Vom Staub zum Glanz: Die Transformation durch Flüssigsandstrahlen
Juli 30, 2024
-
Reinigung von Gussoberflächen: Das Flüssigsandstrahlen entfernt effektiv die Oxidschicht und Rückstände von Gussoberflächen und poliert sie, um die Oberflächenglätte zu verbessern. Diese Methode ist besonders wirtschaftlich und effektiv für komplexe, netzförmige Gussteile, wie z. B. Turbinenschaufeln in Düsentriebwerken. Bei Druckgussteilen bringt das Flüssigsandstrahlen eine einheitliche Metallfarbe zum Vorschein und verbessert das Aussehen der Teile. Flüssigstrahlen kann die Oberflächenhärte und Korrosionsbeständigkeit weiter verbessern und die Oberflächen von Instrumentengehäusen und -rahmen verschönern.
-
Entfernung von Oxidhaut: Nach der Wärmebehandlung werden durch Flüssigsandstrahlen Oxidablagerungen und Restsalze effizient entfernt und die Oberflächenglätte verbessert. Es ist besonders effektiv für komplexe Formen und Präzisionsteile. So verlängert das Flüssigsandstrahlen beispielsweise die Lebensdauer von Feilen nach der Wärmebehandlung, ohne deren Schneiden zu beschädigen. Dieses Verfahren ist von unschätzbarem Wert für Industriezweige, die in hohem Maße auf Präzisionswerkzeuge und -formen angewiesen sind, und gewährleistet Langlebigkeit und gleichbleibende Leistung.
-
Entfernen von Mikrograten von bearbeiteten Teilen: Grate, auch wenn sie klein sind, können erheblichen Schaden anrichten. Im Zuge des technologischen Fortschritts werden mechanische Teile immer komplexer und stellen höhere Präzisionsanforderungen. In Branchen wie der Textilindustrie, der Hydraulik, der Luft- und Raumfahrt und der Medizintechnik, in denen Grate nicht toleriert werden, ist das Flüssigsandstrahlen eine effiziente und qualitativ hochwertige Methode zum Entgraten. Es kann auch kleine abgerundete Ecken an Oberflächenüberschneidungen erzeugen, eine häufige Anforderung bei vielen mechanischen Teilen. Diese präzise Kontrolle der Oberflächenbearbeitung ist für die Erhaltung der Integrität und Leistung von Hochpräzisionskomponenten von entscheidender Bedeutung.
-
Reinigung von Verunreinigungen und Rost: In verschiedenen Formen, wie z. B. Schmiede-, Stanz-, Gummi-, Reifen-, Kunststoff- und Glasformen, sammeln sich mit der Zeit unweigerlich Trennmittel und Brandflecken an. Flüssiges Sandstrahlen reinigt diese Verunreinigungen effektiv und verlängert die Lebensdauer der Formen. Es erfüllt auch die medizinischen Sterilisationsanforderungen für Lebensmittelformen und versetzt alte mechanische Teile wieder in einen neuwertigen Zustand. Diese Wiederherstellungsmöglichkeit ist besonders für Branchen von Vorteil, die teure Geräte aufarbeiten und wiederverwenden wollen, um Kosten und Abfall zu reduzieren.
-
Vorbereiten von Oberflächen für andere Behandlungen: Die Vorbehandlung mit Flüssigsandstrahlen vor dem Galvanisieren verbessert die Haftung der Beschichtung erheblich. Dies gilt insbesondere für Hartverchromungen, wie z. B. bei Kolbenringen von Motoren und Walzen von Textilmaschinen. Bei lackierten oder gespritzten Teilen erhöht das Flüssigsandstrahlen vor der Beschichtung die Haftung der Beschichtung und verbessert die Qualität und Festigkeit der Verbindung. Dieser Schritt gewährleistet, dass die nachfolgenden Behandlungen effektiver sind, was zu einer höheren Qualität und Haltbarkeit der Endprodukte führt.
-
Polieren: Als Poliermethode ist das Flüssigsandstrahlen sehr effektiv, insbesondere bei Teilen mit komplexen Formen wie Laufrädern und Turbinenschaufeln. Es ist auch wirtschaftlich für das Polieren von Formen für Münzen, Keramik und Diamanten. Die Fähigkeit, einen hohen Grad an Politur zu erzielen, ohne komplizierte Details zu beschädigen, macht das Flüssigsandstrahlen zu einem unschätzbaren Werkzeug in der Präzisionsfertigung und der High-End-Produktion.
-
Nicht-reflektierende dekorative Oberflächen schaffen: Das Flüssigsandstrahlen erzeugt nicht reflektierende Oberflächen und ist daher ideal für Teile, die eine glatte, aber nicht reflektierende Oberfläche erfordern, wie z. B. chirurgische Instrumente. Es wird auch für mattierte Glaswaren, Instrumententafeln, Kunststoff-Zeichenpapier und einkristalline Siliziumoberflächen verwendet. Die Vielseitigkeit, mit der sowohl ästhetische als auch funktionale Oberflächenqualitäten erzielt werden können, erweitert die Anwendungsmöglichkeiten des Flüssigsandstrahlens in verschiedenen Bereichen.
-
Verbesserung der mechanischen Leistung: Mechanische Teile wie Zahnräder, Kurbelwellen, Textilmaschinen und Nähmaschinen profitieren vom Flüssigsandstrahlen. Es verbessert die Oberflächenglätte um 0,5-1 Grad und erzeugt Mikrovertiefungen, die das Schmiermittel zurückhalten, die Schmierung verbessern und die Lebensdauer der Teile verlängern. Flüssigstrahlen erhöht die Ermüdungsfestigkeit und Korrosionsbeständigkeit erheblich und legt Oberflächenfehler frei, was die Risserkennung erleichtert. Diese umfassende Verbesserung der mechanischen Leistung ist für die Verlängerung der Lebensdauer kritischer Bauteile von entscheidender Bedeutung.
Was sind die Vorteile des Flüssigsandstrahlens in der modernen Industrie?
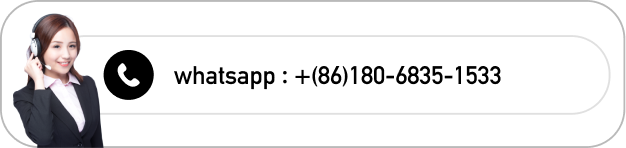
Ansichten insgesamt: 6.350