Maîtriser le processus de sablage : Obtenir un traitement de surface optimal
27 août 2024
Le processus de sablage est une étape cruciale du traitement de surface, qui détermine la qualité et les performances finales de la pièce. De la mise en place de l'équipement de sablage à chaque détail de l'opération, il requiert non seulement un soutien technique, mais aussi la méticulosité et la précision de l'opérateur. Cet article vous guidera à travers les différents aspects du processus de sablage, vous aidant à maîtriser ce processus du début à la fin afin de garantir que chaque opération atteigne les résultats souhaités.
Préparation au sablage
La préparation du sablage est essentielle pour garantir l'effet final du traitement et la qualité de la pièce. Ce processus peut être divisé en plusieurs aspects importants : la préparation de la pièce, la sélection du produit de sablage et la sélection et l'installation de l'équipement.
1. Préparation de la pièce
Avant le sablage, le nettoyage initial de la pièce est crucial. Les étapes de nettoyage permettent d'éliminer la graisse, la saleté, la rouille ou d'autres matériaux de surface non adhérents afin de garantir l'uniformité et l'efficacité du sablage. Les exigences en matière de préparation varient en fonction du matériau de la pièce :
- Pièces métalliques: Tout d'abord, il faut éliminer la graisse et la saleté en surface à l'aide d'un solvant, d'un récurage mécanique ou de nettoyants chimiques. Pour les pièces en fer, l'élimination de la rouille se fait généralement à l'aide de brosses ou d'agents chimiques. La pièce nettoyée doit être soigneusement séchée pour éviter que l'humidité résiduelle n'affecte le résultat du sablage.
- Pièces en plastique: Le plastique est relativement fragile et doit être manipulé avec précaution. Utilisez des nettoyants doux et des chiffons souples pour essuyer la surface et enlever la graisse et la saleté. Pour les taches tenaces, utilisez des nettoyants spécialisés pour le plastique. Faites particulièrement attention aux brosses rugueuses ou aux nettoyants puissants qui risquent d'endommager la surface en plastique.
- Pièces en céramique: Les pièces en céramique sont relativement dures et présentent généralement de la graisse naturelle ou de la poussière sur leur surface. Utilisez une brosse douce ou un flux d'air pour enlever la poussière, puis lavez avec de l'eau chaude et un détergent neutre, et enfin, séchez soigneusement.
2. Sélection des produits de sablage
Le choix du support de sablage affecte directement le processus de sablage et les résultats finaux. Il est donc essentiel de sélectionner le support de sablage approprié en fonction du matériau de la pièce, de l'effet de surface souhaité et des exigences du traitement. Les produits de sablage les plus courants sont les suivants
- Oxyde d'aluminium: D'une grande dureté et d'une grande résistance à l'usure, il convient aux applications nécessitant une forte abrasion. Il est idéal pour traiter les surfaces métalliques, éliminer les oxydes ou les anciens revêtements. En raison de son coût plus élevé, il est généralement utilisé pour des applications haut de gamme ou des traitements spéciaux.
- Perles de verre: Plus doux, il convient aux traitements de surface fins, tels que les boîtiers d'appareils électroniques grand public. Le sablage aux billes de verre élimine efficacement les contaminants de surface, améliore le lissage de la surface et ne provoque pas d'usure excessive de la pièce.
- Supports en céramique: D'une dureté modérée, entre l'oxyde d'aluminium et les billes de verre, ils conviennent aux processus nécessitant une plus grande rugosité de surface. Les médias céramiques sont souvent utilisés pour l'ébavurage ou le renforcement de la surface des pièces métalliques, offrant une rugosité uniforme et une bonne durabilité.
- Grenaille d'acier: Convient pour le nettoyage à grande échelle des surfaces métalliques, comme le traitement anticorrosion des structures en acier. La grenaille d'acier est dure et résistante à l'usure, elle élimine efficacement la rouille et les vieilles couches.
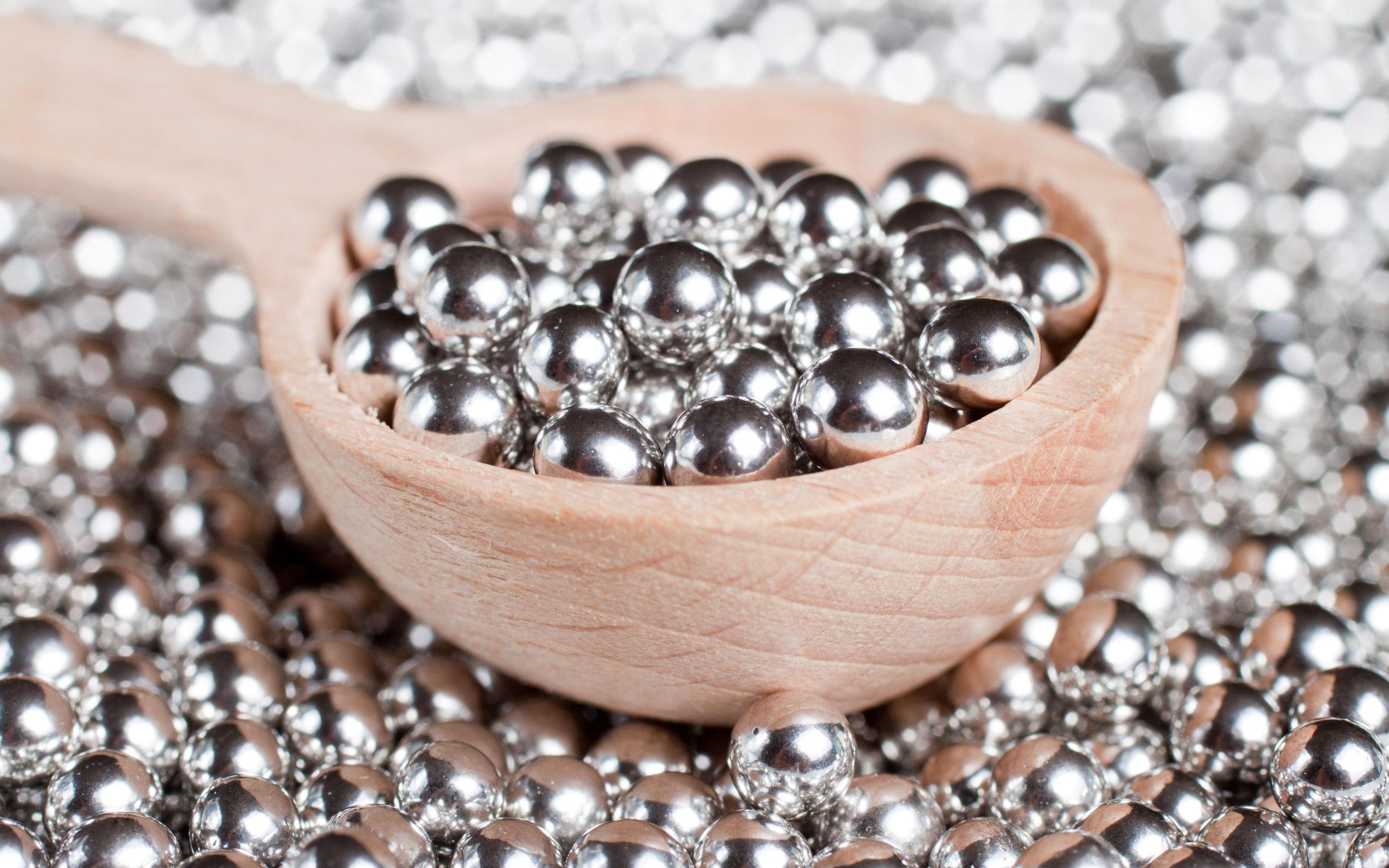
grenaille d'acier
3. Sélection de l'équipement
Le choix et la configuration de l'équipement de sablage ont également un impact sur l'effet du sablage. Les principaux types d'équipement sont les suivants :
- Équipement de sablage sous pression: Utilise de l'air comprimé pour acheminer les abrasifs jusqu'à la buse ; convient aux applications nécessitant un débit et une pression élevés. L'équipement comprend généralement le contrôle de la pression de l'air, le stockage des abrasifs et les composants de la buse. Lors du réglage, il faut ajuster la pression de sablage, généralement entre 4 et 8 bars, en fonction des exigences du traitement.
- Équipement de sablage par aspiration: Utilise le flux d'air pour aspirer les abrasifs dans la buse, ce qui convient pour les petites pièces ou les opérations précises. Lors du réglage, il faut ajuster le diamètre de la buse et l'angle de projection, qui sont généralement plus flexibles et réglables en fonction des besoins.
4. Paramètres de l'équipement :
- Pression de sablage
La pression de sablage est l'un des principaux paramètres du processus de sablage, car elle affecte directement la vitesse de sablage et l'effet du traitement. La pression de sablage est généralement mesurée en unités de pression (psi ou bar, par exemple). Dans le processus de sablage, la pression de sablage détermine la force d'impact des abrasifs. Une pression de sablage élevée augmente la vitesse des abrasifs, ce qui améliore leur impact sur la surface de la pièce et l'efficacité de l'enlèvement. Toutefois, une pression de sablage excessive peut entraîner une sur-usure ou même endommager les surfaces plus douces ou plus fines de la pièce.
- Diamètre de la buse
Le diamètre de la buse détermine la portée et l'uniformité de la pulvérisation des abrasifs. Le diamètre de la buse est généralement mesuré en millimètres. Les buses de grand diamètre (généralement entre 6 et 12 mm) augmentent la zone de couverture et améliorent l'efficacité du traitement, ce qui convient aux tâches portant sur de grandes surfaces, telles que l'élimination de la rouille sur les corps métalliques ou le nettoyage des surfaces en béton. Toutefois, un diamètre de buse plus important peut entraîner un décapage inégal, en particulier pour les surfaces plus fines, ce qui conduit à un surtraitement ou à un sous-traitement dans certaines zones.
- Angle de projection
L'angle de projection est un autre paramètre important du processus de sablage, réglé en ajustant le support de l'équipement ou la buse elle-même. L'angle de sablage affecte directement la direction et l'uniformité des impacts abrasifs. En règle générale, l'angle de sablage doit être ajusté en fonction de la géométrie de la pièce et des exigences de traitement afin de garantir un traitement de surface uniforme. L'angle peut influencer la finesse de l'effet de sablage. Les angles de sablage courants vont de 30° à 90°. Lorsque la buse est perpendiculaire à la surface de la pièce (90°), la force d'impact des abrasifs est la plus forte, ce qui convient au nettoyage en profondeur des surfaces planes. Cet angle garantit que les abrasifs frappent uniformément toute la surface, en particulier pour les grandes surfaces ou les surfaces uniformes ; les angles de sablage plus importants (60°-90°) conviennent au nettoyage à grande échelle mais peuvent entraîner un traitement local inégal ; les angles de sablage plus faibles (30°-45°) conviennent au traitement détaillé et permettent d'obtenir une meilleure qualité de surface.
En ajustant ces paramètres avec précision, le processus de sablage permet d'obtenir un traitement de surface plus efficace et plus précis, répondant aux besoins des différents domaines d'application. La compréhension et la maîtrise de ces paramètres sont essentielles pour optimiser les effets du sablage et améliorer l'efficacité de la production.
Une attention particulière aux travaux de préparation ci-dessus garantit une exécution sans heurts du processus de sablage, permettant d'obtenir l'effet de traitement désiré.
Processus spécifique de l'opération de sablage
- Réglage des paramètres de sablage:
- Réglage de la pression: Discuter de la manière de régler la pression de sablage en fonction du matériau de la pièce et du type de support, et de l'impact d'une pression trop élevée ou trop faible.
- Angle et distance de sablage: Analyser la relation entre l'angle de grenaillage et la planéité et la rugosité de la surface de la pièce, ainsi que l'impact de la distance sur les effets du traitement.
- Vitesse de déplacement de la buse: Expliquer comment la vitesse de déplacement de la buse sur la surface de la pièce affecte l'uniformité et l'efficacité du sablage.
- Positionnement et fixation de la pièce: Veiller à ce que la pièce reste stable pendant le sablage afin d'obtenir un effet de traitement de surface uniforme.
- Méthodes et dispositifs courants de fixation des pièces: (Voir l'image ci-dessous)
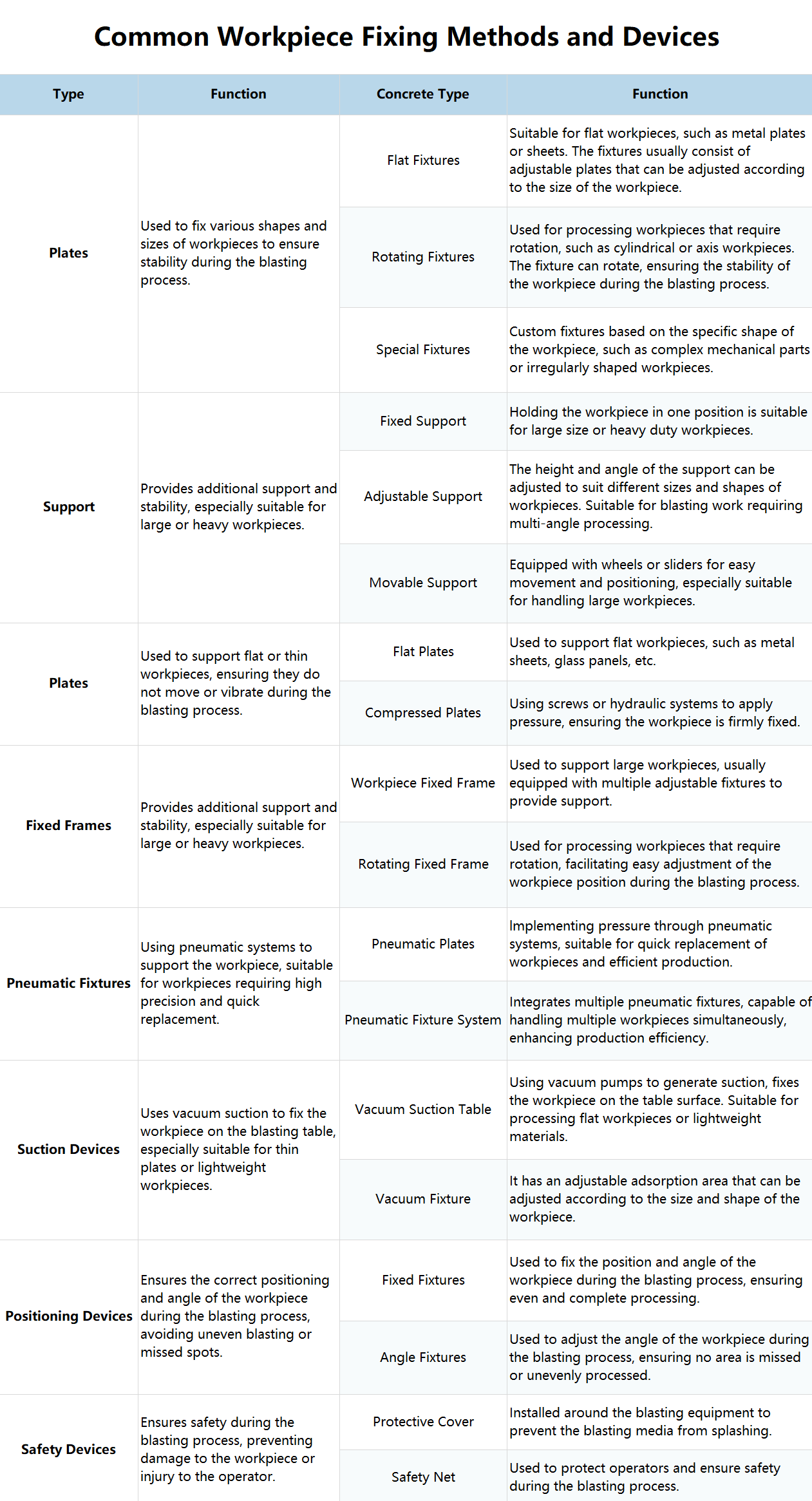
- Procédure de sablage:
- Démarrer le dynamitage: Démarrer l'équipement de sablage, augmenter progressivement la pression de sablage jusqu'à la valeur réglée. Commencer le sablage à partir d'une extrémité de la pièce et se déplacer progressivement vers l'autre extrémité, en veillant à ce que toute la surface soit couverte. Maintenir un mouvement régulier de la buse, éviter de rester trop longtemps dans la même position pour éviter l'usure excessive, et assurer une couverture complète, y compris des bords et des zones difficiles à atteindre.
- Vérifier l'état de la surface: Contrôler régulièrement la surface de la pièce pendant le traitement pour s'assurer qu'elle présente la rugosité ou la propreté voulue. Ajuster la pression de sablage, l'angle de la buse ou le diamètre de la buse en fonction des résultats de l'inspection pour optimiser les effets du traitement.
- Passages multiples: Si nécessaire, effectuer plusieurs passages, en particulier pour les surfaces complexes, pour lesquelles un traitement étape par étape peut être plus efficace.
- Traitement et inspection après sablage:
- Nettoyage après sablage: Utilisez des souffleurs d'air, des brosses ou des aspirateurs pour éliminer les résidus d'abrasifs et de poussière de la surface de la pièce. Vérifiez soigneusement qu'il ne reste pas de résidus d'abrasifs ou d'autres impuretés sur la surface.
- Inspection et mesure des surfaces: Utiliser des instruments de mesure de la rugosité de la surface pour vérifier la qualité de la surface de la pièce et s'assurer qu'elle répond aux exigences. Si le traitement de surface est inégal ou incomplet, effectuez les réparations nécessaires ou procédez à un sablage supplémentaire.

Le modèle de sablage
Les instruments de détection les plus courants sont les suivants
- Instruments de mesure de la rugosité de surface: Comprend les rugosimètres à contact (qui enregistrent les variations de surface à l'aide d'une sonde) et les rugosimètres optiques (qui utilisent des lasers ou des systèmes optiques pour mesurer la surface sans contact) pour évaluer la rugosité de surface des pièces sablées en comparant les valeurs d'essai à des normes définies.
- Testeurs de rugosité: Comprend des rugosimètres portatifs (pratiques pour les opérations sur le terrain et adaptés à différentes formes de pièces) et des rugosimètres de table (adaptés aux environnements de laboratoire et offrant une plus grande précision de mesure) pour enregistrer les valeurs de rugosité et les comparer aux exigences de conception.
- Profilomètres: Principalement utilisé pour mesurer les profils et les formes de la surface des pièces afin d'assurer la cohérence du traitement par sablage.
- Analyseurs de taille de particules abrasives: Utilisé pour mesurer la distribution de la taille des particules des produits de sablage afin de s'assurer de leur conformité aux exigences.
- Manomètres: Mesurer la pression de l'air ou du fluide dans l'équipement de sablage pour s'assurer qu'il fonctionne dans la plage définie.
- Thermomètres: Mesurer l'humidité de l'environnement de sablage pour éviter que l'humidité n'affecte les effets du sablage et la qualité de l'abrasif.
- Débitmètres de gaz: Mesurer le débit de gaz pendant le sablage pour garantir des effets de sablage stables.
- Testeurs d'usure: Mesurer le degré d'usure de la surface de la pièce par les abrasifs pendant le sablage pour s'assurer que l'usure se situe dans les limites autorisées.
Entretien de l'équipement de sablage
- Nettoyer l'équipement : Nettoyer régulièrement l'équipement de sablage, en particulier les buses et les tuyaux, pour éviter qu'ils ne se bouchent ou ne s'usent.
- Vérifier l'usure: Inspecter les différentes parties de l'équipement de sablage, telles que les buses, les manomètres et les tuyaux, pour s'assurer qu'elles fonctionnent correctement.
- Remplacer les buses: Remplacer régulièrement les buses en fonction de l'utilisation, en particulier lorsque l'effet de sablage se détériore.
- Entretien de l'équipement: Effectuer la maintenance et l'entretien conformément aux recommandations du fabricant de l'équipement afin de garantir la stabilité et les performances à long terme.
Problèmes courants dans le processus de sablage et leurs solutions
- Sélection incorrecte du support: L'utilisation d'un produit trop grossier ou trop fin peut endommager la surface ou entraîner un traitement insuffisant. Par conséquent, il faut d'abord s'assurer que la distance et l'angle entre la buse et la pièce sont cohérents, puis ajuster le diamètre de la buse pour rendre le jet plus uniforme et, enfin, vérifier et nettoyer régulièrement l'équipement de sablage pour éviter les obstructions ou les pulvérisations irrégulières.
- Usure et colmatage des buses : Les buses ont tendance à s'user en cas de pulvérisation à haute pression, ce qui peut réduire l'efficacité du sablage et entraîner une dispersion inégale du produit. Utilisez des buses fabriquées dans des matériaux résistants à l'usure, tels que le carbure de bore ou le carbure de tungstène. Contrôlez la pression de pulvérisation pendant l'utilisation afin d'éviter une usure accélérée des buses due à une pression excessive. N'oubliez pas de vérifier régulièrement l'état des buses et de remplacer celles qui sont très usées.
- Pression insuffisante ou fluctuante de l'équipement : Un mauvais contrôle de la pression de pulvérisation peut entraîner un traitement inégal de la surface ou une usure accrue de l'équipement. Si nécessaire, utilisez un régulateur de pression pour contrôler précisément la pression de pulvérisation, en évitant une pression trop élevée ou trop faible. Réglez la pression sur une plage appropriée en fonction du matériau et de la forme de la pièce. Vérifiez également régulièrement le système de pression.
- Questions de sécurité pour les opérateurs de sablage: Si les opérateurs ne prennent pas les mesures de sécurité appropriées pendant le sablage, ils risquent de se blesser. Pour éviter cela, dispensez aux opérateurs une formation complète en matière de sécurité, en mettant l'accent sur les procédures opérationnelles et les mesures de protection. Veillez à ce que les opérateurs portent les équipements de protection nécessaires, tels que des gants, des lunettes et des vêtements de protection, pendant l'utilisation de l'équipement.
- Faible efficacité de la récupération des supports : Une faible efficacité de la récupération des produits peut augmenter les coûts de production et affecter l'environnement. Optimisez le système de récupération de l'équipement de sablage pour garantir une récupération efficace des produits après utilisation. En outre, vérifiez et nettoyez régulièrement le système de récupération pour éviter qu'il ne se bouche ou ne soit endommagé, ou utilisez des produits de haute qualité qui peuvent être recyclés plusieurs fois.
La maîtrise du processus de sablage implique une préparation minutieuse, une configuration précise de l'équipement et un fonctionnement précis. En comprenant et en contrôlant les paramètres du sablage, tels que la pression, le diamètre de la buse et l'angle, ainsi qu'en procédant à une inspection et à un entretien réguliers, vous pouvez obtenir des résultats optimaux en matière de traitement de surface. Qu'il s'agisse de nettoyage, d'ébavurage ou de finition de surface, la maîtrise du processus de sablage garantit que chaque opération répond aux normes les plus strictes, contribuant ainsi à la qualité et aux performances globales de la pièce.
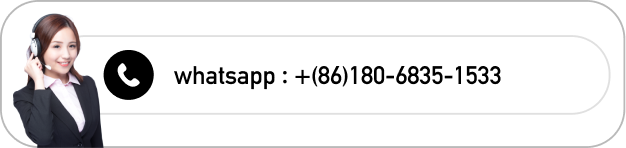