Différences entre Sablage à l'alumine et perles de céramique
27 août 2024
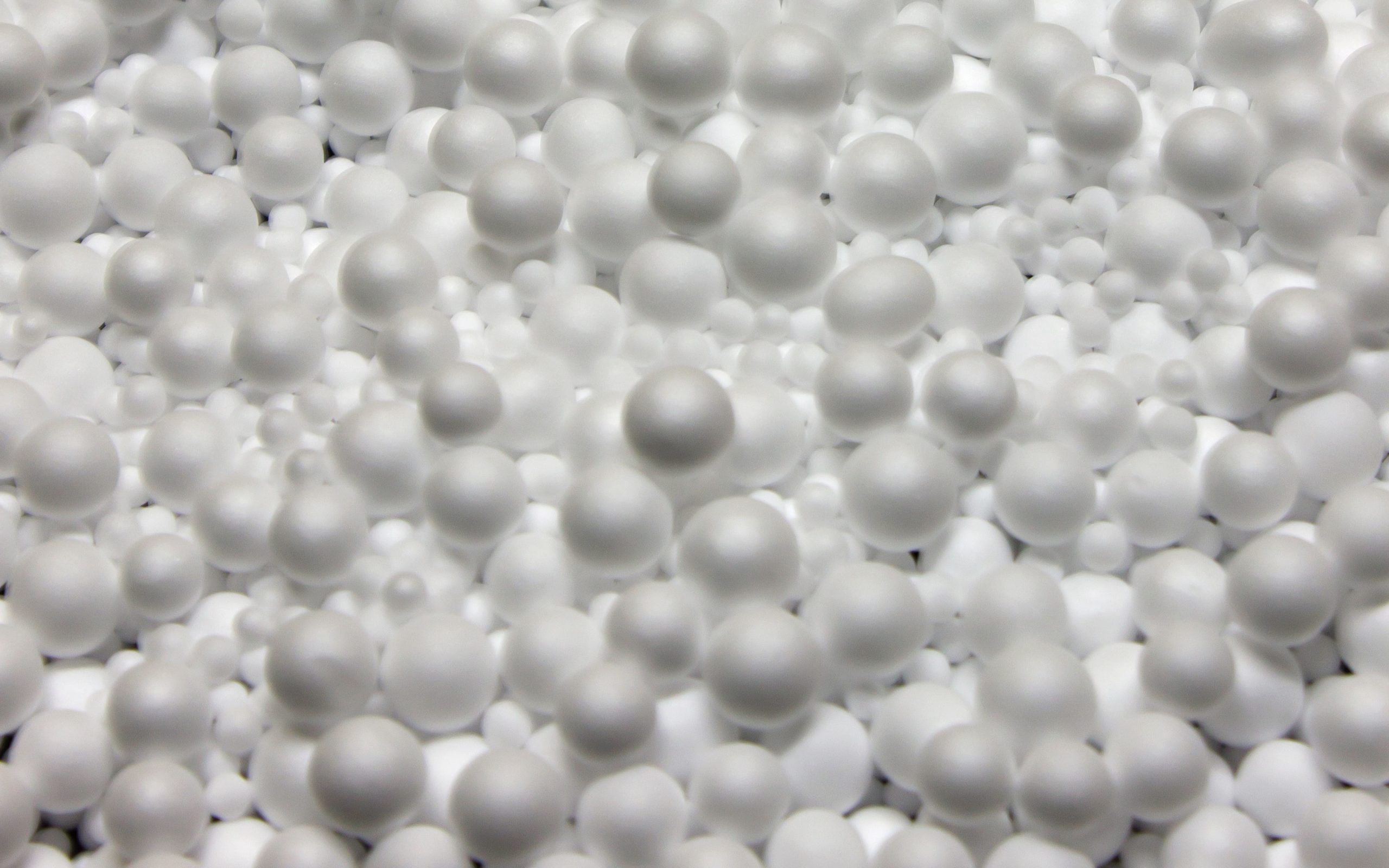
La technologie du sablage joue un rôle important dans le traitement des surfaces en nettoyant, en éliminant les salissures, en améliorant la rugosité de la surface ou en améliorant l'adhérence des matériaux grâce à des jets de sable à haute pression. Toutefois, le choix du support de sablage a une incidence directe sur les résultats et les coûts du traitement. Parmi les abrasifs courants, les abrasifs à base d'oxyde d'aluminium ultrafin et les abrasifs à base de billes de céramique sont largement utilisés. Bien qu'ils présentent des similitudes à certains égards, il existe des différences significatives dans leurs caractéristiques spécifiques, leurs domaines d'application, leurs avantages et leurs inconvénients. Cet article examine en détail les différences entre ces deux types d'abrasifs et résume leurs principales caractéristiques à l'aide d'un tableau comparatif afin de vous aider à choisir l'abrasif le mieux adapté à vos différents besoins de traitement.
Avant tout, les deux médias partagent les caractéristiques communes suivantes :
- Objectif du sablage: Les deux sont utilisés pour impacter la surface des pièces avec des particules en mouvement à grande vitesse afin d'atteindre les objectifs du traitement de surface, y compris l'élimination des dépôts de surface, de la rouille, des revêtements, etc.
- Effet de sablage: Les deux peuvent améliorer efficacement la rugosité de la surface, ce qui la rend plus apte à recevoir un revêtement ultérieur ou d'autres traitements. En outre, les deux médias peuvent produire un léger effet de durcissement à froid sur la surface de la pièce, ce qui contribue à améliorer la résistance à l'usure et la résistance à la fatigue de la pièce.
- Propriétés des matériaux: Les deux ont une dureté élevée et peuvent traiter efficacement divers métaux et céramiques.
- Respect de l'environnement: D'un point de vue relatif, les deux médias sont plus respectueux de l'environnement que certains médias de sablage traditionnels (tels que la grenaille d'acier), car ils provoquent moins d'usure, ce qui réduit la poussière et la pollution.
Ensuite, j'utiliserai un tableau pour vous aider à comprendre rapidement leurs différences, et vous trouverez plus d'informations pertinentes dans l'introduction détaillée ci-dessous.
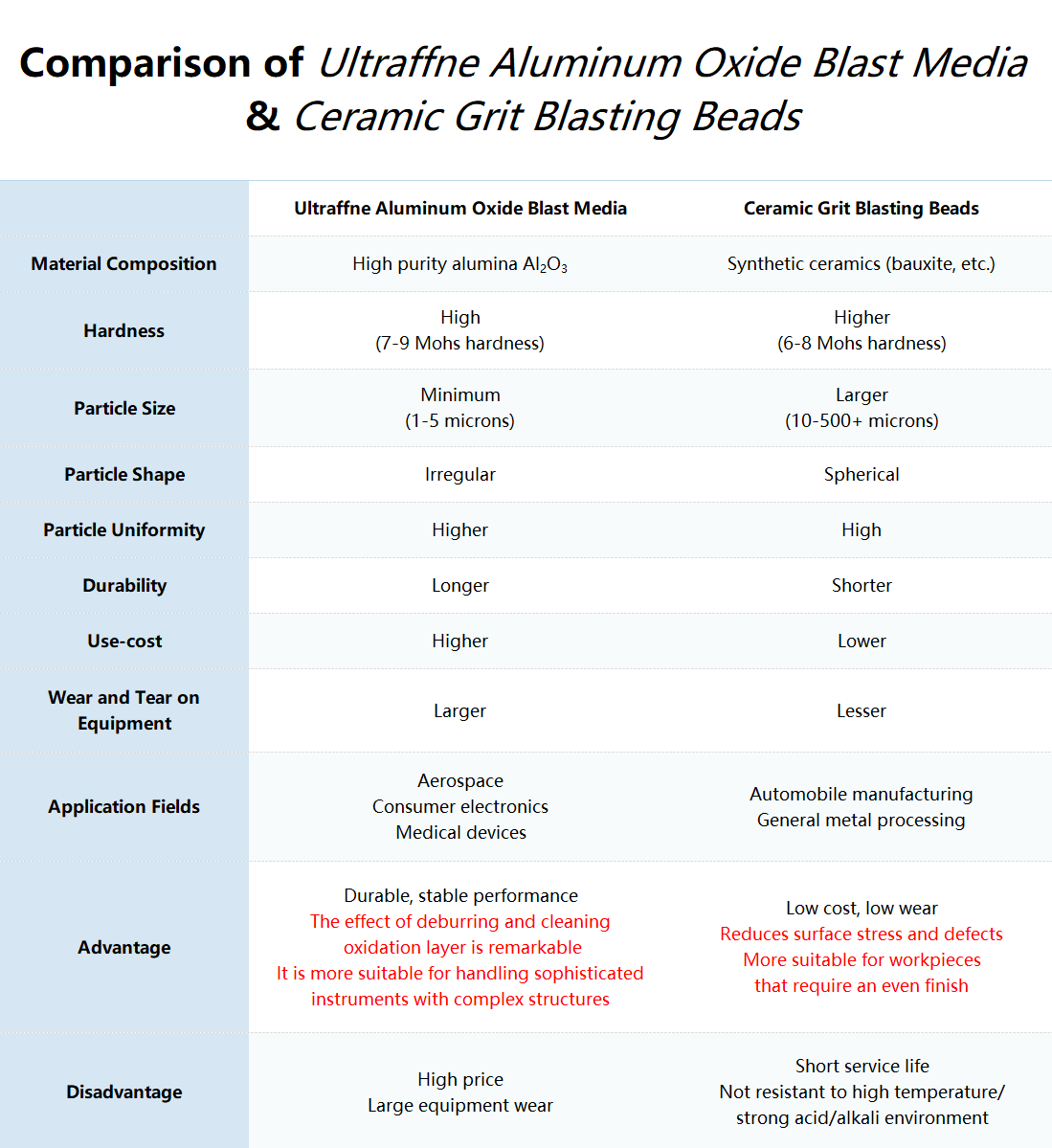
Informations détaillées sur les abrasifs à base d'oxyde d'aluminium ultrafin :
Caractéristiques
- Composition du matériau: Fabriqué à partir d'alumine de haute pureté (Al₂O₃) avec une pureté généralement supérieure à 99%. La taille des particules est très fine, allant généralement de 1 à 5 micromètres.
- Dureté: L'alumine a une dureté élevée, avec une dureté Mohs de 9, la deuxième après le diamant et le carbure de silicium.
- Uniformité des particules: L'alumine ultrafine présente une distribution très uniforme des particules, généralement sous forme de petites particules cristallines, qui peuvent avoir une forme polyédrique, quasi-sphérique ou d'autres formes irrégulières.
- Inertie chimique: Il est difficile de réagir chimiquement avec les matériaux prétraités au cours du traitement, ce qui n'affecte pas les propriétés des matériaux.
Domaines concernés
- Aérospatiale: En raison de ses excellentes performances de coupe et de la taille des particules (de l'ordre du micron), il est utilisé pour le polissage de composants de précision tels que les pales de moteur et les composants d'engins spatiaux, afin d'assurer une finition de surface élevée, facilitant ainsi l'adhésion ultérieure des matériaux.
- Électronique grand public: Utilisé pour éliminer les dépôts sur les produits et les composants électroniques, améliorer la texture de la surface et renforcer la résistance à l'usure et à la corrosion.
- Dispositifs médicaux: Élimine efficacement les bavures et les bords irréguliers des surfaces, garantissant des instruments lisses et réguliers, ce qui est crucial pour les exigences de précision et de qualité de l'industrie médicale.
- Art et design: Grâce au grenaillage fin, les artistes peuvent créer des textures et des motifs uniques sur des matériaux tels que le métal, le verre et la céramique. Cette technologie est largement utilisée dans la sculpture, le mobilier décoratif et la conception architecturale pour donner aux œuvres une texture et des effets visuels uniques.
Avantages
- Haute pureté: Ne produit pas d'impuretés ou de contamination pendant l'utilisation, ce qui garantit une qualité de surface extrêmement élevée après le traitement.
- Particules uniformes et fines: Peut pénétrer dans les petites cavités ou les structures complexes des objets prétraités, ce qui permet d'obtenir un traitement de surface uniforme et de garantir des résultats de sablage constants.
- Inertie chimique: Maintient la stabilité des performances physiques et chimiques dans des environnements difficiles tels que les températures élevées, les acides forts et les alcalis forts.
- Dureté élevée et résistance à l'usure: Maintient sa forme et la stabilité de ses performances sous haute pression, avec une durée de vie plus longue, réduisant ainsi la nécessité d'un remplacement fréquent.
Inconvénients
- Prix relativement élevé.
- Usure importante de l'équipement: Nécessite un entretien régulier et le remplacement des pièces de l'équipement.
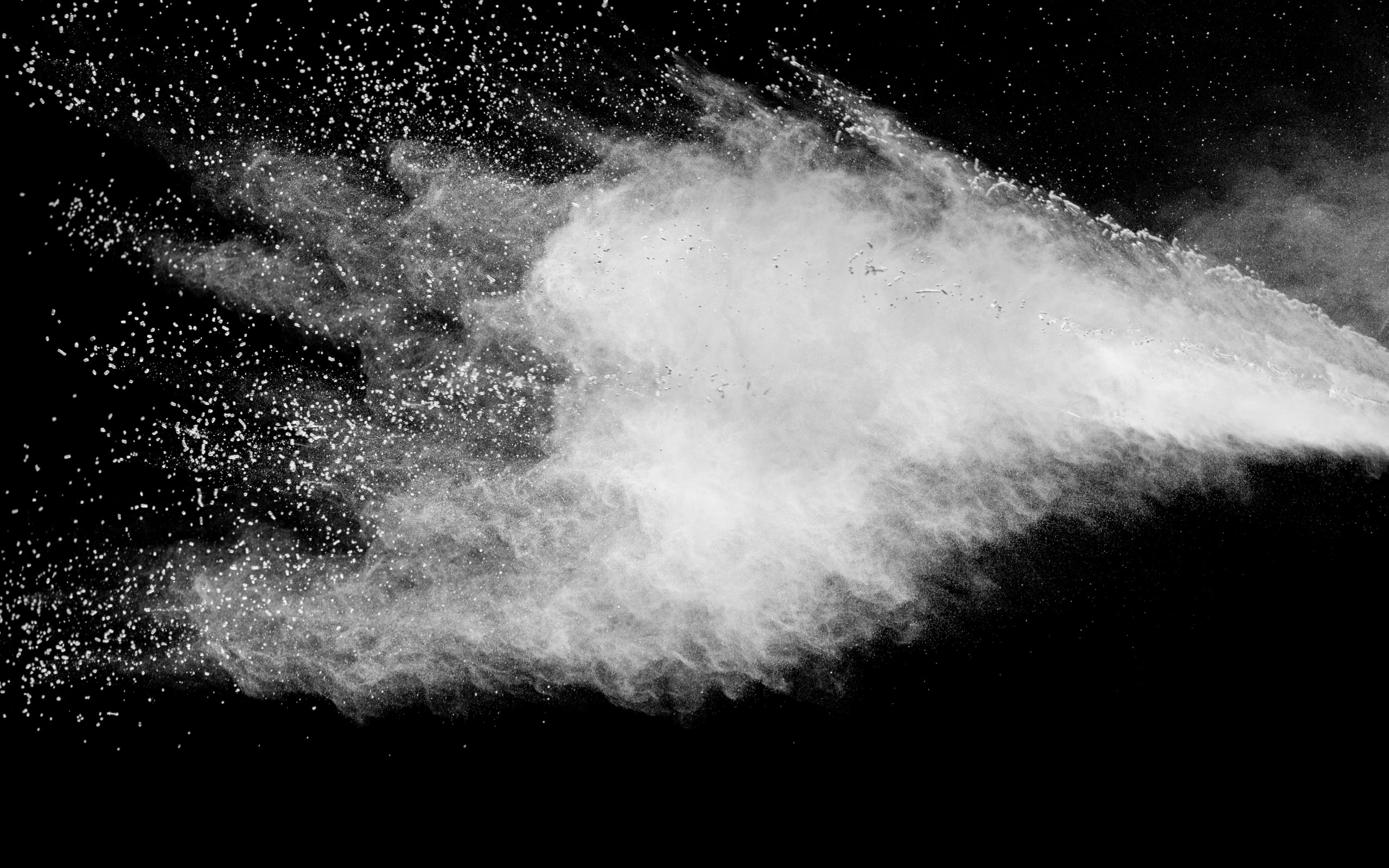
abrasif à l'oxyde d'aluminium ultrafin
Informations détaillées sur les supports de sablage à billes céramiques :
Caractéristiques
- Composition du matériau: Les produits céramiques synthétiques sont généralement composés de zircone, de bauxite et de silice, et sont formés par fusion à haute température.
- Dureté: Les billes de sablage en céramique ont généralement une dureté de Mohs de 6 à 8, légèrement inférieure à celle de l'alumine.
- Forme des particules: Formé en particules sphériques après refroidissement, généralement plus grandes, avec des diamètres allant de quelques dizaines de micromètres à quelques millimètres. Les particules les plus grosses conviennent aux tâches nécessitant une plus grande rugosité de surface.
- Durabilité: Les billes de sablage en céramique ont une résistance à la chaleur relativement faible et peuvent se dégrader ou perdre leurs performances à des températures plus élevées. Elles sont stables dans divers environnements chimiques, mais peuvent être affectées par des conditions fortement acides ou alcalines.
Domaines concernés
- Fabrication automobile: Utilisé pour éliminer les défauts de surface des pièces moulées et améliorer l'adhérence des matériaux afin d'assurer l'uniformité et la durabilité du revêtement.
- Traitement des métaux: Utilisé pour le meulage et le polissage afin d'améliorer la douceur et le toucher des surfaces métalliques.
- Fabrication de meubles: Traite les surfaces de meubles en bois et en métal pour obtenir des effets de ponçage uniformes.
Avantages
- Coût relativement faible: Convient à la production à grande échelle.
- Particules sphériques uniformes: Plus grande taille et possibilité d'atteindre un certain niveau de rugosité de surface, adapté à des besoins spécifiques de traitement de surface.
- Diminution de l'usure de l'équipement.
Inconvénients
- Dureté légèrement inférieure: Ne convient pas pour l'usinage de pièces de précision aux exigences très élevées.
- Mauvaise stabilité chimique: Peut limiter l'utilisation dans des environnements à haute température, fortement acides ou alcalins.
- Durée de vie plus courte: Nécessite un remplacement plus fréquent.
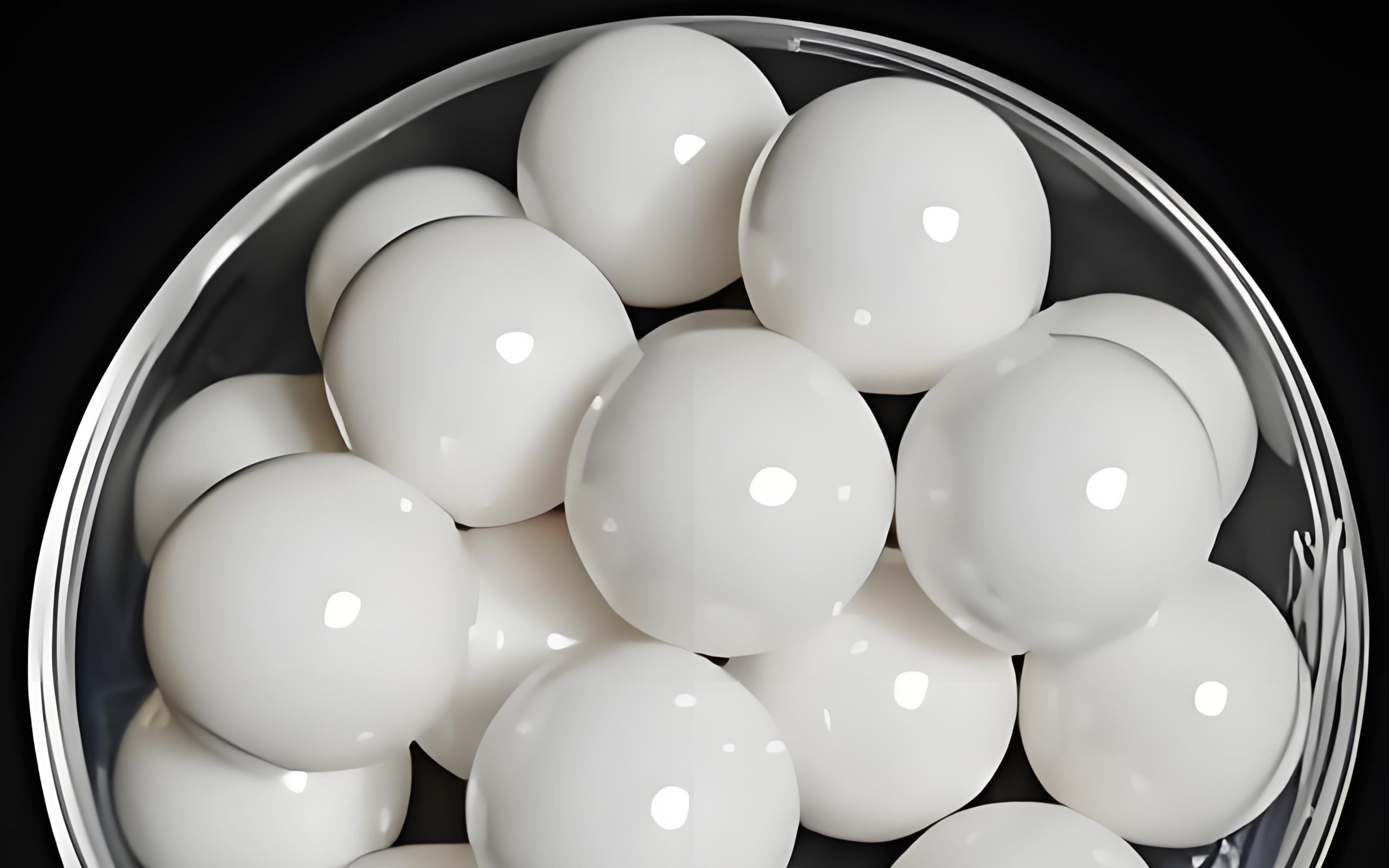
billes de céramique pour le sablage
Dans les applications pratiques, les abrasifs à base d'oxyde d'aluminium ultrafin et les abrasifs à base de billes de céramique excellent tous deux dans leurs domaines respectifs, mais ils présentent des différences significatives en termes d'effets de traitement :
La grenaille d'oxyde d'aluminium ultrafine donne d'excellents résultats lors du traitement de matériaux très durs et très résistants, en éliminant efficacement les oxydes de surface et les bavures, ce qui convient particulièrement au traitement de précision des pièces de forme complexe. Toutefois, en raison de la dureté de ses particules, il provoque une usure importante des machines en cas d'utilisation intensive et continue, ce qui peut nécessiter une inspection et une maintenance régulières.
Les billes de céramique, quant à elles, sont très efficaces pour les tâches nécessitant une finition de surface élevée et une faible tension superficielle, offrant une excellente surface lisse sans endommager la pièce. Ils ont une longue durée de vie et sont réutilisables, ce qui les rend plus rentables en termes de contrôle des coûts et d'efficacité, mais ils peuvent être légèrement inadéquats dans des scénarios très abrasifs et ont certaines exigences et limitations environnementales.
Par conséquent, le choix de l'agent de sablage approprié en fonction des besoins spécifiques permet de maximiser les effets de chaque type, d'améliorer l'efficacité du travail et la qualité du traitement. La grenaille d'oxyde d'aluminium ultrafine, en raison de sa dureté élevée, de sa résistance à l'usure et de la distribution uniforme des particules, est particulièrement adaptée aux applications exigeant une grande précision et une durabilité à long terme.Les billes de grenaillage en céramique, en revanche, sont plus rentables, ont des effets de grenaillage plus uniformes et s'usent moins vite. En revanche, les billes de grenaillage en céramique, avec leur rentabilité, leurs effets de grenaillage uniformes et l'usure moindre de l'équipement, conviennent mieux à la construction automobile et au traitement général des métaux. Pour les traitements de précision nécessitant une finition de surface élevée, les billes de sablage en céramique sont plus appropriées.
En conclusion, outre la prise en compte des besoins de traitement spécifiques, les avantages économiques des deux médias sont également importants :
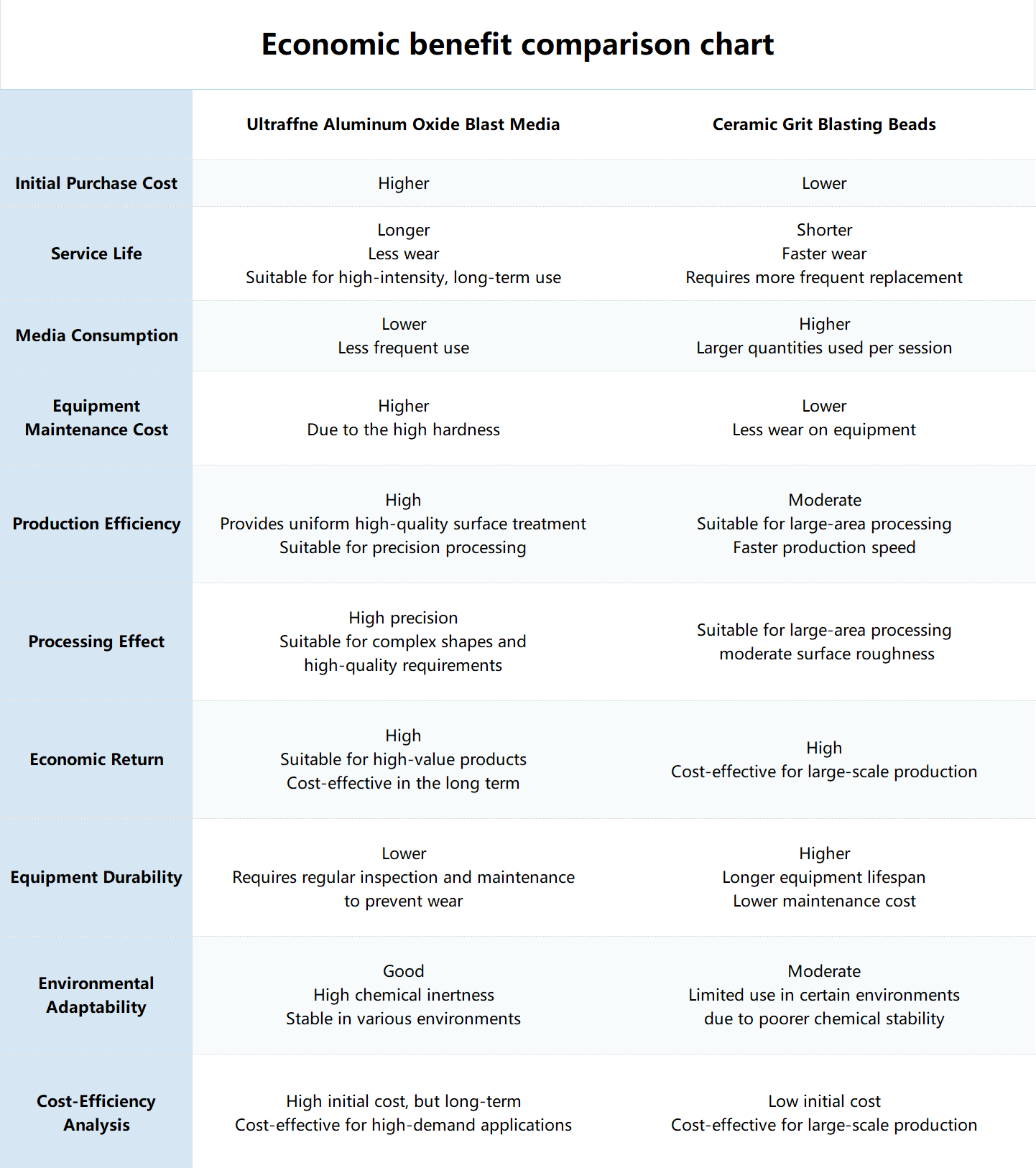
Coût d'achat initial
Les abrasifs à base d'oxyde d'aluminium ultrafin ont un coût d'achat initial plus élevé en raison de leur grande pureté et de la finesse de leurs particules, le processus de fabrication étant plus complexe, le prix du marché est plus élevé. Cet investissement élevé est convient aux applications exigeant un traitement de surface de très haute qualitéLes produits de l'UE sont utilisés dans des domaines tels que l'aérospatiale, les appareils médicaux haut de gamme et l'électronique grand public.
En revanche, les billes de céramique ont un coût de production plus faible en raison des matières premières relativement bon marché telles que la bauxite et la zircone, et des méthodes de production en vrac telles que le frittage à haute température, ce qui se traduit par un prix nettement inférieur à celui des abrasifs à base d'oxyde d'aluminium ultrafin. Les abrasifs à base de billes céramiques conviennent aux industries sensibles aux coûts et aux grands volumes de production., comme la construction automobile et la production de meubles. La réduction des coûts d'achat initiaux permet d'améliorer les marges bénéficiaires globales dans ces domaines.
Vie de service et consommation des médias
Les abrasifs en oxyde d'aluminium ultrafin présentent une dureté et une résistance à l'usure extrêmement élevées. Ainsi, même sous haute pression, ils conservent l'intégrité et la stabilité des particules, ce qui réduit le risque de fragmentation et de détérioration. Cela signifie que Les abrasifs à base d'oxyde d'aluminium ultrafin ont une fréquence de remplacement plus faible et une consommation réduite.et prolonge ainsi sa durée de vie. Bien que le coût d'achat initial soit plus élevé, sa durée de vie plus longue permet d'étaler le coût par utilisation, ce qui est particulièrement important pour les tâches de production à forte demande et à cycle long.
Les billes de sablage en céramique, bien que moins dures, réduisent efficacement l'usure grâce à leur structure sphérique. Toutefois, leur résistance à l'usure et leurs performances anti-fracture sont légèrement inférieures à celles de l'alumine ultrafine, en particulier dans les opérations de sablage à haute intensité, où les billes de sablage en céramique sont moins résistantes que les billes de sablage en aluminium. les billes de céramique s'usent plus rapidement et doivent être remplacées fréquemment. Bien que le coût d'achat initial soit moins élevé, la durée de vie plus courte entraîne une consommation globale plus importante de média, ce qui peut augmenter les coûts de remplacement dans le cadre d'une production à grande échelle à long terme.
Coûts d'entretien et d'exploitation des équipements
Les abrasifs à base d'oxyde d'aluminium ultrafin, en raison de leur dureté plus élevée, provoquent une usure importante des équipements de sablage, en particulier des buses, des pistolets et des tuyauteries. L'équipement peut subir une usure notable après une utilisation prolongée de cet agent, ce qui entraîne une baisse des performances et des besoins potentiels de remplacement et d'entretien. Cette situation peut entraîner une augmentation des coûts de maintenance et des pertes économiques dues aux temps d'arrêt. Par conséquent, les entreprises qui utilisent la grenaille d'alumine ultrafine doivent prendre en compte la fréquence et le coût de l'entretien des équipements et s'ils disposent d'un budget et d'un temps suffisants pour l'entretien régulier.
En revanche, les billes de céramique, dont la dureté est plus faible, provoquent une usure relativement moins importante de l'équipement. Bien que les effets de traitement des billes de céramique n'égalent pas ceux de l'alumine ultrafine dans les applications de haute précision, leur usure moindre se traduit par des coûts de maintenance plus faibles et une durée de vie plus longue de l'équipement. Les billes de céramique sont donc économiquement avantageuses dans la production à grande échelle et de faible précision, où la réduction des temps d'arrêt et de maintenance permet d'améliorer l'efficacité globale de la production.
Efficacité et rentabilité
En termes d'efficacité de production, la dureté élevée et les particules fines de l'alumine ultrafine permettent d'obtenir des effets de traitement de surface extrêmement uniformes, ce qui améliore particulièrement la précision du produit et la qualité de la surface lors du traitement de formes complexes ou de petits composants. Ces performances élevées permettent souvent de fabriquer davantage de produits de haute qualité par unité de temps, ce qui réduit les taux de reprise et de défaut, augmentant ainsi l'efficacité globale de la chaîne de production. Dans la fabrication de certains produits à haute valeur ajoutée, l'utilisation de la grenaille d'alumine ultrafine peut apporter un meilleur rendement économique.
Les billes de céramique, dont la taille des particules est plus importante et la dureté relativement plus faible, peuvent ne pas être aussi fines dans certaines applications, mais permettent de maintenir une efficacité de production élevée dans les tâches nécessitant des surfaces plus grandes ou une plus grande douceur de surface. Dans le cadre d'une production à grande échelle, les avantages en termes de coûts et la vitesse de production plus élevée des billes de grenaillage en céramique en font un choix économique. Pour les entreprises dont les exigences en matière de traitement de surface sont moindres et dont l'objectif principal est la maîtrise des coûts, les billes de sablage en céramique permettent d'équilibrer la qualité et le coût.
Analyse des avantages économiques à long terme
Du point de vue des avantages économiques à long terme, le choix entre les abrasifs à base d'oxyde d'aluminium ultrafin et les abrasifs à base de billes de céramique dépend des tâches de production spécifiques, de la durabilité de l'équipement et du cycle de production global. Si le sablage à l'alumine ultrafine nécessite un investissement initial plus important, sa longue durée de vie et ses résultats de traitement supérieurs le rendent adapté aux produits de grande valeur, offrant un rendement économique à long terme tout en garantissant la qualité. Les billes de grenaillage en céramique, avec leur faible coût et leur grande efficacité, conviennent aux environnements de production à grande échelle et à faible coût, améliorant le bénéfice global en réduisant les coûts opérationnels quotidiens.
Au fur et à mesure que la technologie progresse, de nouveaux agents de sablage et des techniques de sablage améliorées continueront d'apparaître, rendant le traitement de surface futur plus efficace et plus précis. Cette introduction détaillée vous a permis de découvrir les caractéristiques et les domaines d'application de ces deux agents de sablage, ce qui vous aidera à faire un choix plus approprié dans les applications pratiques. En outre, veillez à sélectionner l'agent de sablage le plus approprié en fonction des besoins de production spécifiques de votre entreprise, de votre budget et du positionnement de votre produit. Une réflexion approfondie vous permettra d'optimiser la rentabilité sur le marché concurrentiel.
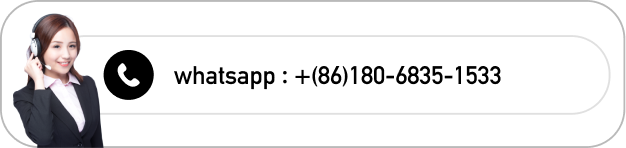