¿Pueden los medios cerámicos sustituir a las perlas de vidrio en el shot peening?
11 de diciembre de 2024
El shot peening es una tecnología de tratamiento de superficies clave en la fabricación moderna. La elección del medio de shot peening adecuado es crucial para el efecto y la economía del proceso. Este artículo compara las ventajas y desventajas de las microesferas de vidrio y los medios cerámicos en el shot peening, revelando que el shot peening cerámico ha sustituido gradualmente a las microesferas de vidrio como una opción más popular bajo requisitos de alto rendimiento y protección del medio ambiente.
La función del Shot Peening
La función principal del shot peening es formar una capa de tensión de compresión en la superficie del material mediante el impacto a alta velocidad de las partículas del medio, mejorando así el rendimiento del material.
Según los requisitos de la aplicación y las características de la industria, estas funciones pueden dividirse en los cuatro aspectos siguientes:
Mejorar la resistencia a la fatiga
Mejorar la resistencia a la corrosión
Mejorar la resistencia al desgaste
Mejorar la rugosidad de la superficie
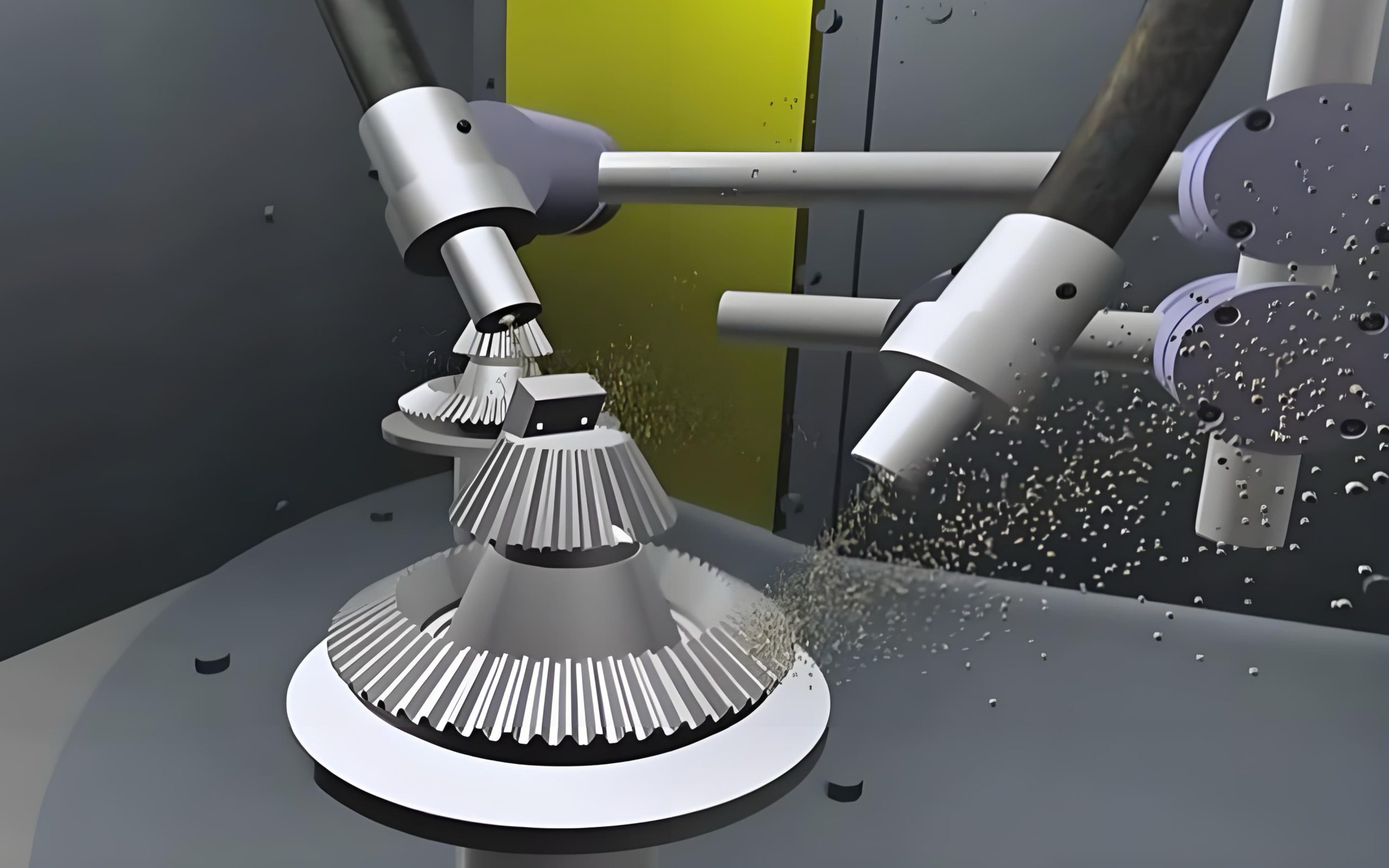
Tras analizar las funciones específicas del shot peening, la elección del medio adecuado se convierte en un eslabón clave que afecta al efecto técnico.
Las microesferas de vidrio y el granallado cerámico son dos medios de gran difusión, y sus respectivas propiedades físicas y rendimiento determinan sus campos de aplicación y los efectos del proceso.
A continuación, nos centraremos en analizar las características y el rendimiento de las aplicaciones de ambos para sentar las bases de la comparación funcional.
Introducción a las microesferas de vidrio y al granallado cerámico
Cuentas de vidrio
Antecedentes históricos:
Las microesferas de vidrio, como medio habitual de chorreado y pulido, tienen una historia de uso que se remonta a principios del siglo XX. Al principio, la aplicación de las microesferas de vidrio se concentraba principalmente en los procesos de limpieza y acabado de superficies metálicas.
Posteriormente, las microesferas de vidrio se convirtieron en un medio de granallado insustituible a la hora de procesar piezas de fundición de precisión, dispositivos de metales no ferrosos y algunas piezas que requieren un tratamiento superficial fino debido a sus ventajas, como el pequeño tamaño de las partículas, la reducida área de contacto con las piezas y la eliminación más uniforme de las tensiones.
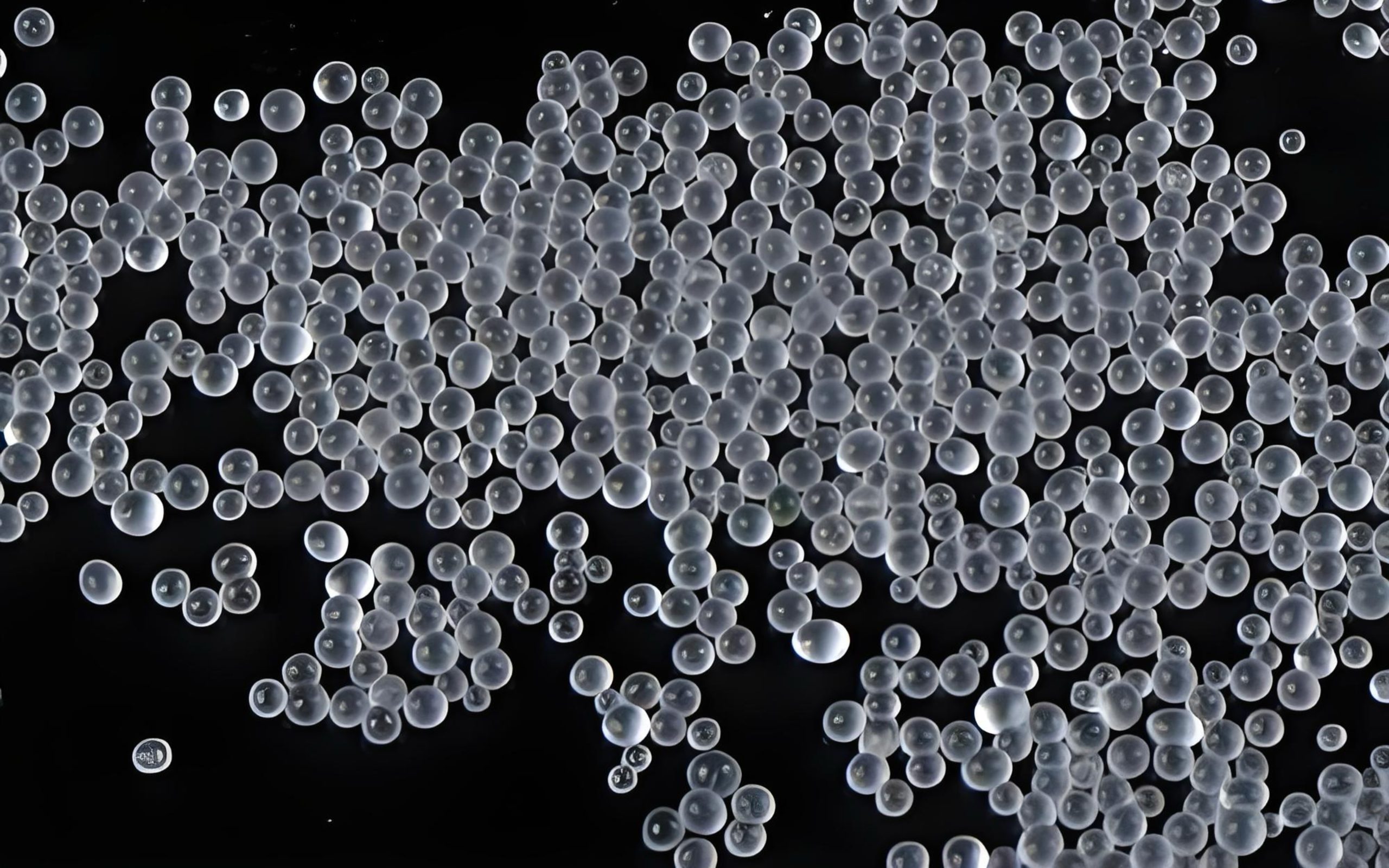
Propiedades físicas:
Partícula fabricada con arena de sílice de gran pureza o vidrio reciclado.
Mayoritariamente transparente o translúcido, uniformemente esférico, de superficie lisa, baja densidad y dureza generalmente entre 5-7 dureza Mohs.
Puede proporcionar una fuerza de bajo impacto y es adecuada para el acabado superficial más que para el refuerzo profundo.
Antecedentes históricos:
El origen del shot peening cerámico se remonta a mediados del siglo XX. Originalmente se utilizaba en los ámbitos aeroespacial y militar para satisfacer requisitos de procesamiento de alta resistencia y precisión.
A medida que madura su tecnología de producción, los medios cerámicos se han ido introduciendo gradualmente en otras industrias, como la fabricación de automóviles, el procesamiento de moldes y la construcción de estructuras de acero. Sus excelentes características de dureza, resistencia al desgaste y protección del medio ambiente hacen que destaque en la fabricación de alta gama.
Propiedades físicas:
Granalla fabricada por fusión a alta temperatura de materias primas cerámicas, enfriamiento y molienda.
Se trata de una esfera blanca de forma uniforme y redonda, que suele tener una dureza de entre 8 y 9 Mohs y una densidad elevada.
Tiene una buena resistencia al desgaste y es adecuado para los requisitos de tratamiento de superficies de alta resistencia.
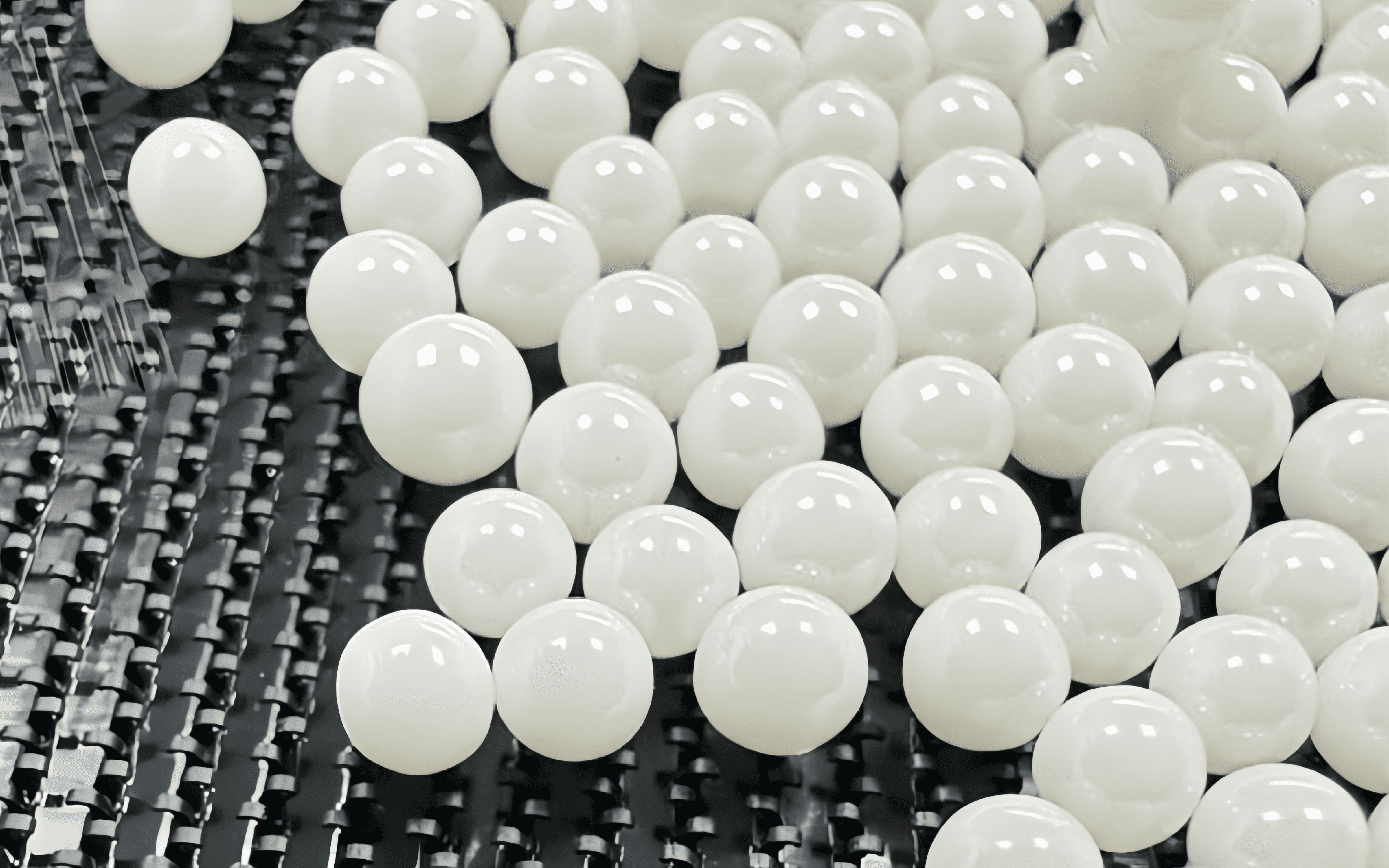
Consulte la tabla siguiente para conocer las propiedades químicas:
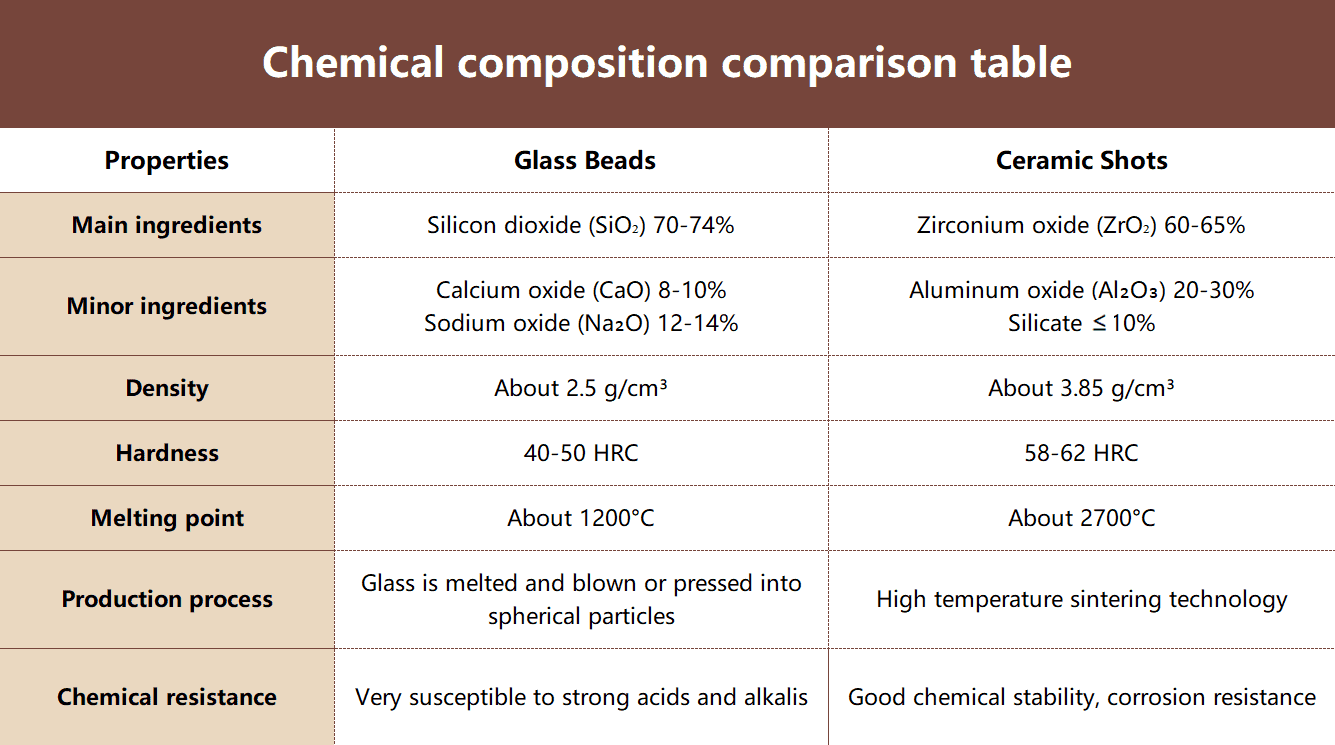
Después de comprender la información básica sobre las microesferas de vidrio y los medios cerámicos, compararemos más a fondo las funciones y los efectos de aplicación de estos dos medios, analizaremos sus ventajas y desventajas en el shot peening, y ayudaremos a los clientes a hacer una elección más científica.
Sectores de aplicación similares
Aeroespacial
Se utiliza para piezas estructurales de aeronaves y componentes de motores, como álabes de turbina y pieles de fuselaje.
Industria del automóvil
Se utiliza para aumentar la vida útil a la fatiga de componentes clave como muelles de suspensión, engranajes y ejes de transmisión de automóviles.
Industria energética (energía eólica y nuclear)
El eje principal y las piezas de conexión de las palas de los equipos de generación de energía eólica necesitan granallado para resistir cargas de alta frecuencia a largo plazo; los recipientes a presión y los componentes de las turbinas de las centrales nucleares también confían en el granallado para prolongar su vida útil.
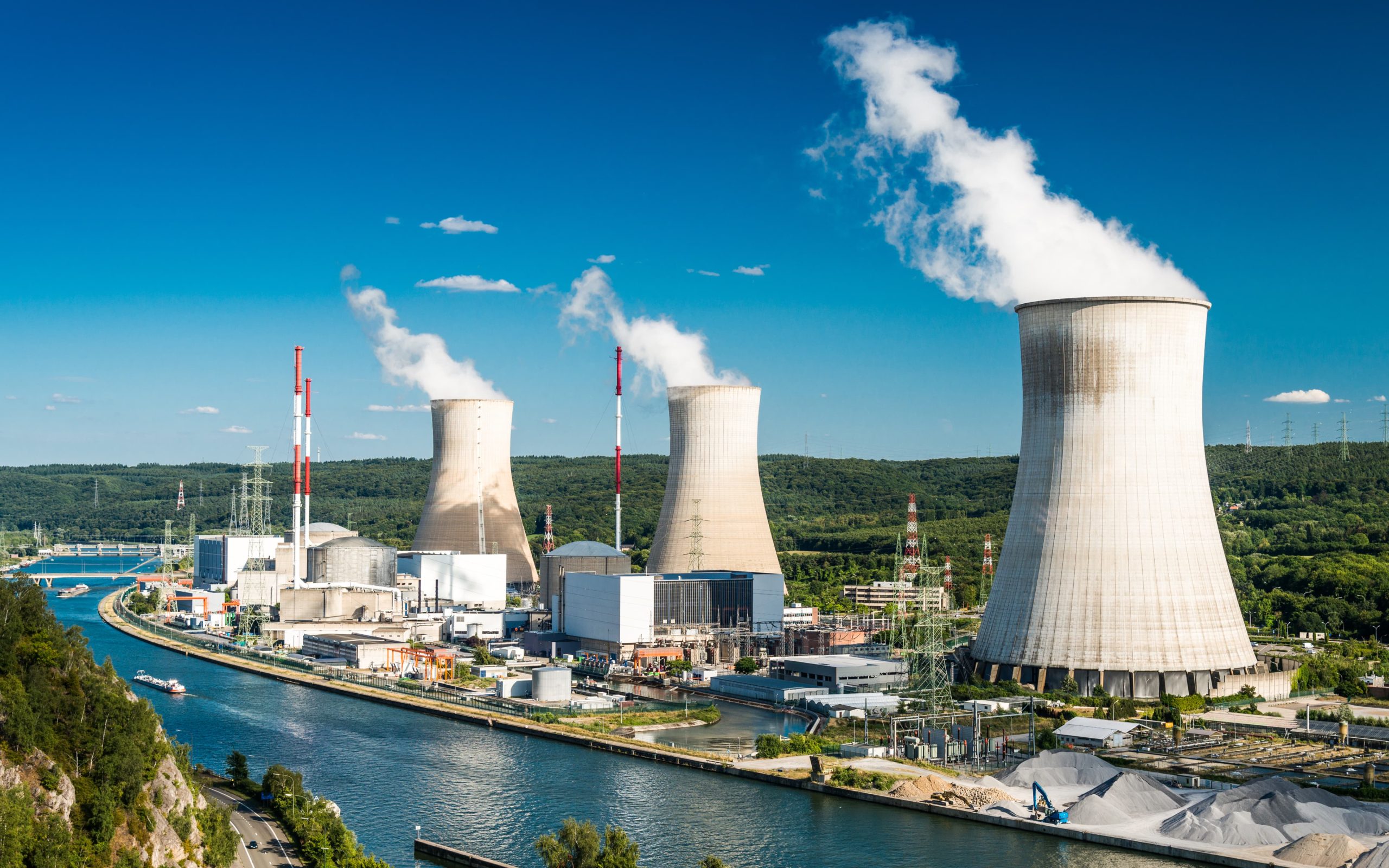
Fabricación de moldes
El granallado de la superficie del molde puede ralentizar el desgaste y aumentar la vida útil.
Productos sanitarios
Se utiliza para reforzar la superficie de implantes (como prótesis de cadera, tornillos, etc.) para aumentar la resistencia a la fatiga.
Aunque las funciones y los campos de aplicación del shot peening son muy amplios, en la producción real, los clientes suelen enfrentarse a una serie de puntos conflictivos, que son la clave para determinar la elección de los medios.
A continuación, analizaremos con más detalle los problemas y necesidades habituales de los clientes en el proceso de granallado.
Análisis de los puntos débiles del cliente
Uniformidad y estabilidad del refuerzo superficial
Por lo general, los clientes se preocupan por si los medios de granallado pueden seguir proporcionando un efecto de refuerzo superficial estable durante su uso. Esto incluye:
- Consistencia de procesamiento: La uniformidad de la forma y el tamaño de las partículas del material afecta directamente a la uniformidad de la capa de refuerzo superficial. Una distribución desigual de la tensión durante el procesamiento puede provocar la degradación o el fallo del rendimiento de los componentes.
- Durabilidad y estabilidad: En escenarios de uso de alta intensidad, la resistencia al desgaste, el índice de rotura y el rendimiento de retención de los medios son fiables, lo que está relacionado con la repetibilidad de la calidad de la superficie.

Compatibilidad de materiales
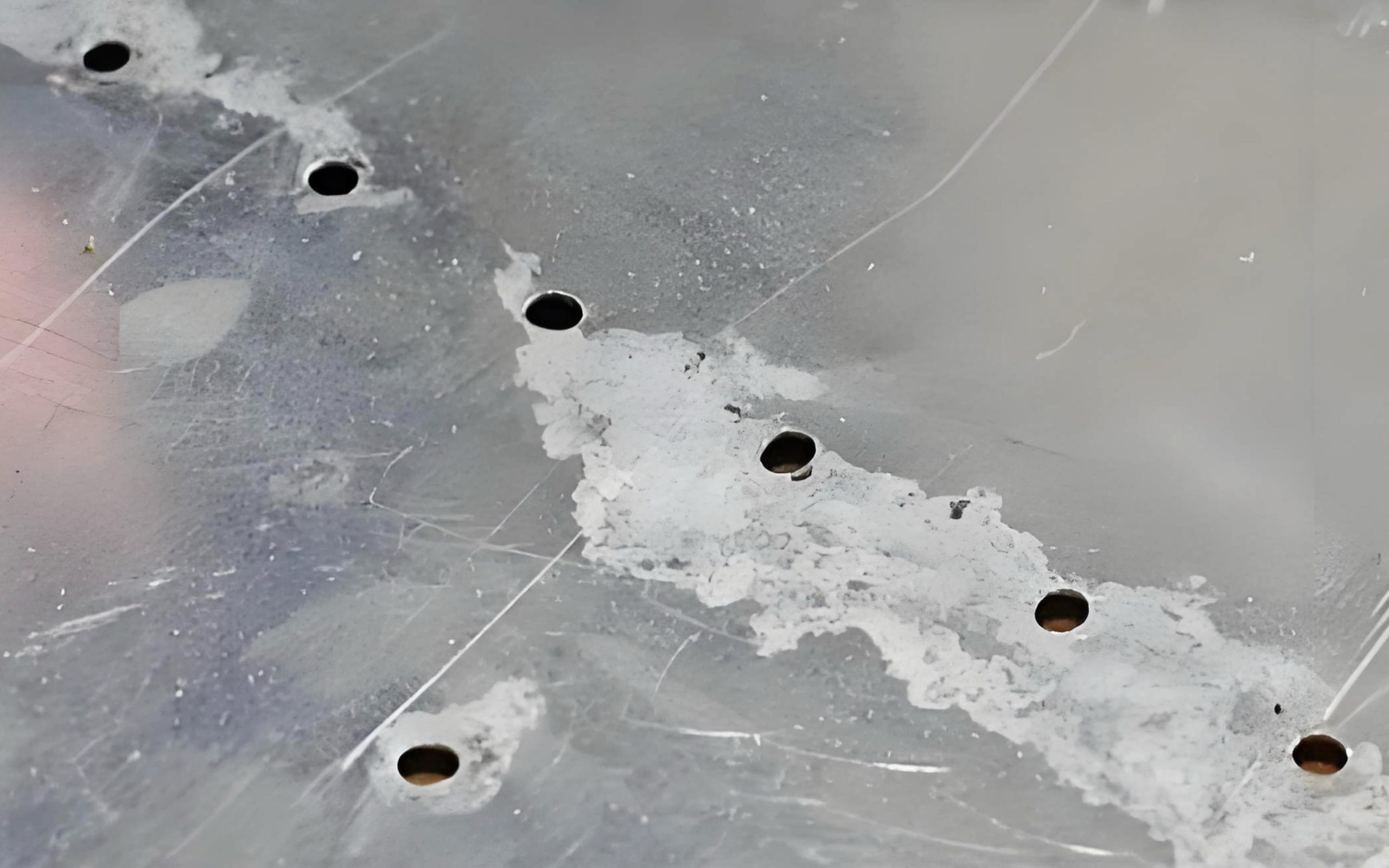
Las piezas de diferentes materiales (como aleaciones de aluminio, aceros de alta resistencia, aceros inoxidables y aleaciones de titanio) tienen diferentes requisitos en cuanto a dureza, densidad y módulo elástico de los medios de granallado. Los clientes deben aclarar las siguientes cuestiones:
- Si la superficie de los materiales flexibles (como el aluminio y el magnesio) se dañará debido a que los medios son demasiado duros o densos.
- Si los materiales de alta resistencia (como las aleaciones de titanio) requieren medios de mayor dureza para lograr una tensión de compresión superficial suficiente.
Eficacia y economía de uso
La elección de los medios de granallado por parte de los clientes suele estar limitada por la eficiencia y el coste, que se manifiestan específicamente en:
- Vida mediática: ¿Tienen los medios una larga vida útil, lo que reduce la frecuencia de sustitución y el tiempo de inactividad?
- Control de costes: ¿Son controlables el coste inicial de compra y el coste de uso a largo plazo, especialmente para las empresas de producción a gran escala?
Requisitos específicos de aplicación
En el caso de los clientes industriales que realizan shot peening, sus necesidades pueden ser muy específicas:
- Prolongación de la vida útil por fatiga: Los clientes desean mejorar significativamente la vida a fatiga de las piezas, pero les preocupa que el proceso de granallado no sea suficiente para lograr el efecto esperado.
- Requisitos de rugosidad de la superficie: Algunas industrias (como la aeroespacial y la de dispositivos médicos) tienen requisitos estrictos sobre la suavidad de la superficie tras el granallado, y cualquier exceso de rugosidad puede aumentar los costes de procesamiento posteriores.
- Mayor resistencia a la corrosión: Especialmente en las industrias aeroespacial y energética, las piezas deben resistir la corrosión en entornos difíciles. Si la capa de tensión de compresión superficial del shot peening puede prevenir eficazmente la propagación de grietas.
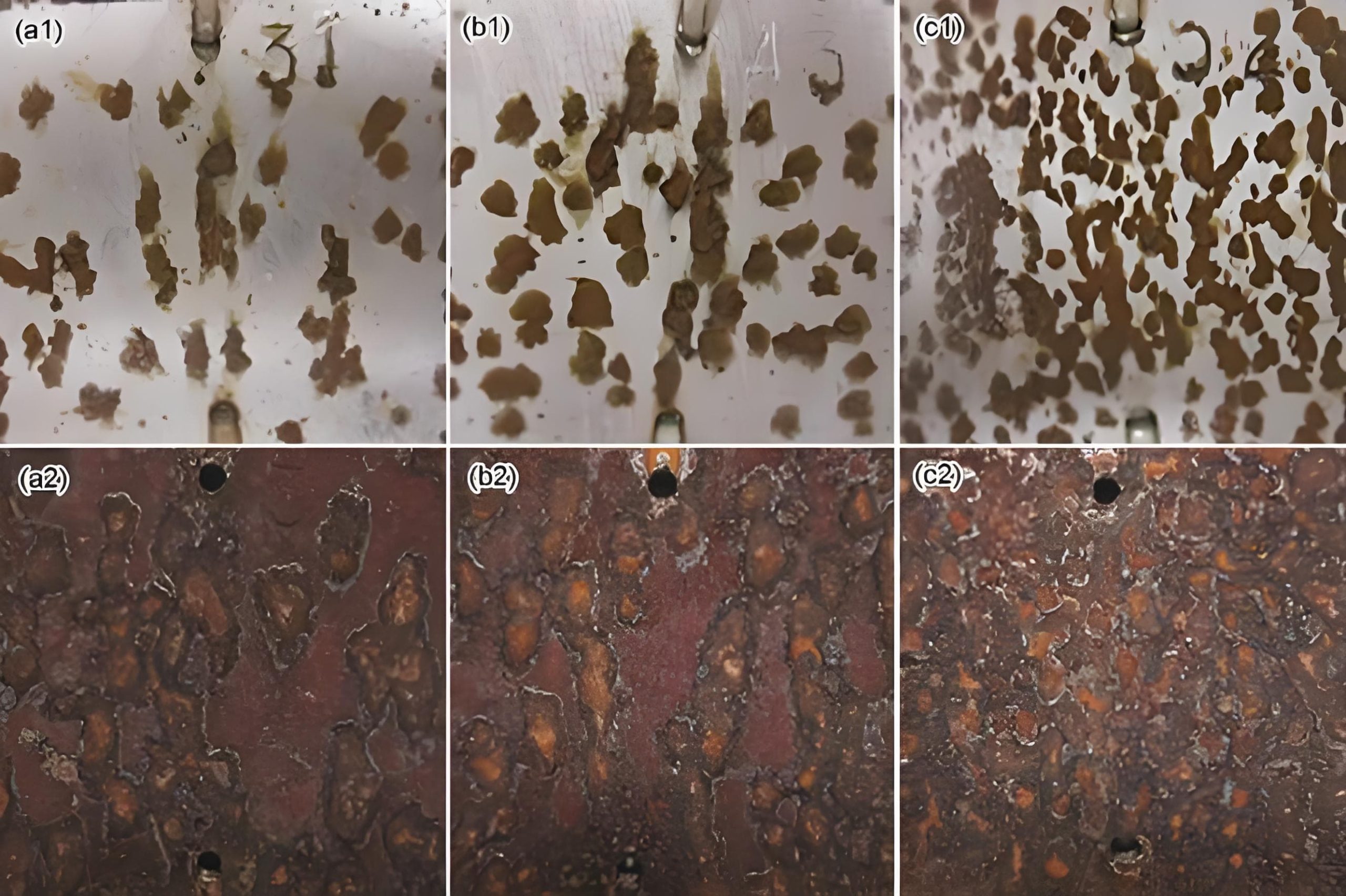
Seguridad medioambiental y sanitaria
Dado que los requisitos de protección del medio ambiente son cada vez más estrictos, los clientes también prestarán atención a si los medios de granallado presentan los siguientes problemas:
- Contaminación por polvo: Los medios de baja calidad o quebradizos pueden generar mucho polvo, lo que afecta al entorno operativo y a la salud del personal.
- Sostenibilidad: ¿Cuál es la reciclabilidad de los soportes y si el coste de eliminación de los residuos es razonable?
Umbrales técnicos y operativos
El shot peening requiere un soporte técnico altamente especializado, pero los clientes pueden enfrentarse a los siguientes problemas:
- Compatibilidad de equipos: ¿Es el equipo de granallado adecuado para los nuevos medios y requiere ajustes o actualizaciones adicionales?
- Complejidad operativa: ¿Requiere el uso del medio condiciones de proceso especiales, una mayor complejidad técnica o costes de formación?
- Adaptabilidad a nuevos materiales: ¿Pueden aplicarse con éxito los nuevos materiales componentes (como los materiales compuestos) a la tecnología de granallado existente?
Granallado cerámico VS perlas de vidrio: ¿Quién tiene más ventajas?
Uniformidad y estabilidad del refuerzo superficial
Ambos medios tienen un aspecto redondo y liso y pueden trabajar uniformemente.
Sin embargo, la estructura cristalina del granallado cerámico tiene una excelente resistencia a la compresión y tenacidad y no es fácil de romper, especialmente adecuada para entornos de trabajo de alta intensidad e impactos repetidos.
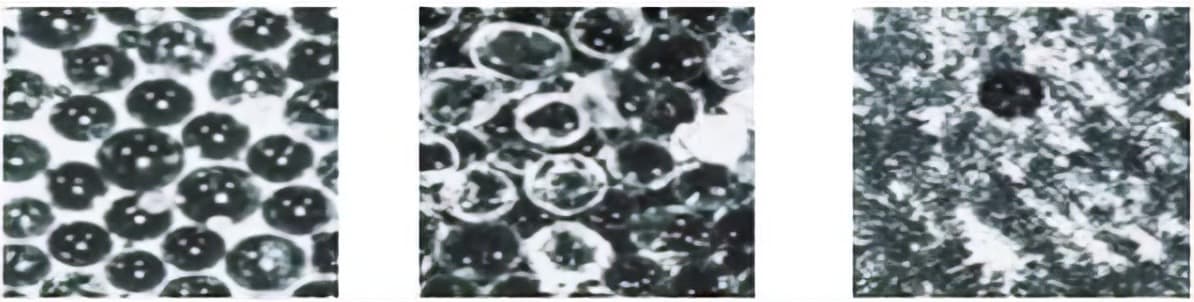
Por el contrario, las microesferas de vidrio se rompen con facilidad en condiciones de uso intenso o frecuente, rayando la superficie de la pieza, y también pueden provocar un grosor desigual de la capa de refuerzo o una distribución inestable de la tensión.
Cuando una empresa de fabricación aeroespacial procesaba álabes de turbina de aleación de titanio, utilizaba originalmente perlas de vidrio para el shot peening. Se descubrió que el grosor de la capa de refuerzo era irregular en el extremo de la pala, lo que provocaba una disminución de la vida a fatiga de la pala. Tras cambiar al shot peening cerámico, la estabilidad del espesor de la capa de refuerzo aumentó en 15%, y la vida a fatiga de la pala aumentó en 20%.
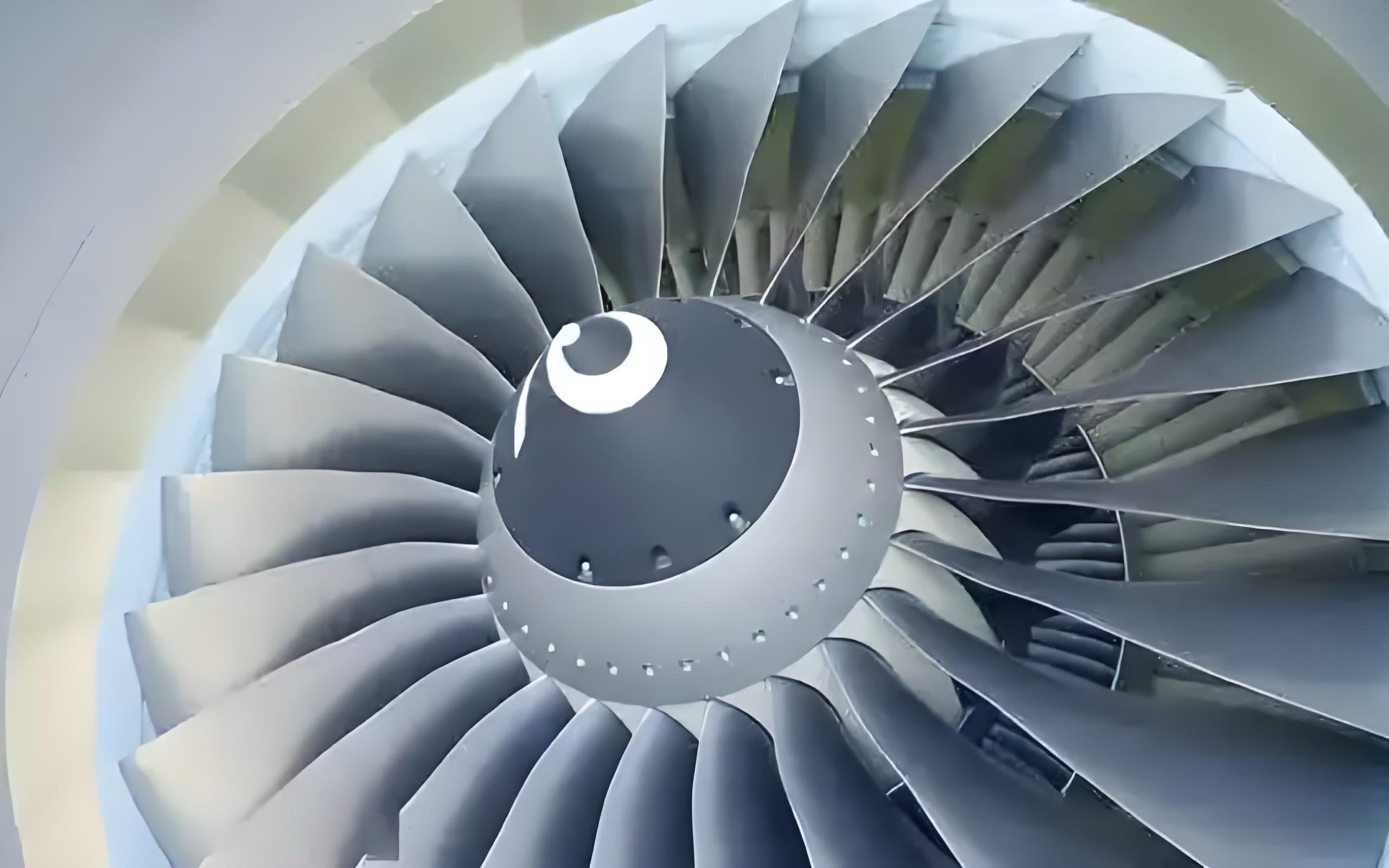
Compatibilidad de materiales
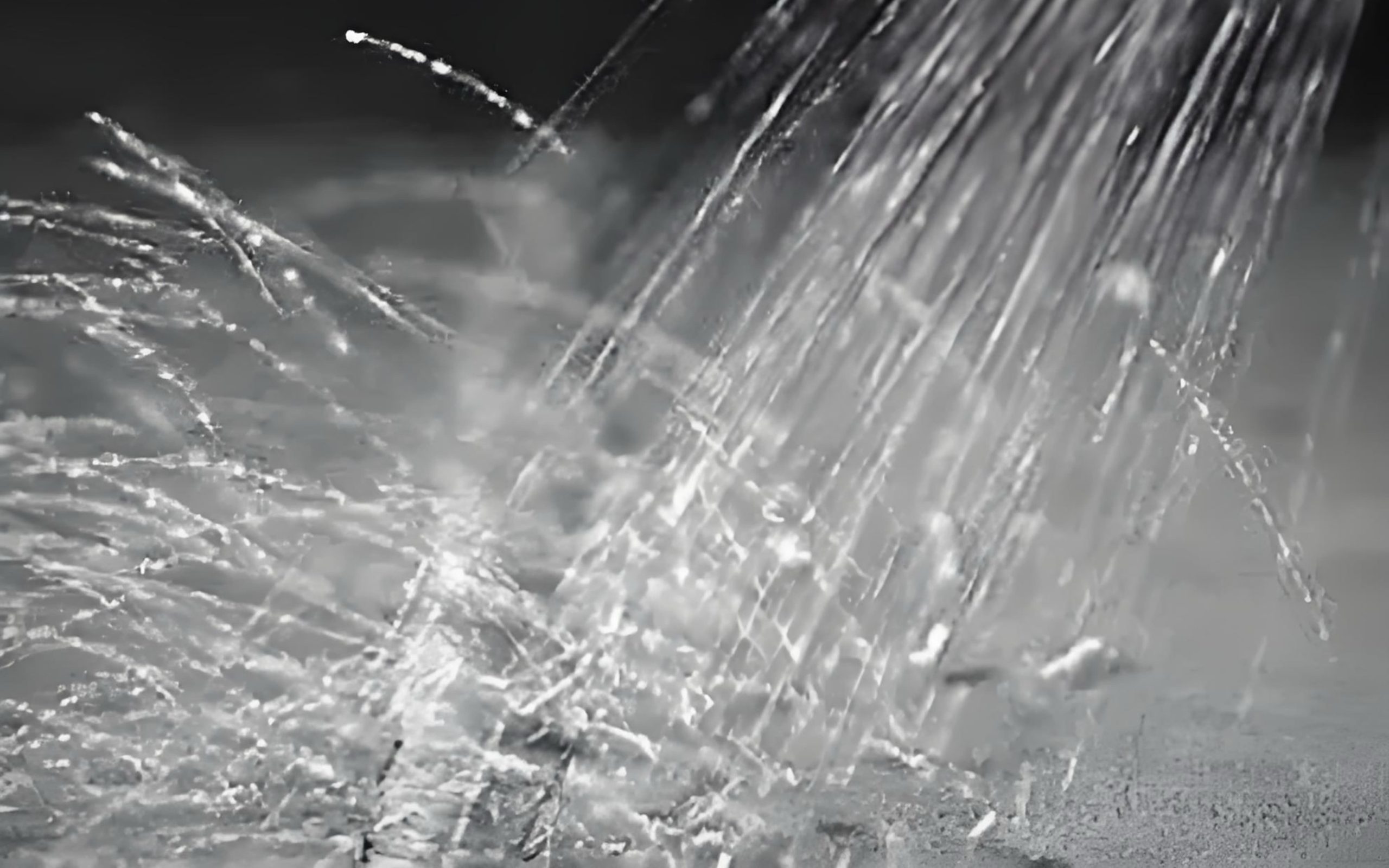
Las perlas de vidrio son fáciles de romper cuando se refuerzan materiales de alta resistencia, y pueden no generar suficiente tensión de compresión superficial en materiales flexibles. Sin embargo, el shot peening cerámico es adecuado para procesos de shot peening desde materiales flexibles (como aleaciones de aluminio) hasta materiales de alta resistencia (como acero inoxidable y aleaciones de titanio) y tiene un gran espacio de programación.
Aunque el shot peening cerámico tiene una gran dureza, también puede tratar bien materiales blandos. Esto depende principalmente del tamaño y la forma de las partículas y de la presión de inyección aplicada.
Siempre que se seleccione el tamaño de partícula adecuado y se utilice la inyección a baja presión, se puede reducir la intensidad del punto de concentración de la fuerza de impacto. Además, el diseño esférico del granallado cerámico también ayuda a dispersar la fuerza de impacto, que es similar a la de las perlas de vidrio y puede lograr un efecto de tratamiento superficial más suave.
En el shot peening de piezas de aluminio del sistema de suspensión, un fabricante de automóviles no consiguió alcanzar la profundidad de la capa de tensión de compresión debido a la insuficiente dureza de las microesferas de vidrio. Tras cambiar al shot peening cerámico, la profundidad de la capa de tensión de compresión superficial aumentó en 30%, y no aparecieron arañazos ni picaduras en la superficie de las piezas de aluminio.
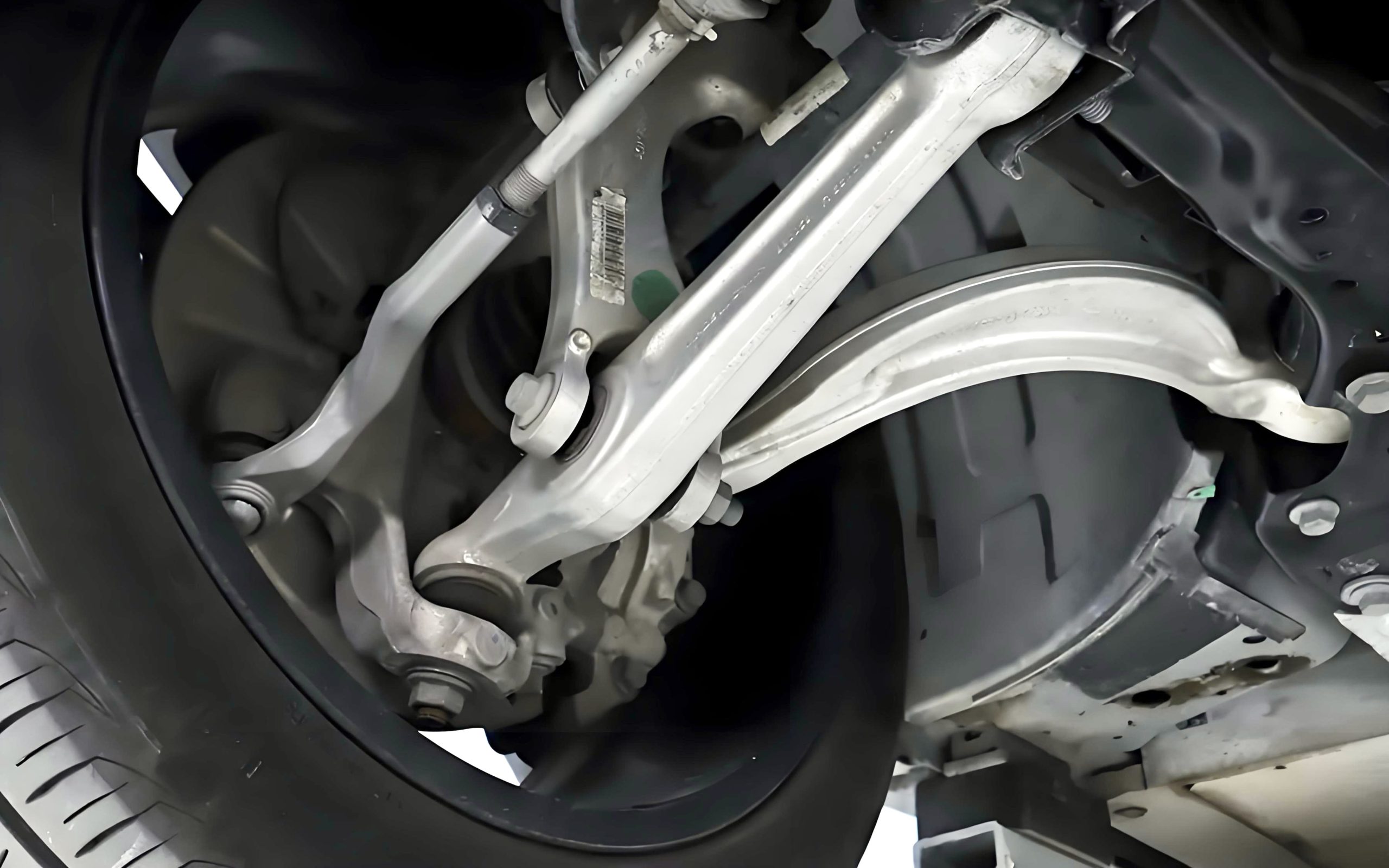
Eficacia y economía de uso
En primer lugar, el granallado cerámico tiene mayor dureza y puede aplicar una mayor tensión de compresión superficial durante el granallado, mejorando eficazmente la resistencia a la fatiga y la durabilidad de la pieza. En segundo lugar, la densidad y la durabilidad de los medios cerámicos son muy superiores a las de las perlas de vidrio.
Aunque el coste de adquisición inicial del shot peening cerámico es superior al de las perlas de vidrio, tras múltiples ciclos de uso, el shot peening cerámico puede seguir manteniendo una forma esférica y puede utilizarse repetidamente, mientras que las perlas de vidrio tienen un alto índice de rotura y deben sustituirse con frecuencia, lo que aumenta el tiempo de inactividad y los costes de adquisición de medios.
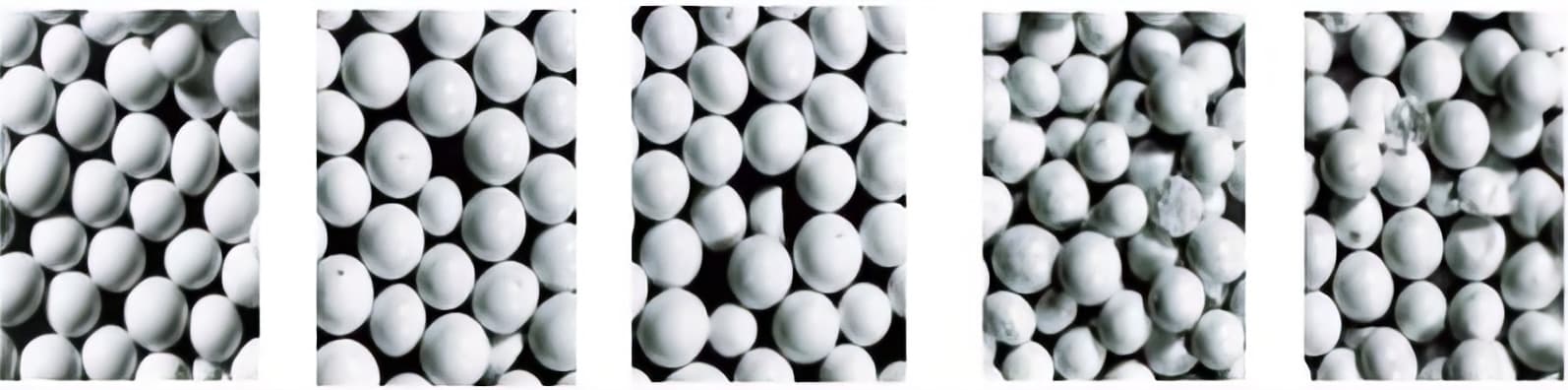
Los medios cerámicos se desgastarán pero no se romperán en polvo, por lo que casi no hay polvo, y las partes no rotas siguen manteniendo su tamaño, forma, dureza y superficie lisa originales.
Un fabricante de piezas de automoción cambió al shot peening cerámico en la producción de cigüeñales. Aunque el coste de aprovisionamiento aumentó en unos 30%, el número de veces que se utilizó un kilogramo de granallado cerámico fue de 3 a 4 veces superior al de perlas de vidrio, y el coste de eliminación de residuos disminuyó en 40%. En conjunto, el coste de producción se redujo en 15% y la eficiencia del proceso aumentó en 10%.
Requisitos específicos de aplicación
Se sabe que la fragilidad de las perlas de vidrio provocará falta de uniformidad en el shot peening, lo que formará puntos débiles en la propagación de grietas de corrosión, especialmente en entornos duros como la ingeniería marina y la industria de la energía nuclear.
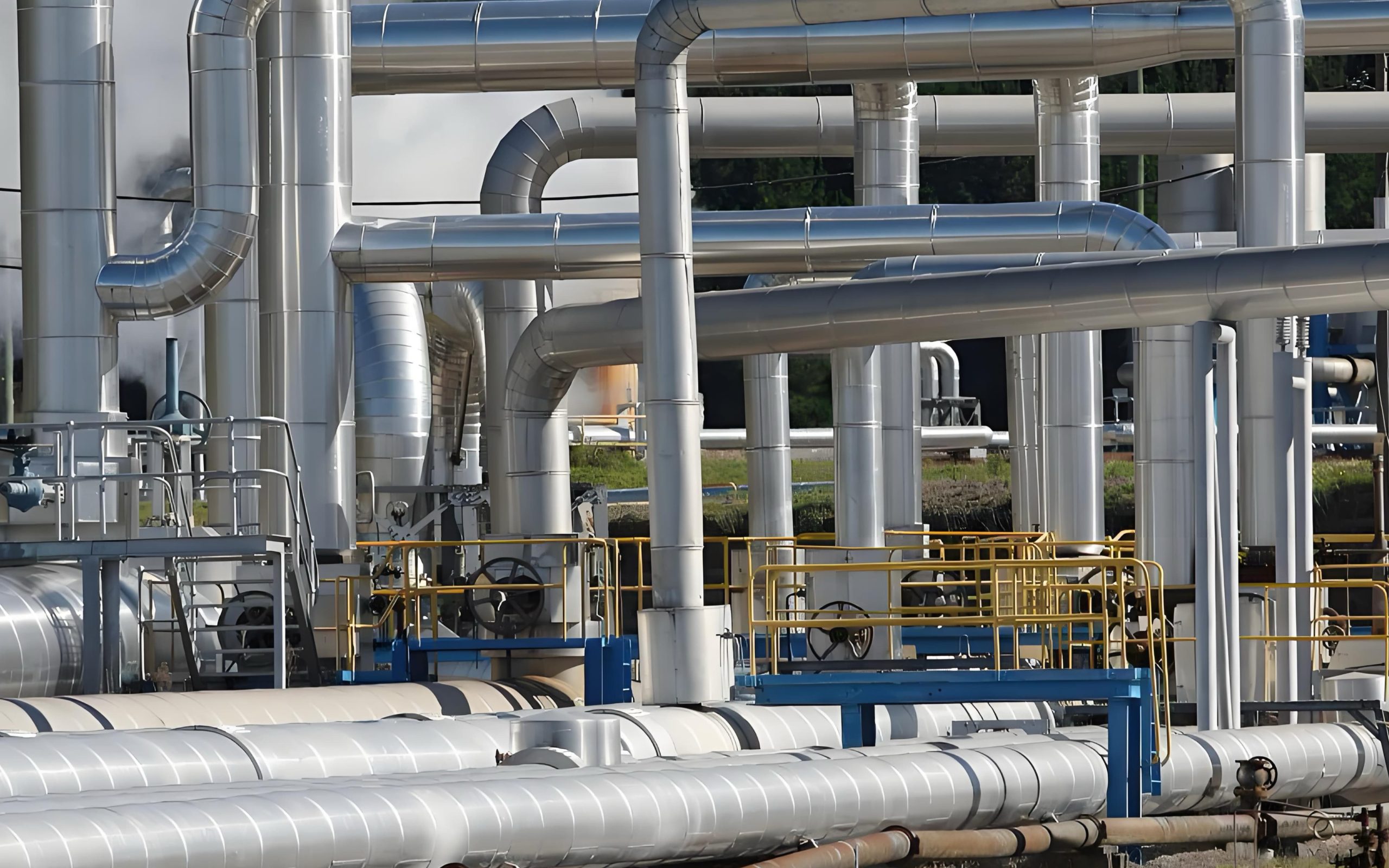
Los fragmentos rotos también pueden incrustarse en la superficie y convertirse en una fuente potencial de corrosión. El material cerámico tiene una forma regular y es tenaz y resistente. Tras el granallado, puede generar una capa de tensión de compresión uniforme, impidiendo eficazmente la expansión de las grietas de corrosión, y es más adecuado para zonas con elevados requisitos de rendimiento anticorrosivo.
Un proyecto de mantenimiento de una central nuclear requiere el shot peening de tuberías de vapor de alta presión para prolongar su vida útil. Tras utilizar perlas de vidrio, el efecto de refuerzo no cumplía la norma, y la vida a fatiga de las tuberías no aumentaba significativamente. Tras sustituir el shot peening cerámico, la vida a fatiga de las tuberías reforzadas aumentó en 25%, y la tasa de propagación de grietas se redujo significativamente.
Eficacia y economía de uso
El granallado cerámico no genera fácilmente polvo durante su uso, y el entorno operativo es más limpio, lo que contribuye a reducir los riesgos para la salud de los trabajadores. Las perlas de vidrio son fáciles de romper, lo que puede producir una gran cantidad de diminuto polvo de vidrio, afectando a la calidad del aire y aumentando los costes de tratamiento de protección medioambiental.
Además, la reciclabilidad de los medios cerámicos es mucho mayor que la de las perlas de vidrio, alcanzando normalmente más de 95%, y la cantidad de residuos generados también es menor, lo que es más fácilmente aceptado por las normativas de protección medioambiental.
Tras sustituir las perlas de vidrio, un proveedor de equipos de proyección redujo los residuos sólidos industriales en unas 20 toneladas al año, con lo que disminuyeron considerablemente los costes de eliminación. Al mismo tiempo, la alta disponibilidad del granallado cerámico le otorga puntos extra en la certificación de producción ecológica, lo que supone un apoyo para que las empresas se abran a los mercados europeo y estadounidense.
Umbrales técnicos y operativos
Desde el punto de vista de la compatibilidad de los equipos, el granallado cerámico es muy compatible con los equipos de granallado modernos. Su forma regular y sus propiedades físicas estables reducen la necesidad de ajustar el equipo, mientras que las microesferas de vidrio son principalmente fáciles de romper, lo que aumenta el riesgo de atascar la boquilla y desgastar el equipo.
El shot peening cerámico también es más tolerante a los parámetros del proceso, como una presión de inyección y una distribución del tamaño de las partículas más uniformes, lo que reduce la complejidad de la tecnología operativa. Al mismo tiempo, puede trabajar en una gama más amplia de condiciones de temperatura y humedad, lo que reduce la necesidad de control ambiental.
Gracias a su elevada dureza y forma regular, puede procesar eficazmente materiales emergentes como aleaciones de titanio y materiales compuestos, satisfaciendo las necesidades de las industrias aeroespacial y médica en cuanto a refuerzo especial de superficies.
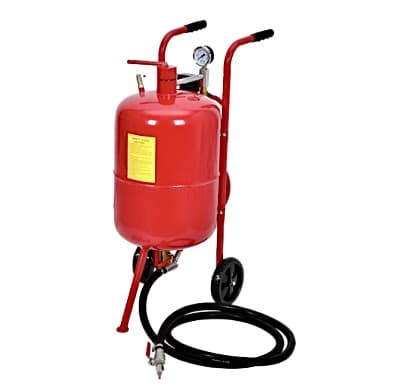
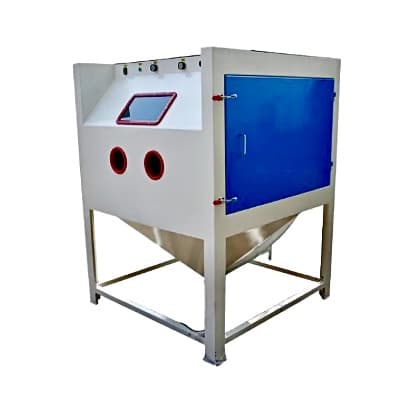
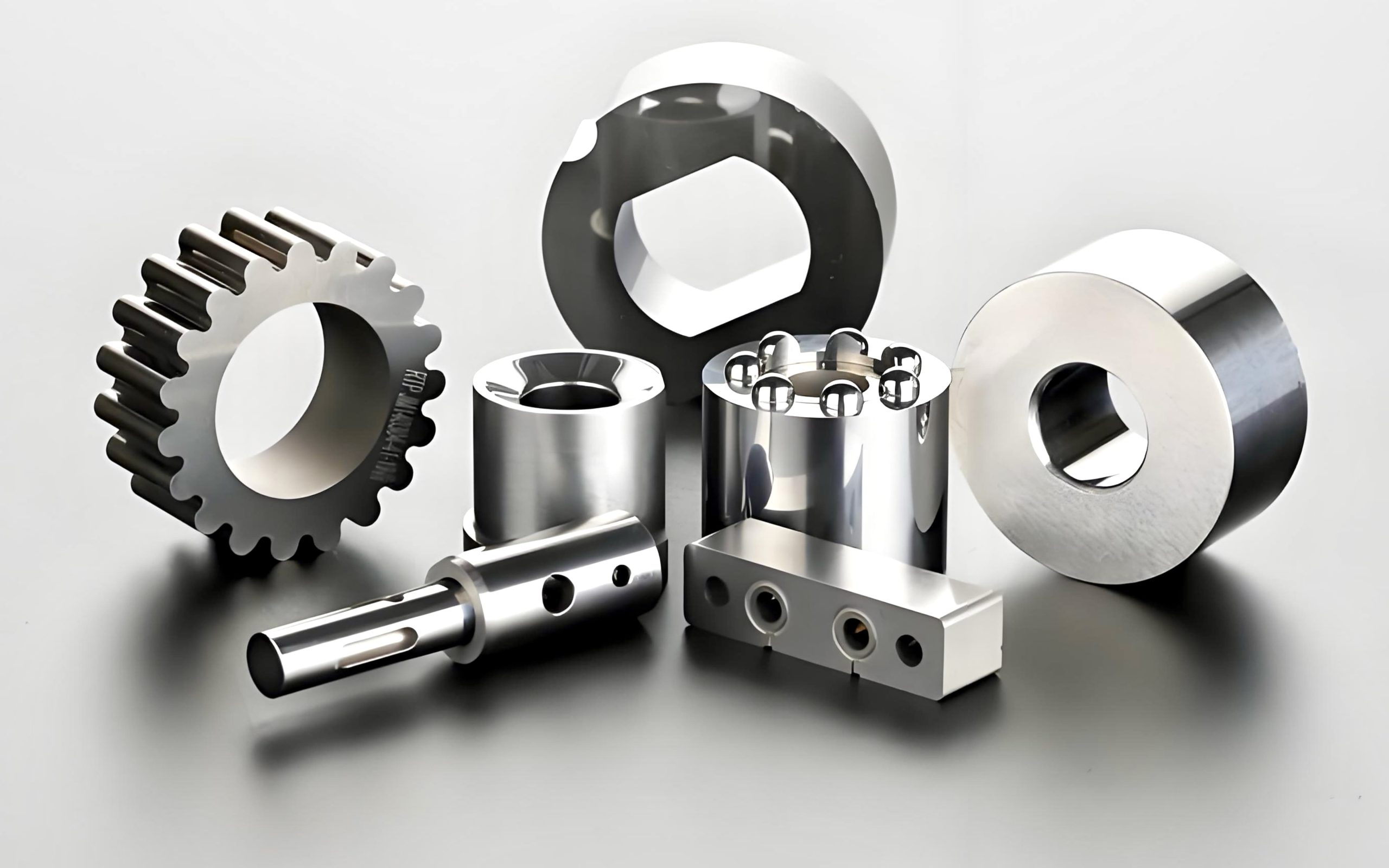
Una empresa de fabricación de moldes de precisión descubrió que la sustitución frecuente de las perlas de vidrio en el proceso de granallado provocaba un aumento del tiempo de inactividad del equipo. Tras sustituir el shot peening cerámico, el tiempo de funcionamiento del equipo se amplió en 25%, y la estabilidad del proceso mejoró notablemente.
En resumen, comparamos el rendimiento de ambos en términos de dureza y profundidad de refuerzo, vida útil y eficacia, y comportamiento medioambiental. Se puede comprobar que los medios cerámicos presentan ventajas evidentes en estas dimensiones clave. Precisamente con estas ventajas, el shot peening cerámico está sustituyendo gradualmente a las microesferas de vidrio como elección de medio de shot peening de alto rendimiento, aportando mayores beneficios económicos y soluciones de producción más sostenibles a diversas industrias.
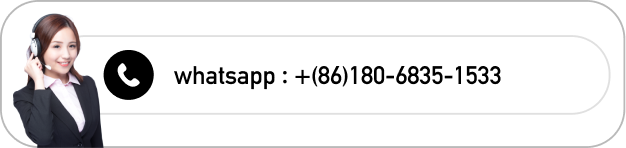