Cerámica frente a perlas de vidrio para el acabado de moldes
7 de febrero de 2025
En el competitivo mundo de la fabricación de moldes, la calidad del acabado superficial repercute directamente en el rendimiento del producto y la eficacia de la producción. Sin embargo, muchos fabricantes indios se enfrentan a retos persistentes con las microesferas de vidrio tradicionales, como altos índices de defectos, exceso de polvo y frecuentes problemas de mantenimiento.
Este informe profundiza en las principales razones por las que las granallas cerámicas se están convirtiendo en la opción preferida para la limpieza de moldes, respaldadas por datos de rendimiento, conocimientos técnicos y estudios de casos reales.
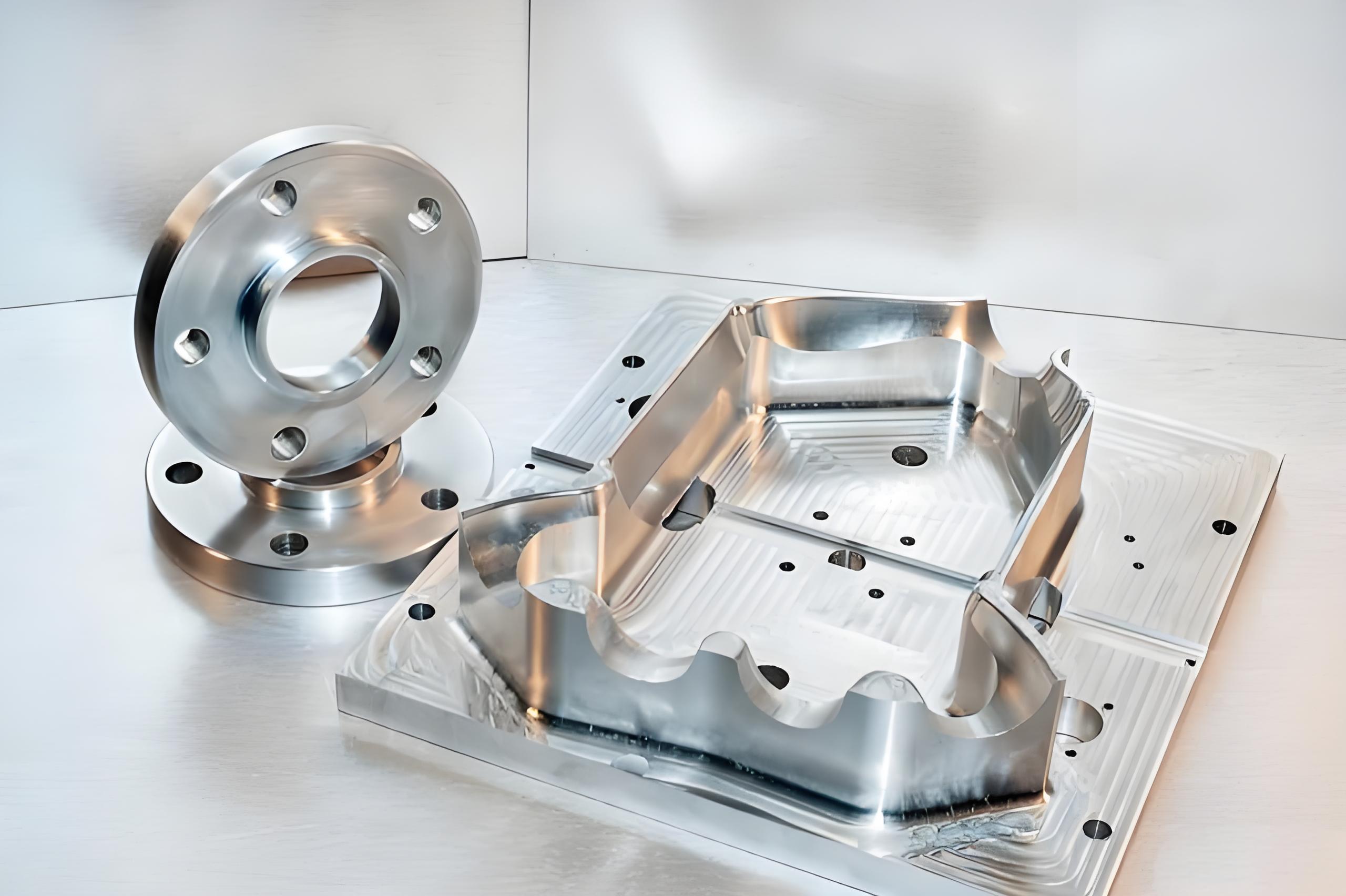
Comparación de prestaciones: Perlas de vidrio frente a perlas de cerámica
Para entender por qué las microesferas cerámicas superan a las de vidrio, examinemos seis parámetros críticos de rendimiento:
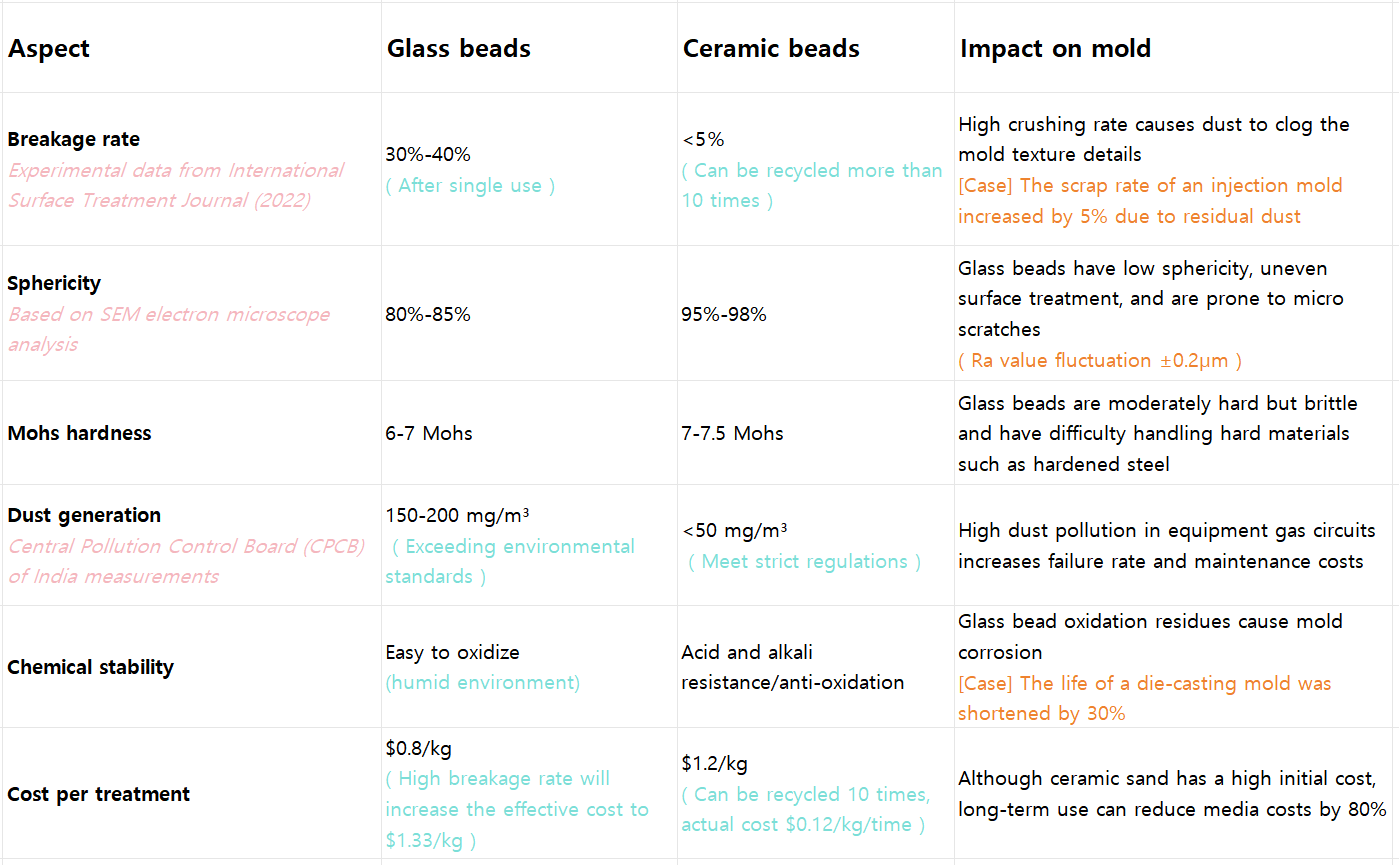
Principios técnicos: Cómo afectan las propiedades de los medios al acabado de los moldes
Índice de rotura y limpieza del molde
Las microesferas de vidrio se rompen y se convierten en polvo fino (<10 µm), que se incrusta en los poros del molde, provocando adherencias y defectos. En cambio, los abrasivos de las microesferas cerámicas (compuestos de circonio y alúmina) minimizan las roturas, lo que garantiza moldes más limpios y una vida útil más larga.
Esfericidad y mecánica del contacto superficial
La menor esfericidad de las microesferas de vidrio (80%-85%) da lugar a una distribución desigual de la presión, lo que crea microarañazos. La esfericidad casi perfecta de las microesferas cerámicas (95%-98%) garantiza una distribución uniforme de las partículas, protegiendo la geometría del molde y consiguiendo valores Ra constantes.
Dureza y compatibilidad de materiales
Mientras que las microesferas de vidrio (6-7 Mohs) son adecuadas para materiales más blandos, fallan en aceros endurecidos. Las perlas de cerámica (7-7,5 Mohs) logran un equilibrio entre dureza y tenacidad, por lo que son ideales para una amplia gama de materiales, desde el aluminio hasta las aleaciones de titanio.
Estabilidad química y longevidad del moho
Las perlas de vidrio se oxidan en ambientes húmedos, dejando residuos corrosivos. La estabilidad química de las microesferas cerámicas garantiza la ausencia de contaminación, lo que prolonga la vida útil del molde y reduce los costes de mantenimiento.
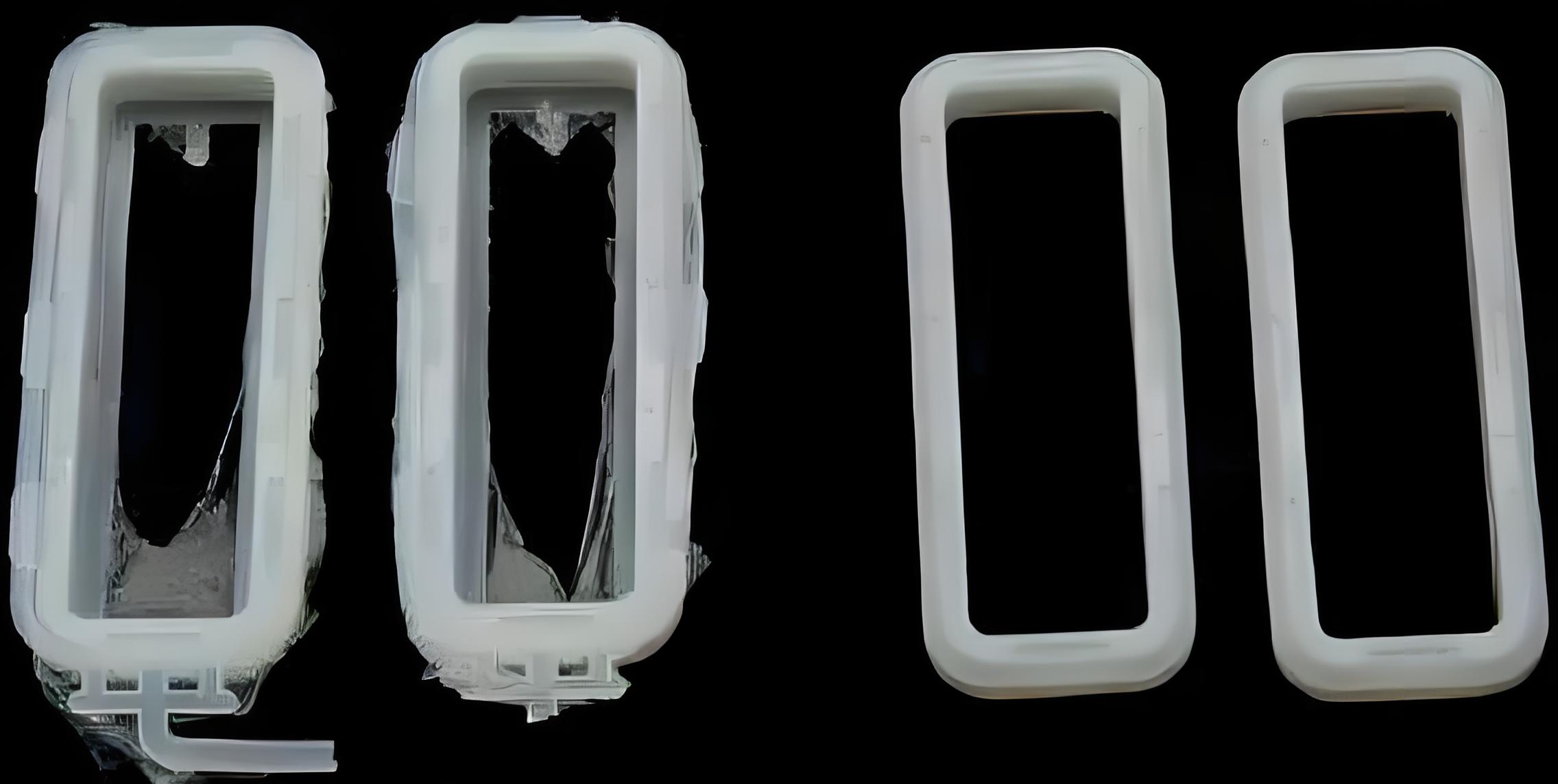
Cómo se adaptan las cuentas de cerámica a los distintos materiales de los moldes
Moldes de plástico (por ejemplo, moldes de inyección)
Los moldes de plástico son relativamente blandos, e incluso un ligero arañazo puede afectar al efecto de desmoldeo o a la calidad del producto acabado.
Las microesferas cerámicas pueden reducir eficazmente la fuerza de impacto y evitar arañazos gracias a su perfecta esfericidad, al tiempo que proporcionan un efecto de pulido uniforme. Mediante el ajuste de la presión de arenado (50-80 PSI), se puede lograr un control preciso para realizar un pulido suave adecuado para moldes de plástico.
Además, las características de bajo nivel de polvo del granallado con microesferas cerámicas reducen la incrustación de partículas en los poros del molde para evitar que afecte al desmoldeo.
Moldes de aluminio (por ejemplo, moldes de fundición a presión)
Los moldes de aleación de aluminio son propensos a las capas de óxido y las rebabas, pero el material es relativamente blando, por lo que hay que controlar la dureza y la fuerza de impacto del medio durante la limpieza.
El granallado con microesferas de cerámica tiene una dureza moderada, superior a la de las microesferas de vidrio pero inferior a la de los medios de corindón, y puede eliminar eficazmente los defectos sin dañar la superficie del molde. Su estructura esférica garantiza una fuerza uniforme y consigue un acabado uniforme de la superficie. Al mismo tiempo, tiene una gran estabilidad química, no reacciona con las aleaciones de aluminio y no deja contaminantes.
Moldes de acero inoxidable (por ejemplo, moldes de estampación de precisión)
Los moldes de acero inoxidable se utilizan a menudo en industrias como la estampación de precisión y la fabricación de dispositivos médicos. La superficie debe estar muy limpia y libre de contaminación química.
Las microesferas cerámicas pueden eliminar eficazmente la escoria de soldadura, las incrustaciones de óxido y las manchas persistentes bajo una presión de chorro de arena de 80-120 PSI, evitando al mismo tiempo las microfisuras o la deformación de la superficie. Su alta resistencia al desgaste y su capacidad de reciclaje reducen el coste de los consumibles y son adecuados para las necesidades de producción en serie.
Moldes de aleación de titanio (por ejemplo, componentes aeroespaciales)
El sector aeroespacial exige requisitos muy estrictos a la superficie de los moldes de aleaciones de titanio. La alta dureza del granallado con microesferas de cerámica puede eliminar la capa de óxido, al tiempo que tiene una buena tenacidad para evitar microfisuras. Su resistencia a altas temperaturas garantiza un rendimiento estable en entornos extremos, y no hay residuos químicos, lo que cumple las normas de la industria aeroespacial.
Moldes de caucho (por ejemplo, moldes de neumáticos)
Los moldes de caucho son propensos a acumular residuos y agentes desmoldeantes, que afectan a la vida útil y la calidad del producto acabado.
La baja fuerza de impacto de las microesferas cerámicas garantiza una limpieza suave y evita daños en el molde. Su estructura esférica mejora la fluidez, ayuda a eliminar a fondo los residuos finos y mejora la eficacia del desmoldeo. Además, el chorreado con microesferas cerámicas es bajo en polvo, respetuoso con el medio ambiente y reduce los costes de mantenimiento del equipo, lo que lo convierte en una opción ideal para el chorreado ecológico.
Casos prácticos de clientes: Resultados reales
Caso 1
Problema:
Un fabricante indio de moldes para automóviles tenía un problema constante con sus moldes de parachoques: el chorreado con microesferas de vidrio dejaba manchas oscuras en la superficie del molde, lo que provocaba una elevada tasa de defectos de 12%. Estos defectos afectaban al aspecto del producto final y aumentaban los costes de reelaboración.
Solución:
Para mejorar la consistencia y durabilidad de la superficie, el fabricante cambió a microesferas cerámicas B120, que ofrecen una dureza y reciclabilidad excelentes. Mediante un proceso de chorreado optimizado, las microesferas cerámicas se reutilizaron 10 veces, lo que garantizó un acabado superficial más uniforme sin comprometer la integridad del molde.
Resultados:
Tras cambiar a microesferas cerámicas, la rugosidad de la superficie se estabilizó en Ra = 0,8µm ± 0,05, lo que redujo significativamente las incoherencias visuales. Como resultado, la tasa de defectos descendió de 12% a sólo 2%, lo que redujo los residuos y las repeticiones. Además, la mayor reutilización y eficiencia de las microesferas cerámicas supuso un ahorro de $18.000 al año y mejoró la rentabilidad global de la producción.
Caso 2
Problema:
Un proveedor líder de moldes de conectores electrónicos de precisión se enfrentó a un gran reto: el polvo de perlas de vidrio estaba obstruyendo los complejos moldes de pasadores. Esta contaminación afectaba al rendimiento del molde y requería una limpieza frecuente, con intervalos de mantenimiento tan cortos como cada dos semanas.
Solución:
Para reducir la acumulación de polvo y prolongar la vida útil del molde, el proveedor adoptó microesferas cerámicas de gran pureza combinadas con un sistema de chorreado turbo para reducir significativamente los niveles de polvo en suspensión a menos de 30 mg/m³. Una mejor selección de los medios minimizó la contaminación por partículas y garantizó una limpieza precisa de las delicadas características del molde.
Resultados:
Tras introducir las bolas cerámicas, los intervalos de mantenimiento se ampliaron significativamente de 2 semanas a 3 meses, lo que redujo el tiempo de inactividad y los costes de mano de obra. Este cambio no solo mejoró la eficiencia operativa, sino que también garantizó un rendimiento constante del molde, consolidando la reputación del proveedor como fabricante de alta precisión.
El cambio de granalla de vidrio a cerámica está revolucionando el acabado de moldes, ofreciendo un rendimiento superior, ahorro de costes y beneficios medioambientales.
¿Está listo para mejorar su proceso de acabado de moldes? Póngase en contacto con nosotros para realizar una prueba gratuita de compatibilidad de soportes y encontrar la solución perfecta para sus necesidades.
Esté atento a nuestro próximo artículo, en el que exploraremos el uso innovador del granallado cerámico en 8 categorías de limpieza de moldes.
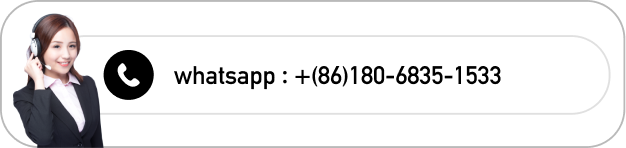