ショットピーニングとは何ですか?
9月 5, 2024
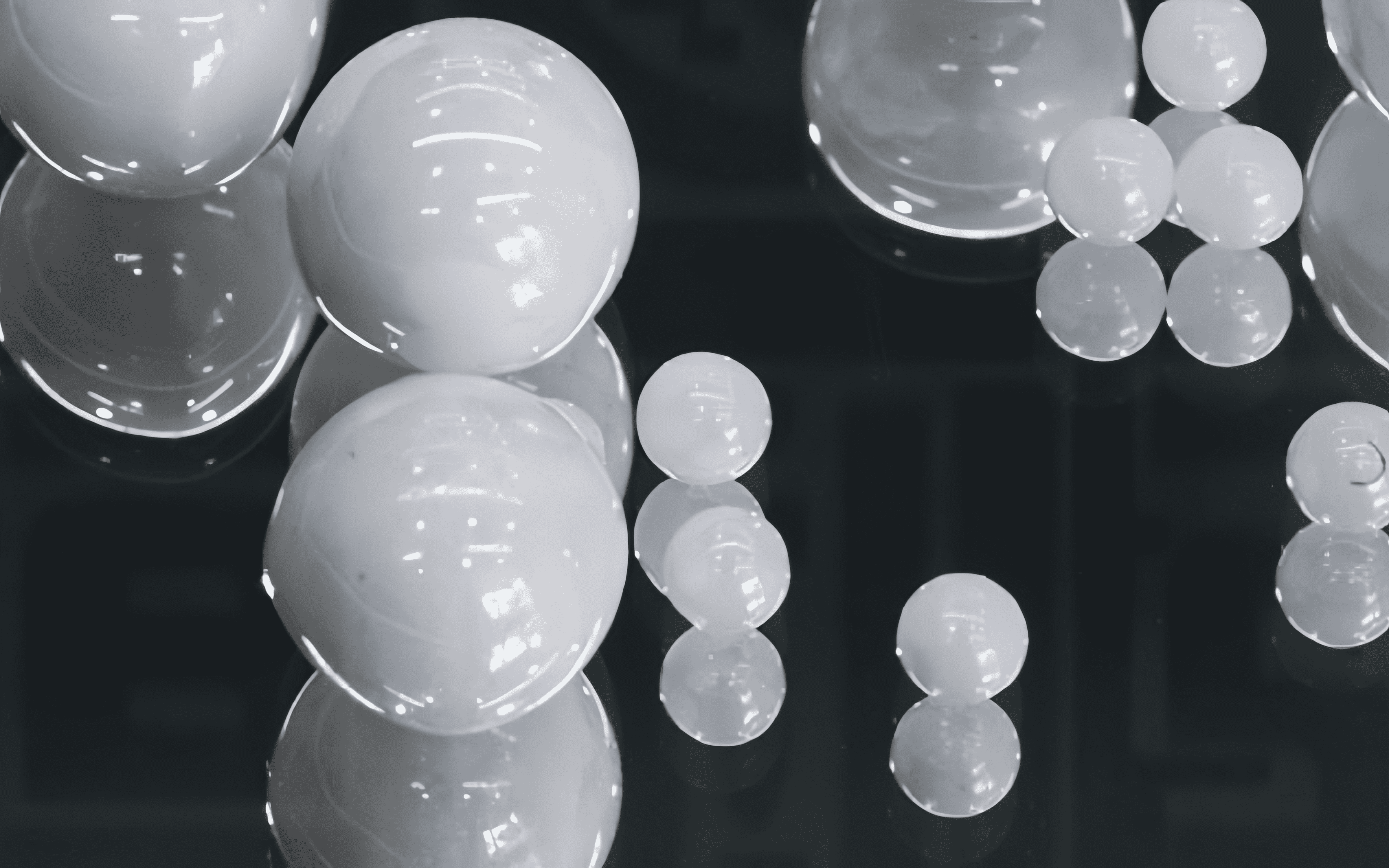
ショットピーニングとは?
ショットピーニングとは、ワークの表面に硬い粒子(ショット)を高速で噴射し、ワークの性能を向上させる表面処理技術である。金属加工、自動車製造、航空宇宙などの分野で広く利用されている。主な目的は、ワークの表面に粒子を衝突させることで、強度、耐摩耗性、表面品質など、ワークの物理的特性を向上させることである。
原則
ショットピーニングの基本原理は、高速の粒子をワークピースの表面に衝突させることによって圧縮応力層を生成し、それによって表面に現れる可能性のある引張応力を相殺し、材料の疲労強度を向上させることである。粒子の高速衝突により、材料の表面層が塑性変形する。この変形は、表面品質を向上させるだけでなく、材料の機械的特性も向上させる。ショットピーニング後は、材料の表面の亀裂や欠陥が効果的に減少し、耐久性がさらに向上します。
素材
ショットピーニング媒体の材料は多様であり、異なる材料は異なる処理要件に適している:
- スチールショット: 硬度が高く、金属材料の加工によく使用され、表面の酸化膜や汚れを効果的に除去できる。
- ステンレス・ショット耐食性に優れ、環境条件の厳しい場所での使用に適している。
- セラミックショット硬度が高く、表面の汚れを除去し、表面品質を向上させるためによく使用され、高い精度が要求される場合に適している。
- グラスショットより軟らかく、微細な表面欠陥の除去などの微細な表面処理に適している。
注: 表面が鉄汚染を許容できない場合は、ステンレス・スチール・ショット、セラミック・ショット、ガラス・ショットを検討すべきである。
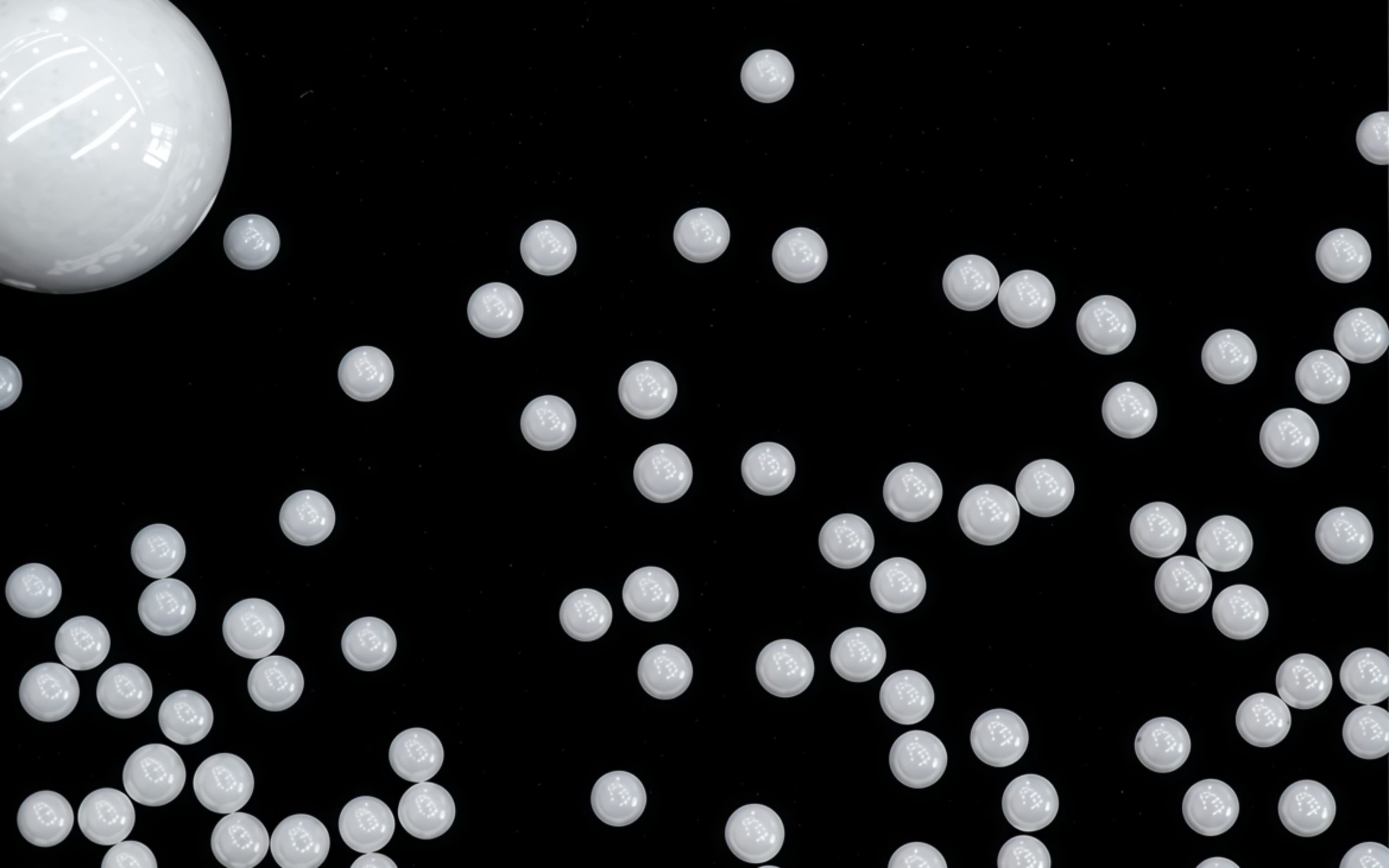
セラミックピーニングビーズ
ショットピーニングの歴史
ショットピーニング技術の発展は、工業生産技術の進歩を反映している。初期の手作業から現代の自動化装置まで、ショットピーニング技術はさまざまな分野で広く使用され、継続的に改良されてきました。
初期開発
ショットピーニング技術の起源は、主に金属部品の強化に使用されていた19世紀初頭にさかのぼることができます。初期のショットピーニング装置は通常、手動式で効率は低かったが、その後の技術開発の基礎を築いた。
近代化プロセス
- 20世紀初頭:工業化の進展に伴い、ショットピーニング技術は徐々に成熟してきた。自動化されたショットピーニング装置の出現により、加工効率と一貫性が大幅に改善され、ショットピーニング技術が広く使用されるようになりました。
- 技術革新: 20世紀半ば、ショットピーニング技術は、材料や設備の改良を含む一連の技術革新を経て、ショットピーニング処理の精度が向上した。新しいショットピーニング媒体とショットピーニング装置の出現は、ショットピーニングの処理効果と生産効率を向上させた。
重要なマイルストーン
- 特許出願:ショットピーニング技術の特許出願は、技術の正式化と標準化を意味し、ショットピーニング技術の開発と応用を促進する。
- 業界標準:例えば、ショットピーニングに関するSAEの規格は、ショットピーニング工程を標準化し、あらゆる分野での統一された作業ガイドラインを提供しています。
ショットピーニング装置とは?
さまざまな表面処理のニーズに対応するため、ショットピーニング装置には多くの種類があります。空気圧式ショットピーニング装置から全自動ショットピーニングシステムまで、装置の選択は特定の用途シナリオと処理要件によって異なります。ショットピーニング装置の種類と構成には、主に次のようなものがあります:
- ショットピーニングマシン
ショットピーニング機は、ショットピーニングの中核となる装置です。これらの装置は、粒子の流れ、速度、方向を制御し、所望の処理効果を確保するために使用されます。圧力、速度、粒子径、形状などの操作パラメータは、ショットピーニング効果に重要な影響を与えます。構造や用途の違いにより、以下のタイプに分けられます:
- 空気圧ショットピーニングマシン:圧縮空気を使用して、ワークピースの表面に高速でボールを吹き付けます。小型部品やメディアサイズの部品の処理に適しています。空気圧式ショットピーニング機は、操作が簡単でメンテナンスも容易ですが、処理効率は比較的低くなります。
- 遠心ショットピーニングマシン: ショットを遠心力でワーク表面に投射するため、大量生産や大型ワークの加工に適しています。遠心ショットピーニング機は、均一な加工が可能で効率が高く、微細な加工が必要な場合に適しています。
- ドラムショットピーニングマシン:ワークをドラムにセットし、ショットピーニング装置で加工します。ドラム式ショットピーニング装置は、異形部品、特に自動車部品や小型金属部品の加工に適しています。
- 吊り下げ式ショットピーニングマシン:ワークを吊り下げ装置でショットピーニング室に吊り下げ、ショットピーニング装置で処理します。機械部品や構造部品など、大型・重量のあるワークの加工に適しています。
- ショットピーニング室:ワークとショットピーニング装置を収容するためのショットピーニング装置を備えた密閉された空間。ショットピーニング室は、ショットピーニング工程中の粒子の飛散を効果的に制御し、作業環境を清潔に保つことができる。
- ショットピーニング機の主要部品
- ノズル:ノズルは、ショットを加速してワークの表面に噴出する役割を果たします。ノズルの設計と材質は、ショットピーニングの効率と効果に直接影響します。
- ショット輸送システム:ホッパーや搬送パイプなどの部品を含め、ショットをノズルに搬送する。
- 回復システム:ショットピーニング工程で飛散したショットを回収し、再び使用することで、材料利用率の向上とコスト削減を実現。
- 制御システム: 処理効果の一貫性と制御性を確保するため、圧力、速度、スプレー角度など、ショットピーニング機の運転パラメーターを調整するために使用します。
自動化は可能か?
ショットピーニング工程は、手動または自動で行うことができる。具体的な操作方法は、ショットピーニング装置の種類、ワークピースの処理要件、生産規模によって異なります。
手動操作
- 手動ショットピーニング:小規模生産や特殊なワーク加工では、ショットピーニング機を手動で操作する必要がある場合があります。この場合、オペレータは、ショットピーニング機の設定を手動で調整し、ショットピーニングの方向と範囲を制御する必要があります。手動ショットピーニングは、小さな部品の修理や微細な表面処理の実施など、処理効果に特別な要件がある場合に適しています。
- 手動アシスト:自動化されたショットピーニングシステムであっても、手動操作は必要である。オペレータは、ショットピーニング工程を円滑に進めるため、定期的に装置の稼働状況を確認し、メンテナンスや清掃作業を行う必要があります。
自動運転
- 全自動ショットピーニング機: 最新のショットピーニング装置では、ワークの搬送、ショットピーニング、リサイクルなど、ショットピーニング工程のさまざまなステップを自動的に完了できる自動制御システムの採用が増えています。完全自動のショットピーニング装置は、生産効率を向上させ、処理効果の一貫性を確保し、人的介入の必要性を減らすことができます。
- ロボットショットピーニングシステム: 一部の複雑なショットピーニングのニーズでは、産業用ロボットがショットピーニング作業に使用されます。ロボットショットピーニングシステムは、ショットピーニングの角度と位置を正確に制御できるため、複雑な形状や高い精度が要求されるワークピースの処理に適しています。
- インテリジェントショットピーニングシステム: 人工知能とデータ分析技術を組み合わせたショットピーニングシステムは、ショットピーニングプロセスのパラメーターをリアルタイムで監視・調整し、処理効果を最適化することができます。これらのシステムは、ショットピーニング工程における問題を自動的に検出して調整し、人的介入を減らし、生産効率と品質を向上させることができます。
最近のショットピーニング装置では、自動化技術の採用が進んでいますが、ショットピーニング工程を円滑に進めるためには、手動操作と監視が依然として重要な役割を果たします。手動操作であれ、自動化されたショットピーニングシステムであれ、装置の機能と操作方法を理解することは、最良の処理効果を得るために不可欠です。
ショットピーニング効果の測定方法
ショットピーニングの効果を測定するには、通常、以下の観点からの評価が必要である:
- 表面硬度:ショットピーニングによって、材料表面の硬度は著しく向上するはずであり、これは硬度計で測定できる。
- 表面粗さ:表面粗さ計で評価できる。
- 圧縮応力層の深さ: ショットピーニングは、材料の表面に圧縮応力層を形成します。圧縮応力の深さは、X線回折または微小硬さ試験によって測定できます。
特筆すべきは、ジョン・アルメンがアルメンテストと呼ばれるショットピーニングの効果を測定する標準的な方法を考案したことである。この方法は、特殊な試験片(アルメン試験片)を使用し、ショットピーニングによる曲げ量を記録することにより、圧縮応力の影響を評価するものである。
具体的な手順は以下の通り:
- アルメン試験片:ショットピーニング工程で試験される標準的な厚さの鋼片です。
- 曲げの測定ショットピーニング後、試験片はある程度曲がりますが、その曲げ具合を専用の測定器(アルメンアークハイトメーター)で測定します。
- アークハイトは強度を示す:測定された曲げ量はアークハイトと呼ばれ、ショットピーニングによる材料表面の圧縮応力の強さを示します。アークハイトが大きいほど、加えられた圧縮応力は強い。
- ショットピーニング効果を制御します:アルメン試験は、ショットピーニング効果を効果的に制御し、加工の一貫性と品質を保証することができます。航空宇宙、自動車、その他の分野の品質管理に広く使用されています。
- 疲労強度: ショットピーニングは材料の疲労強度を向上させることができ、これは疲労試験を通じて知ることができる。
- 表面の形態: 走査型電子顕微鏡(SEM)を使って表面の微細構造を観察し、表面が望ましい効果を達成しているかどうかを分析する。
ショットピーニングの適用シナリオ
ショットピーニング技術は、材料の性能と表面品質の向上に重要な役割を果たし、多くの分野で広く利用されています。
効果
- 疲労強度を高める: ショットピーニングは、衝撃によって圧縮応力層を形成し、材料の耐疲労性を大幅に向上させ、亀裂の発生を低減します。この種の加工は、航空宇宙や自動車製造などの要求の厳しい分野で特に重要です。
- 耐摩耗性の向上: ショットピーニングは、材料の表面硬度を高め、耐摩耗性を向上させます。この効果は、機械や工具などの高摩耗部品にとって極めて重要です。
- 表面品質の向上: ショットピーニングは、表面の不純物を除去し、ワークピースの仕上げを改善し、外観を向上させ、より美しくすることができます。
アプリケーション・シナリオ
- 自動車製造: エンジン部品、トランスミッションシステムなどの表面処理に使用され、耐用年数と信頼性を向上させる。例えば、ショットピーニングは、エンジン部品の耐疲労性を効果的に向上させ、故障率を低減することができる。
- 航空宇宙 ショットピーニング技術は、航空機エンジンや機体構造などの主要部品の加工において重要な役割を果たしています。ショットピーニングは、これらの部品の強度と耐久性を高め、過酷な環境における信頼性を保証します。
- 建設工学:鋼構造物の防錆処理に使用され、その耐久性を向上させる。建設プロジェクトにおいて、ショットブラストは鋼構造物の腐食を効果的に防止し、耐用年数を延ばすことができます。
- 金属加工:金属表面の酸化膜、溶接スパッタなどを除去し、金属表面の清浄度と品質を向上させるために使用される。
- 医療機器:ショットピーニングは、インプラントの生体適合性と耐久性を向上させます。ショットピーニングにより、インプラントの表面はより滑らかになり、体内組織との一体化が向上します。
- 機械設備: 大型機械設備の保守および修理に使用されます。ショットブラストは、機器の作業効率と耐用年数を向上させます。
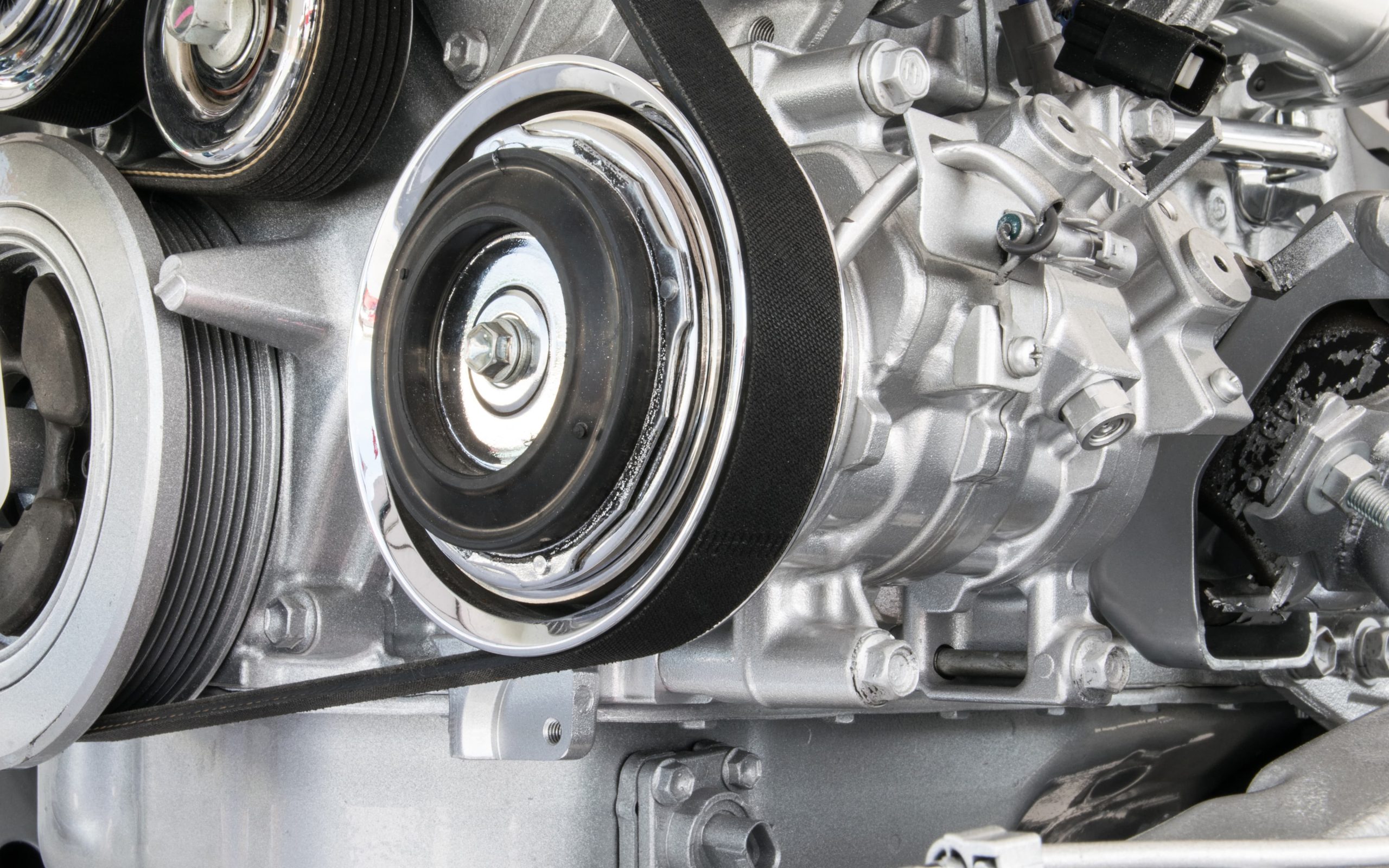
エンジン部品は耐疲労性を向上させる必要がある
ショットブラストとサンドブラストの違い
ショットピーニングとサンドブラストはどちらも表面処理技術です。この2つの原理は似ています。どちらも圧縮空気を動力として高速の噴射流を部品表面に噴射し、高速の衝撃によって材料表面の物理的特性を変化させます。しかし、両者には技術的な詳細があり、また用途にも若干の違いがあります。
使用するメディアが異なる:
- サンドブラスト:サンドブラスト媒体には、砂、ガラスビーズ、セラミックビーズなどさまざまな種類があります。大面積の洗浄に適しており、効果は比較的粗い。
- ショットピーニング:ショットピーニングは、主に強化処理に適した硬鋼ショット、ステンレスショット、セラミックビーズなどを使用する。プロセス要件は高く、処理効果は微細で均一です。
目的も効果も異なる:
- サンドブラスト:主に表面の錆や汚れを除去し、表面粗さを改善するために使用され、洗浄や前処理に適しています。
- ショットピーニング:材料の疲労強度と耐摩耗性を高め、圧縮応力層を形成して材料性能を向上させるために使用される。
適用される材料は異なる:
- サンドブラスト適切なサイズと硬さのサンドブラスト材料を選択することで、金属、ガラス、石、プラスチック、複合材料、木材など、さまざまな材料に適用できます。
- ショットピーニング:薄い板状のワークピースは処理できず、さもなければワークピースが容易に変形する。ショットピーニングは、厚さ2mm以上のメディアや大型金属製品、正確な寸法や輪郭を必要としない鋳物や鍛造品、成形砂、古い塗膜の酸化スケールや錆の除去にのみ使用できます。高炭素鋼、ステンレス鋼、アルミニウム合金、チタン合金、マグネシウム合金、真鍮、銅合金、プラスチックに広く使用されています。
ショットピーニングの今後の発展動向
ショットピーニング技術の今後の発展は、技術革新と市場需要の変化に焦点が当てられる。
技術革新
- インテリジェントショットピーニングシステム: 将来のショットピーニング技術は、人工知能と自動化技術を組み合わせ、ショットピーニングの精度と効率を向上させる。インテリジェントなショットピーニングシステムは、加工パラメータをリアルタイムで監視・調整し、加工効果を最適化できる。
- 環境にやさしいショットピーニング技術:現代の環境保護要件を満たすため、低公害、低騒音のショットピーニング技術を開発する。環境にやさしいショットピーニング技術は、環境への影響を低減し、作業環境の安全性を向上させる。
市場の需要
- ハイエンド産業用アプリケーション:航空宇宙や医療機器などのハイエンド分野でのショットピーニング技術の需要は、今後も増え続けるでしょう。これらの分野では、材料性能と表面品質に対する要求が非常に高く、ショットピーニング技術はこれらの厳しい要求を満たすことができます。
- 小型化と精度: より微細な表面処理の要求に対応するため、小型で精密なショットピーニング装置に対する市場の需要が高まっている。例えば、小型のショットピーニング装置は、複雑な微細部品に対応し、高精度加工のニーズに応えることができる。
異業種への応用
ショットピーニング技術は、3Dプリンティングやナノテクノロジーなどの新興産業への統合が進むだろう。これらの新興産業では、表面処理に対する要求がますます高くなっており、ショットピーニング技術の応用により、その分野がさらに拡大し、製品の品質と性能が向上する。
ショットピーニング技術は、まるで職人のように、高速の粒子でひとつひとつのワークを丹念に削り、耐圧性や総合性能を向上させる。航空機エンジンのソリッド処理、自動車部品の耐摩耗性向上など、ショットピーニングは私たちの生活の目に見えない細部を静かに変えています。技術の進歩とともに、ますますスマートで環境に優しく、精密なものになってきています。今後、ショットピーニング技術は、ハイエンドの製造業から新興技術まで、より多くの分野でその魔法を発揮し、私たちに高品質と長寿命をもたらし続けることが期待されます。ショットピーニングは、産業界の「見えないヒーロー」であるだけでなく、私たちにより完璧な未来を創造し続けるでしょう。
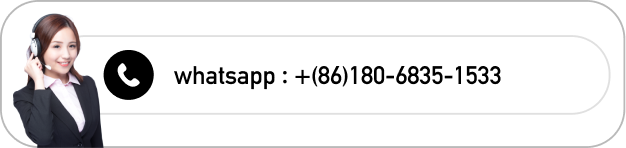