27 de septiembre de 2024
El proceso de chorro de arena es una tecnología de tratamiento de superficies ampliamente utilizada, principalmente para limpiar, desbarbar, esmerilar y pulir diversos materiales como metales, plásticos y cerámica. Con la aceleración de la industrialización, la posición del proceso de chorro de arena en la industria manufacturera se ha vuelto cada vez más importante, especialmente en los campos aeroespacial, automovilístico, electrónico y médico. Sin embargo, algunos problemas a los que se enfrenta el proceso de arenado, como la diferencia de color del producto, el brillo y la inconsistencia de la rugosidad, afectan seriamente a la calidad del aspecto y a la competitividad de los productos en el mercado.
Por diferencia de color se entiende la diferencia evidente de color entre el mismo lote de productos. Este fenómeno no sólo afecta a la estética del producto, sino que también puede provocar la insatisfacción del cliente y devoluciones. La inconsistencia del brillo hace que el producto parezca poco profesional en los efectos visuales, mientras que la rugosidad desigual puede afectar al rendimiento del producto, especialmente en industrias con requisitos estrictos sobre la calidad de la superficie. Estas situaciones son muy graves. Por lo tanto, comprender las causas de estos problemas y explorar soluciones se ha convertido en un tema importante para la mejora del proceso de arenado actual.
En este artículo, exploraré en profundidad las causas de la diferencia de color, el brillo y la inconsistencia de la rugosidad en el proceso de chorro de arena, analizaré los casos de éxito de las empresas actuales a la hora de abordar estos problemas y las medidas de mitigación adoptadas cuando no pueden superarse por completo. Mediante el análisis y la investigación sistemáticos, se pretende ofrecer sugerencias y referencias prácticas a las empresas pertinentes y promover la mejora y la innovación continuas del proceso de arenado.
Causas del problema de diferencia de color
La diferencia de color es un problema común en el proceso de chorreado, especialmente en productos con elevados requisitos estéticos. Comprender las causas de las diferencias de color es crucial para mejorar el efecto del chorreado y la calidad del producto.
Diferencias de materias primas
El material procedente de distintos lotes o fuentes puede presentar diferencias de color, lo que constituye una de las principales causas de los problemas de diferencia de color. Por ejemplo, los diferentes procesos de producción, fórmulas y condiciones de almacenamiento del mismo material pueden afectar al color del material. Además, los cambios en la composición de las materias primas, como el tipo y la proporción de aditivos, también pueden provocar diferencias en el color del producto final. Por lo tanto, garantizar la uniformidad del origen y la composición de las materias primas es crucial para reducir las diferencias de color.
Selección del material de chorreado
El tipo y las características de la granalla afectan directamente al color de la superficie después del chorreado. Por ejemplo, el uso de medios de chorreado de óxido de aluminio y el uso de medios de chorreado de cerámica pueden producir brillos y colores de superficie diferentes. La dureza, la forma y el tamaño de las partículas de la granalla afectarán a la fricción y a la rugosidad de la superficie durante el chorreado, afectando así a la uniformidad del color. Por lo tanto, a la hora de seleccionar el material de chorreado, debe tenerse muy en cuenta su impacto en el color final.
Cambios en los parámetros del proceso
Los cambios en los parámetros del proceso de granallado, como la presión de granallado, la distancia y el ángulo, también pueden afectar significativamente al efecto de la superficie tras el granallado. Una presión de chorreado excesiva o insuficiente puede provocar un tratamiento desigual de la superficie, con las consiguientes diferencias de color. Por ejemplo, cuando la distancia de chorreado es demasiado corta, puede causar un desgaste excesivo en algunas zonas, y los diferentes ángulos de chorreado (ya hemos escrito antes sobre este tema, haga clic para ver) pueden causar diferentes fuerzas de impacto del abrasivo sobre la superficie, lo que da lugar a colores incoherentes. Por lo tanto, es muy importante establecer parámetros de granallado estandarizados.
Factores medioambientales
Factores ambientales como la humedad, la temperatura y la luz también afectan a la diferencia de color en el proceso de granallado. Los entornos muy húmedos pueden aumentar la higroscopicidad del material de chorreado, modificando así sus propiedades físicas y afectando al efecto del chorreado. Además, los cambios de temperatura pueden provocar la dilatación térmica del material, modificando así su rendimiento cromático. Las diferentes condiciones de iluminación también pueden afectar al juicio visual del color, por lo que los factores ambientales deben controlarse en la medida de lo posible durante el proceso de granallado para mantener un efecto de procesado consistente.
A continuación, mostraré los efectos de diferentes métodos de chorreado (como el lijado en seco y el lijado en húmedo) y su impacto en la diferencia de color y el brillo para ayudarle a comprender la importancia de elegir el método adecuado.
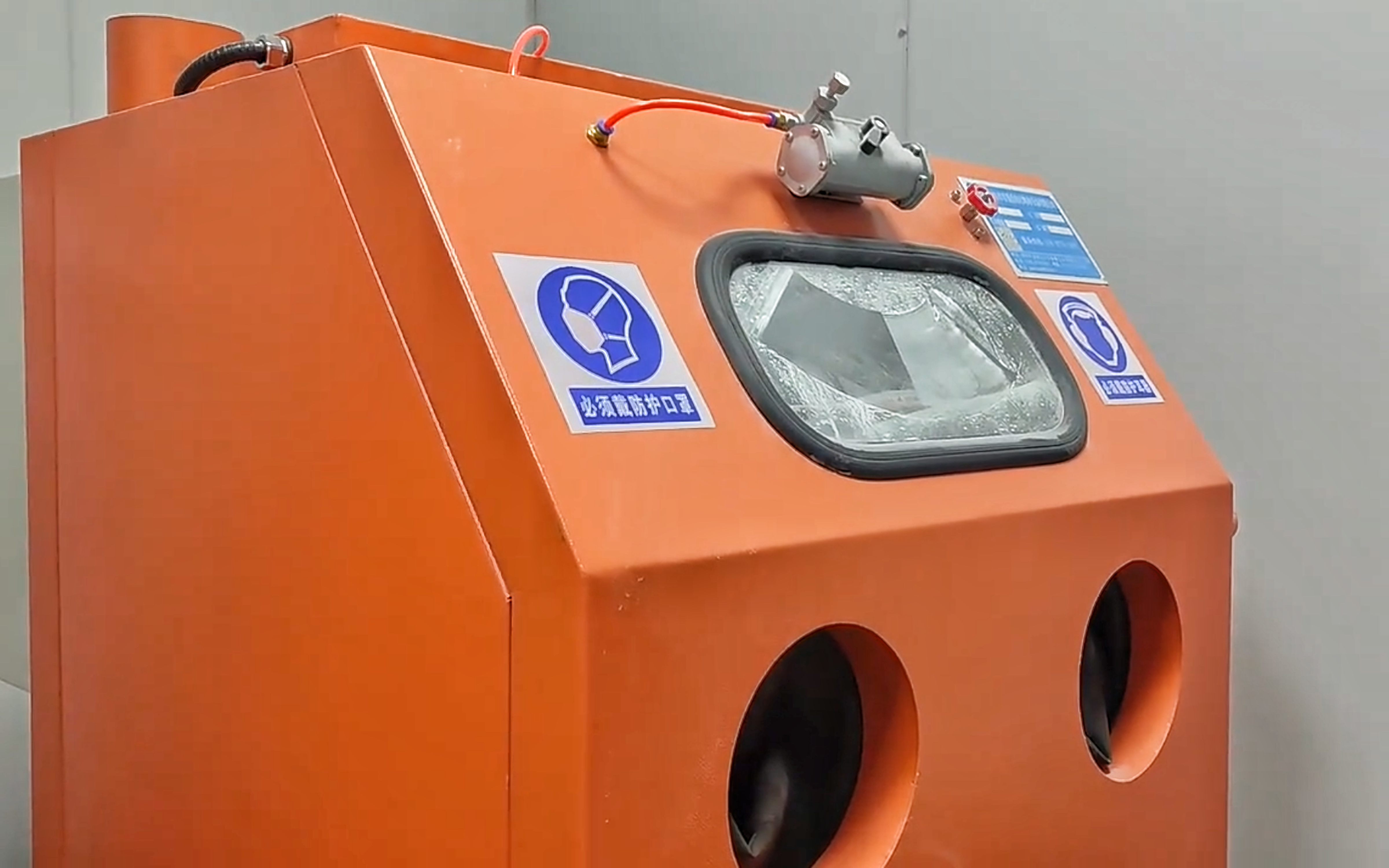
Arenadora en húmedo
Métodos de chorreado
- Chorro de arena en seco
Características: Utilice medios de chorro de arena en seco, adecuado para una variedad de materiales.
Ventajas: Buen efecto en la eliminación de rebabas y suciedad, adecuado para piezas metálicas.
Desventajas: Puede provocar una elevada rugosidad superficial y aumentar el riesgo de diferencia de color.
- Chorro de arena húmedo
Características: Mezcle agua con los medios de arenado para reducir el polvo y la dispersión.
Ventajas: Adecuado para piezas de trabajo con altos requisitos de acabado superficial, y puede controlar eficazmente la rugosidad.
Desventajas: El mantenimiento del equipo y el procesamiento son más complicados, y el tiempo de secado es mayor.
Efecto de diferencia de color
- Chorro de arena en seco
Debido al medio seco utilizado, puede producirse un desgaste desigual durante el chorreado, lo que da lugar a diferencias de color, especialmente cuando se trata de superficies lisas.
Adecuado para ocasiones en las que no se requiere una diferencia de color, pero puede ser necesario un tratamiento posterior en aplicaciones de gran demanda.
- Chorro de arena húmedo
La electricidad estática generada durante el chorreado en seco se reduce gracias a la intervención del agua y puede distribuirse más uniformemente por la superficie de la pieza, lo que reduce la posibilidad de diferencias de color.
Adecuado para productos que requieren una gran consistencia, como dispositivos médicos o componentes electrónicos.
Brillo y rugosidad
- Chorro de arena en seco
Debido a la gran fuerza de desgaste, la rugosidad de la superficie puede aumentar y el brillo puede disminuir.
No apto para piezas que requieran un tratamiento superficial liso, como piezas decorativas de alto brillo.
- Chorro de arena húmedo
Al reducir la dispersión del medio y mejorar la humectabilidad de la superficie, puede mantener un buen brillo y una baja rugosidad tras el arenado.
El chorreado húmedo da buenos resultados en industrias que requieren mucho brillo y poca rugosidad.
Ocasiones aplicables
- Chorro de arena en seco
Adecuado para la limpieza y desbarbado de superficies metálicas, de uso frecuente en la industria pesada.
No apto para productos con requisitos de aspecto estrictos.
- Chorro de arena húmedo
Más adecuado para productos con elevados requisitos de calidad superficial, como piezas de precisión, obras de arte y dispositivos médicos.
Adecuado para industrias con elevados requisitos de acabado superficial y consistencia de las piezas de trabajo.
En resumen, para productos que requieren mucho brillo y poca rugosidad, el chorreado en húmedo puede tener más ventajas, mientras que el chorreado en seco tiene ciertas ventajas en cuanto a eficacia y coste. Es crucial elegir el método de chorreado adecuado en función de los requisitos específicos del producto y las normas del sector.
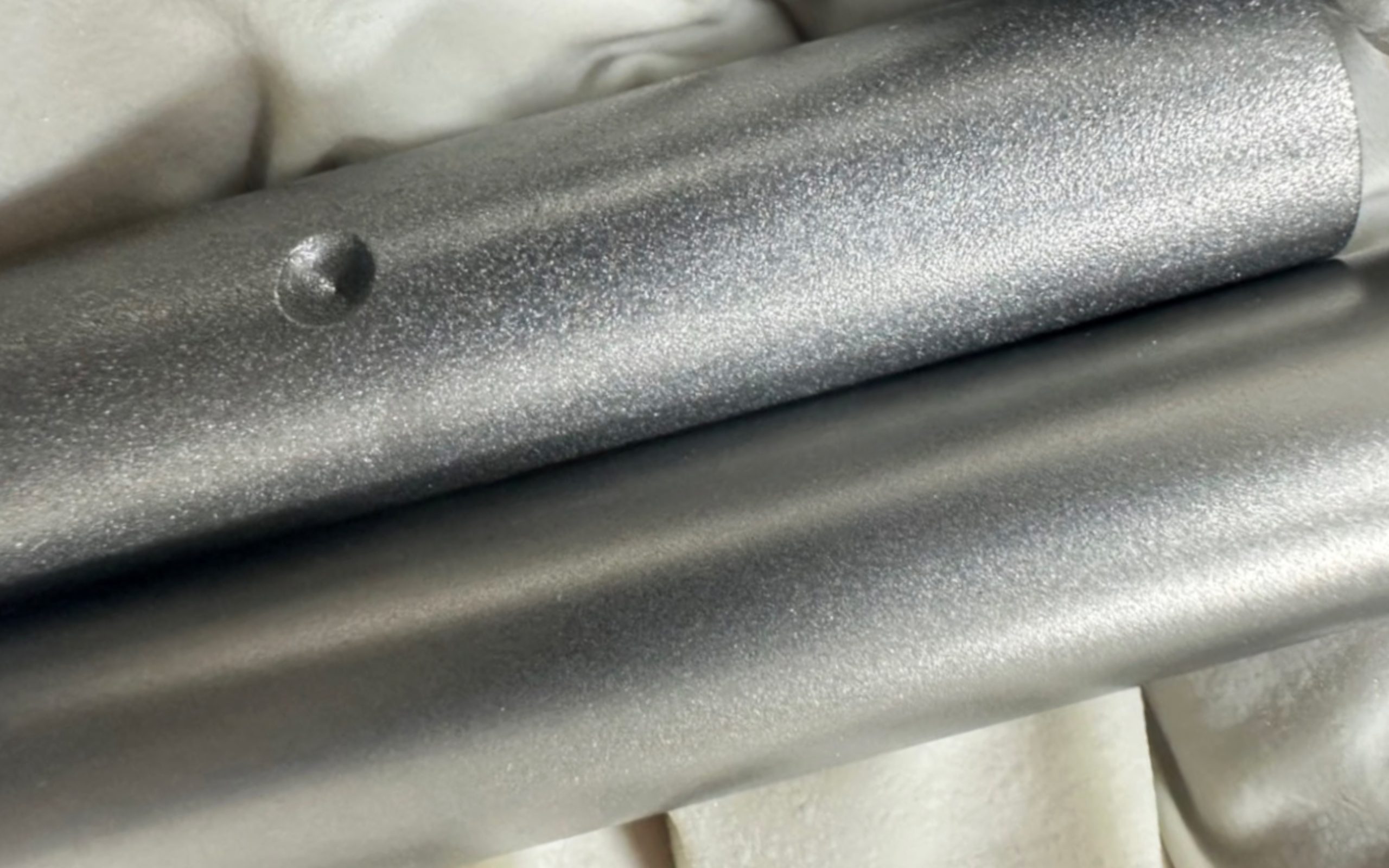
El efecto de diferentes medios sobre la misma pieza de trabajo
Causas de rugosidad incoherente
La rugosidad inconsistente no sólo afecta a la estética del producto, sino que también puede afectar a su funcionalidad, especialmente en aplicaciones que requieren piezas de precisión. A continuación se indican las principales causas de la rugosidad incoherente.
Características de los abrasivos
La dureza, la forma y el tamaño de las partículas de la granalla afectan directamente a la rugosidad. Por ejemplo, el uso de granalla angular puede dar lugar a una mayor rugosidad superficial, mientras que la granalla esférica tiene más probabilidades de producir una superficie lisa. Por lo tanto, al seleccionar la granalla, debe tenerse en cuenta el efecto de sus características sobre la rugosidad de la superficie.
Inconsistencias en el proceso de voladura
Las incoherencias en el proceso de chorreado, como la distancia de chorreado, las fluctuaciones de presión y el flujo inestable del abrasivo, pueden provocar variaciones en la rugosidad. Mantener la consistencia del proceso de granallado es esencial para lograr una rugosidad uniforme.
Estado de mantenimiento de los equipos
El estado de mantenimiento del equipo de granallado también afecta al efecto del granallado. El envejecimiento, el desgaste o los fallos del equipo pueden dar lugar a resultados de chorreado inestables, lo que se traduce en una rugosidad inconsistente. Por lo tanto, el mantenimiento y la inspección periódicos del equipo de chorreado es una medida importante para garantizar la calidad del procesamiento.
Cómo superan estos problemas las empresas existentes
En el proceso de chorro de arena, a pesar de los retos que plantean la diferencia de color, el brillo y la inconsistencia de la rugosidad, muchas empresas han tomado una serie de medidas eficaces para superar estos problemas.
Control del material
Seleccionar materias primas de alta calidad de una fuente unificada es la base para garantizar la consistencia de los efectos del chorro de arena. Las empresas deben establecer relaciones de cooperación con proveedores fiables para garantizar la calidad y estabilidad de las materias primas. Esto no sólo puede reducir los problemas causados por las diferencias de material, sino también mejorar la calidad del producto final. Además, la comprobación y verificación estrictas de las materias primas para garantizar que cumplen los requisitos de producción es también un eslabón al que las empresas deben prestar atención.
Producción normalizada
Establecer parámetros de proceso y procedimientos operativos estrictos es crucial para mejorar la consistencia de los efectos del chorro de arena. Las empresas deben aclarar cada eslabón del proceso de chorreado, incluida la selección del medio de chorreado, la presión de chorreado, la distancia de chorreado y el ángulo de la boquilla. Además, mediante el establecimiento de un manual de funcionamiento estandarizado, se guía y estandariza a cada operario para garantizar que cada operación de chorreado de arena sea coherente, reduciendo así las fluctuaciones de calidad causadas por factores humanos.
Actualización de equipos
El uso de equipos de chorreado avanzados puede mejorar significativamente la consistencia de los efectos del chorreado. Los equipos de chorreado modernos suelen estar equipados con un sistema de control inteligente que puede ajustar con precisión los parámetros de chorreado y supervisar diversos indicadores durante el proceso de chorreado en tiempo real. Las empresas deben evaluar y actualizar periódicamente los equipos y adoptar nuevas tecnologías que se adapten a sus necesidades de producción para mejorar la eficacia de la producción y la calidad del producto.
Formación de los trabajadores
La formación sistemática de los operarios es una medida importante para garantizar la estabilidad del proceso. Las empresas deben organizar periódicamente cursos de formación para ayudar a los empleados a comprender los principios básicos del chorreado de arena, los métodos de funcionamiento de los equipos y las soluciones a los problemas más comunes. Al mejorar la profesionalidad de los empleados, las empresas pueden reducir los errores operativos y mejorar la estabilidad del proceso de chorreado, garantizando así la consistencia de la calidad del producto.
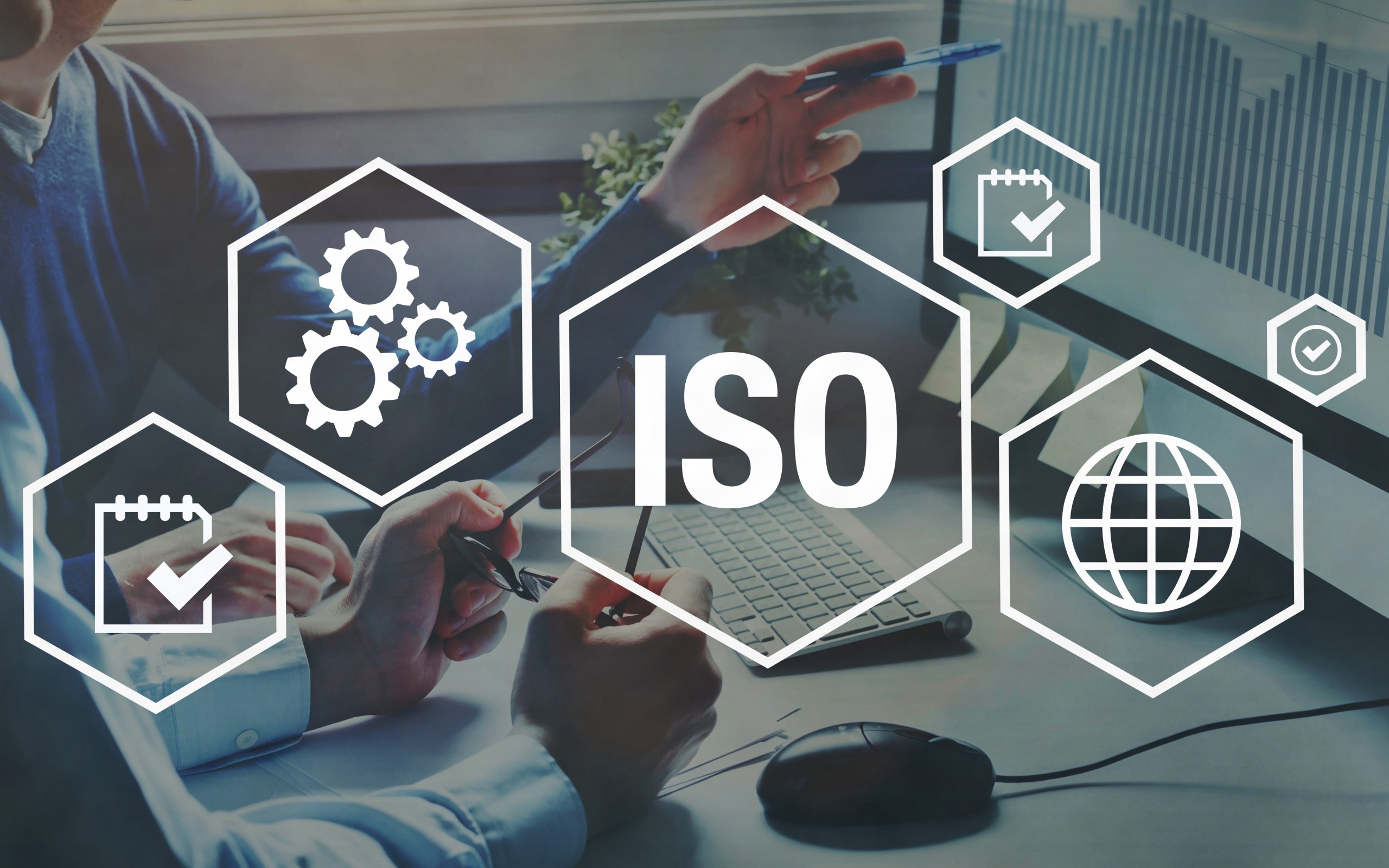
Medidas paliativas
Aunque se tomen las medidas anteriores, es posible que sigan existiendo diferencias de color, brillo y rugosidad que no puedan eliminarse por completo durante el proceso de arenado. En este caso, las empresas pueden considerar las siguientes medidas de mitigación.
Tecnología de corrección de las diferencias de color
En el caso de las piezas chorreadas con arena, la diferencia de color puede corregirse mediante un tratamiento posterior de revestimiento o coloración. La aplicación de revestimientos y técnicas de teñido adecuados puede cubrir o mejorar hasta cierto punto el problema de la diferencia de color. Esto no sólo mejora la calidad del aspecto del producto, sino que también aumenta su resistencia a la corrosión y al desgaste, y prolonga su vida útil.
Optimizar los parámetros del proceso
Ajustando constantemente los parámetros de chorreado, las empresas pueden minimizar las diferencias e incoherencias de color. Por ejemplo, afinar la presión, la velocidad y el ángulo de la boquilla durante el proceso de chorreado para optimizar el efecto del chorro de arena. Tras aplicar estos ajustes, las empresas deben realizar inspecciones de calidad continuas para garantizar que la calidad del producto final cumple las normas.
Inspecciones periódicas
Establecer un estricto mecanismo de inspección de la calidad ayudará a detectar y corregir rápidamente los problemas en el proceso de chorreado. Las empresas pueden realizar inspecciones de calidad a varios niveles antes, durante y después del chorreado para garantizar que cada pieza cumple las normas de calidad especificadas. Mediante la supervisión en tiempo real y el análisis de datos, las empresas pueden identificar rápidamente los posibles problemas y realizar los ajustes y correcciones necesarios.
Cuando se enfrentan a problemas como la diferencia de color o las incoherencias de brillo y rugosidad en el proceso de chorreado, las empresas pueden superarlos y aliviarlos mediante diversos métodos. Ya sea mediante el control de materiales, la producción estandarizada, la actualización de equipos o la formación de los empleados, las empresas pueden mejorar la calidad del producto en el proceso de optimización continua. Aunque estos problemas no puedan eliminarse por completo, medidas como la tecnología de corrección de las diferencias de color, la optimización de los parámetros del proceso y el establecimiento de un mecanismo de inspección periódica pueden reducir eficazmente las fluctuaciones de calidad y garantizar la ventaja del producto en la competencia del mercado. Mediante la mejora continua, las empresas seguirán siendo competitivas en el feroz entorno del mercado y se ganarán la confianza y la satisfacción de los clientes.
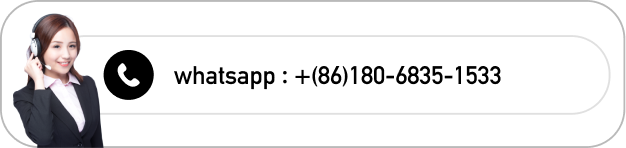