrigeración: Ponga la pieza de trabajo en un ambiente de baja temperatura, generalmente usando nitrógeno líquido, y enfríe rápidamente la pieza de trabajo a -150℃, de modo que las rebabas en la superficie de la pieza de trabajo se vuelvan quebradizas.
- Fresas de endurecimiento: En condiciones de baja temperatura, la parte de la rebaba se vuelve frágil, mientras que la parte principal de la pieza sigue siendo relativamente dura. Las rebabas son más frágiles debido a las diferentes propiedades de los materiales de las rebabas y las piezas.
- Extracción mecánica: Mediante vibración mecánica o un ligero impacto físico, las rebabas quebradizas se eliminan fácilmente, y la superficie de la pieza queda lisa e intacta.
Composición y características
- Composición del material(Click aquí para ver los detalles del producto)
El medio de desbarbado criogénico está hecho principalmente de poliamida 6 (nailon 6). La forma principal es cilíndrica o hexaédrica, y hay una variedad de colores para elegir, incluyendo blanco lechoso translúcido, amarillo, rojo y verde. Se puede elegir según el color de la pieza pretratada, de los cuales el blanco lechoso y el rojo son los dos más utilizados. Durante el funcionamiento, estos diferentes colores pueden facilitar a los operarios la identificación y el manejo en diferentes escenarios de aplicación.
- Principales propiedades físicas
- Resistencia a bajas temperaturas
Una de las propiedades destacables de la poliamida 6 es su elevada tenacidad a temperaturas muy bajas. Incluso a temperaturas tan bajas como -150°C, el material mantiene una estructura resistente, lo que garantiza que las partículas de desbarbado no se rompan debido a las bajas temperaturas. Esto la convierte en un medio de desbarbado criogénico ideal, especialmente cuando se desbarban materiales blandos (como caucho y plásticos blandos), que puede evitar dañar la pieza principal y eliminar eficazmente las rebabas quebradizas.
- Gran resistencia al desgaste
Estas partículas de nylon poliamida 6 están cuidadosamente diseñadas para tener una excelente resistencia al desgaste. Tras un uso prolongado, aún pueden mantener su forma y efecto, y tienen una larga vida útil, lo que reduce la frecuencia de sustitución y los costes de producción. El plástico es ligero y más rentable en el transporte, lo que resulta más económico a largo plazo.
- Ligereza y baja dureza
Al tratarse de un medio plástico, es relativamente ligero y tiene una dureza baja, lo que significa que incluso la superficie de piezas sensibles y de alta precisión no sufrirá daños durante el proceso de desbarbado. Garantiza que la pieza mantenga su superficie lisa original sin crear nuevos defectos debido al impacto de partículas de alta dureza.
- Identificación del color
Los distintos colores de los soportes pueden distinguirse según sus usos y aplicaciones, lo que no sólo es fácil de identificar para los operarios, sino que también permite un control más eficaz de los procesos de producción.
- Propiedades químicas
- Resistencia química
La poliamida 6 tiene una buena resistencia química. Incluso en un entorno químicamente muy activo, no se corroe fácilmente con sustancias como ácidos y álcalis, lo que significa que puede utilizarse durante mucho tiempo en diversos entornos industriales sin deteriorarse por el contacto con productos químicos.
- Estabilidad y no toxicidad
El medio criogénico de desbarbado está fabricado con material de nailon no tóxico e inocuo, que no produce gases ni residuos nocivos cuando se utiliza, y cumple los requisitos de protección medioambiental. Esto hace que no solo sea seguro para los operarios, sino que también tenga un menor impacto en el medio ambiente, especialmente adecuado para la demanda de producción sostenible de la industria moderna.
- Alta resistencia a la presión
Durante el proceso de desbarbado, la presión de contacto entre la pieza de trabajo y el medio es grande, pero debido a las propiedades del material de nylon poliamida 6, tiene buena resistencia a la presión y no se deforma ni daña bajo alta presión, asegurando la continuidad y estabilidad del proceso de desbarbado.
- Beneficios económicos y costes de uso a largo plazo
- Relación coste-eficacia
Gracias a sus características de resistencia al desgaste, durabilidad y reciclabilidad, puede reducir en gran medida el coste de los consumibles en el proceso de producción. La inversión única puede soportar el uso a largo plazo, lo que resulta significativamente rentable en comparación con los medios de desbarbado tradicionales.
- Reciclado y reutilización
El material tiene un buen rendimiento de reciclado. Mediante una limpieza y un reprocesado razonables, estas partículas de desbarbado pueden reutilizarse, reduciendo aún más el consumo de material en la línea de producción.
- Protección del medio ambiente
El producto cumple las normas modernas de protección del medio ambiente y reduce la generación de residuos nocivos. Dado que su proceso de uso no implica la aplicación de productos químicos, tiene escaso impacto en el medio ambiente y es muy adecuado para industrias con estrictos requisitos medioambientales.
Comparación con los métodos tradicionales de desbarbado
Los métodos tradicionales de desbarbado incluyen principalmente el desbarbado mecánico, el desbarbado químico y el desbarbado térmico. Cada método tiene sus ventajas e inconvenientes:
- Desbarbado mecánico se basa en el rectificado físico, que es adecuado para materiales metálicos, pero es fácil dañar la superficie de la pieza cuando se procesan materiales blandos.
- Desbarbado químico utiliza agentes químicos para disolver las rebabas, lo que resulta adecuado para la producción en serie, pero puede contaminar el medio ambiente.
- Desbarbado térmico Elimina las rebabas mediante alta temperatura, pero tiene requisitos estrictos sobre el material de la pieza y es fácil que afecte a la estructura del material.
Estos métodos se basan principalmente en fuerzas elevadas y cambios de temperatura, que pueden causar desgaste, deformación e incluso daños térmicos en la superficie de la pieza. Los métodos mecánicos suelen carecer de precisión debido a la necesidad de un funcionamiento manual o semiautomático, y es difícil tratar rebabas con formas complejas o estructuras diminutas. Aunque el desbarbado químico puede eliminar algunas rebabas pequeñas, es fácil que cause residuos químicos, requiere un tratamiento posterior de la superficie de la pieza y es perjudicial para algunos materiales.
(Hemos escrito un artículo más detallado anteriormente, puede hacer clic en aquí para leerlo.)
En cambio, el proceso de desbarbado criogénico presenta importantes ventajas en cuanto a precisión, no destructividad y eficacia.
- Precisión y no destructividad
En un entorno de baja temperatura, las rebabas se vuelven rápidamente quebradizas, mientras que el material principal de la pieza mantiene su dureza original. Esta característica permite que el proceso de desbarbado criogénico elimine las rebabas con extrema precisión sin dañar la superficie de la pieza. Es especialmente adecuado para piezas con elevados requisitos de acabado superficial, como piezas de precisión moldeadas por inyección o piezas aeroespaciales.
- Alta eficacia
El proceso de desbarbado criogénico es adecuado para equipos automatizados y puede procesar un gran número de piezas en menos tiempo, lo que agiliza todo el proceso y mejora significativamente la eficacia de la producción. Además, gracias a la durabilidad de las partículas del medio a baja temperatura, se reduce la frecuencia de sustitución, lo que mejora aún más la continuidad de la producción.
- Protección del medio ambiente y seguridad
El proceso no utiliza productos químicos nocivos, lo que evita la generación de residuos químicos. En comparación con los métodos tradicionales de desbarbado químico o térmico, el desbarbado criogénico es respetuoso con el medio ambiente y más seguro para los operarios. Además, el entorno de baja temperatura también puede suprimir la generación de electricidad estática y chispas, reduciendo los posibles riesgos de seguridad.
- Amplia gama de materiales aplicables
El proceso de desbarbado criogénico no sólo es adecuado para las rebabas de productos de plástico y caucho, sino que también puede eliminar eficazmente las rebabas de algunas piezas de metal blando. Esta amplia aplicabilidad lo convierte en una herramienta importante en diversos campos industriales, especialmente en la fabricación de precisión y en ocasiones de gran demanda.

Comparación con nylon poliamida medios de desbarbado
Similitudes:
- Los componentes principales de los dos son los mismos, ambos son partículas de chorro de arena hechas de poliamida 6 (nailon 6), y las formas también son cilíndricas o hexaédricas, y las propiedades físicas y químicas son básicamente las mismas.
- Ambos pueden adaptarse a entornos de baja temperatura y mantener un buen efecto de desbarbado a baja temperatura, especialmente adecuado para el procesamiento de caucho, piezas moldeadas por inyección y piezas de fundición de metal.
Aunque la composición y las prestaciones de ambos son las mismas, las diferencias en sus aplicaciones prácticas se reflejan principalmente en los siguientes puntos:
- Equipo aplicable
Los medios de desbarbado criogénicos suelen utilizarse junto con la máquina de crioacabado de nitrógeno líquido, mientras que los medios de desbarbado de poliamida de nailon son más adecuados para el proceso de desbarbado a temperatura normal, y los tipos de equipos utilizados son diferentes.
- Escenario de aplicación
Los medios de desbarbado criogénicos son más adecuados para procesar materiales blandos, como productos de caucho y plásticos, y son especialmente comunes en el procesamiento de termoplásticos y plásticos termoestables, como componentes de dispositivos médicos, juntas de caucho de precisión, etc. Los medios de desbarbado de nylon y poliamida son más adecuados para eliminar rebabas en la superficie de metales y materiales duros, como acero inoxidable, aleaciones de aluminio, cobre, titanio, etc., y también pueden utilizarse para el tratamiento superficial de algunos plásticos duros.
- Temperatura de funcionamiento
Los medios de desbarbado criogénicos deben llevarse a cabo en un entorno de temperatura extremadamente baja, y su funcionamiento es más complicado, mientras que los medios de desbarbado de poliamida de nailon no requieren equipos de refrigeración y su funcionamiento es relativamente sencillo.
Industria de aplicación
- Aeroespacial
- Antecedentes: La industria aeroespacial tiene unos requisitos extremadamente estrictos en cuanto a la precisión de las piezas. Cada pieza debe cumplir unas normas de altísima calidad para funcionar correctamente en entornos adversos como alta temperatura, alta presión y fuertes vibraciones. El desbarbado de piezas como componentes de motores de aviones, carcasas de aviones y sistemas de transmisión es un paso clave para garantizar la seguridad de los vuelos y aumentar la vida útil de las piezas. Los métodos tradicionales de desbarbado pueden causar pequeños daños en la superficie de las piezas o deformaciones del material, lo que resulta inaceptable para la industria aeroespacial.
- Efecto: El proceso de desbarbado criogénico utiliza el efecto refrigerante del nitrógeno líquido para que las rebabas de la superficie de las piezas se vuelvan quebradizas y se desprendan rápidamente sin afectar a la precisión geométrica ni a la resistencia estructural de las piezas. Este método es especialmente adecuado para procesar piezas metálicas de precisión, materiales compuestos y aleaciones de alta resistencia. No sólo mejora el acabado superficial de las piezas, sino que también reduce significativamente el riesgo de daños en la microestructura. Gracias a la tecnología de desbarbado criogénico, los fabricantes del sector aeroespacial pueden controlar más eficazmente la calidad del producto y garantizar sus prestaciones de seguridad.
- Fabricación de automóviles
- Antecedentes: La industria del automóvil requiere la producción en serie de piezas de precisión, especialmente en el proceso de fabricación de motores, juntas y sistemas de control electrónico, que tienen unos requisitos de precisión y funcionalidad extremadamente altos. Por ejemplo, los cilindros, juntas y diversas piezas del sistema de transmisión del motor deben ser lisos y sin defectos para evitar que aumente la fricción o disminuya la estanqueidad. Las piezas internas y externas del coche, como luces, salpicaderos y carcasas de plástico, también necesitan eliminar rebabas y bordes sobrantes generados durante el proceso de producción para mantener la belleza y precisión del producto.
- Efecto: El proceso de desbarbado criogénico puede eliminar con rapidez y precisión las rebabas de las juntas de goma y las piezas de plástico, evitando daños superficiales o en las microestructuras que pueden causar los métodos tradicionales. Puede preservar perfectamente la forma y función de las piezas sin afectar a la calidad general de las mismas. Por ejemplo, las juntas de goma tratadas a bajas temperaturas pueden garantizar su estanqueidad sin dañar la superficie debido al proceso de desbarbado. Además, el proceso de desbarbado criogénico mejora enormemente la eficacia de la producción mediante equipos automatizados, lo que resulta especialmente adecuado para las necesidades de producción en serie de la industria del automóvil.
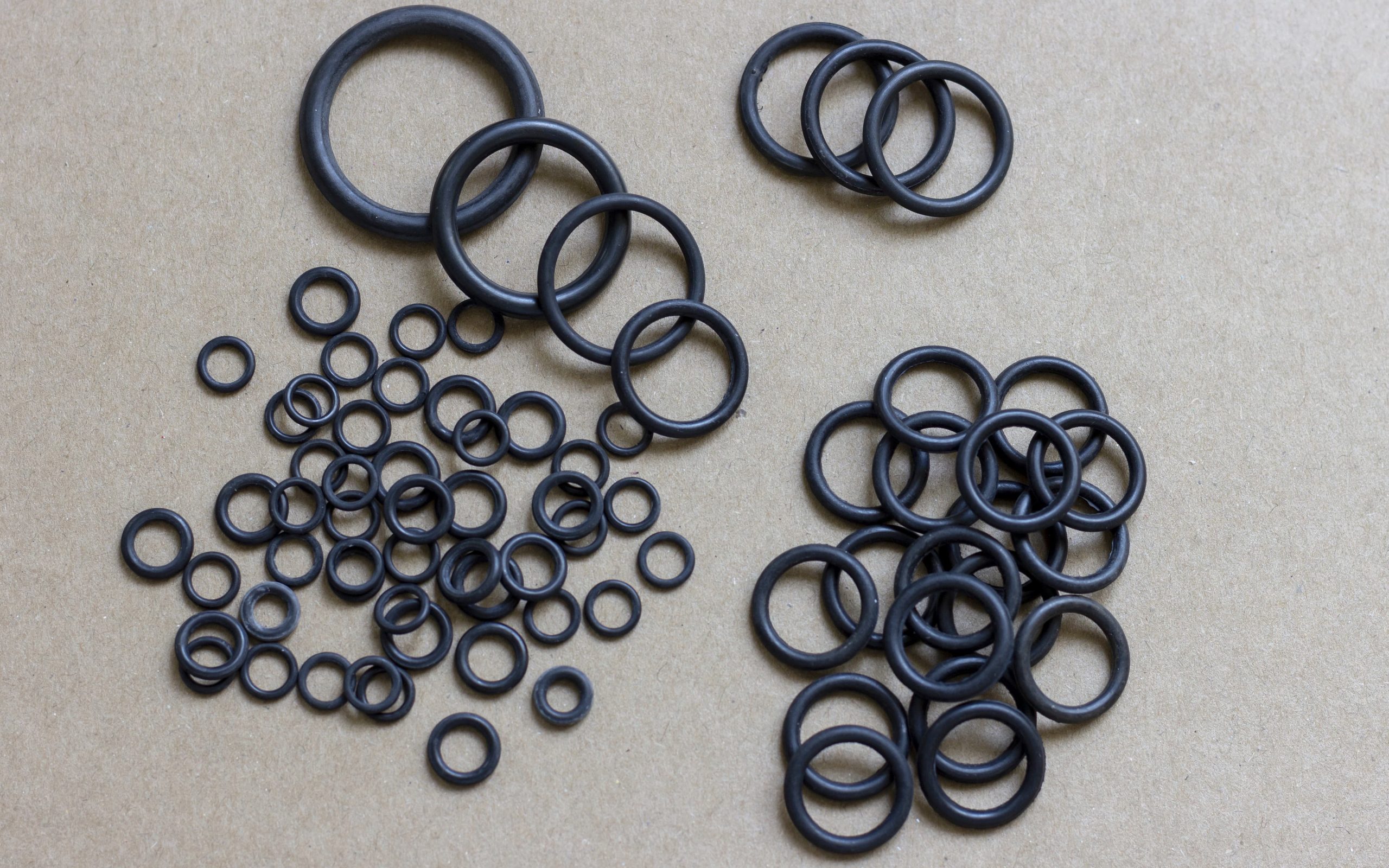
Juntas de goma de diferentes tamaños
- Electrónica digital 3D y equipos de precisión
- Antecedentes: Con el desarrollo de la tecnología de impresión 3D, la fabricación de equipos electrónicos digitales ha planteado mayores exigencias de precisión en el proceso. Las piezas impresas en 3D suelen dejar pequeñas rebabas y bordes sobrantes durante el proceso de fabricación. Estos sutiles defectos pueden afectar a la función real y al aspecto de las piezas. En el sector de la electrónica digital, las placas de circuitos, las carcasas y otros componentes también deben someterse a un desbarbado preciso para garantizar que puedan funcionar correctamente y prolongar su vida útil.
- Efecto: En el caso de las piezas impresas en 3D, el tratamiento a baja temperatura puede garantizar que no se destruyan sus complejas formas geométricas, al tiempo que elimina los diminutos defectos superficiales. En el proceso de producción de equipos electrónicos, el desbarbado a baja temperatura puede eliminar las rebabas de las placas de circuitos y los componentes electrónicos, evitando daños en los circuitos y fallos funcionales que pueden causar los métodos de desbarbado tradicionales. Además, como el proceso de desbarbado a baja temperatura no produce residuos químicos ni afecta a las propiedades de los materiales, es muy adecuado para la fabricación de equipos de precisión y productos electrónicos.
Los medios criogénicos de desbarbado han inyectado un fuerte impulso en el desarrollo de diversas industrias gracias a sus características precisas, eficaces y respetuosas con el medio ambiente. Cuando el frío del nitrógeno líquido abraza la pieza de trabajo, cuando las partículas de nailon eliminan las rebabas con suavidad y firmeza, parece un encuentro perfecto entre tecnología y arte. Ha sido testigo de la altura de la industria aeroespacial, la velocidad de los automóviles y la precisión de la electrónica, y se ha convertido en un socio indispensable de la industria moderna. En los días venideros, que este medio mágico siga escribiendo un capítulo maravilloso en la fabricación industrial y nos cree un mundo más preciso y bello.
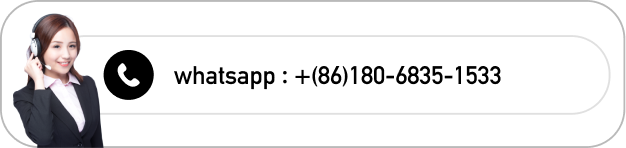