Cómo elegir materiales de chorreado según la forma de la pieza? Guía completa
8 de octubre de 2024
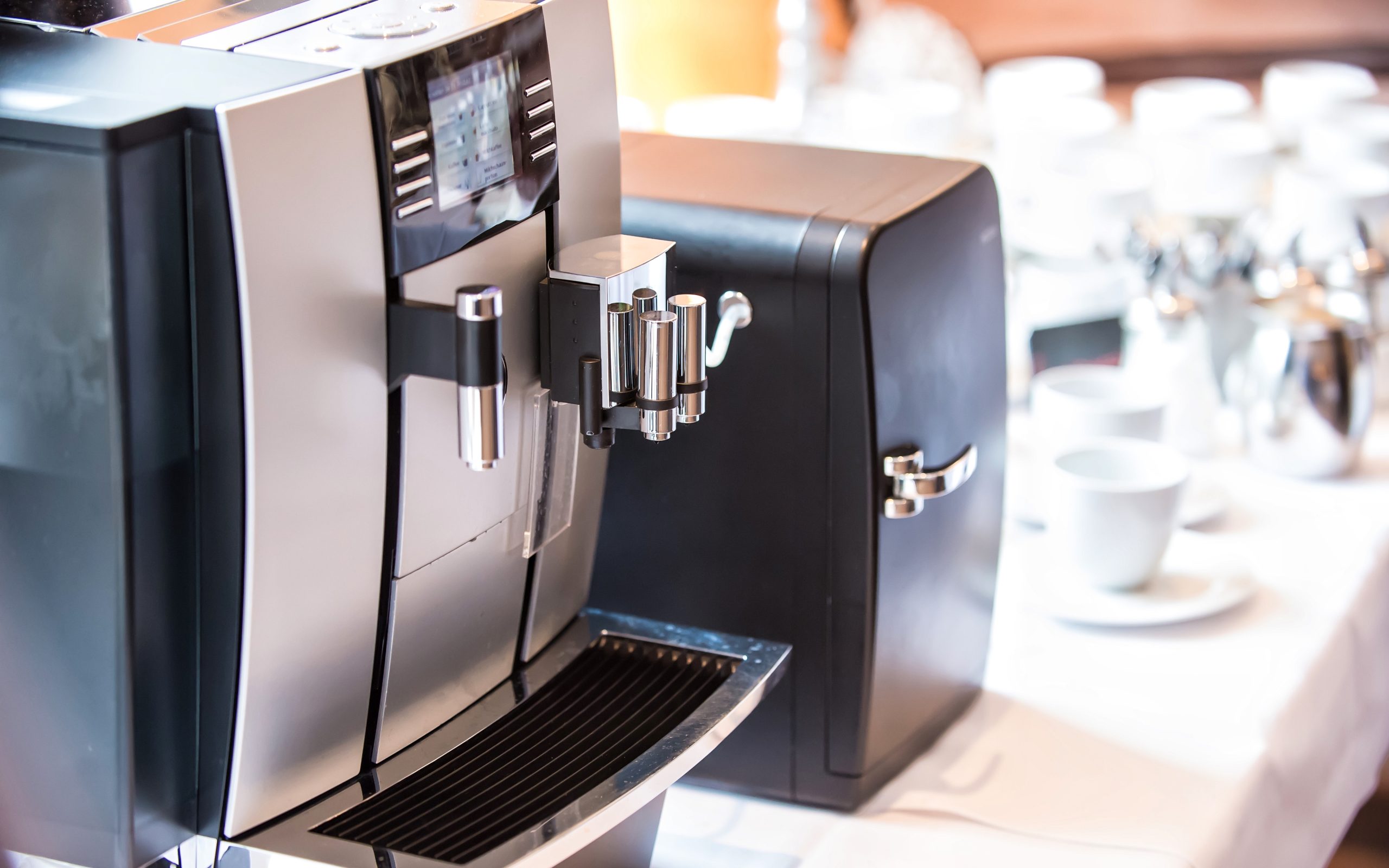
El chorreado de arena desempeña un papel vital en la fabricación moderna, especialmente en el proceso de tratamiento superficial de las piezas. Mediante la pulverización de diferentes tipos de materiales de chorro de arena, podemos eliminar eficazmente las impurezas de la superficie, pulir las superficies irregulares y mejorar la calidad del aspecto de los productos. La forma de las diferentes piezas determina la elección de los materiales de chorro de arena, y la forma de elegir los materiales de chorro de arena adecuados según la forma de las piezas afecta directamente al efecto y la eficacia del chorro de arena.
En este artículo, primero enumeraremos varias formas de piezas comunes, analizaremos las características de cada forma y los retos que pueden encontrar durante el chorreado. A continuación, propondremos una selección adecuada del material de chorreado basada en estas formas, especialmente para algunas piezas más complejas o de alta precisión, cómo utilizar de forma flexible dos o más materiales de chorreado para lograr el efecto de tratamiento ideal.
Formas y requisitos habituales de las piezas
- Piezas planas y de gran superficie
Este tipo de pieza es muy común en muchos campos, como la fabricación de automóviles, la industria de la construcción y la producción de electrodomésticos. Algunos ejemplos concretos son los paneles de carrocería de automóviles, las carcasas metálicas de electrodomésticos, los muros cortina de cristal para edificios, etc. En el caso de estas piezas, es especialmente importante mantener la superficie lisa y plana, ya que suelen utilizarse como parte de presentación externa del producto, lo que afecta directamente a su estética y reconocimiento en el mercado.
Para este tipo de piezas, el proceso de chorreado suele requerir el tratamiento rápido de grandes superficies. En este caso, los medios de chorreado de óxido de aluminio son una opción ideal porque las partículas de óxido de aluminio son duras y tienen fuertes fuerzas de corte, lo que puede eliminar rápidamente grandes áreas de óxidos e impurezas manteniendo una superficie uniforme. Además, se pueden utilizar diferentes tamaños de partículas de óxido de aluminio para ajustar la rugosidad de la superficie a los distintos requisitos del proceso.
Algunas piezas planas requieren una gran suavidad superficial además de eliminar las impurezas durante el proceso, especialmente las superficies de vidrio o acero inoxidable. En este caso, puede utilizarse granalla de perlas cerámicas, que tiene partículas redondeadas y puede pulir la superficie a la vez que elimina la suciedad.
- Piezas redondas y cilíndricas
Las piezas cilíndricas se utilizan ampliamente en la fabricación de maquinaria, petroquímica, ingeniería de tuberías y otros campos. Por ejemplo, piezas como ejes de transmisión, cilindros hidráulicos y juntas de tuberías son comunes en industrias de fabricación de alta gama como la automovilística, la aeronáutica y la aeroespacial. La dificultad del chorreado de este tipo de piezas radica en que es necesario garantizar la uniformidad de todo el tratamiento superficial, especialmente en la zona de transición de la sección transversal circular.
Para el tratamiento de superficies de piezas redondas, el granallado con perlas cerámicas es la opción más idónea. Este medio tiene buena tenacidad y resistencia al desgaste, y también puede proporcionar un efecto de molienda uniforme. No dañará la superficie de la pieza debido a las partículas duras. Es adecuado para el tratamiento de piezas redondas, especialmente algunas piezas cilíndricas de precisión, como los ejes de turbina de motores aeronáuticos, que normalmente necesitan minimizar el desgaste durante el tratamiento.
En algunos casos, la superficie de las piezas cilíndricas necesita alcanzar un acabado muy alto. En ese momento, se pueden utilizar medios de granallado de óxido de aluminio ultrafino en combinación, especialmente cuando se procesan zonas que requieren un control preciso.
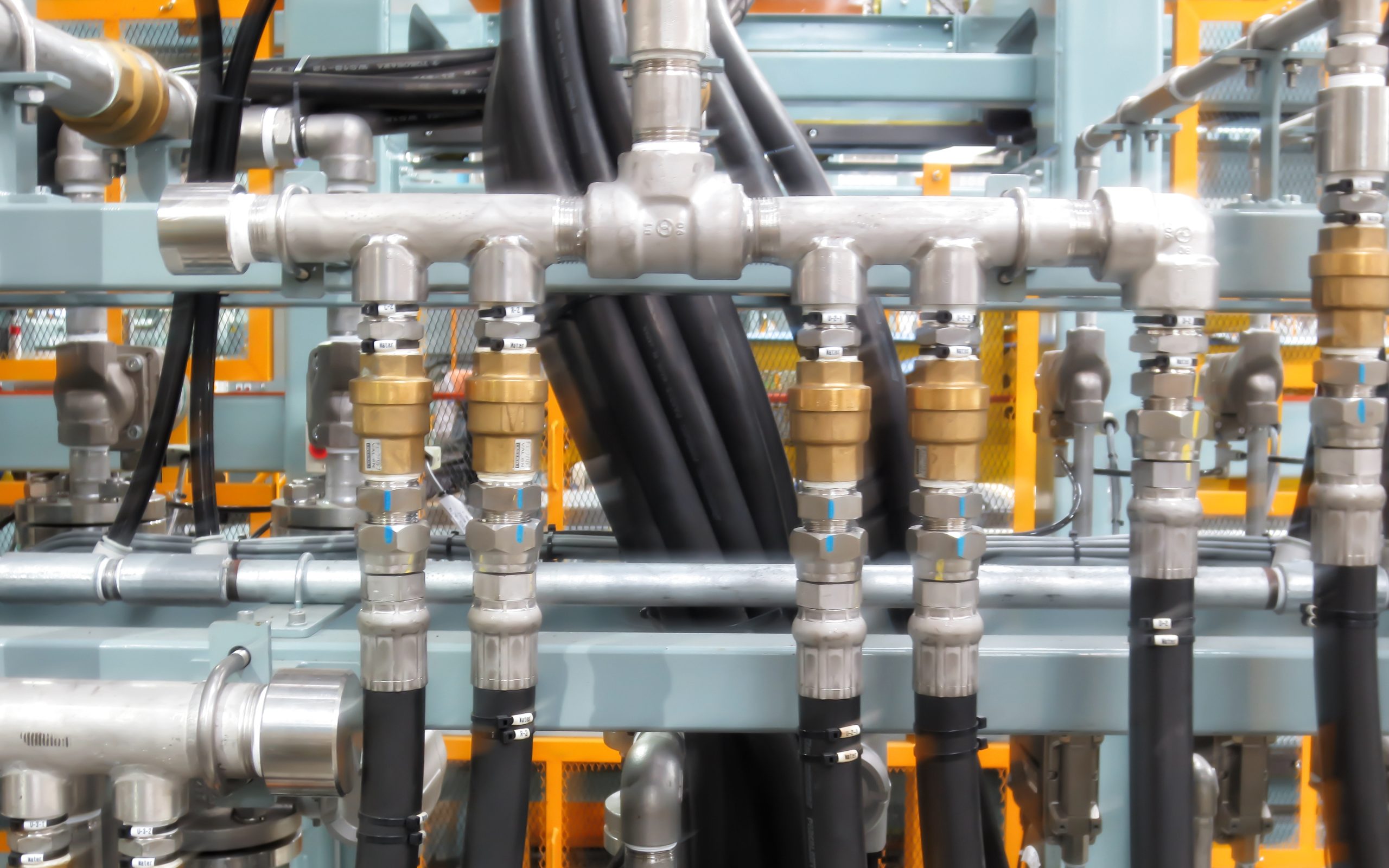
- Formas geométricas complejas y piezas poliédricas
Las piezas de geometría compleja son muy comunes en la industria manufacturera, especialmente las carcasas de motores, álabes de turbinas, carcasas de equipos electrónicos, etc. Tomemos como ejemplo la carcasa del motor. Suele tener una estructura poliédrica con múltiples rebajes y esquinas. En este tipo de piezas, es fácil que se produzcan esquinas muertas al chorrearlas. Si no se trata adecuadamente, algunas zonas no se tratarán correctamente, lo que afectará a la calidad general de la superficie de las piezas.
Para resolver este problema, se recomiendan las bolas de chorreado de óxido de circonio. La alta densidad y dureza del óxido de circonio garantizan un fuerte impacto al eliminar los residuos, y pueden limpiar algunas esquinas y pequeños huecos. Su elevada dureza lo hace especialmente adecuado para el tratamiento superficial de piezas de aleaciones de alta resistencia.
En algunos casos en los que se requiere un tratamiento más suave, como el tratamiento de bordes finos, se pueden utilizar perlas de desbarbado de poliestireno en combinación. Este material es relativamente suave y puede eliminar eficazmente las rebabas finas de las piezas sin dañar su superficie.
- Piezas pequeñas de precisión
Las piezas pequeñas de precisión son muy comunes en los campos de los productos electrónicos, los dispositivos médicos y la fabricación de instrumentos. Por ejemplo, juntas de soldadura de componentes electrónicos, microengranajes en equipos médicos, etc. Estas piezas suelen ser de pequeño tamaño y requieren una precisión muy alta, por lo que la dureza y el impacto del abrasivo deben controlarse estrictamente durante el proceso de arenado para evitar daños en la forma y el tamaño de las piezas.
Los medios de desbarbado de poliamida y nailon son materiales ideales para procesar este tipo de piezas. El nailon es relativamente blando y no daña las piezas de precisión. También tiene buenas propiedades antiestáticas y es adecuado para procesar componentes electrónicos que se ven fácilmente afectados por la electricidad estática. Para garantizar que las piezas de precisión no se sobrecalienten ni se deformen durante el procesamiento, los medios criogénicos de desbarbado son una buena elección. El tratamiento a baja temperatura puede evitar la deformación de las piezas causada por las altas temperaturas o los cambios en las propiedades de los materiales, garantizando la integridad de las piezas de precisión.
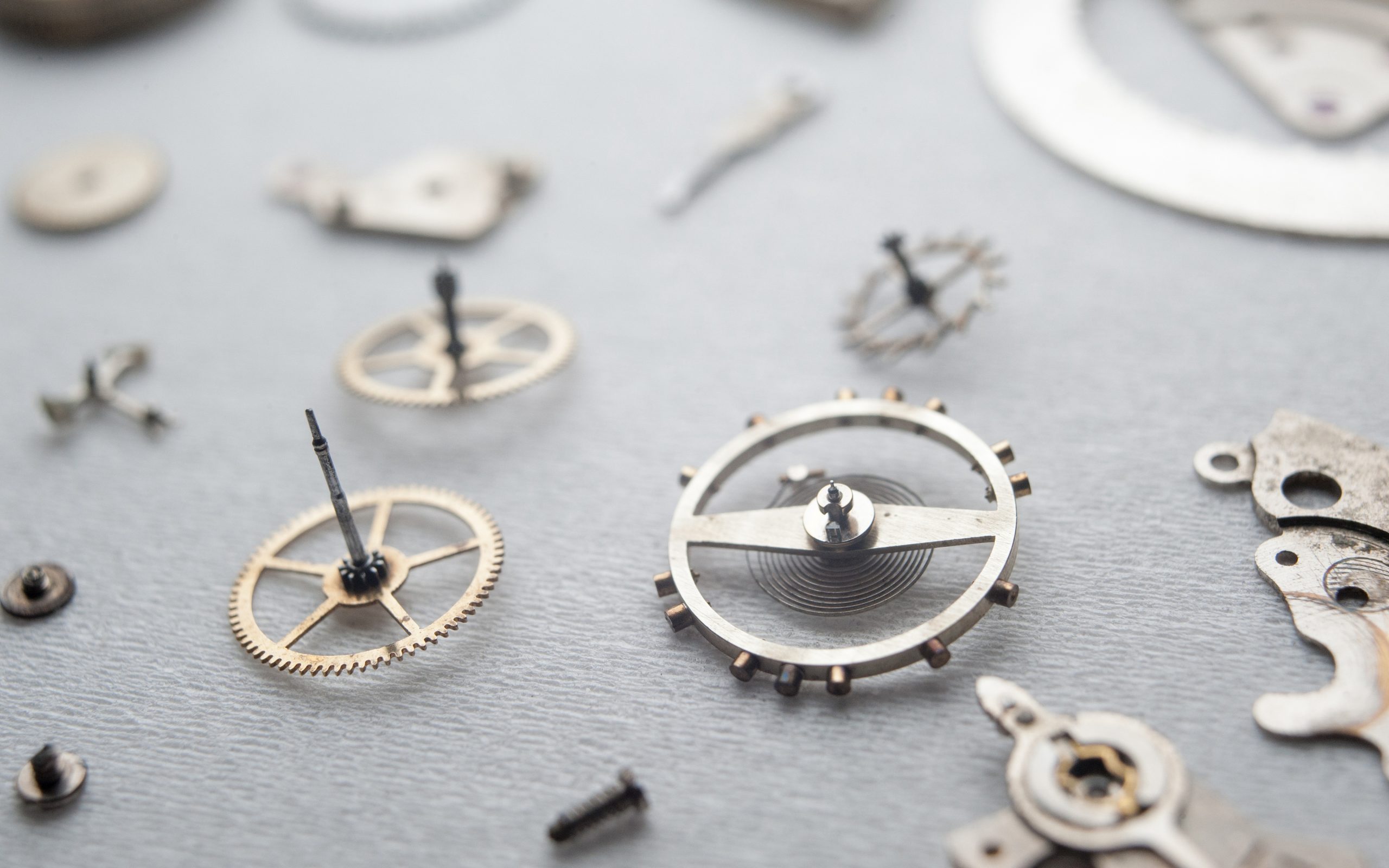
Casos especiales: Combinación de dos o más materiales de arenado
En aplicaciones prácticas, algunas piezas no sólo tienen formas complejas, sino que también pueden estar compuestas de varios materiales diferentes, o los requisitos de tratamiento superficial son muy estrictos. En este caso, a menudo es necesario combinar dos o más materiales de granallado. He aquí algunos ejemplos típicos de uso combinado:
Tratamiento mixto de piezas poliédricas
Tomemos como ejemplo la fundición de un motor de automóvil. El exterior del motor suele ser una estructura poliédrica, y la superficie debe limpiarse uniformemente. Sin embargo, debido a las grandes diferencias en las formas de las distintas partes del motor, un único material de chorreado no puede tratar eficazmente todas las zonas. En este caso, pueden utilizarse perlas de chorreado de óxido de circonio para eliminar rebabas y residuos en la mayor parte de la superficie y, a continuación, granalla ultrafina de óxido de aluminio para el tratamiento secundario de algunas zonas más delicadas a fin de garantizar un acabado superficial uniforme en toda la pieza.
Procesado de piezas compuestas
Un ejemplo típico de piezas compuestas son los componentes de aviación, que suelen estar formados por una mezcla de metales y no metales. Los distintos materiales reaccionan de forma diferente al medio durante el proceso de chorreado, por lo que se requiere una combinación de varios materiales de chorreado. Por ejemplo, las piezas metálicas pueden pulirse con microesferas cerámicas, mientras que las no metálicas pueden tratarse con microesferas de desbarbado de poliestireno. De este modo se garantiza que cada material pueda recibir el tratamiento de superficie adecuado.
Piezas con requisitos de alta precisión
Las piezas de alta precisión, como los componentes de dispositivos médicos, no sólo requieren una superficie impecable, sino también garantizar que su precisión no se verá afectada durante el procesamiento. En este caso, se suelen utilizar medios de desbarbado a baja temperatura para el tratamiento preliminar con el fin de eliminar las impurezas de la superficie y, a continuación, se utilizan medios de poliamida de nailon para un tratamiento de superficie más refinado que garantice la precisión y el acabado superficial de las piezas.
Análisis de las características de diferentes materiales de chorreado de arena
A la hora de seleccionar los materiales de chorreado, es importante conocer sus propiedades físicas y químicas. La elección de los materiales de chorreado no sólo afecta al efecto del tratamiento superficial de las piezas, sino también a la eficacia, el coste y la dificultad del tratamiento posterior. A continuación, exploraremos en profundidad los materiales de chorro de arena mencionados anteriormente y explicaremos sus ventajas únicas y escenarios aplicables.
- Granalla ultrafina de óxido de aluminio
El óxido de aluminio es uno de los materiales para chorro de arena más utilizados. Debido a su elevada dureza, gran resistencia a la compresión y buena estabilidad química, se utiliza ampliamente en el tratamiento de superficies de diversas piezas metálicas y no metálicas. La dureza Mohs del óxido de aluminio es cercana a 9, sólo superada por el diamante y el carburo de silicio, por lo que puede eliminar eficazmente incrustaciones de óxido, pintura, óxido y otros contaminantes de la superficie de las piezas.
- Escenarios aplicables: Adecuado para el mecanizado en bruto de superficies de materiales duros (como acero y fundición), especialmente para ocasiones en las que es necesario mejorar la rugosidad de la superficie. Entre las aplicaciones habituales se incluyen el rectificado superficial de piezas mecánicas y el pretratamiento antes del revestimiento.
- Ventajas: Las partículas de chorro de arena de óxido de aluminio son uniformes y pueden mantener un efecto de tratamiento de superficies relativamente consistente. Tiene una gran durabilidad y reutilización, especialmente adecuada para entornos de procesamiento en los que es necesario reutilizar los materiales de chorreado. La elevada dureza del óxido de aluminio le permite eliminar rápidamente la suciedad persistente y acortar el tiempo de procesamiento.
- Nota: Debido a su elevada dureza, el óxido de aluminio no es adecuado para procesar piezas de precisión o materiales frágiles. Además, el óxido de aluminio es muy abrasivo y puede dejar pequeños arañazos en algunos materiales, por lo que es necesario evaluarlo en función de las necesidades específicas de procesamiento a la hora de seleccionarlo.
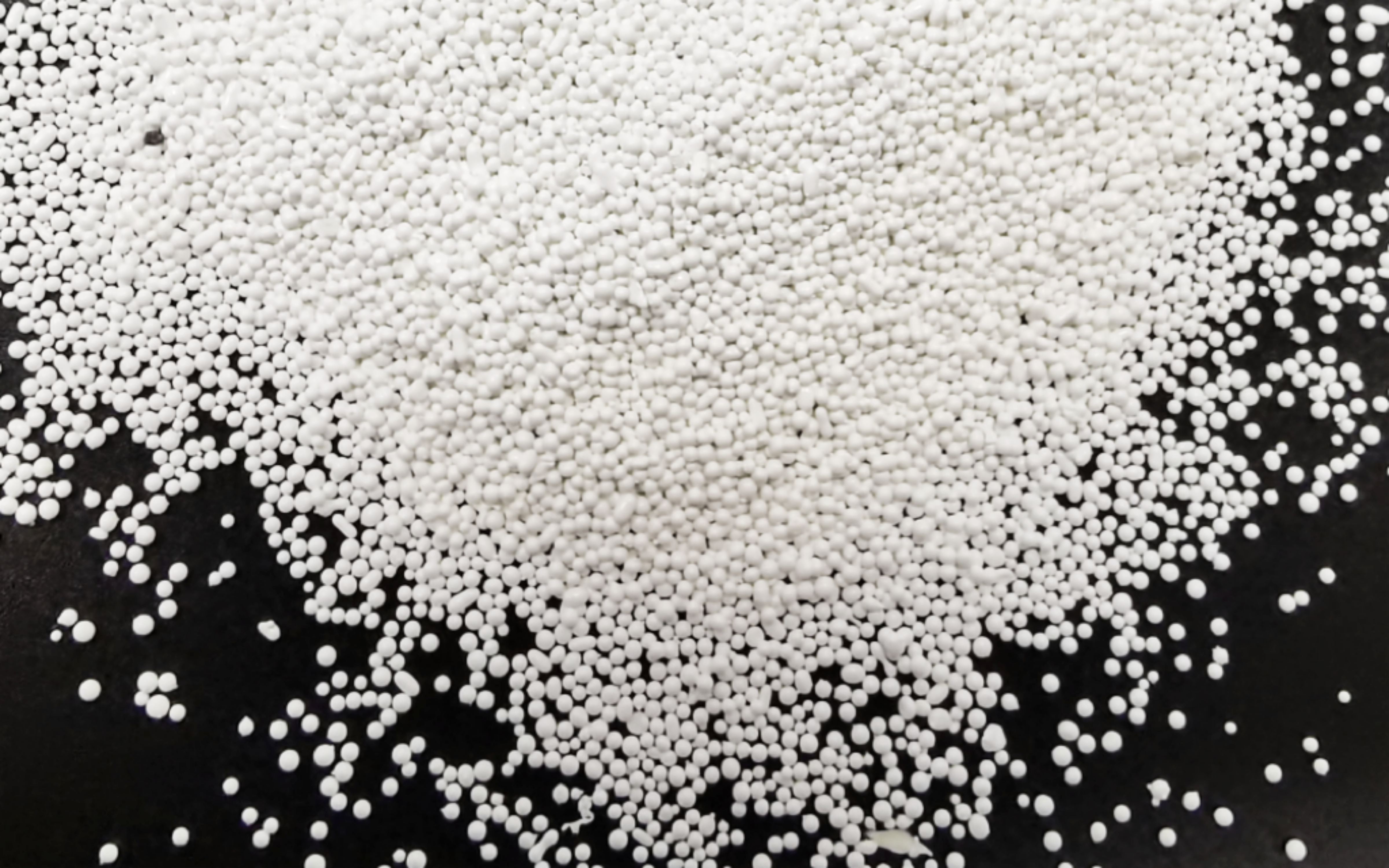
- Medios de limpieza con perlas de cerámica
Las microesferas cerámicas son un tipo de medio de arenado fabricado con una mezcla de circonio, silicio, aluminio y otros materiales, y tienen forma redonda u ovalada. Las microesferas cerámicas tienen una buena resistencia al impacto y una gran dureza, y se utilizan principalmente para pulir y reforzar superficies metálicas en la producción industrial.
- Escenarios aplicables: Debido al tamaño uniforme de las partículas y a la superficie lisa de las microesferas cerámicas, es especialmente adecuado para piezas con elevados requisitos de acabado superficial, como acero inoxidable, aleaciones de aluminio, etc. Suele utilizarse para el tratamiento de superficies de piezas de precisión en industrias como la aeronáutica, la automovilística y la de dispositivos médicos.
- Ventajas: La forma de las partículas de las microesferas cerámicas es relativamente redonda, por lo que no causarán efectos de corte evidentes durante el proceso de arenado como el óxido de aluminio, y son más adecuadas para ocasiones con elevados requisitos de acabado superficial. El uso de microesferas cerámicas para el arenado también puede mejorar la resistencia a la fatiga de las piezas metálicas y prolongar su vida útil. Es especialmente adecuado para piezas que requieren un tratamiento de refuerzo de la superficie.
- Notas: El coste de las microesferas cerámicas es relativamente alto, pero su durabilidad y reutilización son sólidas, y siguen teniendo una alta rentabilidad en el procesamiento a largo plazo. Además, debido a su superficie relativamente lisa, no es adecuada para ocasiones en las que es necesario aumentar la rugosidad de la superficie.
- granallas de ceramica para chorro de arena
Los granos de arenado cerámicos son materiales de arenado no metálicos fabricados triturando materiales cerámicos fundidos a alta temperatura. Su dureza y tenacidad se sitúan entre el óxido de aluminio y las microesferas cerámicas. Se utiliza ampliamente en piezas con elevados requisitos de limpieza y rugosidad superficial.
- Escenarios aplicables: El granallado cerámico se utiliza sobre todo para el tratamiento de superficies de materiales como metales, plásticos y vidrio, especialmente en operaciones como la limpieza de piezas fundidas, la eliminación de soldaduras y el desbaste de superficies. Puede limpiar defectos como óxidos y rebabas en la superficie de las piezas, al tiempo que aumenta la rugosidad de la superficie para mejorar la adherencia de los revestimientos posteriores.
- Ventajas: Las partículas cerámicas tienen una densidad y dureza moderadas, por lo que pueden eliminar eficazmente las impurezas sin dañar la superficie de la pieza. En comparación con el óxido de aluminio, el efecto de tratamiento superficial de las partículas cerámicas es más suave y no causará daños excesivos en la superficie de la pieza de trabajo. También tiene una alta resistencia a la corrosión química y es adecuado para operaciones de chorreado en entornos de alta temperatura o corrosivos.
- Nota: Aunque el rendimiento de las partículas cerámicas es relativamente equilibrado, su fuerza de rectificado no es tan buena como la del óxido de aluminio, y es adecuado para el tratamiento superficial de materiales de dureza media. Para piezas que requieran un rectificado de alta intensidad, puede ser necesario combinarlo con materiales más duros, como el óxido de aluminio.
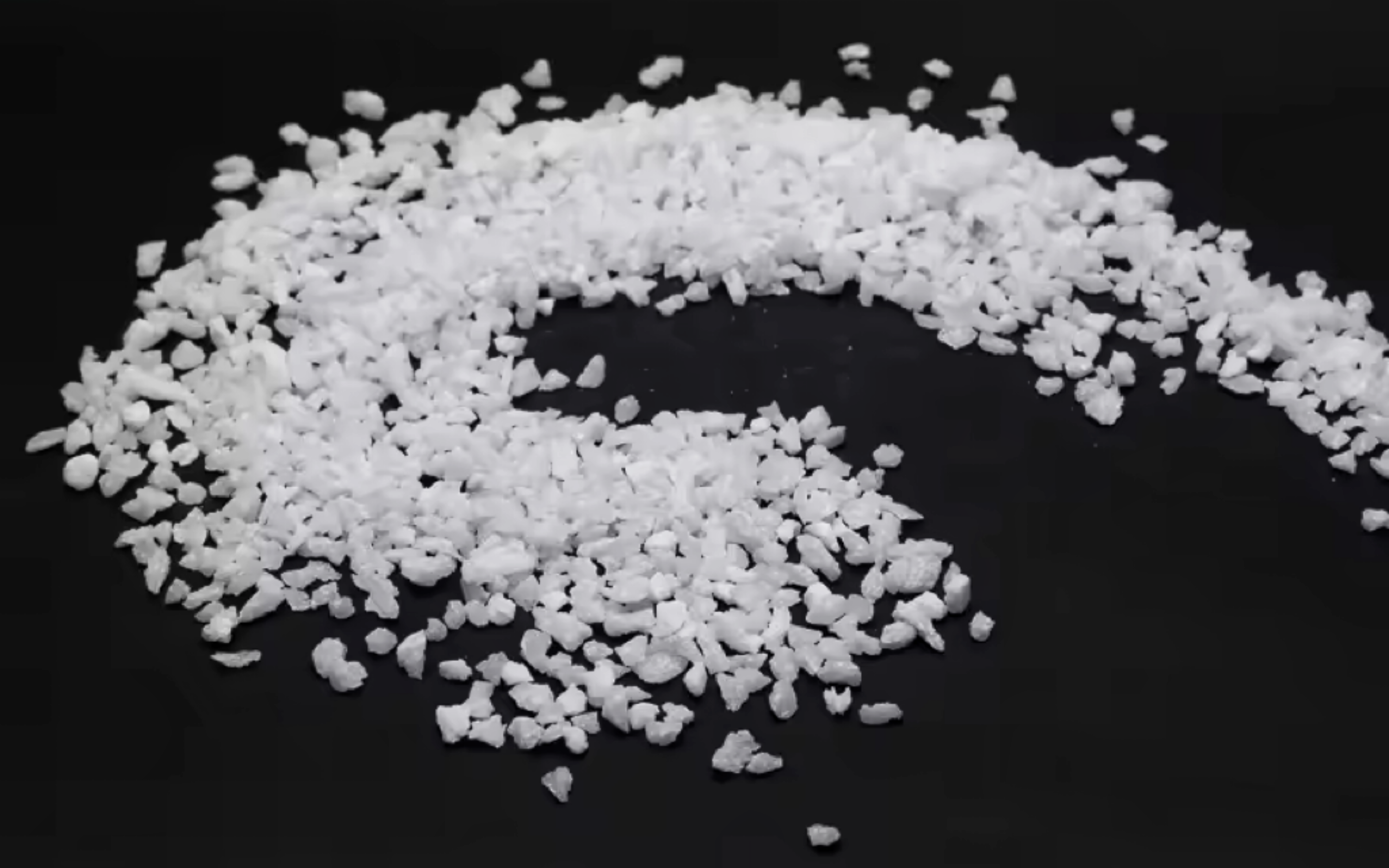
- Perlas de chorro de circonio
Las microesferas de circonio son un material de arenado de alta densidad fabricado mediante la sinterización de polvo de óxido de circonio. Su dureza y resistencia son mejores que las de las microesferas cerámicas convencionales, y son especialmente adecuadas para procesar algunas piezas con requisitos de alta resistencia y gran resistencia al desgaste.
- Escenarios aplicables: Las perlas de circonio son especialmente adecuadas para el tratamiento de superficies de aleaciones de alta resistencia, aleaciones de titanio, acero inoxidable y otros materiales. En las industrias aeroespacial, de fabricación de automóviles y electrónica, las perlas de circonio se utilizan ampliamente para el refuerzo superficial, el desbarbado y el acabado de piezas.
- Ventajas: La gran dureza y la elevada fuerza de impacto de los granos de chorreado de óxido de circonio les permiten eliminar rápidamente la suciedad persistente o las capas de óxido de la superficie de las piezas, al tiempo que aumentan la resistencia a la fatiga de la superficie sin dañar las piezas. Su excelente resistencia al impacto también la convierte en una opción ideal para procesar estructuras complejas y piezas de alta precisión.
- Notas: Debido a su elevado coste, las perlas de óxido de circonio se utilizan sobre todo para procesar piezas de gran valor y precisión. Para algunas piezas de poco valor, el uso de perlas de circonio puede aumentar el coste total de producción, por lo que es necesario encontrar un equilibrio entre coste y efecto.
- Nylon Poliamida Medios de desbarbado
Los medios de poliamida de nylon son materiales de chorreado flexibles y de baja densidad, utilizados principalmente para el desbarbado de piezas de precisión. La poliamida de nailon tiene una buena resistencia al impacto y no causa daños secundarios a la pieza. Es especialmente adecuada para procesar materiales quebradizos y piezas con elevados requisitos de tratamiento superficial.
- Escenarios aplicables: Se utiliza habitualmente en el desbarbado de superficies y la limpieza de piezas delicadas, como componentes electrónicos, instrumentos de precisión y equipos médicos. Su baja dureza lo hace adecuado para procesar materiales fácilmente dañables como plásticos, resinas, aleaciones de aluminio, etc.
- Ventajas: Los medios de arenado de poliamida de nailon tienen buena elasticidad y pueden proteger eficazmente la estructura de precisión de las piezas durante el procesamiento. Su bajo desgaste garantiza que la superficie de la pieza no se raye ni se dañe al eliminar las rebabas, lo que resulta especialmente adecuado para el tratamiento de superficies de componentes electrónicos con elevados requisitos.
- Nota: La poliamida de nailon tiene poca resistencia al desgaste y es adecuada para un solo uso o un desbarbado ligero. Por lo tanto, es posible que haya que sustituir el material con frecuencia durante la producción en serie, lo que aumenta el coste total del material.
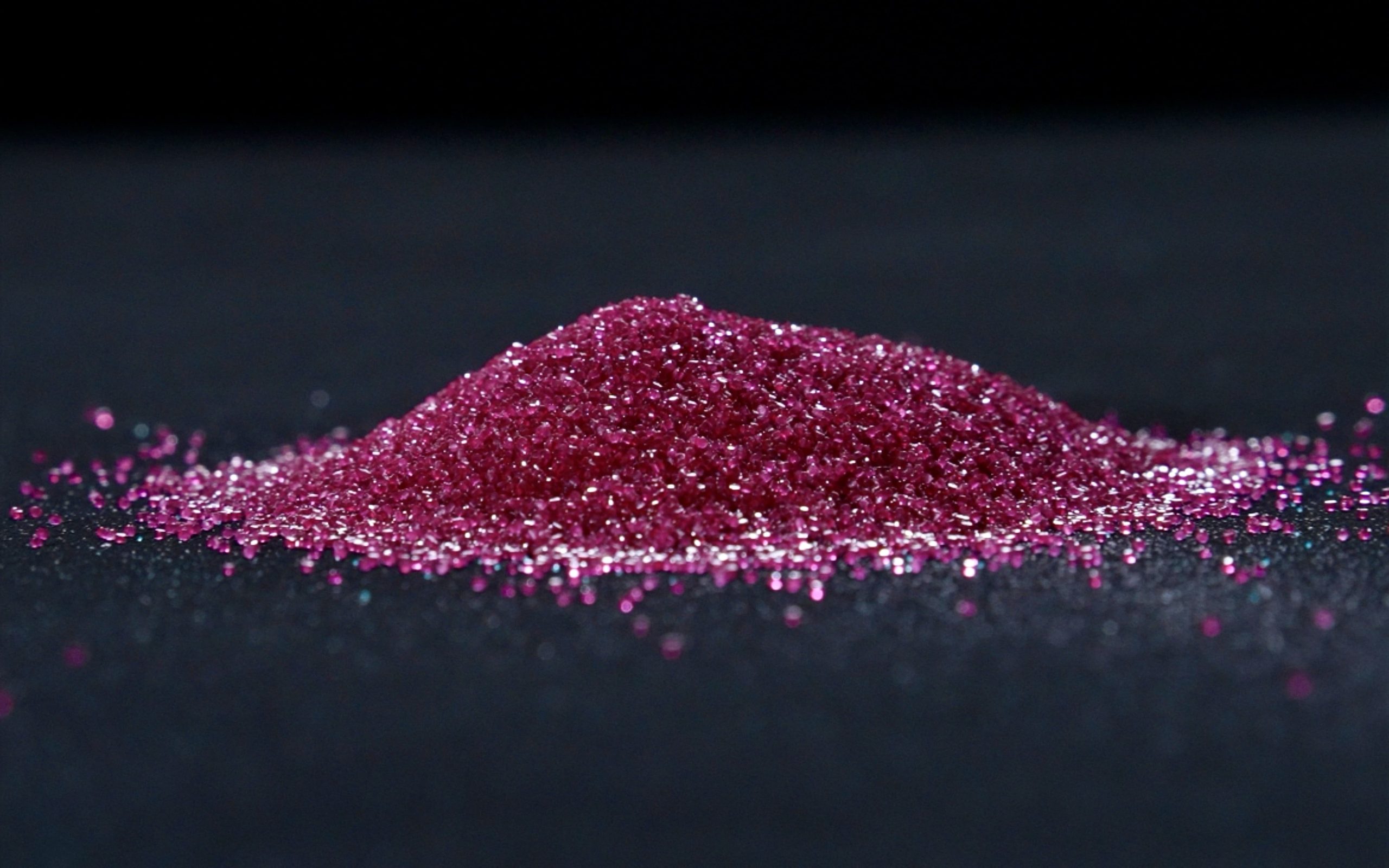
- Perlas de desbarbado de poliestireno
Los granos de desbarbado de poliestireno son medios de desbarbado ligeros y flexibles que se utilizan principalmente para eliminar rebabas de piezas de plástico de precisión y piezas metálicas ligeras. Las características del poliestireno lo hacen muy adecuado para industrias que tienen requisitos estrictos sobre la superficie de la pieza, como la fabricación de instrumentos médicos, electrónicos y de precisión.
- Escenarios aplicables: Los cordones de desbarbado de poliestireno se utilizan sobre todo para eliminar rebabas de piezas de plástico y pequeños defectos en la superficie de piezas moldeadas por inyección y piezas fundidas a presión. Rinde especialmente bien al procesar materiales ligeros, como piezas de plástico y aluminio, y es adecuado para piezas con elevados requisitos de acabado superficial, como equipos médicos, electrodomésticos y componentes electrónicos.
- Ventajas: Los granos de desbarbado de poliestireno son muy adecuados para procesos de desbarbado a baja temperatura y pueden eliminar eficazmente las rebabas de la superficie de las piezas sin dañar el material en entornos de baja temperatura. Debido a su material relativamente blando, el uso de este medio puede evitar arañazos o daños en la superficie de la pieza durante el proceso de desbarbado.
- Nota: Debido a la baja densidad del material de poliestireno, puede no ser tan eficaz como otros materiales de alta dureza en algunos entornos de desbarbado de gran intensidad. Por lo tanto, puede ser necesario utilizarlo en combinación con otros medios en operaciones de limpieza o desbarbado que requieran mayor intensidad.

- Medios criogénicos de desbarbado
Los medios de desbarbado criogénicos son medios especiales diseñados para procesos de desbarbado criogénicos que pueden eliminar rápidamente las rebabas después de que las piezas se congelen a la temperatura de fragilidad. Los medios son estables en entornos de baja temperatura y se utilizan ampliamente en operaciones de desbarbado de materiales frágiles y de alta precisión.
- Escenarios aplicables: Los medios de desbarbado criogénicos son adecuados para piezas de precisión con requisitos de calidad superficial extremadamente elevados, como piezas de caucho, piezas de plástico, dispositivos médicos y piezas de aviación y automoción. Dado que el material se vuelve quebradizo durante el proceso de congelación, las rebabas pueden eliminarse fácilmente sin causar daños a la propia pieza. También es especialmente adecuado para procesar piezas con geometrías complejas y piezas difíciles de desbarbar con los métodos tradicionales.
- Ventajas: El proceso de desbarbado criogénico es muy suave y puede proteger al máximo la superficie de la pieza, al tiempo que garantiza una gran precisión de desbarbado. Los medios también son muy adaptables y pueden procesar eficazmente una gran variedad de materiales y piezas con formas complejas. En comparación con los métodos de desbarbado tradicionales, la tecnología de desbarbado criogénico tiene una mayor precisión y eficacia y es especialmente adecuada para industrias con estrictos requisitos de producción como la médica, la aeronáutica y la automovilística.
- Nota: Aunque los medios criogénicos de desbarbado funcionan bien en el mecanizado de precisión, el coste total es relativamente alto debido a sus elevados requisitos de equipamiento. Por tanto, estos medios son más adecuados para su uso en la producción en serie o en ocasiones especiales con requisitos de extrema calidad.
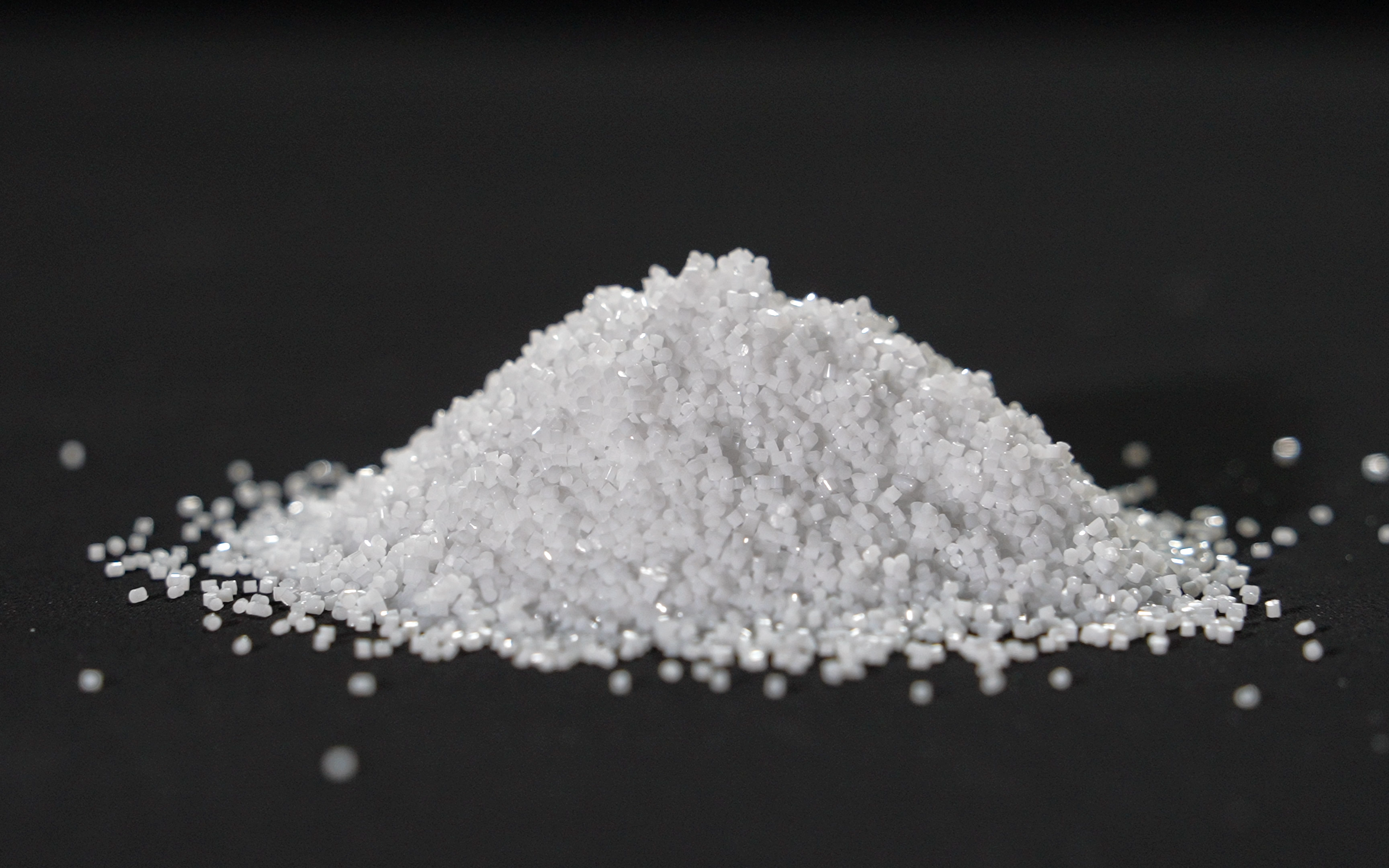
Seleccionar los materiales de chorreado de arena en función de la forma de las piezas es una tarea compleja y que requiere mucha experiencia. La elección correcta de los materiales de chorreado no sólo puede garantizar el efecto del tratamiento superficial de las piezas, sino también mejorar la eficiencia de la producción y reducir el desperdicio innecesario de material. Al procesar algunas piezas complejas o de alta precisión, la combinación de varios materiales de chorreado puede lograr a menudo resultados más idóneos.
En resumen, el núcleo de la tecnología de chorro de arena reside en la flexibilidad y la precisión. Al seleccionar los materiales de arenado, los fabricantes deben considerar exhaustivamente la forma, el material y los requisitos de procesamiento de las piezas para garantizar que cada eslabón pueda lograr el mejor efecto de procesamiento.
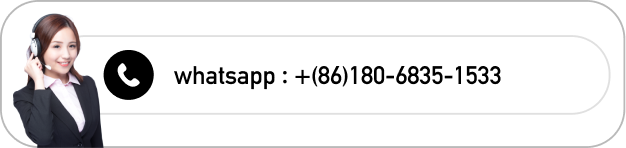