Acabado de moldes: problemas comunes y soluciones para el acabado superficial
17 de enero de 2025
El acabado superficial es una de las consideraciones más importantes en el acabado de moldes. No sólo afecta a la belleza y funcionalidad de las piezas, sino que también determina directamente la vida útil del molde y la calidad del producto. Desde los dispositivos médicos hasta las piezas de automoción, los distintos sectores tienen diferentes requisitos de superficie para los moldes. Los materiales del molde, las tolerancias, las texturas, el rendimiento del desmoldeo, las características de flujo del material y los métodos de procesamiento afectarán al efecto del acabado final. Este artículo se centrará en el problema del acabado superficial de los moldes, analizará sus causas y ofrecerá soluciones para ayudar a los fabricantes de moldes a hacer frente a los complejos retos del procesamiento.
Problemas comunes con el acabado de la superficie del molde
Rugosidad desigual de la superficie
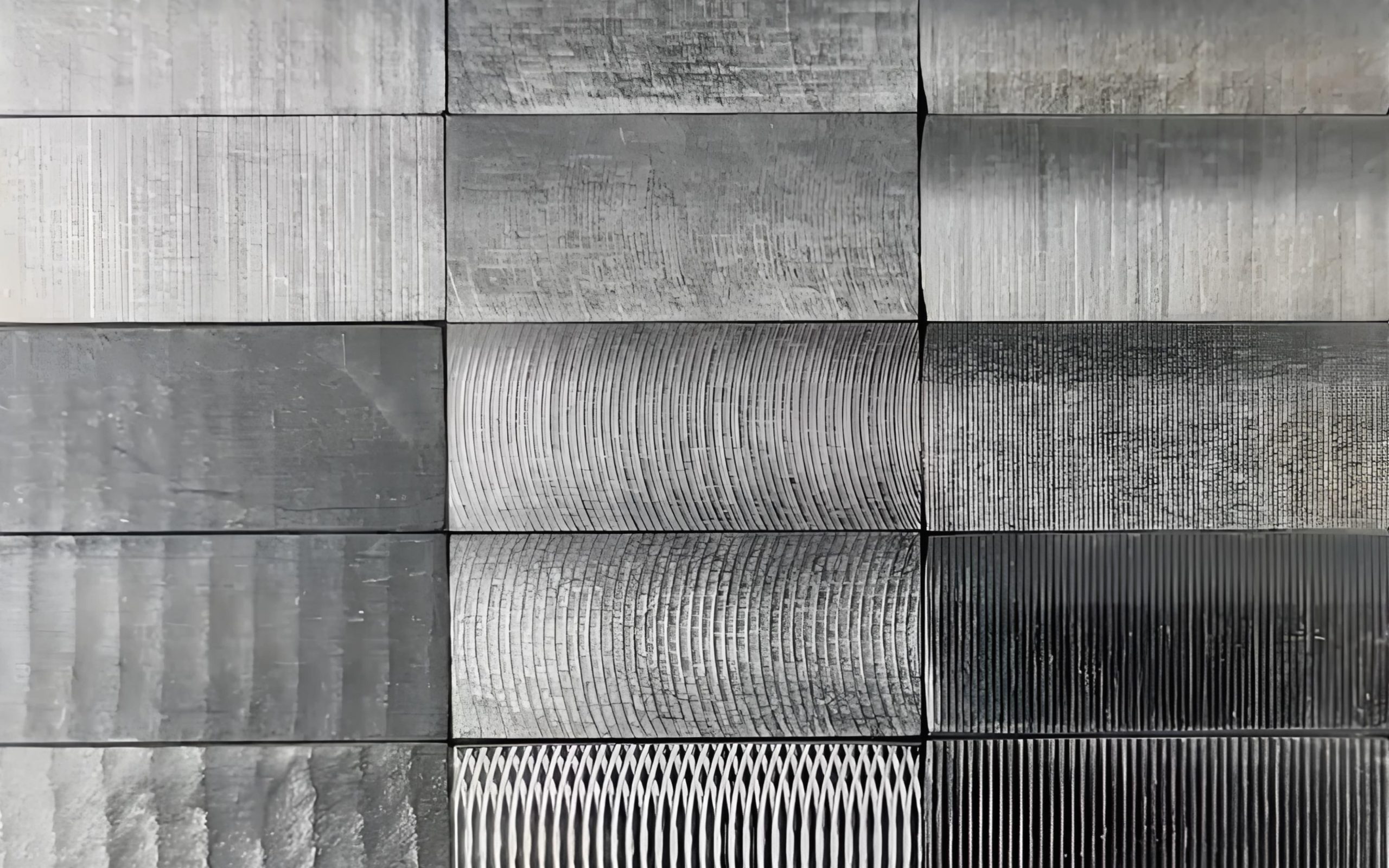
Manifestación del problema
- La rugosidad de las distintas zonas de la superficie del molde es muy diferente, lo que afecta a la consistencia del producto.
- La zona de altas luces y la posición de los bordes son propensas a una rugosidad excesiva.
- En la superficie aparecen importantes marcas de cuchilla tras el mecanizado CNC, que afectan al acabado y al efecto visual.
- La textura de algunas zonas es diferente en profundidad, lo que afecta al efecto de pulido posterior.
Análisis de causas
- Precisión de mecanizado insuficiente y falta de optimización de las zonas complejas.
- El desgaste de la herramienta no se sustituye a tiempo, lo que afecta a la calidad de la superficie.
- Ajuste inadecuado de los parámetros del proceso, coincidencia poco razonable de la velocidad de avance y la velocidad de rotación, lo que provoca diferencias en la textura de la superficie.
- Proceso de tratamiento superficial imperfecto, selección inadecuada del medio en las fases de pulido y chorreado.
Los defectos superficiales dificultan el desmoldeo
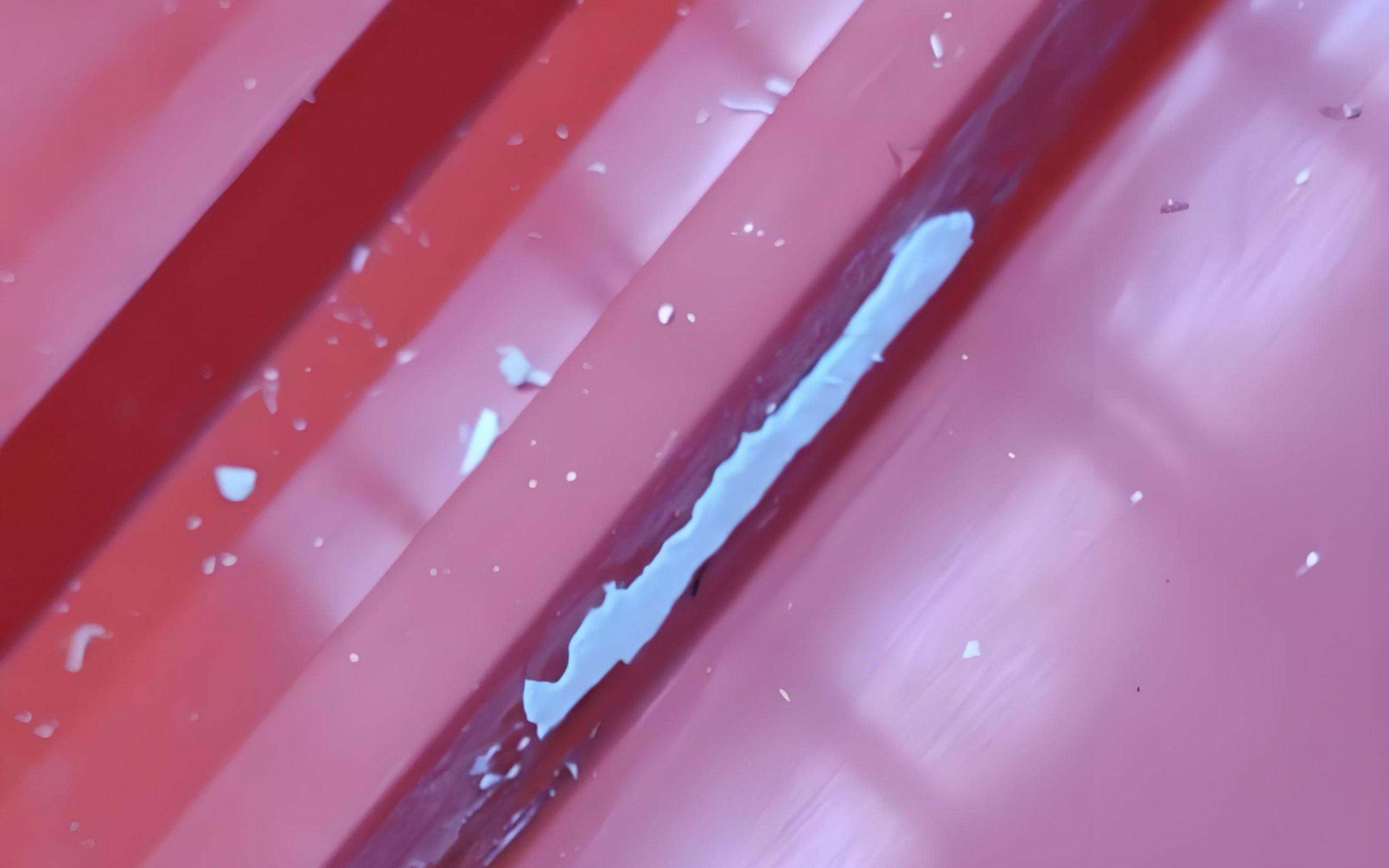
Manifestación del problema
- El material se adhiere a la superficie del molde durante el desmoldeo, lo que afecta a la eficacia de la producción.
- Algunos termoplásticos o siliconas producen marcas de dibujo o residuales después del desmoldeo.
Análisis de causas
- Un acabado insuficiente y una superficie rugosa aumentan la adherencia de los materiales en la cavidad del molde.
- Diseño irrazonable del ángulo de desmoldeo y no consideración completa de los requisitos de desmoldeo de formas geométricas complejas.
- Falta de textura superficial, especialmente para materiales pegajosos como la silicona, la superficie lisa puede aumentar las dificultades de desmoldeo.
Grietas superficiales y problemas de burbujas
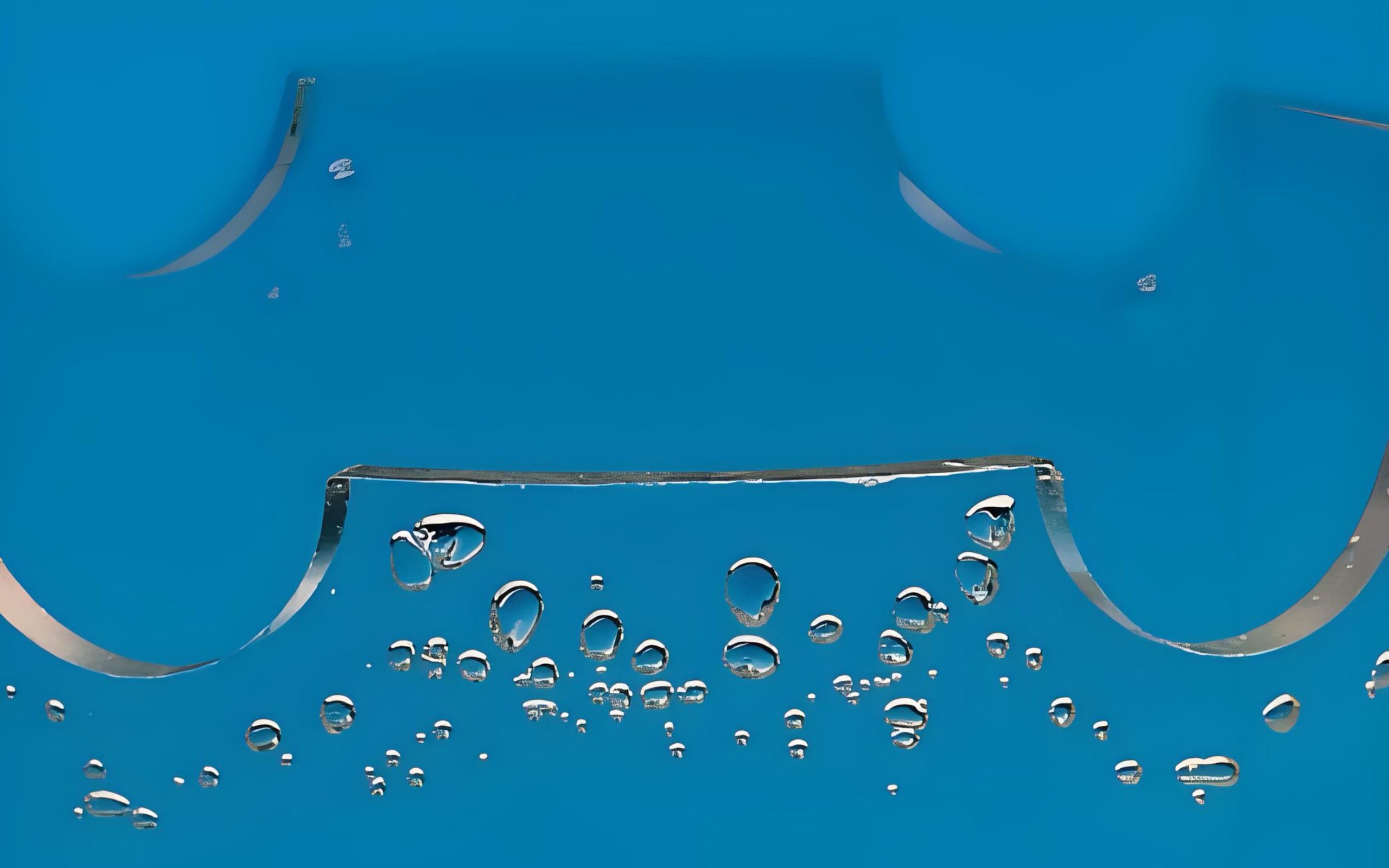
Manifestación del problema
- Aparecen arañazos o motas plateadas en la superficie de la pieza, que afectan a su aspecto y resistencia.
- La extensión de la grieta puede hacer que la pieza falle en la aplicación.
Análisis de causas
- El contenido de agua del material de moldeo por inyección es demasiado alto y se generan burbujas durante el enfriamiento.
- El diseño de la ventilación del molde no es razonable, y el gas no puede ser descargado de la cavidad del molde sin problemas, lo que resulta en la formación de grietas.
- Ningún tratamiento eficaz de reparación y refuerzo de grietas después del procesamiento.
Las impurezas superficiales afectan a los resultados del tratamiento
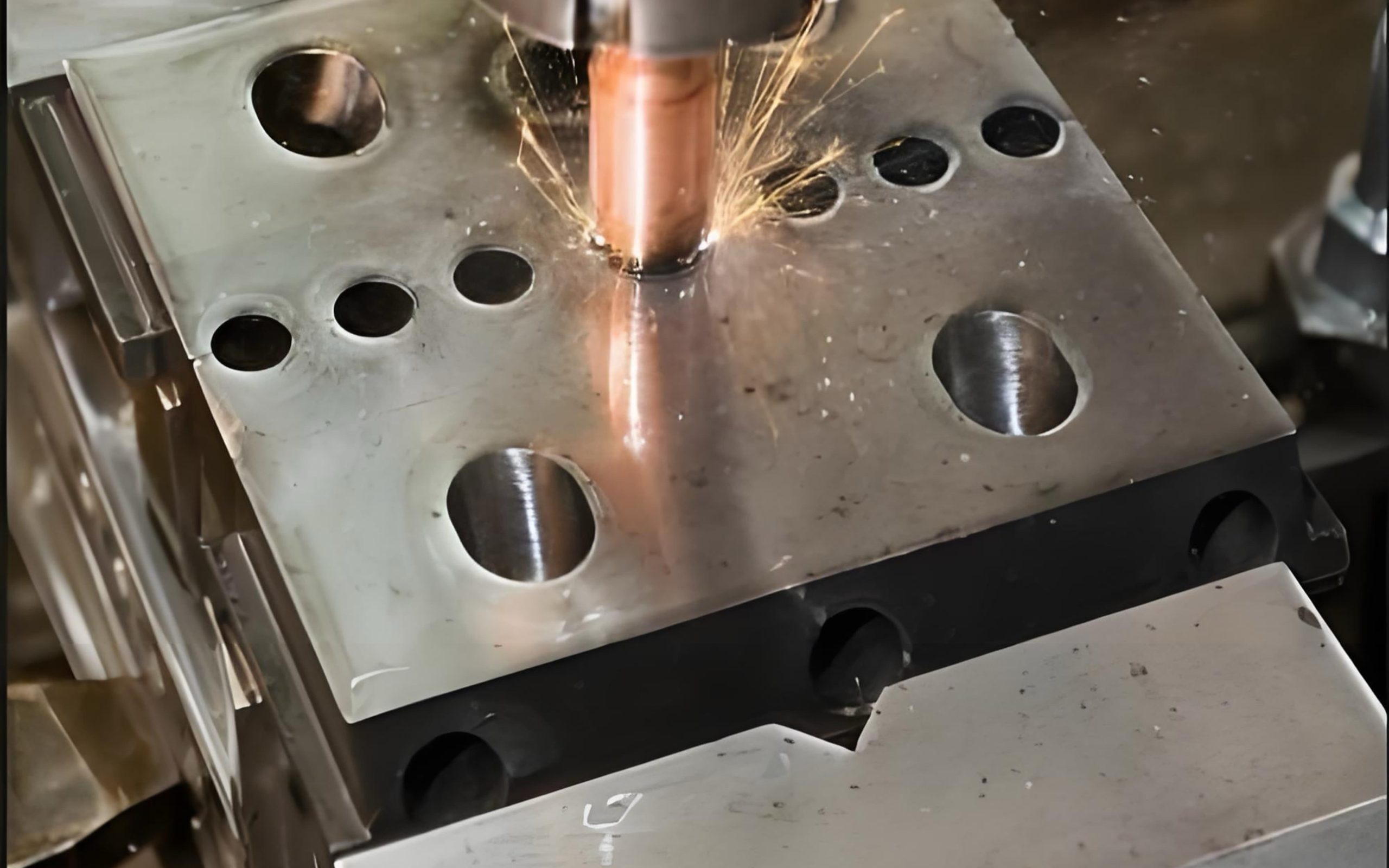
Manifestación del problema
- El polvo o las partículas aún permanecen en la superficie del molde después del arenado o pulido.
- Las impurezas afectan al efecto de los posteriores pasos de recubrimiento o procesado.
Análisis de causas
- Se utilizan perlas de vidrio ordinarias o medios de calidad inferior, y la eficacia de la limpieza es baja.
- Los parámetros de arenado inadecuados, el ángulo o la presión de pulverización no optimizados y las impurezas no pueden eliminarse por completo.
- Falta de pasos de limpieza posteriores o procesos no estandarizados.
Insuficiente fluidez del material
Manifestación del problema
- Durante el proceso de moldeo por inyección, el material no puede llenar la cavidad del molde, lo que da lugar a un moldeo incompleto de la pieza.
- En el molde aparecen problemas como una presión de llenado insuficiente, marcas de material frío o soldaduras.
Análisis de causas
- Una superficie demasiado rugosa o brillante modifica la trayectoria de flujo del material y aumenta la resistencia.
- Defectos de diseño de los canales: posición y tamaño inadecuados de las compuertas y optimización insuficiente de la eficacia de llenado del material.
- Un enfriamiento desigual provoca la solidificación prematura del material.
Solución
Preparación antes de la transformación
- Pretratamiento del material para garantizar que el material esté completamente seco antes del moldeo por inyección y controlar el contenido de humedad.
- Utilice software para optimizar la textura y el diseño del canal de flujo para garantizar un flujo uniforme y la consistencia de la textura.
Optimización del proceso
- En combinación con la tecnología de mecanizado de cinco ejes, ajuste el espaciado de la trayectoria, reduzca las marcas de la herramienta y mejore la uniformidad de la superficie.
- Utiliza tecnología de fresado de alta velocidad para optimizar la relación de alimentación y velocidad y controlar con precisión la calidad de procesamiento.
- Actualización de equipos, máquinas herramienta CNC de alta precisión y tecnología de grabado por láser para mejorar la capacidad de procesamiento de texturas complejas y detalles.
- Detección en tiempo real del desgaste de las herramientas y sustitución oportuna para garantizar la estabilidad del procesamiento.
Limpieza posterior y tratamiento de superficies
- Utilice granos de chorro de arena cerámicos y otros medios para chorrear con arena a fin de eliminar los residuos del procesado y garantizar la suavidad.
- Añada limpieza ultrasónica o purga de gas para eliminar por completo las impurezas diminutas.
- Combinado con pulido espejo o chorro de arena para el tratamiento de refuerzo, mejora aún más la durabilidad de la superficie y reduce las microfisuras.
Desmoldeo y optimización posterior
- Ajuste la pendiente del molde, añada texturas auxiliares, optimice el rendimiento del desmoldeo y evite problemas de adherencia.
- Añada revestimientos antiadherentes a las piezas clave para reducir los coeficientes de fricción y mejorar la eficacia del desmoldeo.
- Utilice un sistema de control de temperatura por zonas y optimice el diseño de los conductos de ventilación para reducir la refrigeración desigual y los problemas de burbujas.
Verificación y mejora de procesos
- Optimice los patines y las compuertas para que el material se llene por completo y de manera uniforme.
- Prueba final: Evaluar el uso real del molde para garantizar que la textura, el acabado y la funcionalidad cumplen plenamente los requisitos.
Los medios de chorreado ayudan a conseguir el acabado superficial
En el proceso de acabado de moldes, el chorro de arena es una tecnología indispensable que puede compensar eficazmente las deficiencias de otros métodos de procesamiento y optimizar la calidad de la superficie. Especialmente en la solución de pequeñas texturas de procesamiento, residuos de impurezas y defectos superficiales, la selección de los medios de chorro de arena es particularmente crítica. Entre ellos, los granos de chorro de arena cerámicos se han convertido en una opción ideal para mejorar el acabado superficial de los moldes gracias a su excelente rendimiento. Sus ventajas son las siguientes
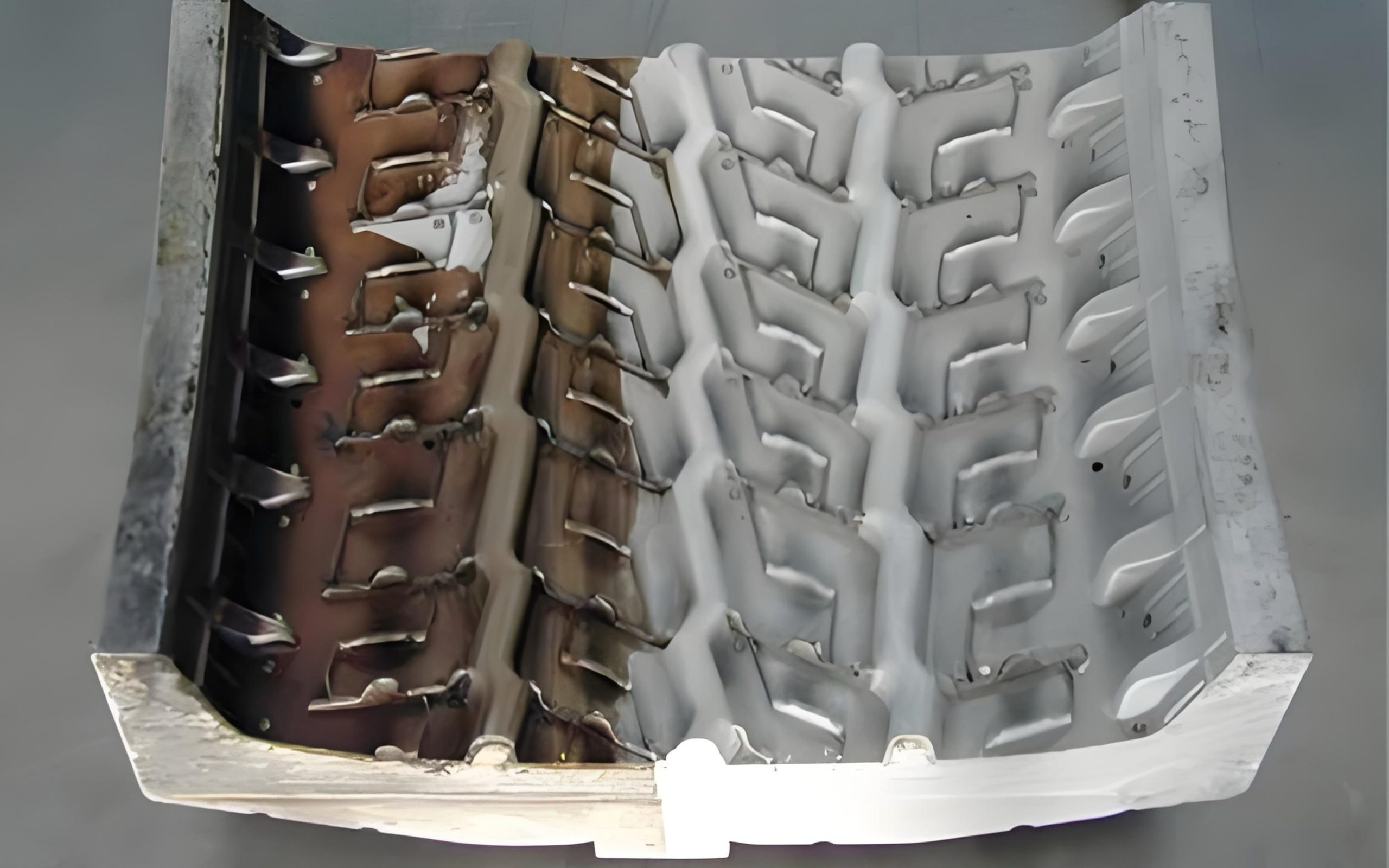
Eliminar microfisuras y texturas de procesamiento. Las microesferas cerámicas tienen una elevada dureza Mohs y partículas uniformes. Pueden eliminar eficazmente las microfisuras y texturas dejadas por el procesamiento de herramientas sin dañar la superficie del molde, y optimizar el acabado.
Mejorar la consistencia de la superficie. Los medios cerámicos tienen una distribución de densidad uniforme y un tamaño consistente, lo que puede cubrir uniformemente la superficie del molde para evitar problemas funcionales y de apariencia causados por una textura desigual o una rugosidad local excesiva.
Reduce los problemas de adherencia. Las perlas cerámicas tienen una buena suavidad superficial y características de bajo polvo, lo que puede reducir eficazmente el coeficiente de fricción de la superficie del molde y reducir los daños causados por la adhesión del material durante el proceso de desmoldeo.
Mejorar la durabilidad de la pieza. El chorro de arena también puede reforzar la superficie del molde, mejorar su resistencia a la fatiga y a la corrosión, y prolongar la vida útil del molde.
Optimizar el entorno de trabajo. En comparación con los granos de vidrio tradicionales, los granos de chorro de arena cerámicos tienen menos polvo, lo que no sólo mejora la precisión del procesamiento, sino que también reduce los riesgos para la salud.
Combinando las ventajas de los granos de chorro de arena cerámicos, los fabricantes de moldes no sólo pueden mejorar significativamente el acabado superficial, sino también evitar eficazmente problemas comunes como grietas, impurezas superficiales y dificultades de desmoldeo, proporcionando a los clientes soluciones de moldes de alto rendimiento.
Si necesita recomendaciones más detalladas sobre el proceso de arenado y los medios, puede póngase en contacto con nosotros.
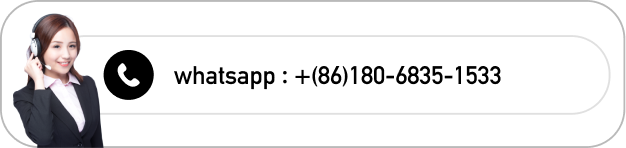