15 de octubre de 2024
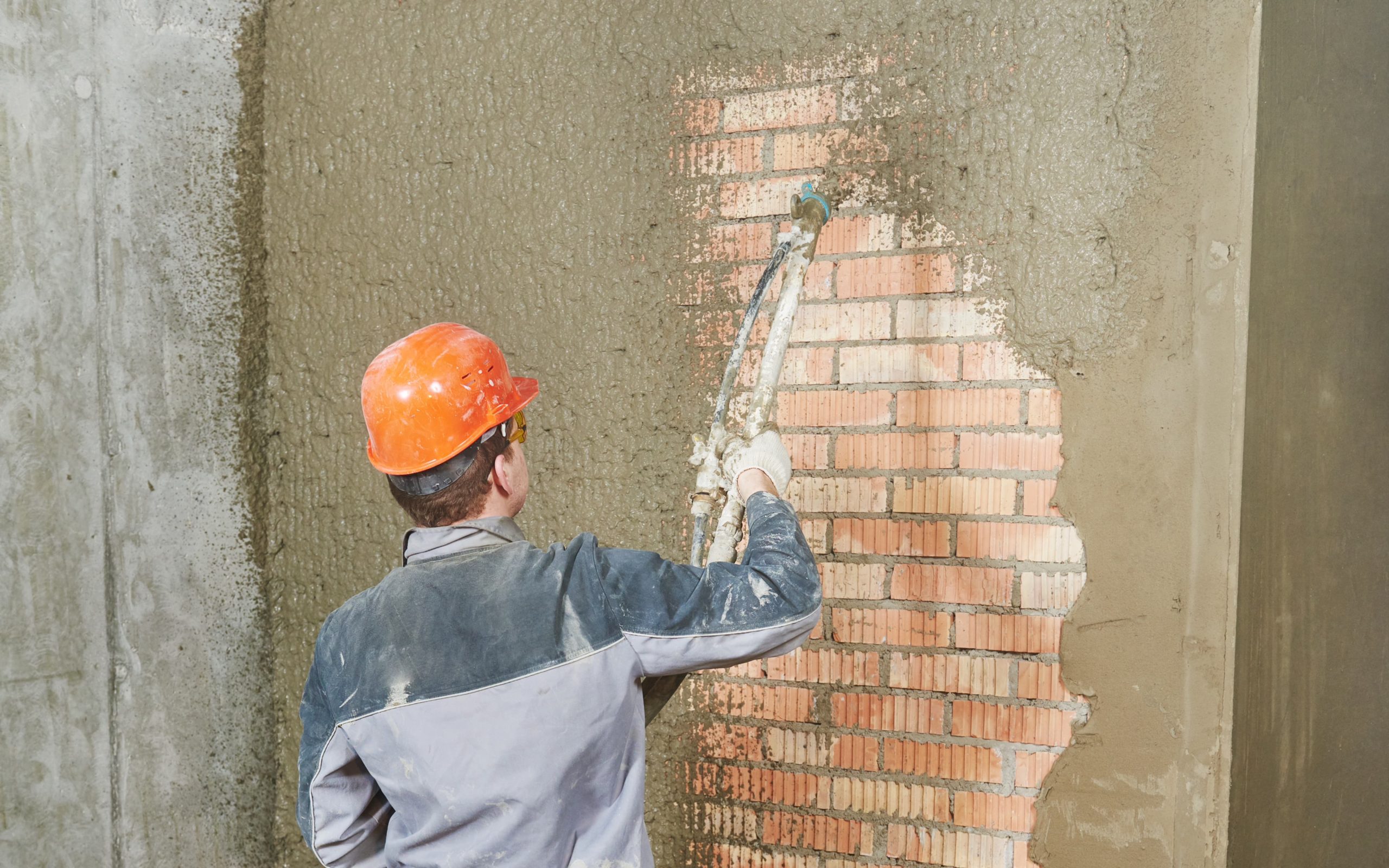
El grabado es un proceso que utiliza métodos físicos o químicos para producir texturas finas en la superficie de los materiales. Se utiliza mucho en el tratamiento de superficies de materiales duros como el vidrio, el metal y la cerámica. Ya sea para aumentar la adherencia del revestimiento o mejorar las propiedades funcionales de la superficie del material, el proceso de grabado desempeña un papel vital en muchas industrias. En las aplicaciones industriales modernas, el grabado mecánico es especialmente habitual. Por medios como el chorro de arena, se puede conseguir un tratamiento preciso de la superficie para lograr un delicado efecto de textura.
En la fabricación de ingeniería, la adherencia del revestimiento es esencial para la estabilidad, durabilidad y rendimiento a largo plazo del producto. Para garantizar que el revestimiento se adhiera firmemente a la superficie del sustrato y no se desprenda o falle debido a los cambios ambientales o al desgaste, se utiliza el proceso de grabado para mejorar la adherencia entre la superficie y el revestimiento. Por lo tanto, este artículo tratará sobre "Cómo el grabado industrial mejora la adherencia del revestimiento" y analizará su valor en aplicaciones mecánicas.
Principios básicos del grabado
El mordentado es el proceso de grabar o corroer la superficie de un material por medios químicos, físicos o mecánicos para lograr el propósito de cambiar las características de la superficie. Este proceso puede refinar la estructura de la superficie y aumentar su rugosidad, mejorando así la adherencia entre el revestimiento y la superficie del material.
Grabado químico frente a grabado mecánico
En las aplicaciones industriales, el grabado se divide generalmente en dos métodos: el grabado químico y el grabado mecánico.
- Grabado químico: Se trata de la reacción de reactivos químicos (como soluciones ácidas o alcalinas) con materiales para provocar corrosión en la superficie. El grabado químico es especialmente adecuado para el tratamiento de materiales de gran superficie y tiene una buena cobertura de piezas con formas complejas. Por ejemplo, en las industrias aeroespacial y de semiconductores, el grabado químico se utiliza ampliamente para el tratamiento superficial de materiales metálicos y obleas de semiconductores.
- Grabado mecánico: Se basa principalmente en acciones físicas como el esmerilado mecánico o el chorro de arena para eliminar la capa superficial. El grabado con chorro de arena consigue un efecto de modificación uniforme de la superficie mediante el uso de materiales de alta dureza (como arena de óxido de aluminio o perlas de arenado cerámicas) para impactar contra la superficie a gran velocidad. La ventaja del grabado mecánico es que es inocuo para el medio ambiente y la profundidad del tratamiento superficial puede controlarse con precisión. El grabado mecánico con chorro de arena se utiliza ampliamente para el tratamiento de superficies metálicas y de vidrio.
Ambos métodos tienen ventajas e inconvenientes. El grabado químico es adecuado para superficies de gran superficie y formas complejas, mientras que el mecánico destaca en aplicaciones que requieren un control muy preciso de la textura y las propiedades físicas de la superficie.
Cómo los procesos de grabado mejoran la adherencia del revestimiento
Para entender cómo el grabado mejora la adherencia del revestimiento, primero tenemos que comprender la relación entre la energía superficial y la adherencia. Cuanto mayor sea la energía superficial entre el revestimiento y el sustrato, mayor será la adherencia del revestimiento. El grabado aumenta el área de contacto entre la energía superficial y el revestimiento al cambiar la microestructura de la superficie del sustrato, lo que permite que el revestimiento se adhiera mejor al sustrato.
Principios de energía superficial y adhesión
La superficie de cada material tiene una propiedad llamada "energía superficial", que afecta a la humectabilidad de los líquidos (como la pintura) en la superficie. Los materiales con alta energía superficial se humedecen más fácilmente con revestimientos líquidos, mientras que los materiales con baja energía superficial no forman fácilmente un revestimiento resistente.
Mediante el grabado, los materiales de arenado (como las microesferas cerámicas o el óxido de aluminio) pueden eliminar los contaminantes y las capas irregulares de la superficie del material, dejando al descubierto una superficie de sustrato limpia y rugosa. La superficie rugosa forma un gran número de diminutas estructuras cóncavas y convexas, lo que aumenta enormemente el área de contacto entre el revestimiento y el sustrato. Debido al aumento de la superficie de contacto, las moléculas del revestimiento pueden unirse más estrechamente a la superficie del sustrato, y la adherencia mejora considerablemente.
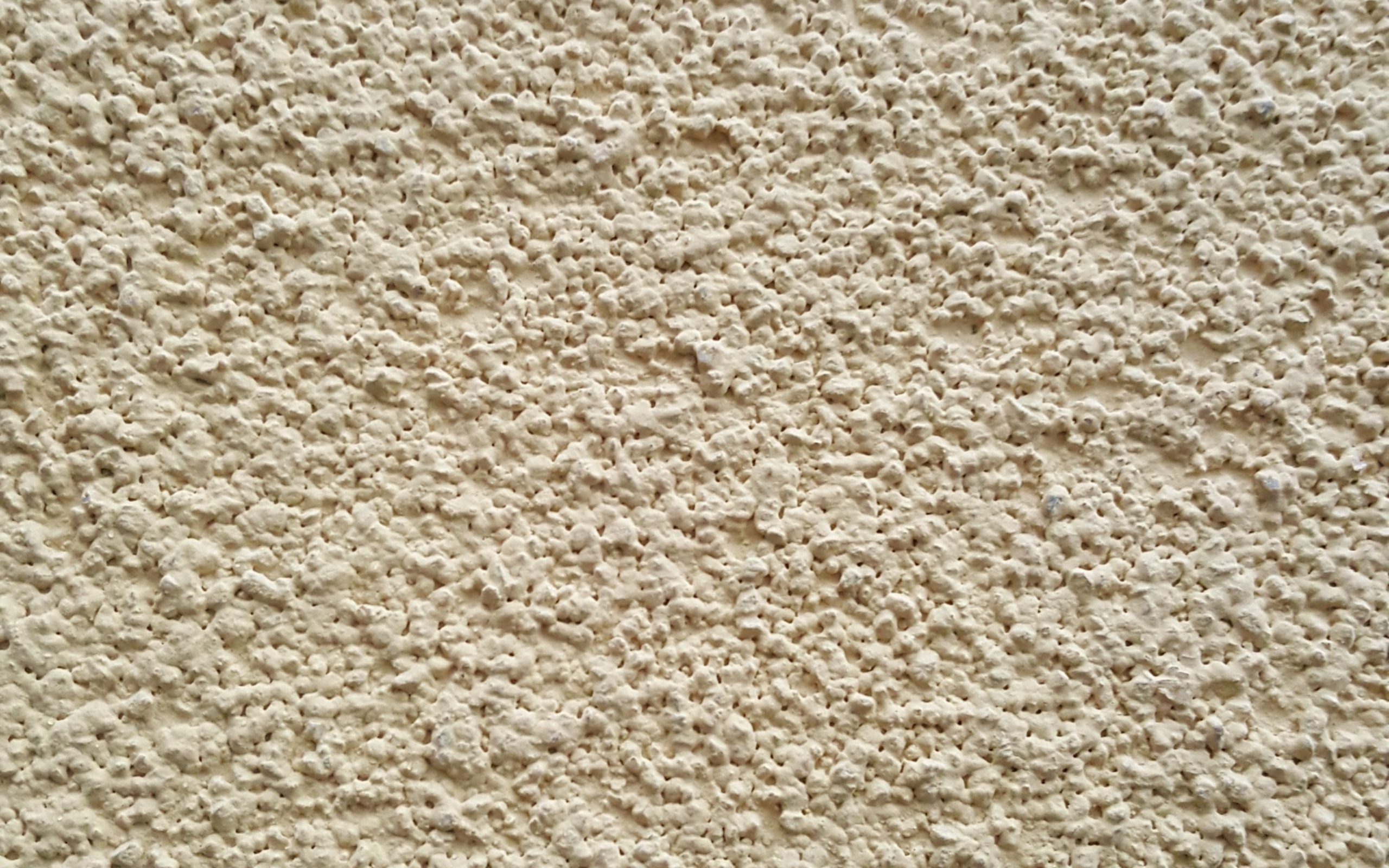
La rugosidad de la superficie influye directamente en la adherencia del revestimiento
Unión mecánica mejorada
Además del aumento de la energía superficial, el grabado mejora aún más la adherencia del revestimiento al crear puntos de bloqueo mecánicos microscópicos. Tras el grabado, las ranuras y protuberancias de la superficie del sustrato proporcionan más "puntos de agarre" para el revestimiento, lo que permite que éste se fije más firmemente a la superficie. Esta unión mecánica es especialmente importante para aplicaciones de revestimiento en entornos de gran tensión, como las superficies de equipos sometidos a altas temperaturas, alta presión o condiciones de carga pesada.
En aplicaciones prácticas, el grabado con chorro de arena no sólo proporciona una mejor adherencia física del revestimiento, sino que también reduce la descamación y el agrietamiento del revestimiento. Especialmente en equipos industriales que se utilizan durante mucho tiempo, la superficie grabada puede prolongar eficazmente la vida útil del revestimiento y reducir los costes de mantenimiento y sustitución.
Comparación con otros métodos de tratamiento de superficies
En comparación con los métodos de tratamiento de superficies como el grabado químico o el tratamiento térmico, el grabado mecánico consigue modificar la superficie por medios físicos. Este método no sólo es más respetuoso con el medio ambiente, sino que también evita los problemas de contaminación que pueden introducirse durante el tratamiento químico. El grabado mecánico también puede controlar con mayor precisión la profundidad del grabado y el tamaño de la textura, por lo que es el proceso preferido en industrias que requieren gran precisión.
Por ejemplo, en la industria de fabricación de automóviles, el revestimiento anticorrosión de la carrocería requiere un alto grado de adherencia para hacer frente al barro, la sal y otras sustancias corrosivas de la carretera. Mediante el grabado mecánico, la superficie de la carrocería no sólo puede obtener una rugosidad uniforme, sino también garantizar que el revestimiento pueda resistir la corrosión externa durante mucho tiempo.
Materiales de chorreado aplicables y sus efectos
En la práctica, los distintos tipos de materiales de chorreado tienen efectos diferentes sobre la adherencia del revestimiento. Por ejemplo, los materiales de arenado de alúmina se utilizan a menudo en procesos de grabado industrial de precisión debido a su gran dureza, tamaño uniforme de las partículas y gran capacidad de control. Su estructura de alta densidad puede aportar efectos de tratamiento superficial estables y consistentes a las superficies metálicas o cerámicas, mejorando en gran medida la adhesión del revestimiento.
Para las piezas que requieren una mayor resistencia superficial y durabilidad en entornos extremos (como las piezas clave de las industrias aeroespacial y del petróleo y el gas), el grabado superficial mediante chorro de arena de alúmina puede mejorar eficazmente la capacidad protectora del revestimiento.
Aplicaciones de grabado industrial
En la fabricación industrial, el grabado no es sólo un proceso para mejorar la estética, sino también un paso importante para sentar las bases de los procesos posteriores. Hemos aprendido de los principios anteriores que lo más importante para que el revestimiento se adhiera firmemente es la rugosidad de la superficie y los cambios en la rugosidad de la superficie afectan directamente a la adhesión del revestimiento. La textura superficial controlable formada por el grabado puede mejorar eficazmente la adherencia del revestimiento, mejorar la durabilidad del producto y garantizar que siga teniendo un excelente rendimiento en entornos extremos. Las siguientes industrias y piezas de trabajo son importantes áreas de aplicación de la tecnología de grabado:
Fabricación de metales
En el campo del procesamiento de metales, la tecnología de grabado mecánico (como el chorro de arena) se utiliza ampliamente para el tratamiento de superficies antes de la pintura. En la producción de piezas metálicas, la adherencia y uniformidad del revestimiento son cruciales. El grabado puede eliminar la capa de óxido, el aceite y otros contaminantes de la superficie metálica, al tiempo que aumenta la rugosidad de la superficie para que el revestimiento se adhiera con mayor firmeza.
Los equipos aeroespaciales, como los componentes de las alas, las palas de las turbinas de los motores, las carcasas de los motores a reacción, etc., tienen que soportar altas temperaturas, fuertes vientos y entornos externos adversos, por lo que la adherencia del revestimiento es especialmente importante. Otras, como las carcasas de los aviones, las alas y las piezas de los motores, suelen estar expuestas a la humedad, los cambios de temperatura y los rayos ultravioleta. Mediante el grabado, las piezas aeroespaciales pueden obtener texturas superficiales precisas, mejorar eficazmente la adherencia de los revestimientos protectores y garantizar que el revestimiento no se desprenda ni se agriete en condiciones extremas. Además, muchas piezas de naves espaciales también deben soportar una presión tremenda. La superficie grabada no sólo puede proporcionar una unión mecánica más fuerte, sino también mejorar la resistencia a la corrosión, garantizando la seguridad del vuelo y la larga vida útil del equipo.
Fabricación de automóviles
En la fabricación de automóviles, especialmente en el chasis, las puertas y las superficies exteriores de la carrocería, la calidad del revestimiento anticorrosión afecta directamente a la vida útil del vehículo. Los vehículos son propensos a oxidarse cuando están expuestos al aire, la humedad, la sal y otros ambientes durante mucho tiempo. Mediante la tecnología de grabado, la superficie de las piezas de automóvil puede producir una rugosidad uniforme, mejorando así la adherencia del revestimiento anticorrosión y evitando la formación de manchas de óxido.
Los materiales de arenado de alúmina se utilizan mucho en este campo. Pueden procesar rápida y eficazmente grandes áreas de la superficie de la carrocería del vehículo para garantizar que el revestimiento tenga una adherencia óptima. Además, el grabado también puede reducir las irregularidades del revestimiento y mejorar la calidad general del recubrimiento, mejorando así la durabilidad del vehículo.
Productos de vidrio
Como material frágil, el proceso de grabado puede conferir al vidrio efectos ópticos y características superficiales únicos controlando la profundidad y la textura de la superficie. En el diseño industrial, el grabado mecánico no sólo puede mejorar la estética del vidrio, sino también su resistencia al rayado y al agrietamiento. Este proceso también se utiliza a menudo en el tratamiento de vidrio arquitectónico de gama alta, pantallas de visualización y carcasas de equipos electrónicos.
Por ejemplo, las pantallas de visualización, las carcasas electrónicas, los cristales protectores, los cristales decorativos arquitectónicos, etc. de los smartphones modernos pueden tratarse con la tecnología de grabado por chorro de arena no sólo para evitar los restos de huellas dactilares, sino también para mejorar la adherencia del revestimiento y evitar arañazos o grietas en el cristal.
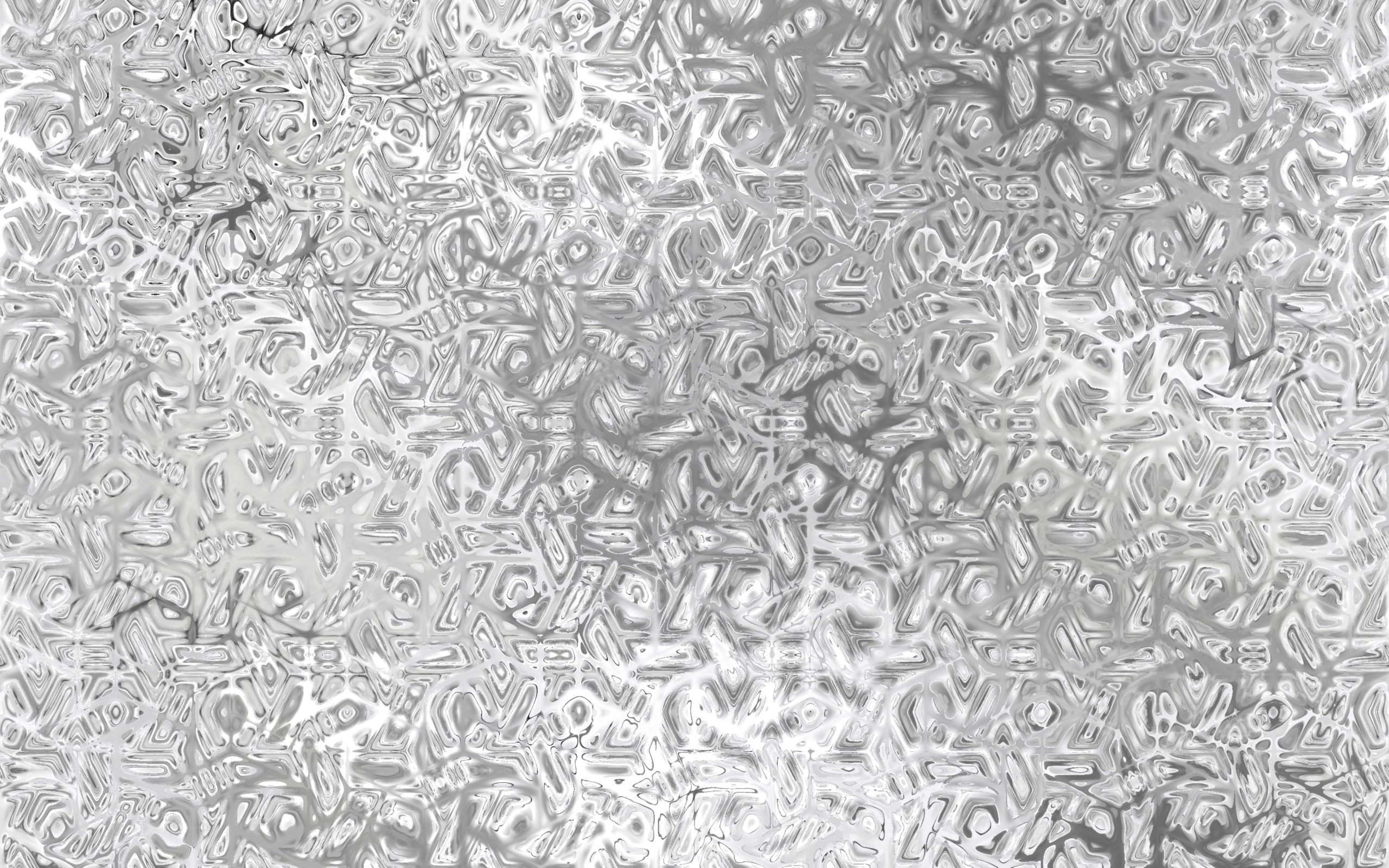
Los motivos del vidrio decorativo
Petróleo y gas
Los equipos de la industria del petróleo y el gas, como brocas de perforación, juntas de tuberías, válvulas y otros componentes de alta presión, trabajan a menudo en entornos de temperaturas y presiones extremadamente altas, por lo que los componentes de los equipos deben tener una gran resistencia al desgaste y a la corrosión. El proceso de grabado puede mejorar la adherencia del revestimiento formando una microtextura en la superficie, lo que garantiza que el revestimiento de la superficie del equipo no se desprenda ni falle en estas duras condiciones.
En los equipos de perforación petrolífera y transmisión de gas natural, componentes como las brocas y las válvulas son especialmente propensos al desgaste y la corrosión debido al contacto frecuente con arena, grava, gases corrosivos y líquidos. Mediante el grabado, la superficie del equipo no sólo puede mejorar la resistencia al desgaste, sino también reducir la tasa de fallos del equipo.
Industria electrónica
La industria electrónica tiene unos requisitos muy exigentes en cuanto a la precisión del tratamiento de superficies, especialmente en el caso de microcomponentes como circuitos integrados y chips, cuyas superficies deben grabarse con gran precisión. El grabado mecánico puede controlar la profundidad y uniformidad de la textura superficial al procesar estos dispositivos de precisión, garantizando que los componentes no se vean afectados por el entorno externo durante su uso, y asegurando su fiabilidad y estabilidad a largo plazo.
Al mismo tiempo, las carcasas metálicas de la industria electrónica (como las carcasas de los portátiles y las carcasas traseras de las tabletas) también se utilizan mucho en procesos de grabado para embellecer y reforzar la superficie.
Medios de chorro de arena para efectos óptimos de grabado
Cuando se realizan procesos de grabado, es fundamental elegir el medio de chorreado adecuado. Las propiedades de los materiales, el tamaño y la forma de las partículas influyen directamente en el efecto de grabado. A continuación se indican varios medios de chorreado comunes y sus escenarios de aplicación.
- Chorro de arena de alúmina
La alúmina es un medio de chorro de arena de uso común con gran dureza y capacidad de molienda, adecuado para el grabado en una variedad de materiales como metales, vidrio y cerámica. Cabe señalar que, al elegir el óxido de aluminio como medio de arenado, debe tenerse en cuenta la elección del tamaño de las partículas. Los tamaños de partícula más pequeños, como granalla ultrafina de óxido de aluminio son adecuados para el grabado detallado, mientras que los tamaños de partícula más grandes son más adecuados para el tratamiento de grandes superficies.
Entre sus ventajas destacan:
- Poderosa habilidad de eliminación: La dureza del óxido de aluminio le permite eliminar eficazmente el óxido superficial y las capas de pintura vieja.
- Adaptabilidad: Adecuado para diversas industrias, como la fabricación de automóviles, aeroespacial, electrónica, etc.
- Textura de superficie controlable: El óxido de aluminio puede controlar con precisión la profundidad de grabado para garantizar la mejor unión entre el revestimiento y el sustrato.
- Granalla cerámica
Los granos de chorreado cerámicos son también medios de chorreado de gran eficacia, especialmente indicados para tratamientos superficiales que requieren un mayor acabado y son muy adecuados para tratamientos superficiales que requieren un alto brillo, como las carcasas de dispositivos médicos y electrónica de consumo de alta gama. Entre sus ventajas se incluyen:
- Menor índice de desgaste: En comparación con el óxido de aluminio, las microesferas de granallado cerámico desgastan menos el sustrato durante el tratamiento y son adecuadas para el tratamiento de superficies de piezas de precisión.
- Protección del medio ambiente: Las bolas de granalla cerámica no contaminan y son adecuadas para industrias con elevados requisitos medioambientales.
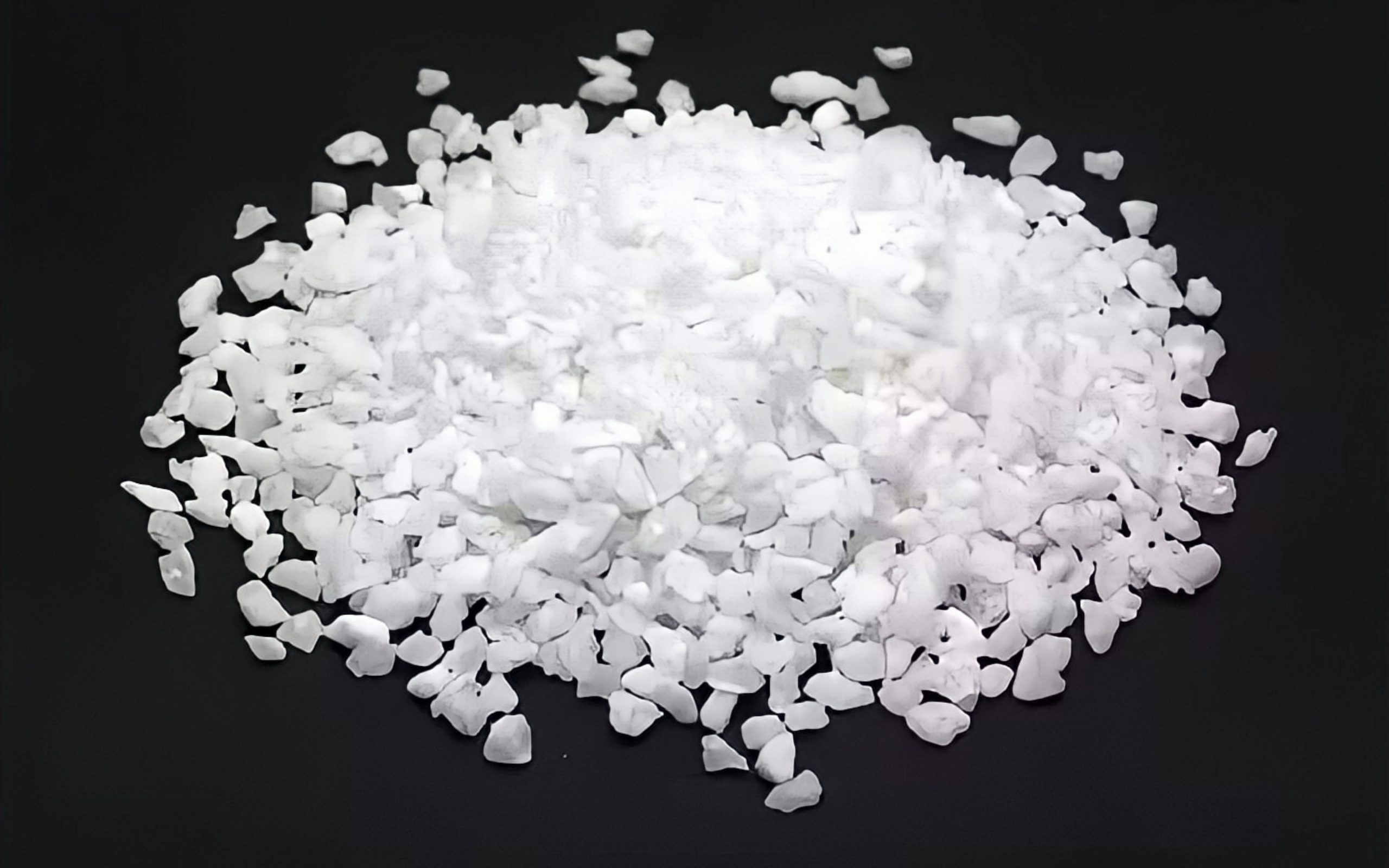
granallas de ceramica para chorro de arena
- Arena de sílice
La arena de sílice es el medio de chorreado más tradicional, utilizado principalmente para la limpieza de superficies y el rectificado, adecuado para industrias como la construcción y la construcción naval, pero debe seleccionarse cuidadosamente cuando se procesan piezas de alta precisión.
Sus características incluyen:
- Económico: En comparación con otros medios de chorreado, la arena de sílice tiene un coste inferior y es adecuada para aplicaciones industriales a gran escala.
- Descontaminación eficaz: Adecuado para eliminar las capas de óxido y pintura más gruesas, pero puede provocar cierto grado de rugosidad en la superficie.
- Granalla
La granalla Pad es un nuevo tipo de granalla que se ha hecho cada vez más popular en los últimos años, utilizada principalmente para el tratamiento de superficies que requieren poco desgaste. Esta granalla es muy adecuada para industrias que requieren un acabado superficial extremadamente alto, como los dispositivos ópticos y los productos de consumo de gama alta.
Entre sus ventajas destacan:
- Tratamiento flexible: Limpieza suave de la superficie para reducir los daños al sustrato.
- Versatilidad: Adecuado para una gran variedad de materiales, incluidos el vidrio y el plástico.
- Otros abrasivos especiales
Además de los abrasivos comunes mencionados anteriormente, existen algunos abrasivos especiales, como partículas de plástico, corindón, etc., cada uno de los cuales tiene un escenario de aplicación específico. La selección debe analizarse en función de los requisitos específicos de grabado y las propiedades del material.
Al seleccionar el material de chorreado, además de considerar las propiedades del material, deben tenerse en cuenta los siguientes factores:
- Material de la pieza: Los distintos materiales influyen mucho en la selección de la granalla. Materiales como el metal, el vidrio y la cerámica requieren medios diferentes.
- Requisitos de superficie: Seleccione el tamaño y el tipo de partícula de material adecuados en función de los requisitos de rugosidad y acabado de la superficie.
- Escala de procesamiento: Las aplicaciones industriales a gran escala pueden requerir medios más económicos, mientras que los trabajos de alta precisión requieren materiales más especializados.
Comparando y seleccionando distintos medios de chorreado, se puede conseguir el mejor efecto de grabado, mejorando así la adherencia del revestimiento y garantizando la seguridad y eficacia de las aplicaciones industriales.
El grabado industrial es de gran importancia para mejorar la adherencia de los revestimientos. Seleccionando los medios y la tecnología de chorreado adecuados, se pueden conseguir efectos de grabado más precisos. No sólo se ha utilizado en muchas industrias, como la aeroespacial, la de fabricación de automóviles y la del petróleo y el gas, sino que también proporciona un sólido apoyo técnico a la industria moderna. Con el desarrollo industrial y el progreso tecnológico, los procesos de grabado seguirán evolucionando para satisfacer requisitos de rendimiento más elevados y escenarios de aplicación más complejos. Dominar los principios científicos y las aplicaciones prácticas del grabado dará a las empresas más ventajas en la feroz competencia del mercado.
Espero que este artículo pueda proporcionar a los lectores una comprensión profunda del grabado y su aplicación en la adhesión de revestimientos, e inspirar una exploración más profunda de este campo.
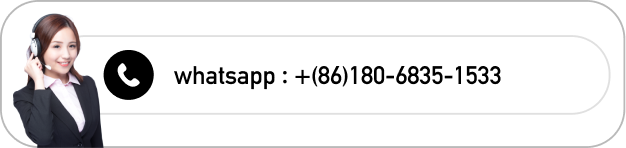