¿Qué impurezas hay que eliminar para producir alúmina de gran pureza?
30 de julio de 2024
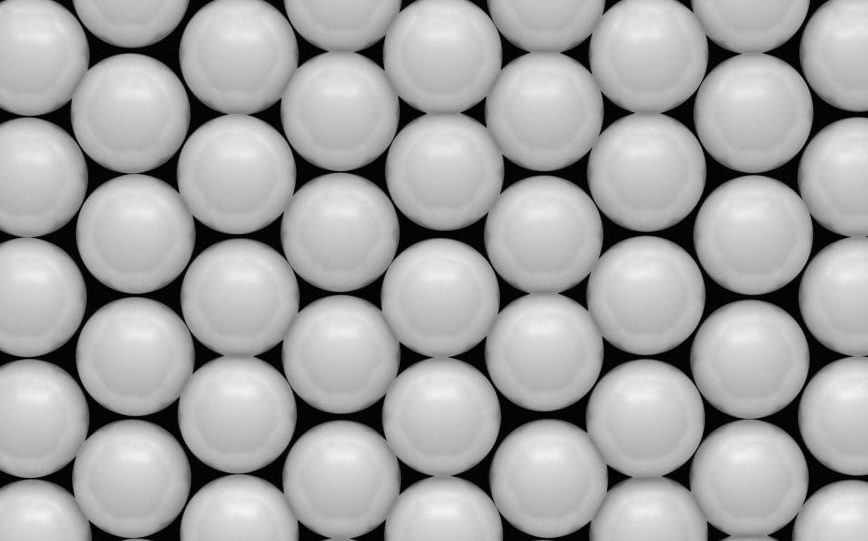
-
Alta dureza: La alúmina de alta pureza tiene una gran dureza, que puede eliminar eficazmente las capas de óxido, herrumbre y otras impurezas de la superficie de la pieza de trabajo sin romperse fácilmente, alargando así la vida útil del medio.
-
Alta resistencia al desgaste: Gracias a su excelente resistencia al desgaste, la alúmina de gran pureza puede mantener un rendimiento estable durante los procesos de arenado y granallado, reduciendo el desgaste y la frecuencia de sustitución, con la consiguiente reducción de costes.
-
Estabilidad química: La alúmina de gran pureza es químicamente estable y no reacciona fácilmente con la pieza tratada, lo que garantiza la calidad y consistencia de la superficie de la pieza.
-
Rendimiento a altas temperaturas: La alúmina de gran pureza puede soportar altas temperaturas, lo que la hace adecuada para operaciones de arenado y granallado en entornos de alta temperatura, evitando la descomposición o el deterioro del medio a altas temperaturas.
Sin embargo, en la producción real puede haber impurezas como hierro, sodio, magnesio, silicio y calcio. Estas impurezas se presentan sobre todo en forma de óxidos como Fe₂O₃, Na₂O, CaO, MgO y CuO. Su contenido variable puede afectar directamente al rendimiento del material. Por ejemplo, el Fe₂O₃ puede reducir la eficiencia de luminiscencia de los materiales de fósforo, y el SiO₂ puede deteriorar el rendimiento de sinterización de la alúmina, limitando así en gran medida la aplicación de la alúmina de gran pureza en diversos campos.
-
Menor dureza y resistencia al desgaste: La alúmina de pureza insuficiente tiene menor dureza y resistencia al desgaste, por lo que es más propensa a romperse o desgastarse durante el uso, reduciendo así la vida útil del medio y aumentando la frecuencia y los costes de sustitución.
-
Impactos sobre el efecto del tratamiento: La alúmina de baja pureza puede contener impurezas que pueden contaminar la superficie de la pieza durante el arenado o granallado, afectando al efecto del tratamiento. Esto puede provocar marcas de tratamiento desiguales o residuos en la superficie de la pieza, lo que afecta a la calidad y el aspecto del producto final.
-
Reacciones químicas: La alúmina de baja pureza puede contener sustancias químicas activas que pueden reaccionar con la pieza durante el chorreado o granallado, causando corrosión o deterioro de la superficie de la pieza, afectando así a su rendimiento y vida útil.
-
Mala estabilidad térmica: La alúmina de baja pureza es menos estable a altas temperaturas, lo que puede provocar su descomposición o deterioro, afectando a la estabilidad y eficacia del proceso de arenado y granallado. En operaciones a alta temperatura, esto puede hacer que el medio falle rápidamente.
-
Aumento del polvo y la contaminación: La alúmina de baja pureza es más propensa a producir polvo y residuos durante su uso, lo que aumenta la dificultad de limpieza y mantenimiento y puede suponer un riesgo para la salud de los operarios y causar contaminación medioambiental.
Por lo tanto, el uso de bolas de alúmina de gran pureza es crucial para garantizar la eficacia del proceso de arenado y granallado y la calidad de la pieza.
Los principales métodos para preparar alúmina de gran pureza incluyen la hidrólisis del alcóxido de aluminio, la descomposición térmica del sulfato de aluminio y amonio y la descomposición térmica del carbonato de aluminio y amonio. Actualmente, la investigación sobre la eliminación de impurezas para obtener alúmina de gran pureza se centra principalmente en la purificación de las materias primas que intervienen en estos métodos.
Impurezas de hierro
Las impurezas de hierro existen sobre todo en forma de óxidos divalentes o trivalentes en el producto principal. Existen numerosas investigaciones sobre la eliminación de las impurezas de hierro de distintas sustancias, como la bauxita y el alcohol isopropílico de aluminio. La bauxita, formada en climas tropicales o subtropicales, se encuentra ampliamente en diversas rocas y esquistos, y contiene impurezas comunes como ferrita, goethita, cuarzo, kyanita, corindón y dióxido de titanio. La bauxita de alta calidad contiene como mínimo 40% de Al₂O₃ y como máximo 15% de SiO₂. Las impurezas de la bauxita de baja calidad incluyen principalmente cuarzo, Fe₂O₃ y CaO. En el proceso de recuperación de alúmina a partir de bauxita mediante lixiviación con ácido sulfúrico, A Aziz descubrió que el uso de etanol 68% (C₂H₅OH) eliminaba casi por completo las impurezas de Fe, aunque el etanol es caro. Para que el proceso resulte más económico, el etanol puede recuperarse y reutilizarse mediante condensación.
También es frecuente encontrar hierro en la preparación de alúmina mediante el método del alcóxido de aluminio. El alcohol isopropílico de aluminio puede purificarse mediante los métodos de extracción-complexación y complejación-cristalización, seleccionando los agentes complejantes adecuados para separar las impurezas en función de las diferentes solubilidades de las distintas sustancias. Las ventajas de este método incluyen la obtención de alcohol isopropílico de aluminio de gran pureza a bajo coste, aunque el proceso es complejo y requiere mucho tiempo.
Cuando se prepara alúmina de gran pureza a partir de sulfato de aluminio y amonio, los métodos habituales para eliminar el Fe incluyen la precipitación, la extracción con aminas primarias orgánicas y la recristalización. La precipitación puede conseguirse añadiendo MnO₂, KMnO₄, K₃[Fe(CN)₆] o K₄Fe(CN)₆-3H₂O. Las ventajas de este método son su bajo coste y su facilidad de aplicación, aunque puede provocar una pérdida importante de iones de aluminio e introducir nuevas impurezas a través de los aditivos utilizados.
Impurezas de silicio
Las impurezas de silicio son relativamente inertes y difíciles de eliminar. Cuando se utiliza el método de hidrólisis de alcóxido de aluminio, el silicio es una de las muchas impurezas del alcohol isopropílico de aluminio, y puede eliminarse utilizando un método que implica la adición de un aditivo de óxido de lantano durante la destilación al vacío. En este proceso, el óxido de lantano reacciona con el silicio para formar una sustancia de alto punto de ebullición, que permanece en el recipiente de reacción después de destilar el alcohol isopropílico de aluminio, purificando así el alcohol isopropílico de aluminio. Este método es eficiente desde el punto de vista energético, sencillo de manejar y tiene un tiempo de reacción corto en comparación con los métodos generales de extracción y cristalización.
Las impurezas de Si y Fe en las muestras tostadas pueden quedar expuestas y luego eliminarse mediante repetidos lavados ultrasónicos con ácido y lavados con agua, lo que da como resultado alúmina hidróxida con contenidos de Si y Fe inferiores a 0,001%. También se sugiere utilizar columnas de carbón activado o membranas de filtración de titanio microporoso para la filtración de la materia prima a fin de eliminar las impurezas. La cal puede utilizarse como agente desiliconizante en la solución de aluminato sódico, reaccionando con el agua para formar hidróxido de calcio, que a su vez reacciona con el aluminato sódico para formar aluminato tricálcico. Los iones de silicato reaccionan con el aluminato tricálcico para formar granate hidratado insoluble, precipitándose y consiguiendo una tasa de eliminación de silicio de hasta 98%.
Algunos métodos pueden introducir impurezas como Na y Ca, mientras que otros son adecuados para eliminar trazas de Si, pero no para eliminar trazas de Si en profundidad. Por tanto, es crucial buscar un método eficaz para eliminar las trazas de Si.
Impurezas cálcicas
Las impurezas de calcio pueden eliminarse mediante agentes de extracción, precipitación química, cristalización de sales, intercambio iónico y quelación. Inicialmente, la baja solubilidad del sulfato de calcio puede aprovecharse para precipitar el Ca²⁺ como CaSO₄, seguido de una eliminación secundaria mediante métodos como la extracción con disolventes. El agente de extracción P204, que es barato y un extractante ácido, sigue el orden de extracción de Fe³⁺ > Zn²⁺ > Cu²⁺ > Co²⁺ > Mg²⁺ > Mn²⁺ > Ca²⁺. H. Xie utilizó P204 para extraer iones de calcio de una mezcla de calcio, magnesio y manganeso, reduciendo significativamente la concentración de iones de calcio, aunque no consiguió una gran pureza. R. Zhao eliminó eficazmente las impurezas de calcio del fosfoyeso utilizando fosfato de tri-n-butilo, obteniendo partículas de sulfato de calcio con una pureza superior a 99%.
Impurezas de sodio
Los métodos habituales para eliminar las impurezas de sodio en la preparación de alúmina incluyen el lavado, el tratamiento hidrotérmico y la adición de ácido bórico. L. Lu utilizó un método de lavado para eliminar el sodio de los cristales de sulfato de aluminio y amonio, calentando los cristales a 150-200°C para facilitar la eliminación del sodio. J. Li comparó el tratamiento hidrotérmico y la adición de ácido bórico para la eliminación de sodio durante la preparación de alúmina, eligiendo el tratamiento hidrotérmico por sus resultados de mayor pureza. H. He añadió ácido bórico durante la calcinación del hidróxido de aluminio para que reaccionara con las impurezas de sodio y formara metaborato sódico, seguido de lavado ácido y secado para obtener alúmina con un contenido de sodio inferior a 0,001%.
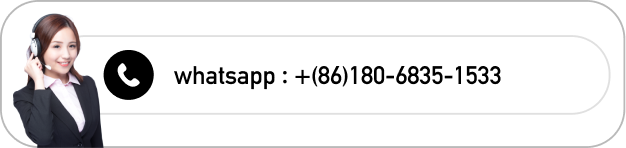