研削とサンドブラストの違い
9月 24, 2024
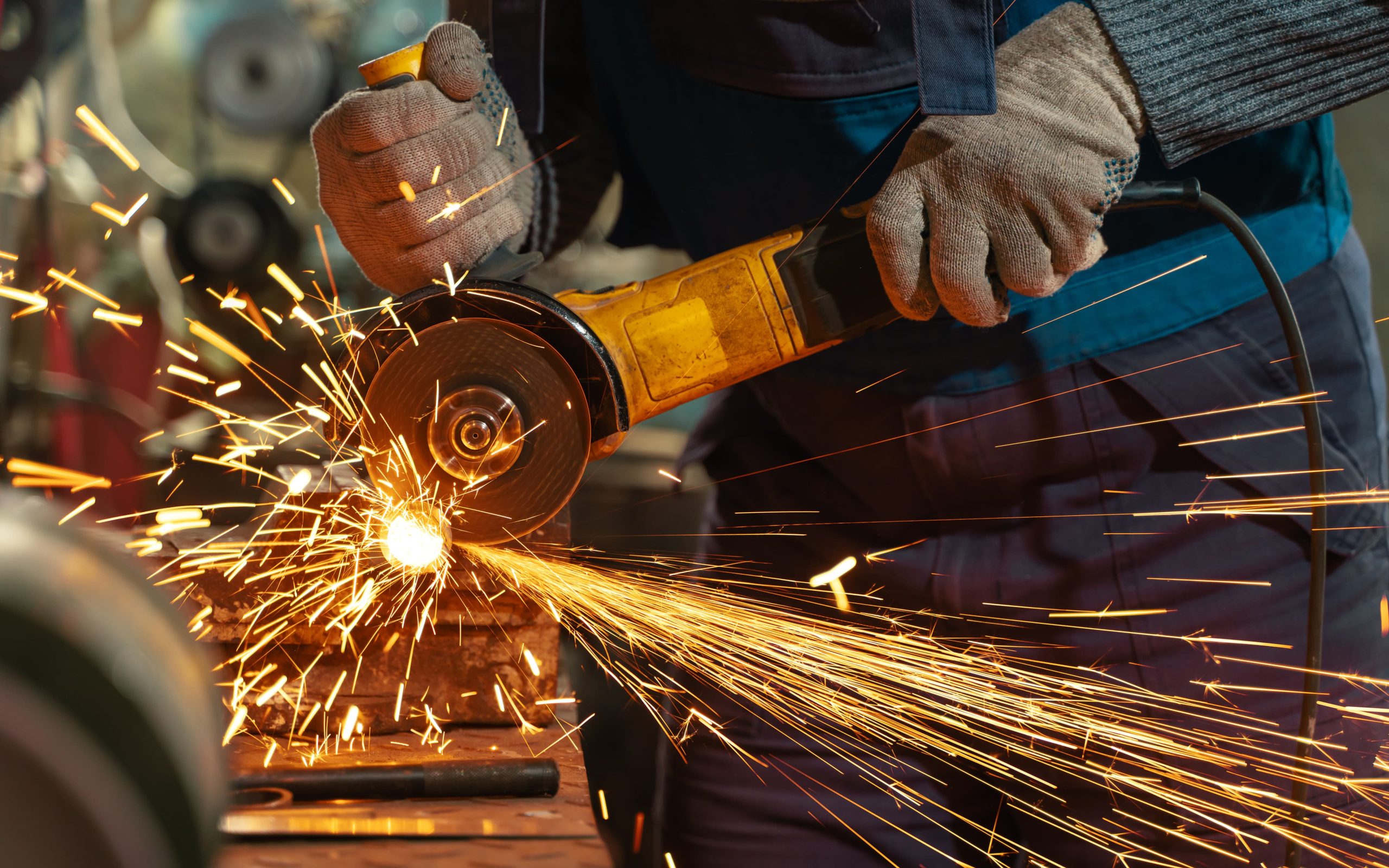
研削とサンドブラストは、表面処理の分野における2つの重要なプロセスです。一見似ているように見えますが、実際には用途、機能、材料に大きな違いがあります。金属加工、自動車製造、航空宇宙産業のいずれにおいても、どちらの技術も製品の表面品質と性能を向上させる重要なステップです。この記事では、研削材料とサンドブラスト材料の違いと関連性を、定義、材料、プロセスという異なる観点から掘り下げていきます。
研削材とは?
定義
研削材は、摩擦、切削、研削によって加工物の表面形状を変化させる材料である。研削材は、表面粗さの調整、酸化膜の除去、精密加工の前処理などに使用される。
Function
研削加工は、主にワークピースの前処理に使用され、大きな汚れ、スケール、表面欠陥、凹凸を除去する。この工程は、表面改質、溶接加工、大面積研削によく使用され、材料表面をより滑らかにし、サンドブラストや塗装など、その後の加工に適した土台を提供します。研削はまた、工作物の耐用年数を効果的に延ばし、製品の仕上がりと全体的な性能を向上させることができる。
研削の歴史
研削加工は、数千年前から存在する古代の加工技術である。その起源は、人類が道具や武器を作るために自然の石を使って粗い表面を研磨・加工していた石器時代まで遡ることができる。やがて研削加工は進化し、その応用範囲も広がっていった。
古代、研磨は主に手作業に頼っていた。職人たちは、砂や砂利のような自然素材や植物の粗い繊維を使って金属や木材を磨いていた。この段階での研磨工程は比較的単純で、主に人間の力と経験に頼っており、効率は低い。
産業革命の時代、特に19世紀後半に入ると、生産の機械化が進み、研削技術が急速に発展した。蒸気機関や電気機械の普及に伴い、研削盤が登場した。特に「砥石」の発明は、研削加工が新たな時代を迎えたことを意味する。砥石にはさまざまな研削材が使用され、より精巧で効率的な研削が可能になった。
20世紀に入り、新素材の開発が進み、研削技術が絶えず進歩する中で、研削技術は多くの分野で広く利用されるようになった。現代の研削加工は金属にとどまらず、セラミックス、プラスチック、ガラスなど、さまざまな材料の加工に広がっている。一定の強度と靭性を持つ材料であれば、天然に産出されたものであれ、人工的に製造されたものであれ、どのようなものでも使用できるため、クルミの殻でさえも研削媒体として適している。
近年、インテリジェント製造の概念が登場し、研削技術は自動化とデジタル化に向けて徐々に発展している。高精度CNC研削盤、ロボットなどの出現により、研削工程の効率と精度がかつてないほど向上した。同時に、環境保護に対する意識の高まりは、研削材料と研削プロセスのグリーン開発を促進し、業界の持続可能な発展を推進している。
研削工程で使用される技術
- 乾式粉砕: 研削加工中にクーラントを加えることはなく、研削とワークの接触時間と圧力を制御することで研削を行う。この方法は、変形しにくい材料に適している。
- 湿式粉砕: 研削中にクーラントを添加することで、摩擦による発熱を抑え、研削効率を向上させます。高硬度材の加工に適しています。
- 精密研削: ミクロンレベルの表面仕上げは、高精度な装置とプロセスパラメーター制御によって達成される。光学部品や高精度部品の加工によく使用される。
- 超精密研削: 超音波技術やレーザー技術と組み合わせることで、ナノメートルレベルの表面精度を実現し、主に半導体や光学機器などのハイテク分野で使用されている。
- CNC(コンピュータ数値制御)研削: コンピュータが研削盤の動きを制御することで、効率的で精密な加工を実現し、複雑な形状のワークにも対応する。
- レーザー研磨: レーザー光線で材料表面を加熱し、軟化させて研削効果を得る。高硬度材料の微細加工に適している。
研削材の分類
- プラスチックとポリマー
- ポリメチルメタクリレート(PMMA):透明性が高く、光学部品によく使われる。
- ポリカーボネート(PC):耐衝撃性があり、保護具や電子機器のハウジングに適している。
- ナイロン(PA):耐摩耗性が強く、機械部品に広く使用されている。
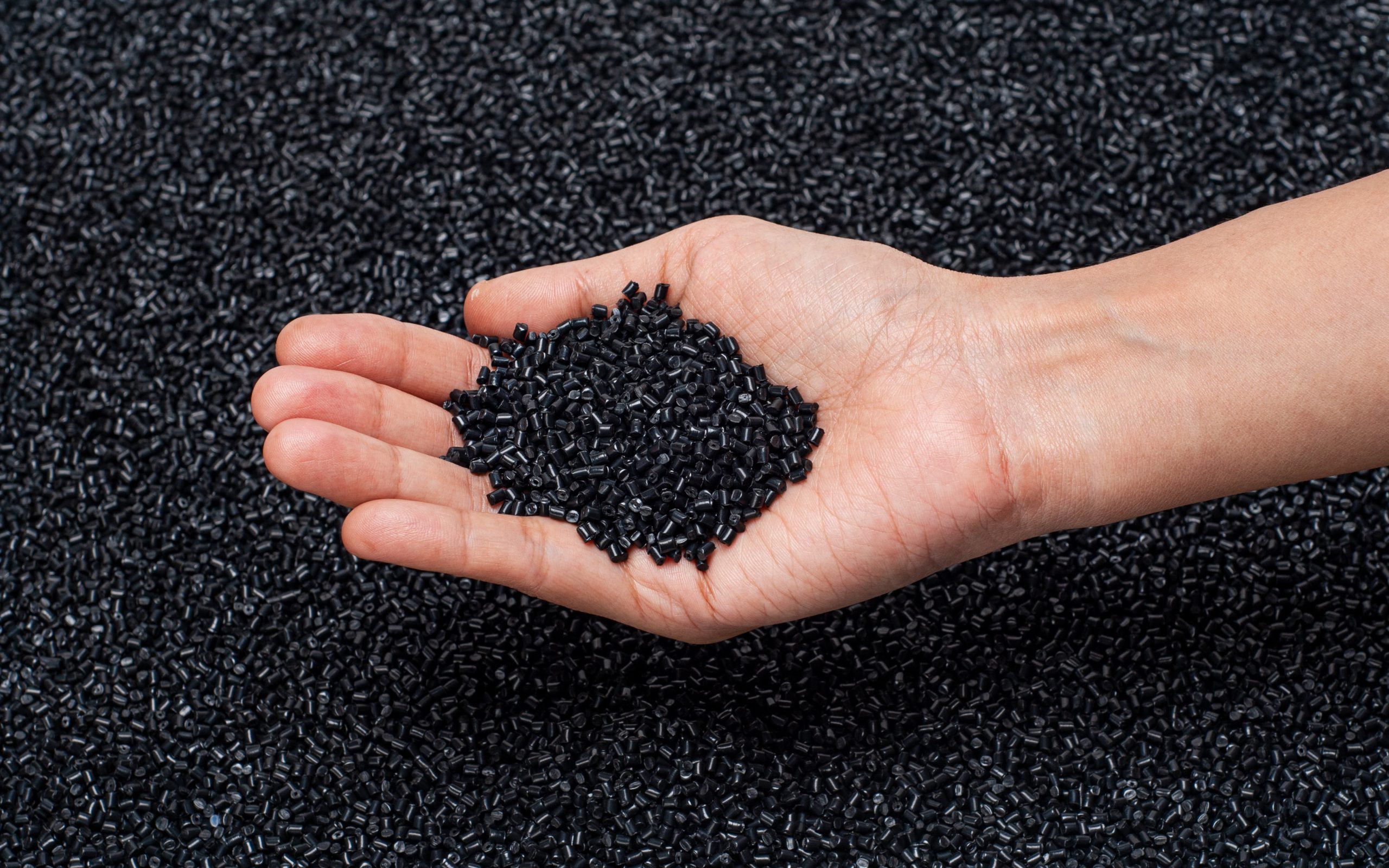
プラスチックポリマー
- メタル
- アルミニウム:航空宇宙産業や自動車産業で広く使用されている軽量素材。
- ステンレススチール:耐食性に優れ、医療機器や食品産業に適しています。
- 銅:電気伝導性に優れ、電子部品によく使われる。
- チタン合金:高強度で軽量、航空宇宙分野で広く使用されている。
- 複合材料
- 炭素繊維複合材料:軽量かつ高強度で、航空宇宙産業や自動車産業で広く使用されている。
- ガラス繊維複合材料:耐腐食性で、建築や造船によく使われる。
- セラミックス
- アルミナ・セラミックス:硬度と耐摩耗性が高く、ナイフや研削工具によく使用される。
- 炭化ケイ素セラミックス:熱伝導率と強度が高く、切削工具や耐火物に適している。
- ジルコニア・セラミックス:優れた靭性と耐クラック性を持ち、医療機器や歯科材料に使用される。
- ガラス
- 普通のガラス:窓や容器に使われる。
- 光学ガラス:レンズや光学機器に使用され、高い透明度と低い不純物が要求される。
- 木材製品
- 無垢材:オーク材、パイン材など、家具や装飾品に適している。
- 複合木材:合板のようなもので、建築や室内装飾によく使われる。
- 半導体
- シリコンウェーハ:極めて高い平坦性と平滑性が要求される電子部品の製造に使用される。
- ガリウムヒ素:光電子工学や高周波用途に使用され、優れた電子特性を持つ。
- 消しゴム
- 天然ゴム:弾力性に富み、各種シールや衝撃吸収材に使用される。
- 合成ゴム:耐摩耗性、耐油性があり、タイヤや工業製品に使用される。
- 発泡ゴム:軽量で防音性に優れ、梱包材や車の内装によく使われる。
- バライト:充填材料およびバリア材料として使用され、石油掘削に広く使用されている。
- 石工
- 花崗岩:強度が高く、耐摩耗性に優れ、建築材や装飾材によく使用される。
- 大理石:美しく、屋内外の装飾に適しているが、柔らかく、着用しやすい。
- セラミックタイル:硬くて耐摩耗性があり、床や壁の装飾に広く使用されている。
- バイオマテリアル
- ポリ乳酸(PLA):医療機器や包装材に使用される生分解性プラスチック。
- ポリヒドロキシアルカノエート(PHA):生体適合性が高く、バイオメディカル用途に適している。
- 天然セルロース:医薬品や食品包装に使用され、生体適合性に優れている。
- 鉱石
- 石英:硬度が高く、ガラス製造や電子産業でよく使用される。
- 長石:重要な原料としてセラミックやガラス産業で使用される。
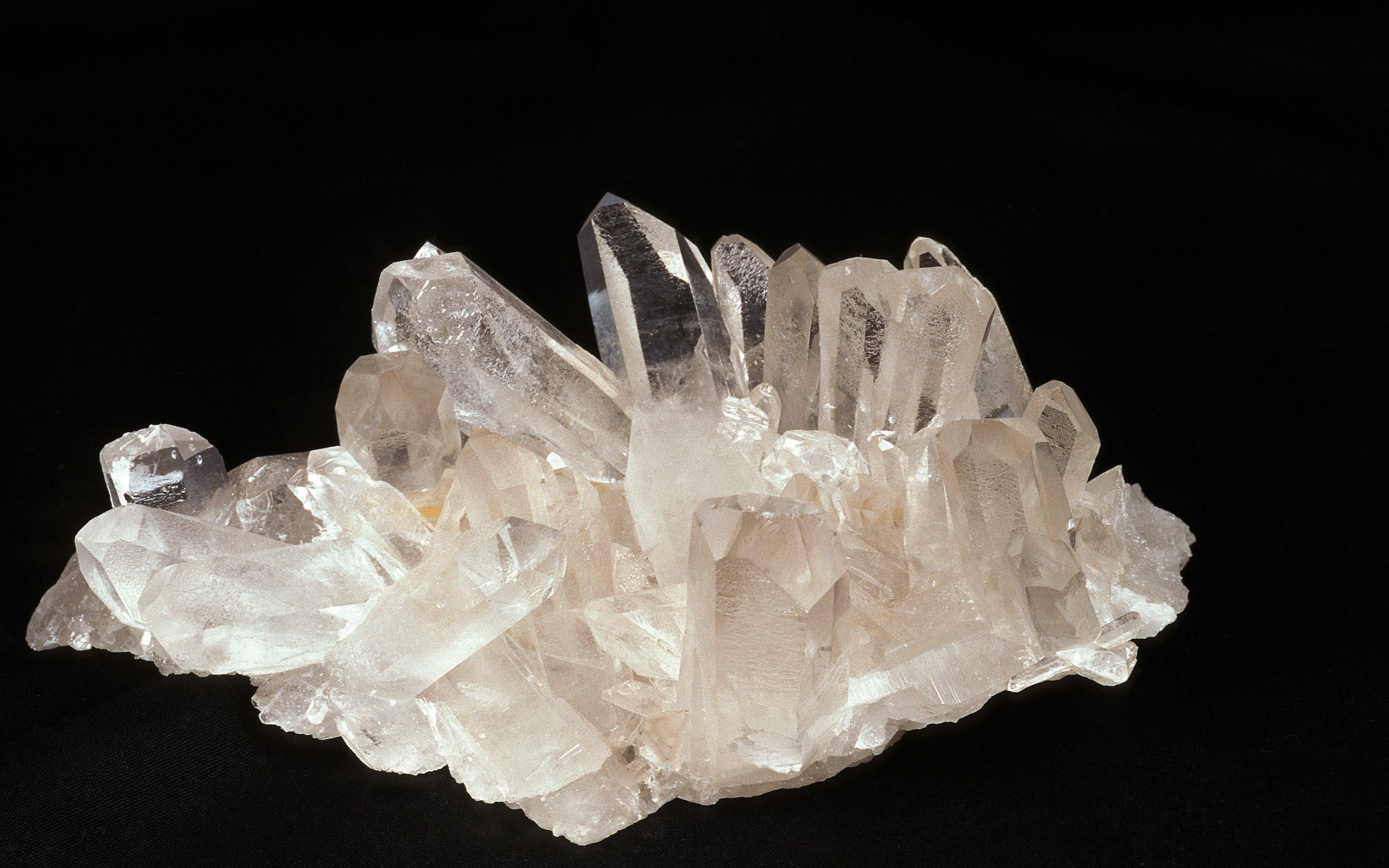
クォーツ
材料の特性と選択方法
特徴
- 硬度:様々な研削材料の硬度は、その適用性を決定する。一般的に、硬度が高いほど適用できる材料の範囲が広くなります。
- 耐摩耗性:プレミアム研削材は、長時間の使用にも研削の形状と性能を維持します。
- 粒子の形状:粒子の形状と分布は研削効果に影響する。規則正しい形状の砥粒は、研削の均一性を向上させることができる。
- 粒子径:粒度が細かいほど研削効果が高く、通常精密加工に使用される。
- 適応性:建設業界における石材や石積みの用途のように、さまざまな素材の適応性は、特定の業界においてより際立ったものとなる。
- 環境保護:持続可能な開発が重視される中、バイオ素材や分解可能な素材が研削盤の人気選択肢となっている。
方法を選択
- 加工材料による選択まず、加工する材料の種類と特性を考慮し、その硬度と靭性に適した研削材を選択する。
- 加工条件を考慮する:要求される表面仕上げと精度の要件に応じて、対応する粒子径と形状を選択する。
- コストを評価する:材料の性能とコストを組み合わせて、費用対効果の高い研削材を選択する。
- 試用とフィードバック:正式生産の前に小規模なトライアルを実施し、実際の結果に基づいて調整を行う。
- 業界の用途に応じて:業界によって研削材に求められるものは異なる。例えば、建設業界では耐摩耗性の高い砥石を使用する傾向があり、一方、生物医学分野では材料の生体適合性が重視される。
- 環境への影響を考慮する:研削材を選ぶ際には、環境保護やリサイクル性を考慮し、環境に優しい材料を選ぶべきである。
研削に使用される機械の種類
研削盤は、研削プロセスを実現するための主要な装置です。多くの種類があり、さまざまな材料やプロセスの要件に適しています。研削盤を選ぶ際には、具体的な加工ニーズに基づいて決定する必要があります。考慮される要素には、工作物の材質、形状、寸法要件、表面処理の精度と仕上げなどがあります。ここでは、一般的な研削盤の種類をご紹介します:
- 平面研削盤
平面研削盤は、金属や他の材料の平らな表面を加工するために使用されます。研削盤と工作物の摩擦によって、平面研削と平滑化を実現する。平面研削盤は通常、高精度の制御システムを備えており、需要の高い精密加工に適している。
- 円筒研削盤
円筒研削盤は、円筒形工作物の外面および内面を加工するために使用される。回転する砥石を介して工作物に接触し、工作物の均一な研削を実現します。円筒研削盤は、機械部品の加工に広く使用されています。
- ベルトグラインダー
ベルトグラインダーは、連続した研削ベルトを研削工具として使用し、平面や曲面の広い面積の加工に適している。ベルトグラインダーは操作が簡単で効率的であり、木材、プラスチック、金属の表面処理によく使用される。
- 縦型グラインダー
立形研削盤は、研削を垂直方向に固定し、ワークを移動させながら研削する装置です。複雑な形状のワークや難加工面に適しており、加工精度を効果的に向上させることができる。
- CNC研削盤
CNC研削盤は、現代の研削技術の代表である。コンピュータプログラムによって研削工程を制御し、高精度・高能率加工を実現する。CNC研削盤は複雑な形状の工作物にも対応でき、航空宇宙、自動車、金型製造などのハイテク産業で広く使用されている。
- 光学研磨機
光学研磨機は主に、極めて高い表面仕上げと精度が要求される光学部品やレンズの製造に使用されます。この装置では、光学製品の品質を確保するために特殊な砥粒と工程を使用します。
- ウェット&ドライ・グラインダー
加工条件の違いにより、研削盤も湿式研削盤と乾式研削盤に分けられる。湿式研削盤は、研削とワークの温度を効果的に低減し、加工効果を向上させることができ、加工中にクーラントを追加します。乾式研削盤は、通常、乾燥した環境で材料を処理するために使用されます。
サンドブラスト材とは何ですか?
定義
サンドブラスト材とは、高速噴射によって被加工物の表面に作用し、洗浄、バリの除去、表面粗さの変化などを実現する材料のこと。一般的なサンドブラスト材料には、ガラスビーズ、石英砂、金属粒子などがある。
Function
サンドブラスト工程は、工作物の表面を洗浄、バリ取り、粗面化、または微細に研磨するために使用されます。酸化皮膜、汚れ、表面の残留物を除去し、表面に特定のテクスチャや粗さを形成して材料の接着性を向上させることができます。コーティングやメッキの前の表面処理などの特性。
Examples of sandblasting materials
- 石英の砂: 石英砂は、サンドブラストで最も一般的に使用される材料の1つです。安価で、粒子が均一で、ほとんどの金属および非金属材料の表面洗浄に適しています。
- ガラスビーズ: ガラスビーズブラストは通常、微細研磨に使用され、アルミニウム、ステンレス鋼などの仕上げに適しており、加工物の表面を滑らかでつや消しにします。
- スチールショットとスチールグリット: スチールショットとスチールグリットは、高負荷のサンドブラスト工程でよく使用されます。これらは、錆、酸化スケール、または広範囲の汚れを効果的に除去でき、高強度の表面処理が必要な金属部品に適しています。
- プラスチックだ: プラスチック・メディア、ナイロン・サンド、凍結砂など、特に高精度で複雑な形状の部品のバリ取りが得意で、柔らかいワークピースに適している。
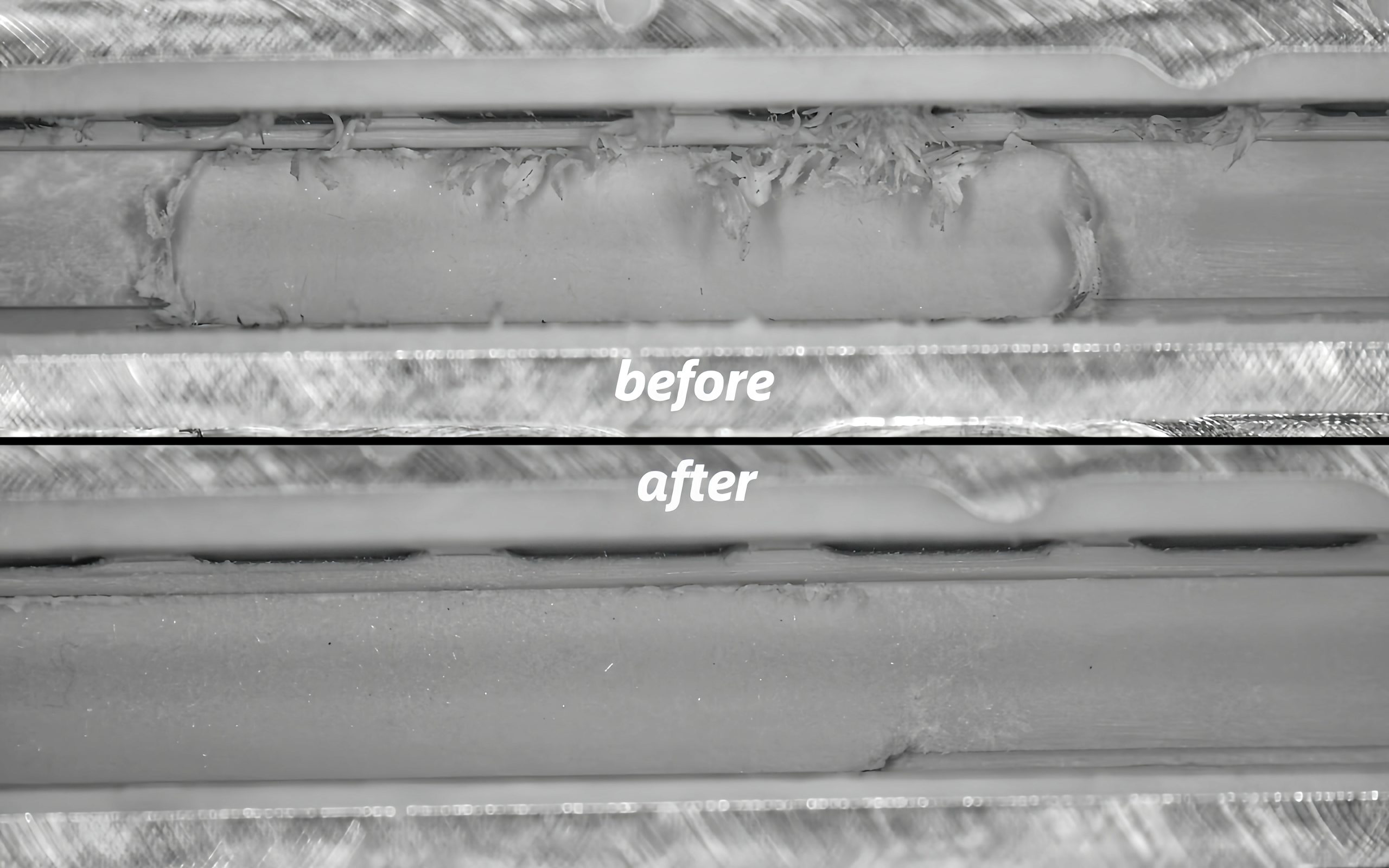
バリ取り前後のHLHポリスチレンデフラッシングビーズ
サンドブラスト材料の選択は通常、ワークピースの材料、希望する表面効果、およびプロセス要件に基づいて決定される。硬い金属の処理には硬いスチールグリットが適しており、微細な処理にはガラスビーズとセラミック粒子が適しています。
共通点と相違点
コネクションだ: 研削とサンドブラストはどちらも研削材を使用して工作物に表面処理を施すため、その用途には重なる部分があると言える。どちらも表面の洗浄、研磨、粗面化に使用できます。ある種の研削材料(酸化アルミニウム、炭化ケイ素など)はサンドブラスト材料としても使用できるため、2つのプロセス間の材料選択には重複があります。サンドブラスト材料は研削材料の一部と考えることができますが、すべての研削材料がサンドブラスト材料というわけではありません。
違いだ: 主な違いは、プロセスの順序と適用シナリオに反映されます。一般的に、研削はサンドブラストの前の前処理工程であり、特に大面積の欠陥、凹凸のある表面、大量の汚れを除去する必要がある場合に行われる。研削は、大面積の表面修正と基本的なサンディングにより注意を払い、サンドブラストは細部の精製により注意を払います。
- 研削材は一般に粗い。 で、主に初期段階の大面積処理に使用される。その機能は、不純物、スケール、油汚れなどの大きな粒子を除去することである。通常、サンドブラストや塗装工程に適した表面を整えるため、機械加工の前に行う予備工程である。
- サンドブラストの材料はより洗練されている サンドブラストは、微小なバリや微細な欠陥を除去し、表面に所望の質感や粗さを与えるために使用されます。サンドブラストはミクロン単位の表面調整に対応でき、特に最終表面処理段階での使用に適しています。
例えば、自動車の製造工程では、溶接や金型の製造が完了した後、最初に粗い研削材で車体を洗浄し、その後、研磨やその後の準備など、より細かい表面処理の要求を達成するためにサンドブラスト処理を行う必要がある場合がある。
研削とサンドブラストにはそれぞれ固有の役割と機能がありますが、表面処理工程ではこの2つが補完し合うことがよくあります。この2つの工程を合理的に選択し組み合わせることで、製品の表面品質と性能を大幅に向上させることができます。
研削およびブラスト材料は、現代の製造および表面処理工程で重要な役割を果たしています。研削材は表面を粗くし、下地を整えるために使用され、サンドブラスト材は表面の細部と品質をさらに向上させます。両者の材料特性、適用シナリオ、プロセス特性を理解することで、お客様はニーズに合った処理ソリューションをより適切に選択し、製品の最終品質が期待に沿うようにすることができます。
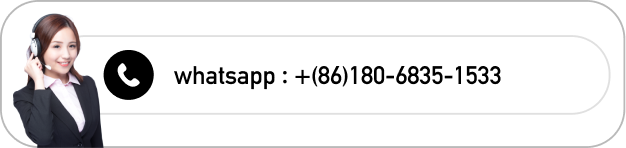