Granalla cerámica o granalla de acero: ¿Qué es mejor para la limpieza a chorro?
7 de enero de 2025
El chorreado de arena desempeña un papel vital en la fabricación y el mantenimiento modernos. No sólo proporciona una base lisa para el posterior pintado u otros tratamientos superficiales, sino que también mejora eficazmente las propiedades mecánicas y la calidad del aspecto de la superficie.
En el chorreado de arena es fundamental elegir el medio de chorreado adecuado. Aunque la granalla de acero se ha utilizado ampliamente durante mucho tiempo como medio de chorreado tradicional, los medios de chorreado cerámicos han ido superando gradualmente a la granalla de acero en muchas de las mismas aplicaciones debido a su excelente rendimiento. En este artículo se compararán en detalle estos dos medios especiales de chorreado de arena para ayudar a los lectores a hacer la elección más adecuada en aplicaciones prácticas.
Cuentas de cerámica
Se trata de un tipo relativamente nuevo de material para chorro de arena, que se ha ido extendiendo gradualmente a medida que aumentaba la demanda de la industria de medios de chorro de arena finos, respetuosos con el medio ambiente y duraderos. Los medios de chorro de arena con óxido de circonio y otros materiales altamente resistentes al desgaste como componentes principales, un proceso de fabricación único que hace que tenga una estructura esférica uniforme y una textura dura, que puede proporcionar un efecto de limpieza eficiente al procesar la superficie de la pieza de trabajo.
Características del producto
- Forma esférica, la presión generada durante el proceso de arenado es relativamente uniforme, lo que puede reducir eficazmente los daños superficiales.
- Una baja generación de polvo es esencial para la protección del medio ambiente y la salud de los operarios.
- En comparación con otros medios de chorreado, tiene una vida útil más larga y puede reciclarse varias veces, lo que reduce los costes de uso a largo plazo.
- Su elevada dureza (dureza Mohs 9) y su moderada fuerza de impacto le confieren importantes ventajas en la eliminación eficaz de revestimientos, escamas, manchas de aceite, etc.
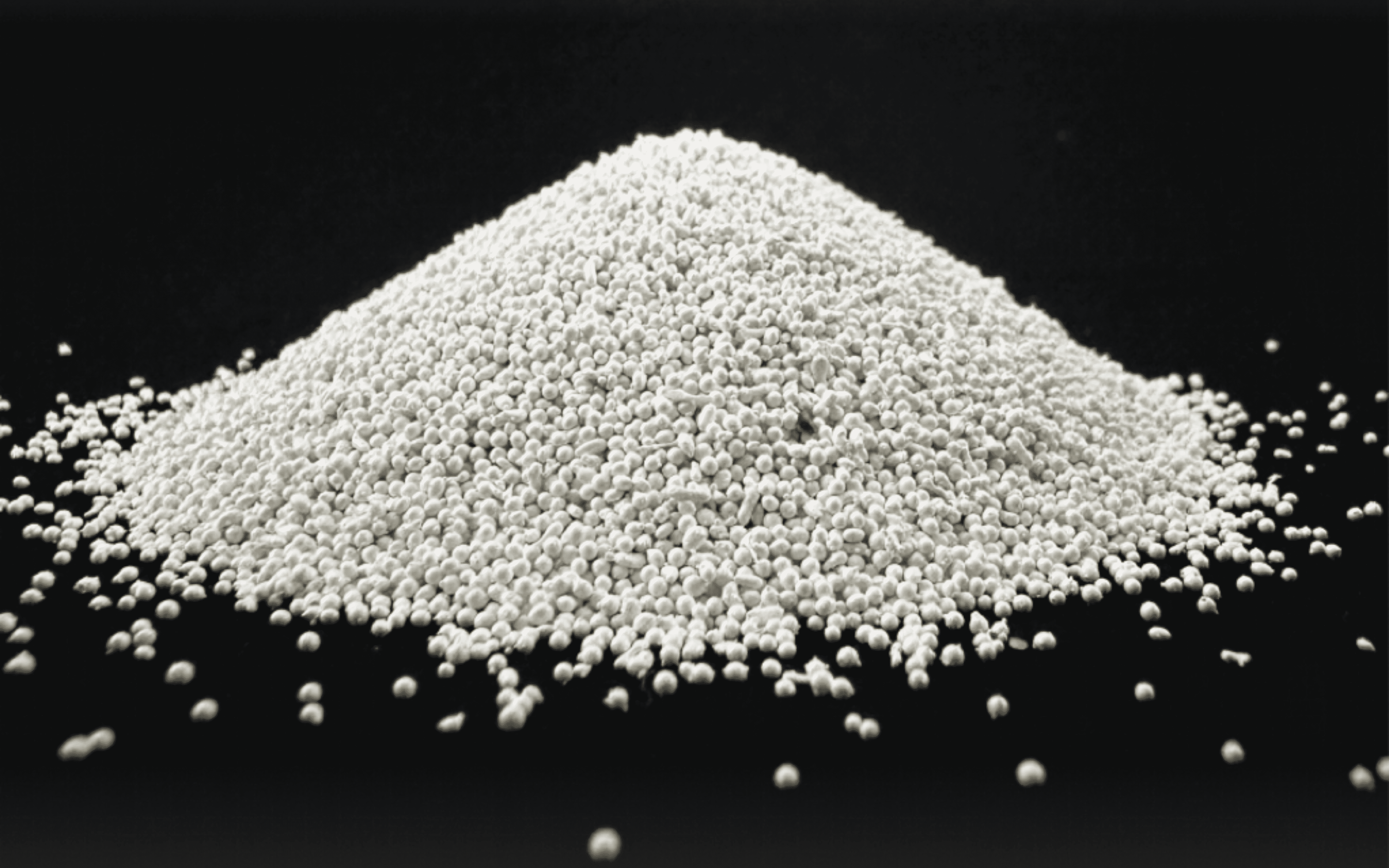
Grano de acero
Es un medio de chorro de arena tradicional que ha desempeñado un papel en las primeras aplicaciones industriales, como el tratamiento de superficies metálicas. Sus características de alto impacto lo han convertido en un material importante para el tratamiento de superficies en el proceso de chorro de arena. Las partículas de granalla de acero son relativamente rugosas y tienen formas angulares irregulares. En comparación con las microesferas cerámicas, tiene una vida útil más corta y debe sustituirse con más frecuencia.
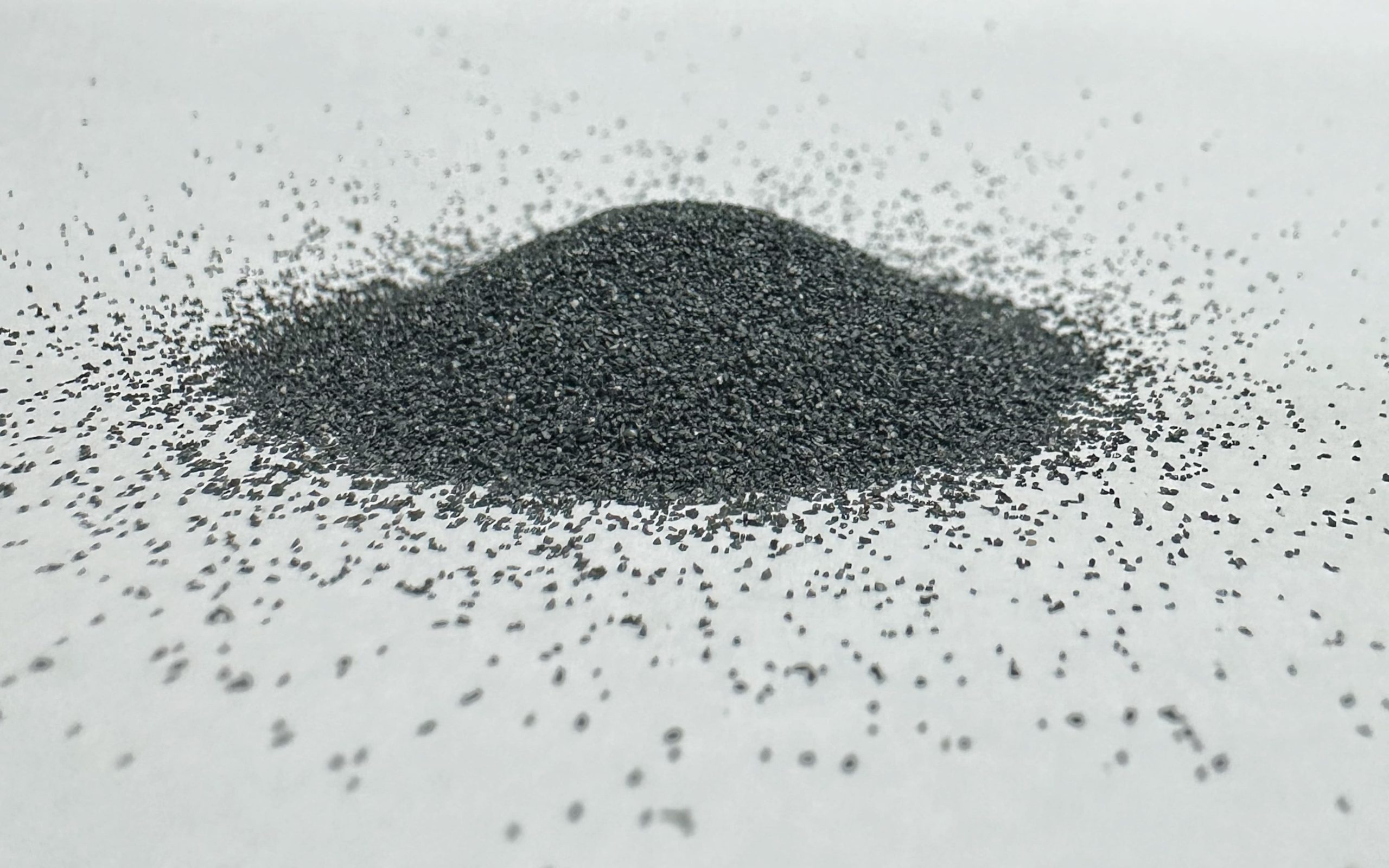
Características del producto
- La estructura angular permite un mayor impacto durante el proceso de arenado, lo que resulta adecuado para eliminar óxido pesado, revestimientos resistentes, etc.
- La granalla de acero suele ser más barata que los granos de chorreado cerámicos, y su menor coste es adecuado para proyectos con presupuestos limitados y a gran escala.
- Debido a su alto impacto, la granalla de acero dejará una textura más rugosa en la superficie de la pieza, lo que favorece la adherencia del revestimiento.
Campos de aplicación de la granalla de acero y las microesferas cerámicas
Componentes electrónicos
- Obleas semiconductoras
- Placas de circuito impreso
- Conectores y clavijas
- Carcasas de sensores
Autopartes
- Componentes del motor
- Discos y pastillas de freno
- Partes del cuerpo
- Componentes del tubo de escape
- Piezas del sistema de dirección
Productos sanitarios
- Instrumental quirúrgico
- Implantes
- Catéteres
- Carcasas de bombas médicas
- Agujas y piezas médicas pequeñas
Moldes
- Moldes de inyección
- Moldes de fundición
- Moldes de estampación
- Moldes de fundición a presión
Aeroespacial
- Álabes de turbina
- Carcasas del fuselaje
- Ruedas de avión
- Carcasas de aviónica
- Piezas de motor
Piezas de barcos
- Hélices
- Juntas del casco
Piezas de equipos industriales
- Carcasas de bombas y válvulas
Ventajas del granallado cerámico
Los granos de chorreado cerámicos presentan ventajas significativas en la limpieza con chorro de arena. Estas características las hacen superiores a la granalla de acero tradicional en los escenarios de aplicación mencionados. A continuación se detallan las ventajas únicas de las granallas cerámicas en términos de rendimiento medioambiental, vida útil, efectos superficiales, etc.
Rendimiento medioambiental: menor generación de polvo
Según los datos de investigación medioambiental de la Asociación de la Industria Alemana, la generación de polvo de los abrasivos cerámicos en funcionamiento real es más de 80% inferior a la de la granalla de acero, como se muestra a continuación:
- Perlas de cerámica: la concentración de polvo es de aproximadamente 0,2 mg/m³
- Granalla de acero: la concentración de polvo alcanza 1 mg/m³
Esto no sólo cumple las normas de seguridad de la OSHA (Occupational Safety and Health Administration), sino que también reduce en gran medida la frecuencia de mantenimiento de los equipos de eliminación de polvo.
Vida útil: mayor eficiencia del ciclo
Los datos medidos muestran que la granalla cerámica puede reciclarse una media de 35 veces y hasta 50 veces en operaciones de chorro de arena de alta intensidad, mientras que la vida útil de la granalla de acero suele ser de 7 a 10 veces.
Un experimento comparativo realizado por una empresa de fabricación aeronáutica demostró que las microesferas cerámicas pueden procesar más de 4 veces la superficie por kilogramo de granalla de acero, y aún así pueden mantener más del 70% de su eficacia original tras un uso repetido.

Efecto de superficie: calidad de procesamiento más uniforme
Los datos facilitados por el Laboratorio Internacional de Procesamiento de Materiales muestran que los abrasivos cerámicos pueden controlar con mayor precisión la rugosidad superficial de las piezas tras el chorreado, lo que resulta idóneo para situaciones de alta exigencia:
- Industria del molde: El valor Ra de rugosidad de la superficie del molde tratada con granalla cerámica se distribuye uniformemente en el rango de 0,3-0,5 μm, mientras que la granalla de acero fluctúa mucho, pudiendo estar entre 1-2 μm.
- Las microesferas de chorreado cerámico pueden producir un efecto mate uniforme en la superficie de la aleación de titanio, manteniendo al mismo tiempo la biocompatibilidad del material.
Seguridad operativa: la baja fuerza de impacto reduce los daños en la superficie
Los experimentos demuestran que la fuerza de impacto de las microesferas cerámicas es sólo 50% de la de la granalla de acero, lo que se manifiesta específicamente de la siguiente manera:
- Tras el chorreado de la superficie de piezas de aluminio, la profundidad de indentación superficial de los medios de chorreado cerámicos es de 10 μm, mientras que la profundidad de indentación de la granalla de acero alcanza los 30 μm, lo que aumenta significativamente el riesgo de daños materiales.
- En la aplicación de superficies de equipos de precisión (como álabes de turbinas aeroespaciales), el granallado cerámico puede reducir significativamente las microfisuras y las reducir la tasa de reprocesamiento en unos 30%.
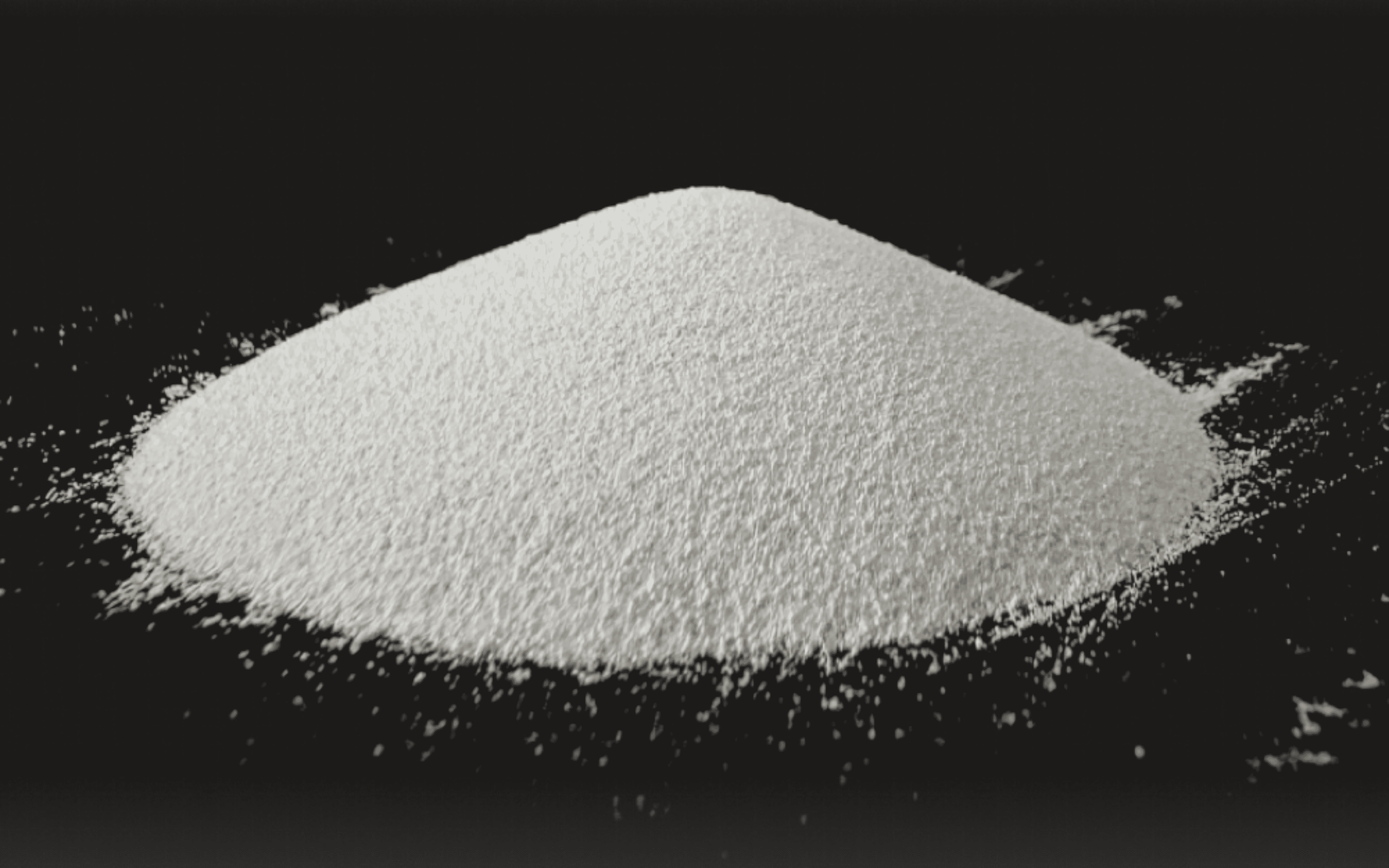
Gran adaptabilidad: amplia gama de aplicaciones
Según los comentarios de los clientes, las granallas cerámicas se utilizan ampliamente en los siguientes sustratos y escenarios especiales:
- Sustratos metálicos: se utiliza para limpiar y pulir las superficies de aleaciones de titanio y aleaciones con base de níquel en la industria aeronáutica.
- Sustratos plásticos: proporcionan texturas suaves en el tratamiento de superficies de piezas interiores de automóviles (como salpicaderos y guarnecidos de puertas), sustituyendo a los procesos tradicionales de limpieza química.
- Sustratos cerámicos y de vidrio: consigue una representación de texturas finas, como el grabado de espejos de vidrio industriales.
Ventajas económicas: reducción de los costes generales de explotación
Según datos de casos reales, las empresas que utilizan granalla cerámica pueden ahorre hasta 25%-40% de costes cada año, debido principalmente a:
- Costes de mantenimiento del equipo: la baja generación de polvo reduce la frecuencia de limpieza del sistema de filtrado, prolonga la vida útil y reduce los costes de mantenimiento en unos 20%.
- Ahorro de costes de mano de obra: el efecto del tratamiento superficial producido por el granallado cerámico es más fino, no se requiere ningún tratamiento secundario adicional y el tiempo de operación se reduce en 15%-25%.
- Inversión en material a largo plazo: a pesar del mayor coste inicial, el tiempo medio de uso de cada tonelada de granalla cerámica es unas 3 veces superior al de la granalla de acero.
Ventajas de la granalla de acero
Como medio de chorreado tradicional y ampliamente utilizado, la granalla de acero es inferior a los granos de chorreado cerámicos en todos los aspectos, pero sigue ocupando una posición importante en muchos campos industriales debido a su gran resistencia y economía únicas.
Gran fuerza de impacto: elimina rápidamente los contaminantes más resistentes de la superficie
- Al eliminar capas gruesas de óxido, escamas de óxido duro y revestimientos multicapa, la granalla de acero puede producir un fuerte efecto de impacto en poco tiempo y eliminar rápidamente los contaminantes de la superficie.
- La estructura angular de las partículas mejora aún más el rendimiento de corte y es especialmente adecuada para limpiar la superficie de materiales de alta resistencia. En los proyectos de eliminación de óxido superficial de puentes, barcos y maquinaria pesada, suele preferirse la granalla de acero.
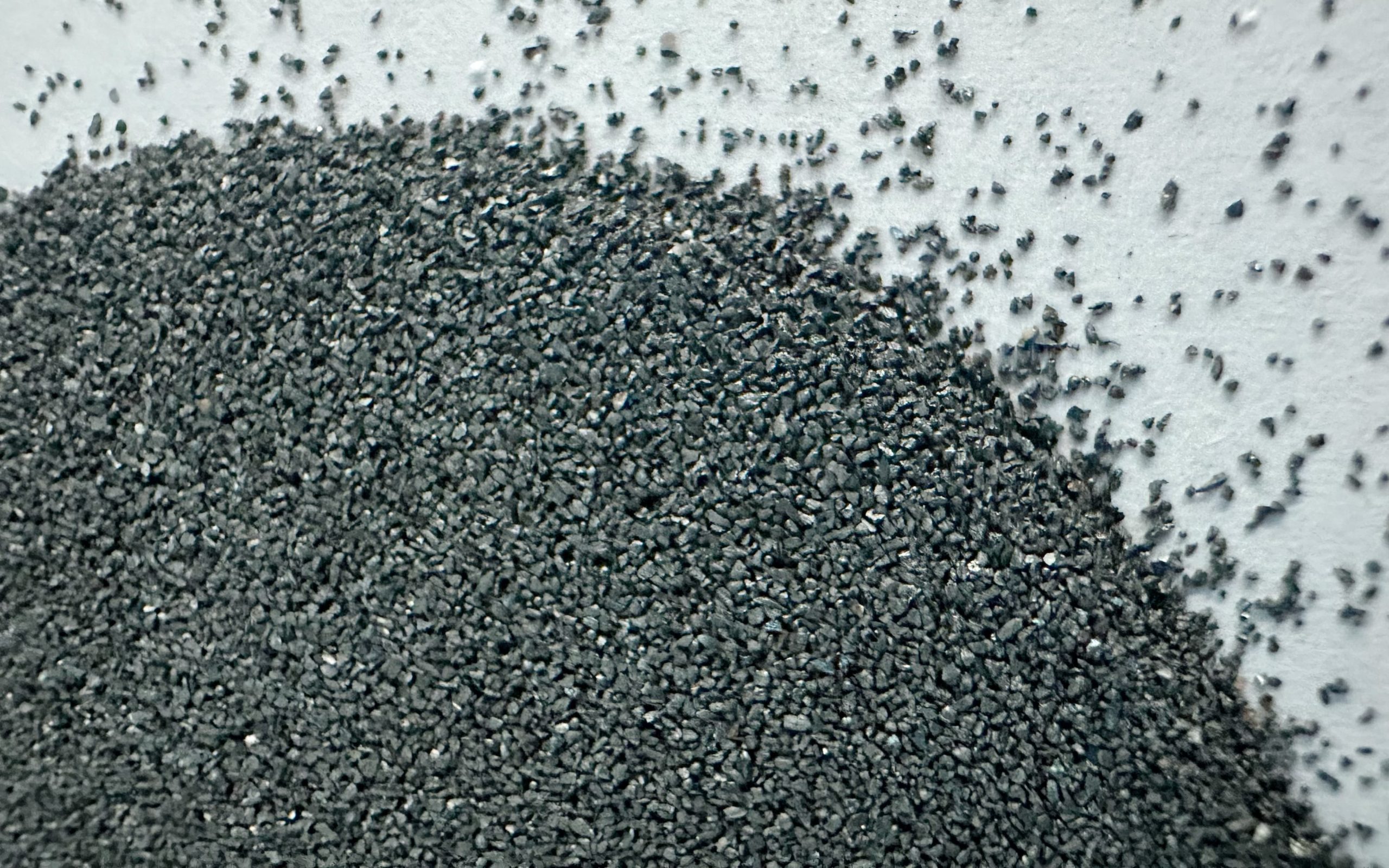
Rentabilidad: bajo precio del material
-
En comparación con los abrasivos de gama alta, como las microesferas cerámicas, el coste de adquisición inicial de la granalla de acero es relativamente bajo, normalmente entre 1/3 y 1/2 del de los abrasivos cerámicos, lo que resulta especialmente adecuado para proyectos a gran escala con presupuestos limitados.
-
Aunque haya que sustituirlo con frecuencia, el coste total del material sigue siendo muy competitivo gracias a su bajo precio.
Múltiples opciones de tamaño de partícula: satisfacen diferentes requisitos de proceso
- La granalla de acero puede proporcionar una gran variedad de especificaciones granulométricas según los requisitos de la aplicación, desde partículas ultrafinas a partículas gruesas:
La granalla de acero de grano grueso es adecuada para eliminar contaminantes pesados y crear texturas superficiales rugosas, proporcionando una mayor adherencia para el revestimiento posterior.
La granalla de acero de grano fino se utiliza para el tratamiento relativamente fino de superficies, como el lijado ligero y el pretratamiento suave de superficies metálicas.
- Por ejemplo, en la industria de reparación de automóviles, la granalla de acero de grano grueso se utiliza para prevenir la oxidación y limpiar el chasis, mientras que la granalla de acero de grano fino se emplea para el chorreado de la superficie de la carrocería.
Propiedades mecánicas superiores: gran dureza y tenacidad
- La granalla de acero tiene una dureza elevada (normalmente entre 40 y 65 HRC) y una gran tenacidad. Puede soportar impactos de alta intensidad sin romperse fácilmente. Es especialmente adecuada para procesar sustratos de gran dureza, como acero al carbono, acero inoxidable y hierro fundido.
- Incluso en entornos de altas temperaturas, el rendimiento de la granalla de acero se mantiene estable sin ablandarse ni degradarse.
Bajo umbral técnico: adaptable a una gran variedad de equipos
- La mayoría de los equipos de chorro de arena del mercado admiten granalla de acero como medio, sin necesidad de costes adicionales de modificación del equipo.
- El equipo tiene un bajo coste de uso, especialmente adecuado para pequeñas y medianas empresas y contratistas de proyectos.
Buena resistencia al desgaste: adecuada para un uso repetido
- Aunque el número de ciclos de la granalla de acero no es tan bueno como el de las microesferas cerámicas, su resistencia al desgaste sigue siendo competitiva entre los medios tradicionales. La vida útil individual es de unas 7-10 veces, lo que basta para satisfacer las necesidades de los proyectos a medio y corto plazo.
- Los experimentos muestran que el índice de pérdida de volumen de la granalla de acero de alta calidad en condiciones normales de uso es inferior a 1,5%, lo que demuestra una buena durabilidad.
Amplio reconocimiento del mercado
- El proceso de producción de la granalla de acero está maduro, la cadena de suministro es perfecta y puede adquirirse fácilmente en todo el mundo.
- Los operarios suelen estar familiarizados con el funcionamiento y el uso de la granalla de acero, lo que reduce los costes de formación.
Resumen: ¿Cómo elegir el medio de chorreado adecuado?
La granalla de acero y las microesferas cerámicas son los dos principales medios de limpieza por chorro de arena, y cada uno de ellos presenta ventajas significativas. Su aplicabilidad depende de los requisitos específicos de la aplicación, las características de la pieza y las limitaciones presupuestarias.
En aplicaciones industriales reales, la estrategia de chorreado "primero grueso y luego fino" es una solución común y eficaz. La combinación de granalla de acero y microesferas de chorreado cerámicas puede aprovechar al máximo las características de ambas:
- Tratamiento preliminar: Utilice granalla de acero para la limpieza preliminar de alto impacto para eliminar rápidamente grandes áreas de óxido o recubrimientos gruesos, sentando una base sólida para el tratamiento posterior.
- Tratamiento de refinado: Utilice granallas cerámicas para completar la homogeneización y el refinamiento de la superficie, mejorar la calidad de la superficie y lograr mayores requisitos visuales y funcionales.
Esta estrategia no sólo reduce el tiempo de procesamiento, sino que también encuentra un equilibrio ideal entre economía y efecto. Por ejemplo, en el mantenimiento de buques, la granalla de acero puede limpiar rápidamente la suciedad persistente del casco, mientras que las microesferas cerámicas se utilizan para el tratamiento detallado de hélices o piezas de precisión.
Los usuarios pueden elegir o combinar con flexibilidad granalla de acero y granalla cerámica en función de los requisitos específicos del proyecto. En la práctica, ajustar constantemente los parámetros del proceso y las soluciones de combinación de granallas es la clave para satisfacer las distintas necesidades. Espero que este artículo le proporcione una idea clara para elegir la granalla adecuada.
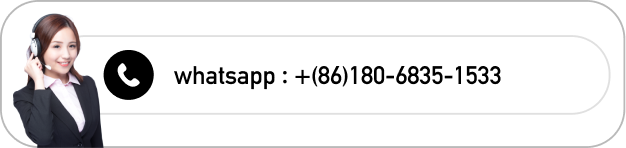