表面仕上げ加工 包括的な概要
11月 7, 2024
表面仕上げは、多くの産業において不可欠なプロセスである。その主な目的は、材料や製品の外観、機能、耐久性などの表面品質を向上させることです。自動車業界、航空業界、建築装飾業界、家電業界を問わず、表面仕上げは微細な加工を施すことで、さまざまな応用シーンにより良いソリューションを提供し、製品の価値を大きく高めることができます。
表面仕上げ加工の種類
表面仕上げには様々な工程があり、それぞれに固有の特性、利点、欠点、適用可能な場面がある。一般的な仕上げ加工には、機械研磨、電気メッキ、サンドブラスト、化学処理、熱処理などがある。以下は、いくつかの主要な仕上げ加工について簡単に分析したものである:
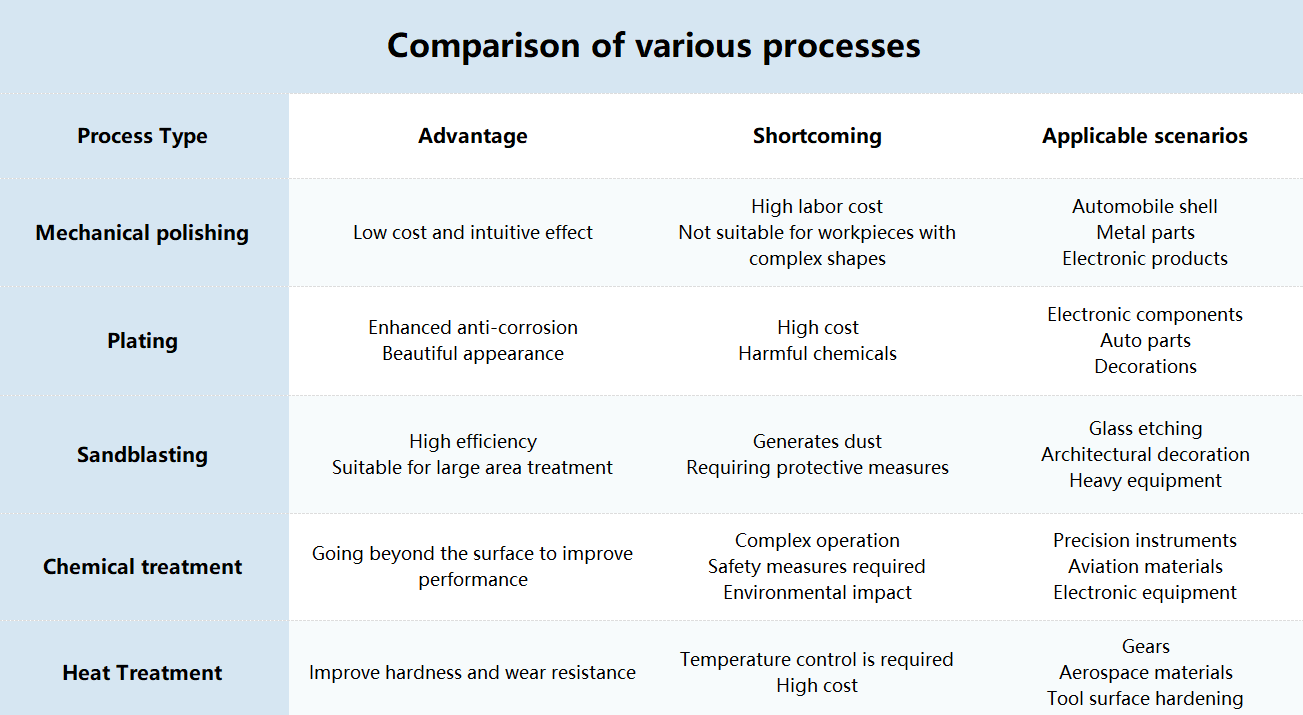
- 機械研磨
- 定義 研磨剤、サンドペーパーなどによる材料表面の物理的な摩擦により、滑らかな表面効果を得ること。
- メリット 低コストで直感的な効果。金属、プラスチック、ガラスなど、さまざまな素材に適している。
- デメリット 人件費が高く、広い面積や複雑な形状のワークには適さない。
- 適用されるシナリオ 自動車シェルの研磨、金属部品の修正、エレクトロニクス製品の外観仕上げ。
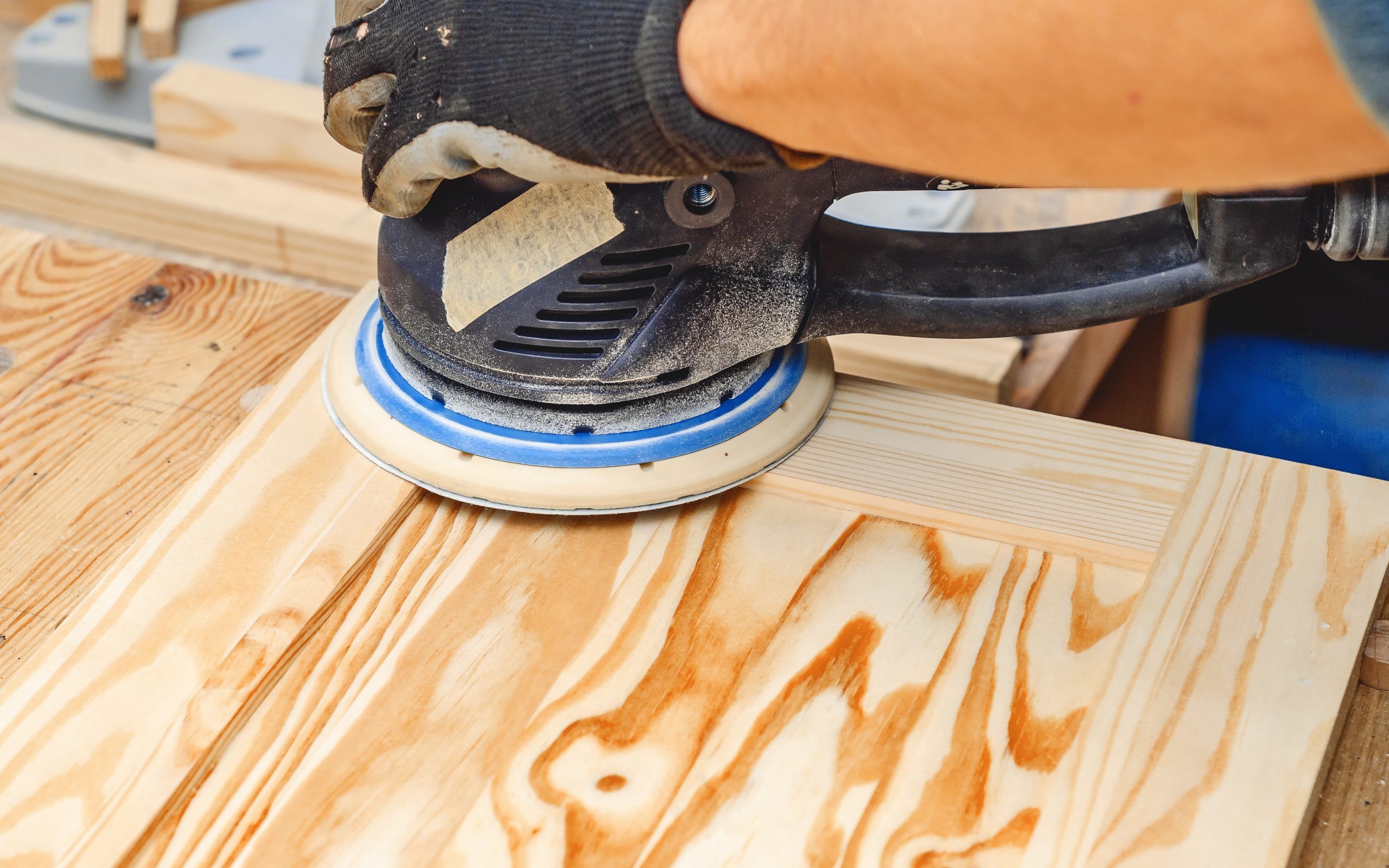
機械研磨
- 電気めっき
- 定義 材料の表面に電解反応によって金属膜を析出させ、材料の耐食性や美観を向上させること。
- メリット 金属の耐食性と美観を大幅に向上させることができる。
- デメリット コストが高く、処理過程には有害な化学薬品が使用され、専門的な操作が必要である。
- 適用されるシナリオ 電子部品の防錆処理、自動車部品の表面改質、高級装飾品の加工。
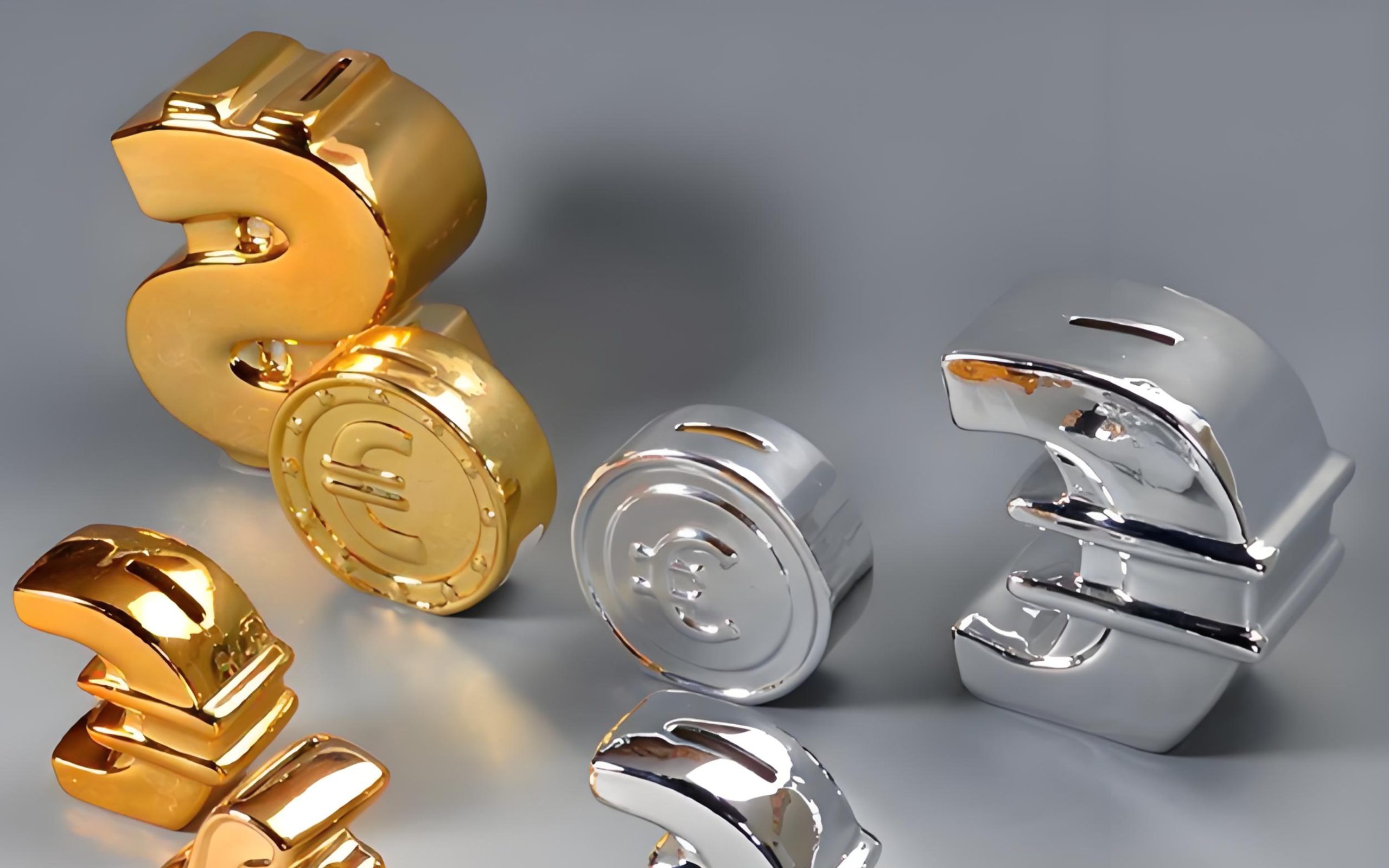
電気メッキ製品
- サンドブラスト
- 定義 砥粒を高速で噴射して材料の表面を研磨し、酸化膜や汚れを除去したり、均一な表面形状を形成したりすること。
- メリット 効率的で速く、さまざまな材料に適しており、大面積処理に最適。
- デメリット 材料によっては粉塵が発生するため、保護措置を講じる必要がある。閉鎖環境での運転に適しています。
- 適用されるシナリオ ガラスエッチング、建築装飾材加工、重工業設備の表面洗浄。
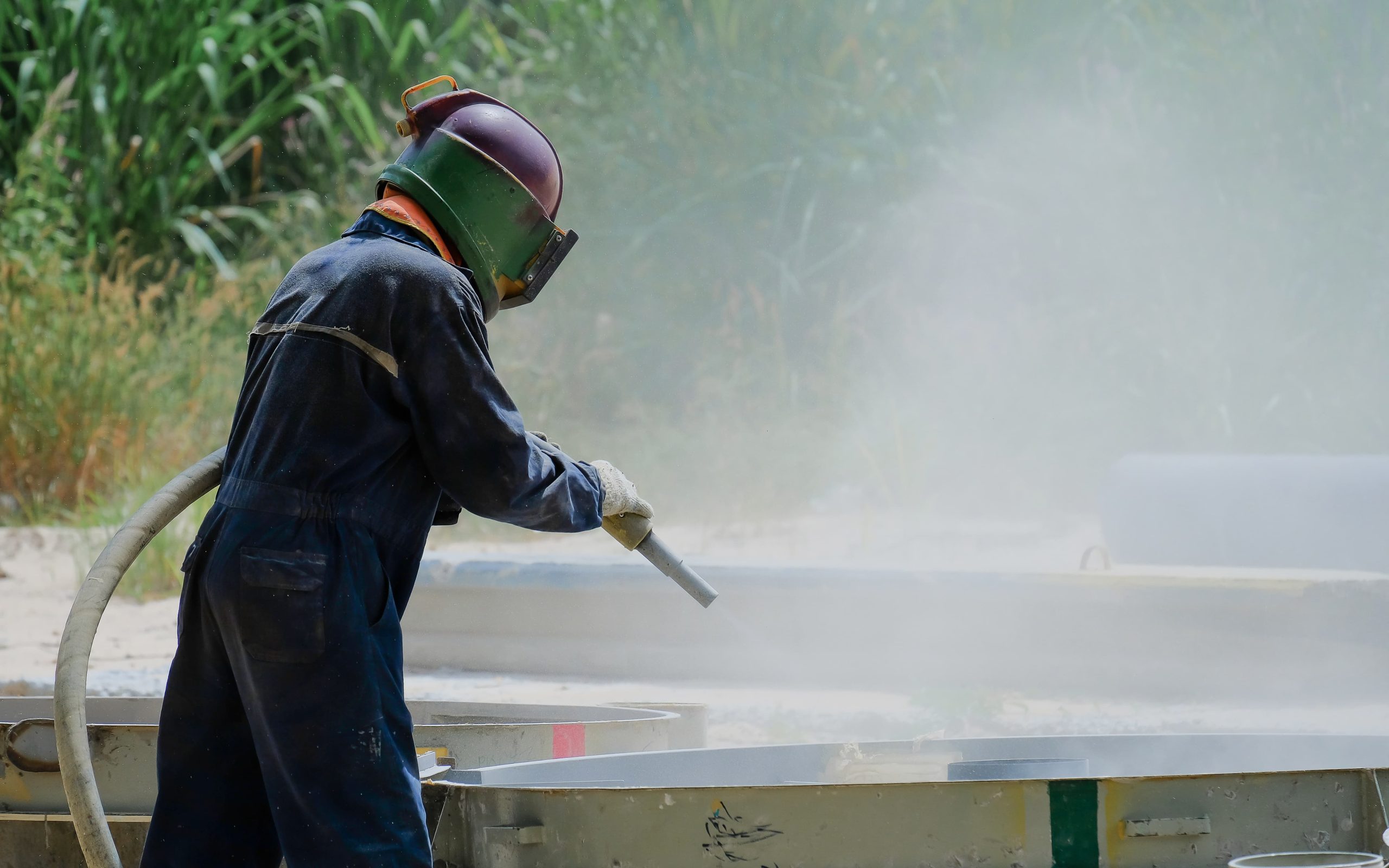
サンドブラスト実演
- 化学処理
- 定義:化学反応によって材料表面の酸化物や不純物を除去したり、表面に保護膜を形成すること。
- メリット 材料の表面に浸透し、表面性能を向上させることができる。複雑な形状の工作物に適している。
- デメリット 作業には化学的知識と厳重な安全対策が必要であり、不適切な取り扱いは環境に影響を与える可能性がある。
- 適用されるシナリオ 精密機器部品の表面処理、航空宇宙材料の防錆処理、電子機器の表面処理。
- 熱処理
- 定義 加熱や冷却などの熱サイクルプロセスにより、材料の表面または全体の硬度や靭性などの物理的特性を変化させること。
- メリット 材料の表面硬度を向上させ、耐摩耗性と耐衝撃性を高める。
- デメリット 温度と冷却速度を制御する必要があり、コストが比較的高く、主に金属に適用される。
- 適用されるシナリオ 歯車などの機械部品の強化処理、航空材料の構造強化、工具の表面硬化処理など。
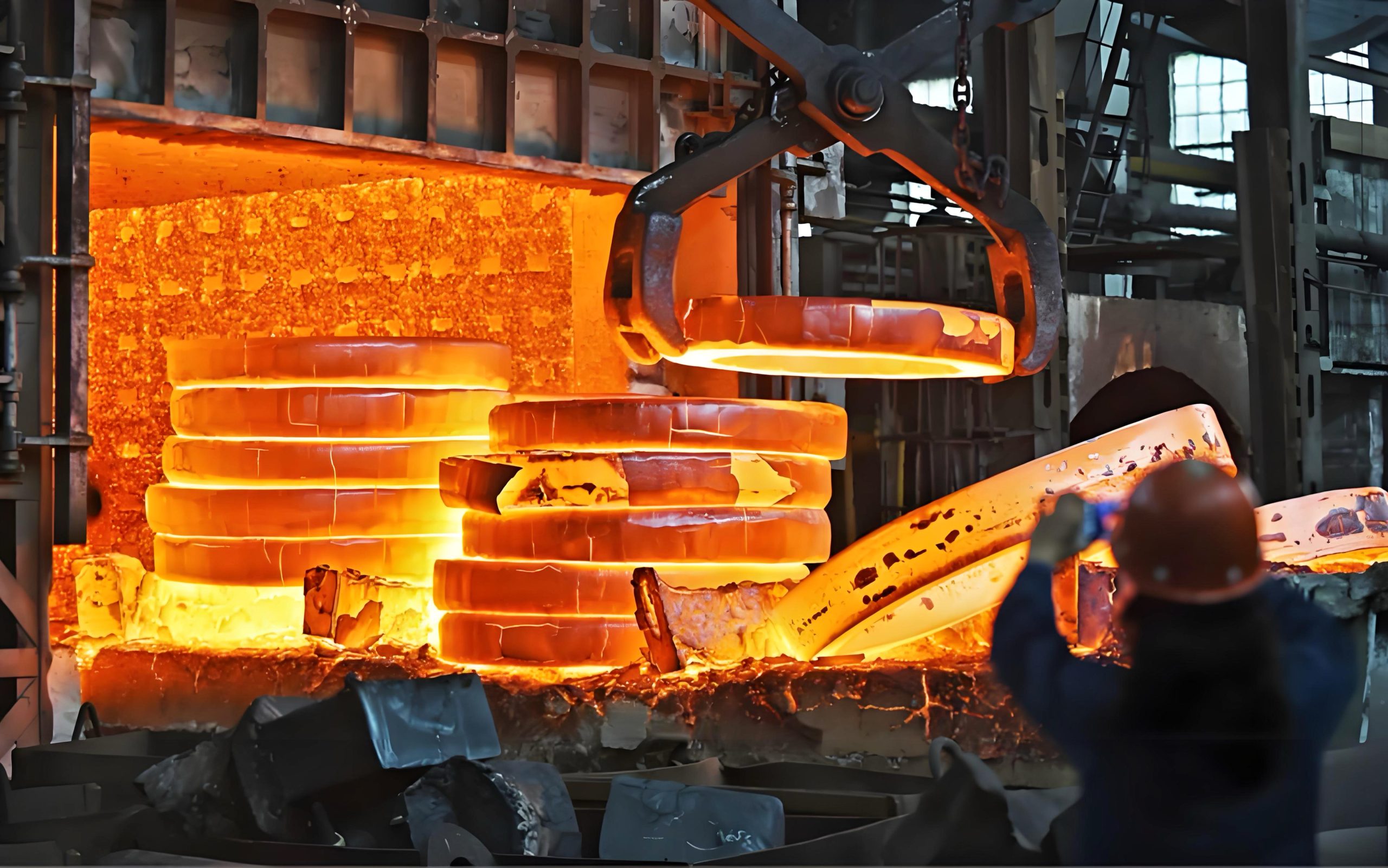
熱処理
表面仕上げ効果に影響する要因
表面仕上げの品質と効果は、材料の選択から工程実行の細部に至るまで、多くの要因に影響され、最終結果に大きな影響を与える。以下では、これらの影響要因について、材料、工程、環境条件、要求精度の4つの側面から詳しく説明する。
- 材料特性
表面仕上げを行う際、素材によって異なる反応を示す。金属、セラミックス、ガラス、プラスチックは硬度、熱伝導率、化学的性質が異なるため、適切なプロセスを選択する必要がある。
- 硬度と耐摩耗性: 例えば、硬い金属はより強い研削材を必要とし、柔らかい金属は過研磨や表面の凹凸の影響を受けやすい。
- 熱伝導率: 熱処理中、材料の熱伝導率が冷却速度を決定し、それが表面仕上げに影響する。
- 化学反応性: 反応性金属の場合、化学エッチングでは、過度の腐食を避けるために特別な防腐剤とプロセスパラメーターを使用する必要がある。
- プロセスパラメーター
仕上げ加工のパラメータ設定は、表面処理の精度と効果に直接影響する。一般的な影響因子には、研削速度、圧力、加工時間などがあります。
- 研削速度: ポリッシングやサンドブラストでは、回転数が高すぎると表面が粗くなり、低すぎると効率に影響します。
- 圧力をかける: 例えば、サンドブラストの場合、圧力が高すぎると材料が損傷する可能性があり、圧力が低すぎると処理が不完全になる可能性がある。
- プロセス時間: 通常、研磨やエッチングの時間を長くすると仕上がりはよくなるが、材料が失われることもあるので、時間を厳密に管理する必要がある。
- 環境条件
表面仕上げは環境条件に対して厳しい要求があり、温度や湿度などの環境要因は加工効果に影響する。
- 温度だ: 熱処理や化学処理の工程は温度に非常に敏感である。温度が高すぎても低すぎても、表面に欠陥が生じる可能性がある。
- 湿度: 高湿度環境は酸化反応を促進し、金属表面の平滑な処理には適さない。特にケミカルエッチングでは、防湿に特に注意を払う必要がある。
- 清潔さ: 空気中のほこりや不純物がワークの表面に付着し、処理効果が低下する可能性がある。そのため、仕上げ工程では環境の清浄度を確保する必要がある。
- 精度と公差の要件
用途が異なれば、表面精度と公差に対する要求も異なる。仕上げ加工では、特定の用途に応じてプロセスパラメータを調整する必要があります。
- 仕上げの条件: 航空宇宙部品や医療機器などの精密部品では、表面仕上げの要求が非常に高く、わずかな粗さの違いでも機能性に影響を及ぼす可能性がある。
- 耐性コントロール: 加工中の公差を管理することは、部品組立の精度を保証する鍵です。同じバッチであっても、各部品は厳しい公差要件を満たすために特定の工程調整が必要になる場合があります。
表面仕上げの適用場面
表面仕上げは、複数の産業、特に自動車製造、建築装飾、航空宇宙、民生用電子機器において幅広い用途がある。以下は、各用途シナリオの詳細な分析であり、さまざまな産業における表面仕上げ技術がもたらす需要のペインポイント、直面する課題、ソリューションについて詳述している。
- 自動車製造
- 業界の需要 自動車製造業界では、主に車体や部品の美しさや耐久性を向上させるために表面仕上げが行われている。車体には滑らかな外観が、エンジンやトランスミッションなどの部品には耐食性や耐摩耗性が求められます。
- よくあるペインポイント 車体塗装後の表面の凹凸、部品の摩耗による性能低下、過酷な環境下での金属部品の腐食。
- 仕上げ工程: 機械研磨とサンドブラストは通常、表面をより光沢のあるものにするために使用される。部品の耐食性や硬度を向上させるためには、電気めっきや熱処理技術が用いられる。
- 典型的なケースだ: 一部の高級車ブランドでは、多層サンドブラストと研磨を組み合わせて使用することで、さまざまな光の条件下で車体が均一な光沢効果を発揮し、視覚的なインパクトを高めている。
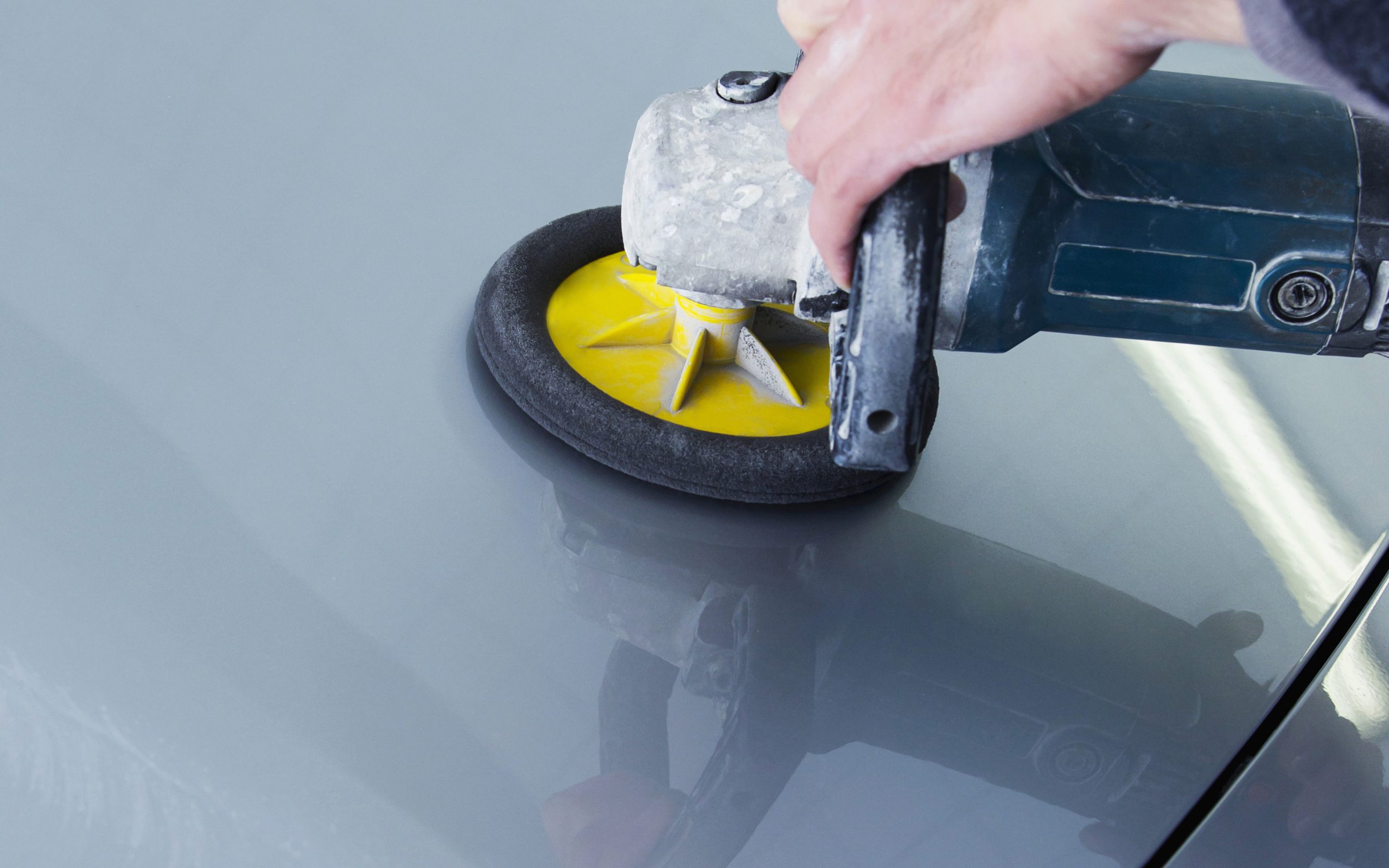
機械的に磨かれる車
- 建物の装飾
- 業界の需要 建築装飾業界では、金属、ガラス、大理石などの表面仕上げ技術を広く使用し、構造物の装飾性と耐久性を高めている。
- よくあるペインポイント 外壁材は長期間の日差しや雨で腐食しやすく、高層ビルのガラス材は耐風圧性を向上させる必要があり、内装材は汚れに強いものが求められる。
- 仕上げ工程: サンドブラストと化学処理技術は、質感を高めたり耐候性を高めたりするために、建築装飾材料の表面に広く使用されている。機械研磨は、大理石などの装飾石の表面処理に使用され、平滑性と美的効果を与えることができる。
- 典型的なケースだ: 近代的な建物の多くは、金属外壁の装飾にサンドブラストやエッチング加工を施し、独特のテクスチャー効果を生み出している。
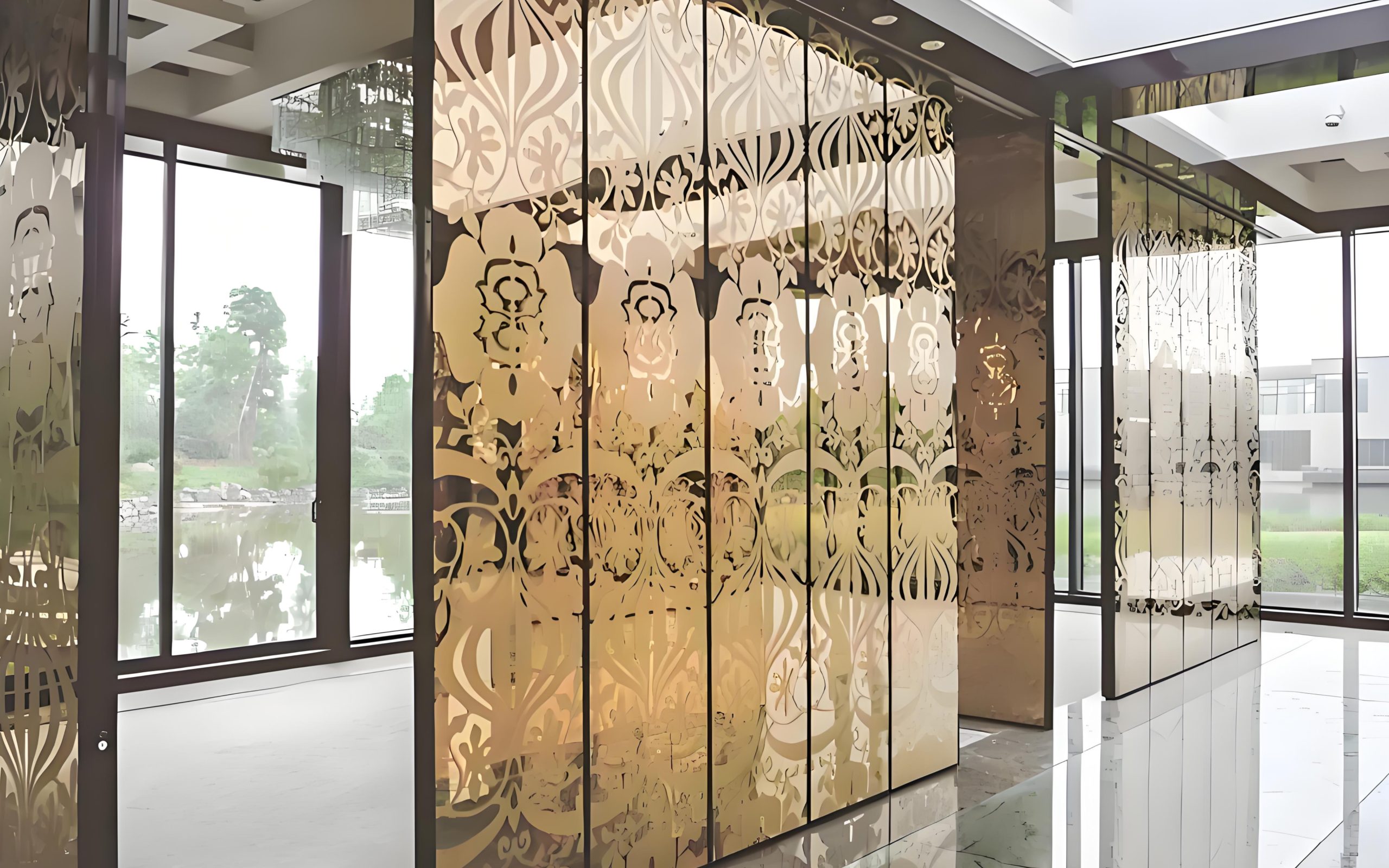
エッチング・ガラス・パーティション
- 航空宇宙
- 業界の需要 航空宇宙産業の材料は、非常に高い耐食性と耐摩耗性が要求され、表面仕上げは部品の寿命を延ばし、メンテナンスコストを削減するために使用されます。
- よくあるペインポイント 航空機のシェルは高高度の過酷な条件下で酸化・腐食しやすく、エンジン部品は高温で摩耗しやすく、ボディ金属は強風や圧力に耐える必要がある。
- 仕上げ工程: 熱処理と化学処理は、材料の硬度と高温耐性を向上させることができる主な表面仕上げ方法です。また、サンドブラストは表面の不純物を除去し、耐食性を向上させることができる。
- 典型的なケースだ: ボーイングは、航空機エンジン部品の表面処理に特殊な化学ニッケルめっきプロセスを使用しており、これにより耐食性が向上し、部品の耐用年数が延びます。
- 家電製品
- 業界の需要 消費者向け電子製品の外観や感触は、ユーザーの体験に大きな影響を与えるため、仕上げ加工は電子機器の筐体、ボタン、内部部品に広く使用されている。
- よくあるペインポイント 筐体には傷がつきやすく、部品は湿気で腐食しやすく、プラスチック筐体の光沢にはムラがある。
- 仕上げ工程: 機械研磨は金属ハウジングに光沢感を与えることができ、サンドブラストはプラスチックや金属ハウジングの手触りや耐摩耗性を高めるために使用され、化学処理はプラスチックの耐紫外線性を高めるために使用される。
- 典型的なケースだ: アップル製品の筐体には、アルマイト処理やサンドブラスト処理など複数の表面仕上げ技術が採用されており、手触りと外観の両方に優れた製品となっている。
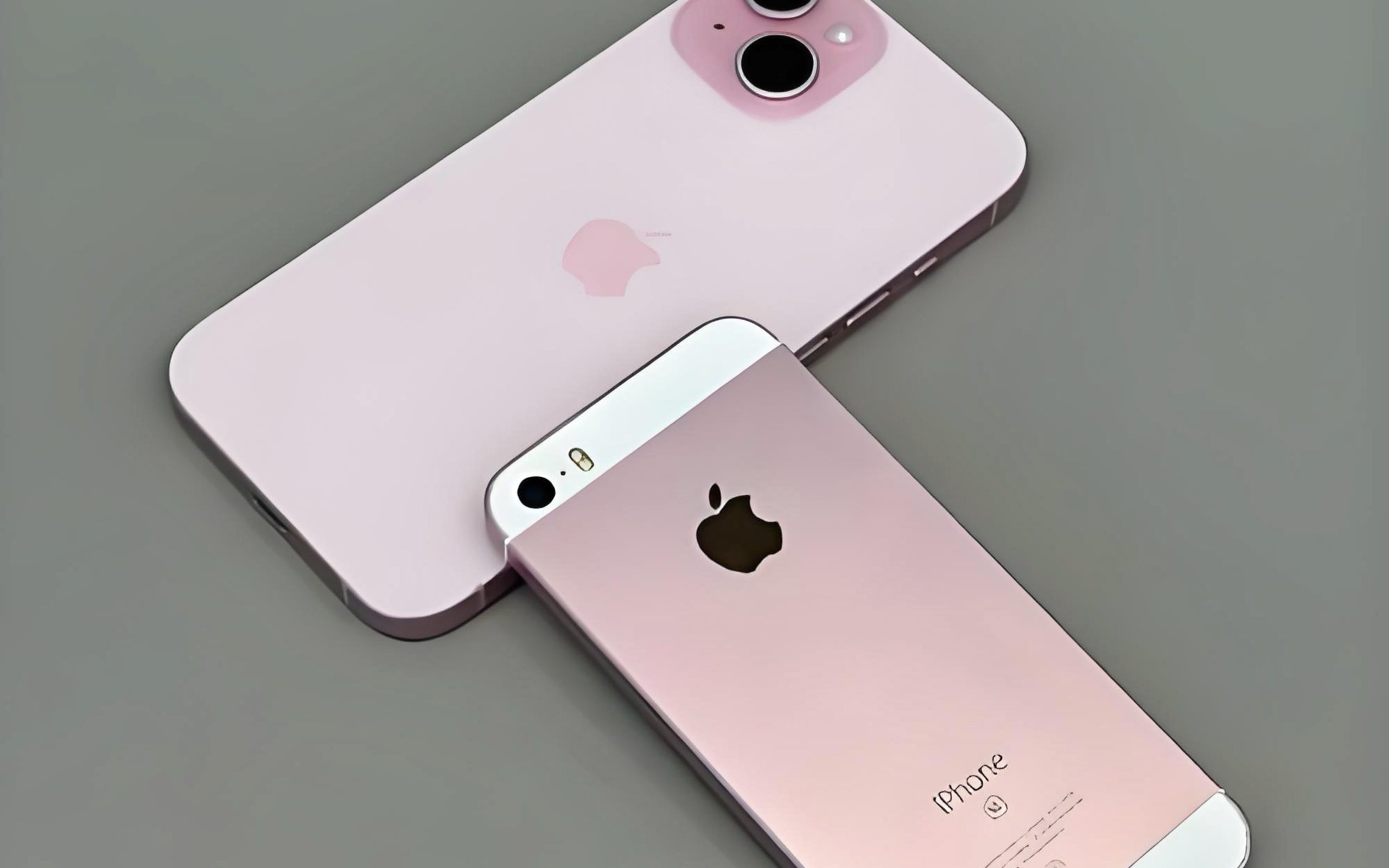
携帯電話筐体の陽極酸化処理
サンドブラスト媒体および装置
表面仕上げ工程では、サンドブラストは、ワークピースの表面品質を効果的に向上させ、さまざまな仕上げ要件を満たすことができる広く使用されている技術です。効率的で高品質の表面処理を保証するには、適切なサンドブラスト媒体と装置を選択することが不可欠です。以下では、一般的に使用されるいくつかのサンドブラスト媒体とその適用場面を紹介し、適切なサンドブラスト装置を推奨します。
推奨サンドブラスト媒体
- ガラスビーズ
ガラスビーズはその滑らかな粒子形状のため、加工時に表面に傷をつけることが少なく、均一な艶消し効果が得られるため、表面の仕上がりが大幅に向上する。
金属やガラスの精密研磨と表面クリーニングに適しており、通常、より高い仕上げが要求される装飾ワークに使用される。
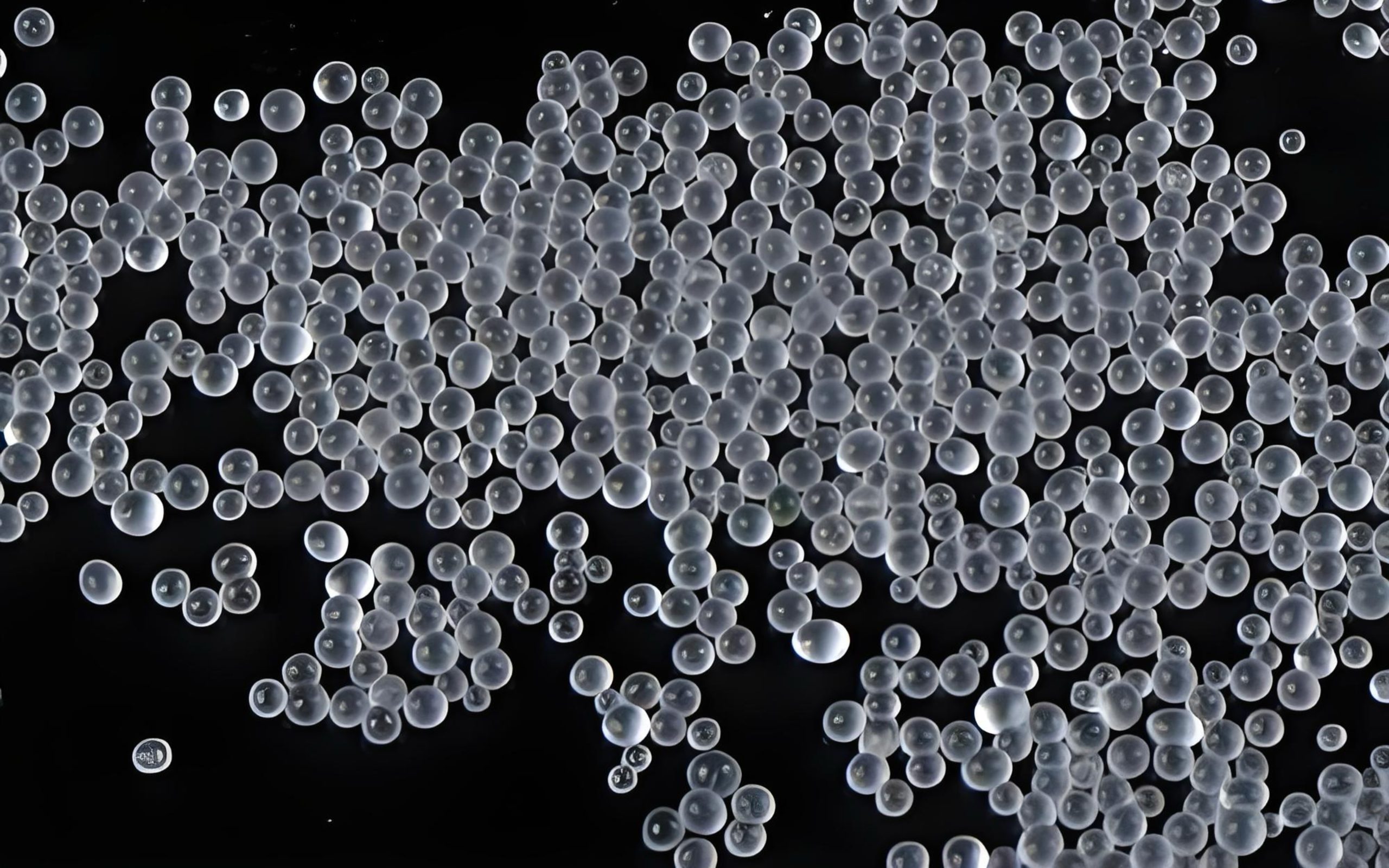
ガラスビーズ
- アルミナ
アルミナは高い硬度と切削力を持ち、表面の欠陥を素早く除去でき、良好な粗さが得られるため、特にその後のコーティングや接着工程に適している。
高硬度金属、セラミックス、石材の表面粗面化、特に酸化被膜や重汚れの除去が必要なワークピースの粗面化に適している。
アルミナブラスト媒体
- 炭化ケイ素
炭化ケイ素は非常に高い硬度と強い切削力を持つ。硬い材料の表面の汚れや欠陥を効果的に除去することができ、コーティング前の前処理によく使用されます。
主にセラミック、炭素繊維、一部の金属の深部除染と粗面化に使用。
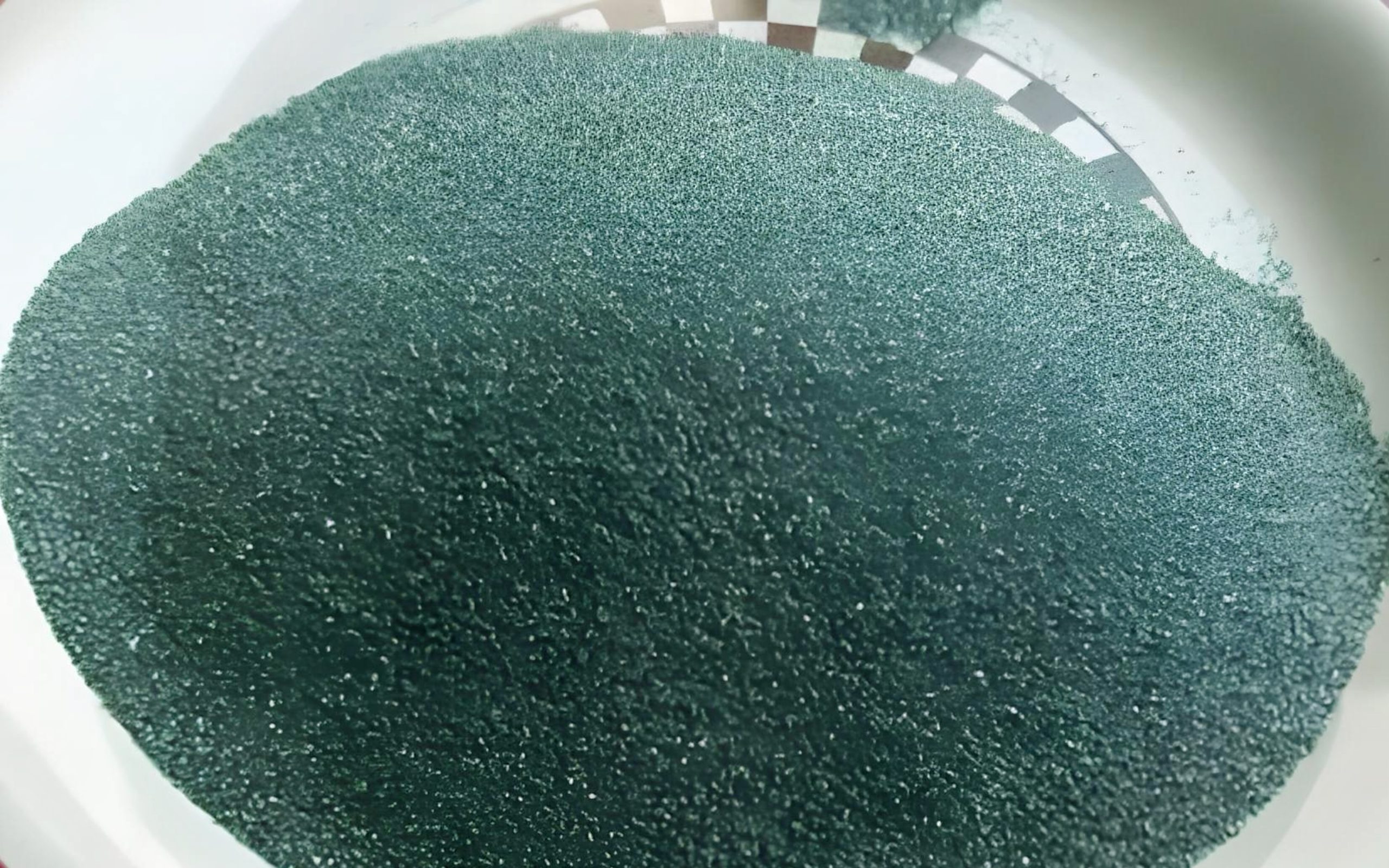
炭化ケイ素
- セラミック・ビーズ
セラミックビーズは硬度が高く、耐摩耗性が強い。重圧サンドブラストに適しており、微細な傷を減らし、均一な艶消し表面を形成することができます。
高い耐摩耗性が要求され、平滑性を維持する必要がある表面処理に適しており、精密機械や航空部品の平面研削によく使用される。
- プラスチックメディア
プラスチックサンドブラスト媒体は、その柔らかい材料の特性により、ワークピースの表面に硬い傷をほとんど付けず、微細な表面処理に適している。
アルミニウム合金やプラスチック部品などの柔らかい素材の表面処理に使用され、特に表面へのダメージが許されないシーンで使用される。
推奨サンドブラスト装置
- 圧入サンドブラスト機
- 特徴 圧入サンドブラスト機の圧力調整範囲は大きく、様々な硬度の材料を処理するのに適しており、特に高精度と高効率を必要とするサンドブラスト工程で広く使用されている。
- 適用メディア: ガラスビーズ、セラミックビーズ、酸化アルミニウムなど
- 吸引式サンドブラスト機
- 特徴 簡単な操作で、軽量な表面処理のニーズ、特に小さな部品の洗浄と研磨に適しています。
- 適用メディア: ガラスビーズ、プラスチックメディア。
- 湿式サンドブラスト機
- 特徴 ウォーターミストと研磨剤の混合物を使用し、粉塵のない環境での作業に適しており、主に高精度で傷のない表面が要求されるワーク加工に使用される。
- 適用メディア: ガラスビーズ、酸化アルミニウム
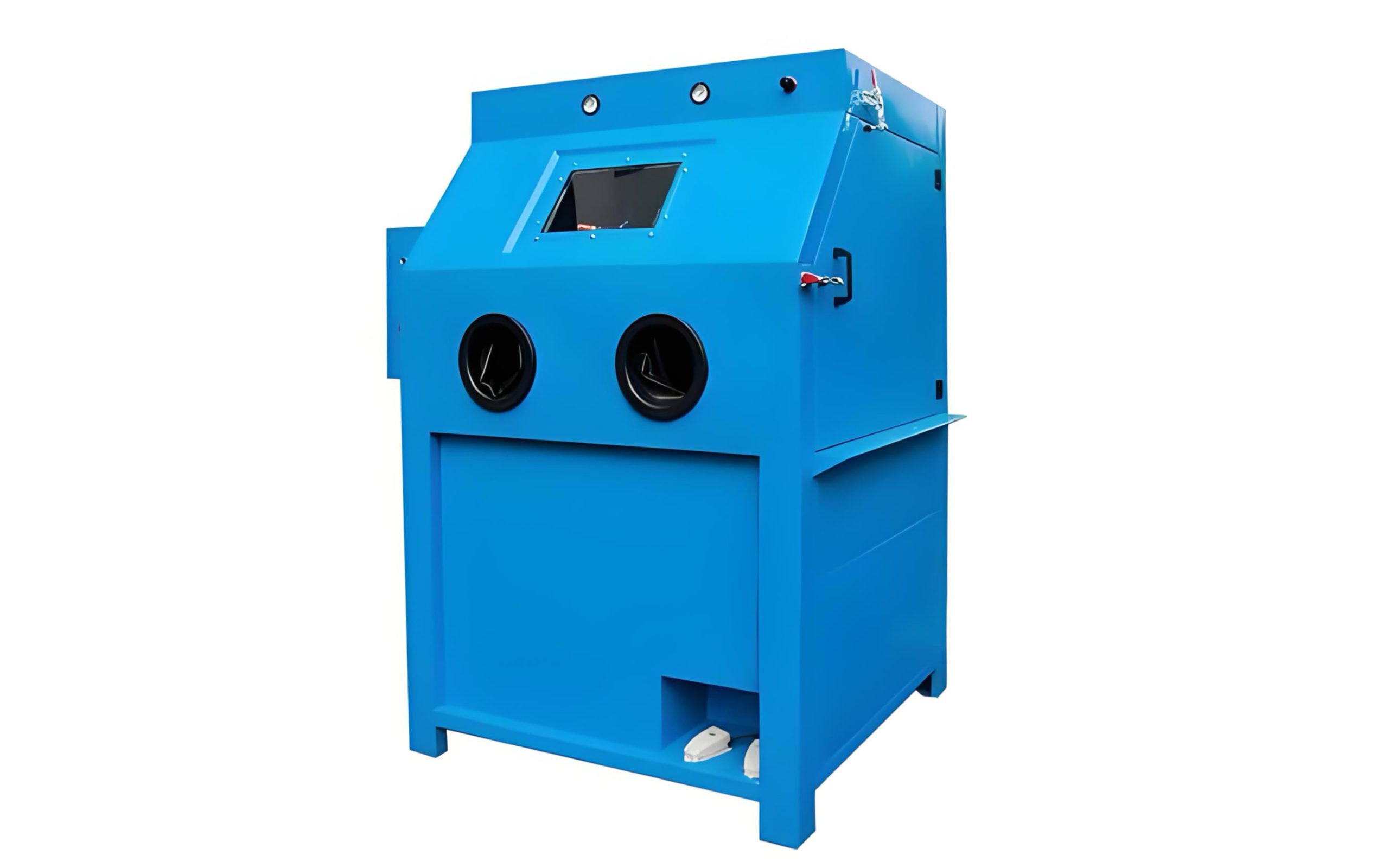
湿式サンドブラスト機
- 移動式サンドブラスト機
- 特徴 移動や操作が簡単で、大型のワークや、屋外の大型建築部材の表面処理など、固定した場所での作業が難しいシーンに適している。
- 適用メディア: 酸化アルミニウム、炭化ケイ素。
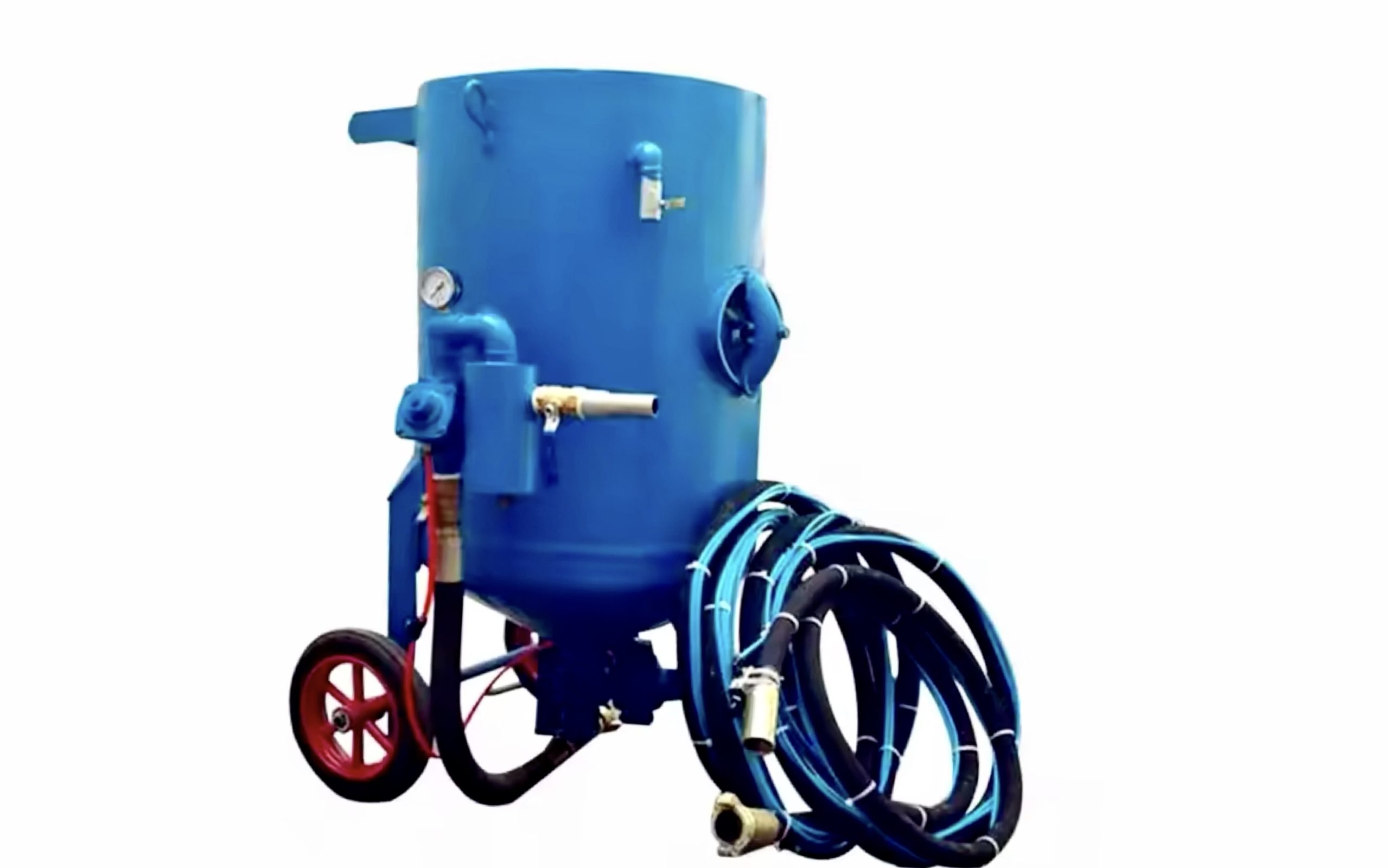
移動式サンドブラスト機
正しいメディアと機材の選び方
表面仕上げにおけるメディアと装置の選択は、ワークの材質、要求される仕上げ、加工目標に基づいて総合的に評価する必要がある。硬い材料や表面の粗面化の場合は、酸化アルミニウムや炭化ケイ素のような硬度の高いメディアを選択するのが適切である。仕上げおよび表面損傷の要求が高いワークピースの場合、ガラスビーズおよびセラミックビーズ サンドブラスト媒体を湿式サンドブラスト機と組み合わせると、より理想的な表面効果が得られる。
よくある質問と解決策(Q&A)
Q: より環境に優しく、より安全な表面処理工程は?
A: 湿式サンドブラスト、レーザーマーキング、電解研磨は比較的環境に優しい。湿式サンドブラストはウォーターミストによって粉塵を低減し、レーザーマーキングは化学媒体を必要とせず、電解研磨は有害物質を使用しない。これらのプロセスを選択すれば、環境汚染や操業上のリスクを最小限に抑えることができます。
Q: ワークピースに適した表面仕上げ方法を選ぶには?
A: ワークピースの材質、目標とする表面効果、経済性などの要因を考慮する必要がある。仕上げに対する要求が高いワークピースには、研磨または電解研磨を選択することができます。表面粗さに対する特別な要求があるワークピースには、サンドブラストやレーザーエッチングの方が適している場合があります。
Q: 金属表面の酸化を抑えるには?
A: 金属を酸化防止コーティングで処理し、適切な研磨工程を選択し、防錆油を使用する。電解研磨は酸化膜を効果的に除去し、平滑な表面を形成して酸化の発生を抑えることができる。
Q: 化学治療における安全上の注意点は?
A: 作業者は適切な保護衣、手袋、眼鏡などを着用し、換気の良い環境で作業すること。酸洗などの工程では、化学物質の使用規定を厳守し、化学物質の漏出や人体への接触が予想される場合には、十分な緊急措置を講じること。
Q: 表面処理中の不均一な影響を避けるには?
A: 表面処理の均一性は、プロセスパラメーター、オペレーターのスキル、装置の安定性など、複数の要因に影響される。適切な装置とプロセスパラメーターを選択し、装置を定期的にメンテナンスすることで、表面の不均一な影響を効果的に回避することができます。
Q: サンドブラスト、研磨、化学処理の違いは何ですか?
A: サンドブラストは表面酸化物の除去や粗い表面の処理に適しており、研磨は表面仕上げの改善に使用される。化学処理(酸洗など)は、主に金属表面の汚染物質や酸化層を除去するために使用される。各工程の選択は、ワークピースの要件と工程特性に基づいて決定されるべきである。
Q: 表面仕上げ後のワークの表面処理は?
A: 処理されたワークピースは通常、さらなる保護が必要となる。金属表面の場合は、保護層(防錆油など)を塗布することができるが、ガラスやプラスチックのような素材は、表面効果の耐久性を維持するために、加熱や研磨が必要になる場合がある。
Q: 表面処理の一貫性を確保するには?
A: 一貫性を確保するためには、プロセスパラメーター(圧力、温度、処理時間など)を厳密に管理し、人為的ミスを減らすために自動化された機器を使用しなければならない。さらに、各処理の標準化を確実にするため、工程検査が定期的に行われる。
Q: なぜ塗装前に表面処理が必要なのですか?
A: 表面処理は、不純物、酸化物、汚染物質を除去し、ワークの表面をより滑らかできれいにし、塗膜の密着性と耐久性を高めます。金属ワークピースの場合、表面処理は塗装の性能と寿命を確保するために塗装前に必要なステップです。
Q: 化学処理された表面は人体に有害か?
A: 化学処理(酸洗やリン酸塩処理など)の際には、安全性を考慮する必要がある。合理的な操作と環境にやさしい化学物質の使用により、健康リスクを最小限に抑えることができる。作業者は適切な保護具を着用し、化学物質との直接接触を避け、作業環境が安全基準を満たすようにすべきである。
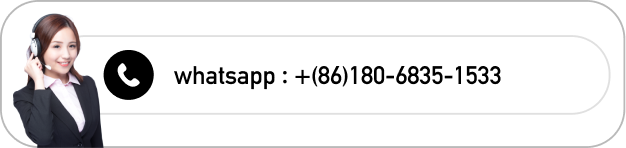