Tipo II VS Tipo III: Cómo elegir el soporte plástico adecuado
3 de diciembre de 2024
Las granallas de plástico de tipo II y las granallas de plástico de tipo III se utilizan ampliamente en operaciones de chorreado de arena debido a su excelente rendimiento y versatilidad, especialmente para componentes sensibles y delicados. ¿En qué se diferencian? ¿Cómo podemos hacer la elección correcta para diferentes tareas de procesamiento y materiales?
Principales ámbitos de aplicación
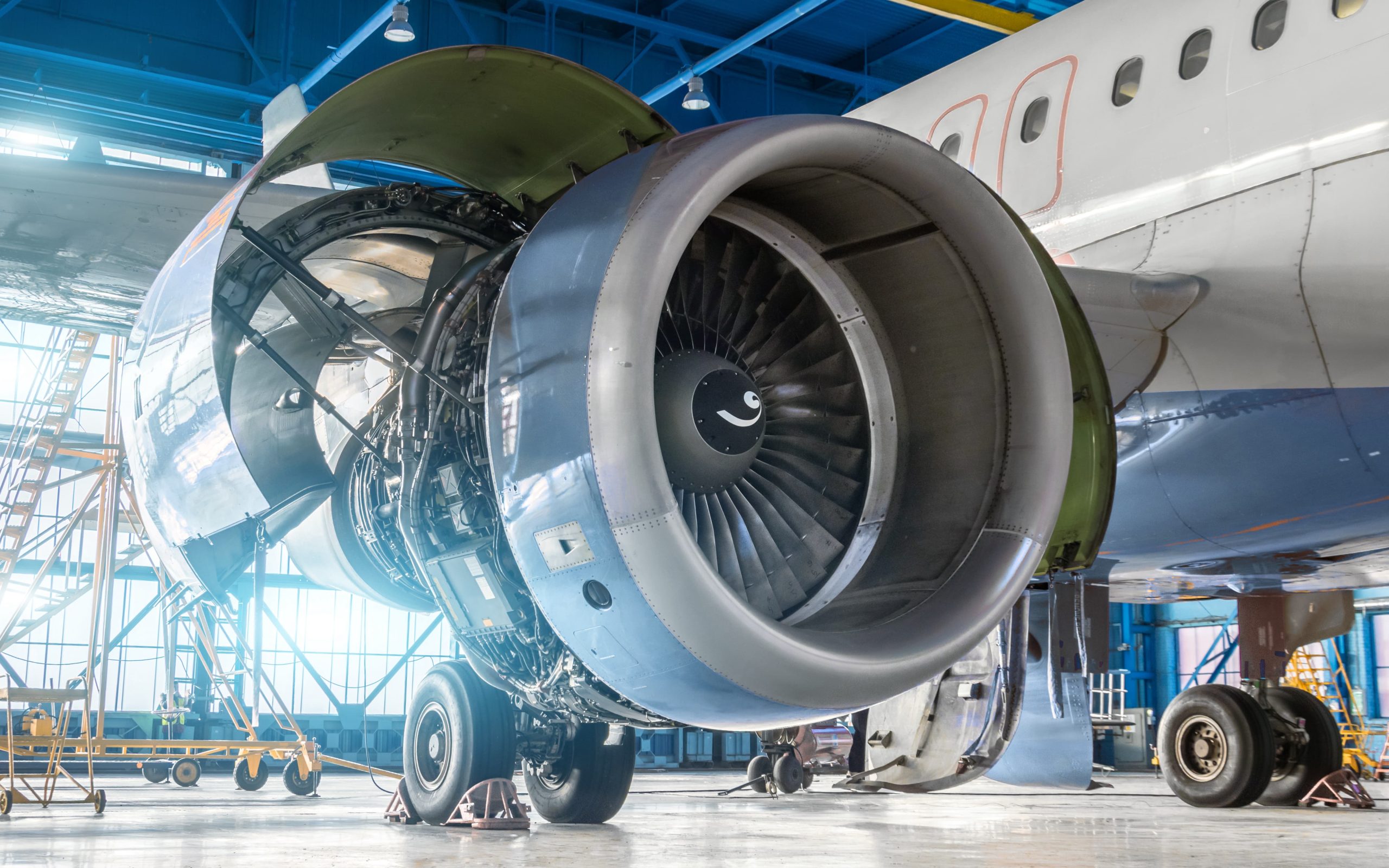
Soportes de plástico de tipo III
- Mantenimiento de equipos industriales
La mayor dureza y fuerza de corte de los medios plásticos de tipo III permiten una limpieza rápida de las superficies de equipos de acero o maquinaria de gran tamaño, mejorando la eficacia del procesamiento y reduciendo al mismo tiempo la frecuencia de consumo de medios.
- Reparación de automóviles y refabricación de piezas
Excelente rendimiento en la limpieza de piezas del motor o estructuras del chasis, eliminando eficazmente los contaminantes y creando una superficie ideal para el posterior pintado o montaje.
- Limpieza de fibra de vidrio y materiales compuestos
Las formas irregulares y los tamaños pequeños facilitan la manipulación de estos materiales complejos, lo que garantiza la eficacia de la limpieza y evita el corte excesivo.
- Pretratamiento de pintura de alta gama
El potente rendimiento de corte completa rápidamente las tareas de desbaste y mejora significativamente la posterior adherencia del revestimiento.
Soportes de plástico de tipo II
- Industria aeroespacial
La baja dureza del material plástico de tipo II elimina eficazmente las capas de óxido, los revestimientos antiguos y la suciedad sin dañar el sustrato, por lo que resulta ideal para la limpieza de estructuras interiores de aeronaves y componentes metálicos ligeros.
- Componentes electrónicos y placas de circuitos
Elimina suavemente la suciedad de las zonas sensibles evitando dañar las vías conductoras que pueden causar los abrasivos de mayor dureza.
- Piezas y moldes de plástico de precisión
Precisamente limpiar el molde y las superficies acabadas manteniendo la suavidad y la funcionalidad.
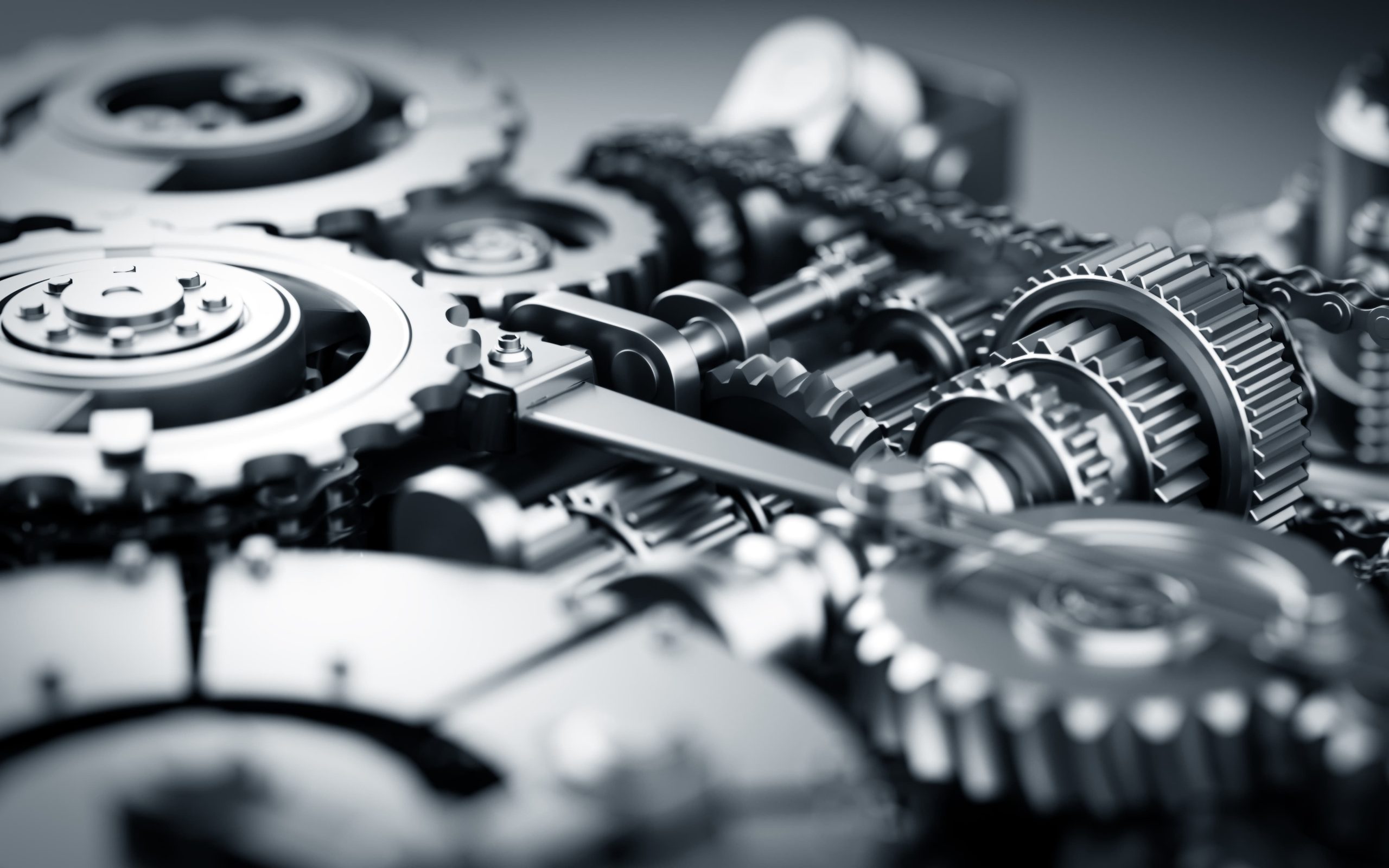
Puntos en común
Aunque los soportes de plástico de Tipo II y los de Tipo III difieren en escenarios de aplicación específicos, ambos son adecuados para una gran variedad de materiales, entre los que se incluyen:
- Fibra de vidrio
- Aluminio
- Cobre/latón
- Plástico/goma
- Componentes electrónicos y placas de circuitos
- Otros materiales compuestos
Funciones principales
- Limpieza de superficies: Elimina las capas de óxido, la suciedad y los revestimientos antiguos de la superficie para garantizar la pureza del sustrato.
- Optimización de la superficie: Mejora la estética, la funcionalidad o la adherencia de los revestimientos posteriores ajustando la textura de la superficie.
Sin embargo, en operaciones específicas, las necesidades del cliente suelen implicar consideraciones más detalladas, como las propiedades del material, el coste, los requisitos medioambientales, etc. Analizaremos estos aspectos en profundidad para ayudar a los clientes a tomar la decisión correcta en función de su situación real.
Factores de selección de los medios abrasivos
En las operaciones de chorreado de arena, la elección del medio abrasivo adecuado es la clave para garantizar los efectos del tratamiento y la rentabilidad. Los siguientes cinco factores básicos proporcionarán a los clientes una clara orientación de referencia.
Materiales a tratar con chorro de arena
Los distintos tipos de materiales tienen sus propios requisitos en cuanto a dureza, fuerza de impacto y métodos de tratamiento de los abrasivos:
Materiales blandos
- Limpieza de piezas de aluminio en el sector aeroespacial
- Tratamiento superficial de productos de fibra de vidrio
- Descontaminación de piezas de plástico de precisión, etc.
(como aleaciones de aluminio, materiales compuestos y piezas de plástico) La superficie es relativamente blanda y se daña o deforma fácilmente por impacto, por lo que es necesario seleccionar abrasivos de baja dureza y baja fuerza de impacto para conseguir un efecto de limpieza suave.
Por lo tanto, los medios plásticos de Tipo II serán más adecuados para este tipo de materiales. Su menor dureza y su densidad más ligera pueden proteger el sustrato de daños al tiempo que eliminan la suciedad superficial y las capas de óxido.
Materiales de gran dureza
- Eliminación de óxido superficial de equipos industriales
- Limpieza de pintura vieja de grandes piezas estructurales
- Tratamiento superficial de piezas de aleación resistentes al desgaste
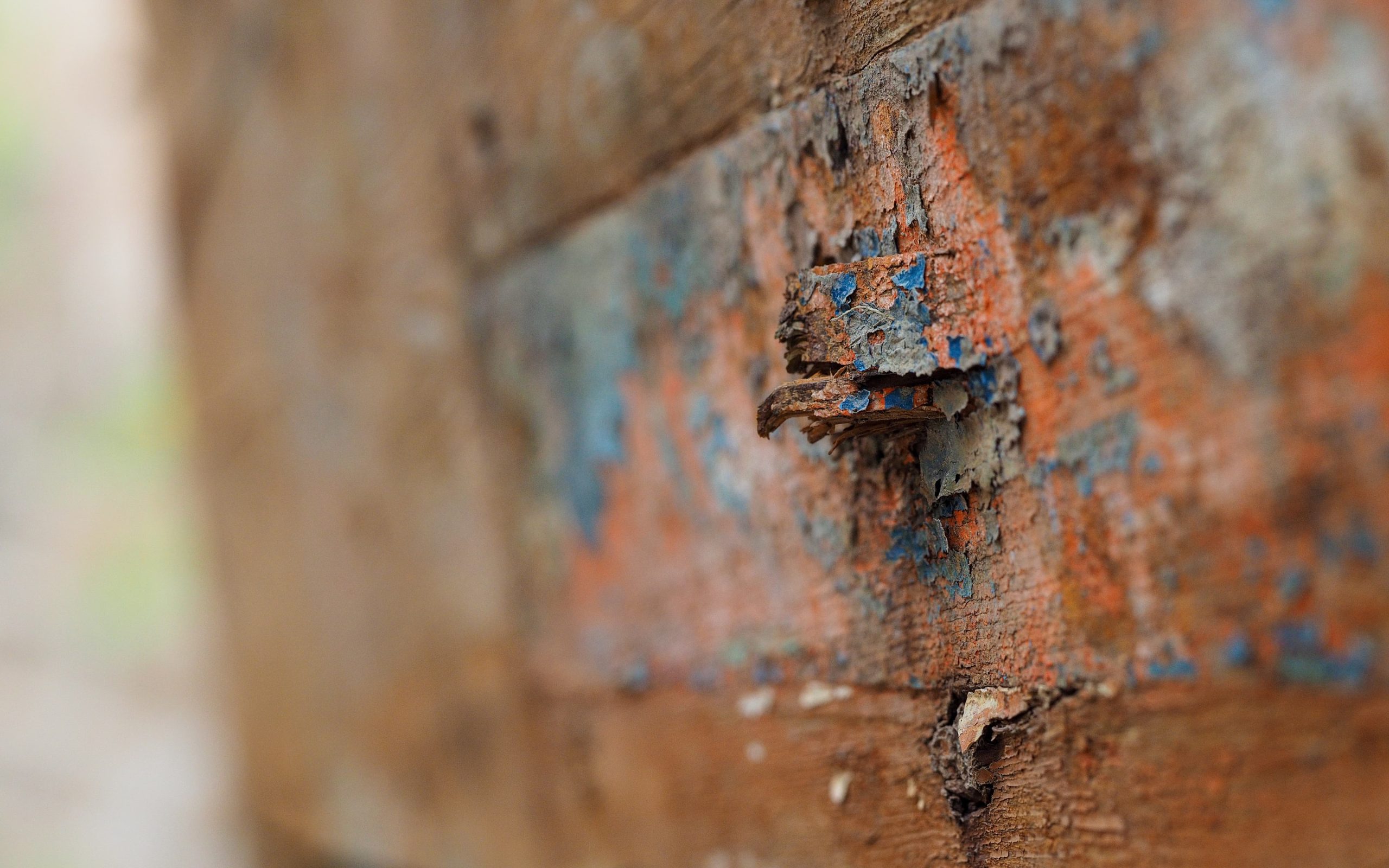
(Como el acero inoxidable, el acero al carbono, la aleación de titanio) suelen tener una gran solidez y resistencia al desgaste, y el óxido o revestimiento de la superficie es relativamente tenaz. Es necesario utilizar un medio con mayor dureza y forma de partícula más afilada para mejorar la eficacia de la limpieza.
La granalla de plástico de tipo III tiene la mayor dureza entre las granallas de plástico, y sus partículas angulares afiladas también pueden limpiar rápidamente los revestimientos más resistentes o las capas de óxido, manteniendo al mismo tiempo una alta eficacia de procesamiento.
Resumen
Según las propiedades del material, se recomienda dar prioridad al Tipo II para materiales blandos, con el fin de garantizar la seguridad y la precisión de procesamiento de la pieza; mientras que para superficies de gran dureza y obstinadamente contaminadas, los medios plásticos del Tipo III son más adecuados y pueden mejorar significativamente la eficacia del trabajo.
Acabado superficial
Uno de los objetivos principales del chorreado es ajustar el acabado superficial de la pieza. Las distintas tareas de limpieza o procesamiento tienen diferentes requisitos de rugosidad superficial, lo que afecta a la elección de los medios abrasivos.
Superficie rugosa
- Pretratamiento de la superficie antes de pintar para garantizar la adherencia a largo plazo del revestimiento.
- Desbaste de superficies de equipos industriales o piezas de gran tamaño.
- Tratamiento de piezas unidas o superficies soldadas para mejorar el rendimiento de la unión.
Algunas aplicaciones industriales requieren una mayor rugosidad de la superficie para garantizar que el material de revestimiento o de unión pueda adherirse firmemente. Estas operaciones tienden a elegir medios con una mayor fuerza de corte. Dado que el Tipo III suele tener formas de partículas angulares, tiene una mayor capacidad de impacto y de corte, lo que puede lograr rápidamente la rugosidad de la superficie y mejorar la adherencia y la fuerza de unión mecánica.
Superficie lisa
- Limpieza y pulido de piezas de instrumentos ópticos.
- Tratamiento decorativo de piezas de precisión de plástico o composite.
- Chorreado fino para componentes electrónicos o piezas de paredes finas.
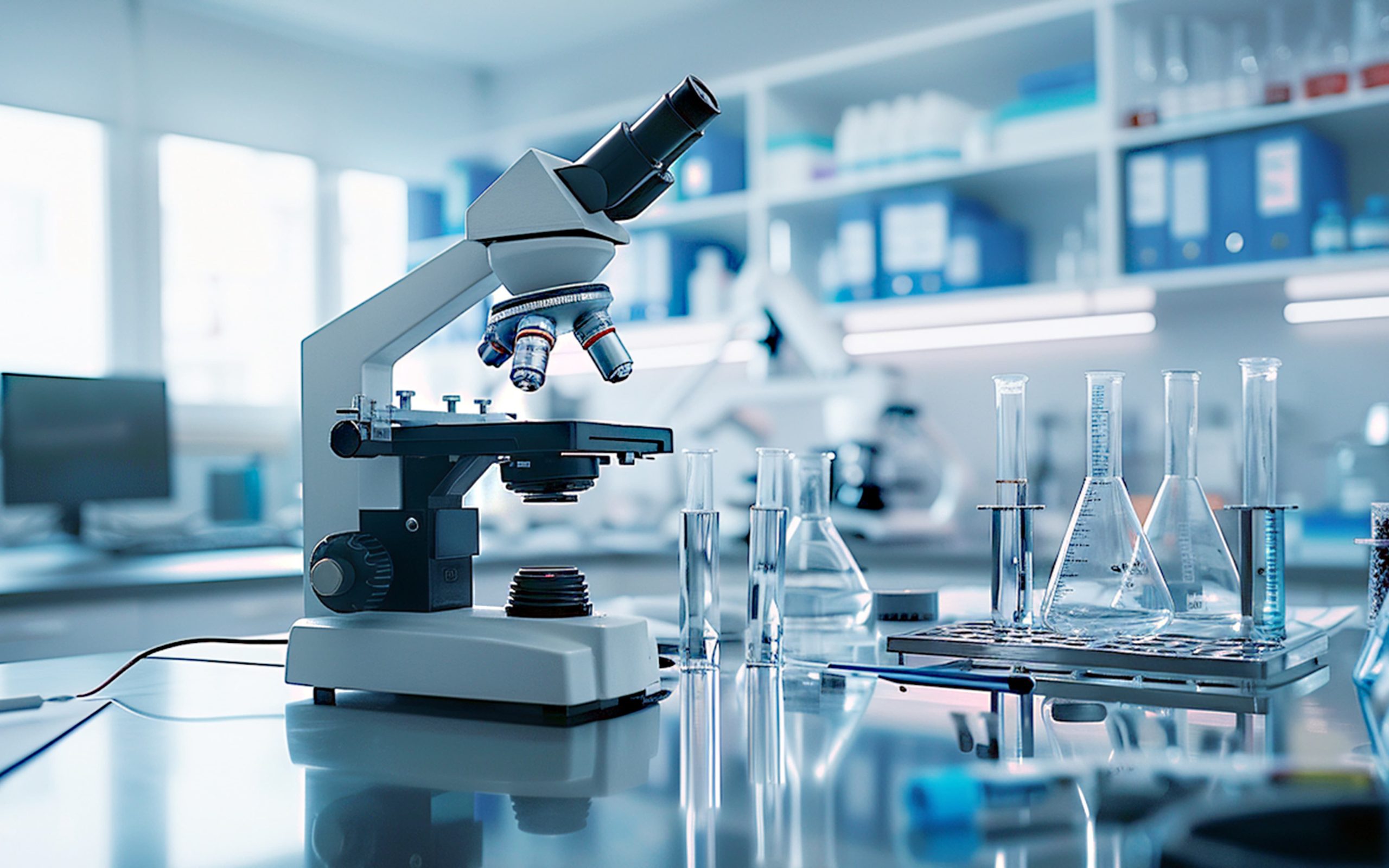
Para la decoración de exteriores o piezas mecanizadas de precisión, los clientes suelen desear una superficie lisa y uniforme para mejorar los efectos visuales o cumplir requisitos funcionales. En estos casos se prefiere utilizar materiales de menor impacto y desgaste. Los abrasivos plásticos de tipo II son los más adecuados. Su suave acción puede eliminar contaminantes superficiales manteniendo la integridad y suavidad de la superficie de la pieza.
Resumen
Si su objetivo es conseguir una superficie limpia y lisa, el Tipo II es una mejor elección, especialmente para piezas con elevados requisitos de aspecto o integridad superficial; cuando el objetivo es aumentar la rugosidad para cumplir requisitos funcionales, la capacidad de corte del Tipo III es más adecuada.
Compatibilidad con los equipos existentes
La elección del material abrasivo depende no sólo de los requisitos de la pieza, sino también de la compatibilidad del equipo de chorreado existente. El tipo de equipo, la presión de chorreado, la forma de la boquilla, etc., pueden afectar al efecto de chorreado y a la vida útil del abrasivo.
Equipos de baja presión
Generalmente adecuado para procesar medios más ligeros, como abrasivos plásticos. Este tipo de equipo tiene menos requisitos de resistencia al desgaste de la boquilla, pero depende más de la flexibilidad y la estabilidad de forma del material.
Los abrasivos de tipo II tienen una densidad relativamente baja (alrededor de 1,48 - 1,52 g/cm³), y la forma triangular irregular de las partículas les permite actuar uniformemente sobre la superficie durante el chorreado, lo que resulta especialmente adecuado para sistemas de chorreado pequeños o portátiles con una presión de salida del equipo limitada.
Equipos de alta presión
Diseñado para manejar medios de alta dureza y densidad, puede proporcionar suficiente fuerza de impacto para revestimientos y óxidos resistentes, pero requiere una mayor resistencia al desgaste de la boquilla y la pared interior del equipo.
La granalla de plástico de tipo III es muy adecuada para equipos de chorro de arena de alta presión (especialmente equipos con boquillas de alta dureza). Puede dar pleno juego al rendimiento de corte de sus partículas angulares bajo alto impacto, y es más resistente al desgaste. Puede mantener su integridad y eficacia operativa durante operaciones de alta presión a largo plazo.
Resumen
En cuanto a la adaptabilidad de los equipos, las características del Tipo II lo hacen más adecuado para equipos portátiles y de baja presión, especialmente en términos de flexibilidad y protección de los equipos; mientras que el Tipo III puede mostrar una mayor capacidad de limpieza en entornos de alta presión, adecuado para equipos de grado industrial y tareas de alta intensidad.
Factores de coste
El coste es una consideración clave a la hora de elegir los medios abrasivos. El coste del chorreado de arena incluye no solo el precio de compra del abrasivo, sino también su durabilidad, reciclabilidad e impacto potencial en el equipo y la pieza de trabajo.
Coste de adquisición
El coste de fabricación tanto del Tipo II como del Tipo III es relativamente bajo, por lo que su precio de mercado es competitivo. La diferencia es que el Tipo II es especialmente adecuado para pequeñas empresas o proyectos puntuales sensibles a los costes. El Tipo III suele ofrecer una alta rentabilidad en aplicaciones industriales de gama alta.
Vida útil
Los abrasivos duraderos pueden reciclarse varias veces, lo que reduce el coste de una sola limpieza. El Tipo III tiene una resistencia al desgaste significativamente mayor que el Tipo II debido a su mayor dureza y tenacidad, y es adecuado para escenarios industriales con más ciclos, lo que puede reducir los costes totales a largo plazo.
Gastos conexos
Incluidos los costes de mantenimiento de los equipos, las medidas de control del polvo y los costes de indemnización por daños en las piezas de trabajo que puedan deberse a un uso inadecuado.
Soportes de plástico de tipo II:
- Un menor desgaste del equipo puede reducir la frecuencia de sustitución de boquillas y tuberías.
- Debido a las partículas ligeras, se genera menos polvo durante el proceso de pulverización, lo que puede reducir los costes de gestión del polvo.
Soportes de plástico de tipo III:
- Mejor rendimiento en equipos de alta presión. Aunque la dureza es la más alta entre los medios plásticos, causa poco desgaste en la boquilla y la pared interior del equipo, ahorrando costes de mantenimiento.
- Las partículas más pesadas pueden suponer mayores costes de transporte y almacenamiento, pero al mismo tiempo reducen la cantidad de polvo en suspensión en el aire tras la pulverización, lo que contribuye a optimizar el entorno de trabajo.
Resumen
En términos de coste, estos dos medios son comparables, ambos son económicos, y además tienen resistencia al desgaste en usos posteriores, y son rentables a largo plazo.
Cuestiones medioambientales
Incluye la reciclabilidad de los medios abrasivos, las emisiones de polvo, los posibles riesgos de contaminación para el medio ambiente y el cumplimiento de las leyes y normativas.
Reciclabilidad
Los abrasivos respetuosos con el medio ambiente deben tener una elevada capacidad de reciclado para reducir la frecuencia y el coste de la eliminación de residuos. Tanto los abrasivos de plástico de tipo II como los de tipo III son reciclables, y el índice de rotura es bajo durante múltiples ciclos, lo que mejora significativamente la eficiencia del reciclado.
Gestión del polvo
Un exceso de polvo no sólo afecta al entorno de trabajo, sino que también puede poner en peligro la salud de los trabajadores. Por tanto, la forma, la densidad y la durabilidad del abrasivo afectarán directamente al nivel de polvo.
Debido a la baja densidad y a la forma irregular de las partículas de Tipo II, se genera menos polvo durante el proceso de pulverización, no quedan residuos y la eliminación de residuos es sencilla.
Debido a la alta densidad y a la forma más regular de las partículas de Tipo III, el polvo generado durante el proceso de pulverización es fácil de sedimentar rápidamente, lo que reduce significativamente la concentración de partículas en suspensión en el aire y reduce la amenaza potencial del polvo para la salud de los trabajadores.
Cumplimiento de la normativa
Las normativas medioambientales de las distintas regiones imponen requisitos estrictos en materia de emisiones para las operaciones industriales. La selección de medios abrasivos conformes puede reducir los riesgos legales a los que se enfrentan las empresas.
Los residuos de tipo II se componen principalmente de sustratos de plástico, que pueden reciclarse y reutilizarse de forma centralizada. Un tratamiento normalizado puede reducir el riesgo de contaminación por microplásticos.
El tipo III no es tóxico ni nocivo, y sólo presenta un pequeño riesgo de microplásticos. Puede cumplir estrictas normas medioambientales en su conjunto y es especialmente popular en los mercados europeo y estadounidense. Suele recomendarse para proyectos de protección medioambiental de alto nivel.
Resumen
En términos de rendimiento medioambiental, el Tipo II es adecuado para operaciones ligeras a corto plazo, y su baja generación de polvo es apropiada para empresas con requisitos estrictos sobre el entorno de trabajo; mientras que la alta durabilidad y la baja generación de residuos del Tipo III son más adecuadas para proyectos industriales que persiguen beneficios medioambientales a largo plazo. Las empresas deben elegir el medio más adecuado en función de la intensidad de la operación y los requisitos de cumplimiento de la normativa medioambiental.
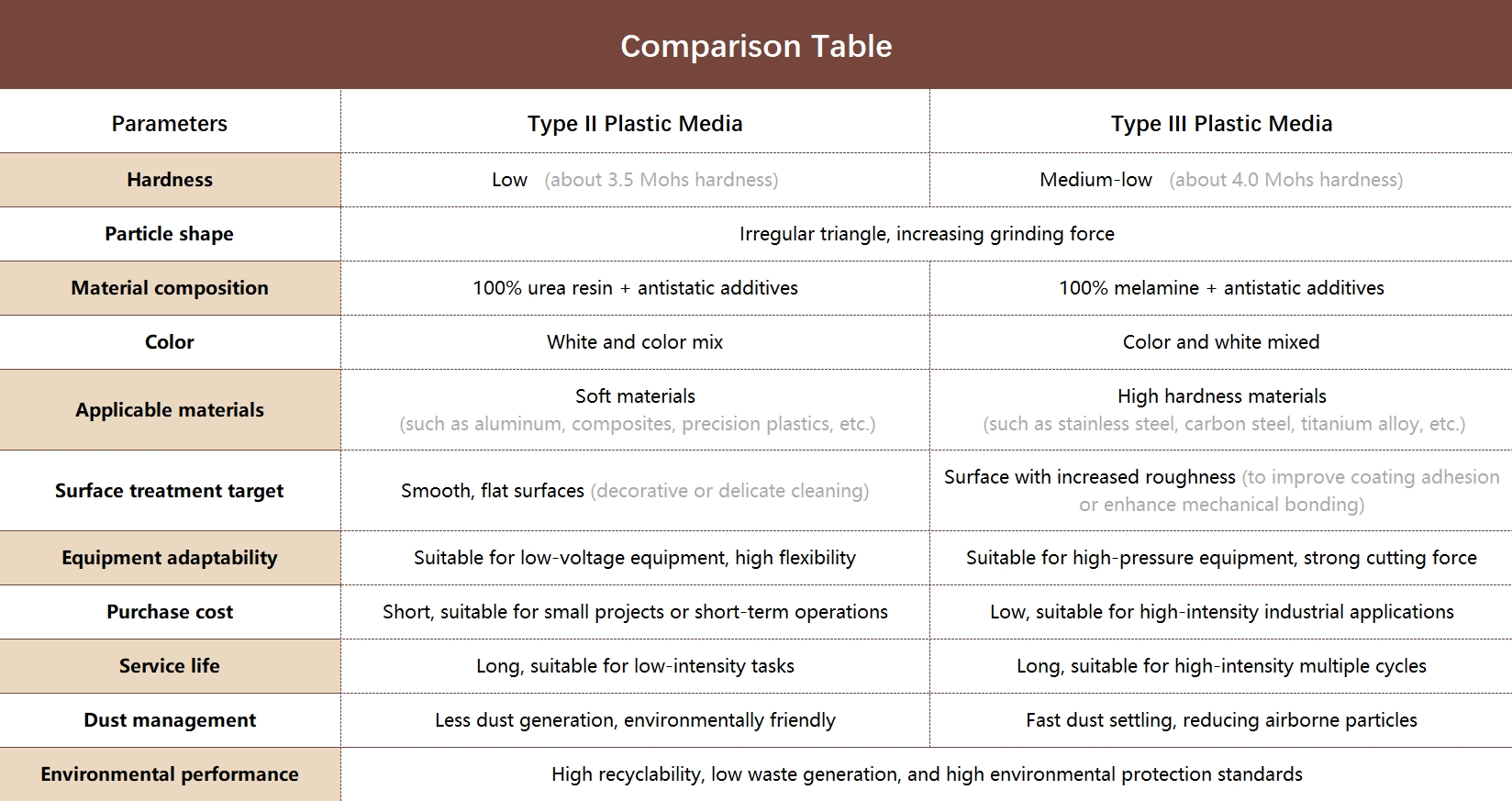
Resumen del caso
Antecedentes:
Un fabricante de equipos industriales se enfrenta a un reto clave: reducir las emisiones de polvo durante el pulido y prolongar la vida útil de los consumibles manteniendo la calidad de las piezas. Aunque los medios abrasivos tradicionales (como las microesferas de vidrio) pueden conseguir un efecto suave, su elevado índice de fragmentación conlleva una alta frecuencia de sustitución de consumibles y un elevado coste global.
Desafíos:
- Respeto del medio ambiente: Los medios tradicionales generan mucho polvo, lo que afecta a la salud de los trabajadores y al cumplimiento de la normativa medioambiental.
- Durabilidad: Los abrasivos existentes tienen una vida útil limitada en el rectificado de alta intensidad y suelen tener que sustituirse con frecuencia.
- Economía: La mayor frecuencia de sustitución conlleva directamente un aumento de los costes de explotación.
Solución:
Tras múltiples pruebas, el cliente eligió el material abrasivo plástico de tipo II, que presenta las siguientes características:
- El diseño triangular irregular de las partículas puede mejorar la eficacia y la cobertura de la molienda.
- Menor dureza, lo que reduce los posibles daños en las superficies de las piezas.
Resultados:
- 30% mayor duración de los consumibles: En comparación con los medios de microesferas de vidrio, el tipo II tiene una 25% menor tasa de generación de polvo y menos mantenimiento.
- 15% menor coste total: Se reduce la frecuencia de sustitución de consumibles y se mejora la eficacia de la producción. [1]
- Cumplimiento de la normativa medioambiental: El cliente superó los requisitos de emisión de polvo de la norma OSHA y mejoró la protección de la salud de los empleados.
Escenario de aplicación:
Una empresa de mantenimiento aeronáutico utiliza abrasivo plástico de tipo III para limpiar piezas de motores de aviones y superficies de materiales compuestos. El objetivo es eliminar revestimientos e impurezas manteniendo la integridad del material sin causar deformaciones ni problemas de sobrecalentamiento.
Abrasivo utilizado: Melamina tipo III Malla 12-16 (1,7-1,2 mm) para tareas de limpieza fina.
Objetivos de limpieza:
- Materiales compuestos para aeronaves: Elimine los revestimientos antiguos y los sellantes anticorrosión de la superficie.
- Piezas de aleación de aluminio: Eliminar las capas de corrosión y conservar una superficie lisa.
Resultados:
- El tiempo de limpieza se reduce en 30% [2] en comparación con los métodos tradicionales de microesferas de vidrio, y la consistencia del acabado superficial mejora significativamente.
- No se induce ninguna deformación ni tensión térmica en el sustrato.
- Cumple la norma MIL-P-85891 (norma militar de eliminación de revestimientos).
Obtenga ahora una solución de arenado personalizada
Ofrecemos servicios gratuitos de consulta profesional para ayudarle a seleccionar con precisión los materiales de chorreado más adecuados.
Simplemente envíenos sus muestras y completaremos la prueba de acuerdo con sus necesidades específicas y le recomendaremos los mejores materiales de chorreado (simples o combinados).
Además, le ofrecemos pruebas de muestras en pequeños lotes para que compruebe el efecto y se asegure de tomar la decisión correcta.
¿Le interesa saber más sobre nuestros productos u obtener un presupuesto? Le invitamos a dejarnos sus datos de contacto.
Al mismo tiempo, no olvide marcar nuestro sitio web. Actualizaremos el blog periódicamente para ofrecerle más información del sector y consejos prácticos que le ayuden a que cada operación de chorreado de arena sea más eficiente y sobresaliente.
Haga clic en el enlace para ponerse en contacto con nosotros
[1] Análisis de casos de aplicación del sitio web de Extrude Hone
[2] Según el caso en el sitio web oficial de Kramer Industries
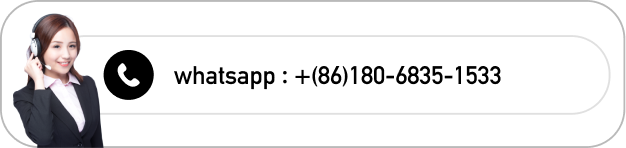