Billes de sablage céramique pour le traitement de surface du verre des écrans tactiles
29 août 2024
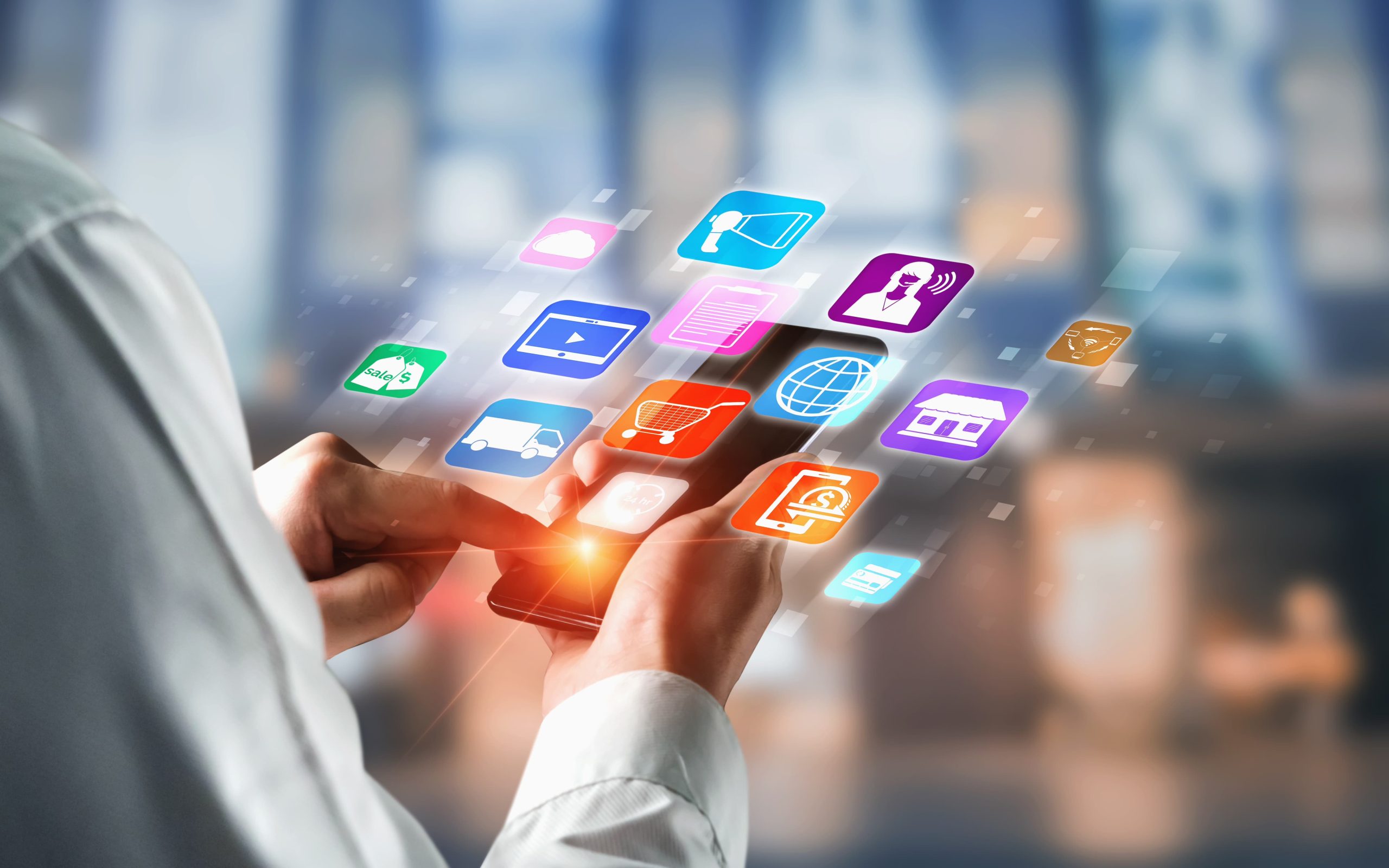
Ces dernières années, la technologie des écrans tactiles a fait des progrès significatifs dans le domaine de l'électronique grand public. En particulier, l'introduction de nouveaux écrans tactiles à haute résolution a porté la qualité d'affichage et l'expérience utilisateur des appareils électroniques à de nouveaux sommets. Par exemple, en septembre 2023, Samsung a officiellement lancé son dernier Galaxy Z Fold 5, doté d'un écran tactile AMOLED de sixième génération. Ce nouveau modèle présente non seulement une amélioration significative de la précision des couleurs, mais fait également des percées substantielles en matière de résistance aux rayures. Samsung affirme que des technologies révolutionnaires ont été employées pour améliorer la sensibilité tactile et la clarté de l'écran, les processus avancés de traitement de la surface du verre de l'écran tactile jouant un rôle central dans ces améliorations. Cette technologie a joué un rôle clé dans l'amélioration des performances du verre des écrans tactiles, devenant l'un des principaux facteurs garantissant les performances exceptionnelles de l'écran.
Le processus de fabrication du verre pour écran tactile est une procédure complexe et précise qui comprend plusieurs étapes clés pour produire au final un verre de haute performance répondant aux normes requises. Chaque étape joue un rôle crucial dans la détermination de la performance et de la qualité finales du verre. Ci-dessous, je vous propose une description détaillée du processus de fabrication du verre pour écran tactile, en mettant l'accent sur le processus de traitement de surface final. À la fin, vous comprendrez pourquoi le grenaillage est si important.
Aperçu du processus de fabrication du verre pour écran tactile
- Sélection des matériaux: La première étape de la production de verre pour écran tactile de haute qualité consiste à sélectionner les matières premières appropriées. En général, le composant principal du verre est le dioxyde de silicium (SiO₂), avec une certaine proportion de sodium, de potassium, de calcium et d'autres éléments pour ajuster les propriétés physiques et chimiques du verre.
- Fusion et mise en forme: Une fois la formule du matériau déterminée, ces matériaux sont fondus à haute température pour former un liquide de verre uniforme. Le verre fondu est ensuite façonné à l'aide de divers procédés de formage tels que le flottage ou le laminage pour produire du verre plat. Cette étape définit la forme et l'épaisseur initiales du verre, servant de base au traitement ultérieur.
- Recuit: Le verre formé subit généralement un recuit, un processus de traitement thermique destiné à éliminer les tensions internes générées lors du façonnage. Le verre est chauffé à une certaine température puis lentement refroidi afin de répartir uniformément les contraintes internes et d'éviter toute rupture spontanée lors d'une utilisation ultérieure.
- Traitement de surface: Après le recuit, le verre passe à l'étape du traitement de surface, qui est cruciale pour améliorer les performances des écrans tactiles. Le traitement de surface vise à améliorer les propriétés de la surface du verre afin de mieux répondre aux exigences de l'application tactile. Les méthodes courantes de traitement de surface comprennent le sablage, le renforcement chimique et le revêtement physique. Parmi ces procédés, les billes de sablage en céramique sont largement utilisées pour l'optimisation de la surface en raison de leurs propriétés uniques.
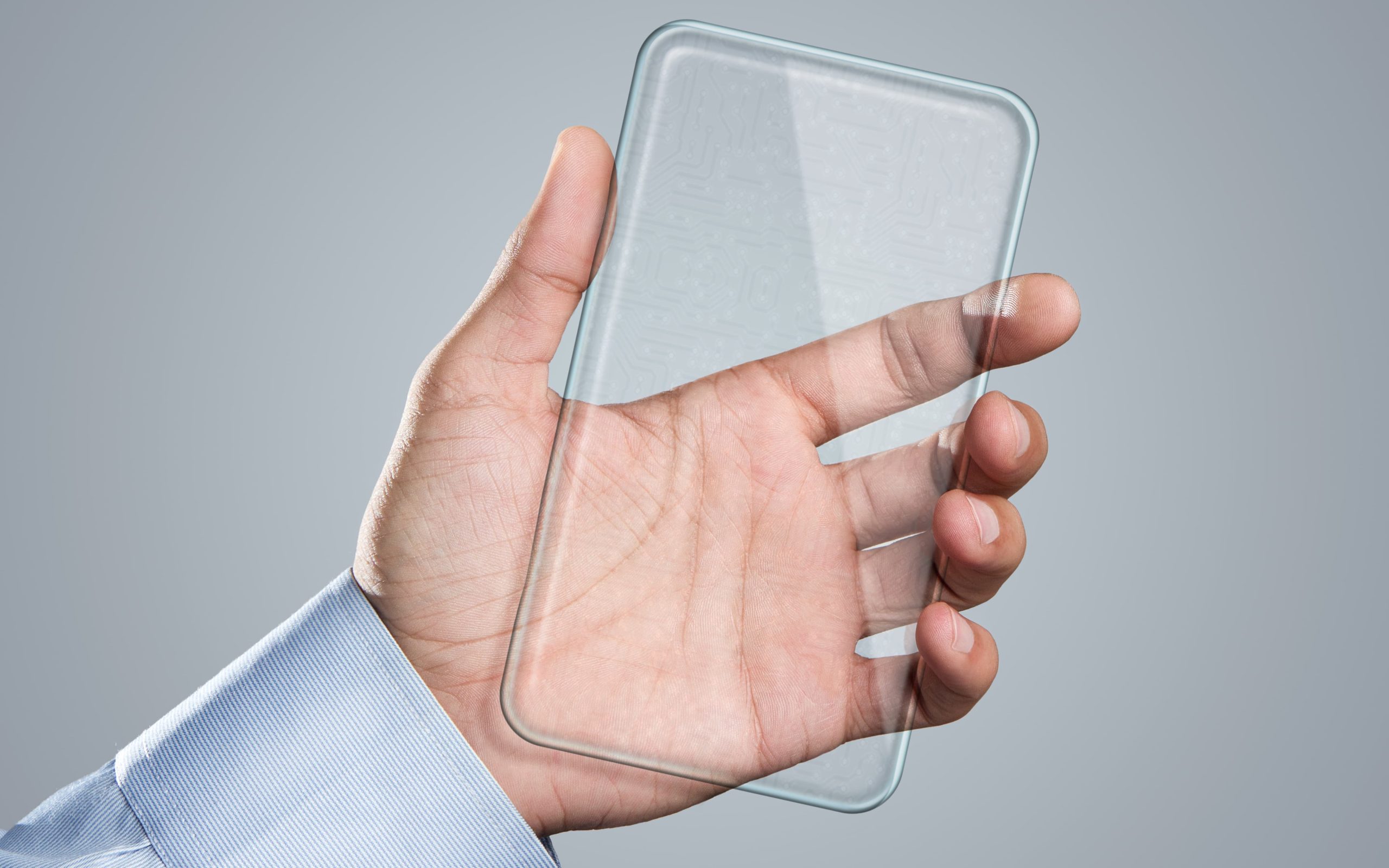
Verre de l'écran tactile
Le traitement de surface du verre des écrans tactiles n'est pas seulement esthétique, il vise également à lui conférer des caractéristiques fonctionnelles spécifiques afin de répondre aux exigences élevées des produits électroniques modernes sur l'écran. Voici quelques technologies clés de traitement de surface et leurs applications dans le domaine du verre pour écran tactile.
Sablage céramique: L'utilisation de billes de sablage en céramique permet d'améliorer considérablement les effets tactiles et visuels du verre, ce qui rend les écrans tactiles plus durables. Comparé à d'autres méthodes de traitement de surface, le sablage céramique offre une efficacité et une précision élevées, améliorant de manière significative les performances de la surface sans affecter la transparence globale du verre.
Renforcement chimique: Généralement associé au sablage céramique, le renforcement chimique consiste à immerger le verre dans un bain de sel fondu contenant des ions de potassium à des températures élevées. Ce processus d'échange d'ions renforce la dureté de la surface du verre en remplaçant les petits ions sodium par des ions potassium, ce qui crée une contrainte de compression à la surface. Il en résulte une meilleure résistance aux chocs et aux rayures, ce qui est essentiel pour les smartphones et les tablettes modernes.
Revêtements physiques: Outre le renforcement physique et chimique, les revêtements physiques constituent un aspect important du traitement de la surface du verre des écrans tactiles. Les revêtements les plus courants sont les revêtements anti-traces de doigts, anti-reflets et anti-éblouissement. Ces revêtements sont appliqués par des méthodes telles que la pulvérisation cathodique ou le dépôt chimique en phase vapeur pour conférer des fonctions spéciales au verre. Par exemple, les revêtements anti-traces de doigts réduisent les résidus de traces de doigts sur les écrans, tandis que les revêtements anti-reflets améliorent la visibilité sous la lumière du soleil.
Combinaison de technologies: Dans la pratique, le traitement de la surface du verre des écrans tactiles implique souvent une combinaison de technologies. Par exemple, le sablage céramique peut d'abord améliorer la rugosité de la surface, suivi d'un renforcement chimique pour augmenter la dureté, et enfin de l'application d'un revêtement anti-traces de doigts. Cette approche globale du traitement permet d'obtenir d'excellentes propriétés multiples, répondant ainsi à des normes élevées en matière de performances des écrans tactiles.
Grâce à l'application combinée de ces technologies clés, le verre de l'écran tactile a atteint un équilibre idéal en termes de résistance aux rayures, de résistance aux chocs, de confort tactile, etc.
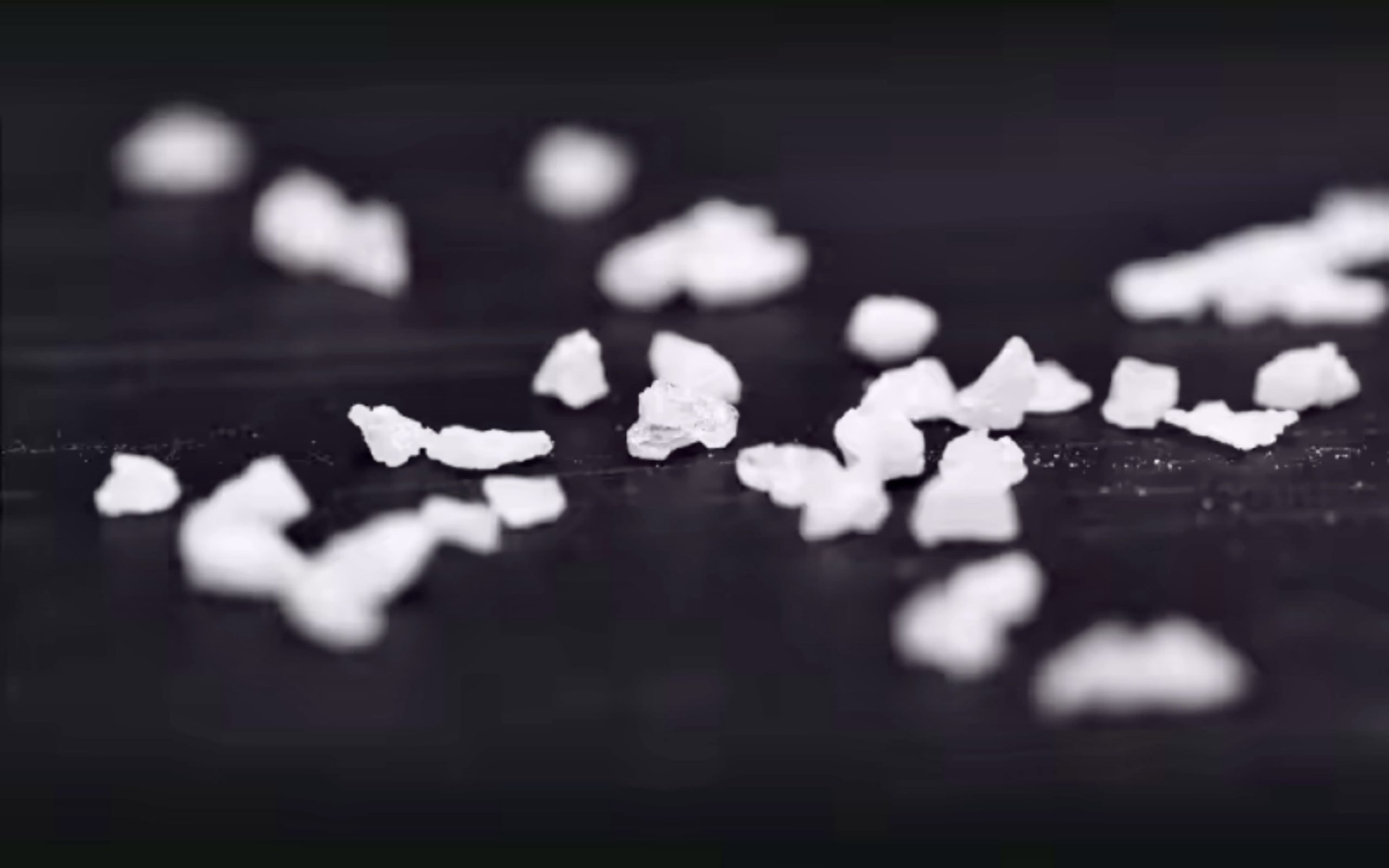
Détail des billes de sablage en céramique
Rôle spécifique des billes de sablage céramique
- Optimisation de la rugosité de surface: Le traitement de surface du verre des écrans tactiles est essentiel pour améliorer les effets tactiles et visuels. Les billes de sablage en céramique, en raison de leur dureté et de leur uniformité supérieures, ajustent précisément la rugosité de la surface du verre. Le sablage crée une micro-texture uniforme sur le verre de l'écran tactile, ce qui améliore le confort du toucher et la fluidité du glissement de l'écran. Dans le cas cité, le sablage a considérablement amélioré la sensation tactile de l'écran, rendant l'expérience tactile plus douce et plus naturelle, ce qui a permis de conquérir des parts de marché.
- Élimination des contaminants de surface: Lors de la production de verre pour écrans tactiles, la surface accumule souvent de petits oxydes, des huiles et de la poussière. Les billes de sablage en céramique excellent dans le nettoyage de ces contaminants. Par rapport aux méthodes de nettoyage traditionnelles, le sablage peut éliminer en profondeur les salissures de surface tout en évitant les rayures ou autres dommages, ce qui permet de conserver une surface de verre propre et lisse. Cet effet de nettoyage est essentiel pour améliorer les performances optiques de l'écran tactile.
- Amélioration de l'adhérence: Le verre des écrans tactiles doit souvent être recouvert d'une couche anti-traces de doigts ou d'autres couches fonctionnelles. Le traitement par sablage peut améliorer l'adhérence de la surface du verre, garantissant que ces couches adhèrent fermement et ne se décollent pas. Cette meilleure adhérence prolonge non seulement la durée de vie de l'écran, mais garantit également une meilleure résistance aux empreintes digitales et aux rayures, ce qui améliore l'expérience de l'utilisateur.
- Améliorer la durabilité: Grâce à leur dureté élevée, les billes de céramique utilisées pour le sablage améliorent considérablement la durabilité du verre de l'écran tactile. Les surfaces en verre sablé résistent mieux aux rayures et à l'usure quotidiennes, préservant ainsi les performances visuelles et tactiles de l'écran.
Sélection des particules et technologie d'application
- Impact de la taille des particules: La taille des particules des billes de grenaillage en céramique affecte directement les résultats du traitement du verre des écrans tactiles. Les différentes tailles de particules produisent des effets différents lors du traitement de surface. Par exemple, les particules F120 63-125 microns conviennent aux finitions très brillantes, tandis que les particules F170 45-90 microns sont plus adaptées à une rugosité moyenne. Le choix de la taille de particule appropriée est crucial pour obtenir l'effet de surface désiré.
- Optimisation des paramètres de sablage: Les paramètres tels que la pression de sablage, l'angle et le temps de traitement ont un impact significatif sur les résultats. L'optimisation de ces paramètres garantit que les particules agissent uniformément sur la surface du verre, ce qui permet d'obtenir la meilleure rugosité et la meilleure propreté de la surface. Par exemple, une pression de sablage excessive peut provoquer trop de rayures, tandis qu'une pression trop faible peut ne pas permettre d'éliminer efficacement les contaminants.
- Sélection de l'équipement de sablage: Le choix du bon équipement de sablage est également important. Les équipements modernes offrent des fonctions de contrôle précises, permettant d'ajuster le débit et la pression de sablage afin d'appliquer efficacement différentes tailles de particules. L'entretien et les contrôles réguliers de l'équipement sont également essentiels pour garantir des résultats de sablage constants.
Analyse de cas pratiques
- Cas de réussite: Outre le Samsung Galaxy Z Fold 5, le Huawei Mate X2 est un autre exemple de réussite. Huawei a utilisé des billes de céramique de haute qualité lors de la production, ce qui a permis d'obtenir une excellente résistance aux rayures et une excellente expérience tactile. La vitre de l'écran tactile de ce téléphone utilise la technologie de sablage céramique, ce qui améliore les effets visuels et la durabilité. Apple a également utilisé des billes de céramique pour son iPad Pro, améliorant ainsi considérablement la durabilité de l'écran et la précision du toucher.
- Cas de défaillance: Malgré les excellentes performances des billes de grenaillage en céramique dans de nombreuses applications, une utilisation inappropriée peut entraîner des problèmes. Par exemple, l'utilisation de particules trop grosses peut provoquer des rayures mineures sur la surface du verre, ce qui affecte l'expérience tactile et la clarté visuelle. Après avoir ajusté le processus, ce problème a été résolu, mais cet exemple souligne la nécessité d'un contrôle précis de la taille des particules et des paramètres de traitement pour éviter les effets négatifs potentiels.
- Potentiel futur: Les billes de sablage en céramique ne sont pas seulement performantes dans le verre des écrans tactiles, elles présentent également un large potentiel d'application dans les futurs produits électroniques. Par exemple, dans les appareils de réalité virtuelle (VR) et de réalité augmentée (AR), la technologie de sablage peut être utilisée pour traiter les écrans haute résolution afin d'améliorer l'immersion et la clarté de l'image. En outre, l'utilisation de billes de sablage en céramique dans les appareils portables et les produits domestiques intelligents peut améliorer la durabilité et l'esthétique, offrant ainsi une meilleure expérience à l'utilisateur.
Applications dans d'autres domaines de l'électronique grand public
- Traitement de surface des composants électroniques: Outre le verre des écrans tactiles, les billes de sablage en céramique jouent également un rôle important dans le traitement de surface d'autres composants électroniques. Par exemple, lors de la fabrication de composants électroniques, la technologie de sablage peut améliorer efficacement la finition de la surface, accroître la fiabilité des pièces soudées et améliorer les performances globales.
- Boîtiers d'appareils électroniques: Le traitement de surface des boîtiers d'appareils électroniques doit également tenir compte de la durabilité et de l'esthétique. Les billes de grenaillage céramique peuvent fournir une texture de surface uniforme, donnant au boîtier un aspect moderne tout en améliorant la résistance aux rayures et la durabilité.
- Instruments de précision: Dans la production d'instruments électroniques de précision, les billes de sablage en céramique peuvent optimiser la qualité de la surface. Le traitement par sablage fin permet de réduire efficacement les défauts de surface et d'améliorer la précision et la stabilité des instruments.
- Matériel informatique: Dans la fabrication de matériel informatique, comme les processeurs et les cartes graphiques, les billes de grenaillage en céramique peuvent être utilisées pour améliorer le traitement de surface des dissipateurs thermiques, ce qui améliore la conductivité thermique ainsi que les performances globales et la durabilité du matériel.
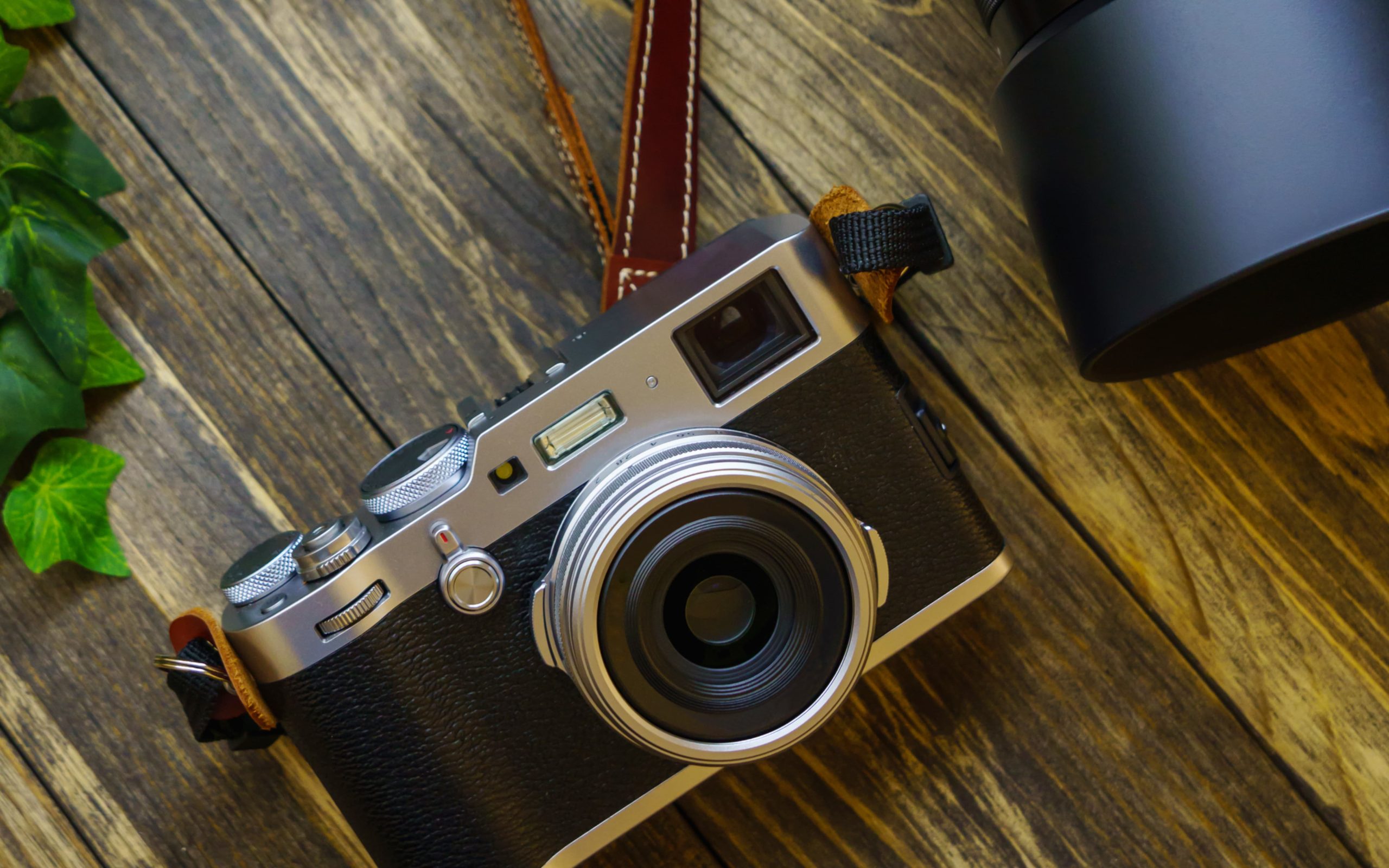
Le boîtier et le toucher de l'appareil photo influencent la décision d'achat
Tendances futures dans le traitement de surface du verre des écrans tactiles
Avec les progrès technologiques constants, la technologie des écrans tactiles évolue également. À l'avenir, le traitement de surface des écrans tactiles pourrait non seulement se concentrer sur l'amélioration des effets tactiles et visuels, mais aussi englober des exigences plus fonctionnelles. Par exemple, le verre des futurs écrans tactiles pourrait intégrer des fonctions telles que la protection contre la lumière bleue et les propriétés antibactériennes, les progrès réalisés dans le domaine des billes de sablage en céramique permettant de prendre en charge ces nouvelles caractéristiques. En optimisant continuellement les processus de sablage et les spécifications des particules, les fabricants peuvent développer des écrans tactiles plus performants pour répondre aux demandes en constante évolution du marché.
Orientations futures pour le développement des billes de grenaillage en céramique
La tendance du progrès technologique
Grâce aux progrès constants de la technologie du sablage, la nouvelle génération de billes de sablage en céramique a non seulement considérablement amélioré sa dureté et son uniformité, mais a également optimisé sa forme et la distribution de ses particules. Ces innovations permettent au processus de sablage d'obtenir une finition de surface plus fine. Des applications telles que les billes de sablage en céramique à l'échelle nanométrique permettent d'effectuer des ajustements de surface à des échelles encore plus petites, ce qui améliore encore la qualité et les performances du verre des écrans tactiles. En outre, des équipements de sablage plus efficaces sont également en cours d'introduction, destinés à fonctionner avec de nouvelles particules de sablage. Les futures technologies de sablage pourraient également introduire des éléments plus intelligents et automatisés, tels que la surveillance en temps réel des effets du sablage grâce à des capteurs et l'ajustement automatique des paramètres de sablage afin d'obtenir un traitement de surface plus précis.
Protection de l'environnement et développement durable
La protection de l'environnement et la durabilité deviendront une orientation importante pour le développement de la technologie de sablage à l'avenir. L'utilisation de matériaux respectueux de l'environnement et la réduction des déchets générés par le processus de production seront des objectifs importants des futures innovations technologiques. Aujourd'hui, la recherche et le développement de billes de sablage en céramique respectueuses de l'environnement sont en cours, et certaines d'entre elles peuvent même être mises sur le marché. L'utilisation de technologies permettant de développer des particules de sablage recyclables et de réduire les émissions de gaz d'échappement réduira efficacement l'impact environnemental du processus de production et contribuera également à améliorer le niveau de protection de l'environnement de l'ensemble de l'industrie.
En résumé, les billes de sablage céramique jouent un rôle crucial dans l'amélioration des performances et de la qualité du verre des écrans tactiles. En optimisant la rugosité de la surface, en éliminant les contaminants, en améliorant l'adhérence et en renforçant la durabilité, la technologie de sablage céramique augmente considérablement les performances des écrans tactiles. L'application pratique de ces particules dans des marques connues comme Samsung, Huawei et Apple met en évidence leur efficacité. Les progrès technologiques, les considérations environnementales et les solutions personnalisées continueront à stimuler le développement des billes de sablage en céramique, en veillant à ce qu'elles répondent aux besoins évolutifs des produits électroniques et contribuent à améliorer l'expérience de l'utilisateur.
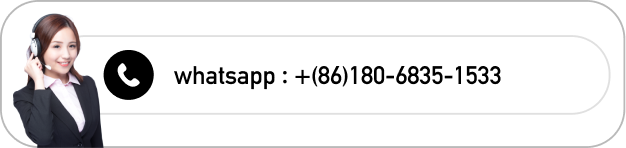