La différence entre le meulage et le sablage
24 septembre 2024
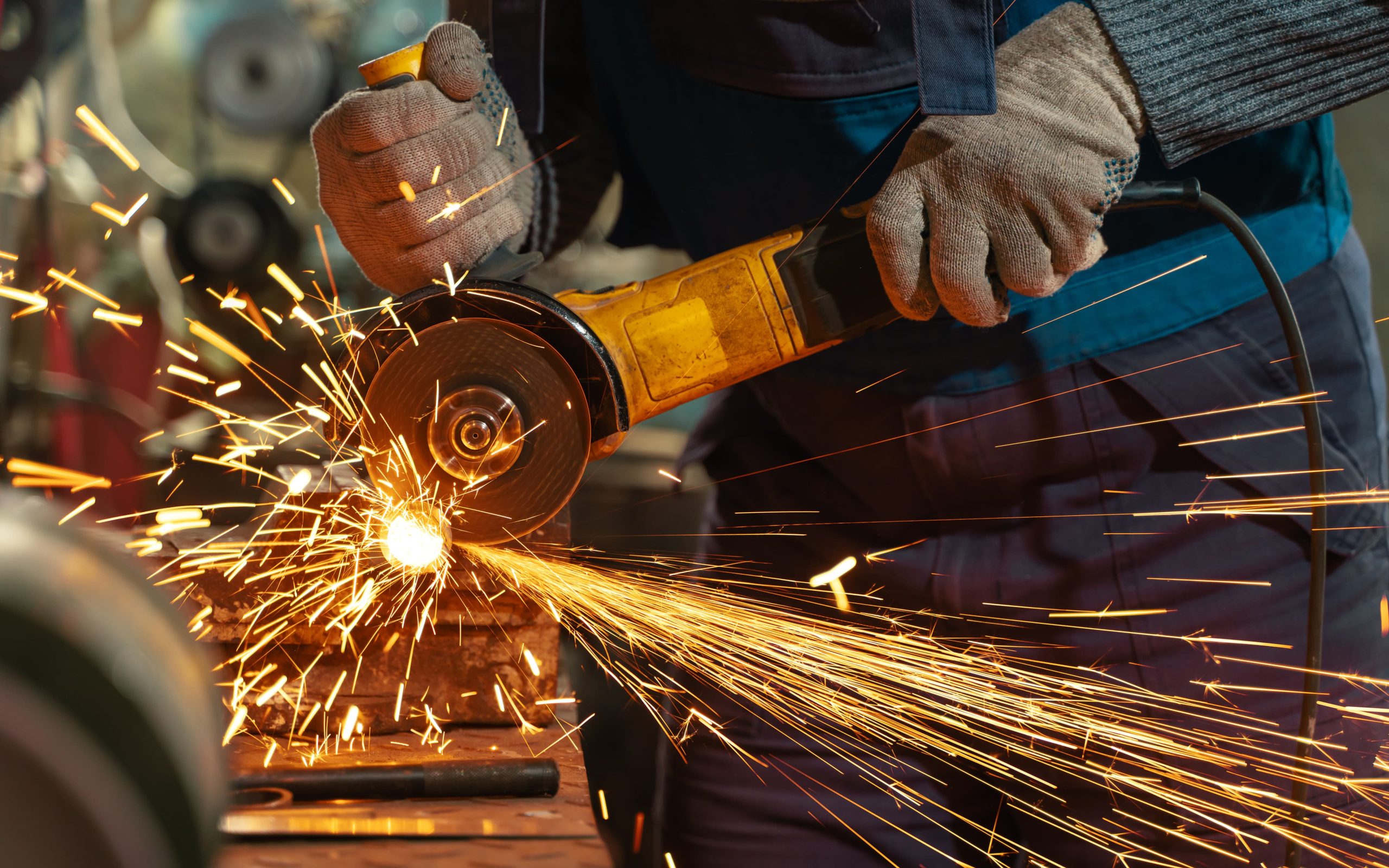
Le meulage et le sablage sont deux procédés importants dans le domaine du traitement des surfaces. Bien qu'ils semblent similaires, ils présentent en réalité des différences significatives en termes d'utilisation, de fonctions et de matériaux. Qu'il s'agisse du traitement des métaux, de la construction automobile ou de l'industrie aérospatiale, ces deux technologies sont des étapes essentielles pour améliorer la qualité et les performances de la surface des produits. Cet article se penche sur les différences et les liens entre les matériaux de meulage et les matériaux de sablage du point de vue des définitions, des matériaux et des processus.
Qu'est-ce qu'un matériau de broyage ?
Définition : Le matériau de rectification est un matériau qui modifie la topographie de la surface de la pièce à usiner par frottement, coupe ou rectification. Les matériaux de rectification peuvent être utilisés pour l'ajustement de la rugosité de la surface, l'élimination de la couche d'oxyde et le prétraitement pour l'usinage de précision.
Fonction : Le meulage est principalement utilisé pour prétraiter les pièces afin d'éliminer les gros morceaux de saleté, la calamine, les défauts de surface et les irrégularités. Ce processus est souvent utilisé pour la modification de la surface, le traitement des soudures et le meulage de grandes surfaces afin de rendre la surface du matériau plus lisse et de fournir une bonne base pour les traitements ultérieurs tels que le sablage et la peinture. Le meulage peut également prolonger efficacement la durée de vie de la pièce et améliorer la finition et les performances globales du produit.
Historique du broyage
Le meulage est une technologie de traitement ancienne qui existe depuis des milliers d'années. Ses origines remontent à l'âge de pierre, lorsque les hommes utilisaient des pierres naturelles pour meuler et traiter des surfaces rugueuses afin de fabriquer des outils et des armes. Au fil du temps, le processus de meulage a évolué et sa gamme d'applications s'est élargie.
Dans l'Antiquité, le meulage reposait principalement sur des techniques manuelles. Les artisans utilisaient des matériaux naturels tels que le sable et le gravier et des fibres végétales rugueuses pour polir le métal et le bois. À ce stade, le processus de meulage est relativement simple, repose principalement sur la force et l'expérience humaines et est moins efficace.
À l'aube de la révolution industrielle, en particulier à la fin du XIXe siècle, l'essor de la production mécanisée a entraîné un développement rapide de la technologie du broyage. Avec la popularité des machines à vapeur et des machines électriques, les machines à meuler ont vu le jour. En particulier, l'invention de la "meule" a marqué l'entrée du processus de meulage dans une nouvelle ère. Les meules sont fabriquées à partir de divers matériaux de meulage, ce qui permet un meulage plus raffiné et plus efficace.
Au 20e siècle, avec le développement continu de nouveaux matériaux et les progrès constants de la technologie de broyage, cette dernière a été largement utilisée dans de nombreux domaines. Le broyage moderne ne se limite pas aux métaux, mais s'est également étendu au traitement d'une variété de matériaux tels que les céramiques, les plastiques, le verre, etc. Tout matériau présentant une certaine résistance et ténacité, qu'il soit produit naturellement ou artificiellement, peut être utilisé, de sorte que même les coquilles de noix constituent un bon moyen de broyage.
Ces dernières années, le concept de fabrication intelligente a émergé et la technologie de meulage a progressivement évolué vers l'automatisation et la numérisation. L'apparition de rectifieuses CNC de haute précision, de robots et d'autres équipements a amélioré de manière sans précédent l'efficacité et la précision du processus de rectification. Parallèlement, la sensibilisation croissante à la protection de l'environnement a également favorisé le développement écologique des matériaux et des processus de rectification, promouvant ainsi le développement durable de l'industrie.
Techniques utilisées dans le processus de broyage
- Broyage à sec : Aucun liquide de refroidissement n'est ajouté pendant le processus de meulage, et le meulage est réalisé en contrôlant le temps de contact et la pression entre le meulage et la pièce à usiner. Cette méthode convient aux matériaux qui ne se déforment pas facilement.
- Broyage humide : Ajouter du liquide de refroidissement pendant le processus de meulage pour réduire la chaleur générée par la friction et améliorer l'efficacité du meulage. Il convient au traitement des matériaux à dureté élevée.
- Meulage de précision : La finition de surface au micron est obtenue grâce à un équipement de haute précision et au contrôle des paramètres du processus. Il est souvent utilisé dans le traitement des composants optiques et des pièces de haute précision.
- Meulage de haute précision : Combinée à la technologie ultrasonique ou à la technologie laser pour obtenir une précision de surface de l'ordre du nanomètre, elle est principalement utilisée dans des domaines de haute technologie tels que les semi-conducteurs et les dispositifs optiques.
- Meulage CNC (commande numérique par ordinateur) : L'ordinateur contrôle le mouvement de la rectifieuse pour obtenir un traitement efficace et précis, et peut traiter des pièces de forme complexe.
- Meulage au laser : Le faisceau laser est utilisé pour chauffer la surface du matériau et le ramollir afin d'obtenir l'effet de meulage. Il convient au traitement fin des matériaux à dureté élevée.
Classification des matériaux de broyage
- Plastiques et polymères
- Polyméthacrylate de méthyle (PMMA) : il présente une bonne transparence et est souvent utilisé dans les composants optiques.
- Polycarbonate (PC) : Résistant aux chocs, il convient aux équipements de protection et aux boîtiers électroniques.
- Nylon (PA) : Il présente une forte résistance à l'usure et est largement utilisé dans les pièces mécaniques.
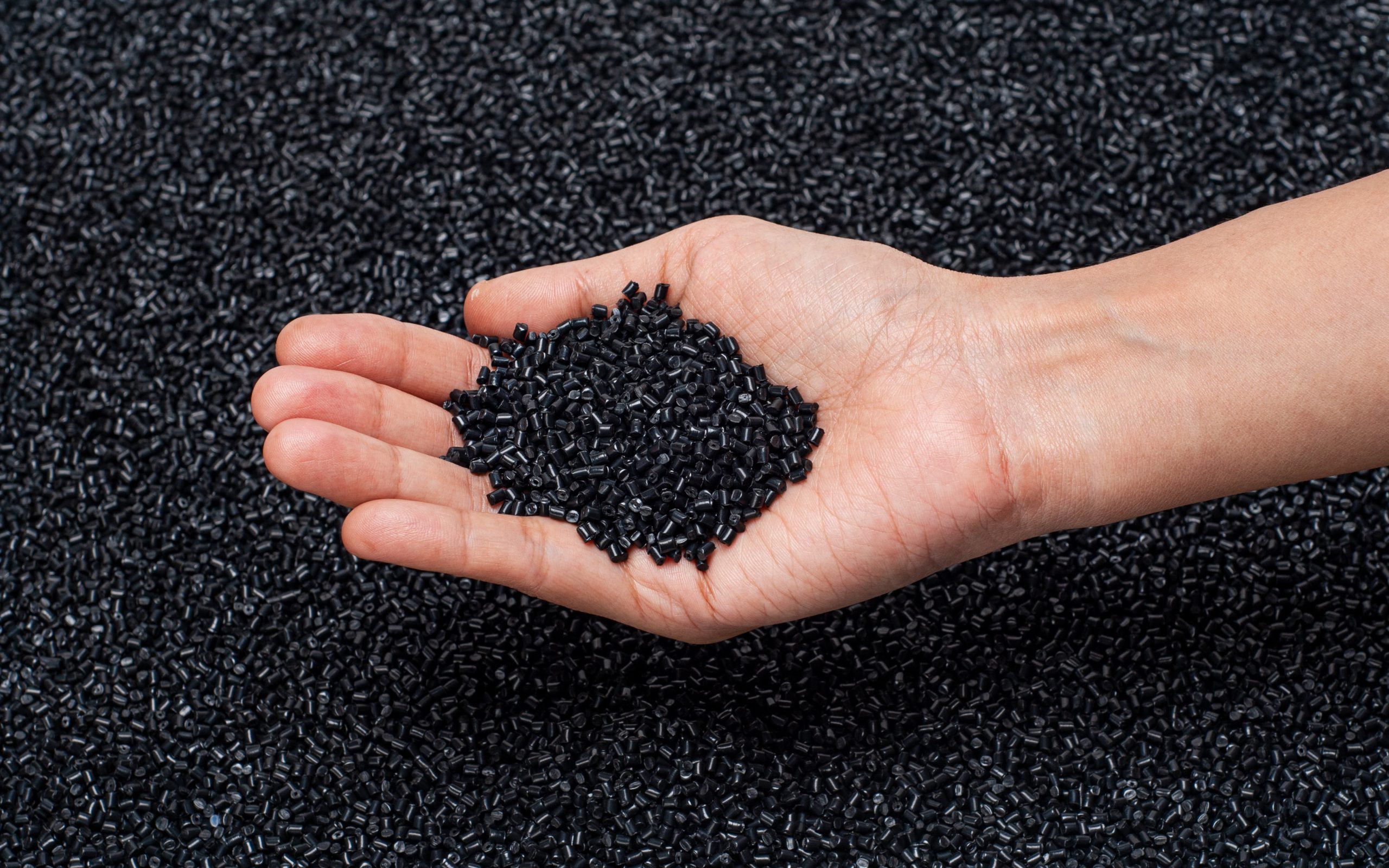
Polymères plastiques
- Métal
- Aluminium : matériau léger largement utilisé dans les secteurs de l'aérospatiale et de l'automobile.
- Acier inoxydable : très résistant à la corrosion, convient aux dispositifs médicaux et à l'industrie alimentaire.
- Cuivre : il possède une excellente conductivité électrique et est souvent utilisé dans les composants électroniques.
- Alliage de titane : très résistant et léger, largement utilisé dans l'aérospatiale.
- Matériaux composites
- Matériaux composites à base de fibres de carbone : légers et très résistants, ils sont largement utilisés dans les secteurs de l'aérospatiale et de l'automobile.
- Composites en fibre de verre : résistants à la corrosion, souvent utilisés dans la construction et la construction navale.
- Céramique
- Céramique d'alumine : dureté élevée et résistance à l'usure, souvent utilisée dans les couteaux et les outils de meulage.
- Céramiques de carbure de silicium : conductivité thermique et résistance élevées, adaptées aux outils de coupe et aux matériaux réfractaires.
- Céramiques de zircone : excellente ténacité et résistance aux fissures, utilisées dans les appareils médicaux et les matériaux dentaires.
- Verre
- Verre ordinaire : utilisé pour les fenêtres et les récipients.
- Verre optique : utilisé dans les lentilles et les instruments optiques, exigeant une grande transparence et peu d'impuretés.
- Produits du bois
- Bois massif : tel que le chêne et le pin, adapté à l'ameublement et à la décoration.
- Bois composite : tel que le contreplaqué, il est couramment utilisé dans la construction et la décoration intérieure.
- Semi-conducteurs
- Plaquettes de silicium : utilisées pour la fabrication de composants électroniques, qui nécessitent une planéité et un lissage extrêmement élevés.
- Arséniure de gallium : utilisé dans des applications optoélectroniques et à haute fréquence, il possède d'excellentes propriétés électroniques.
- Gomme
- Caoutchouc naturel : il possède une bonne élasticité et est utilisé pour la fabrication de divers joints et matériaux d'absorption des chocs.
- Caoutchouc synthétique : résistant à l'usure et à l'huile, utilisé dans les pneus et les produits industriels.
- Caoutchouc mousse : léger et bien insonorisé, il est souvent utilisé dans les emballages et les intérieurs de voiture.
- Barytine : utilisée comme matériau de remplissage et comme barrière, largement utilisée dans les forages pétroliers.
- Maçonnerie
- Granit : très solide et résistant à l'usure, il est souvent utilisé dans la construction et les matériaux de décoration.
- Marbre : beau et adapté à la décoration intérieure et extérieure, mais doux et facile à porter.
- Carreaux de céramique : durs et résistants à l'usure, ils sont largement utilisés pour la décoration des sols et des murs.
- Biomatériaux
- Acide polylactique (PLA) : plastique biodégradable utilisé dans les dispositifs médicaux et les matériaux d'emballage.
- Polyhydroxyalcanoate (PHA) : hautement biocompatible et adapté aux applications biomédicales.
- Cellulose naturelle : utilisée dans les emballages pharmaceutiques et alimentaires, avec une bonne biocompatibilité.
- Minerais
- Quartz : haute dureté, souvent utilisé dans la fabrication du verre et dans l'industrie électronique.
- Feldspath : matière première importante utilisée dans les industries de la céramique et du verre.
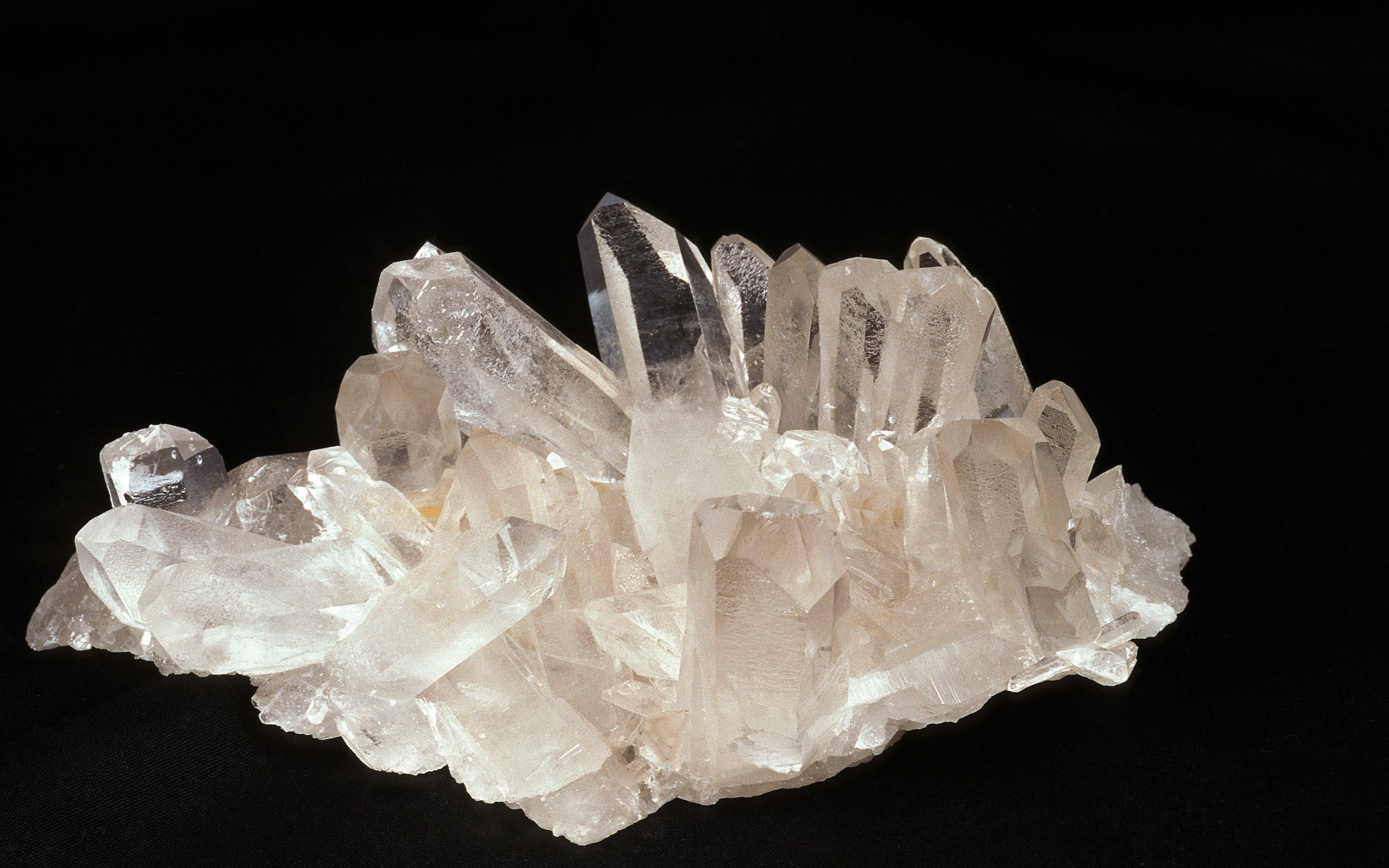
Quartz
Caractéristiques des matériaux et méthodes de sélection
Caractéristiques
- Dureté : La dureté des différents matériaux de broyage détermine leur applicabilité. En général, plus la dureté est élevée, plus la gamme de matériaux applicables est large.
- Résistance à l'usure : Les matériaux de meulage de première qualité conservent la forme et les performances du meulage pendant de longues périodes d'utilisation.
- Forme des particules : La forme et la distribution des particules affectent l'effet de broyage. Les abrasifs de forme régulière peuvent améliorer l'uniformité du broyage.
- Taille des particules : Plus la taille des particules est fine, plus l'effet de broyage l'est aussi, et elle est généralement utilisée pour l'usinage de précision.
- Adaptabilité : L'adaptabilité des différents matériaux les rend plus remarquables dans des industries spécifiques, comme l'application des matériaux de pierre et de maçonnerie dans l'industrie de la construction.
- Protection de l'environnement : L'accent étant mis sur le développement durable, les biomatériaux et les matériaux dégradables deviennent des choix populaires pour le broyage.
Sélectionner la méthode
- Sélection en fonction des matériaux de traitement : Il faut d'abord tenir compte du type et des caractéristiques du matériau à traiter, puis sélectionner des matériaux de rectification adaptés à sa dureté et à sa ténacité.
- Tenir compte des exigences de traitement : Sélectionnez la taille et la forme des particules en fonction de la finition de surface et de la précision requises.
- Évaluer le coût : Combinez les performances et le coût du matériau pour sélectionner des matériaux de broyage rentables.
- Essai et retour d'information : Effectuer un essai à petite échelle avant la production formelle et procéder à des ajustements en fonction des résultats réels.
- Selon les applications industrielles : Les exigences en matière de matériaux de broyage varient d'une industrie à l'autre. Par exemple, l'industrie de la construction a tendance à utiliser des pierres très résistantes à l'usure, tandis que le secteur biomédical accorde plus d'attention à la biocompatibilité des matériaux.
- Tenir compte de l'impact sur l'environnement : Lors de la sélection des matériaux de broyage, il convient de tenir compte de leur protection environnementale et de leur recyclabilité, et de choisir des matériaux respectueux de l'environnement.
Type de machine utilisée pour le broyage
La rectifieuse est l'équipement principal pour réaliser le processus de broyage. Il en existe de nombreux types, adaptés à différents matériaux et exigences de traitement. Lorsque vous choisissez une rectifieuse, vous devez vous baser sur vos besoins spécifiques en matière de traitement. Les facteurs pris en compte comprennent le matériau de la pièce, sa forme, les exigences dimensionnelles, ainsi que la précision et la finition du traitement de surface. Voici quelques types courants de rectifieuses :
- Meuleuse de surface
La rectifieuse plane est utilisée pour traiter la surface plane du métal ou d'autres matériaux. Elle réalise le ponçage et le lissage de la surface grâce à la friction entre le disque abrasif et la pièce à usiner. Les rectifieuses planes sont généralement dotées de systèmes de contrôle de haute précision et conviennent à l'usinage de précision très exigeant.
- Machine à rectifier cylindrique
Une rectifieuse cylindrique est utilisée pour traiter les surfaces extérieures et intérieures de pièces cylindriques. Elle entre en contact avec la pièce par l'intermédiaire de la meule en rotation afin d'obtenir un meulage uniforme de la pièce. Les rectifieuses cylindriques sont largement utilisées dans le traitement des pièces mécaniques.
- Ponceuse à bande
La ponceuse à bande utilise une bande abrasive continue comme outil de ponçage et convient au traitement de grandes surfaces planes et incurvées. Les ponceuses à bande sont faciles à utiliser et efficaces, et sont souvent utilisées pour le traitement de surface du bois, du plastique et du métal.
- Meuleuse verticale
Une rectifieuse verticale fixe la rectification dans le sens vertical et rectifie la pièce en la déplaçant. Cet équipement convient aux pièces de forme complexe et aux surfaces difficiles à usiner, et peut améliorer efficacement la précision du traitement.
- Machine à rectifier CNC
La rectifieuse CNC est un représentant de la technologie de rectification moderne. Elle contrôle le processus de meulage par le biais d'un programme informatique afin d'obtenir un traitement de haute précision et de grande efficacité. Les rectifieuses CNC peuvent traiter des pièces de forme complexe et sont largement utilisées dans les industries de haute technologie telles que l'aérospatiale, l'automobile et la fabrication de moules.
- Machine de meulage optique
La rectifieuse optique est principalement utilisée pour fabriquer des composants optiques et des lentilles, qui nécessitent un état de surface et une précision extrêmement élevés. L'équipement utilise des abrasifs et des procédés spéciaux pour garantir la qualité des produits optiques.
- Broyeurs humides et secs
En fonction des différentes exigences de traitement, les meuleuses sont également divisées en deux catégories : les meuleuses humides et les meuleuses sèches. Les machines à meuler par voie humide ajoutent un liquide de refroidissement pendant le traitement, ce qui permet de réduire efficacement la température du meulage et de la pièce à usiner et d'améliorer l'effet du traitement. Les meuleuses à sec sont généralement utilisées pour traiter des matériaux dans des environnements secs.
Qu'est-ce que le matériel de sablage ?
Définition : Les matériaux de sablage sont des matériaux qui agissent sur la surface de la pièce par pulvérisation à grande vitesse pour nettoyer, éliminer les bavures ou modifier la rugosité de la surface. Les matériaux de sablage courants comprennent les billes de verre, le sable de quartz, les particules métalliques, etc.
Fonction : Le processus de sablage est utilisé pour nettoyer, ébavurer, rendre rugueuse ou polir finement la surface de la pièce. Il permet d'éliminer la couche d'oxyde, la saleté ou les résidus de surface, et peut également former une texture ou une rugosité spécifique sur la surface afin d'améliorer l'adhérence du matériau. Propriétés, telles que la préparation de la surface avant le revêtement ou le placage.
Exemples de matériaux de sablage :
- Sable de quartz : Le sable de quartz est l'un des matériaux les plus couramment utilisés pour le sablage. Il est bon marché, ses particules sont uniformes et il convient au nettoyage de la surface de la plupart des matériaux métalliques et non métalliques.
- Perles de verre : Le sablage aux billes de verre est généralement utilisé pour le polissage fin et convient à la finition de l'aluminium, de l'acier inoxydable, etc., en donnant à la surface de la pièce un aspect lisse et mat.
- Grenaille d'acier et grenailles d'acier : La grenaille d'acier et les grains d'acier sont souvent utilisés dans les processus de sablage intensif. Elles peuvent éliminer efficacement la rouille, les dépôts d'oxyde ou de grandes surfaces de saleté, et conviennent aux composants métalliques qui nécessitent un traitement de surface de haute intensité.
- Plastique : tels que les médias plastiques, le sable de nylon, le sable congelé, etc., qui sont particulièrement efficaces pour l'ébavurage des pièces de haute précision et de forme complexe, et qui conviennent aux pièces souples.
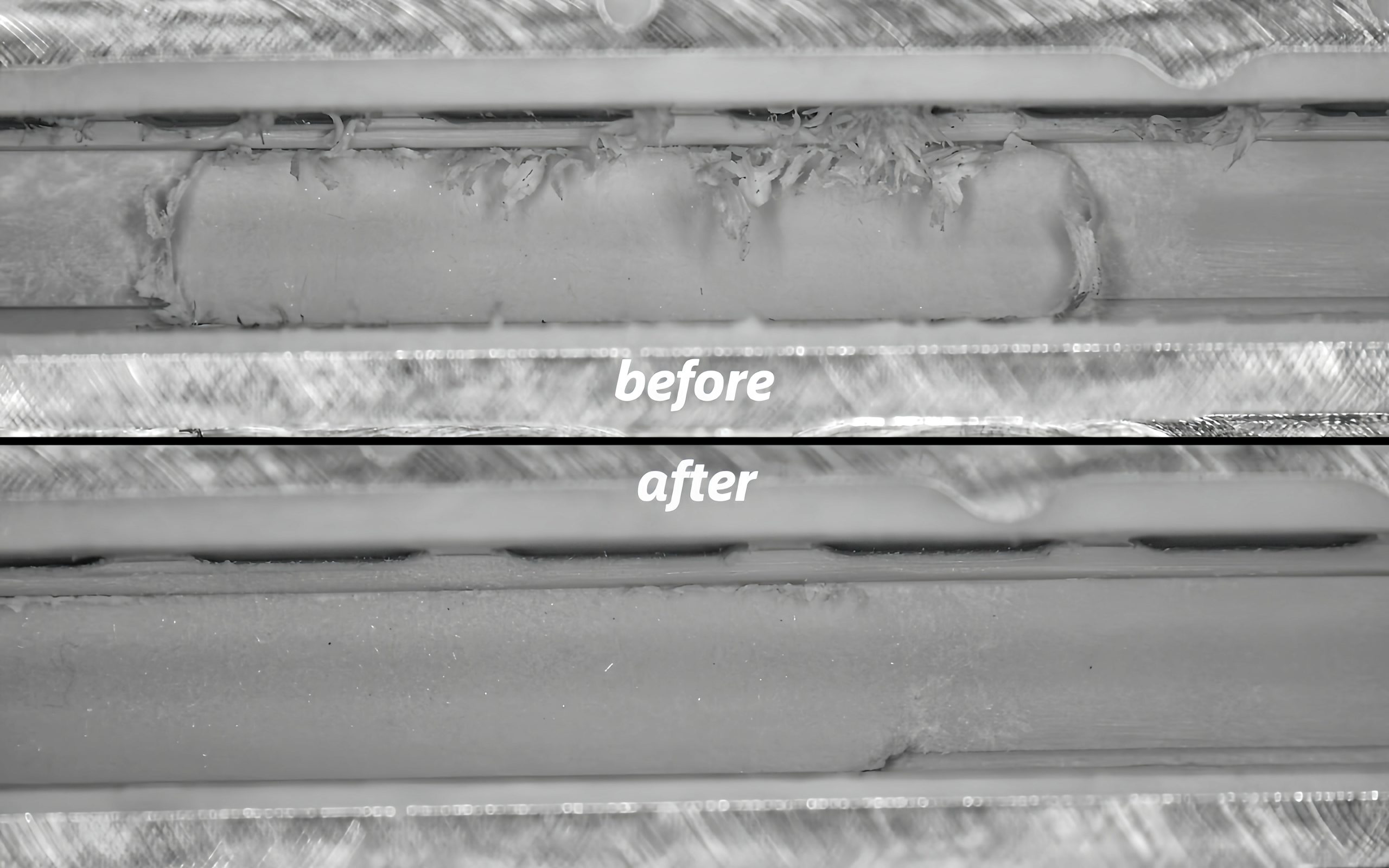
Billes d'ébarbage en polystyrène HLH avant et après l'ébarbage
Le choix des matériaux de sablage est généralement déterminé en fonction du matériau de la pièce, de l'effet de surface souhaité et des exigences du processus. Les grains d'acier plus durs conviennent au traitement des métaux durs, tandis que les billes de verre et les particules de céramique conviennent au traitement fin.
Similitudes et différences
Connexion : Le meulage et le sablage utilisent tous deux des matériaux de meulage pour traiter la surface des pièces à usiner, de sorte que l'on peut dire que leurs utilisations se chevauchent. Tous deux peuvent être utilisés pour le nettoyage, le polissage et le dépolissage des surfaces. Certains matériaux de meulage (tels que l'oxyde d'aluminium et le carbure de silicium) peuvent également être utilisés comme matériaux de sablage, de sorte qu'il y a un chevauchement dans la sélection des matériaux entre les deux processus. Les matériaux de sablage peuvent être considérés comme faisant partie des matériaux de meulage, mais tous les matériaux de meulage ne sont pas des matériaux de sablage.
Différence : La principale différence se reflète dans le déroulement du processus et les scénarios d'application. En règle générale, le meulage est une étape de prétraitement avant le sablage, en particulier lorsqu'il s'agit d'éliminer de grandes zones de défauts, des surfaces irrégulières ou de grandes quantités de saletés. Le meulage est plus axé sur la modification de grandes surfaces et le ponçage de base, tandis que le sablage est plus axé sur le raffinement des détails.
- Les matériaux de broyage sont généralement rugueux et sont principalement utilisés pour le traitement de grandes surfaces au stade initial. Leur fonction est d'éliminer les grosses particules d'impuretés, la calamine, les taches d'huile, etc. Il s'agit généralement d'une étape préliminaire à l'usinage afin de préparer une bonne surface pour le processus de sablage ou de peinture.
- Les matériaux de sablage sont plus raffinés et sont utilisés pour éliminer les petites particules de bavures et les minuscules imperfections, et pour donner à la surface la texture ou la rugosité souhaitée. Le sablage peut traiter des ajustements de surface jusqu'au niveau du micron et est particulièrement adapté à l'étape finale du traitement de surface.
Par exemple, dans le processus de fabrication automobile, après le soudage ou la fabrication du moule, la carrosserie peut devoir être nettoyée dans un premier temps avec des matériaux de broyage plus grossiers, puis sablée pour obtenir un traitement de surface plus fin, tel que le polissage ou une préparation ultérieure.
Le meulage et le sablage ont chacun leur rôle et leur fonction propres, mais ils sont souvent complémentaires dans les processus de traitement de surface. En sélectionnant et en combinant rationnellement ces deux procédés, la qualité de la surface et les performances du produit peuvent être grandement améliorées.
Les produits de ponçage et de sablage jouent un rôle essentiel dans les processus modernes de fabrication et de traitement de surface. Les matériaux de ponçage sont utilisés pour rendre la surface rugueuse et la préparer, ce qui permet d'obtenir une bonne base, tandis que les matériaux de sablage améliorent encore les détails et la qualité de la surface. En comprenant les propriétés des matériaux, les scénarios d'application et les caractéristiques des processus, les clients peuvent mieux choisir une solution de traitement adaptée à leurs besoins et s'assurer que la qualité finale du produit répond aux attentes.
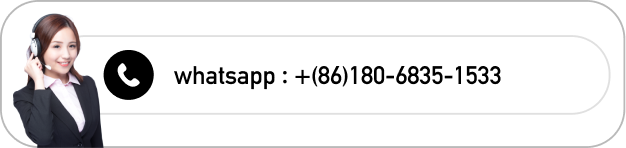