Granallado con óxido de aluminio Problemas de funcionamiento del proceso y soluciones
27 de agosto de 2024
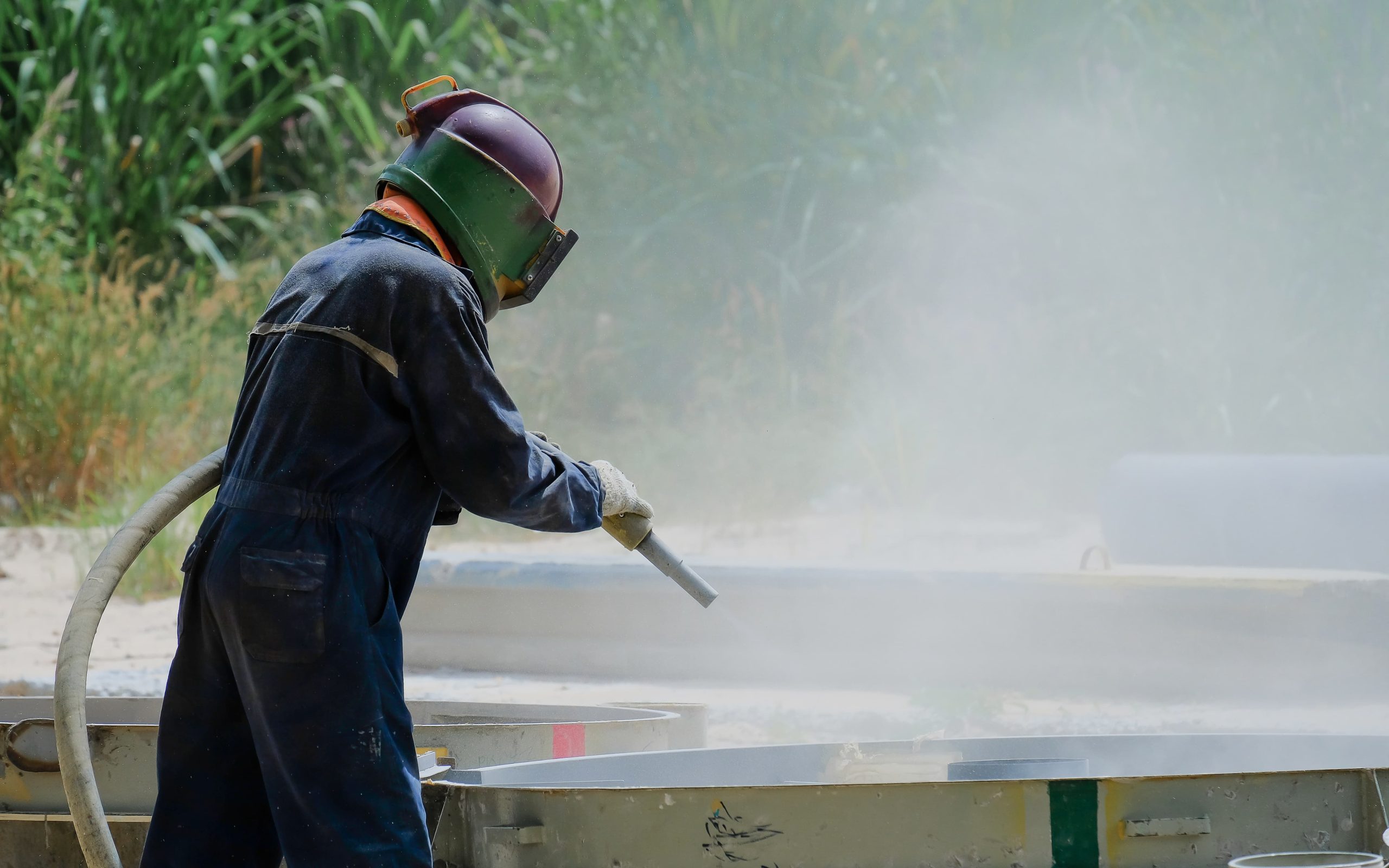
El granallado con óxido de aluminio, como tecnología de tratamiento de superficies, se ha utilizado ampliamente en diversas industrias. Sin embargo, a pesar de las importantes ventajas de la tecnología de chorreado con óxido de aluminio, pueden surgir diversos problemas durante el funcionamiento real debido a la complejidad de los equipos, los materiales y las condiciones de funcionamiento. Si no se gestionan adecuadamente, estos problemas pueden afectar directamente al efecto final del proceso e incluso provocar una disminución de la calidad del producto. En este artículo se analizan en detalle 18 de estos problemas, se ofrecen las correspondientes soluciones y medidas de mejora, y se concluye con algunos consejos para optimizar el efecto del chorreado de alúmina, con el fin de ayudarle a utilizar mejor esta tecnología.
Problema 1: Desgaste del equipo
- Descripción: Debido a la elevada dureza de la alúmina, el arenado puede provocar un desgaste acelerado del equipo de arenado (especialmente boquillas y tuberías).
- Solución: Elija boquillas y tubos fabricados con materiales muy resistentes al desgaste, como el carburo de tungsteno o la cerámica, para reducir significativamente el desgaste del equipo.
- Medidas de mejora: Controlar periódicamente el desgaste del equipo; mantener y sustituir las piezas desgastadas; ajustar oportunamente la presión de chorreado y el caudal de los medios; evitar el uso excesivo del mismo equipo.
Tema 2: Problemas de manipulación del polvo
- Descripción: Una gran cantidad de polvo generado durante el chorreado puede afectar a la salud de los operarios.
- Solución: Instale equipos eficaces de eliminación de polvo para reducir las emisiones de polvo, como colectores de polvo por impulsos o precipitadores electrostáticos. Los operarios también deben estar equipados con equipos de protección individual adecuados, como respiradores y ropa protectora.
- Medidas de mejora: Optimice el sistema de ventilación en el entorno de trabajo, inspeccione y mantenga regularmente el equipo de eliminación de polvo para garantizar su funcionamiento normal. La tecnología de chorreado húmedo también puede reducir eficazmente la generación de polvo.
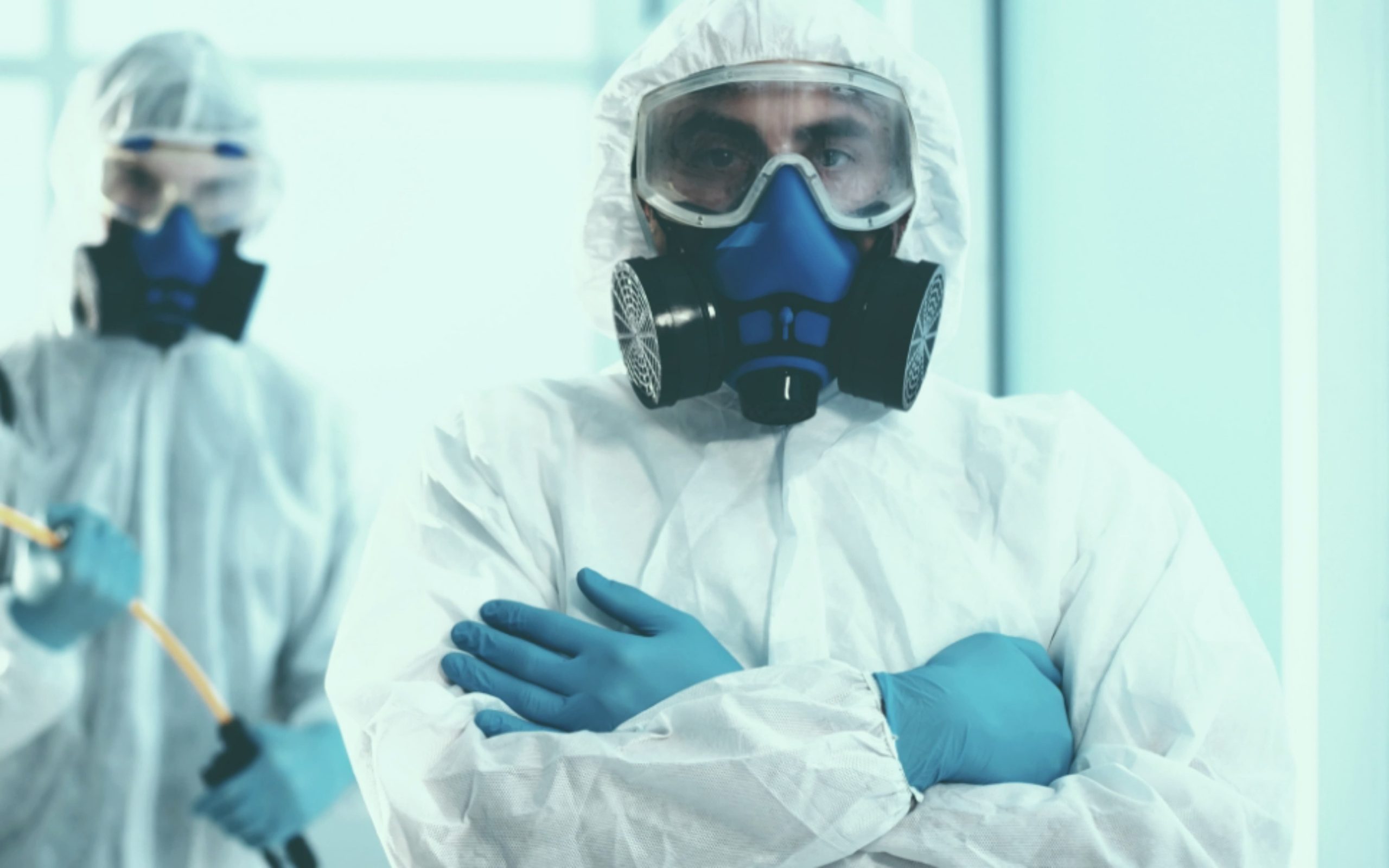
Demostración de indumentaria de protección
Problema 3: Presión de chorreado desigual
- Descripción: Una presión desigual durante el chorreado puede provocar un tratamiento desigual de la superficie, lo que afectaría a la calidad final de la misma.
- Solución: Utilizar equipos de control de presión de alta calidad para garantizar la estabilidad de la presión. Calibre y mantenga periódicamente los equipos de control de la presión para garantizar su precisión.
- Medidas de mejora: Experimente para determinar la presión de chorreado óptima, ajuste los valores de presión según los distintos materiales y requisitos del proceso, y consiga el mejor efecto.
Tema 4: Recuperación y reutilización de soportes
- Descripción: La granalla de óxido de aluminio usada puede contaminarse o mezclarse con impurezas, lo que reduce el efecto del chorreado.
- Solución: Instale un sistema específico de recuperación de medios con dispositivos de separación y limpieza para eliminar las impurezas y garantizar la pureza de los medios. Los medios que estén muy desgastados o contaminados deben sustituirse rápidamente.
- Medidas de mejora: Compruebe periódicamente el estado de los medios, utilice microscopios u otros métodos de detección para evaluar su calidad y asegúrese de que siguen siendo eficaces durante su reutilización.
Problema 5: La rugosidad de la superficie no cumple las normas tras el arenado
- Descripción: La rugosidad de la superficie de la pieza tras el chorreado puede no cumplir los requisitos esperados, siendo posiblemente demasiado rugosa o demasiado lisa, lo que afecta al procesamiento posterior.
- Solución: Ajustar la granulometría y la distribución del abrasivo en función de la rugosidad superficial deseada. Acorte o prolongue adecuadamente el tiempo de arenado para controlar la rugosidad de la superficie.
- Medidas de mejora: Ajuste el ángulo de la boquilla para que el medio de chorreado impacte en la superficie con el ángulo óptimo, alcanzando gradualmente la rugosidad deseada. Para piezas de alta precisión, determine los mejores parámetros de chorreado mediante pruebas en pequeños lotes.
Problema 6: Dificultad para controlar el caudal de medios
- Descripción: En diferentes condiciones de funcionamiento, puede resultar difícil controlar con precisión el caudal de la granalla de óxido de aluminio, lo que afecta al efecto del chorreado.
- Solución: Utilice válvulas de control de flujo y sensores de alta precisión para supervisar el flujo de medios en tiempo real y garantizar un proceso de arenado estable.
- Medidas de mejora: Implantar un sistema de control automatizado para lograr un control preciso del caudal de los medios, e inspeccionar y calibrar periódicamente el equipo de control del caudal para garantizar su correcto funcionamiento.
Problema 7: Sobrecalentamiento del material que provoca deformaciones o daños
- Descripción: En el arenado de alta intensidad, el calor excesivo generado por la fricción puede provocar deformaciones o daños en el material tratado.
- Solución: Controle el tiempo y la presión de chorreado para evitar operaciones prolongadas de alta intensidad. El chorreado intermitente puede utilizarse para dar tiempo al material a enfriarse.
- Medidas de mejora: Introducir un sistema de refrigeración o utilizar tecnología de arenado en frío para reducir el calor generado durante el procesamiento y minimizar el riesgo de deformación térmica del material.
Problema 8: Consumo excesivo de medios de alúmina
- Descripción: Las operaciones frecuentes de arenado pueden provocar un consumo excesivo de medios de alúmina, lo que aumenta los costes de producción.
- Solución: Optimice los parámetros del proceso, como el ajuste de la presión de chorreado, el caudal y el tiempo para reducir el desperdicio de abrasivo. Además, el reciclaje y la reutilización de los medios no contaminados también pueden reducir el consumo total.
- Medidas de mejora: Supervise regularmente el uso de los medios, utilice sistemas de arenado inteligentes para ajustar automáticamente la cantidad en función de las necesidades reales y mejorar la eficacia.
Tema 9: Reacciones químicas entre medios y materiales
- Descripción: En determinadas condiciones, los medios de alúmina pueden reaccionar químicamente con el material tratado (aunque esto es poco frecuente), lo que provoca una disminución de la calidad de la superficie o la formación de películas superficiales indeseables.
- Solución: Elija los medios de chorreado y los entornos de trabajo adecuados para evitar reacciones adversas con los materiales. Si es necesario, considere el uso de medios con mayor inercia química.
- Medidas de mejora: Realice pruebas de estabilidad química de los materiales antes del chorreado para asegurarse de que no se producen reacciones adversas entre los medios y los materiales. Además, considere el uso de entornos de gas inerte o el control de la humedad ambiental para reducir la aparición de reacciones químicas.
Tema 10: Problemas de limpieza tras el tratamiento de superficies
- Descripción: El polvo de alúmina residual o los restos pueden permanecer en la superficie del material después del arenado, afectando a los tratamientos superficiales posteriores, como el revestimiento o el chapado.
- Solución: Implemente procesos de limpieza específicos, como la limpieza por ultrasonidos o la limpieza por aire a alta presión, para eliminar a fondo los residuos de la superficie y garantizar la fluidez de los procesos posteriores.
- Medidas de mejora: Mejorar los equipos y procesos de limpieza para acortar el tiempo de limpieza, aumentar la eficacia y reducir el impacto ambiental durante la limpieza.
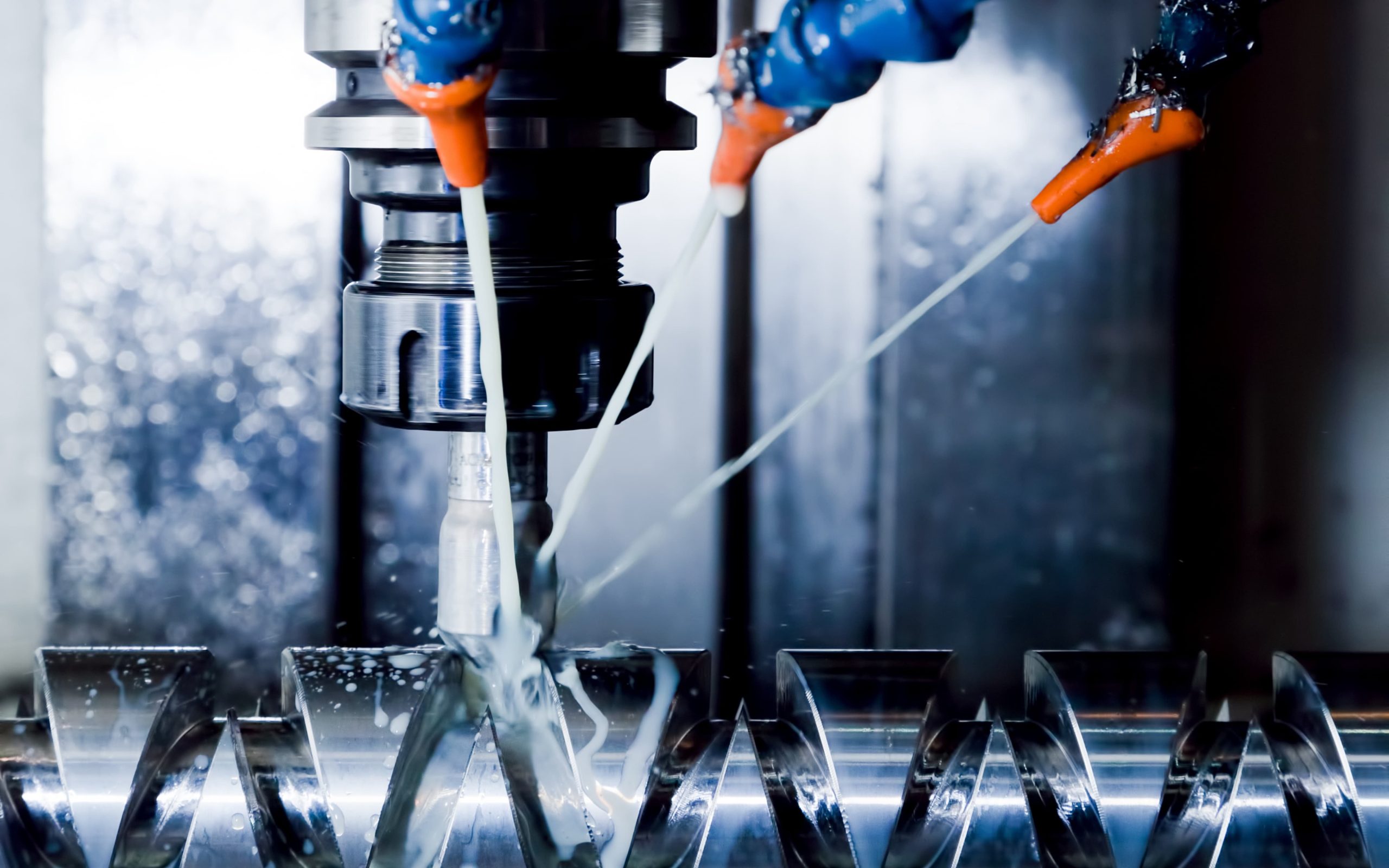
máquina de limpieza
Tema 11: Acumulación de electricidad estática en los medios de comunicación
- Descripción: En las operaciones de chorreado en seco, la electricidad estática puede acumularse en el medio de chorreado debido a la fricción, afectando al efecto del chorreado.
- Solución: Instale equipos de eliminación de estática, como sopladores de iones o dispositivos de puesta a tierra, para reducir el riesgo de acumulación de estática.
- Medidas de mejora: Aplicar procesos de arenado en húmedo para reducir eficazmente la generación de electricidad estática, y utilizar materiales conductores, como tubos o boquillas conductores, en el sistema de arenado para disipar la electricidad estática y reducir la acumulación de medios.
Problema 12: Efectos de las vibraciones durante el chorreado con arena
- Descripción: Durante el tratamiento de piezas de paredes finas o de precisión, las vibraciones generadas por el equipo de arenado pueden afectar a la fijación y a la uniformidad del tratamiento superficial.
- Solución: Diseñe o instale dispositivos amortiguadores en los equipos de chorreado y las mesas de trabajo para reducir el impacto de las vibraciones en las operaciones. Asegúrese de que la pieza de trabajo está bien sujeta durante el chorreado para evitar que se desplace o se afloje debido a las vibraciones.
- Medidas de mejora: Ajuste los parámetros de funcionamiento del equipo, como la presión y el caudal de chorreado, para reducir las fuentes de vibración y estabilizar el efecto del chorreado.
Problema 13: Problemas de almacenamiento de medios
- Descripción: Las bolas de alúmina pueden verse afectadas por el aceite, la humedad u otros contaminantes durante el almacenamiento o el funcionamiento, reduciendo el efecto del chorro de arena.
- Solución: Almacene los medios de alúmina en un entorno seco y limpio para evitar la contaminación o la absorción de humedad. Limpie el soporte antes de utilizarlo para eliminar los contaminantes de la superficie y garantizar su pureza.
- Medidas de mejora: Compruebe periódicamente si el abrasivo está contaminado o degradado y sustitúyalo por otro nuevo de alúmina según sea necesario para garantizar la calidad del chorreado.
Problema 14: Oxidación de las piezas tras el chorreado con arena
- Descripción: Si no se procesa con prontitud después del arenado, la superficie de la pieza tratada puede oxidarse rápidamente, afectando a la calidad final de la superficie.
- Solución: Realice inmediatamente los tratamientos posteriores al chorreado, como el revestimiento, la pasivación o el recubrimiento protector, para evitar la oxidación de la superficie.
- Medidas de mejora: Utilizar una cobertura de gas inerte en la superficie de la pieza después del arenado para evitar la oxidación cuando se requiera una alta calidad superficial. Supervise periódicamente la oxidación con instrumentos de inspección de superficies para garantizar un procesamiento posterior oportuno.
Problema 15: Contaminación acústica provocada por las operaciones de chorro de arena
- Descripción: Los altos niveles de ruido generados durante el arenado pueden dañar el oído de los operarios y provocar contaminación acústica en el entorno de trabajo.
- Solución: Instale equipos de aislamiento acústico, como paneles insonorizados o ventanas, fuera de la cámara de chorro de arena; o proporcione a los operarios tapones para los oídos u orejeras con cancelación de ruido.
- Medidas de mejora: Elija equipos de chorreado con un diseño poco ruidoso o modifique los equipos existentes para reducir el ruido de funcionamiento.
Problema 16: Dificultad para garantizar la coherencia de los efectos del chorro de arena
- Descripción: En la producción en serie, especialmente con múltiples lotes, pueden surgir problemas de consistencia.
- Solución: Desarrollar normas y procedimientos operativos estrictos para garantizar que cada operación siga parámetros de proceso uniformes. Implemente la gestión de lotes para etiquetar y registrar cada lote, realizando un seguimiento de los parámetros y efectos del chorreado de arena para garantizar la coherencia.
- Medidas de mejora: Utilice sistemas automatizados de inspección de superficies para supervisar y ajustar los efectos del arenado en tiempo real a fin de garantizar la uniformidad de cada pieza.
Problema 17: Complejidad del funcionamiento de los equipos de chorreado de arena
- Descripción: Los equipos de chorro de arena de alta precisión pueden tener procedimientos operativos complejos, que requieren una formación especializada para su uso correcto, lo que afecta a la eficiencia de la producción.
- Solución: Impartir formación sistemática a los operarios para garantizar que dominan las técnicas de funcionamiento de los equipos.
- Medidas de mejora: Introducir sistemas de control automatizados para reducir la intervención humana, simplificar el proceso de funcionamiento y mejorar la eficiencia.
Tema 18: Control de la temperatura del entorno de arenado
- Descripción: Las temperaturas excesivamente altas o bajas en el entorno de chorreado pueden afectar a los efectos del chorreado o al rendimiento del material.
- Solución: Instalar sistemas de control de la temperatura en el taller de chorro de arena para mantener temperaturas de funcionamiento adecuadas y supervisar periódicamente las temperaturas ambientales para garantizar que se mantienen dentro de un rango razonable.
- Medidas de mejora: Ajuste los parámetros de chorreado según las diferentes estaciones para garantizar efectos de chorreado estables. Utilice medios de chorreado resistentes a la temperatura para reducir el impacto de las temperaturas ambientales en el rendimiento.
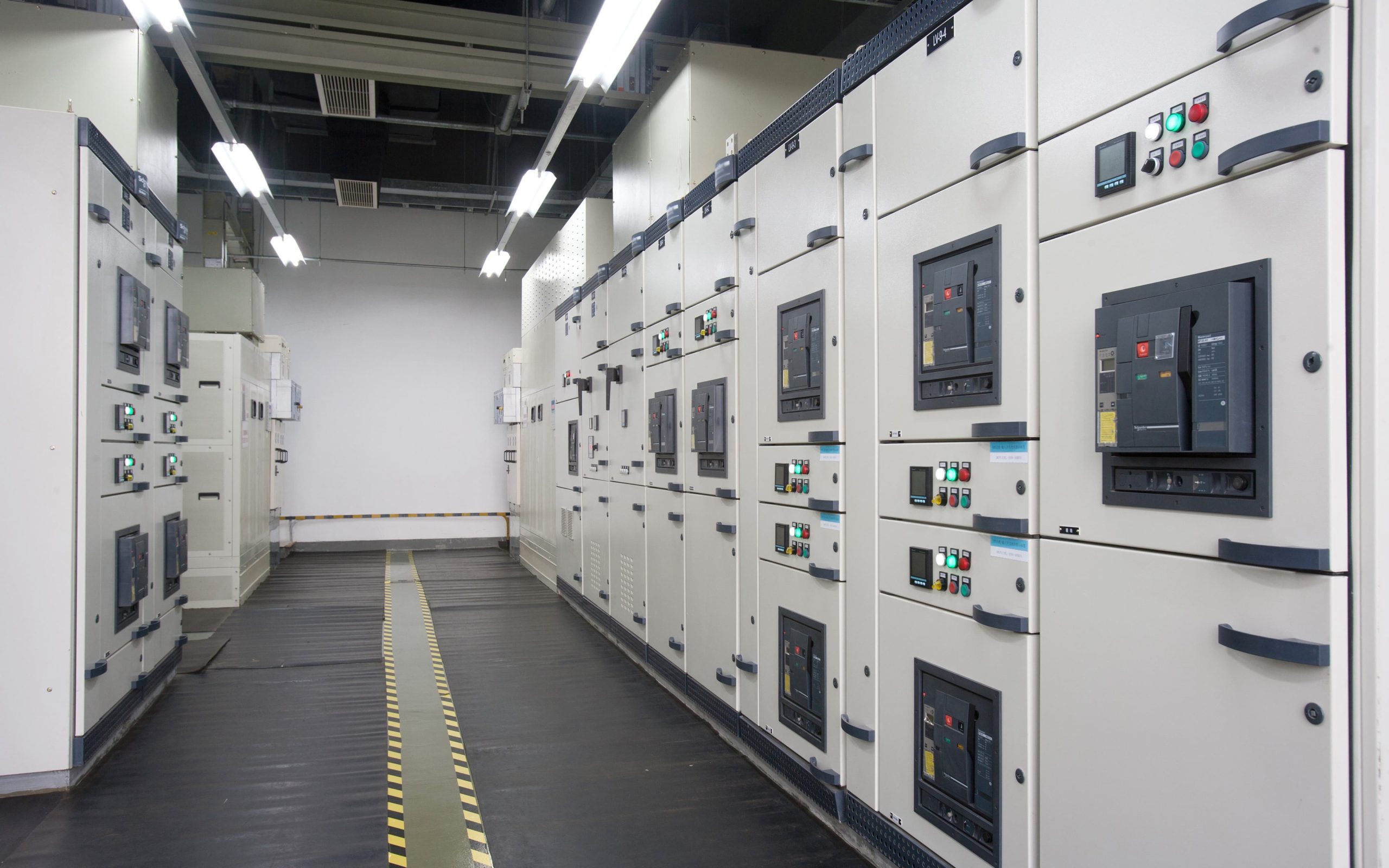
sistema de control de la temperatura
Resumen de consejos para optimizar los efectos del arenado con alúmina:
- Elija el tamaño de partícula y las boquillas adecuados: Las diferentes formas de boquilla y tamaños de partícula afectan a los resultados del chorreado; la selección de los medios y equipos adecuados puede mejorar eficazmente la eficacia y la calidad de la superficie.
- Optimice los parámetros de chorreado: Ajuste con precisión la presión, el caudal, la distancia y el ángulo de chorreado en función de las características del material y los requisitos de chorreado para obtener el mejor efecto superficial.
- Utilice abrasivos de alta calidad: Los abrasivos de alúmina de gran pureza y calidad pueden mejorar el efecto del chorreado, prolongar su vida útil y reducir el desgaste del equipo. Sin embargo, es esencial sustituir a tiempo los abrasivos inadecuados (muy desgastados, contaminados, etc.).
- Mantenimiento regular del equipo: El rendimiento del equipo es crucial para los efectos del chorro de arena. Inspeccione y mantenga periódicamente el equipo para garantizar que funcione de forma óptima.
- Implemente el control de automatización: Utilice sistemas de chorreado inteligentes para supervisar y ajustar los parámetros del proceso en tiempo real, garantizando la coherencia y la eficacia. Preste atención a los tiempos operativos y organice operaciones escalonadas.
- Pruebas de lotes pequeños: Realice pruebas de lotes pequeños antes de la producción a gran escala para verificar los parámetros del proceso y la idoneidad del equipo, garantizando una producción sin problemas.
- Formar a los operarios: Los conocimientos y la experiencia de los operarios influyen directamente en los resultados del chorreado. Imparta formación periódica para mejorar su nivel operativo y su adaptabilidad.
- Registre y analice datos: Registre los parámetros y resultados de cada operación de chorreado, optimice continuamente los procesos de chorreado mediante el análisis de datos y mejore la calidad del producto.
- Controlar el entorno de trabajo: Instale sistemas eficientes de eliminación de polvo para garantizar un entorno de arenado limpio y estable, reducir la interferencia de polvo e impurezas y mantener la temperatura y humedad adecuadas para evitar el impacto material de las condiciones ambientales.
Analizando a fondo las 18 cuestiones anteriores, no sólo comprendemos las causas de estos problemas, sino que también encontramos soluciones viables y medidas de mejora. Estas estrategias pueden abordar eficazmente los retos operativos actuales y proporcionar referencias para la optimización futura de los procesos. Con un mantenimiento razonable de los equipos, la optimización de los parámetros y la aplicación de tecnología avanzada, junto con una orientación técnica y una formación adecuadas del personal pertinente, podemos mejorar significativamente los efectos del chorro de arena y garantizar la consistencia y estabilidad de la calidad del producto. De cara al futuro, con la continua exploración y aplicación de nuevas tecnologías, la tecnología de chorro de arena con alúmina liberará sin duda un mayor potencial, aportando más posibilidades para el tratamiento de superficies en diversas industrias.
Apéndice:
Medidas de seguridad en el proceso de arenado
Existen ciertos riesgos de seguridad asociados al uso de granalla de óxido de aluminio, como la exposición al polvo, el ruido y los peligros mecánicos. A continuación se indican algunas medidas de seguridad clave:
- Equipos de protección individual (EPI) Los operarios deben llevar ropa y guantes de protección para evitar el contacto de la piel con los medios o equipos de arenado. Además, deben llevar equipo de protección personal adecuado, incluidas gafas de seguridad, máscaras faciales, máscaras antipolvo o respiradores, para evitar la inhalación de polvo o lesiones oculares. También son necesarios tapones para los oídos u orejeras con supresión de ruido para evitar daños auditivos debidos a la exposición prolongada a altos niveles de ruido.
- Sistema de ventilación de polvo La instalación de un sistema eficaz de ventilación de polvo en la zona de operaciones de chorreado de arena es crucial. Puede reducir eficazmente la concentración de polvo y mejorar la calidad del aire en el entorno de trabajo. Las salas de chorreado modernas suelen contar con sistemas de captación de polvo que recogen y filtran el polvo para evitar su propagación a otras zonas de trabajo.
- Formación de operadores La formación periódica de los operarios en materia de seguridad es esencial para mejorar su concienciación sobre la seguridad y su capacidad de actuación en caso de emergencia. El contenido de la formación debe incluir el uso adecuado de los equipos de protección, los procedimientos operativos de seguridad, el mantenimiento de los equipos y las medidas de emergencia en caso de accidente, para ayudar a reducir los incidentes de seguridad causados por un manejo inadecuado.
- Preparación para emergencias Debe existir un plan de emergencia bien desarrollado en la zona de operaciones de chorreado de arena, que incluya medidas para hacer frente a incendios, explosiones u otras emergencias. Asegúrese de que dispone de equipos de extinción de incendios y suministros de primeros auxilios adecuados y realice simulacros de emergencia con regularidad para mejorar la capacidad de respuesta de los operarios.
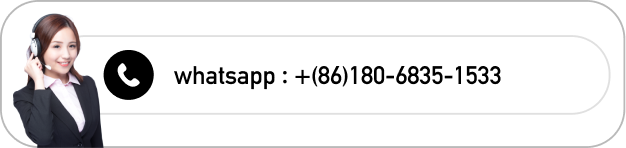