Proceso de acabado superficial | Panorama general
7 de noviembre de 2024
El acabado de superficies es un proceso indispensable en muchas industrias. Su principal objetivo es mejorar la calidad de la superficie de los materiales o productos, incluyendo su aspecto, función y durabilidad. Ya sea en los sectores de la automoción, la aviación, la decoración arquitectónica o la electrónica de consumo, el acabado de superficies, mediante un procesamiento fino, puede ofrecer mejores soluciones para diversos escenarios de aplicación y aumentar enormemente el valor de los productos.
Tipos de procesos de acabado superficial
El acabado de superficies abarca varios procesos, cada uno con sus características únicas, ventajas, desventajas y escenarios aplicables. Los procesos de acabado más comunes son el pulido mecánico, la galvanoplastia, el chorro de arena, el tratamiento químico y el tratamiento térmico. A continuación se ofrece un breve análisis de los principales procesos de acabado:
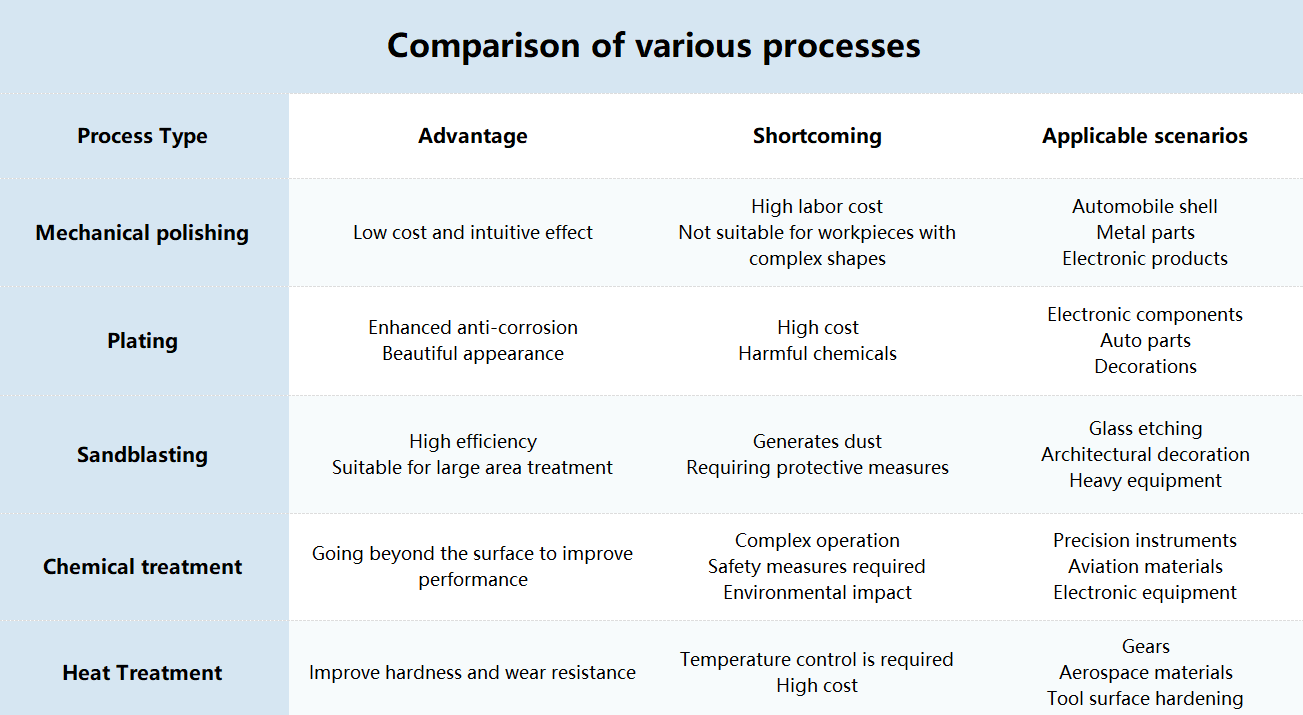
- Pulido mecánico
- Definición: Fricción física de la superficie del material mediante abrasivos, papel de lija, etc. para conseguir un efecto de superficie lisa.
- Ventajas: Bajo coste y efecto intuitivo; adecuado para diversos materiales, como metal, plástico y vidrio.
- Desventajas: Alto coste de mano de obra, no adecuado para una gran superficie o piezas de forma compleja.
- Escenarios aplicables: Pulido de carcasas de automóviles, modificación de piezas metálicas y acabado estético de productos electrónicos.
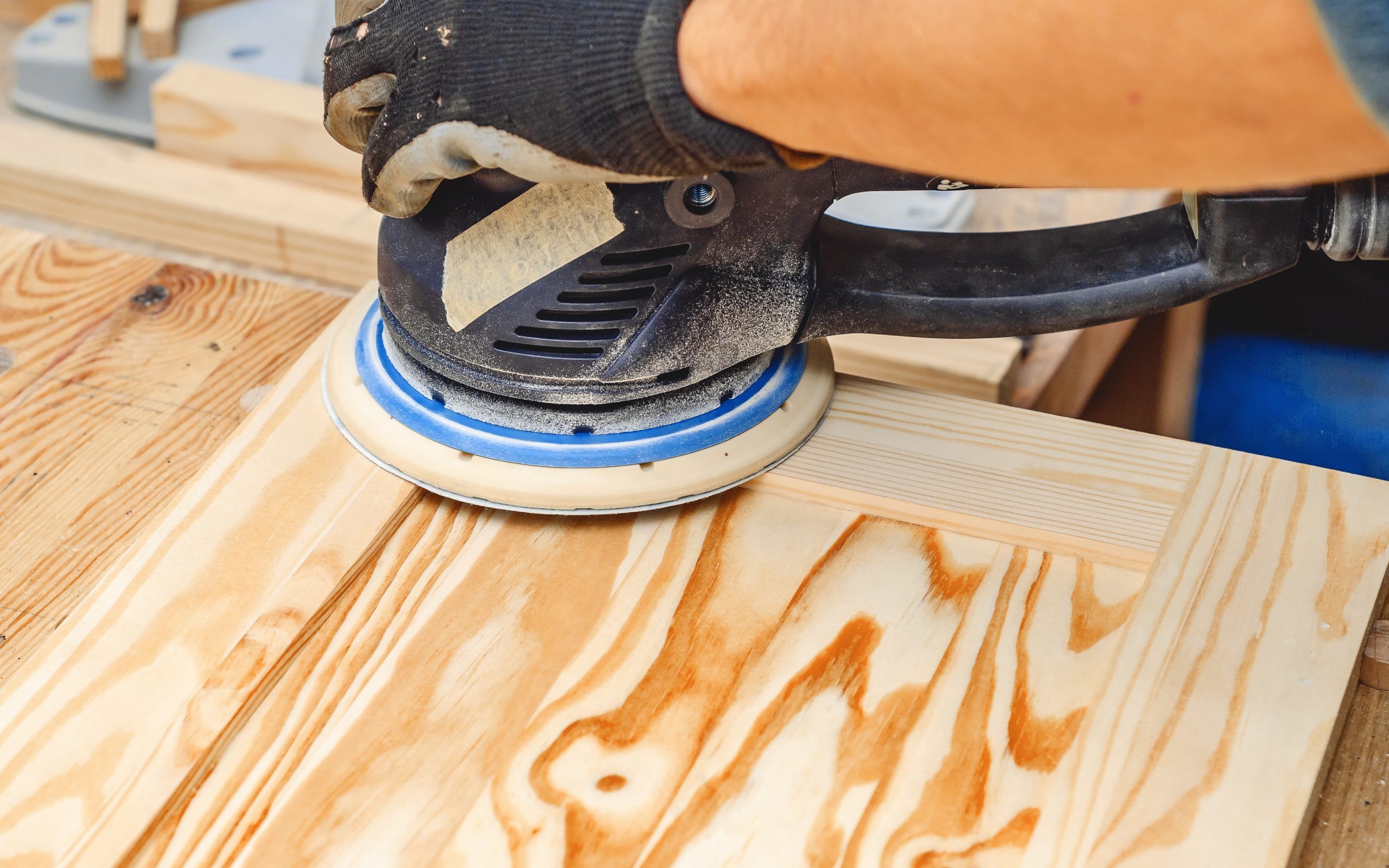
Pulido mecánico
- Galvanoplastia
- Definición: Depositar una película metálica en la superficie de un material mediante una reacción electrolítica para mejorar la resistencia a la corrosión y la estética del material.
- Ventajas: Puede mejorar significativamente la resistencia a la corrosión y la estética de los metales; Aplicable a diferentes superficies metálicas.
- Desventajas: Alto coste, el proceso de tratamiento implica productos químicos nocivos y requiere un funcionamiento profesional.
- Escenarios aplicables: Tratamiento anticorrosión de componentes electrónicos, modificación superficial de piezas de automoción y procesamiento de artículos decorativos de alta gama.
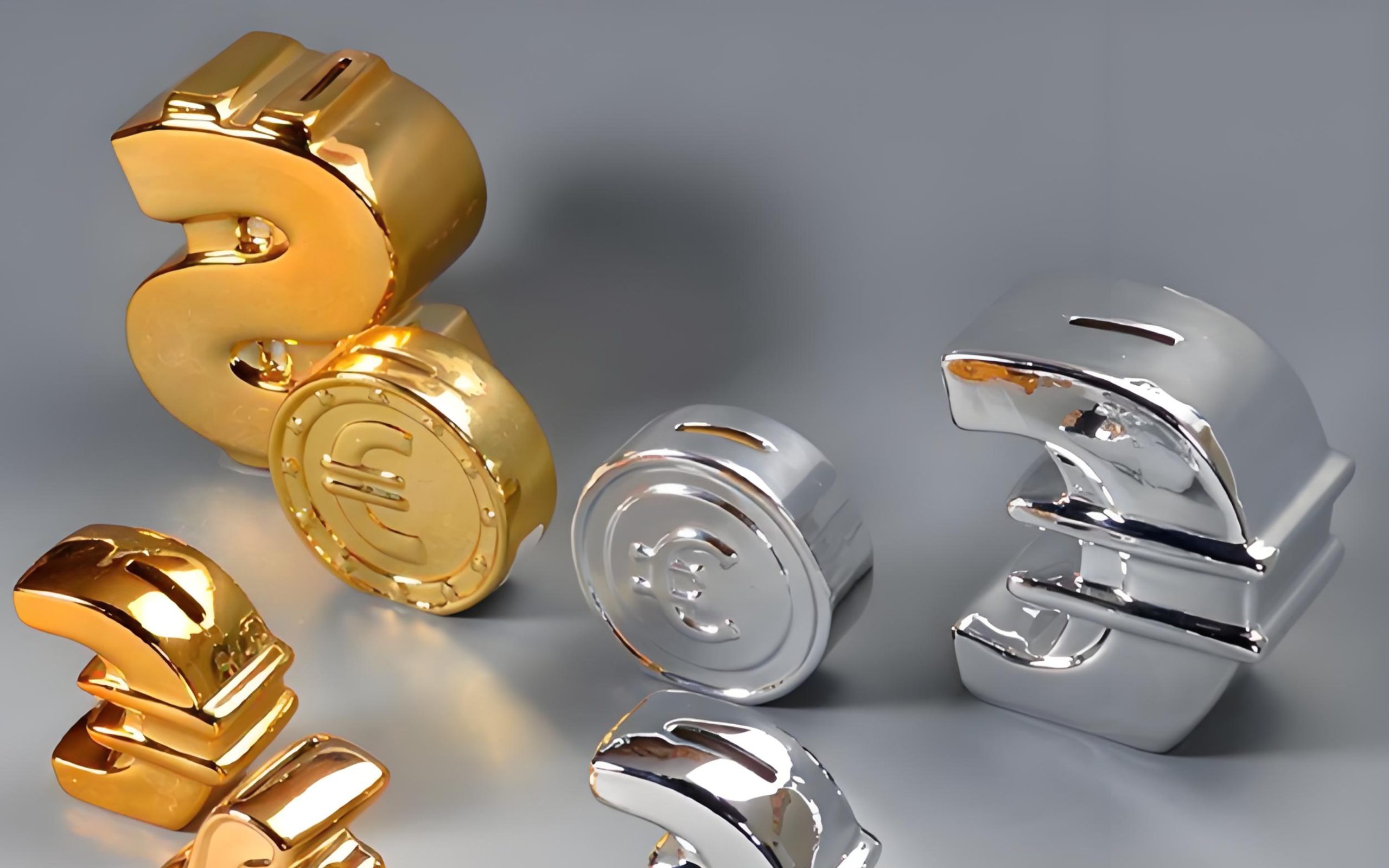
Productos galvanizados
- Chorro de arena
- Definición: Rectificado de la superficie de un material mediante chorro de abrasivos a alta velocidad para eliminar capas de óxido o suciedad, o para formar una textura superficial uniforme.
- Ventajas: Eficaz y rápida, adecuada para una gran variedad de materiales e ideal para el tratamiento de grandes superficies.
- Desventajas: Algunos materiales generan polvo, por lo que es necesario adoptar medidas de protección. Es adecuado para el funcionamiento en un entorno cerrado.
- Escenarios aplicables: Grabado de vidrio, procesamiento de materiales de decoración de edificios y limpieza de superficies de equipos industriales pesados.
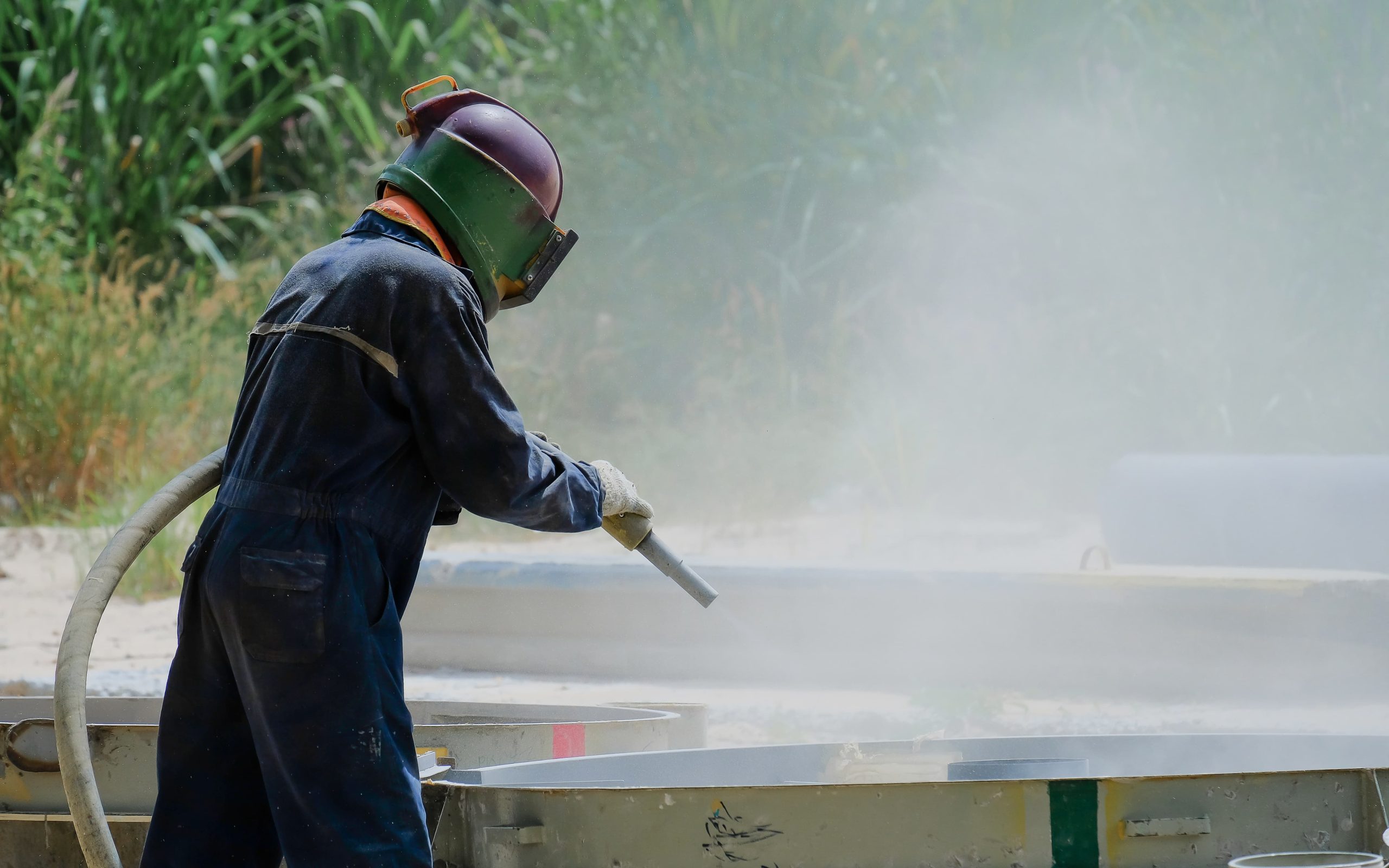
Demostración de chorro de arena
- Tratamiento químico
- Definición: Eliminación de óxidos o impurezas en la superficie del material mediante reacciones químicas, o formación de una película protectora en la superficie.
- Ventajas: Capaz de penetrar en la superficie del material y mejorar el rendimiento superficial; Adecuado para piezas con formas complejas.
- Desventajas: La operación requiere conocimientos químicos y estrictas medidas de seguridad, y una manipulación inadecuada puede tener repercusiones en el medio ambiente.
- Escenarios aplicables: Acabado de superficies de piezas de instrumentos de precisión, tratamiento anticorrosión de materiales aeroespaciales y tratamiento de superficies de equipos electrónicos.
- Tratamiento térmico
- Definición: Modificar las propiedades físicas de la superficie o del conjunto del material, como la dureza y la tenacidad, mediante procesos de ciclos térmicos como el calentamiento y el enfriamiento.
- Ventajas: Mejorar la dureza superficial del material y aumentar la resistencia al desgaste y al impacto.
- Desventajas: Es necesario controlar la temperatura y la velocidad de enfriamiento, y el coste es relativamente elevado; se aplica principalmente a los metales.
- Escenarios aplicables: Tratamiento de refuerzo de piezas mecánicas como engranajes, refuerzo estructural de materiales de aviación y tratamiento de endurecimiento superficial de herramientas.
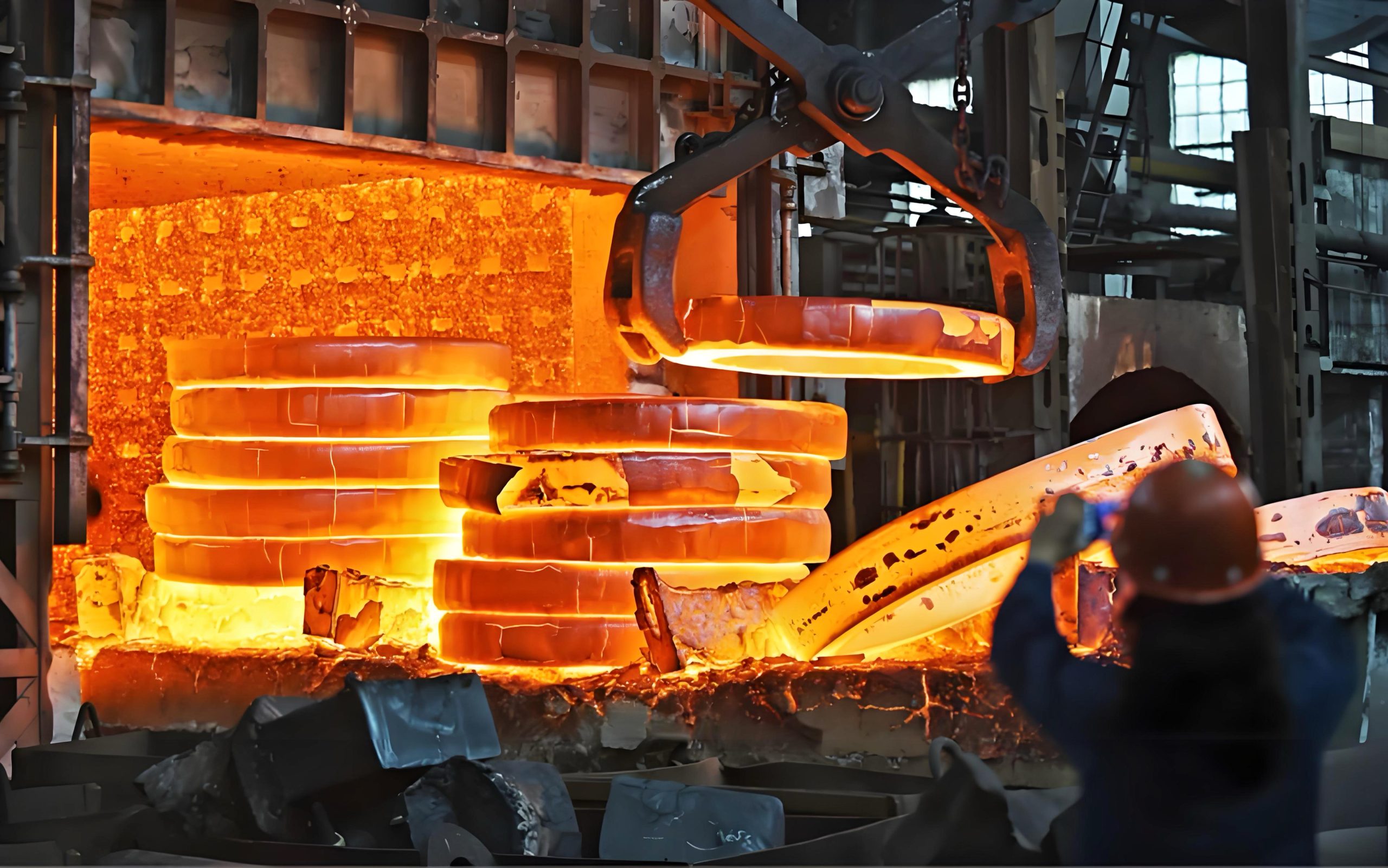
Tratamiento térmico
Factores que afectan a los efectos del acabado superficial
La calidad y el efecto del acabado superficial se ven afectados por muchos factores, desde la selección de materiales hasta los detalles de ejecución del proceso, que tendrán un impacto significativo en el resultado final. A continuación se analizan en detalle estos factores influyentes desde cuatro aspectos: materiales, procesos, condiciones ambientales y requisitos de precisión.
- Propiedades de los materiales
Los distintos materiales presentan reacciones diferentes en el acabado de superficies. Los metales, la cerámica, el vidrio y los plásticos tienen distinta dureza, conductividad térmica y propiedades químicas, por lo que es necesario elegir un proceso adecuado.
- Dureza y resistencia al desgaste: Por ejemplo, los metales duros requieren materiales de rectificado más resistentes, mientras que los metales blandos son susceptibles de sufrir un rectificado excesivo y superficies irregulares.
- Conductividad térmica: Durante el tratamiento térmico, la conductividad térmica del material determina la velocidad de enfriamiento, que a su vez afecta al acabado superficial.
- Reactividad química: En el caso de los metales reactivos, el grabado químico requiere el uso de conservantes y parámetros de proceso especiales para evitar una corrosión excesiva.
- Parámetros del proceso
Los ajustes de los parámetros del proceso de acabado afectan directamente a la precisión y el efecto del tratamiento superficial. Entre los factores que suelen influir se encuentran la velocidad de rectificado, la presión y la duración del proceso.
- Velocidad de rectificado: Durante el pulido o chorreado, una velocidad demasiado alta dará como resultado una superficie áspera, mientras que una velocidad demasiado baja afectará a la eficacia.
- Ejerciendo presión: Por ejemplo, durante el chorro de arena, una presión demasiado alta puede dañar el material, mientras que una presión demasiado baja puede provocar un tratamiento incompleto.
- Tiempo de proceso: Prolongar el tiempo de esmerilado o grabado suele mejorar el acabado, pero también puede provocar pérdidas de material, por lo que el tiempo debe controlarse estrictamente.
- Condiciones medioambientales
El acabado de superficies tiene requisitos estrictos en cuanto a las condiciones ambientales, y factores ambientales como la temperatura y la humedad afectarán al efecto del procesado.
- Temperatura: Los procesos de tratamiento térmico y químico son muy sensibles a la temperatura. Una temperatura demasiado alta o demasiado baja puede provocar defectos superficiales.
- Humedad: Un entorno con mucha humedad acelerará la reacción de oxidación, lo que no favorece el tratamiento suave de las superficies metálicas. Especialmente en el grabado químico, debe prestarse especial atención a la prevención de la humedad.
- Limpieza: El polvo y las impurezas presentes en el aire pueden adherirse a la superficie de la pieza y provocar un efecto de tratamiento deficiente. Por lo tanto, debe garantizarse la limpieza del entorno durante el proceso de acabado.
- Requisitos de precisión y tolerancia
Los distintos escenarios de aplicación tienen diferentes requisitos de precisión superficial y tolerancia. En el acabado, los parámetros del proceso deben ajustarse en función de los usos específicos.
- Requisitos de acabado: Para las piezas de precisión, como las aeroespaciales o los dispositivos médicos, los requisitos de acabado superficial son extremadamente altos, e incluso una ligera diferencia de rugosidad puede afectar a su funcionalidad.
- Control de tolerancia: Controlar las tolerancias durante el proceso es la clave para garantizar la precisión del ensamblaje de las piezas. Incluso en el mismo lote, cada pieza puede requerir ajustes específicos del proceso para cumplir estrictos requisitos de tolerancia.
Escenarios de aplicación del acabado de superficies
El acabado de superficies tiene una amplia gama de aplicaciones en múltiples industrias, especialmente en la fabricación de automóviles, la decoración arquitectónica, la industria aeroespacial y la electrónica de consumo. A continuación se presenta un análisis en profundidad de cada escenario de aplicación, en el que se detallan los puntos débiles de la demanda, los retos a los que se enfrentan y las soluciones que aporta la tecnología de acabado de superficies en diversos sectores.
- Fabricación de automóviles
- Demanda del sector: En la industria de fabricación de automóviles, el acabado de superficies se utiliza principalmente para mejorar la belleza y la durabilidad de la carrocería y las piezas. La carrocería necesita un aspecto liso, mientras que el motor, la transmisión y otras piezas necesitan resistencia a la corrosión y al desgaste.
- Puntos de dolor comunes: superficie irregular tras el pintado de la carrocería, degradación del rendimiento debido al desgaste de las piezas y corrosión de las piezas metálicas en entornos difíciles.
- Proceso de acabado: El pulido mecánico y el chorro de arena suelen utilizarse para dar más brillo a la superficie. Las tecnologías de galvanoplastia y tratamiento térmico se utilizan para mejorar la resistencia a la corrosión y la dureza de las piezas.
- Un caso típico: Algunas marcas de automóviles de gama alta utilizan una combinación de chorro de arena multicapa y pulido para garantizar que la carrocería pueda presentar un efecto de brillo uniforme en diferentes condiciones de luz y mejorar el impacto visual.
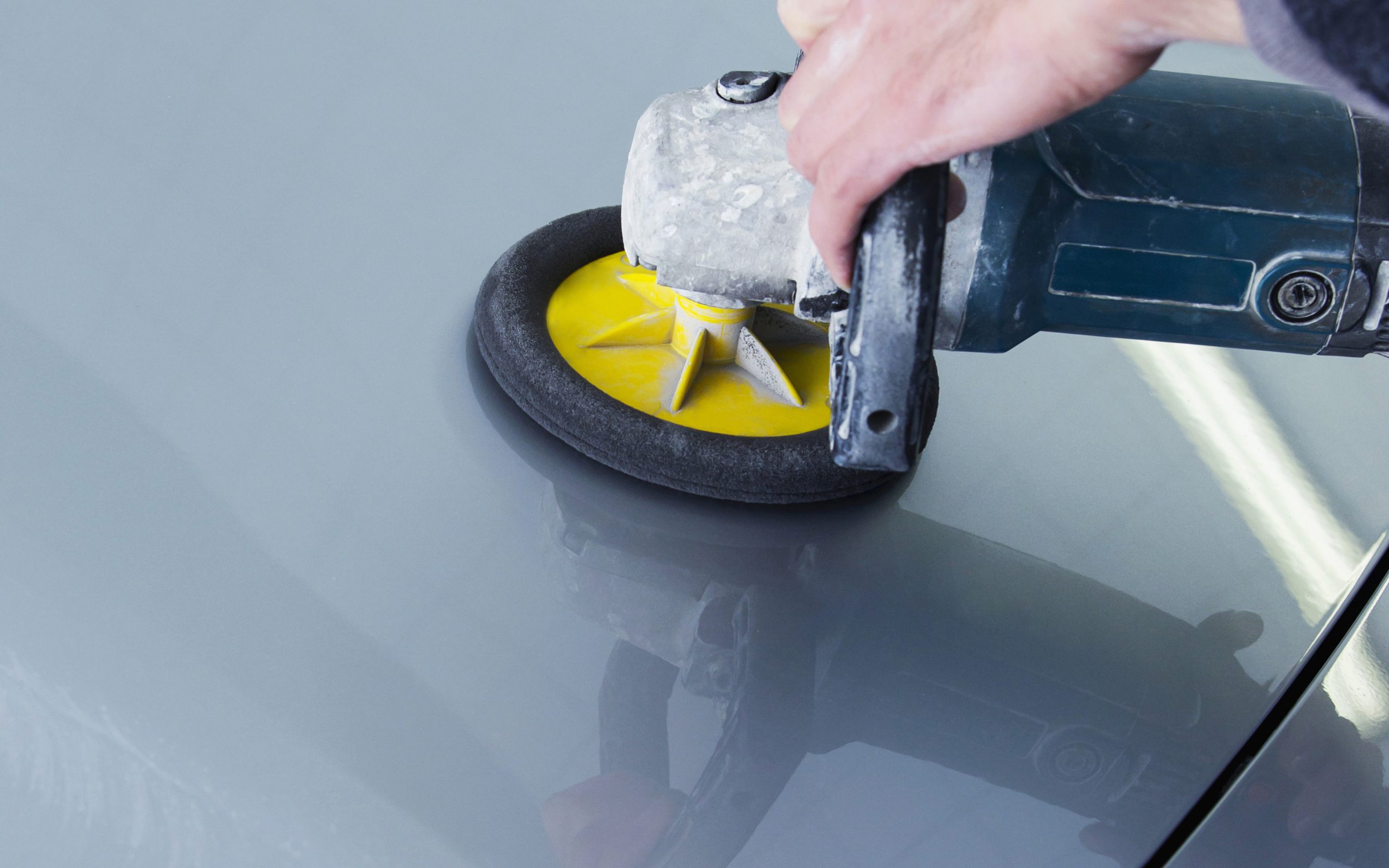
Coches pulidos mecánicamente
- Decoración de edificios
- Demanda del sector: La industria de la decoración de edificios utiliza ampliamente la tecnología de acabado en las superficies de metal, vidrio, mármol y otros materiales para mejorar el aspecto decorativo y la durabilidad de la estructura.
- Puntos de dolor comunes: Los materiales de las paredes exteriores son propensos a la corrosión bajo el sol y la lluvia a largo plazo, hay que mejorar la resistencia a la presión del viento de los materiales acristalados de los edificios altos y los materiales de decoración interior deben ser resistentes a las manchas.
- Proceso de acabado: Las tecnologías de arenado y tratamiento químico se utilizan ampliamente en la superficie de los materiales de decoración de edificios para aumentar la textura o mejorar la resistencia a la intemperie. El pulido mecánico puede utilizarse para el tratamiento superficial de piedras decorativas como el mármol para dar suavidad y efectos estéticos.
- Un caso típico: Muchos edificios modernos utilizan procesos de chorro de arena y grabado en la decoración de las paredes exteriores metálicas para crear un efecto de textura único, que hace que el edificio tenga visualmente más capas.
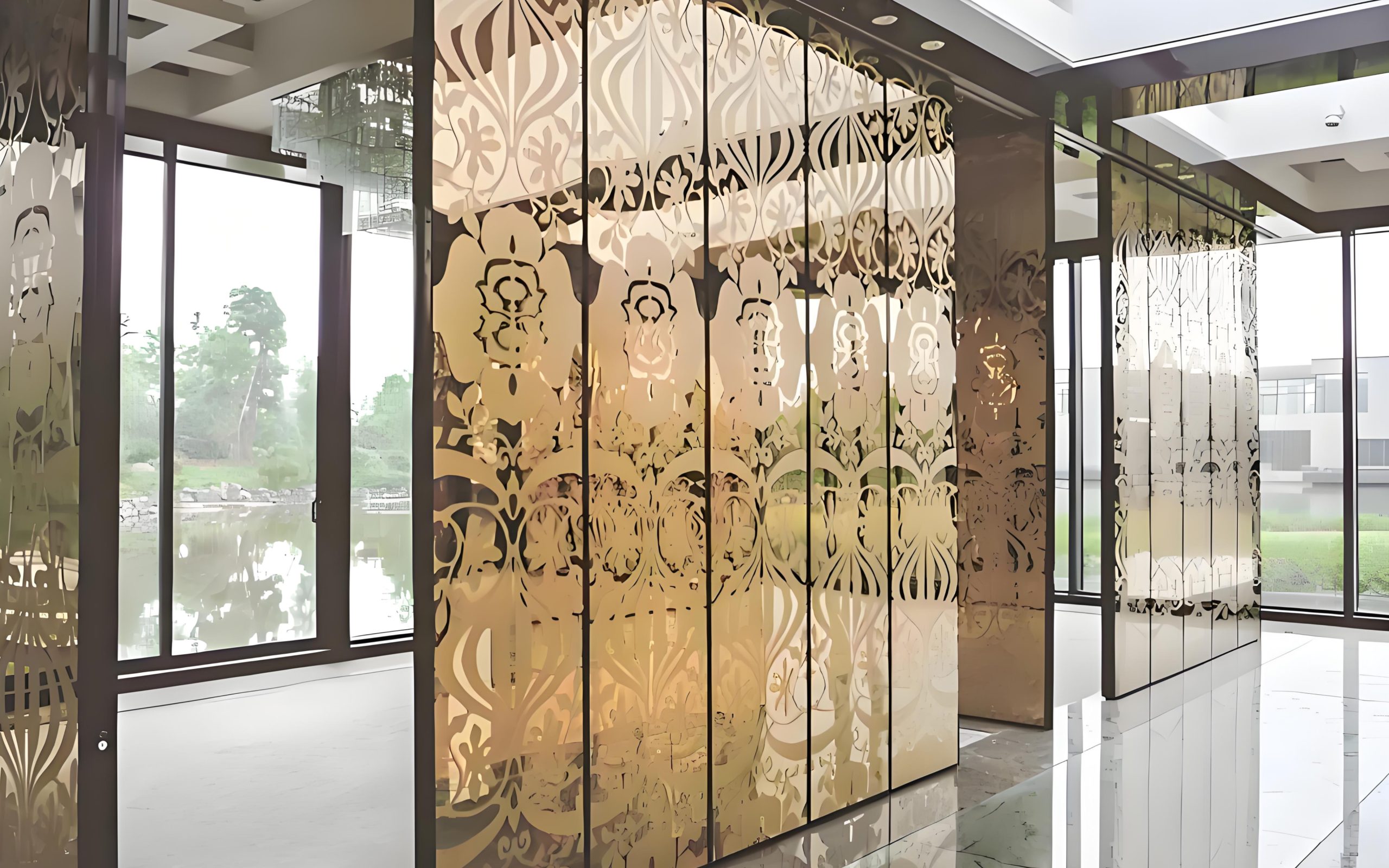
Mampara de cristal grabado
- Aeroespacial
- Demanda del sector: Los materiales de la industria aeroespacial requieren una resistencia extremadamente alta a la corrosión y al desgaste, y el acabado de superficies se utiliza para prolongar la vida útil de los componentes y reducir los costes de mantenimiento.
- Puntos de dolor comunes: Las carcasas de los aviones son propensas a la oxidación y la corrosión en condiciones extremas a grandes altitudes, los componentes del motor son propensos al desgaste a altas temperaturas y el metal de la carrocería tiene que soportar fuertes vientos y presiones.
- Proceso de acabado: El tratamiento térmico y el tratamiento químico son los principales métodos de acabado superficial, que pueden mejorar la dureza y la resistencia a altas temperaturas de los materiales. Además, el chorro de arena puede eliminar las impurezas de la superficie y mejorar la resistencia a la corrosión.
- Un caso típico: Boeing utiliza un proceso especial de niquelado químico para tratar las superficies de las piezas de los motores de los aviones, lo que mejora la resistencia a la corrosión y prolonga la vida útil de las piezas.
- Electrónica de consumo
- Demanda del sector: El aspecto y el tacto de los productos electrónicos de consumo tienen un impacto significativo en la experiencia del usuario, por lo que los procesos de acabado se utilizan ampliamente en carcasas electrónicas, botones y piezas internas.
- Puntos de dolor comunes: La carcasa se raya con facilidad, las piezas se corroen con facilidad tras humedecerse y el brillo de la carcasa de plástico es irregular.
- Proceso de acabado: El pulido mecánico puede dar brillo a la carcasa metálica, el chorro de arena se utiliza para mejorar el tacto y la resistencia al desgaste de las carcasas de plástico o metal, y el tratamiento químico se emplea para mejorar la resistencia a los rayos UV de los plásticos.
- Un caso típico: La carcasa de los productos Apple utiliza múltiples tecnologías de acabado superficial, como el anodizado y el chorro de arena, durante el proceso de producción, lo que hace que sus productos sean excelentes tanto al tacto como en apariencia.
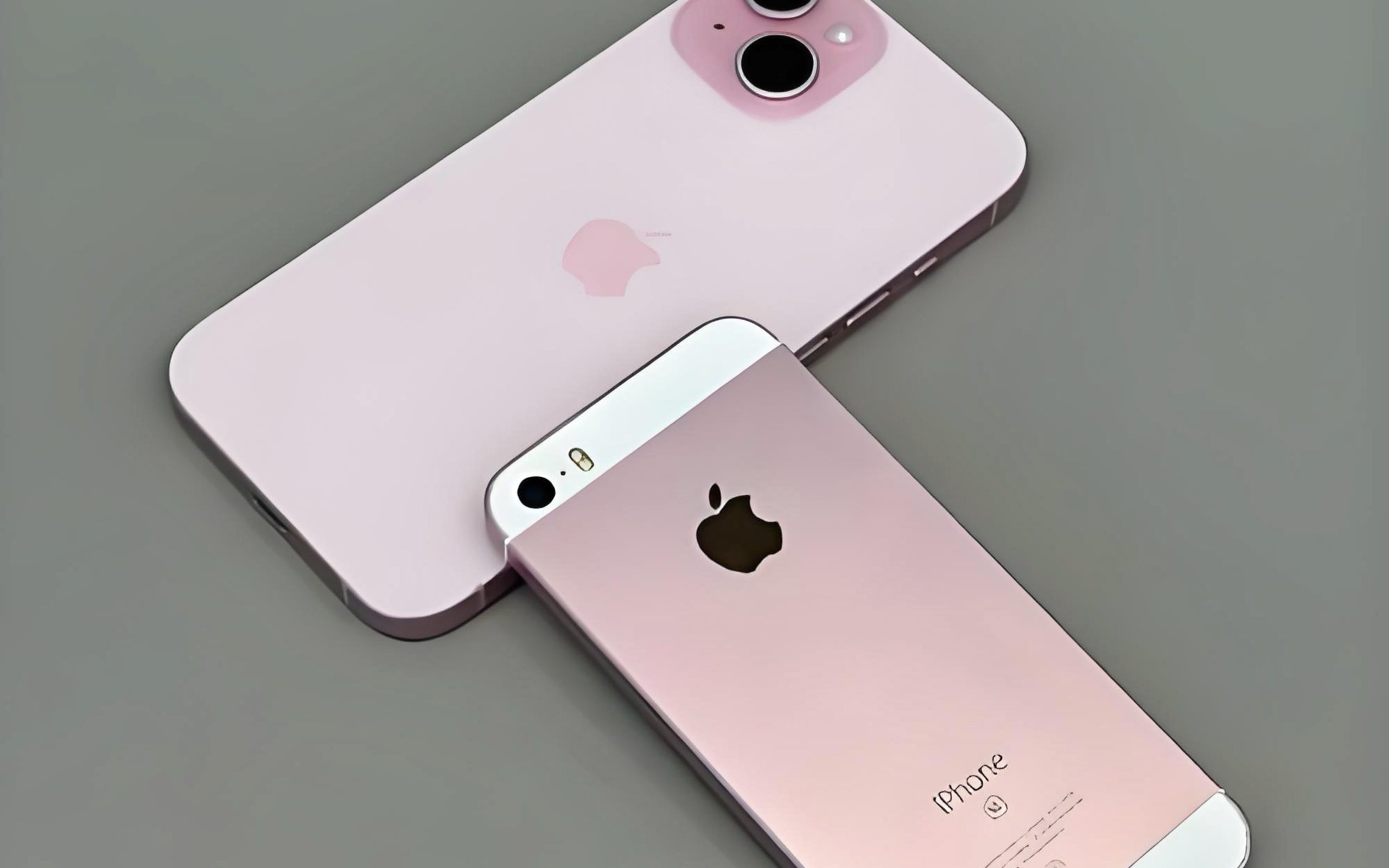
Proceso de anodizado para carcasas de teléfonos móviles
Medios y equipos de arenado
En el proceso de acabado de superficies, el chorro de arena es una tecnología muy utilizada que puede mejorar eficazmente la calidad de la superficie de la pieza y satisfacer diversos requisitos de acabado. Para garantizar un tratamiento eficaz y de alta calidad de las superficies, es esencial seleccionar los medios y equipos de chorreado adecuados. A continuación se presentan varios medios de chorreado de arena de uso común y sus escenarios de aplicación, y se recomiendan los equipos de chorreado de arena adecuados.
Medios de chorreado recomendados
- Cuentas de vidrio
Debido a la forma lisa de sus partículas, las microesferas de vidrio provocan menos arañazos en la superficie durante el procesado y pueden producir un efecto mate uniforme, lo que mejora notablemente el acabado de la superficie.
Adecuado para el pulido fino y la limpieza de superficies de metales y vidrio, normalmente utilizado para piezas decorativas que requieren un acabado superior.
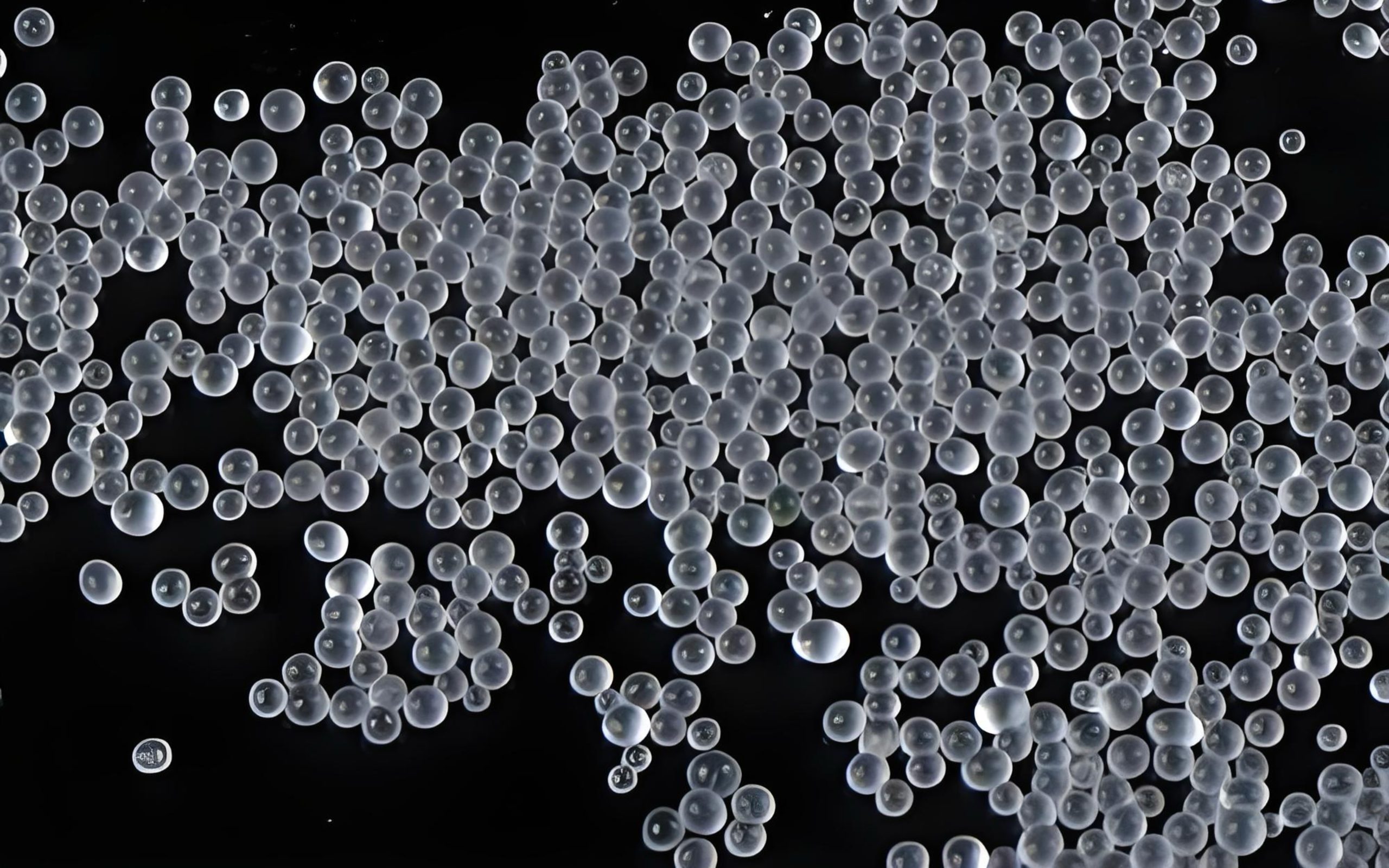
Cuentas de vidrio
- Alúmina
La alúmina tiene una gran dureza y fuerza de corte, puede eliminar rápidamente los defectos de la superficie y produce una buena rugosidad, especialmente adecuada para procesos posteriores de revestimiento o pegado.
Adecuado para el desbaste superficial de metales de alta dureza, cerámica y piedras, especialmente en piezas que necesitan eliminar capas de óxido y suciedad pesada.
Granalla de alúmina
- Carburo de silicio
El carburo de silicio tiene una dureza extremadamente alta y una gran fuerza de corte. Puede eliminar eficazmente la suciedad y los defectos de la superficie de materiales duros y suele utilizarse para el pretratamiento antes del revestimiento.
Se utiliza principalmente para la descontaminación profunda y el desbaste de cerámica, fibras de carbono y algunos metales.
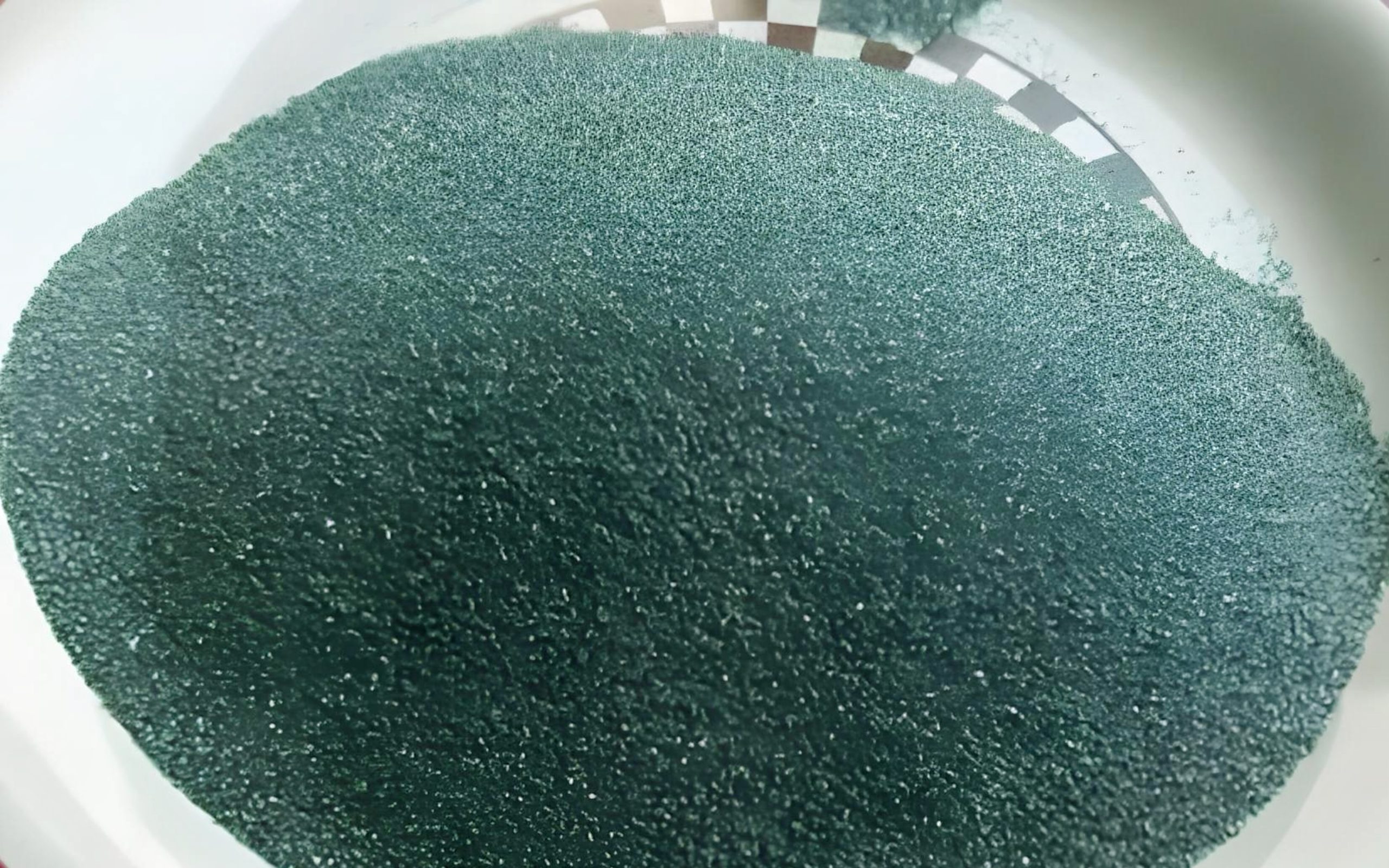
Carburo de silicio
- Cuentas de cerámica
Las microesferas cerámicas tienen una gran dureza y resistencia al desgaste. Son adecuadas para el chorreado a alta presión, pueden reducir los microarañazos y formar una superficie mate uniforme.
Adecuado para el tratamiento de superficies que requieren una alta resistencia al desgaste y necesitan mantener la suavidad, comúnmente utilizado en el rectificado de superficies de maquinaria de precisión y piezas de aviación.
- Soportes de plástico
Debido a sus características de material blando, el chorro de arena de plástico apenas produce arañazos duros en la superficie de la pieza y es adecuado para el tratamiento fino de superficies.
Se utiliza para el tratamiento superficial de materiales más blandos, como aleaciones de aluminio y piezas de plástico, especialmente en escenas en las que no se permite dañar la superficie.
Equipo de chorro de arena recomendado
- Chorreadora a presión
- Características: El rango de presión ajustable de la máquina de chorro de arena a presión es grande, y adecuado para el procesamiento de materiales de diversa dureza, especialmente ampliamente utilizado en los procesos de chorro de arena que requieren alta precisión y alta eficiencia.
- Medios aplicables: perlas de vidrio, perlas de cerámica, óxido de aluminio, etc.
- Chorreadora por aspiración
- Características: Funcionamiento sencillo, adecuada para necesidades de tratamiento de superficies ligeras, especialmente limpieza y pulido de piezas pequeñas.
- Medios aplicables: perlas de vidrio, soportes de plástico.
- Arenadora en húmedo
- Características: Utiliza una mezcla de agua nebulizada y abrasivos, adecuada para el funcionamiento en un entorno sin polvo, y se utiliza principalmente para el procesamiento de piezas de trabajo con requisitos de alta precisión y superficie sin arañazos.
- Medios aplicables: perlas de vidrio, óxido de aluminio.
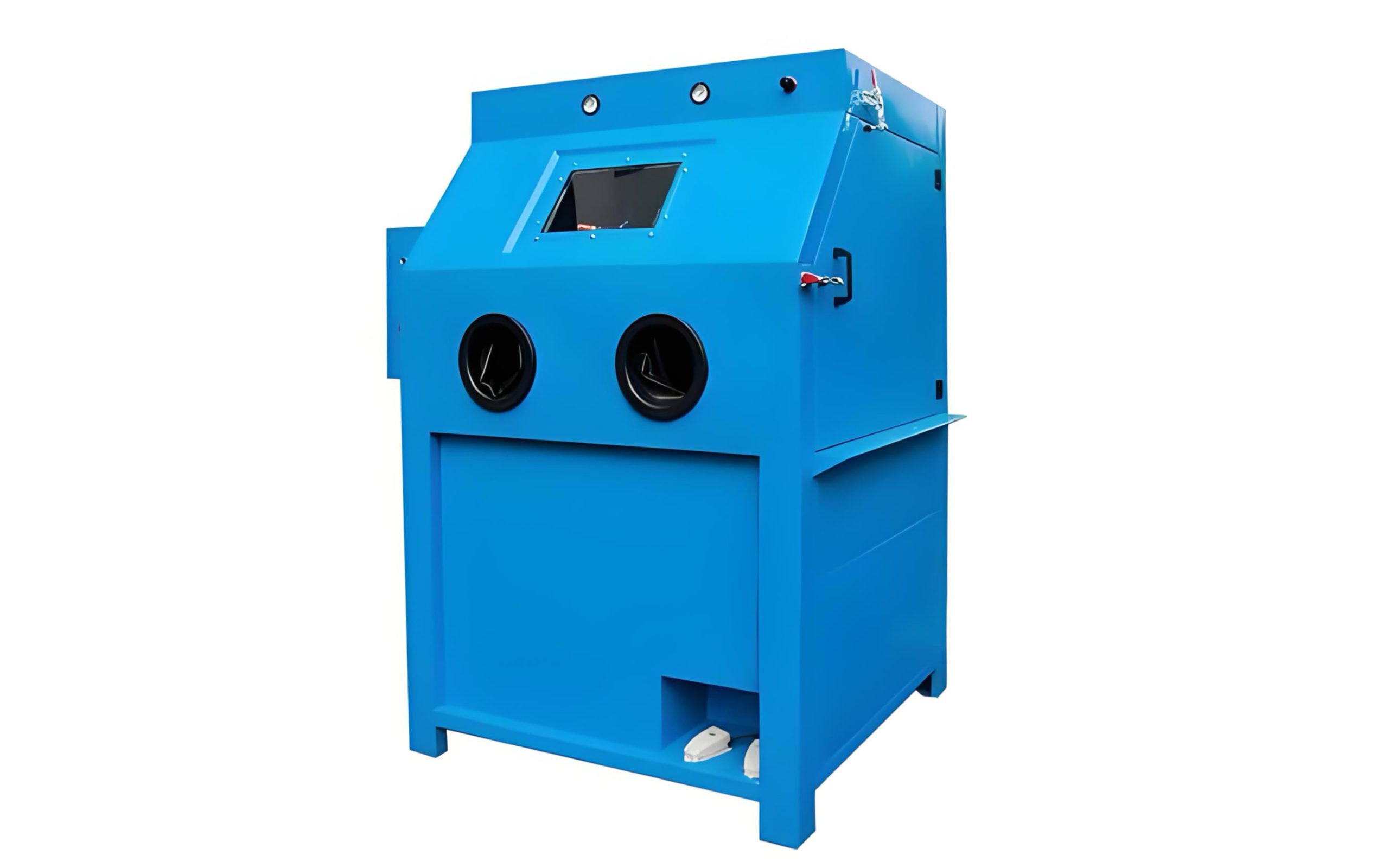
Arenadora en húmedo
- Chorreadora móvil
- Características: Es fácil de mover y manejar, y adecuada para piezas grandes o escenas en las que es difícil operar en lugares fijos, como el tratamiento de superficies de grandes componentes de edificios al aire libre.
- Medios aplicables: óxido de aluminio, carburo de silicio.
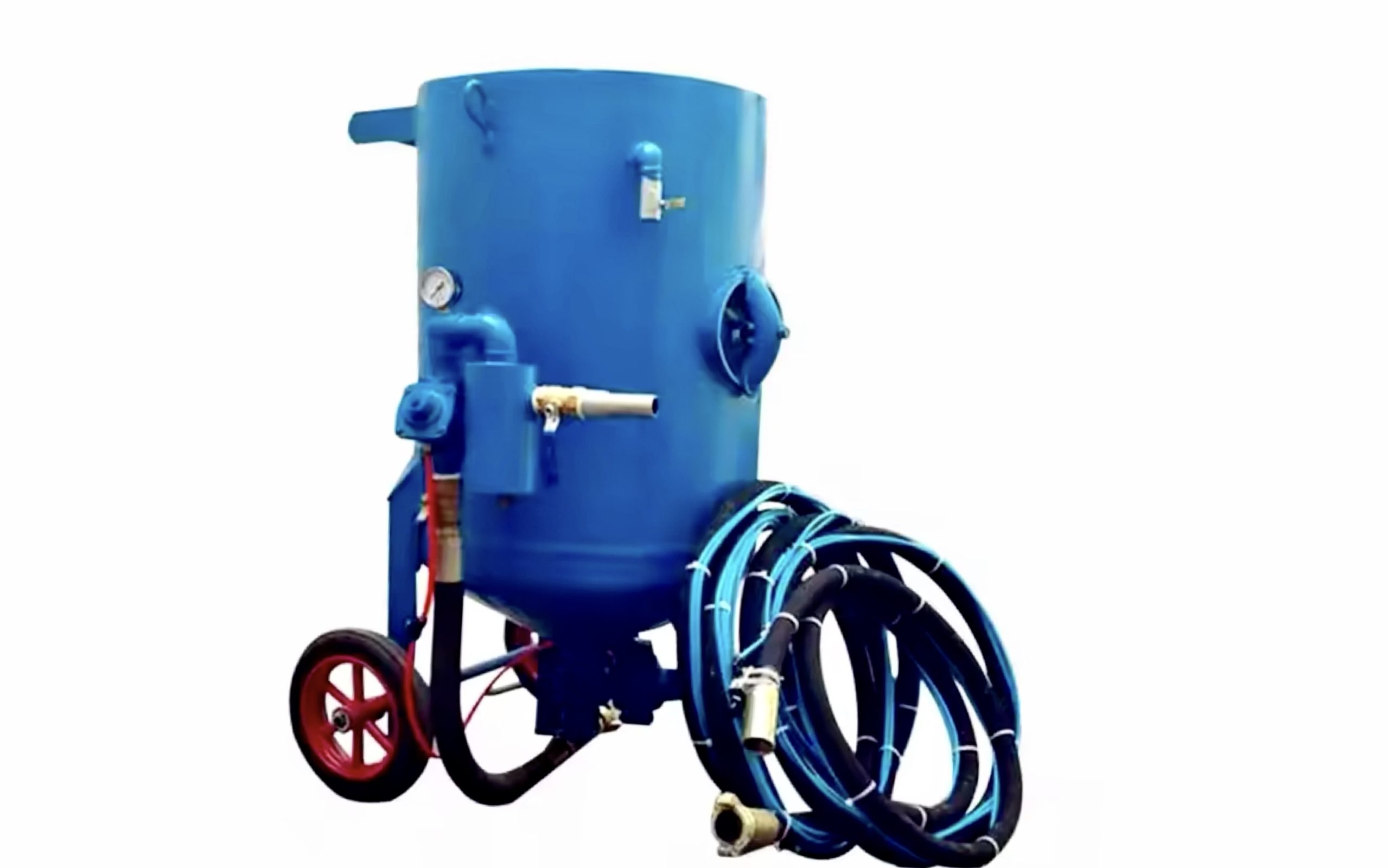
Chorreadora móvil
Cómo elegir los medios y equipos adecuados
La selección de medios y equipos en el acabado de superficies requiere una evaluación exhaustiva basada en el material de la pieza, el acabado requerido y el objetivo de procesamiento. En el caso de materiales duros y desbastado de superficies, es más apropiado elegir medios con mayor dureza, como el óxido de aluminio o el carburo de silicio. Para piezas con elevados requisitos de acabado y daños superficiales, los medios de chorreado con perlas de vidrio y perlas cerámicas combinados con máquinas de chorreado húmedo pueden proporcionar efectos superficiales más idóneos.
Preguntas frecuentes y soluciones (Q&A)
Q: ¿Qué procesos de acabado de superficies son más respetuosos con el medio ambiente y más seguros?
A: El chorro de arena húmedo, el marcado por láser y el pulido electrolítico son relativamente respetuosos con el medio ambiente. El chorro de arena húmedo reduce el polvo mediante nebulización de agua, el marcado por láser no requiere medios químicos y el pulido electrolítico no implica el uso de sustancias nocivas. Al elegir estos procesos, se puede minimizar la contaminación ambiental y los riesgos operativos.
Q: ¿Cómo elegir un método de acabado superficial adecuado para mi pieza?
A: Hay que tener en cuenta factores como el material de la pieza, el efecto de la superficie objetivo y la economía. Para piezas con elevados requisitos de acabado, puede optarse por el pulido o el pulido electrolítico; para piezas con requisitos especiales de rugosidad superficial, pueden ser más adecuados el chorro de arena y el grabado láser.
Q: ¿Cómo reducir el problema de la oxidación de las superficies metálicas?
A: Trate el metal con un revestimiento antioxidante, seleccione un proceso de pulido adecuado y utilice aceite antioxidante. El pulido electrolítico puede eliminar eficazmente la capa de óxido y formar una superficie lisa para reducir la aparición de oxidación.
Q: ¿Cuáles son las precauciones de seguridad en el tratamiento químico?
A: Los operarios deben llevar ropa de protección adecuada, guantes, gafas, etc., y trabajar en un entorno bien ventilado. Para procesos como el decapado, siga estrictamente las especificaciones de uso de productos químicos y asegúrese de que existen medidas de emergencia adecuadas para hacer frente a posibles fugas de productos químicos o al contacto humano.
Q: ¿Cómo evitar efectos desiguales durante el tratamiento de superficies?
A: La uniformidad del tratamiento de superficies se ve afectada por múltiples factores, como los parámetros del proceso, las habilidades del operario y la estabilidad del equipo. La elección del equipo y los parámetros de proceso adecuados y el mantenimiento periódico del equipo pueden evitar eficazmente los efectos de superficie desigual.
Q: ¿Cuál es la diferencia entre chorro de arena, pulido y tratamiento químico?
A: El arenado es adecuado para eliminar óxidos superficiales o tratar superficies rugosas, mientras que el pulido se utiliza para mejorar el acabado superficial. El tratamiento químico (como el decapado) se utiliza principalmente para eliminar contaminantes y capas de óxido en la superficie metálica. La elección de cada proceso debe determinarse en función de los requisitos y las características de la pieza.
Q: ¿Cómo tratar la superficie de la pieza tras el acabado superficial?
A: La pieza tratada suele necesitar más protección. En el caso de las superficies metálicas, puede aplicarse una capa protectora (como aceite antioxidante), mientras que materiales como el vidrio y el plástico pueden necesitar ser calentados o pulidos para mantener la durabilidad del efecto superficial.
Q: ¿Cómo garantizar la coherencia del proceso de tratamiento de superficies?
A: Para garantizar la coherencia, los parámetros del proceso (como la presión, la temperatura, el tiempo de tratamiento, etc.) deben controlarse estrictamente y deben utilizarse equipos automatizados para reducir los errores humanos. Además, se realizan inspecciones periódicas del proceso para garantizar la normalización de cada tratamiento.
Q: ¿Por qué es necesario tratar la superficie antes de pintar?
A: El tratamiento de superficies elimina impurezas, óxidos y contaminantes para que la superficie de la pieza sea más lisa y limpia, y mejorar la adherencia y durabilidad del revestimiento. En el caso de las piezas metálicas, el tratamiento superficial es un paso necesario antes del pintado para garantizar el rendimiento y la vida útil del revestimiento.
Q: ¿Será perjudicial para la salud humana la superficie tratada químicamente?
A: Debe tenerse en cuenta la seguridad durante el tratamiento químico (como el decapado y la fosfatación). Un funcionamiento razonable y el uso de productos químicos respetuosos con el medio ambiente pueden minimizar los riesgos para la salud. Los operarios deben llevar el equipo de protección adecuado, evitar el contacto directo con los productos químicos y asegurarse de que el entorno de trabajo cumple las normas de seguridad.
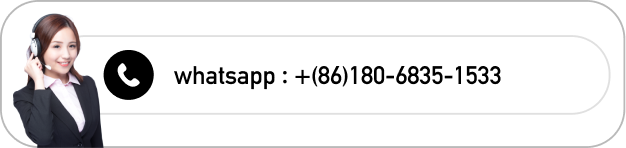