Ceramic Beads User Manual: 7 Steps to Improve Mold Finish
12 de febrero de 2025
Maintaining a consistent finish is one of the key goals during mold manufacturing and maintenance. However, even if the standard process is strictly followed, many customers still encounter the following problems:
“Why is the mold finish still not up to standard?”
“How to avoid scratching the mold surface during sandblasting?”
“How to optimize the use efficiency of ceramic beads?”
The essential needs of these problems are:
- Repeatability – the finish of different batches of molds must be consistent.
- Cost controllability – reduce media loss and labor costs and improve cost performance.
- Seguridad operativa – ensure safe production through dust control and equipment protection.
In response to the above needs, we have summarized a 7-step professional process to help you improve the mold finish efficiently and safely.
Step 1: Pre-treatment inspection to eliminate the source of hidden dangers
Puntos débiles del cliente
- Ignoring minor defects (such as 0.1mm scratches) leads to subsequent polishing failure.
- Poor equipment status (such as nozzle wear) wastes media and reduces the sandblasting effect.
Solución
1.1 Mold Defect Detection
Use a 20x magnifying glass to check the mold surface, focusing on the parting line and venting groove. A portable surface roughness meter (such as Mitutoyo SJ-210) is recommended to measure the surface condition accurately.
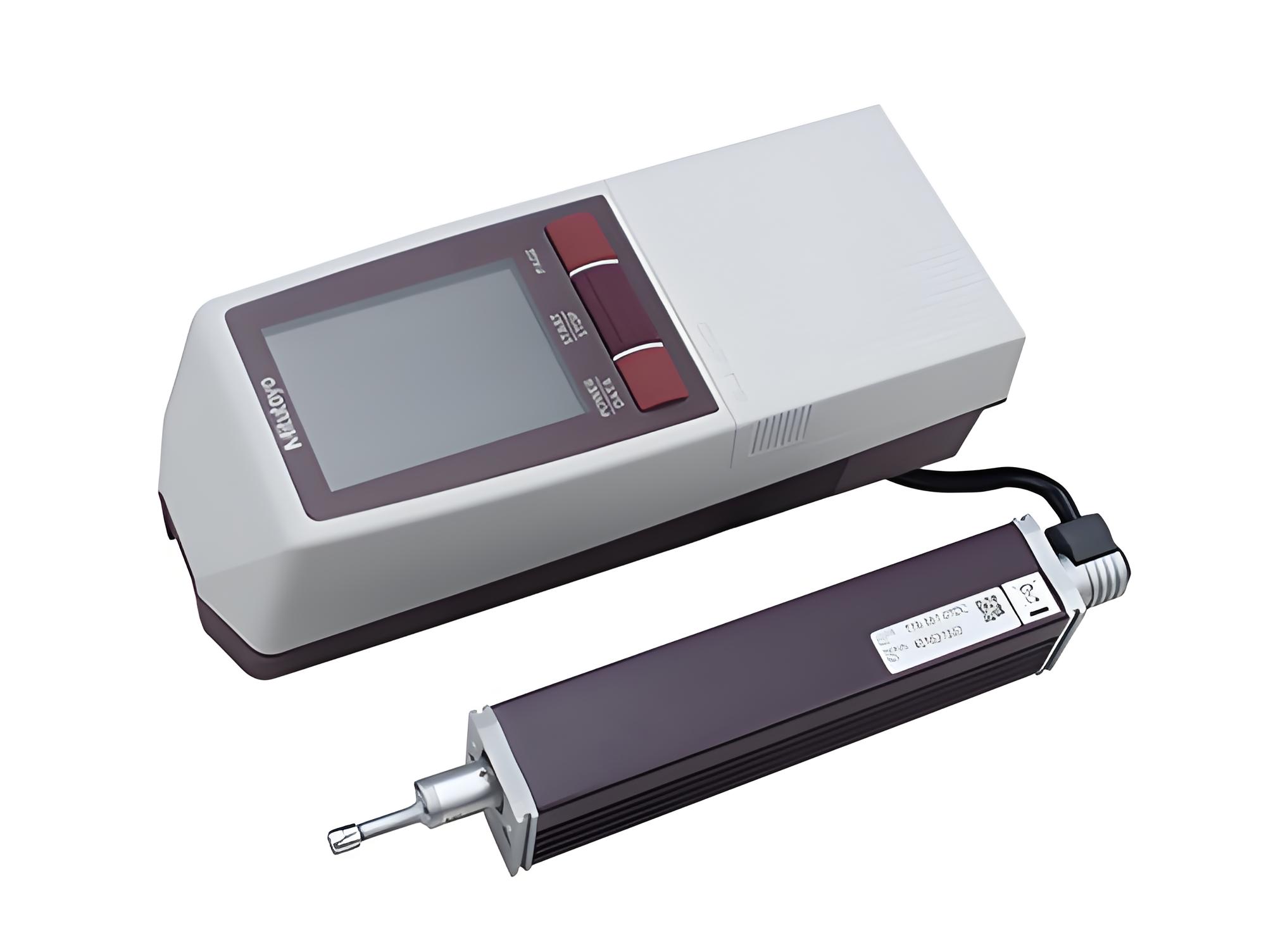
1.2 Equipment pre-inspection list
- Nozzle wear: The inner diameter change should be≤5%, and it needs to be replaced if it exceeds.
- Air pressure stability: Fluctuation range≤±2 PSI to avoid unstable injection.
Step 2: Pressure setting formula, science replaces experience
Puntos débiles del cliente
- Relying on experience to set pressure leads to over-grinding of soft materials or insufficient cleaning of hard materials.
Material type | Material coefficient |
---|---|
Plastic (ABS) | 0.8 |
Aluminum alloy | 1.2 |
Acero inoxidable | 1.5 |
Titanium alloy | 2.0 |
Carbide | 2.5 |
Solución
2.1 PSI calculation formula
PSI = medium hardness × workpiece material coefficient × 10
Example calculation:
Titanium alloy mold, using ceramic beads with 7 Mohs hardness:
PSI = 7 × 2.0 × 10 = 140
2.2 Pressure adjustment tips
Measure the Ra value after the first operation: if the Ra value is too high, increase PSI 5-10; if the Ra value is too low, reduce PSI 5-10.
Soft material protection: For plastic molds, the upper limit of PSI is 80 to avoid over-grinding.
Efficient cleaning of hard materials: For titanium alloy molds, the lower limit of PSI is 140 to ensure the cleaning effect.
Step 3: Angle and distance control, the victory of geometric mechanics
Puntos débiles del cliente
- Vertical injection leads to local over-grinding, and the 30°incident angle is difficult to accurately control.
Solución
3.1 30°incident angle optimization solution
- At a 30°incident angle, tangential force accounts for 70%, and normal force accounts for 30%, balancing cleaning efficiency and surface protection.
- Spray distance = nozzle diameter × 10 (for example: 8mm nozzle → 80mm distance)
3.2 Practical tools
The laser angle indicator (error ±1°) ensures precise angle control.
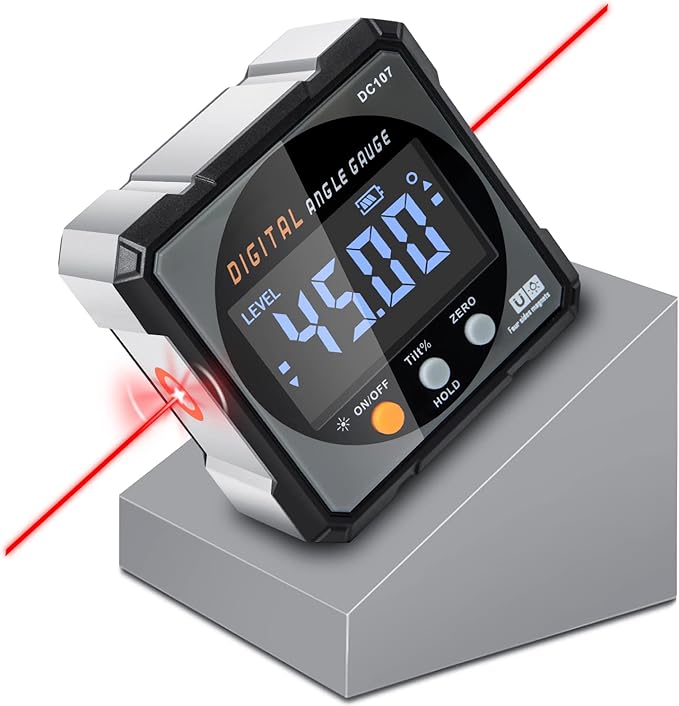
Step 4: Media status monitoring, the key to extending life
Puntos débiles del cliente
- Unable to determine when to replace ceramic beads, resulting in cost waste or quality degradation.
Solución
4.1 Crushing rate detection
Take 100g of media and manually sort the crushed particles. If the crushing rate is >5%, it needs to be replaced.
4.2 Online Intelligent Monitoring
Install an online particle size sensor to monitor the change of media particle size in real-time.
HLH ceramic beads model | Standard particle size (µm) | Allowable deviation (µm) |
---|---|---|
B20 | 600-850 | ±50 |
B30 | 425-600 | ±35 |
B40 | 250-425 | ±20 |
B60 | 125-250 | ±15 |
B80 | 180-250 | ±15 |
B100 | 125-180 | ±10 |
B120 | 63-125 | ±8 |
B125 | 0-125 | ±8 |
B170 | 45-90 | ±5 |
B205 | 0-63 | ±5 |
B400 | 30-63 | ±3 |
B505 | 10-30 | ±2 |
Step 5: Post-processing quality inspection standards, data-based acceptance
Puntos débiles del cliente
- Only visual inspection leads to delayed exposure of the problem of substandard finish.
Solución
5.1 Recommended Ra value measurement tools
Basic model: Time 3220 handheld roughness tester
Advantages: portable and easy to use, suitable for rapid on-site detection, accuracy ±5%.
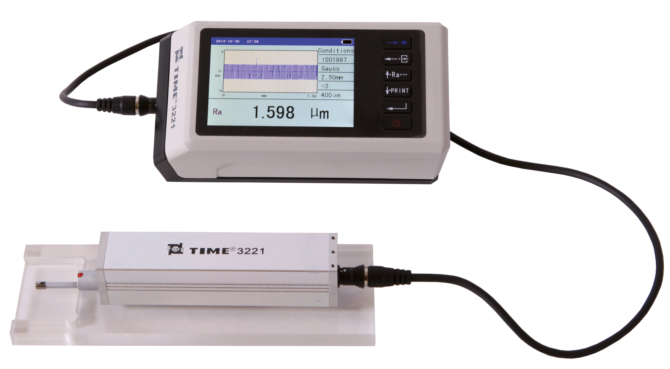
High-precision model: Zygo NewView 9000 3D optical profiler.
Advantages: high-precision measurement, suitable for complex surfaces, resolution up to nanometer level.
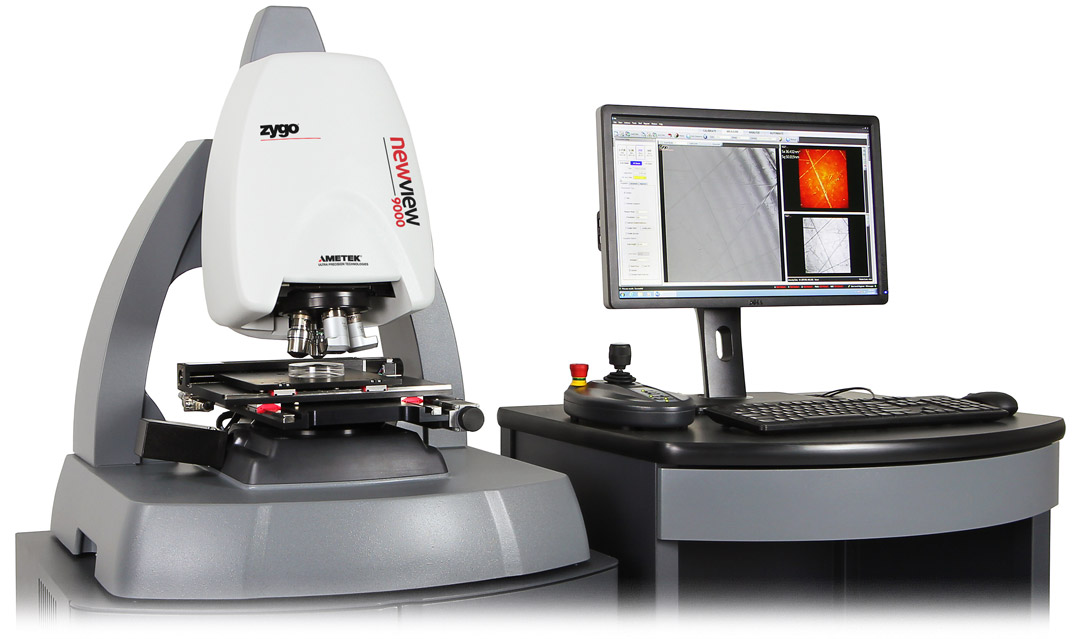
5.2 Industry Ra value standards
Selected industries | Common materials | Ra requirements (µm) | Number of test points |
---|---|---|---|
Componentes electrónicos | Copper alloy connectors | ≤0.4 | ≥10 points/㎡ |
Precision plastic housings | ≤0.6 | ≥8 points/㎡ | |
Autopartes | Aluminum alloy engine parts | ≤0.8 | ≥5 points/㎡ |
Stainless steel brake discs | ≤1.0 | ≥6 points/㎡ | |
Medical devices/implants | Titanium alloy orthopedic implants | ≤0.4 | ≥12 points/㎡ |
Stainless steel surgical instruments | ≤0.6 | ≥10 points/㎡ | |
Aeroespacial | Palas de turbina de aleación de titanio | ≤0.3 | ≥15 points/㎡ |
High temperature alloy engine parts | ≤0.5 | ≥10 points/㎡ |
Step 6: Waste treatment specifications, compliance and cost reduction in parallel
Puntos débiles del cliente
- Waste treatment costs are high, and there are environmental risks.
Solución
6.1 ceramic beads recycling process
Magnetic separation (removal of metal impurities) → air separation (removal of dust) → screening (grading and reuse)
Recovery rate: ≥85% (crushing rate must be controlled <5%).
6.2 Compliance treatment of waste materials
- Ceramic dust (harmless landfill)
- Metal debris (professional recycling)
Step 7: Troubleshooting common problems, quick response guide
Puntos débiles del cliente
- Sudden problems (such as uneven surface) cause production line stagnation
Solución
Problem phenomenon | Possible reasons | Solución |
---|---|---|
Partial matte | Uneven distribution of media | Check the sand separator and clean the blockage point |
Periodic stripes | Nozzle eccentric wear | Replace the nozzle and calibrate the concentricity |
Over-polishing of edges | The incident angle is too large (>45°) | Adjust the angle to 30° and reduce the PSI |
Surface scratches | Improper selection of media granularity | Replace the ceramic sand with the appropriate particle size |
Excessive dust residue | Dust removal system is inefficient | Check the dust removal equipment and clean the filter element |
Partial overheating of mold | Injection time is too long | Shorten the single injection time and increase the cooling interval |
FAQ: Quick answer to high-frequency questions
Q: How many times do the ceramic beads need to be replaced after being recycled?
A: It is recommended to be 20 times, or the crushing rate is >5% (whichever comes first).
Q: How do you deal with the electrostatic adsorption dust of the mold after the ceramic beads operation?
A: Use an ion air gun to blow + wipe with anhydrous ethanol.
Q: How do we avoid deformation of thin-walled molds (<1mm)?
A: Use fine sand above #220, PSI≤50, and reduce the angle of incidence to 20°.
Through this 7-step professional process, you can not only solve the surface problem of the mold finishes not meeting the standard but also achieve:
- Cost reduction: medium loss is reduced by 30%, and the equipment maintenance interval is extended by 2 times.
- Quality improvement: finish consistency (CV value) is compressed from 5% to ≤2%.
- Compliance guarantee: 100% meets ISO 9001/14001 and industry-specific standards.
Go and practice it now.
If you have any questions, please contact us for a free consultation~
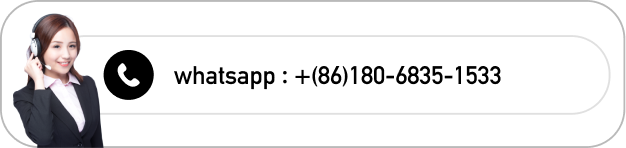